Year: 2017
NAT 2018
Event Name: 2018 North American Tunneling Conference
Dates: June 24-27, 2018
Location: Washington, D.C.
Venue: Washington Marriott Wardman Park
The Robbins Company looks forward to seeing you at the 2018 North American Tunneling Conference in Washington, DC, June 24 through 27. Stop by booth 317 to learn more about past successes and exciting current tunneling endeavors.
Robbins Presentations
Monday, June 25
Technology Track – Project Controls
“Logistics and Performance of a Large Diameter Crossover TBM for the Akron Ohio Canal Interceptor Tunnel”
P. Salazar (presented by D. Ofiara); Robbins, Solon, OH and C. Maxon; Kenny-Obayashi JV
Case Histories Track – Sewer/Water 1
“Boring Hard, Abrasive Gneiss with a Main Beam TBM at the Atlanta Water Supply Program”
T. Fuerst; Robbins, Solon, OH and D. Del Nero; Stantec, Atlanta, GA
Tuesday, June 26
Technology Track – TBM Technology 1
“TBM Tool Wear Analysis for Cutterhead Configuration and Resource Planning in Glacial Geology”
K. Mosavat; The Robbins Company, Kent, Washington, J. Aguilar; CDM Smith, Burnaby, British Columbia, Canada, U. Gwildis; CDM Smith, Bellevue, Washington
Wednesday, June 27
Planning Track – Planning for Success: Risk Management & Contracting Strategies
“The Risks Associated with TBM Procurement and the Next Steps Towards Industry Change”
L. Home; The Robbins Company, Solon, OH and G. Brierley; Doctor Mole Incorporated, Denver, CO
WTC 2018
Event Name: WTC 2018
Dates: April 21-26, 2018
Location: Dubai, United Arab Emirates
Venue: Dubai World Trade Centre
The Robbins Company will be attending ITA-AITES World Tunnel Congress 2018 in Dubai, United Arab Emirates, April 21 through 26. Be sure to visit us at stand 70-71 between April 23 through 25 to learn more about Robbins TBMs operating world-wide.
Robbins Presentations
Monday, April 23
14:20 – 14:40 Robbins Vice Present Doug Harding, “Excavating Turkey’s Hardest Rock at the Bahce-Nurdag Railway Tunnel”
Wednesday, April 25
9:40 – 10:00 Robbins Director of Engineering Brad Grothen, “Excavating Turkey’s Most Challenging Project – The Gerede Water Transmission Tunnel”
12:15 – 12:35 Robbins Mexico Managing Director Roberto Gonzalez, “Excavating Mexico City’s Mega-Tunnel in Mixed Ground at 150 Meters Deep: Emisor Oriente Wastewater Tunnel Lot 5”
NASTT 2018
Event Name: NASTT’s No-Dig Show 2018
Dates: March 25-29, 2018
Location: Palm Springs, CA, USA
Venue: Palm Springs Convention Center
The Robbins Company is looking forward to seeing you in Palm Springs, CA for NASTT’s No Dig 2018 March 25 through 29. Visit booth 470 during exhibit hours to discover how renting or owning a Robbins Small Boring Unit (SBU) can save you time and money on your next boring project.
Congreso Nacional de Ingenieria Civil
Event Name: Congreso Nacional de Ingenieria Civil
Dates: March 1-8, 2018
Location: Mexico City, Mexico
Venue: World Trade Center
Join The Robbins Company at Congreso Nacional de Ingenieria Civil March 1 through 8, in Mexico City, Mexico. Visit our booth to learn more about current techniques being used on Robbins projects throughout the world.
UCT 2018
Event Name: Underground Construction Technology (UCT) 2018
Dates: January 30-February 1, 2018
Location: New Orleans, LA, USA
Venue: Ernest N. Morial Convention Center
The Robbins Company will be attending Underground Construction Technology 2018 January 30 through February 1. Be sure to visit our booth to learn more about Robbins Small Boring Units (SBUs)—the most cost effective and time efficient way to bore through hard rock.
What's Going On? A Quarterly Worldwide Jobsite Roundup
At any given time, Robbins TBMs are operating at dozens of jobsites around the world. Our dedicated Field Service personnel take video and pictures of the TBM progress often, so we’ve decided to offer a quarterly roundup of what’s going on in picture and video format–from deep TBM assembly in New York, USA to an epic TBM launch in the Himalayan mountains of Nepal. Read on to found out the latest.
