Category: Hidden Underfoot
Breakthroughs While Breaking Ground: The First TBM Conveyor
Modern Achievements
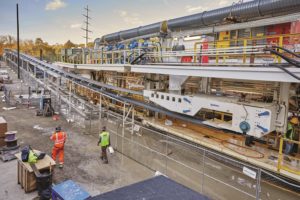
The 100th conveyor system has been refurbished and customized for the job in a process that Robbins has been perfecting for decades.
There are many elements that contribute to the success of a project: having an accurate report of ground conditions, choosing the proper equipment, having a well-trained team operating the tunnel boring machine—and behind it all—the utilization of a high-quality conveyor system. As tunneling machines evolve and bore at continuously faster rates, rapid muck removal becomes more important than ever. Robbins conveyor systems are capable of moving more than two thousand US tons of muck per hour—saving time and money on every project that uses the complete system.
In Akron, Ohio, a major milestone has been reached for Robbins conveyors. Running behind a Robbins 9.26 m (30.4 ft) diameter Crossover TBM is the 100th Robbins Continuous Conveyor System supplied for muck removal—more than any other TBM conveyor supplier has sold. The conveyor in Akron is just one landmark event in the long history of Robbins conveyors, the start of which can be traced back to the first ever documented use of a continuous conveyor system behind a TBM.
Pioneering Muck Removal
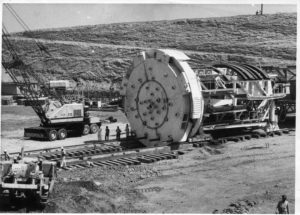
No roads were at the site in West Pakistan so goods were transported by rail car, requiring surveying of hundreds of bridges from the port city of Karachi.
The prototype for the conveyor systems we know today was developed by James S. Robbins in 1963 and was built using a Goodman coal-mine conveyor instead of muck cars which were more commonly used during that period. The conveyor ran behind what was, at the time, the largest TBM in the world. The 11.2 m (36.7 ft) diameter Robbins Main Beam was built for the Mangla Dam Project in what was then known as West Pakistan. The 4.3 km (2.7 mi) long tunnel was built to control water flow from the Jhelum River for use in agriculture and hydro-electric power.
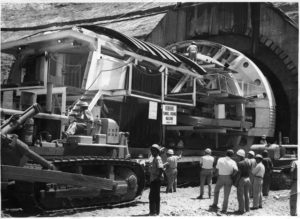
Temperatures at the jobsite climbed up to 53 degrees C (127 degrees F) in the shade.
The conveyor design had originally been used for coal and potash mines and was adapted for use behind the TBM. An extendable belt was side-mounted in the tunnel, leaving room for man-access and rail tracks to carry materials. Belt tension was maintained using a belt cassette. “They were able to operate continuously. It worked like a charm—and then the extensible conveyor was forgotten by the industry because it was perceived by contractors and owners as too much of an investment,” explained Dick Robbins, former President and CEO of The Robbins Company, in a 2013 article for World Tunnelling. It would be another 30 years after the successful completion of the Mangla Dam tunnel until conveyors became a standard means of muck removal in the tunneling industry.
Persistently Moving Forward
Conveyors have come a long way since their first use. Unlike the system used for the Mangla Dam project—which was limited to the use of a straight belt—conveyors can now wrap around curves and bring rock vertically up a shaft to the surface. “The control system, along with monitoring systems, has dramatically improved,” says Dean Workman, Robbins Director of Conveyors, Cutters, and SBUs. “The components have all been enhanced, giving a much longer life to the conveyor system. Contractors are using the same conveyors on multiple projects with minor refurbishments between projects.” While the basic function of a conveyor has stayed the same—muck hauling—the quality of conveyor systems has certainly changed.
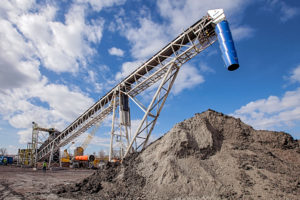
Did You Know: At least 75% of all world records achieved by TBMs were done with a continuous conveyor system for spoils removal rather than muck cars.
