Category: Blog
3 Ways to Bore More Efficiently in Extremely Hard Rock: Maximize your TBM Advance through Minimized Downtime
When the rock seems unbreakable, stresses are multiplied: The cutters must be stronger, the TBM more durable, and the operation optimized to keep equipment running smoothly. Once rock hardness rises beyond 180 to 200 MPa UCS, the limits of cutting tools are put to the test.
Given the clear risks of excavating massive, hard rock, how can tunnellers set themselves up for the best possible chance of success? The combination of knowledgeable personnel, properly designed equipment, and rigorous TBM operation and maintenance are making excavation of hard rock—even extremely hard rock strengths of 300 MPa UCS or more—possible.
1: Consider your Cutting Tools
Cutters are a significant factor for efficient excavation when rock is extremely hard. To that end, Robbins has developed Extra Heavy Duty (XHD) rings for projects where Heavy Duty (HD) rings are close to their design limit in terms of the thrust force required to break the rock. The XHD rings resist chipping, mushrooming, and other damage that can occur in very hard rock conditions. Enhanced heat treatment gives the discs increased hardness and strength without the normally-associated reduction in fracture toughness.
The rings have a proven track record: they’ve been put to the test at several jobsites, including Norway’s Røssåga headrace tunnel bored in rock from 200 to 280 MPa UCS. Initially, HD cutters mounted on the Main Beam TBM’s cutterhead experienced low cutter life in the range of 100 to 150 cubic meters bored per cutter. XHD rings were gradually introduced onto the cutterhead to determine what, if any improvement in cutter life could be obtained. It is likely that the performance in the very hard sections was improved by a minimum of 25%. The benefits of the XHD are also likely to explain the superior cutter life for the remainder of the project, even in the relatively softer ground.
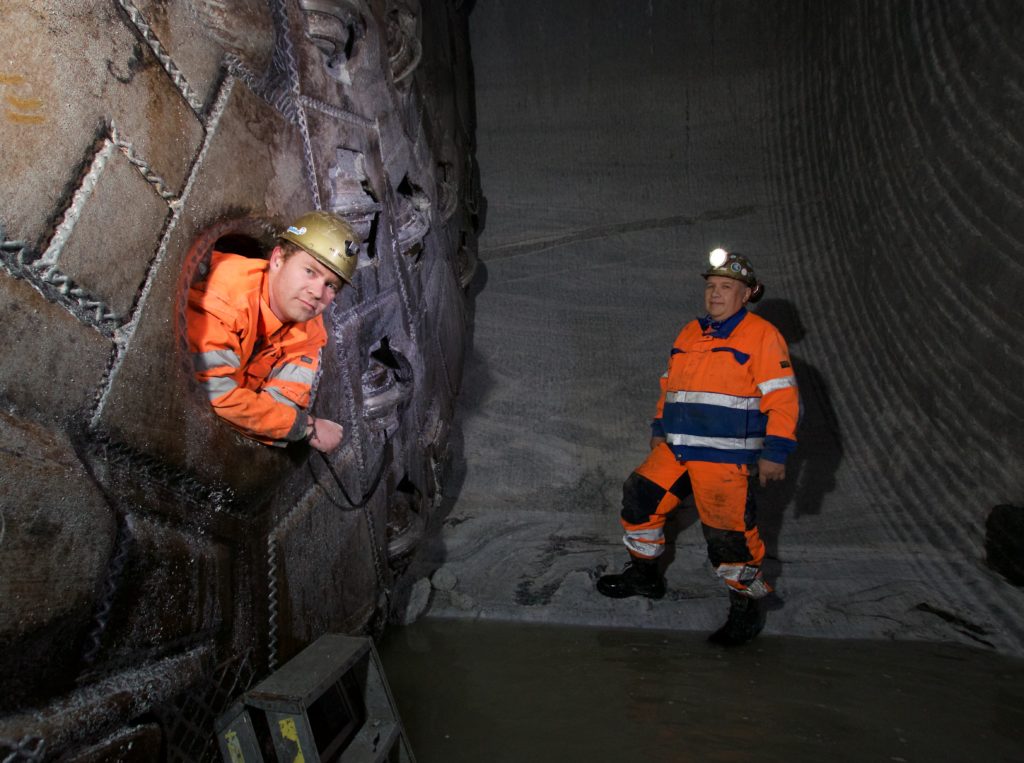
The rock at Norway’s Røssåga headrace tunnel averaged from 200 to 280 MPa UCS, requiring XHD rings.
2: Optimize Penetration Rate
Harder rock requires equipment that can stand up to high stresses. Penetration rate and thrust are exponential functions. The first rule is: Push as hard as you can. The more thrust the better. A machine with a robust steel structure is needed to take the higher loads without damage.
But penetration rate is trickier: The overall goal in hard rock should be to operate TBMs as efficiently as possible to maximize production. This means increasing penetration per revolution as much as possible. Consumption of cutterhead wear parts is related to the number of revolutions of the cutterhead, so it follows that increased penetration per revolution will result in fewer total revolutions of the cutterhead, reduced consumption of wear parts and fewer cutter changes for the duration of the tunnel.
The TBM Operator should therefore be looking for the best advance at the lowest RPM, because lower RPM reduces wear on the outer cutters and periphery of the cutterhead. Robbins has conducted site tests at multiple sites over several years showing that a lower RPM achieves the same and often better penetration rates than a higher RPM in hard rock. This can be clearly seen in the data: For example, on an 8 m diameter cutterhead, the circumference is 25.12 m. At 10 RPM during TBM operation, this would mean 251.2 m of travel in one minute. If the speed is reduced to 8 RPM, the distance would be 200.9 m of rotation—a full 50 m less in one minute. That is 3000 m less per hour, reducing wear substantially.
Malaysia’s Pahang Selangor Water Tunnel was a good example of this phenomenon. What is now the longest tunnel in Southeast Asia, at 44.6 km, required excavation using three 5.2 m diameter Main Beam TBMs mounted with 19-inch disc cutters. The machines operated in abrasive granitic rock exceeding 200 MPa UCS, up to 1,200 m below the Titiwangsa Mountain Range. RPM trials were conducted on the three TBMs, showing that an increase in penetration rate per revolution of 15 to 20 percent could be achieved by decreasing the RPM from between 11.5 and 12 to just 9.5. While the overall advance rate was lower because of fewer revolutions, downtime was decreased and cutter changes were reduced by as much as 19%. The overall time savings more than made up for the decreased advance rate.
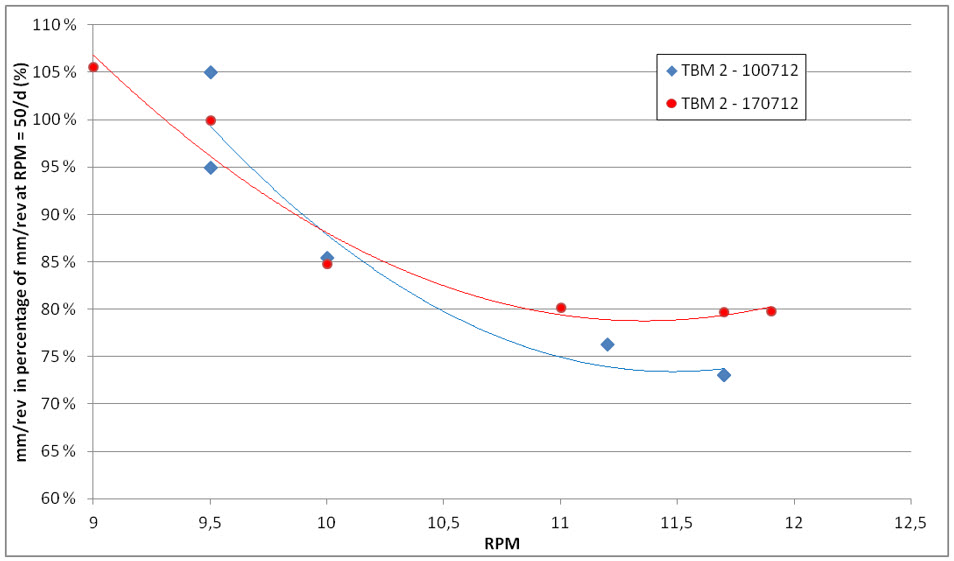
In site tests, reduced RPM resulted in increased TBM penetration rates.
3: Your Crew is the Key
Knowledgeable operators are key in hard rock: there needs to be a balance between cutterhead speed and thrust force. An experienced TBM Operator will be able to identify when ground conditions change and react accordingly. In addition, knowledgeable operators know how to react if varying rock strengths are present in the excavation face. The most effective way to prevent impact loading in such conditions is to reduce cutterhead speed and penetration rate per revolution.
Maintenance is another key point and is especially important for extremely hard rock conditions. At the start of a project it is recommended to set a maintenance period for each day, say four hours out of each 24-hour period, which enables the crews to become familiar with the maintenance regime. This equates to approximately 24 hours of maintenance in a 6-day working week. Cutter change time can take up substantially more than four hours per day in hard rock tunnels, so once the crews are familiar with the maintenance tasks they are best carried out concurrently with cutter change operations.
