Year: 2017
A Smart Disc Cutter Monitoring System Using Cutter Instrumentation Technology
In mechanized tunneling, continuous information from the excavation face is essential. The ultimate goals of cutter instrumentation are to monitor real-time individual cutter operation, acquire more realistic cutterhead thrust force values, and gain a better knowledge of the geology in front of the cutterhead. Analysis of this information can provide in-depth knowledge of machine excavation. Information about cutter operation has direct and indirect advantages: It helps better predict and monitor cutter usage rates, and it can reduce the cost of unplanned cutter or ring replacement, which can result in a better planning of inventory, manpower, and cutter rebuild requirements.
Current disc cutter instrumentation technology is designed to be a conveniently mounted instrumentation package that monitors individual cutter rpm, wear, temperature, and vibration. A data logger service receives the cutter information wirelessly using low-power radio technology and displays cutter conditions in real time. With cutter instrumentation, the operator continuously monitors cutter conditions, which results in higher efficiency, lower incidence of down time, and prevents unexpected ring wear-related damage from causing further damage to bearings and hubs. Cutter instrumentation technology has been tested on Robbins’ rock machines and results from previous and recent projects are presented. Design improvements for longer lifetime and increased reliability are discussed.
High Cover TBM Tunneling in the Andes Mountains—A Comparative Study of Two Challenging Tunnel Projects in Chile
The Andes Mountain range is among the youngest and most complex in the world, geologically speaking. Tunneling projects, particularly for hydroelectric and water transfer schemes, are not new to the range but their past history has met with mixed success. Two new projects utilizing very different tunnel boring machines and excavation strategies are now providing a testing ground for modern underground construction equipment in the Chilean Andes.
This paper will analyze two projects: the Alto Maipo and Los Condores Hydroelectric Projects, located approximately 100 km apart in the Andes Mountains. The two strategies being employed will be analyzed in detail, as one project is using an open-type Main Beam TBM plus extensive ground support, while the other is utilizing a Double Shield TBM and segmental lining. The authors will look at TBM performance and ground conditions encountered in the two tunnels and what effects the TBM selection and ground support strategy may have had on each tunneling operation.
Successful Excavation of Mexico City’s Emisor Poniente II Wastewater Tunnel—Use of a Dual-Mode, Crossover TBM in Challenging Geology
The history of Mexico City is inextricably linked to the issue of its geographic location. In the last 100 years, Mexico City has sunk by nearly 12 m. As a result, the city’s buildings, main streets, sewage systems, etc. have been extensively damaged.
In July 2015, the launch of a dual mode, Crossover type TBM marked the start of Mexico City’s next challenging wastewater project: the Túnel Emisor Poniente (TEP II). The 5.5 km long tunnel travels below a mountain at depths of 170 m as well as a section just 8 m below residential buildings, and the geology is equally varied. Ground consists of andesite and dacite with bands of tuff and fault zones, as well as a section of soft ground at the tunnel terminus.
This paper will detail the unique 8.7 m diameter Crossover TBM designed for the challenging conditions, and the successful excavation of the machine through fault zones, soft ground, and more. Strategies for excavation and advance rates, and downtimes will be analyzed. As the machine can be converted from hard rock mode to EPB mode in the tunnel, the authors will also look at the conversion process and how both modes worked to excavate in widely varying geological conditions.
Design and Implementation of a Large-Diameter, Dual-Mode “Crossover” TBM for the Akron Ohio Canal Interceptor Tunnel
The Ohio Canal Interceptor Tunnel (OCIT) Project involves construction of a conveyance and storage tunnel system to control combined sewer overflows for several regulators in the downtown Akron area. A Robbins dual mode type “Crossover” (XRE) Rock/ EPB TBM, Ø9.26m bore in diameter, will be used to excavate the tunnel and install the precast segmental lining.
The XRE TBM will feature characteristics of both Single Shield Hard Rock machines and EPBs for efficient excavation in mixed soils with rock, such as a flexible cutterhead design for proficient boring in both rock and soil conditions, adjustable main drive speed with an over-speed mode for operation in hard rock, and special screw conveyor wear protection measures. This paper describes these design features, their manufacturing process, and implementation in the field.
What’s New, What’s Next: TBM Equipment for the Mining Industry
TBMs have become well accepted in civil construction tunneling and excavate a high percentage of civil construction projects each year. But each year in the mining industry, far more kilometers of tunnels are excavated for mining purposes than for civil purposes. The amount of tunnels needed for mining operations is staggering.