In a new design that is being used for the Los Angeles Purple Line Extension, continuous conveyors have gained another ability, they are now able to change direction. The unique system can be flipped to accommodate two machines boring parallel tunnels eastward before being re-launched to bore west. Due to the narrow launch shaft, modular components were designed to save space, and were built using a kit of secondhand parts, showcasing the long-life conveyor systems are capable of. “We are always looking to improve the design and function of the system,” says Workman, “modular components are a benefit to the contractor when installing, maintaining, and shipping the equipment.”
As progress continues and new technology provides advancements for the industry, The Robbins Company continues to uphold the pioneering spirit that James S. Robbins brought to tunneling with his trailblazing developments.
Read More:
Robbins Conveyor Systems
Conveyor Spec Sheet
100th Conveyor
Boring the Blue Mountains: The Inside Story on the World’s Fastest TBM
Over 20 years ago, a Robbins open-type machine set three world records while tunneling in the picturesque Blue Mountains in Australia. You may be asking yourself, why is this significant? Why drudge up a project that is surely outdated at this point in our industry’s history? The fact of the matter is, two decades have passed and the Robbins open-type TBM chosen for this project is still considered to be the world’s fastest TBM.
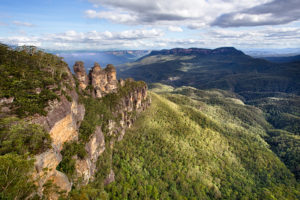
The picturesque Blue Mountains in New South Wales, Australia.
Project Background
In 1993, the 3.4 m (11 ft) diameter TBM was chosen to bore two sewage tunnels in the Blue Mountains near Sydney, Australia. At the time, there had been a rapid expansion of urban developments within the Blue Mountain National Park, causing an influx of pollution to enter streams as the result of septic tank runoff and outdated sewage treatment plants.
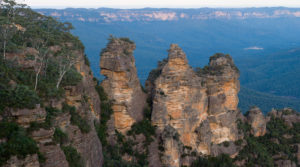
A closer look at the Three Sisters, a unique rock formation in the Blue Mountains.
The Blue Mountains Sewage Transfer Project comprised of approximately 40 km (25 mi) of tunnels, two of which were TBM-driven using the Robbins machine. The first, the Katoomba Carrier tunnel, was 13.4 km (8.3 mi) long and the second, the Lawson Carrier, was 3.5 km (2.1 mi) long. While the Lawson Carrier tunnel was finished five weeks prior to the expected completion date, it was during the Katoomba Carrier tunnel that all three records were set. During excavation the machine set the following world records: best day of 172.4 m (565.6 ft), best week of 702.8 m (2,305.7 ft), and a best monthly average of 1,189 m (39,000 ft) within its size range of 3 to 4 m (9.8 to 13.1 ft) diameter machine. Two of those records—the best day and best week—are the fastest ever recorded and have yet to be surpassed by any TBM of any size.
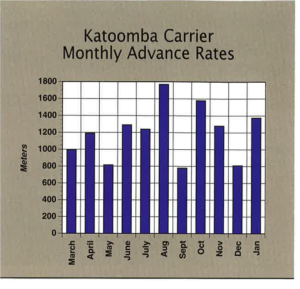
The 3.4 m (11 ft) diameter TBM set three world records while boring the Katoomba Carrier tunnel. Photo credit: tunneltalk.com
Custom Machine Design
There were many factors that played into this machine’s success—the system utilized on this project required a well-planned design, careful operation, and regular maintenance. As many people involved in tunneling know, choosing the right equipment for the geology can make or break a project. Detailed empirical data allowed the contractor to accurately predict what kind of ground they would encounter and prepare accordingly. The National Park is located within the Triassic Sydney Sedimentary Basin and is comprised primarily of sandstones and claystones. Anticipating this geology, the 3.4 m (11 ft) diameter machine’s cutterhead was dressed with 25 Robbins 17-inch diameter disc cutters designed for soft yet abrasive rock formations.
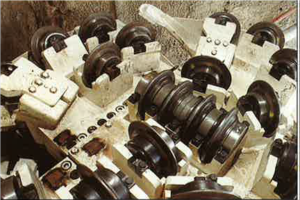
A close-up of the 17-inch cutters.
Logistics
The 13.4 km (8.3 mi) long Katoomba Carrier tunnel was originally planned to comprise of multiple short tunnels, several kilometers in length each, with intermittent portals to shorten drives. Ultimately it was decided to make the project one continuous tunnel, which led to higher advance rates and deemed it—at the time—the longest single-drive TBM tunnel. Not only did this change save time, but it also allowed boring to be less disruptive to the landscape.
