Author: Robbins
Sustainable Tunneling with Rebuilt TBMs
Sustainability in tunneling is more than just a hot topic: current and future tunnel projects can and should seek ways to reduce environmental impacts. One of the simplest ways to reduce impacts and carbon footprint is with a renewable resource: a tunnel boring machine. TBMs have been proven to last for decades, and can be rebuilt cost effectively project after project with proper maintenance. In fact, several known, active TBMs are still boring tunnels after more than five decades of use and 50 km of total tunneling.
Just how successful can rebuilt TBMs be? We explore this question through the lens of the DigIndy Project in Indianapolis, Indiana, USA, where contractor J.F. Shea is using a rebuilt TBM to great effect. The 6.2 m diameter Main Beam TBM on that project, originally built in 1980, recently bored the last of more than 40 km of tunnels below the city. During the course of boring, the machine set three world records in its size class of 6 to 7 m, including a best month of 1,754 m.
In this complimentary, 60-minute webinar we discuss rebuilt TBMs as a key to sustainable tunneling with Doug Harding, Robbins Vice President, and Christian Heinz, Project Manager for J.F. Shea. Listen in on our conversation with Julian Champkin of Tunnels & Tunnelling International as we discuss recommendations for rebuilt machine use, and case studies from around the world. The on demand recording is available now.
A Clean Solution for Renewable Energy: Small Diameter Hydro Tunnels
Small hydroelectric power projects, with installed capacity up to 10 MW, are a relatively untapped but potentially game-changing source of renewable energy worldwide. In Norway, hydro projects are pioneering the use of small diameter TBMs in hard rock. Compared with drill and blast, TBMs offer increased production rates and reduction in cross section, as well as lowered rock support requirements and reduced project schedules.
The uniquely designed machines are engineered to take on steep gradients, up to a 45-degree angle in some cases. Both shielded and open-type TBM designs have been developed that utilize safety grippers and customized mucking systems to operate at steep grades. This paper will discuss the specialized TBMs and their performance at several projects in Norway, as well as the potential to use this technology throughout Europe and internationally.
Non-Circular Tunnel Boring for Underground Mine Development
TBMs have been used in mining in decades past, but their use has been limited and sporadic. This has changed in recent years, with TBMs being used at Stillwater Mine, Grosvenor Coal Mine Slopes, and Sirius Minerals potash mine. These machines are all full face, circular TBMs. With their circular bores, these machines have thus far been unable to tackle a larger issue for mines—the need for a flat floor. While the mining industry excavates many more kilometers of tunnel each year than the civil construction industry, typically a flat floor is needed for mining vehicles to traverse.
A novel type of non-circular boring machine is now answering that need with its ability to cut a rectangular profile in hard rock. This cross section allows for use of typical mine trucks and other rubber-tired mine vehicles. It provides more useable space, compared to a circular profile, and minimizes the amount of excavated rock that must be hoisted out of the mine. This machine uses typical disc cutters to cut the rock and has a support structure similar to an open type TBM; however, the cutting geometry is entirely different. The machine is currently cutting an access tunnel at a silver mine.
Bauma 2025
Event Name: Bauma
Dates: April 7-13, 2025
Location: Munich, Germany
Venue: Messe München
Stand: C2.102
Meet us in Munich, where Robbins will be exhibiting at Bauma, the largest construction machinery trade show in the world. Join us in Hall C2, stand 102 between April 7 and 13, and get the latest on our products and projects. From underground mining solutions to record-setting civil tunneling bores, Robbins is committed to excellence across industries.
Unprecedented Diameter Change: The Mill Creek Tunnel
At the Mill Creek Drainage Relief Tunnel in Dallas, Texas, USA, a Robbins Main Beam TBM underwent an in-tunnel diameter change for the first time in the industry. The machine went from 11.6 m diameter to 9.9 m diameter through teamwork, perseverance, and top-notch engineering. Watch the video to find out more about the ground-breaking process and unique project.
