Author: Sarah Crawford
Difficult Ground Solutions (DGS): New TBM Solutions carve a Path to Success
In many TBM-driven tunnels, the occurrence of squeezing ground, high inrushes of water, blocky rock, and other challenges is a real possibility. Difficult Ground Solutions (DGS) reduces risk to contractors and owners in these conditions while providing accurate ground investigation. The story of how these methods came into practice involves hardship that tested the mettle of a shielded hard rock TBM on a recent project. What came out of those challenges is a new way to deal with both predicted and unforeseen ground conditions in rock and mixed ground. DGS features such as dual-range cutterhead drives, high pressure grout injection systems for face stabilization, and water inrush control are customizable and should be considered to be built into shielded TBMs. This paper will cover solutions informed by field experiences, the tools it takes to be successful in difficult ground, and how they are applied.
The Return of TBMs to Norway at Røssåga HEPP—TBM Operation Through Extremely Hard Rock, Unstable Rock Mass, and Other Challenges
The TBM that broke though at Røssåga HEPP in December 2015 was the first to breakthrough in Norway in more than 20 years. During the excavation the TBM encountered extremely hard rock (over 280 MPa), which posed an extreme challenge for both the TBM and the cutters. During the excavation a highly efficient main bearing replacement was also performed in the tunnel. This paper discusses the project as a whole, including TBM design, Onsite First Time Assembly (OFTA) of the machine, challenges faced, and project outcomes.
Large-Diameter 20-Inch Disc Cutters: A Comparison of Tool Life and Performance on Hard Rock TBMs
Optimization of disc cutter life and penetration rate in hard rock can be one of the biggest predictors of project success. With hard rock TBMs being used today in ever more difficult conditions and longer tunnels, the question of which type of disc cutter to be used becomes critical. At one such project in Northeastern China, varying disc cutter tool steels and sizes were put to the test on a total of nine different 8.5m diameter hard rock, Main Beam TBMs from various manufacturers. The TBMs excavated sections of a vast water tunnel in similar granitic geology.
This paper will look at the development of 20-inch disc cutters and the case for large diameter cutters, using the most recent example in China as a focus area of study. Varying advance rates, cutter life, tool steels, and challenges excavating the rock will be discussed. The paper will conclude with recommendations for optimal cutter life in TBMs destined to bore long tunnels in hard rock.
Use of “Command Chair” Simulator Technology to Optimize Modern TBM Performance
TBM operator cabs and controls are often a long way down the list of priorities when it comes to the overall design of a Tunnel Boring Machine. However, their proper design and inclusion of the latest technology can mean the difference between a successful project and an unsuccessful one.
On soft ground machines the industry often puts operators in control of machines with little or no practical experience of that particular machine or the control systems. This practice can, in some cases, lead to major incidents such as ground heave or sinkholes in densely populated urban zones causing major disruption, downtime and untold damages and cost.
This paper will discuss the advances and developments in TBM operator controls and the use of “command chair” technology as both a training tool in the form of a boring machine simulator and as a way of controlling modern-day TBMs.
Rondout West Branch Bypass Tunnel—TBM Boring in Hard Rock Against High Water Pressure and High Water Inflows Beneath the Hudson River in New York
This paper focuses on a single shield hard rock tunnel boring machine that is set to bore in hard rock, high water inflows and high water pressure in New York State. To overcome the difficult conditions the TBM is designed to handle 2500 gpm water inflows and seal against 30 bar of pressure. The TBM will bore a tunnel to replace a damaged portion of the Delaware Aqueduct that supplies half the raw water to New York City. The 2.5 mile bypass tunnel passes beneath the Hudson River with geology consisting of shale and limestone.
Due to the high water pressure and inflows, the TBM was designed with new sealing systems for the main bearing and to close the TBM off if high water inflows are encountered. The TBM is to be equipped with two dewatering systems and multiple drilling and grouting systems for pre excavation grouting and segmental lining backfill. Systematic drilling and grouting procedures specific to the project were developed and incorporated into the TBM and backup design to ensure that the TBM can handle the extremely difficult ground conditions of the project.
A Smart Disc Cutter Monitoring System Using Cutter Instrumentation Technology
In mechanized tunneling, continuous information from the excavation face is essential. The ultimate goals of cutter instrumentation are to monitor real-time individual cutter operation, acquire more realistic cutterhead thrust force values, and gain a better knowledge of the geology in front of the cutterhead. Analysis of this information can provide in-depth knowledge of machine excavation. Information about cutter operation has direct and indirect advantages: It helps better predict and monitor cutter usage rates, and it can reduce the cost of unplanned cutter or ring replacement, which can result in a better planning of inventory, manpower, and cutter rebuild requirements.