TBM Assembly in a Deep Shaft in New York, USA
A 6.8 m (22.3 ft) Robbins Single Shield TBM, designed for water pressures up to 20 bar, is undergoing assembly and testing at the Delaware Aqueduct Repair Project. The TBM will be launched from a starter tunnel at the bottom of a 274 m (900 ft) deep shaft.
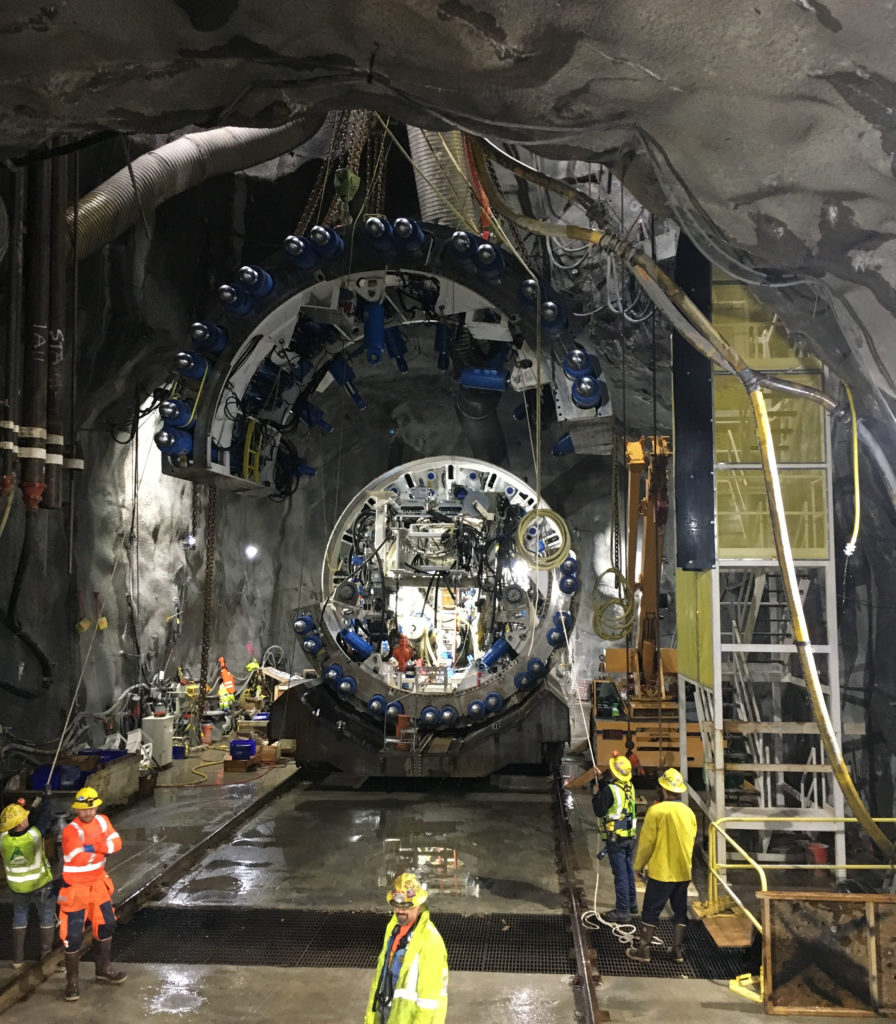
TBM Assembly at the Delaware Aqueduct Repair in Newburgh, New York, USA. The shaft is an incredible 274 m (900 ft) deep.