Cutterhead inspections should be carried out on a regular basis to enable worn, damaged or blocked cutters to be replaced as soon as possible. Boring with even one blocked cutter can result in a cascading type wipe-out, which will progress rapidly in a chain reaction effect through multiple cutters if not immediately recognized. In hard rock this can also result in damage to the cutterhead over the course of just a couple of boring strokes. The same applies to the inspection of the bucket lips—these should be performed regularly and the bucket lips kept in good condition.
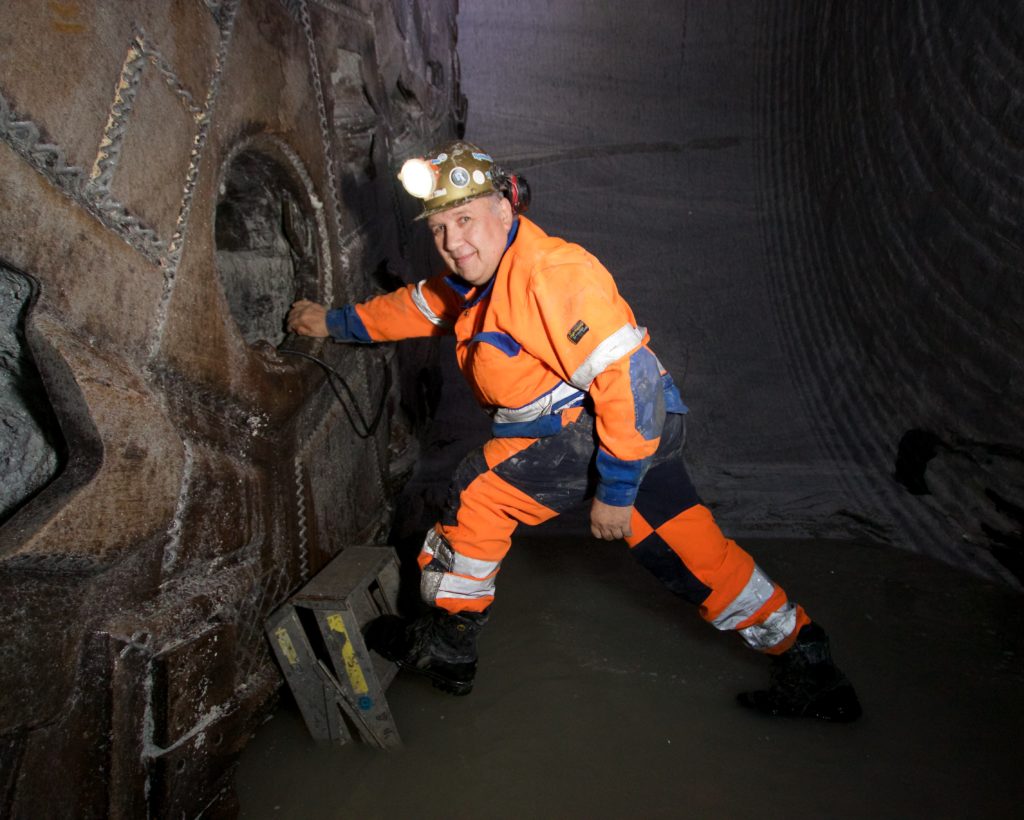
A crew member inspects a TBM cutterhead.
The Takeaways
Overall, ensuring success in some of the most difficult rock in the world requires pre-planning with proper machine design, good cooperation by all parties involved, a knowledgeable crew, and dedicated maintenance. More than that, it also takes some experimentation on the part of the contractor or those overseeing the TBM operation. Contractors can look at different cutter types and test the parameters of TBM operation, do regular penetration tests, vary the RPM, and vary the thrust to see what gets the best cutter life and the best TBM performance. Taking the time to do such testing can make all the difference between a successful project and an unsuccessful one.
Lastly, new and innovative cutter designs and housing designs exist for extremely hard rock. Consider XHD cutter rings, cutter mountings with hardened replaceable seats, and other designs that may be in development or available for testing.
A Bevy of Breakthroughs: The Robbins Jobsite Roundup Featuring 6 Epic Projects
Dozens of Robbins TBMs are normally in operation at any given time in countries around the world, but this month’s breakthrough extravaganza is exceptional. No less than six breakthroughs occurred during April 2019, and more are on the way. We take a look at these epic completions in pictures below.
Galerie des Janots, France
On April 3, 2019, a Robbins 3.5 m diameter Main Beam TBM broke through into open space, completing its 2.8 km long water tunnel. It was not the first time the machine had encountered open space: twice during tunneling, the machine hit uncharted caverns, the largest of which measured a staggering 8,000 cubic meters in size.
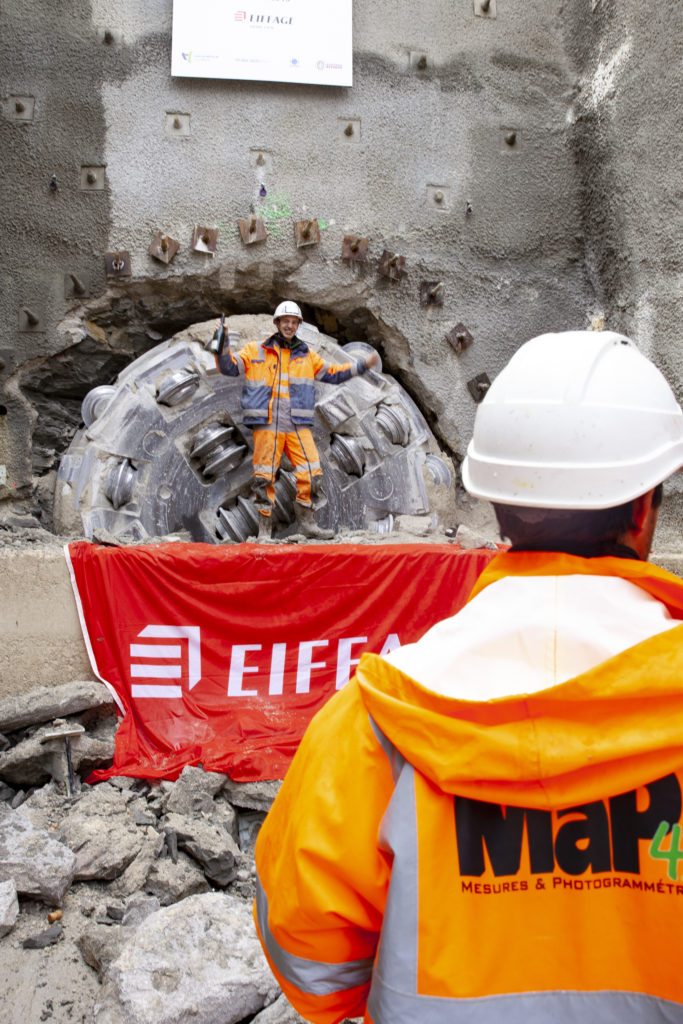
Contractor Eiffage Civil Construction celebrates the April 3 breakthrough of the Robbins TBM in Cassis, France.
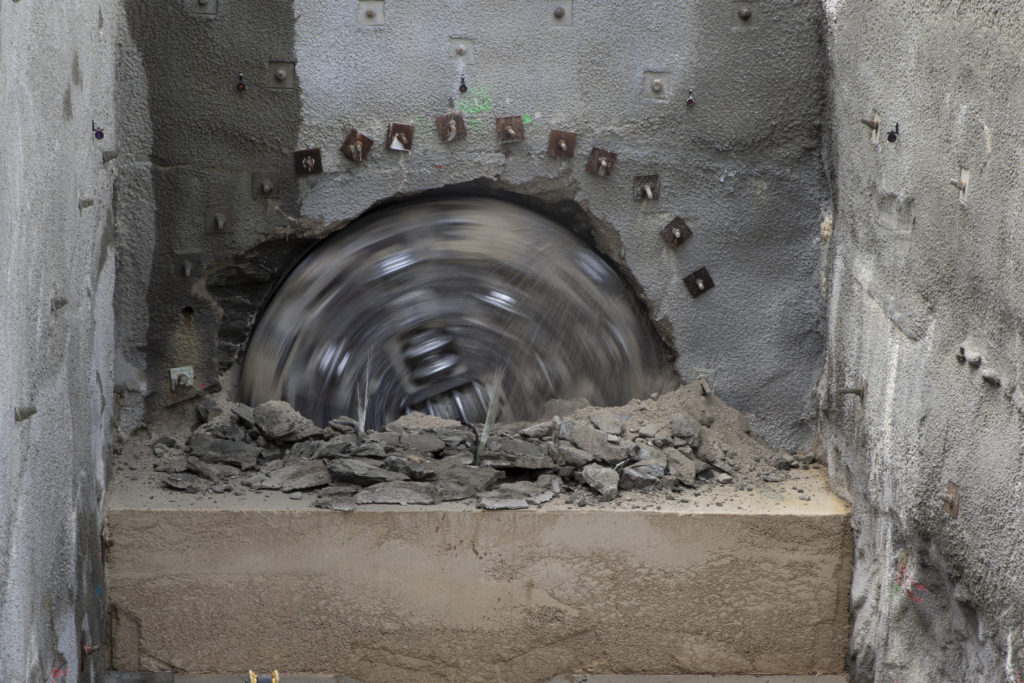
The Robbins TBM achieved rates of up to 25 m per day despite incredibly difficult geology including powdery clays and karstic limestone.