Continuous Conveyor
In addition, the project was the first in Australia to utilize a continuous conveyor system. Due to the length of the tunnel, the use of traditional muck cars for muck removal would have taken too much time and were seen as an inadequate solution. The 106-m (347.8 ft) long system boosted production rates, with a best day of 1,565 m³ (55,267 ft³) of in-situ material removed from the Katoomba tunnel.
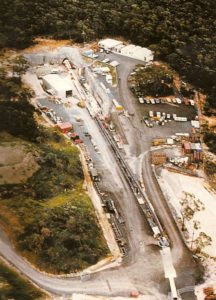
The Blue Mountains project was the first TBM-driven tunnel in Australia to utilize a continuous conveyor system.
Good Geology
Ground support throughout the tunnel comprised of a combination of resin grouted bolts, mesh, steel straps and steel sets. In the sturdier sandstone, however, the tunnel was left largely unlined and instead shotcrete was applied to areas of poorer, softer rock.
As boring progressed, the sandstone proved to be softer than expected. Instead of the predicted average of 80 MPa ranging from 20 MPa to 150 MPa, it averaged 40 MPa to 50 MPa with a range of 10 MPa to 100 MPa. This ideal material could also have contributed to the Robbins machine’s record breaking results and its early breakthrough, which occurred nine months ahead of schedule.
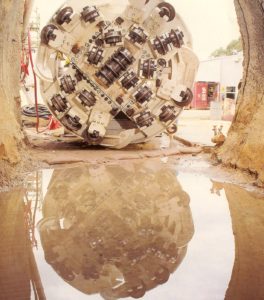
The machine’s record breaking boring enabled the project as a whole to finish 17 months ahead of schedule.
Exceeding Expectations
The Robbins Mk 12C’s performance on the tunnel boring portion of the project substantially surpassed all expectations. Not only did it set the previously mentioned world tunneling records, but it also helped the project as a whole finish 17 months ahead of schedule, saving not only on time but on significant financial costs.
The Creation of the Crossover
The Real Field Experiences that Resulted in a Versatile Design
This blog is the first in a series called “Hidden Underfoot”, exploring the little-known history and behind-the-scenes happenings of the tunneling industry.
Many technological breakthroughs have been the direct result of the necessity to solve a problem; the creation of the first Crossover TBM was no exception. While much has been written about Central Turkey’s Kargi Kizilirmak Hydroelectric Project, we interviewed Field Service personnel who were there working in the conditions every day to get the untold story behind the genesis of the versatile Crossover TBM.
Behind the Scenes
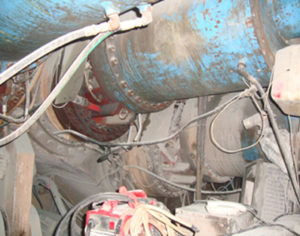
Custom-made gear reducers retrofitted to the motors in the tunnel.
The Kargi HEPP, now complete, generates 470 Gwh of power annually for project owner Statkraft, and supplies an estimated 150,000 homes.
Robbins supplied a 9.84 meter (32 ft) diameter Double Shield TBM and continuous conveyor system to Turkish contractor Gülermak for the project. The machine was to bore an 11.8 km (7.3 mi) headrace tunnel to divert water from the dam to powerhouse. Initial geological reports predicted softer ground for the first 2.5 km (1.6 mi), which would be lined with pre-cast concrete segments. The remainder of the tunnel was to be supported by a combination of shotcrete, rock bolts, and wire mesh in more competent rock.
The project became arduous soon after startup, when the machine encountered blocky rock, sand, and clays that were not initially predicted. “We realized modifications needed to be made as soon as we started experiencing flowing materials and squeezing ground,” said Glen Maynard, Robbins Site Manager, who worked on the project throughout the challenging conditions. Maynard’s prognosis was apt, as 80 meters (262 ft) into the bore the TBM became trapped in a section of collapsed ground. “The machine faced serious blockages,” added Maynard, “there was no one fix, each problem needed its own solution. Thrust, cutterhead, and ground support all needed adjustment.” The machine was freed but continued to struggle, requiring not just one but seven bypass tunnels to free it each time it encountered collapsing ground.