Some examples from metal mines:
- A large, deep gold mine has over 800 km of tunnels. That is a single mine!
- One small underground metal mine excavates over 13 km of tunnel each year
- In the Sudbury, Ontario mining district, there are over 5000 km of mine tunnels
If tunnels for coal mining were included, the statistics would be even more dramatic. But all these tunnels hold a little-known secret.
The Lack of Mechanized Tunneling
How many of the above thousands of kilometers of mine tunnels do you think have been excavated by TBM? The answer is “Nada”. Compare that to the thousands of kilometers of civil construction tunnels built over the last decades, which required hundreds of TBMs. Why such a great disparity when the objective in both industries is to excavate underground openings as rapidly, economically, and as safely as possible? What are the differences in these industries?
In TBM civil construction, the TBM crew members that know how to make things happen underground, that know how to drive the machines, how to lift heavy components and repair the equipment, how to get the trains in and out to remove the muck and to bring in supplies, are known by a special name. They are known as the “miners”. Yet the only thing they are mining is the muck, no coal, no minerals. But “miners” is a term of reverence for someone who knows how to excavate a tunnel rapidly and efficiently. When a civil tunnel is progressing well, they say “now we’re mining”. (Well, sometimes they also say this sarcastically sometimes when things are going poorly underground.) Why aren’t such talented miners, who know how to make a TBM perform, using their TBMs to excavate thousands of kilometers of mine tunnels each year? What are the differences between civil tunneling and mine tunneling?
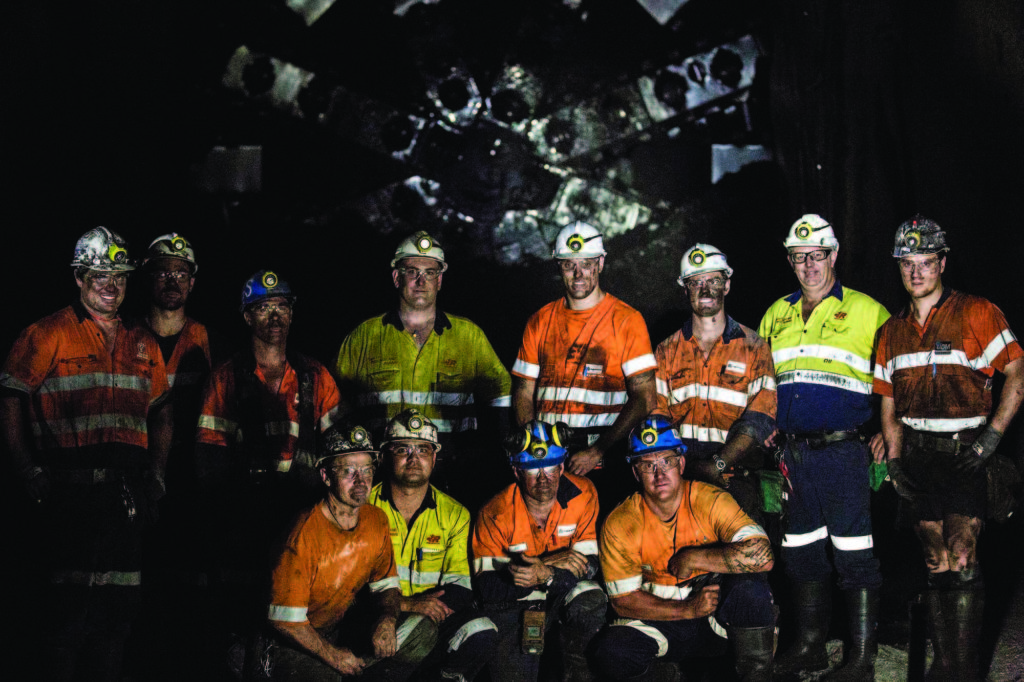
A group of talented miners at Australia’s Anglo American Coal Mine, where a Robbins Crossover TBM excavated two drifts for haulage and personnel access.
TBMs for Civil Tunnels
TBMs have become well accepted for civil tunneling. TBMs designs have become widely adapted for different ground conditions or specialized applications: Hard rock, soft ground, mixed face, pressurized face. Various types of ground support can be installed, according to current geological conditions. More current “hybrid” or “Crossover” TBM designs can handle widely different geological conditions, with the TBM adaptable to cope as conditions change.