Current disc cutter instrumentation technology is designed to be a conveniently mounted instrumentation package that monitors individual cutter rpm, wear, temperature, and vibration. A data logger service receives the cutter information wirelessly using low-power radio technology and displays cutter conditions in real time. With cutter instrumentation, the operator continuously monitors cutter conditions, which results in higher efficiency, lower incidence of down time, and prevents unexpected ring wear-related damage from causing further damage to bearings and hubs. Cutter instrumentation technology has been tested on Robbins’ rock machines and results from previous and recent projects are presented. Design improvements for longer lifetime and increased reliability are discussed.
High Cover TBM Tunneling in the Andes Mountains—A Comparative Study of Two Challenging Tunnel Projects in Chile
The Andes Mountain range is among the youngest and most complex in the world, geologically speaking. Tunneling projects, particularly for hydroelectric and water transfer schemes, are not new to the range but their past history has met with mixed success. Two new projects utilizing very different tunnel boring machines and excavation strategies are now providing a testing ground for modern underground construction equipment in the Chilean Andes.
This paper will analyze two projects: the Alto Maipo and Los Condores Hydroelectric Projects, located approximately 100 km apart in the Andes Mountains. The two strategies being employed will be analyzed in detail, as one project is using an open-type Main Beam TBM plus extensive ground support, while the other is utilizing a Double Shield TBM and segmental lining. The authors will look at TBM performance and ground conditions encountered in the two tunnels and what effects the TBM selection and ground support strategy may have had on each tunneling operation.
Successful Excavation of Mexico City’s Emisor Poniente II Wastewater Tunnel—Use of a Dual-Mode, Crossover TBM in Challenging Geology
The history of Mexico City is inextricably linked to the issue of its geographic location. In the last 100 years, Mexico City has sunk by nearly 12 m. As a result, the city’s buildings, main streets, sewage systems, etc. have been extensively damaged.
In July 2015, the launch of a dual mode, Crossover type TBM marked the start of Mexico City’s next challenging wastewater project: the Túnel Emisor Poniente (TEP II). The 5.5 km long tunnel travels below a mountain at depths of 170 m as well as a section just 8 m below residential buildings, and the geology is equally varied. Ground consists of andesite and dacite with bands of tuff and fault zones, as well as a section of soft ground at the tunnel terminus.
This paper will detail the unique 8.7 m diameter Crossover TBM designed for the challenging conditions, and the successful excavation of the machine through fault zones, soft ground, and more. Strategies for excavation and advance rates, and downtimes will be analyzed. As the machine can be converted from hard rock mode to EPB mode in the tunnel, the authors will also look at the conversion process and how both modes worked to excavate in widely varying geological conditions.
Design and Implementation of a Large-Diameter, Dual-Mode “Crossover” TBM for the Akron Ohio Canal Interceptor Tunnel
The Ohio Canal Interceptor Tunnel (OCIT) Project involves construction of a conveyance and storage tunnel system to control combined sewer overflows for several regulators in the downtown Akron area. A Robbins dual mode type “Crossover” (XRE) Rock/ EPB TBM, Ø9.26m bore in diameter, will be used to excavate the tunnel and install the precast segmental lining.
The XRE TBM will feature characteristics of both Single Shield Hard Rock machines and EPBs for efficient excavation in mixed soils with rock, such as a flexible cutterhead design for proficient boring in both rock and soil conditions, adjustable main drive speed with an over-speed mode for operation in hard rock, and special screw conveyor wear protection measures. This paper describes these design features, their manufacturing process, and implementation in the field.
The Creation of the Crossover
The Real Field Experiences that Resulted in a Versatile Design
This blog is the first in a series called “Hidden Underfoot”, exploring the little-known history and behind-the-scenes happenings of the tunneling industry.
Many technological breakthroughs have been the direct result of the necessity to solve a problem; the creation of the first Crossover TBM was no exception. While much has been written about Central Turkey’s Kargi Kizilirmak Hydroelectric Project, we interviewed Field Service personnel who were there working in the conditions every day to get the untold story behind the genesis of the versatile Crossover TBM.
Behind the Scenes
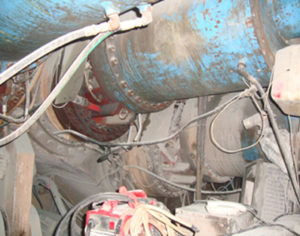
Custom-made gear reducers retrofitted to the motors in the tunnel.
The Kargi HEPP, now complete, generates 470 Gwh of power annually for project owner Statkraft, and supplies an estimated 150,000 homes.