Landmark Breakthrough for Robbins TBM ‘Big Tex’
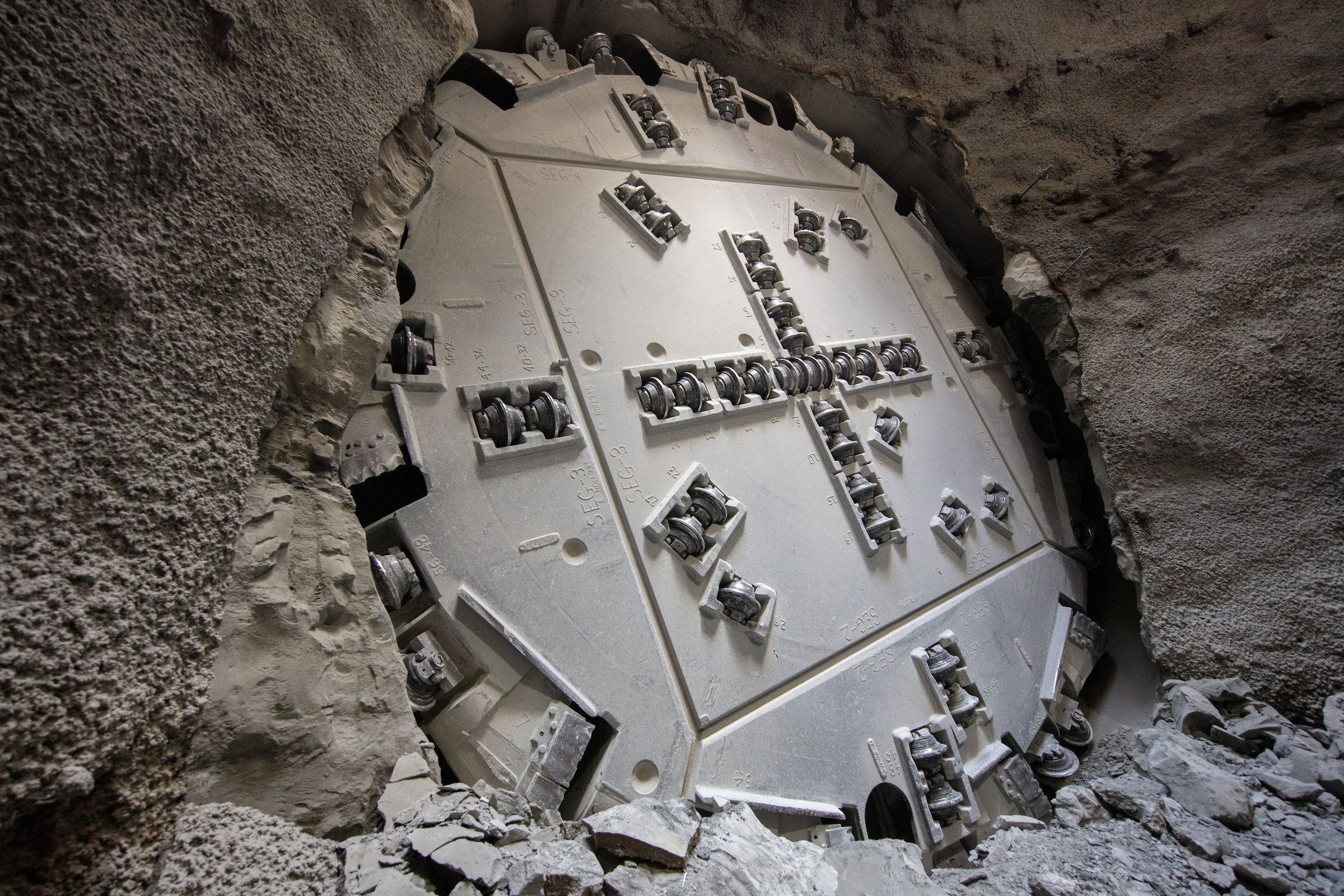
The Robbins Main Beam TBM, dubbed ‘Big Tex’, broke through on July 25, 2022 in Dallas, Texas, USA.
On July 25, 2022, a crowd gathered as a large Robbins Main Beam TBM, dubbed ‘Big Tex’, broke through in Dallas, Texas, USA. The machine and its continuous conveyor system, for the Mill Creek Drainage Relief Tunnel, successfully bored 8 km (5 mi) in chalk and shale at up to 498 m (1,634 ft) advance in one month. “I think when you step back and look at what was accomplished by this team as whole…the overall length and size of this tunnel, the TBM conversion, the everyday grind to keep moving forward…it truly is something to be proud of, professionally and personally. No single individual could reach this milestone. It took a great team of skilled individuals. I am fortunate to be a part of it,” said Nick Jencopale, Sr. Project Manager for contractor JV Southland/Mole.