TBM Assembly Time Lapse
Epic TBM Launch in the Himalayan Mountains
In the Siwalik Range of the southern Himalayan Mountains of Nepal, a 5.06 m (16.6 ft) Robbins Double Shield embarked to bore the Bheri Babai Diversion Multipurpose Project (BBDMP). The TBM launched on October 14. See the drone footage taken by our own Field Service TBM Mechanic Thomas Fuchs:
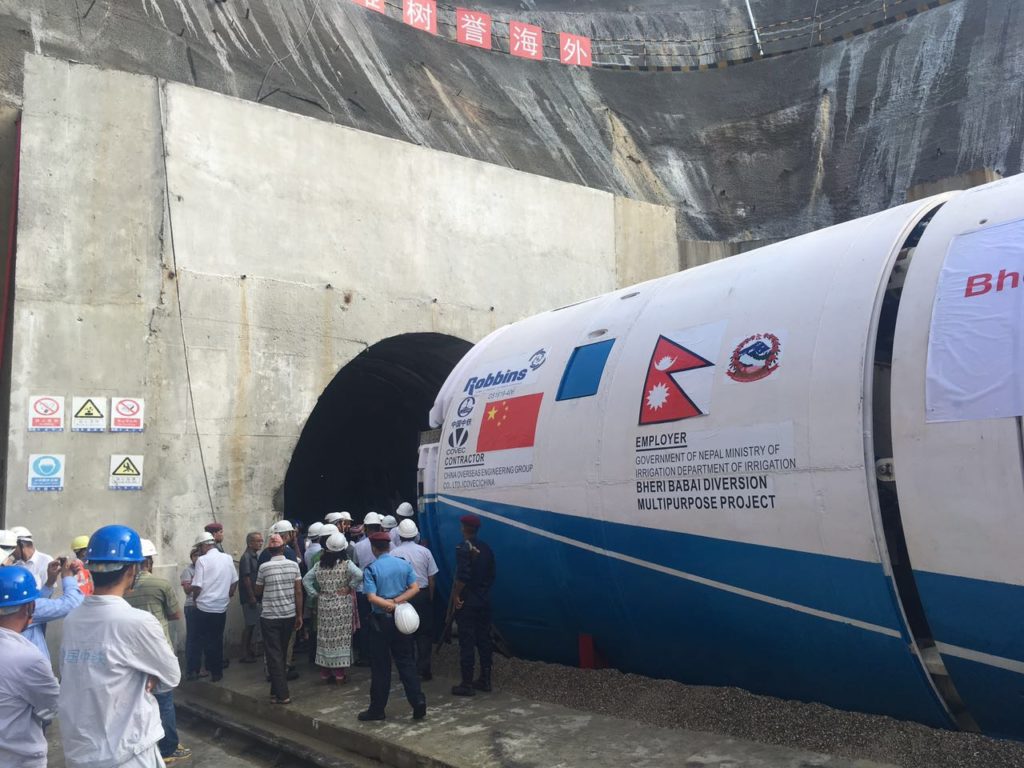
Launch of the Robbins Double Shield at Nepal’s BBDMP on October 14.
Crossover Machine Startup in Akron, Ohio
On October 19, a Robbins 9.26 m (30.4 ft) diameter Crossover (XRE) TBM launched below Akron, Ohio, USA to bore the OCIT tunnel. The machine is excavating in soft soils that will transition into mixed face and then full face shale. Before its launch, personnel at the jobsite filmed the cutterhead testing in a unique way. Watch the video below for more:
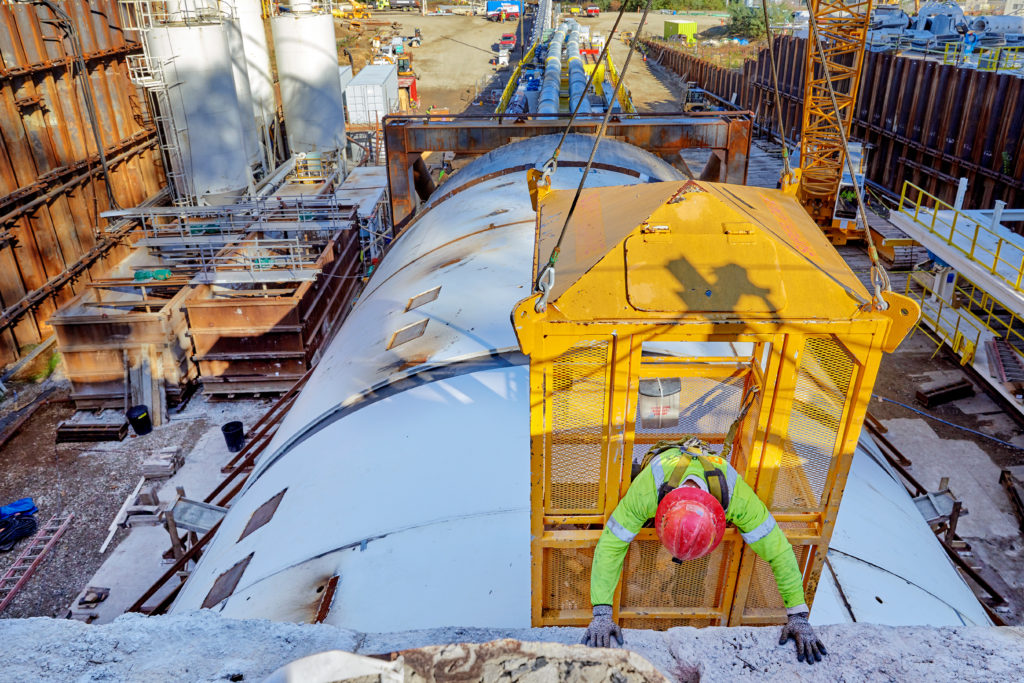
A worker surveys the TBM prior to its launch on the Akron OCIT October 19.