Robbins supplied a 9.84 meter (32 ft) diameter Double Shield TBM and continuous conveyor system to Turkish contractor Gülermak for the project. The machine was to bore an 11.8 km (7.3 mi) headrace tunnel to divert water from the dam to powerhouse. Initial geological reports predicted softer ground for the first 2.5 km (1.6 mi), which would be lined with pre-cast concrete segments. The remainder of the tunnel was to be supported by a combination of shotcrete, rock bolts, and wire mesh in more competent rock.
The project became arduous soon after startup, when the machine encountered blocky rock, sand, and clays that were not initially predicted. “We realized modifications needed to be made as soon as we started experiencing flowing materials and squeezing ground,” said Glen Maynard, Robbins Site Manager, who worked on the project throughout the challenging conditions. Maynard’s prognosis was apt, as 80 meters (262 ft) into the bore the TBM became trapped in a section of collapsed ground. “The machine faced serious blockages,” added Maynard, “there was no one fix, each problem needed its own solution. Thrust, cutterhead, and ground support all needed adjustment.” The machine was freed but continued to struggle, requiring not just one but seven bypass tunnels to free it each time it encountered collapsing ground.
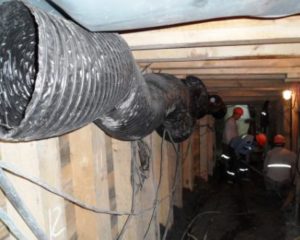
Construction of one of several bypass tunnels at Kargi.
Concerns that the machine would need to be buried were quickly mollified. Robbins President Lok Home told the Kargi team to build a “wish list” of all the materials they would need to modify the machine and get it moving again. Robbins and Gülermak worked together to determine what changes would need to be made, and parts were shipped to the jobsite as quickly as possible. This of course, was not the first time a machine had required modifications while in the tunnel, and Robbins engineers were able to pull from past projects in order to know what needed to be done.
In-Tunnel Effort
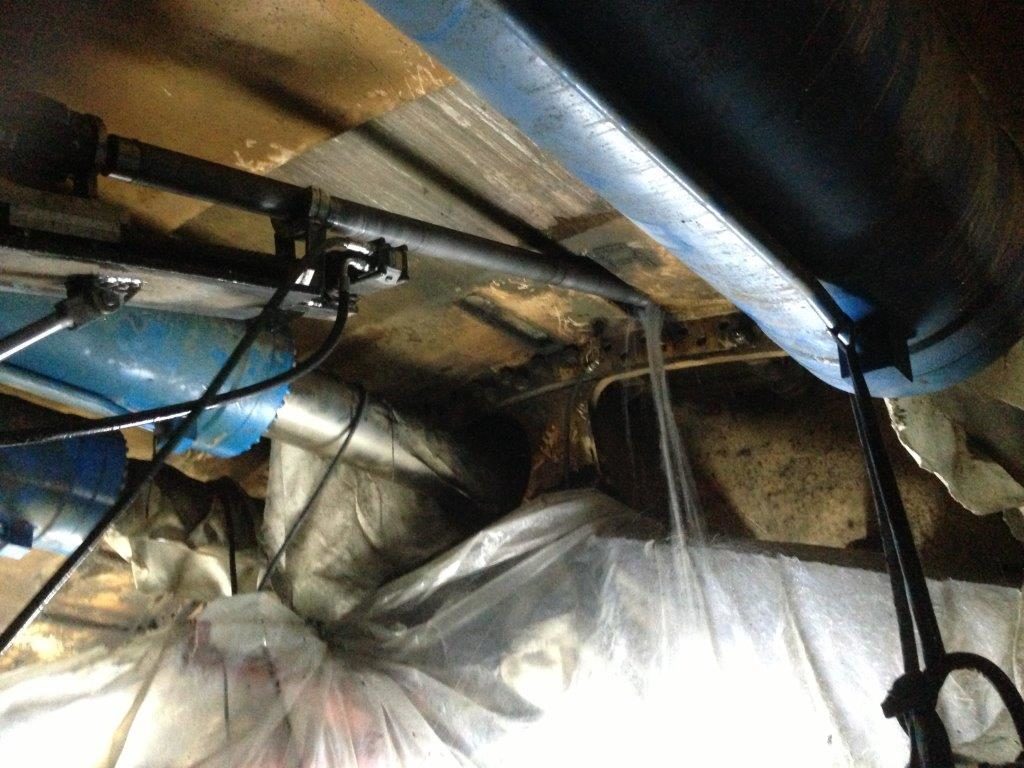
Canopy drill installed in the tunnel.