Good advance rates were not the only cause for celebration: the unique project required a planned in-tunnel diameter change of the TBM from its original 11.6 m (38 ft) to a more compact 9.9 m (32.5 ft). The first-of-its-kind conversion process was undertaken 2.8 km (1.7 mi) into the bore and was not done inside a shaft or pre-excavated portal. “The TBM conversion was a unique challenge that we were excited about, and ultimately provided a more efficient method for the desired product compared to the alternative options. Hopefully the successful conversion proved that this option can be considered for future tunnel projects,” said Jencopale.
While there were many detailed steps to the conversion process, precision design of the machine was a key aspect. “We started with a smaller machine, then we made a kit or second skin that was slightly larger. And then when the time came, we just took that skin off. It was essentially that simple,” said Evan Brinkerhoff, Robbins Field Service Manager. The conversion took about four months and was completed in April 2021.
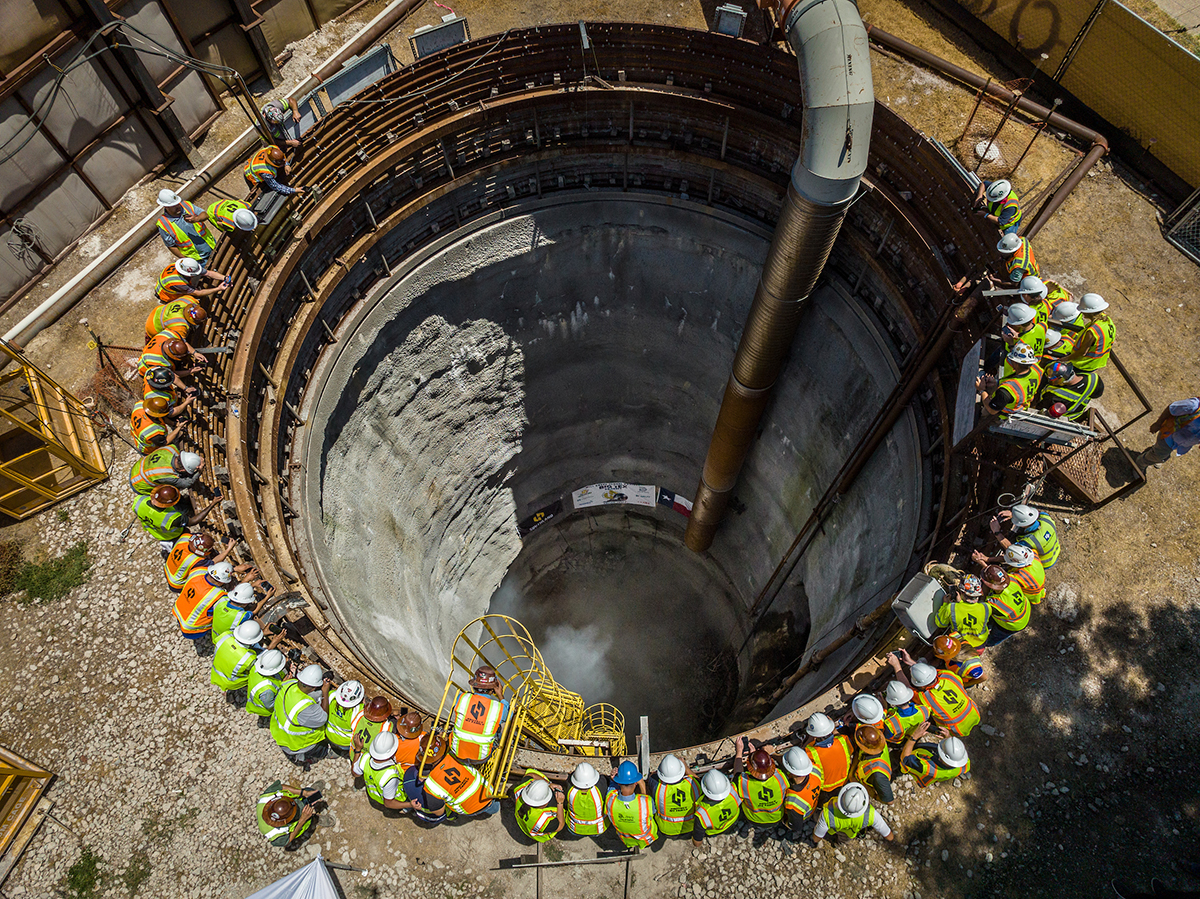
A crowd gathers as the Robbins TBM breaks through into a shaft at the Mill Creek Drainage Relief Tunnel in Dallas, Texas, USA.
