Blog
The Creation of the Crossover
The Real Field Experiences that Resulted in a Versatile Design
This blog is the first in a series called “Hidden Underfoot”, exploring the little-known history and behind-the-scenes happenings of the tunneling industry.
Many technological breakthroughs have been the direct result of the necessity to solve a problem; the creation of the first Crossover TBM was no exception. While much has been written about Central Turkey’s Kargi Kizilirmak Hydroelectric Project, we interviewed Field Service personnel who were there working in the conditions every day to get the untold story behind the genesis of the versatile Crossover TBM.
Behind the Scenes
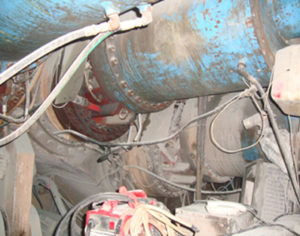
Custom-made gear reducers retrofitted to the motors in the tunnel.
The Kargi HEPP, now complete, generates 470 Gwh of power annually for project owner Statkraft, and supplies an estimated 150,000 homes.
Robbins supplied a 9.84 meter (32 ft) diameter Double Shield TBM and continuous conveyor system to Turkish contractor Gülermak for the project. The machine was to bore an 11.8 km (7.3 mi) headrace tunnel to divert water from the dam to powerhouse. Initial geological reports predicted softer ground for the first 2.5 km (1.6 mi), which would be lined with pre-cast concrete segments. The remainder of the tunnel was to be supported by a combination of shotcrete, rock bolts, and wire mesh in more competent rock.
The project became arduous soon after startup, when the machine encountered blocky rock, sand, and clays that were not initially predicted. “We realized modifications needed to be made as soon as we started experiencing flowing materials and squeezing ground,” said Glen Maynard, Robbins Site Manager, who worked on the project throughout the challenging conditions. Maynard’s prognosis was apt, as 80 meters (262 ft) into the bore the TBM became trapped in a section of collapsed ground. “The machine faced serious blockages,” added Maynard, “there was no one fix, each problem needed its own solution. Thrust, cutterhead, and ground support all needed adjustment.” The machine was freed but continued to struggle, requiring not just one but seven bypass tunnels to free it each time it encountered collapsing ground.
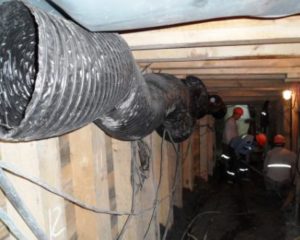
Construction of one of several bypass tunnels at Kargi.
Concerns that the machine would need to be buried were quickly mollified. Robbins President Lok Home told the Kargi team to build a “wish list” of all the materials they would need to modify the machine and get it moving again. Robbins and Gülermak worked together to determine what changes would need to be made, and parts were shipped to the jobsite as quickly as possible. This of course, was not the first time a machine had required modifications while in the tunnel, and Robbins engineers were able to pull from past projects in order to know what needed to be done.
In-Tunnel Effort
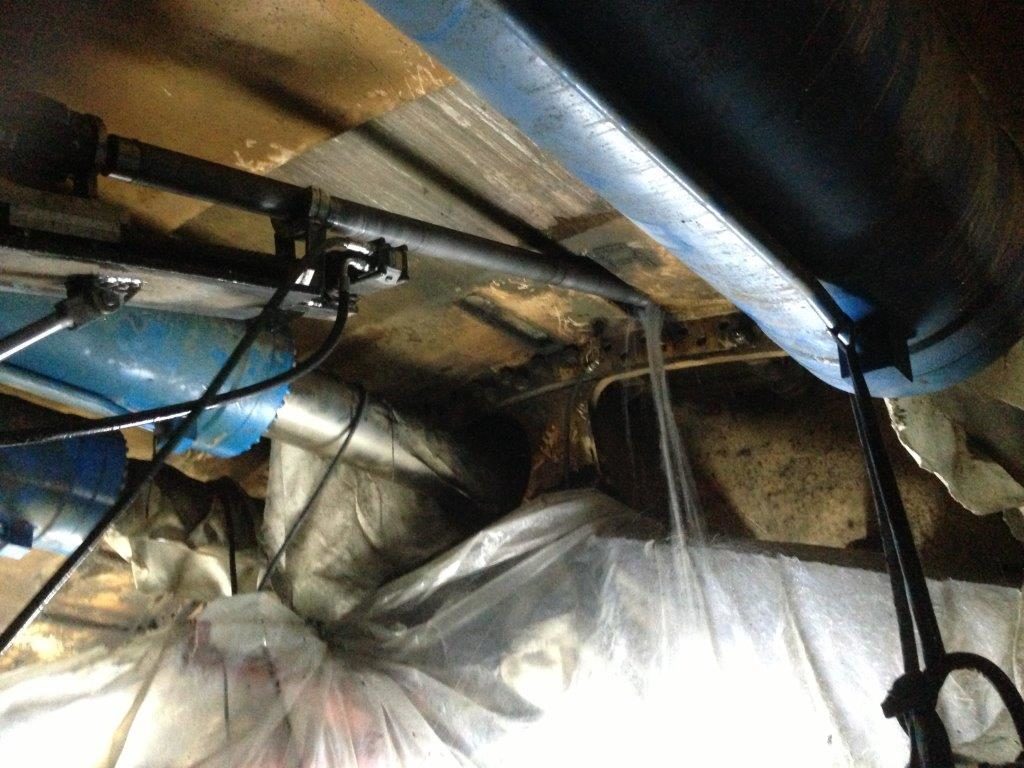
Canopy drill installed in the tunnel.