GKI, Austria
On April 8, 2019, the first of two 6.5 m diameter Robbins Double Shield TBMs completed its bore for Austria’s Gemeinschaftskraftwerk Inn (GKI) project. A second Double Shield TBM will break through later this year. The 22 km long headrace tunnel near the alpine town of Pfunds was bored under high cover (maximum of 1,200 m) in schist rock.
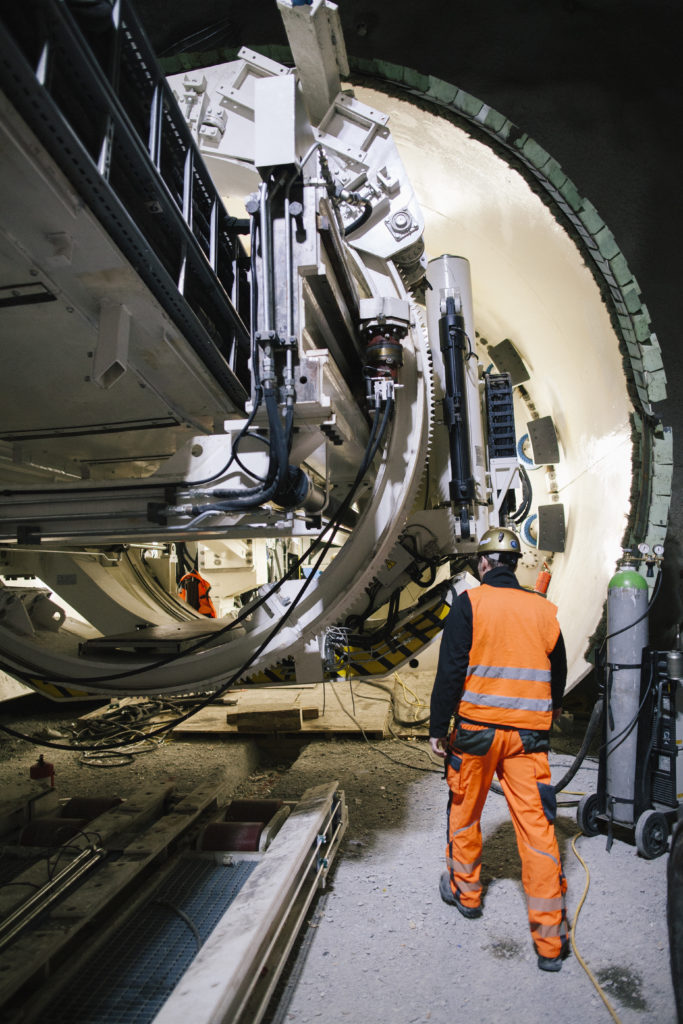
The first of two Robbins Double Shield TBMs, seen at launch, broke through on April 8.
DigIndy Tunnel System, USA
On April 10, 2019, a Robbins TBM completed the White River and Lower Pogues Run Tunnels, part of the DigIndy project in Indianapolis, Indiana, USA. The 36-year-old, refurbished 6.2 m diameter Robbins Main Beam machine was launched in 2013 in Indianapolis, and has done exceedingly well. Multiple world records in the 6 to 7 m diameter range were broken on the job, including “Most Feet Mined in One Day” (124.9 m), “Most Feet Mined in One Week” (515.1 m), and “Most Feet Mined in One Month” (1,754 m). Over the course of the project the TBM will bore more than 40 km of tunnels.
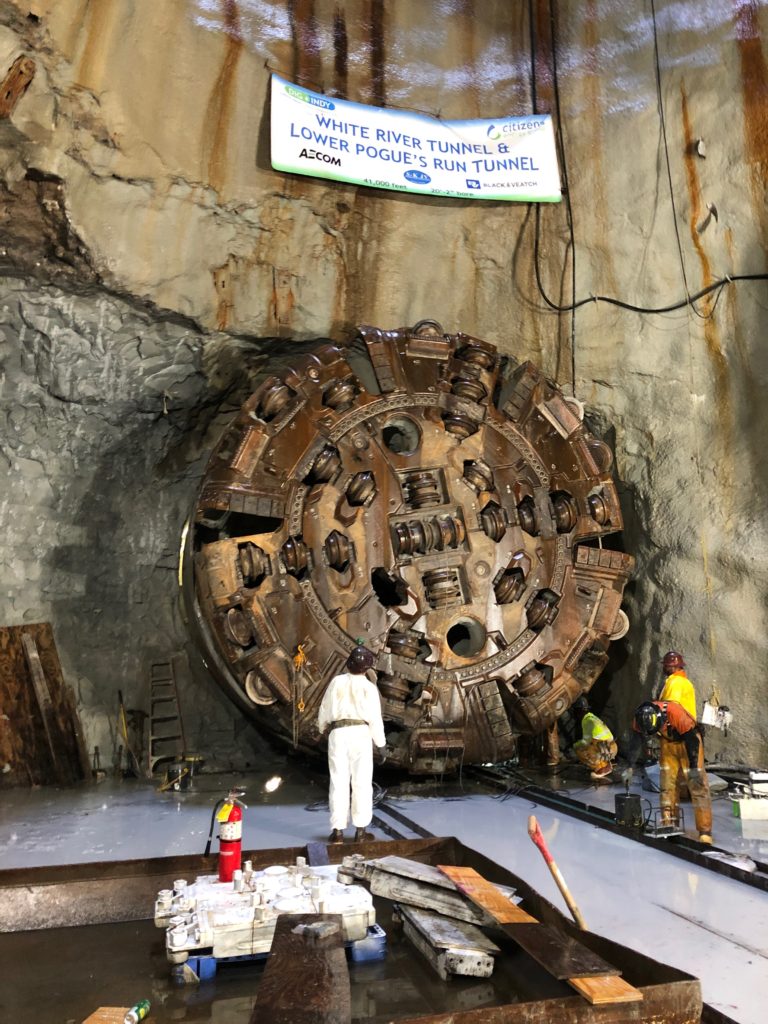
The Robbins Main Beam TBM completed two drives, the White River and Lower Pogues Run Tunnels, as part of the DigIndy Tunnel System.
Bheri Babai Diversion Multipurpose Project, Nepal
On April 16, 2019, the Prime Minister of Nepal and other government officials, contractor COVEC and Robbins gathered to celebrate the breakthrough of the first ever TBM in Nepal. The machine holed through months ahead of schedule after excavating in excess of 1,000 m per month.

The Robbins 5.09 m diameter Double Shield TBM bored through sandstone and mudstone, completing the 12.2 km long drive in 18 months.
Mumbai Metro Line 3, India
On April 18, 2019, the first of two 6.65 m Robbins Crossover XRE TBMs made its first intermediate breakthrough at the Mumbai Metro Line 3. The TBM completed its 1.2 km long tunnel drive from Cuffe Parade to Vidhan Bhawan station, and will now be readied for its second section on the 2.8 km lot.
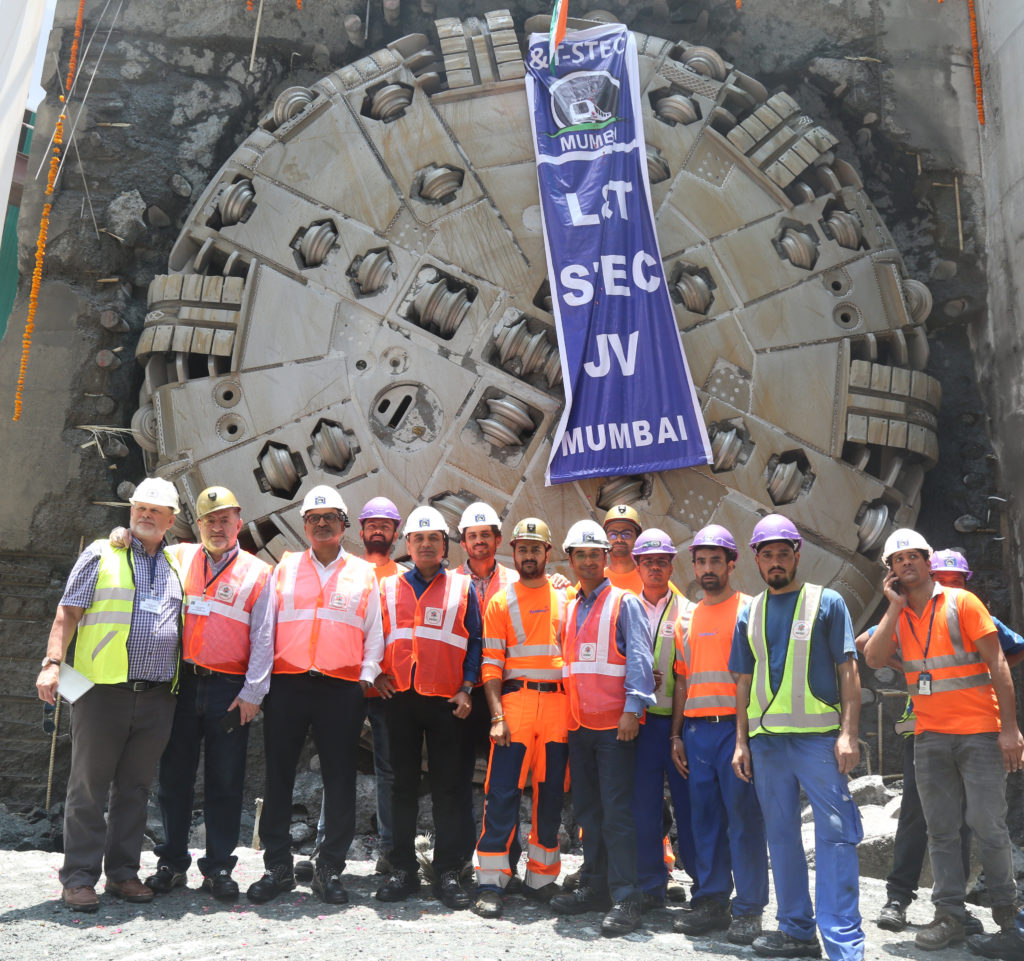
Contractor Larsen & Toubro-Shanghai Tunnel Engineering Co Joint Venture (L&T-STEC JV) celebrates the breakthrough of the Crossover XRE with Robbins personnel on April 18. Video and Photos: Nagarjuna R. Musikara, Robbins Field Service.