Robust Robbins EPB Completes Third Bore for Chennai Metro Project
On Tuesday, October 31, 2017, a 6.65 m (21.8 ft) diameter Robbins EPB TBM broke through at Chennai Metro, making this the third tunnel the machine has bored for the project and for contractor Afcons Infrastructure Ltd. The three separate bores for the EPB are part of an increasing trend, as many Robbins EPBs have been used on multiple tunnel drives with good performance. Robbins EPBs are built one third heavier than any other EPB on the market and are designed for 10,000 hours of usable life, making them ideal machines for use over many kilometers. “Robbins is known for designing resilient machines,” said Mr. Gopal Dey, Afcons Senior Manager. “For this project, we needed a machine that was specifically tailored to project conditions from soft clay to mixed ground with rock. Robbins EPB TBMs have unique design features that optimize the machine for the geology.”
After completing its original twin tunnels, the EPB was refurbished in preparation to bore its latest 1.8 km (1.1 mi) section. During refurbishment, the inner seal greasing system was changed from auto to manual mode and the foam nozzle system was modified. These changes optimized the machine for excavation in the highly variable mixed face conditions encountered in the first two tunnels.
The EPB was launched on February 3, earlier this year. According to contractor Afcons, the machine faced a major challenge right out of the gate. “When the TBM came out of the launching shaft, a few rings were erected and then the machine had to cross a live railway track, which meant there would be a possibility of ground settlement,” said Afcons Director, Mr. Manivannan. “At this stage, we had to closely monitor TBM face pressure and advance the machine at a uniform rate to ensure proper primary grouting.” The bore’s geology mainly consisted of clayey sand and about 60 meters (197 ft) of mixed ground.
“We [Afcons] chose this machine for this project due to the underground geology in Chennai, which continuously changes from soil to mixed ground,” said Mr. Dey. “We also liked that Robbins EPB machines are designed with active articulation to allow the machine to turn or steer with ease.” During active articulation, thrust cylinders react evenly against the entire circumference of the tunnel lining, even in a curve—a design that eliminates the problem of tunnel lining deformation. “This feature enabled the machine to negotiate through well-controlled conditions,” added Mr. Manivannan.
With all three tunnels, Robbins Field Service members were on location to assist and support as required. During the course of each bore, Robbins was there to advise Afcons on how best to maneuver through challenging ground and provide instruction for machine operation. The ability of the contractor and manufacturer to work well together, as Robbins and Afcons have throughout their contracts, was critical to the good advance rates. The result was a robust machine that advanced at rates of 80 mm (3 in) per minute in challenging conditions.
This latest tunnel connects multiple stations along the metro line, starting from Washermenpet through to Sir Theagaraya and to Kurukpet. The Chennai Metro Project will provide much needed transportation to a rapidly developing city.
Tunnel Turkey 2017
Event Name: Tunnel Turkey 2017
Dates: December 2-3, 2017
Location: Istanbul, Turkey
Venue: Wyndham Grand Istanbul Levent Hotel
The Robbins Company will be exhibiting at the 2017 International Tunneling Symposium, also known as Tunnel Turkey, in Istanbul December 2-3. In keeping with this year’s theme, “Challenges in Tunneling,” stop by stand S-4 to learn more about how Robbins overcomes our own challenging projects.
During the conference, be sure to attend, “Use of dual mode, crossover TBM to excavate challenging geology at Mexico City’s Emisor Poniente II Waste Water Tunnel” presented by Robbins Public Relations Manager, Desiree Willis. The presentation will take place on Saturday, December 2 at 2:00 pm.