Civil tunnels are generally long tunnels, where the efficiency of TBM excavation offsets the longer mobilization and demobilization times. And civil tunnels are generally designed with equipment mobilization/demobilization in mind. Suitable sized shafts are located to allow relatively simple introduction or retrieval of the TBM equipment. The most efficient type of TBM is the full face, rotary type TBM, which produces a circular tunnel profile. The circular profile is nearly universally accepted for civil construction. It is the optimum profile for fluid flow for fresh water, waste water, or hydro tunnels. It is also widely accepted for vehicular civil tunnels that need a flat roadbed. A flat roadway is constructed within the circular tunnel profile and the remainder of the profile within the circle is used for ventilation, services, escapeways, etc.
Some efforts have been made to develop non-circular profile TBMs for the civil sector. These machines include the Mini-Fullfacer, the Mobile Miner, and horseshoe shaped shields with excavator boom or roadheader. Such machines may produce a non-circular profile that is better for that specific job. But usually, there is a penalty in production rate compared to full face, circular TBMs.
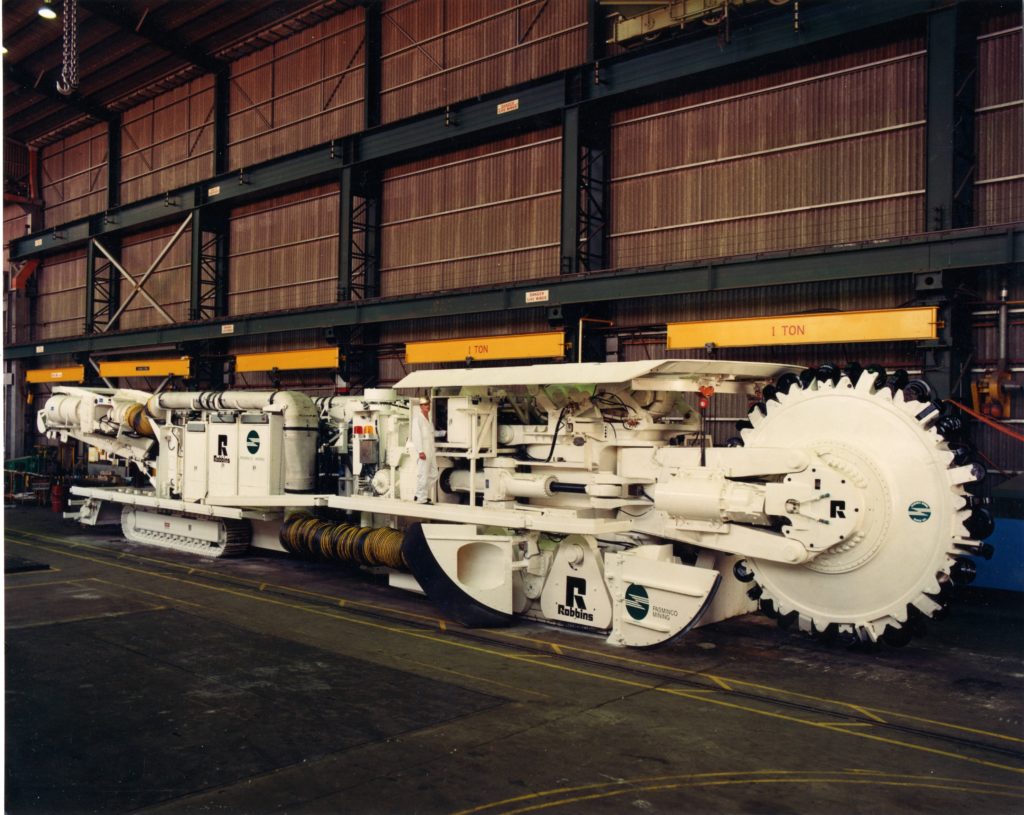
The mobile miner, a non-circular profile TBM developed by Robbins.
TBMs for Mine Tunnels
There have been some notable successes to the application of circular profile “civil type” TBMs for mining projects. Benefits have been lower costs, quicker access, and improved safety. Some examples include:
- Magma Copper, San Manuel Tunnels
- Stillwater Mines (four TBMs used)
- Grosvenor Coal Mine, Two Inclined Access Drifts to the coal seam
However, application of TBMs for mine tunnel construction has remained surprisingly limited. Why is this? Tunnels for mining are often not so long, or a developed in shorter phases, with the excavation front moved from place to place within the mine. TBMs and their constituent components are large and heavy. It is not easy to mobilize a TBM deep underground in a mine at a remote face. Better efforts must be made to make TBM transport and mobilization within the mine practical. This includes considerations for steep ramp roads and other restricted cross sections within the mine.