Los Condores HEPP, Chile
On April 25, 2019, a 4.56 m Robbins Double Shield TBM completed tunneling a 12 km intake tunnel for the Los Condores HEPP in Region del Maule, Chile. Contractor Ferrovial Agroman overcame challenging mixed face conditions and high water inflows to break through into an underground chamber. A second machine—a 4.56 m Crossover XRE TBM—will be launched to bore another section of tunnel later this year.
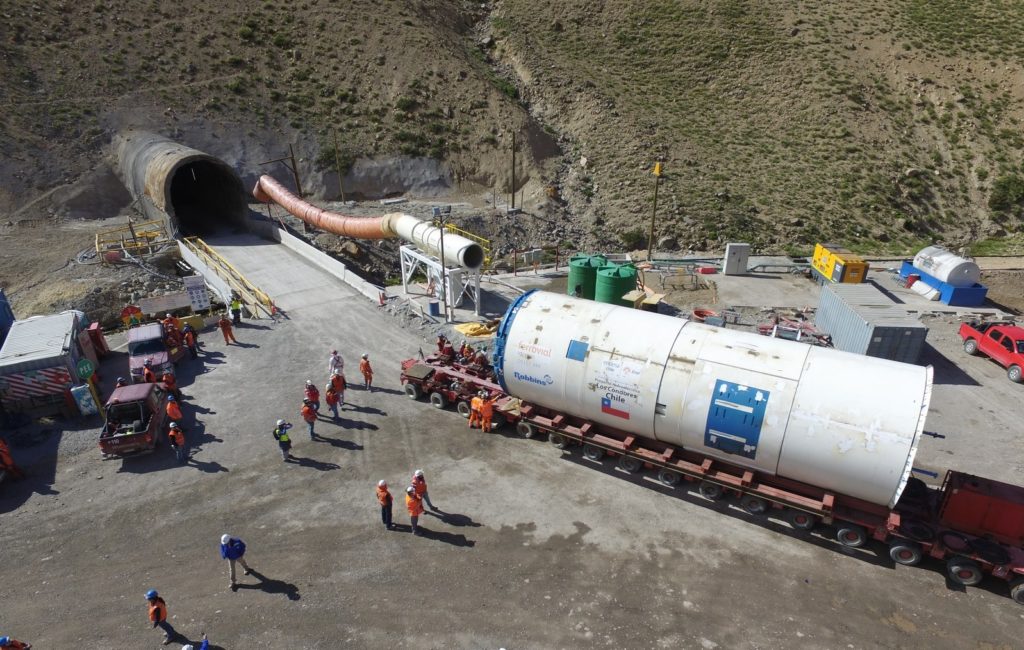
The Robbins Double Shield TBM, seen here during the launch, completed its 12 km intake tunnel on April 25.
A Brief History of Rapid Excavation in 7 Key Points
Rapid Excavation: It’s a term bandied about throughout our industry, but what does it mean? It’s considered by many to be the ultimate goal in TBM tunneling—machines that reliably complete projects on time (or early) with faster rates of excavation, regardless of conditions. However, speeding up a project schedule is not as straightforward as pushing a machine harder, working longer hours, or increasing your crew size. The issue is complex, and we’ve put together 7 key points to help you navigate it.
1. Consider the Entire Project Schedule
First of all, consider that increasing the excavation rate may not be the only way—and indeed may not be the best way—to speed up a project schedule. The generalized graphic below illustrates my point: TBM excavation often makes up around 25% or less of the total time to complete a public works tunnel. In fact this is a conservative value as by many estimations the total project time is often 15 years. Even if we were to increase the excavation rate by several times what TBMs are currently capable of, it wouldn’t significantly speed up project delivery.
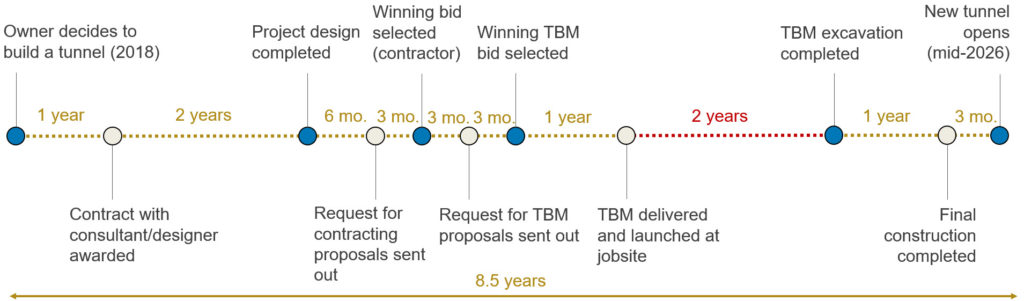
Figure 1. Generalized process of delivering a public works tunnel. TBM excavation show in red.
Shortening the decision-making process or the design and consulting process is much more feasible than creating a “super-fast TBM” and would have a bigger impact on the project schedule as well.
2. Know the Facts about TBMs
TBMs are fast, and they’ve been fast for decades. In fact, 50% of all known TBM world records were set more than two decades ago. Much of the seeming lack of progress is illusory–it has to do with the fact that modern tunnels are being built in ever more difficult geology, while more stringent health and safety standards put necessary limits on the excavation process, among other things. Today’s TBMs are capable of boring in harder rock, in higher water pressures, in mixed ground conditions and a host of other environments that would have been impossible in the 1970s and 1980s. And they do it while performing well; indeed, at much higher rates than conventional excavation. The below chart is a good illustration of just how far TBMs have come in recent years.
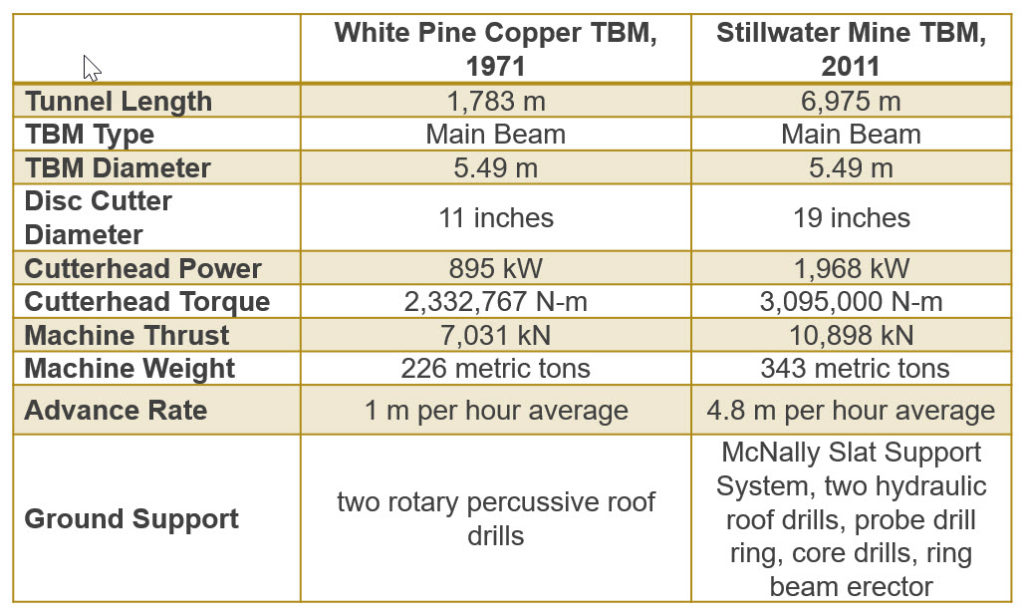
Figure 2. The long way that TBMs have come since the 1970s.
3. Know That Productivity Has Vastly Improved
There have been some recent articles looking at decreasing productivity in the construction industry overall, such as this article in The Economist. While the productivity of the overall construction industry is up for debate, productivity is not decreasing in the tunneling industry. Moreover, productivity is incredibly reliant on each project’s limitations and requirements. When considering productivity, think about logistics, geology, and data.