A 100th System for Robbins Continuous Conveyors
On October 18, 2017, a Robbins 9.26 m (30.4 ft) diameter Crossover machine started up at the Akron Ohio Canal Interceptor Tunnel (OCIT) in Ohio, USA—but the startup wasn’t the only milestone. Running behind the Crossover TBM is the 100th Robbins Continuous Conveyor system supplied for muck removal. The side-mounted conveyor is a design standard, but the landmark is a significant one: “With this system we have provided more conveyors than any other TBM conveyor supplier,” said Dean Workman, Robbins Director of Conveyors, Cutters, & SBUs. Counting conveyor systems the company has on order but has not yet delivered, that number is now well above 100, Workman added.
The Akron OCIT conveyor system consists of the belt plus a main drive, splice stand, storage unit, and advancing tailpiece, operating through several curves requiring patented self-adjusting curve idlers that correct themselves based on varying belt tension and belt load. The system discharges onto a customer-supplied overland conveyor, which delivers the muck to a large storage yard near the portal site. The belt was designed to handle variable geology, from soft soils to partial face rock and finally full-face shale rock.
The 100th conveyor system has been refurbished and customized for the job in a process that Robbins has been perfecting for decades: “We design our conveyor systems to last for five to ten years, but many last for decades longer. We have systems utilizing components that have been in operation for 30 years. We haven’t reached a limit for many of our systems—for example we had a specialized conveyor system built more than a decade ago for the Parramatta Rail Link in Sydney, Australia. Those components were refurbished for a job in Atlanta, Georgia, and now they are being used at the Dig Indy tunnels in Indianapolis, Indiana. These are long and challenging tunnel drives and the components are up to it.” While the Akron OCIT conveyor is just beginning to haul muck, it is sure to be a benefit throughout the project’s varying ground conditions.
The conveyor in Akron is also part of a long history for Robbins conveyors—the first of which (not counted in the list of 100) was the first ever continuous conveyor system used behind a TBM. That prototype, developed by founder James S. Robbins in 1963, was successfully used behind the 11.2 m (36.7 ft) diameter Main Beam TBM at the Mangla Dam project in what was then known as West Pakistan. While conveyors would not be adopted as a standard method of muck removal for many years afterward, the project laid the groundwork for future success.
Today’s conveyor systems are capable of spanning dozens of kilometers and hauling 1,800 metric tons (2,000 US tons) an hour or more. It’s a legacy that Workman sees will continue to grow: “This is my 20th year with Robbins and I remember when we started our conveyor list. It is amazing to look at all of the jobs and things we’ve done. It’s amazing to see what these systems can do.”
Boring the Blue Mountains: The Inside Story on the World’s Fastest TBM
Over 20 years ago, a Robbins open-type machine set three world records while tunneling in the picturesque Blue Mountains in Australia. You may be asking yourself, why is this significant? Why drudge up a project that is surely outdated at this point in our industry’s history? The fact of the matter is, two decades have passed and the Robbins open-type TBM chosen for this project is still considered to be the world’s fastest TBM.
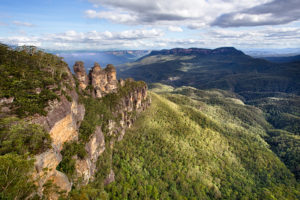
The picturesque Blue Mountains in New South Wales, Australia.
Project Background
In 1993, the 3.4 m (11 ft) diameter TBM was chosen to bore two sewage tunnels in the Blue Mountains near Sydney, Australia. At the time, there had been a rapid expansion of urban developments within the Blue Mountain National Park, causing an influx of pollution to enter streams as the result of septic tank runoff and outdated sewage treatment plants.
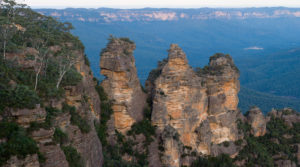
A closer look at the Three Sisters, a unique rock formation in the Blue Mountains.
The Blue Mountains Sewage Transfer Project comprised of approximately 40 km (25 mi) of tunnels, two of which were TBM-driven using the Robbins machine. The first, the Katoomba Carrier tunnel, was 13.4 km (8.3 mi) long and the second, the Lawson Carrier, was 3.5 km (2.1 mi) long. While the Lawson Carrier tunnel was finished five weeks prior to the expected completion date, it was during the Katoomba Carrier tunnel that all three records were set. During excavation the machine set the following world records: best day of 172.4 m (565.6 ft), best week of 702.8 m (2,305.7 ft), and a best monthly average of 1,189 m (39,000 ft) within its size range of 3 to 4 m (9.8 to 13.1 ft) diameter machine. Two of those records—the best day and best week—are the fastest ever recorded and have yet to be surpassed by any TBM of any size.