The contractor, with the assistance of the field service team, installed a Robbins custom-built canopy drill and positioner to allow pipe tube support installation through the forward shield. This allowed drilling with a distance of up to 10 m (33 ft) ahead of the cutterhead while 90 mm (3.5 in) diameter pipe tubes provided extra support across the top 120 to 140 degrees at the tunnel crown. Injection of resins and grout protected against collapse at the crown while excavating through soft ground. “There were a lot of risks to the modified machine, but we gave comprehensive instructions on how to operate it to the contractor,” said Maynard. “The contractor team was open to change and had great cooperation. They were a really hard working team.”
To further mitigate the effects of squeezing ground or collapses, custom-made gear reducers were ordered and retrofitted to the cutterhead motors. They were installed between the drive motor and the primary two-stage planetary gearboxes. When the machine encountered loose or squeezing ground the reducers were engaged, which resulted in a reduction in cutterhead RPM and a doubling of the available torque. The net effect of the modifications allowed the Double Shield TBM to operate much like an Earth Pressure Balance Machine in fault zones and squeezing ground with high torque and low RPM—these methods effectively kept the machine from getting stuck. In addition, short stroke thrust jacks were installed between the normal auxiliary thrust to double total thrust capabilities.
The results of the modifications led to astonishing results. An advance rate of 600 m (1,986 ft) in one month was achieved in March 2013 and a project best of approximately 723 m (2,372 ft) was achieved in spring 2014, including a daily best of 39.6 m (130 ft) in April 2014. The TBM bored 7.8 km (4.8 mi) of the tunnel in total, making its final breakthrough in July 2014. The remainder was excavated by drill and blast—of which it is notable that the modified TBM achieved advance rates more than twice that of the traditional mining operation. “It was enjoyable to find a way to overcome this challenge,” added Maynard.
Mixed Ground Legacy
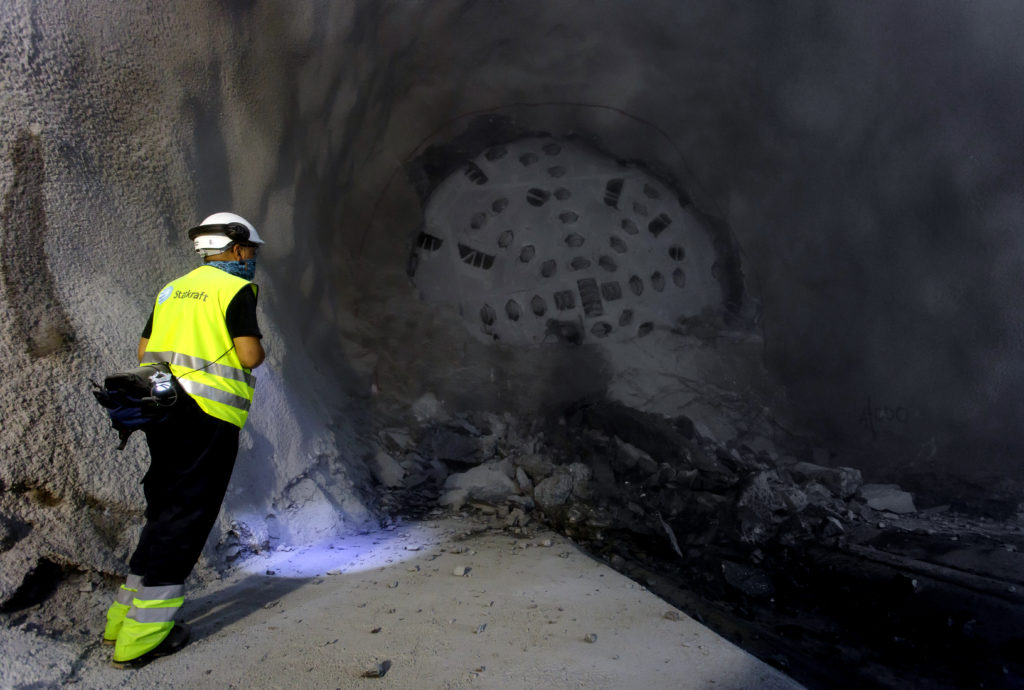
Successful breakthrough in July 2014.
A project that had started out as a disheartening one transformed into one that encouraged others. The insights gained by implementing changes to the Kargi machine were quickly applied to other projects facing mixed ground conditions that would otherwise require multiple tunneling machines. From these creative solutions came the design of a new line of Robbins dual-mode machines—TBMs that contain features of two machine types—termed Crossovers. Everything from multi-speed gearboxes to canopy drills, and emergency thrust are regular features of Crossover machines, and they owe their genesis to the hard work involved at Kargi HEPP.
Recent Posts
- Tunneling in Turkey: The Esme Salihli Railway
- Incredible India: Machines on the Move in Agra and Delhi
- Notice of Retraction and Apology
- Four Things You Need to Know about Probe Drilling and Pre-Grouting
- The Latest Updates: Records in Toronto, the News from Nepal, and More