Based on decades of field data, we’ve found that a typical TBM heading is two to three times faster than a drill & blast heading. This effect is more pronounced the longer the tunnel drive, and more than makes up for the typically longer lead time to acquire and mobilize a TBM.
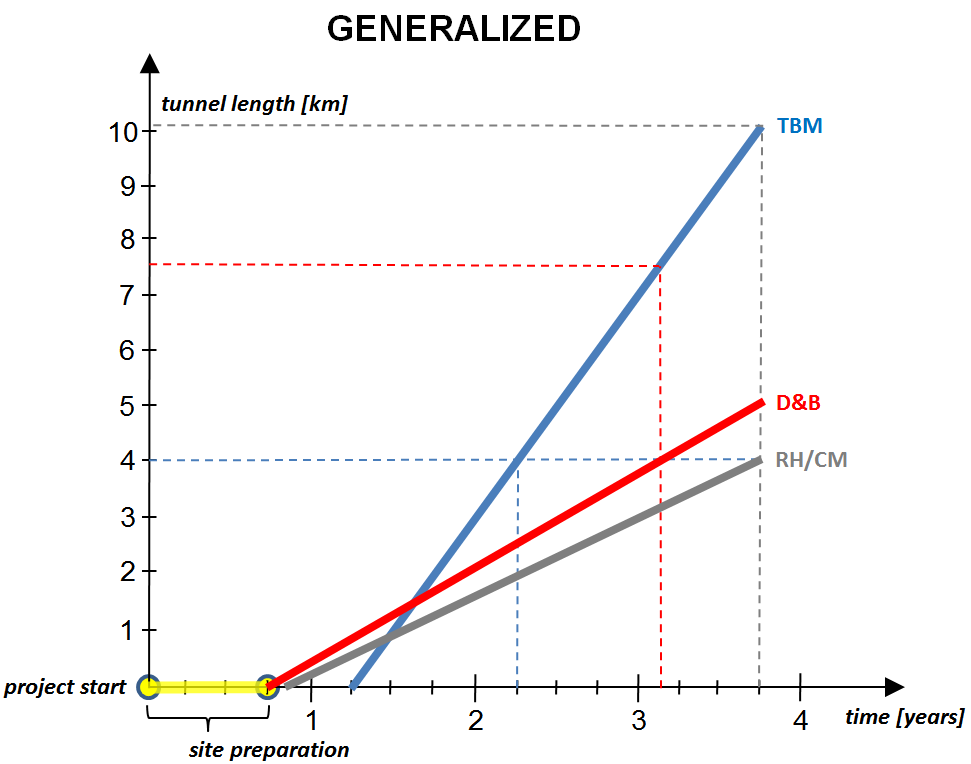
Figure 3. TBMs are two to three times faster on average than drill & blast and multiple times faster than a roadheader.
So it’s safe to say that TBMs are the way to go for more productive tunneling in all but the shortest tunnels. Logistics is the other key: scheduling of crew and materials, particularly in long tunnels, is so important. This is doubly so if using muck cars. For this reason, using continuous conveyors for muck removal is more efficient, as the removal process does not need to stop for personnel and material movements. In fact at least 75% of all TBM world records were set while using a continuous conveyor for muck removal.
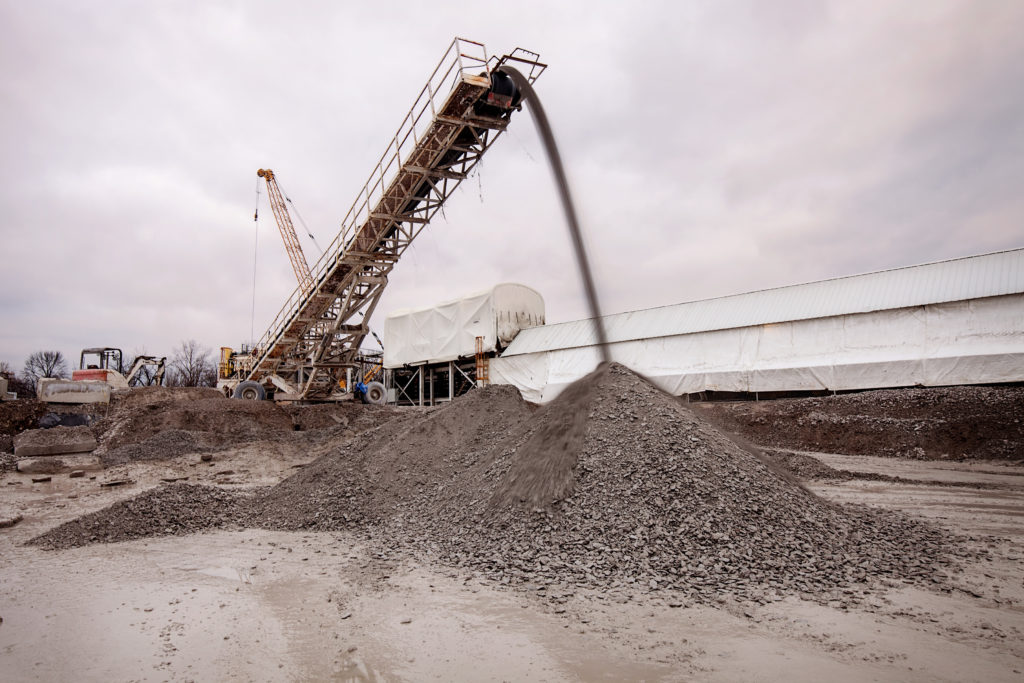
Figure 4. Today’s conveyors are capable of hauling 1,800 metric tons per hour or more.
Lastly, consider geology when planning the construction schedule. Even a customized machine with streamlined logistics will bore more slowly in fractured volcanic rock with significant fault zones than in competent sandstone. Setting the excavation schedule requires a close look at geology and the excavation rates of recent projects in those conditions.
4. Identify the Bottlenecks
The bottlenecks must be identified and alleviated if productivity is to be increased. Think about the operations that can be done simultaneous with boring that are now done separately:
- Applying a Concrete Lining: Continuous concrete lining can be done concurrent with boring in many cases. This type of lining eliminates the separate operation of lining a tunnel with segments. Waterproofing membrane can be applied with a membrane gantry if needed
- Increasing Automation: Processes such as cutter changes and segment erection can and are being fully automated on research projects in the industry. Full automation could significantly reduce downtime
- Eliminate re-grip time: When setting segments and thrusting off rings, elimination of re-grip time could be key to increasing advance rates. New innovations such as helical segments are promising to do this through a simple change in segment architecture
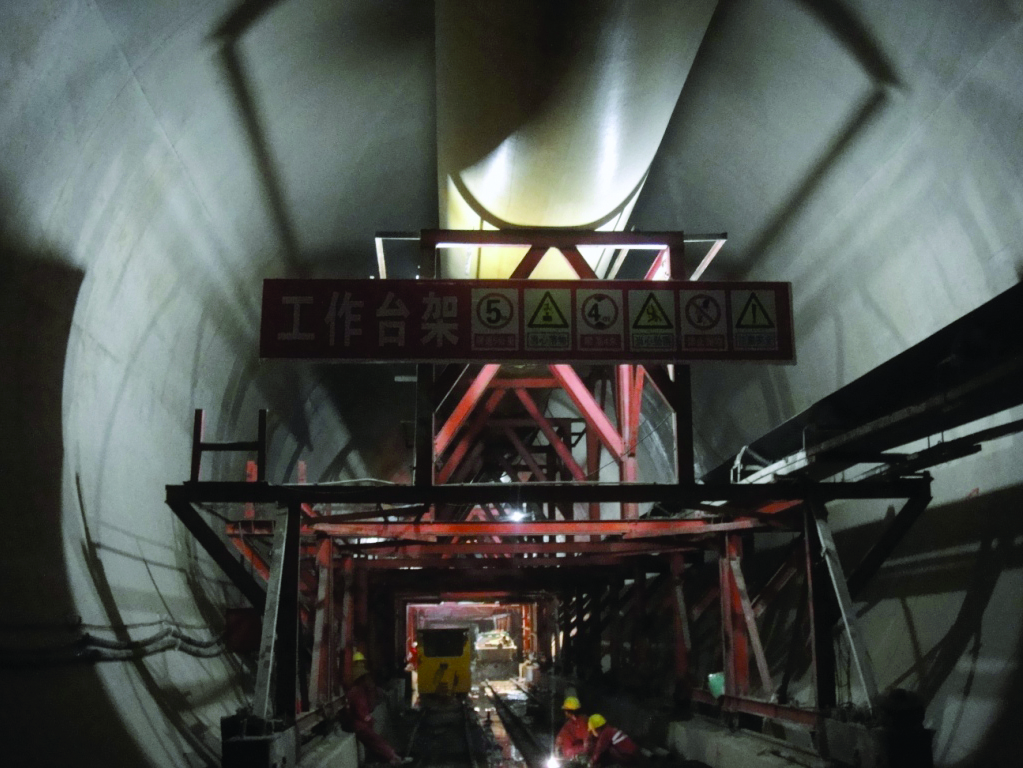
Figure 5. Continuous concrete lining applied behind a Main Beam TBM.