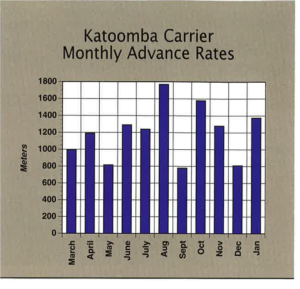
The 3.4 m (11 ft) diameter TBM set three world records while boring the Katoomba Carrier tunnel. Photo credit: tunneltalk.com
Custom Machine Design
There were many factors that played into this machine’s success—the system utilized on this project required a well-planned design, careful operation, and regular maintenance. As many people involved in tunneling know, choosing the right equipment for the geology can make or break a project. Detailed empirical data allowed the contractor to accurately predict what kind of ground they would encounter and prepare accordingly. The National Park is located within the Triassic Sydney Sedimentary Basin and is comprised primarily of sandstones and claystones. Anticipating this geology, the 3.4 m (11 ft) diameter machine’s cutterhead was dressed with 25 Robbins 17-inch diameter disc cutters designed for soft yet abrasive rock formations.
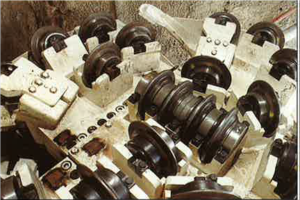
A close-up of the 17-inch cutters.
Logistics
The 13.4 km (8.3 mi) long Katoomba Carrier tunnel was originally planned to comprise of multiple short tunnels, several kilometers in length each, with intermittent portals to shorten drives. Ultimately it was decided to make the project one continuous tunnel, which led to higher advance rates and deemed it—at the time—the longest single-drive TBM tunnel. Not only did this change save time, but it also allowed boring to be less disruptive to the landscape.
Continuous Conveyor
In addition, the project was the first in Australia to utilize a continuous conveyor system. Due to the length of the tunnel, the use of traditional muck cars for muck removal would have taken too much time and were seen as an inadequate solution. The 106-m (347.8 ft) long system boosted production rates, with a best day of 1,565 m³ (55,267 ft³) of in-situ material removed from the Katoomba tunnel.
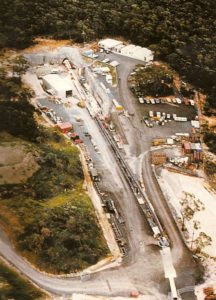
The Blue Mountains project was the first TBM-driven tunnel in Australia to utilize a continuous conveyor system.
Good Geology
Ground support throughout the tunnel comprised of a combination of resin grouted bolts, mesh, steel straps and steel sets. In the sturdier sandstone, however, the tunnel was left largely unlined and instead shotcrete was applied to areas of poorer, softer rock.
As boring progressed, the sandstone proved to be softer than expected. Instead of the predicted average of 80 MPa ranging from 20 MPa to 150 MPa, it averaged 40 MPa to 50 MPa with a range of 10 MPa to 100 MPa. This ideal material could also have contributed to the Robbins machine’s record breaking results and its early breakthrough, which occurred nine months ahead of schedule.
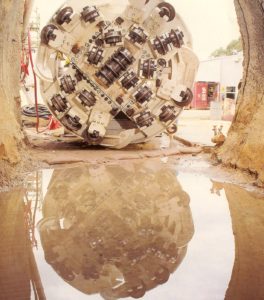
The machine’s record breaking boring enabled the project as a whole to finish 17 months ahead of schedule.
Exceeding Expectations
The Robbins Mk 12C’s performance on the tunnel boring portion of the project substantially surpassed all expectations. Not only did it set the previously mentioned world tunneling records, but it also helped the project as a whole finish 17 months ahead of schedule, saving not only on time but on significant financial costs.
Recent Posts
- Tunneling in Turkey: The Esme Salihli Railway
- Incredible India: Machines on the Move in Agra and Delhi
- Notice of Retraction and Apology
- Four Things You Need to Know about Probe Drilling and Pre-Grouting
- The Latest Updates: Records in Toronto, the News from Nepal, and More