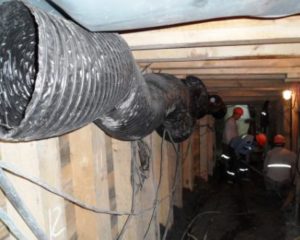
Construction of one of several bypass tunnels at Kargi.
Concerns that the machine would need to be buried were quickly mollified. Robbins President Lok Home told the Kargi team to build a “wish list” of all the materials they would need to modify the machine and get it moving again. Robbins and Gülermak worked together to determine what changes would need to be made, and parts were shipped to the jobsite as quickly as possible. This of course, was not the first time a machine had required modifications while in the tunnel, and Robbins engineers were able to pull from past projects in order to know what needed to be done.
In-Tunnel Effort
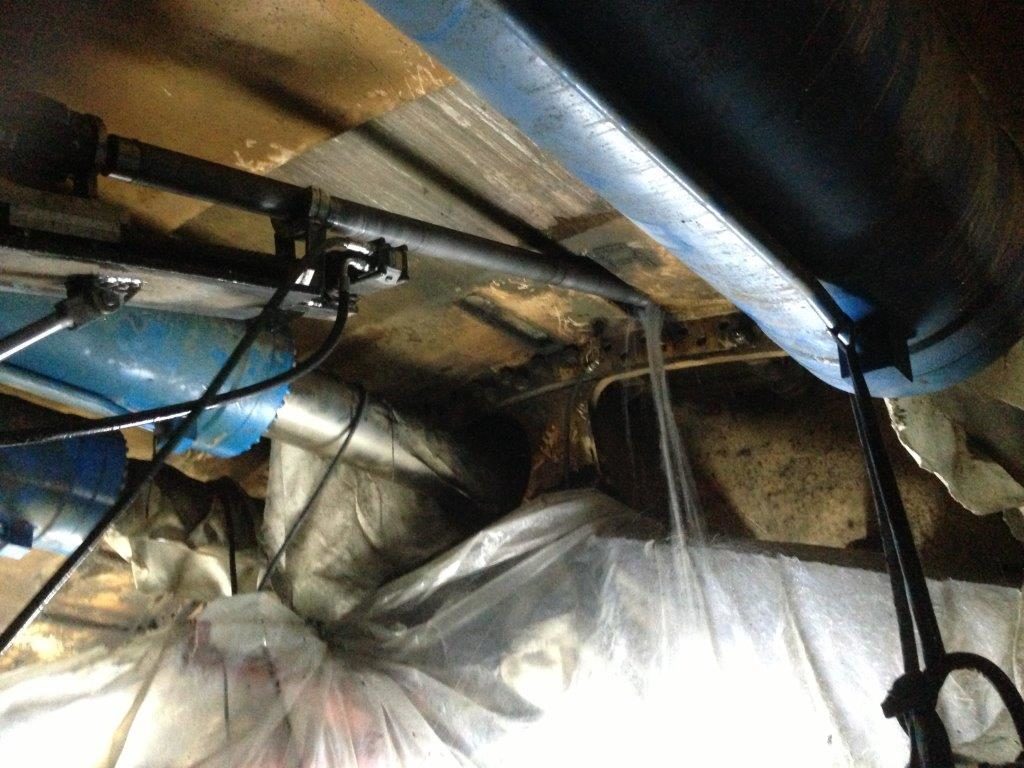
Canopy drill installed in the tunnel.
The contractor, with the assistance of the field service team, installed a Robbins custom-built canopy drill and positioner to allow pipe tube support installation through the forward shield. This allowed drilling with a distance of up to 10 m (33 ft) ahead of the cutterhead while 90 mm (3.5 in) diameter pipe tubes provided extra support across the top 120 to 140 degrees at the tunnel crown. Injection of resins and grout protected against collapse at the crown while excavating through soft ground. “There were a lot of risks to the modified machine, but we gave comprehensive instructions on how to operate it to the contractor,” said Maynard. “The contractor team was open to change and had great cooperation. They were a really hard working team.”