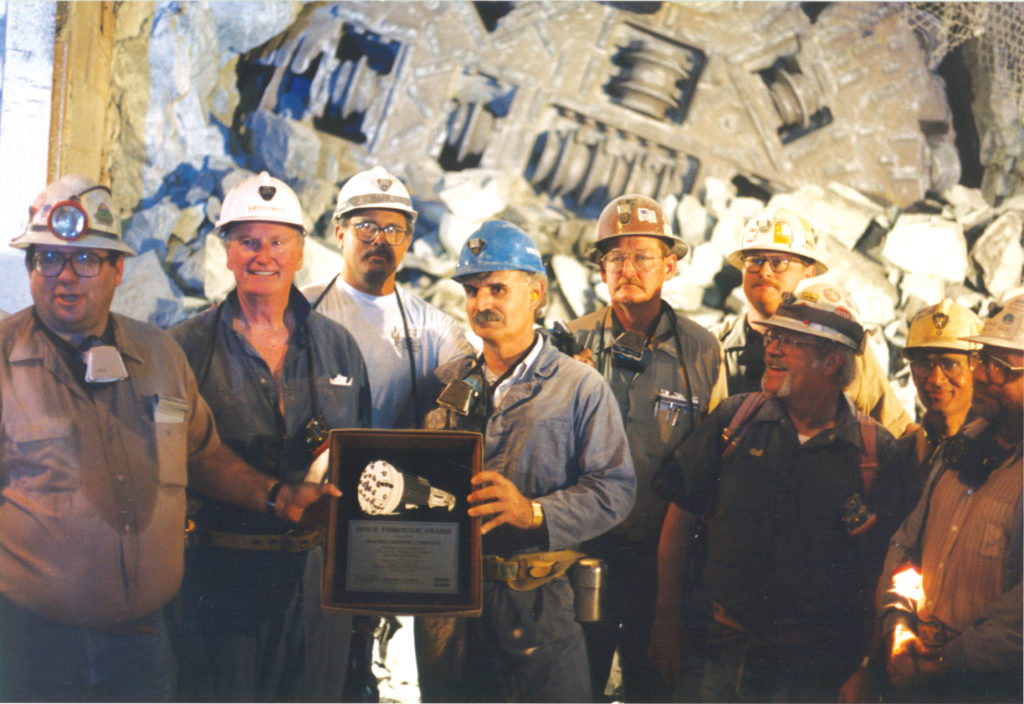
Breakthrough at the Magma Copper Mine in the 1990s.
Efficient TBMs are highly productive, but require a lot of power, ventilation, cooling, and support services. These need to be part of the mining plan so that the TBM has the necessary support and can provide the full benefit. Operating personnel with proper skills are also essential. If a TBM is introduced into a mining environment, either the mine personnel need proper TBM training or motivation, or the TBM drive must be isolated as a “stand alone” operation within the mine and be given proper priority of skilled personnel and the necessary services so the full benefit can be realized.
Mines often do not accept the circular profile produced by the most efficient, full face rotary TBMs. Mine tunnels are usually designed with a flat invert to allow for passage of rubber tired vehicles during the production phase of the mine tunnel. Many efforts have been made to provide TBM type equipment that produces a flat invert. Some have been relatively successful. But generally these machines do not provide the same productivity of efficient, full face circular profile TBMs. Rail bound mining vehicles can be used in the circular tunnel to take advantage of this TBM efficiency. Or, precast invert slabs, poured in place concrete, or partial invert filling can be used in a circular tunnel to provide a flat roadway. The cost/benefits must be analyzed and presented to the industry for a change to occur.
Mining plans often have tunnels with steep gradients and sharp radius curves. On steep gradients (up to 12-15 degrees), the most efficient haulage is usually by belt conveyor. However, the belt system is not effective if there are sharp radius curves. And typical TBM curve ability is limited. Special TBM designs can be made that allow for excavation in sharp curves, but there is a compromise in reduced TBM performance.