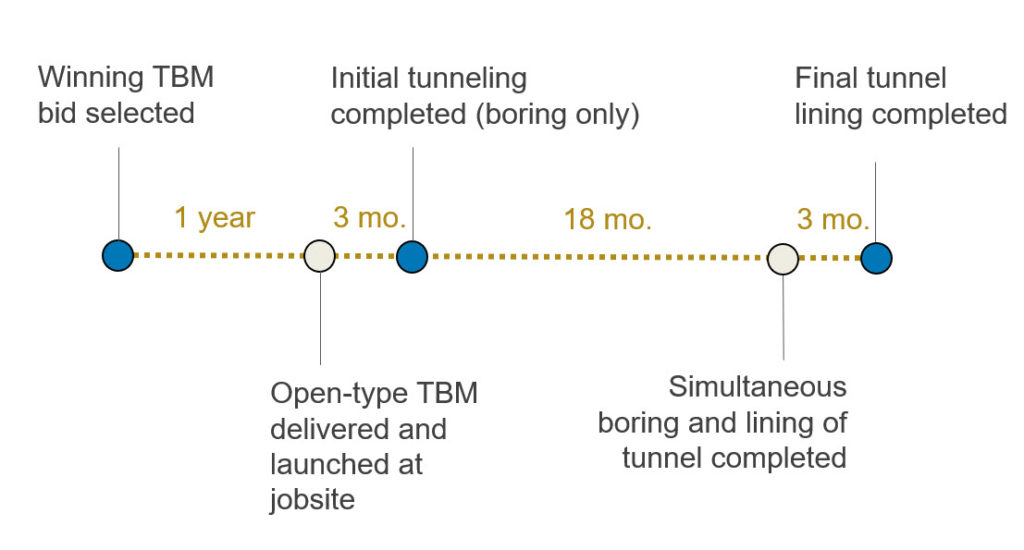
Figure 6. By boring and lining the tunnel simultaneously with a final, continuous concrete liner, a substantial amount of time—perhaps six months—could be shaved off of the excavation schedule (as compared to previous example that showed two years’ excavation time).
5. Understand the Limitations
There has been talk in our industry of making TBMs excavate up to ten times faster. While this is all well and good to aim for, in many cases it may not be realistic. For example, when boring in soft ground using EPB TBMs the penetration rate is limited by material flow and additive permeation. Boring at faster rates could cause heave in front of the TBM followed by subsidence at the surface.
So how could we bore faster in softer ground? It would require a change in the mechanism of excavation—no short order. It would require a better way of holding pressure than the screw conveyor can currently achieve. This is just one of many examples where physical limitations are the barrier to speed, not efficiency.
6. Think Outside the Circle
The possibilities for tunnel construction in the future are intriguing. Consider non-circular tunneling machines, of rectangular, square or other shapes. How much efficiency could be gained by creating a tunnel that requires no back-filling or invert segments to create a flat tunnel invert? Robbins has been exploring these types of machines for decades, with machines such as the Mobile Miner, seen here.
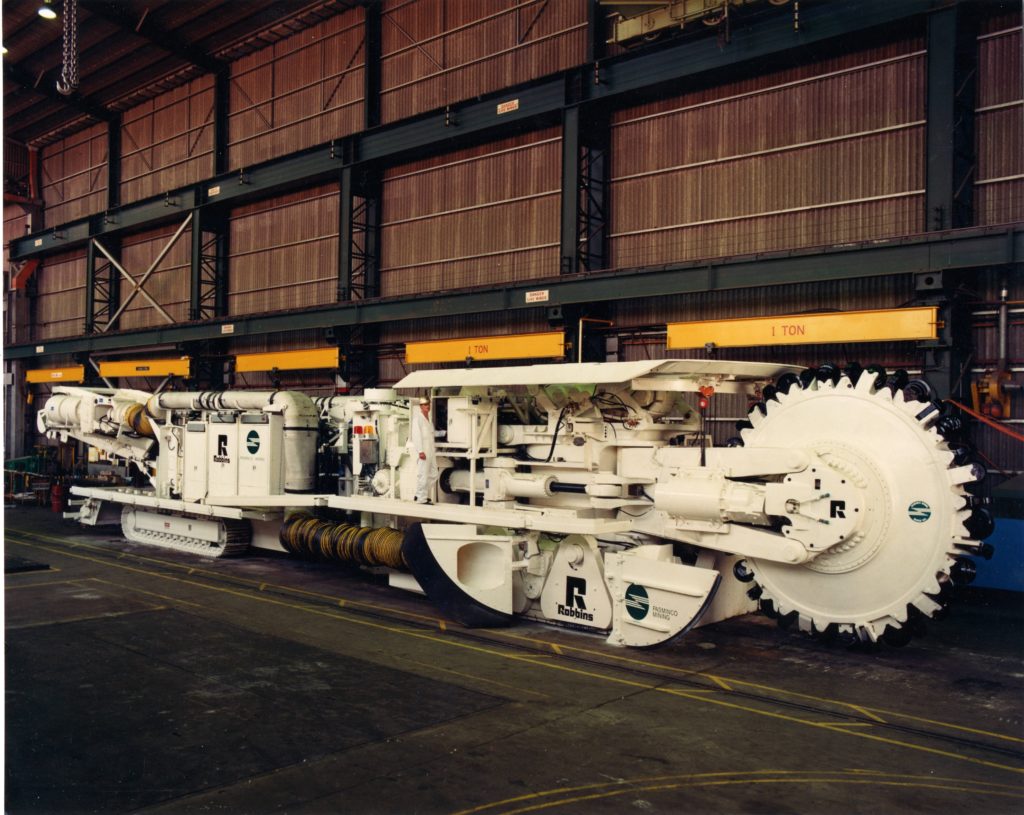
Figure 7. The Mobile Miner was developed in years past to bore non-circular tunnels.
7. Promote Industry R&D
Lastly, there are things all of us in the industry can do to advance technology towards faster and safer tunneling. R&D in our industry is necessarily incremental as technology must be tested for safety and efficacy. But the rate of advancements could be sped up with better funding and closer cooperation between owners, consultants, contractors and TBM suppliers.
Namaste Nepal: How I Learned to Live with Less and Appreciate Tunnels More
In Nepal, the greeting ‘Namaste’, while pressing both palms together in front of the chest, signifies both ‘hello’ and ‘goodbye’. It implies a circular concept of time that I rather like—I certainly think I will be coming back to this country of high mountains, valley forests, and yes, tunnels.
The Adventure Begins
When I first learned that I would be visiting Nepal to see a swift-moving tunnel project making an impact in a local community, I was pretty jazzed. I also took it upon myself to overpack. The Bheri Babai Diversion Multipurpose Project (or BBDMP for short) is a 12 km long tunnel that travels below protected forest considered part of the Bardia National Wildlife Reserve. This is an area home to tigers, rhinos, Asian elephants, leopards, and more. And, most worryingly for me, mosquitoes.

The BBDMP portal. Note the trees: perfect mosquito territory.
Mosquitoes love me. I’m not entirely sure why they love me so much, but let’s just say that if there’s a mosquito within a 2 km radius it will find me. Thus, I decided to be prudent and go all out when packing. I purchased a whole new set of safari clothes, the most potent bug spray I could find in copious amounts, and much, much more. I stuffed everything into two suitcases and set off on my journey.
A full 24 hours of traveling later (the journey from Seattle, USA to Kathmandu is no joke, folks), and I arrived in the Kathmandu airport…with no checked luggage. Through a gross miscalculation (what a way to learn a lesson!) I also had not packed hardly anything in my carry-on bag. I had no clothing with me, and more importantly, no bug spray. What was I to do?
Rolling with It
After discovering that my bags were several days away, I decided to forego any hope of reuniting with them during my trip. Instead, I rolled with it. After a one-hour local flight from Kathmandu to Nepalgunj, we arrived at our destination. Nepalgunj is a frenetic, dusty town located around 8 km from the Indian border and one hour from the BBDMP site. The culture is heavily influenced by India, and we had many meals of delicious spicy curry and fried bread. The streets were lined with small shops and marketplace stalls, but to my dismay, no department stores.