“The Robbins Main Beam TBM (‘Big Tex’) performed consistently throughout the duration of the tunnel excavation. There were very minor issues and little overall downtime as a result of the TBM itself,” said Jencopale. Due to the relatively favorable ground conditions in much of the tunnel, including low rock strength and low abrasivity, only eight disc cutters were changed during the length of tunnel bored at the larger diameter. At the time of diameter change the full dress of cutters was changed, and since that change only 14 cutters have needed replacing. Crews did encounter some fault zones, and installed rock bolts and wire mesh in the tunnel crown as needed.
With the TBM-driven portion of the tunnel now complete, work can commence to remove the machine from the tunnel and install a final lining. The tunnel is a designated critical infrastructure project for the City of Dallas, providing 100-year flood protection for areas of East Dallas that have experienced severe flooding in the past. Construction work is expected to be complete in late 2024/early 2025.
Unprecedented In-Tunnel Diameter Conversion of the Largest Hard Rock TBM in the U.S.
The largest hard rock TBM ever to bore in the USA, an 11.6 m diameter Robbins Main Beam TBM, recently underwent a planned in-tunnel diameter change to a more compact 9.9 meters. The first-of-its-kind conversion process for the Main Beam TBM was undertaken 2.8 km into the bore and was not done inside a shaft or pre-excavated portal. This paper will detail the unique dual-diameter machine designed for the Mill Creek Drainage Relief Tunnel in Dallas, Texas, USA, machine performance, and successful size conversion process that took place in early 2021—a process that utilized the four C’s of construction to enormous benefit: Communication, Cooperation, Collaboration and Coordination.
Hard Rock Tunnel Boring at the Jefferson Barracks Tunnel
The Metropolitan St. Louis Water District’s Project Clear is a 28-year program targeting wastewater capacity throughout St. Louis, MO. The extensive program includes the Jefferson Barracks Tunnel, running parallel to the Mississippi River at 2 m ID and 5,400 m long. A rebuilt Robbins Main Beam TBM began boring but hit challenging conditions about 2,400 m in, including water inflows. A larger 4.1 m Robbins Main Beam machine, launched in 2022, is now completing the remaining 3,050 m in limestone, dolomite, and shale. The TBM is utilizing a high-powered, high breakout torque cutterhead along with enhanced 360-degree probing & grouting capabilities to detect any karst formations.
The Next Generation of Mixed Ground Tunnel Boring Machines
What is the most economical way of tunneling in mixed ground that may experience high pressures? Non-continuously pressurized, mixed ground Tunnel Boring Machines (TBMs) are being utilized to deal with a wide range of geology. Continuous improvements in these mixed ground machines allow for ever-increasing efficiency and reduction of project risk due to unexpected conditions. Read this paper for a look at how new improvements to Crossover machines will enable excavation of an expanded range of ground conditions. These conditions include mixed ground with low fines, mixed face rock, and fracture / fault zones with high pressures where in the past a Slurry TBM may have been utilized.
World Tunnel Congress 2022
Event Name: ITA-AITES World Tunnel Congress
Dates: September 2-8, 2022
Location: Copenhagen, Denmark
Stand: E-11B
Come join us September 2-8 in Copenhagen, Denmark for the ITA-AITES World Tunnel Congress, the premiere event for tunneling and underground construction. More than 160 exhibitors will convene, and hundreds of technical papers will be presented on the latest topics of interest. Stop by our stand E-11B to converse with our expert international team, and find out the latest about our products, projects, and talks at the conference.
Technical Presentation:
Wednesday September 7
Track 4, Mechanized Tunnelling 6
Hard Rock TBM Tunnelling Session, Room Wed6
11:30 – 11:50 AM
Rock Tunnels at High Water Pressure: Non-Continuous Pressurized Tunneling vs. Slurry Tunneling
Presented by Lok Home, Robbins President
Poster Presentations:
Tuesday September 6
1:10 – 1:30 PM
Hall C, Station 10
A Clean Solution for Renewable Energy: Small Diameter Hydro Tunneling
Presented by Detlef Jordan, Sales Manager Europe
Tuesday September 6
1:30 – 1:50 PM
Hall C, Station 6
A Novel, Non-Circular Tunnel Boring Machine for Underground Mine Development
Presented by Brad Grothen, Technical Director