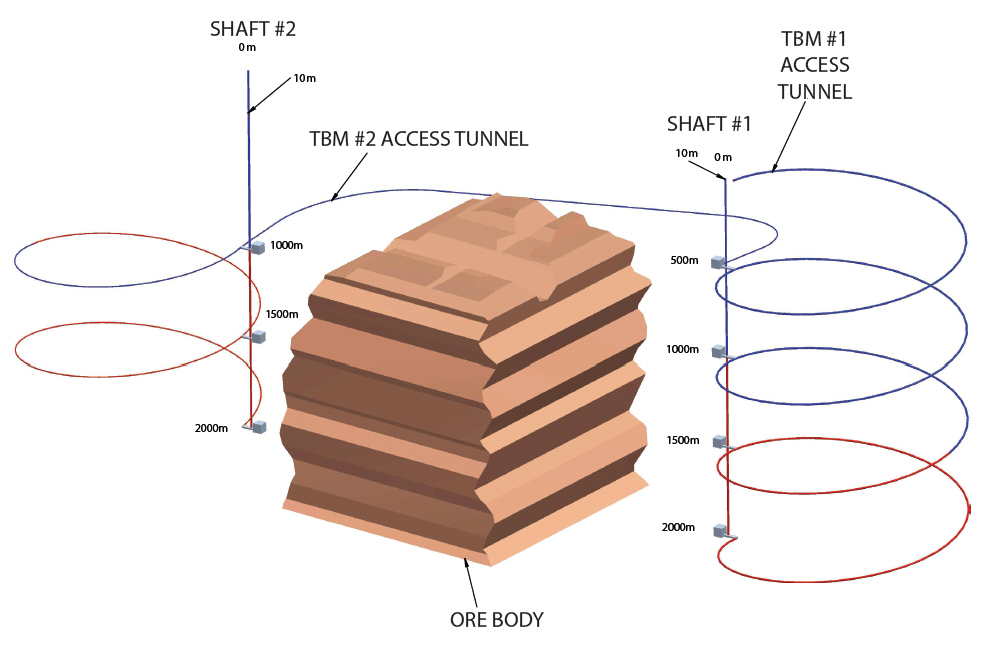
An example of a mine access and haulage plan to reach a deep ore body.
Mines need Versatile TBMs
It seems the mining industry needs the benefits that TBMs can provide. Open pit mines are becoming depleted, and mining activities are reaching deeper. Longer access tunnels are needed. Safety and speed of development are paramount. TBMs can offer these advantages, but have limitations. Special TBMs can be developed that meet special requirements, but usually there is a penalty in reduced TBM performance. The mine planners and the TBM equipment designers must work together at an early stage in the mine planning to determine the optimum compromise between most desirable mine plan, and most beneficial application of TBM equipment. A good partnering approach is necessary in the planning stage, as well as the operating stage, to allow for the most efficient application of TBM equipment to the needs of the mine.
By Dennis Ofiara, Chief Engineer
The Creation of the Crossover
The Real Field Experiences that Resulted in a Versatile Design
This blog is the first in a series called “Hidden Underfoot”, exploring the little-known history and behind-the-scenes happenings of the tunneling industry.
Many technological breakthroughs have been the direct result of the necessity to solve a problem; the creation of the first Crossover TBM was no exception. While much has been written about Central Turkey’s Kargi Kizilirmak Hydroelectric Project, we interviewed Field Service personnel who were there working in the conditions every day to get the untold story behind the genesis of the versatile Crossover TBM.
Behind the Scenes
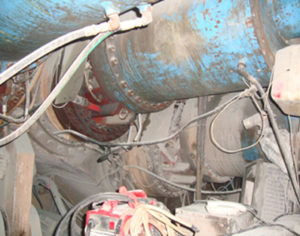
Custom-made gear reducers retrofitted to the motors in the tunnel.
The Kargi HEPP, now complete, generates 470 Gwh of power annually for project owner Statkraft, and supplies an estimated 150,000 homes.
Robbins supplied a 9.84 meter (32 ft) diameter Double Shield TBM and continuous conveyor system to Turkish contractor Gülermak for the project. The machine was to bore an 11.8 km (7.3 mi) headrace tunnel to divert water from the dam to powerhouse. Initial geological reports predicted softer ground for the first 2.5 km (1.6 mi), which would be lined with pre-cast concrete segments. The remainder of the tunnel was to be supported by a combination of shotcrete, rock bolts, and wire mesh in more competent rock.