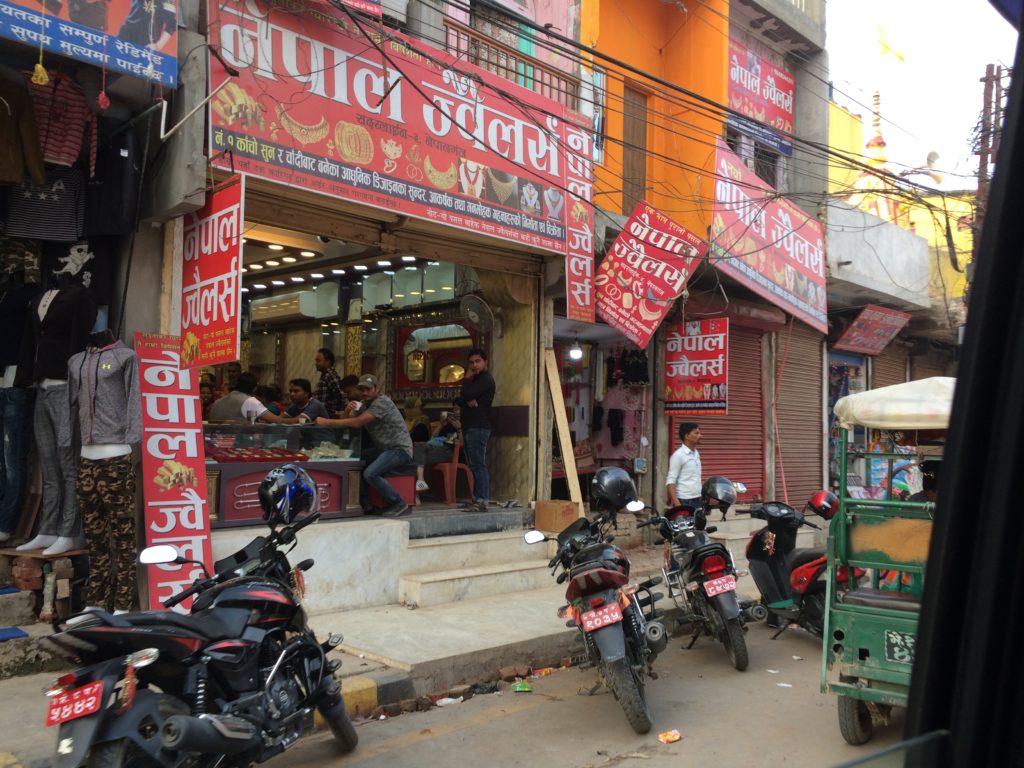
The crowded marketplace in Nepalgunj.
After a quick Google search my coworkers and our guests with us for the site visit headed to the nearest approximation, known as Rani Mart (Rani means ‘queen’ in Hindi). To my surprise, I purchased a whole new wardrobe and everything I needed for 1/10th of the price I would have paid for it in the U.S. (though the sizing on the tags was quite a bit larger!) I was feeling very pleased with myself.
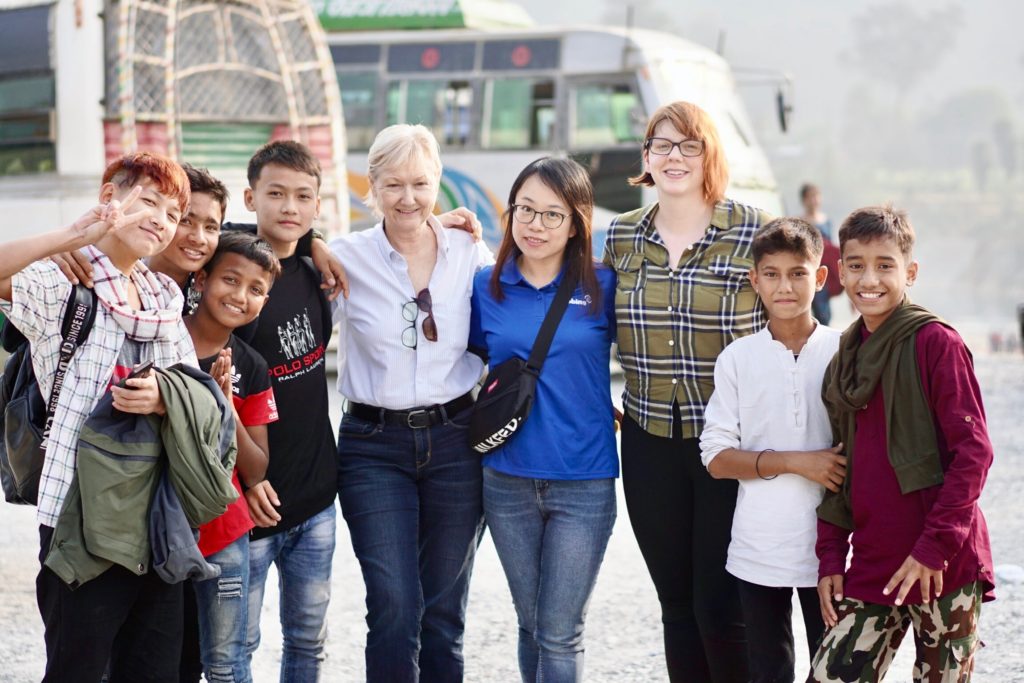
We took pictures with the local kids next to the BBDMP site. I’m the one rocking the green plaid shirt—the latest fashion from Rani Mart.
A Little Perspective
The next day we were ready to visit the jobsite. I couldn’t help but notice the rolling blackouts that plagued the city and the vast stretches of farmland requiring huge water resources. The people in the surrounding area make do with limited resources in ingenious ways—I was intrigued to see, for example, that every outlet requires you to flip an on-switch before the current becomes available. Perhaps we Americans could save significant energy if we made a setup like this a national standard. Local hotels, including one we stayed at, use solar panels for their power and air conditioning, and harvest rain water in order to reduce their usage.
All of this made me realize how much the BBDMP will impact the surrounding areas. This was confirmed in a meeting we had with Nepal’s Department of Irrigation (DOI), the project’s contractor China Overseas Engineering Group Co. Ltd. (COVEC), and consultant Geodata. The tunnel is sourcing water from the Bheri River to the Babai River, traveling through mountainous Himalayan geology known as the Siwalik Range. The water, as the project’s name suggests, is for multiple purposes. The estimated annual benefit in Nepalese Rupees is $2.9 billion for irrigation, and $4.3 billion for hydropower, making a total of $7.2 billion in benefits once the project becomes active.
The completed tunnel will irrigate 51,000 Ha of land and provide 48 MW annual generating capacity. That’s not to mention the environmental benefits: The Babai River currently swells each monsoon season and then runs extremely low in drier seasons. It is connected directly to the groundwater table, which is being aggressively depleted. With a regulated flow during all seasons, the groundwater table will see less depletion year-round.
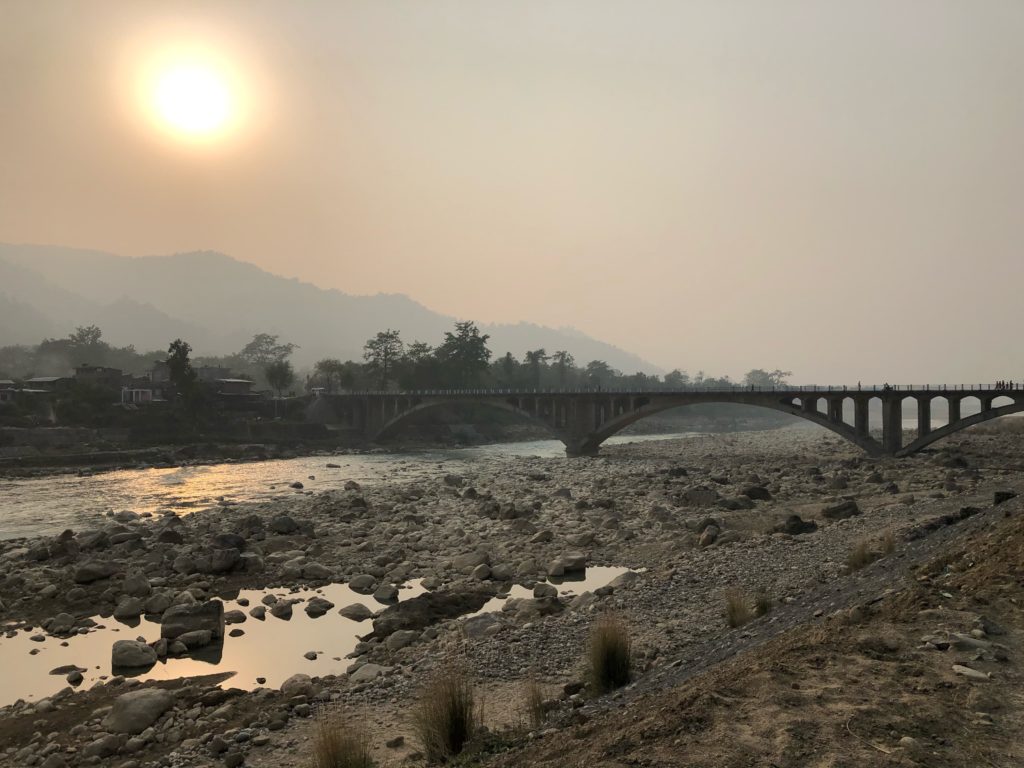
We crossed the Babai River on the way to the jobsite, seen here at low water levels.
The impact, in other words, is huge. Learning all of this made my obsession with my missing luggage seem inconsequential in comparison. I had my bug spray and some clothes. That was all I needed.
The First Nepalese TBM
With such a landmark project for the region, its proponents were willing to look to the latest technology during the planning phase. Our local representatives, MOSH Tunnelling, had been working since the 1990’s to bring a TBM to Nepal, a country known for its Drill & Blast tunneling. While TBMs had been considered multiple times, each time conventional tunneling had been chosen.
When the BBDMP was fast-tracked as one of the country’s “National Pride Projects” feasibility studies showed that Drill & Blast excavation could take as long as 12 years. The DOI needed a faster option, and they found it in TBMs. They began working with MOSH Tunnelling and Robbins to bring what would be the first Nepalese TBM ever into the country—a 5.06 m diameter Robbins Double Shield. The process for the DOI to acquire funding for the project and select a contractor through international competitive bidding took seven years, spanning from 2007 to 2015, when project commencement officially began.