The contractor, with the assistance of the field service team, installed a Robbins custom-built canopy drill and positioner to allow pipe tube support installation through the forward shield. This allowed drilling with a distance of up to 10 m (33 ft) ahead of the cutterhead while 90 mm (3.5 in) diameter pipe tubes provided extra support across the top 120 to 140 degrees at the tunnel crown. Injection of resins and grout protected against collapse at the crown while excavating through soft ground. “There were a lot of risks to the modified machine, but we gave comprehensive instructions on how to operate it to the contractor,” said Maynard. “The contractor team was open to change and had great cooperation. They were a really hard working team.”
To further mitigate the effects of squeezing ground or collapses, custom-made gear reducers were ordered and retrofitted to the cutterhead motors. They were installed between the drive motor and the primary two-stage planetary gearboxes. When the machine encountered loose or squeezing ground the reducers were engaged, which resulted in a reduction in cutterhead RPM and a doubling of the available torque. The net effect of the modifications allowed the Double Shield TBM to operate much like an Earth Pressure Balance Machine in fault zones and squeezing ground with high torque and low RPM—these methods effectively kept the machine from getting stuck. In addition, short stroke thrust jacks were installed between the normal auxiliary thrust to double total thrust capabilities.
The results of the modifications led to astonishing results. An advance rate of 600 m (1,986 ft) in one month was achieved in March 2013 and a project best of approximately 723 m (2,372 ft) was achieved in spring 2014, including a daily best of 39.6 m (130 ft) in April 2014. The TBM bored 7.8 km (4.8 mi) of the tunnel in total, making its final breakthrough in July 2014. The remainder was excavated by drill and blast—of which it is notable that the modified TBM achieved advance rates more than twice that of the traditional mining operation. “It was enjoyable to find a way to overcome this challenge,” added Maynard.
Mixed Ground Legacy
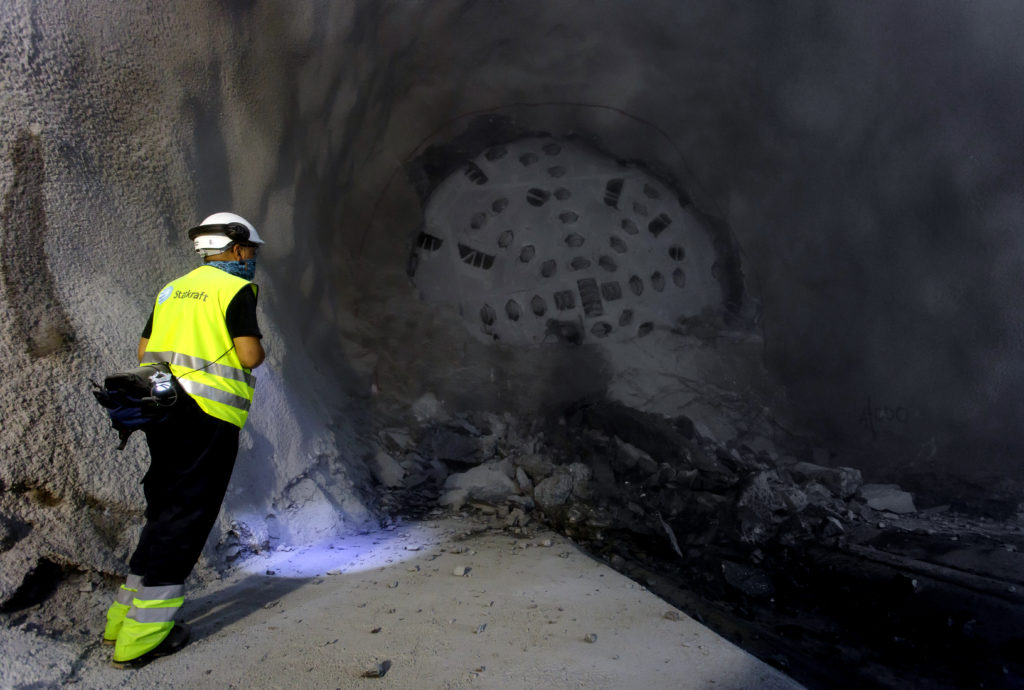
Successful breakthrough in July 2014.
A project that had started out as a disheartening one transformed into one that encouraged others. The insights gained by implementing changes to the Kargi machine were quickly applied to other projects facing mixed ground conditions that would otherwise require multiple tunneling machines. From these creative solutions came the design of a new line of Robbins dual-mode machines—TBMs that contain features of two machine types—termed Crossovers. Everything from multi-speed gearboxes to canopy drills, and emergency thrust are regular features of Crossover machines, and they owe their genesis to the hard work involved at Kargi HEPP.
Sarah Crawford
Recent Posts
- Tunneling in Turkey: The Esme Salihli Railway
- Incredible India: Machines on the Move in Agra and Delhi
- Notice of Retraction and Apology
- Four Things You Need to Know about Probe Drilling and Pre-Grouting
- The Latest Updates: Records in Toronto, the News from Nepal, and More