The project became arduous soon after startup, when the machine encountered blocky rock, sand, and clays that were not initially predicted. “We realized modifications needed to be made as soon as we started experiencing flowing materials and squeezing ground,” said Glen Maynard, Robbins Site Manager, who worked on the project throughout the challenging conditions. Maynard’s prognosis was apt, as 80 meters (262 ft) into the bore the TBM became trapped in a section of collapsed ground. “The machine faced serious blockages,” added Maynard, “there was no one fix, each problem needed its own solution. Thrust, cutterhead, and ground support all needed adjustment.” The machine was freed but continued to struggle, requiring not just one but seven bypass tunnels to free it each time it encountered collapsing ground.
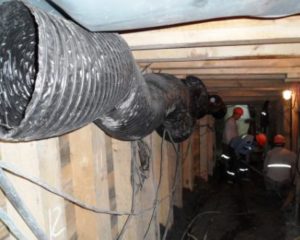
Construction of one of several bypass tunnels at Kargi.
Concerns that the machine would need to be buried were quickly mollified. Robbins President Lok Home told the Kargi team to build a “wish list” of all the materials they would need to modify the machine and get it moving again. Robbins and Gülermak worked together to determine what changes would need to be made, and parts were shipped to the jobsite as quickly as possible. This of course, was not the first time a machine had required modifications while in the tunnel, and Robbins engineers were able to pull from past projects in order to know what needed to be done.
In-Tunnel Effort
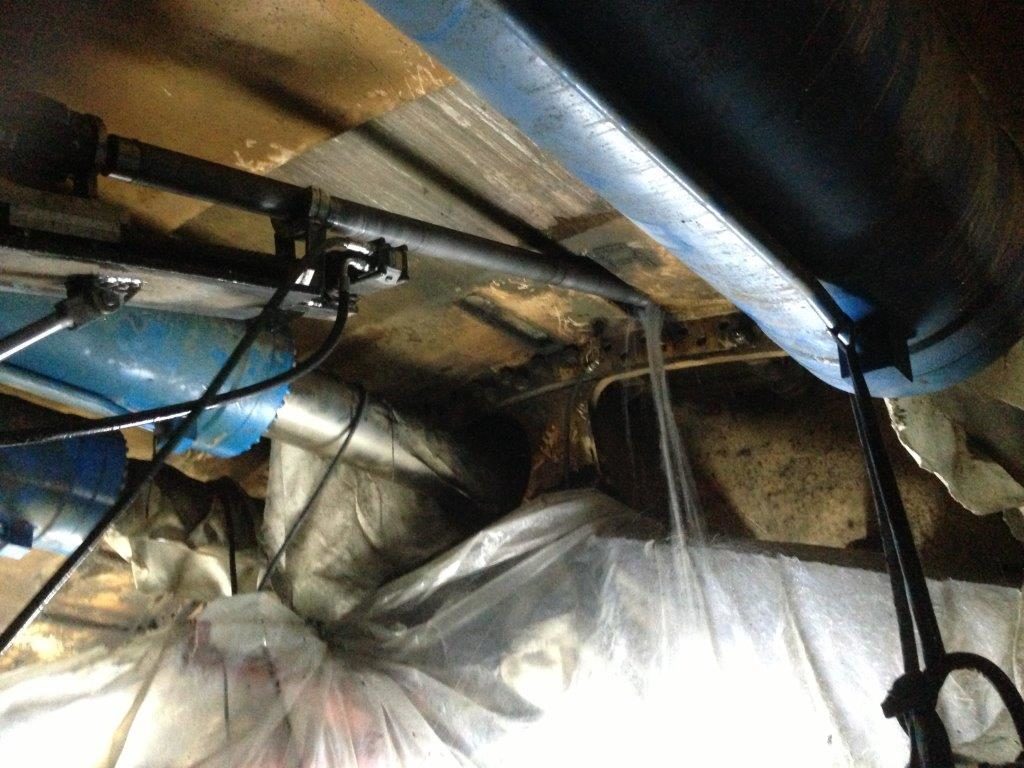
Canopy drill installed in the tunnel.
The contractor, with the assistance of the field service team, installed a Robbins custom-built canopy drill and positioner to allow pipe tube support installation through the forward shield. This allowed drilling with a distance of up to 10 m (33 ft) ahead of the cutterhead while 90 mm (3.5 in) diameter pipe tubes provided extra support across the top 120 to 140 degrees at the tunnel crown. Injection of resins and grout protected against collapse at the crown while excavating through soft ground. “There were a lot of risks to the modified machine, but we gave comprehensive instructions on how to operate it to the contractor,” said Maynard. “The contractor team was open to change and had great cooperation. They were a really hard working team.”