To further mitigate the effects of squeezing ground or collapses, custom-made gear reducers were ordered and retrofitted to the cutterhead motors. They were installed between the drive motor and the primary two-stage planetary gearboxes. When the machine encountered loose or squeezing ground the reducers were engaged, which resulted in a reduction in cutterhead RPM and a doubling of the available torque. The net effect of the modifications allowed the Double Shield TBM to operate much like an Earth Pressure Balance Machine in fault zones and squeezing ground with high torque and low RPM—these methods effectively kept the machine from getting stuck. In addition, short stroke thrust jacks were installed between the normal auxiliary thrust to double total thrust capabilities.
The results of the modifications led to astonishing results. An advance rate of 600 m (1,986 ft) in one month was achieved in March 2013 and a project best of approximately 723 m (2,372 ft) was achieved in spring 2014, including a daily best of 39.6 m (130 ft) in April 2014. The TBM bored 7.8 km (4.8 mi) of the tunnel in total, making its final breakthrough in July 2014. The remainder was excavated by drill and blast—of which it is notable that the modified TBM achieved advance rates more than twice that of the traditional mining operation. “It was enjoyable to find a way to overcome this challenge,” added Maynard.
Mixed Ground Legacy
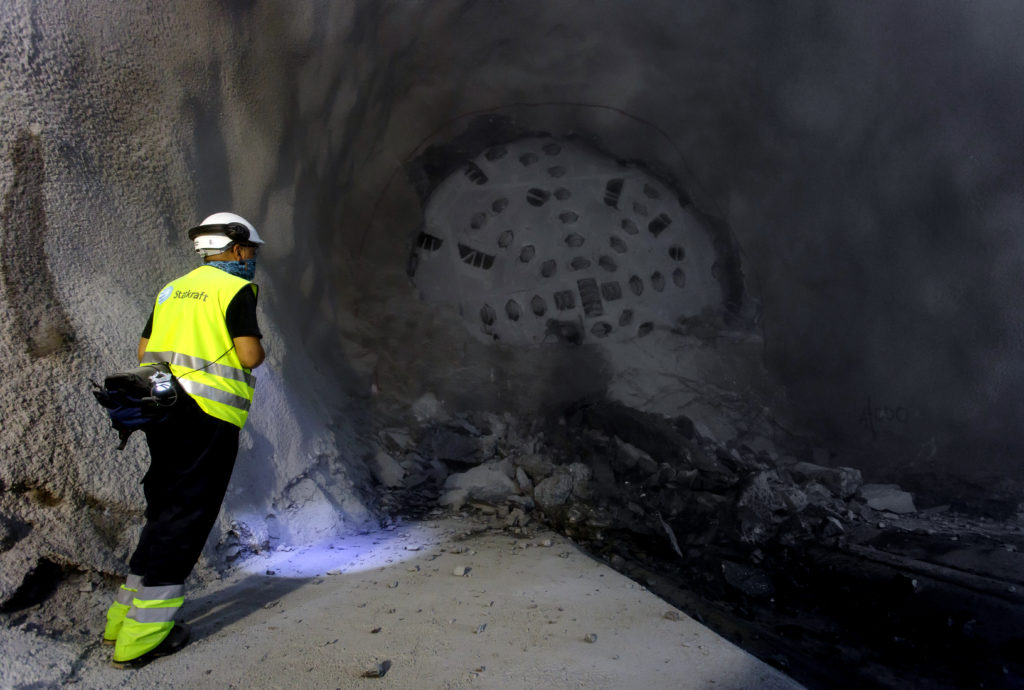
Successful breakthrough in July 2014.
A project that had started out as a disheartening one transformed into one that encouraged others. The insights gained by implementing changes to the Kargi machine were quickly applied to other projects facing mixed ground conditions that would otherwise require multiple tunneling machines. From these creative solutions came the design of a new line of Robbins dual-mode machines—TBMs that contain features of two machine types—termed Crossovers. Everything from multi-speed gearboxes to canopy drills, and emergency thrust are regular features of Crossover machines, and they owe their genesis to the hard work involved at Kargi HEPP.
Recent Posts
- Tunneling in Turkey: The Esme Salihli Railway
- Incredible India: Machines on the Move in Agra and Delhi
- Notice of Retraction and Apology
- Four Things You Need to Know about Probe Drilling and Pre-Grouting
- The Latest Updates: Records in Toronto, the News from Nepal, and More