To further mitigate the effects of squeezing ground or collapses, custom-made gear reducers were ordered and retrofitted to the cutterhead motors. They were installed between the drive motor and the primary two-stage planetary gearboxes. When the machine encountered loose or squeezing ground the reducers were engaged, which resulted in a reduction in cutterhead RPM and a doubling of the available torque. The net effect of the modifications allowed the Double Shield TBM to operate much like an Earth Pressure Balance Machine in fault zones and squeezing ground with high torque and low RPM—these methods effectively kept the machine from getting stuck. In addition, short stroke thrust jacks were installed between the normal auxiliary thrust to double total thrust capabilities.
The results of the modifications led to astonishing results. An advance rate of 600 m (1,986 ft) in one month was achieved in March 2013 and a project best of approximately 723 m (2,372 ft) was achieved in spring 2014, including a daily best of 39.6 m (130 ft) in April 2014. The TBM bored 7.8 km (4.8 mi) of the tunnel in total, making its final breakthrough in July 2014. The remainder was excavated by drill and blast—of which it is notable that the modified TBM achieved advance rates more than twice that of the traditional mining operation. “It was enjoyable to find a way to overcome this challenge,” added Maynard.
Mixed Ground Legacy
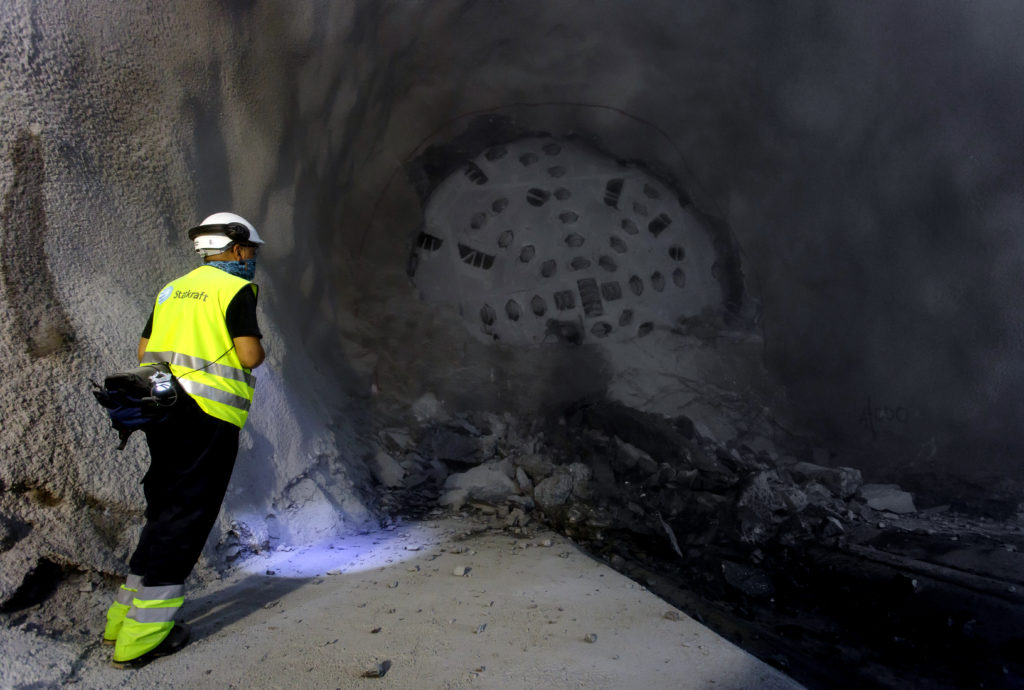
Successful breakthrough in July 2014.
A project that had started out as a disheartening one transformed into one that encouraged others. The insights gained by implementing changes to the Kargi machine were quickly applied to other projects facing mixed ground conditions that would otherwise require multiple tunneling machines. From these creative solutions came the design of a new line of Robbins dual-mode machines—TBMs that contain features of two machine types—termed Crossovers. Everything from multi-speed gearboxes to canopy drills, and emergency thrust are regular features of Crossover machines, and they owe their genesis to the hard work involved at Kargi HEPP.
Robbins: Focused Forward
Robbins has been the foremost manufacturer of Tunnel Boring Machines and underground construction equipment for nearly 70 years. Journey through the company history as told by Robbins employees, and hear about the latest innovations and design concepts that make Robbins a thought-leader in the industry.
Robbins TBM “Rosie” is First Crossover TBM in the U.S.
A Robbins Crossover (XRE) TBM measuring 9.26 m (30.4 ft) in diameter underwent factory acceptance on May 30, 2017. The gargantuan machine was initially unveiled at Robbins’ Solon, Ohio headquarters during a press day on May 25 before being shipped 40 km (25 mi) south for construction of the Ohio Canal Interceptor Tunnel (OCIT) in Akron. Those present included Akron Mayor Daniel Horrigan, Robbins chief engineer Dennis Ofiara, and David Chastka, project engineer for contractor Kenny-Obayashi JV.
The TBM, which includes features of both EPB and Hard Rock Single Shield TBM types, is the first Crossover machine to be used in the United States. It will be launched from a 12 m (40 ft) deep portal site and build the first 68 m (226 ft) in soft ground, transitioning to a 183 m (600 ft) long zone of partial face shale before switching to hard-rock mode for the remainder of the drive in full face shale. Probe drilling will be done continuously using two probe drills to determine which mode the TBM should be in. “Robbins has provided a robust design that we are confident will be able to handle all of the challenges of the OCIT Project tunnel drive,” said Chastka.
Unique aspects of the machine include a versatile cutterhead that will be configured with consideration for both the short soft ground section and the longer section (about 65% of the tunnel) in hard rock. A combination of disc cutters and sacrificial rippers will be used in case a cutter becomes blocked. The required rolling torque of the disc cutters has been reduced by 25% to encourage smooth rotation in soft ground. The motors of the XRE machine have been reworked from an original EPB configuration to permit higher motor speed at reduced torque for the open mode segments of the drive.
Muck removal will be achieved with a durable screw conveyor, the first flight of which is covered welded-in wear plates. The auger shaft is lined with hard facing in a crosshatch pattern, while the screw conveyor casing has been similarly lined in wear plates and hard facing. A wear monitoring plan has been prepared for the entire drive in order to maximize efficiency in the section of more abrasive rock. Robbins Project Manager Pablo Salazar is proud of the utilization of local jobs during the TBM construction and design process: “We have built good portion of the machine in the northeast Ohio area. Many components were fabricated locally with sub-suppliers, as well as in our own shop.”
The machine was dubbed “Rosie” in honor of Rosie the Riveter, an icon representing the American women who worked in factories and shipyards during World War II. Hundreds of “Rosies” including Akron resident Rose May Jacob worked in factories to turn out materials and armaments for the Allied war effort. The TBM will be shipped in truckloads to the jobsite, with the large cutterhead shipped in four pieces. “The entire process of assembly has allowed to the contractor to follow very closely through the testing of the machine, so they are very familiar with the TBM at this point. At the jobsite, we will also provide immediate support for both spare parts and personnel,” said Salazar. Jobsite supervisors from Robbins will assist in TBM assembly and excavation for at least the first 1,000 m (3,280 ft) of boring. Tunnel boring is scheduled to begin in August of this year.
The OCIT Project for the City of Akron consists of the construction of a conveyance and storage tunnel system to control Combined Sewer Overflows (CSOs) for several regulators in the downtown Akron area. The EPA-mandated project includes the 1.89 km (1.17 mi) conveyance and storage tunnel, as well as drop shafts, diversion structures, consolidation sewers, and related structures. The consent decree specifies that the tunnel must be operational by December 31, 2018.
Crossover XSE Spec Sheet
If the geology of your project includes high permeability soils combined with sections of low permeability ground, the Crossover XSE is the solution for you. Not all projects fit within the parameters of specific TBM types, and at Robbins we believe that your machine should be custom-engineered for your unique project requirements. That’s where the Crossover Series of TBMs comes in.
Crossover XRE Spec Sheet
Whether the geology of your project includes sections of hard rock, soft ground, boulders, or a little bit of everything, Robbins has a solution for you. Not all projects fit within the parameters of specific TBM types, and at Robbins we believe that your machine should be custom-engineered for your unique project requirements. The XRE TBM offers the best features of both EPB and Hard Rock Single Shield TBMs.
Recent Posts
- MDM5000 Brochure
- Difficult Ground Brochure
- SBU-RC Spec Sheet
- Continuous Conveyor Spec Sheet
- Crossover XSE Spec Sheet