Fast forward to our site visit in November 2018 and the project is far exceeding expectations. Tunneling has topped out at 1,202 m in one month with an average of around 740 m per month. The knowledgeable COVEC team have traversed a major fault zone, the Bheri Thrust, with no problems, and overcome a stuck TBM shield with a bypass tunnel constructed in just five days. Overall, the TBM is far ahead of schedule and the results are of national importance.
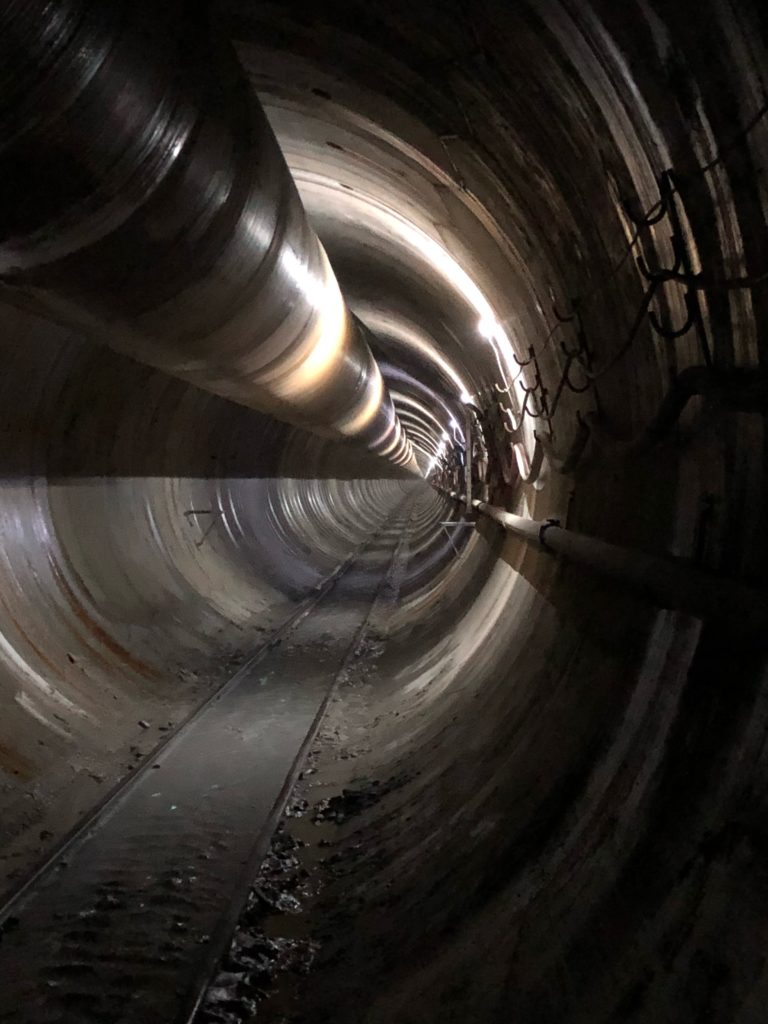
The tunnel is lined with hexagonal segments for rapid excavation.
The local community, national media, and government are all watching how the TBM excavation plays out at BBDMP. Given the strong performance, they are now considering TBMs for a host of future multipurpose water projects. It’s the kind of result that opens up a whole new marketplace.
Into the Forest
After a great site visit, we chose to relax for one day at a spectacular local lodge that offered jeep safaris into the Bardia Wildlife Reserve. Currently home to nearly 90 tigers (a number that is rapidly increasing through conservation efforts) we were hopeful of perhaps seeing one of the striped cats in the forest. Our guide was knowledgeable, our jeep sturdy and our driver adept as we traversed bumpy roads and forded a few streams on our safari drive. We saw mischievous macaques, tree-dwelling langurs, a host of brightly colored birds, and various deer. We saw several enticing tiger prints…but the tiger itself remained elusive. Obviously, this means that I must go back!
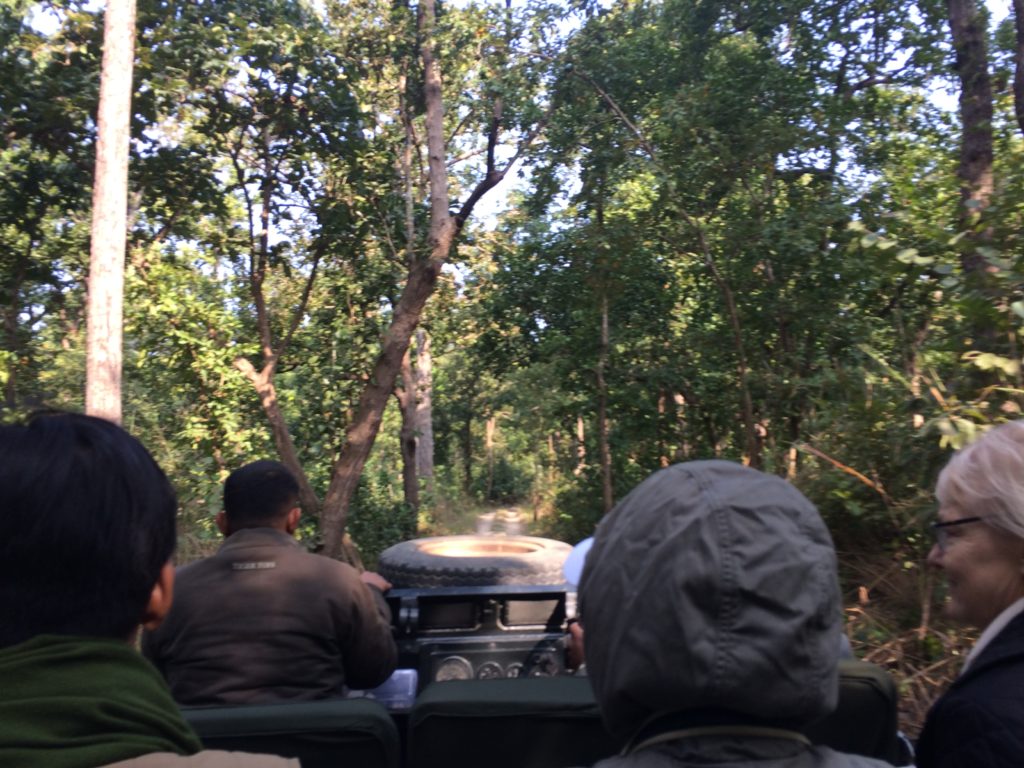
Over the river and through the woods…
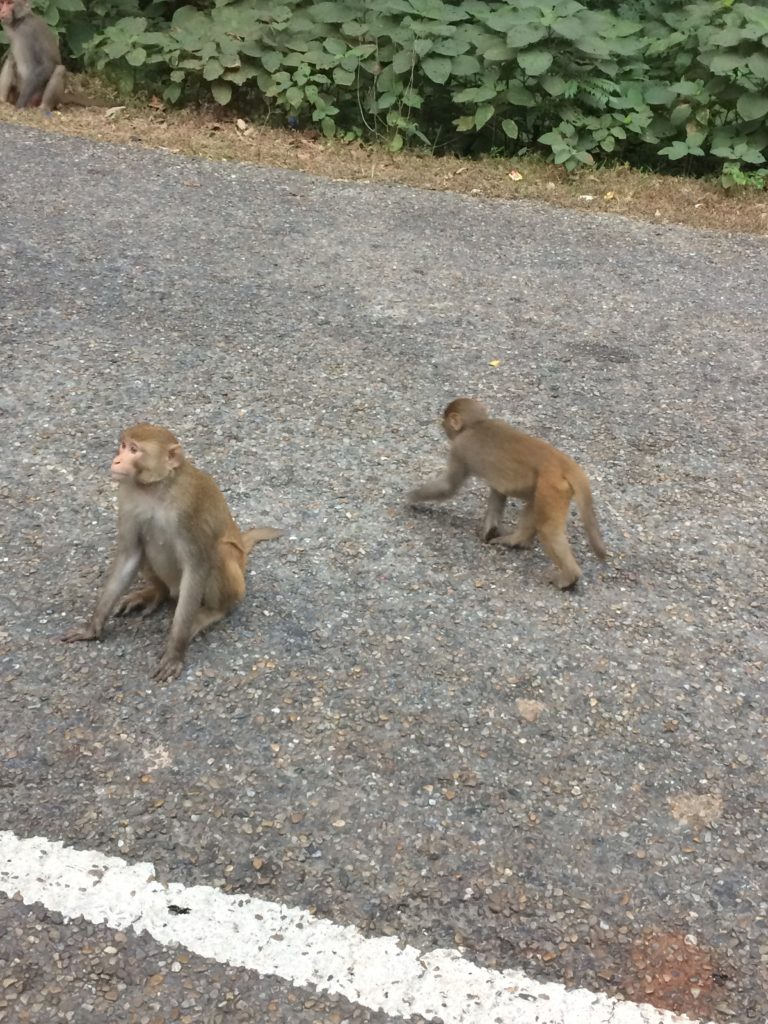
…past mischievous macaques waiting for food from tourists…
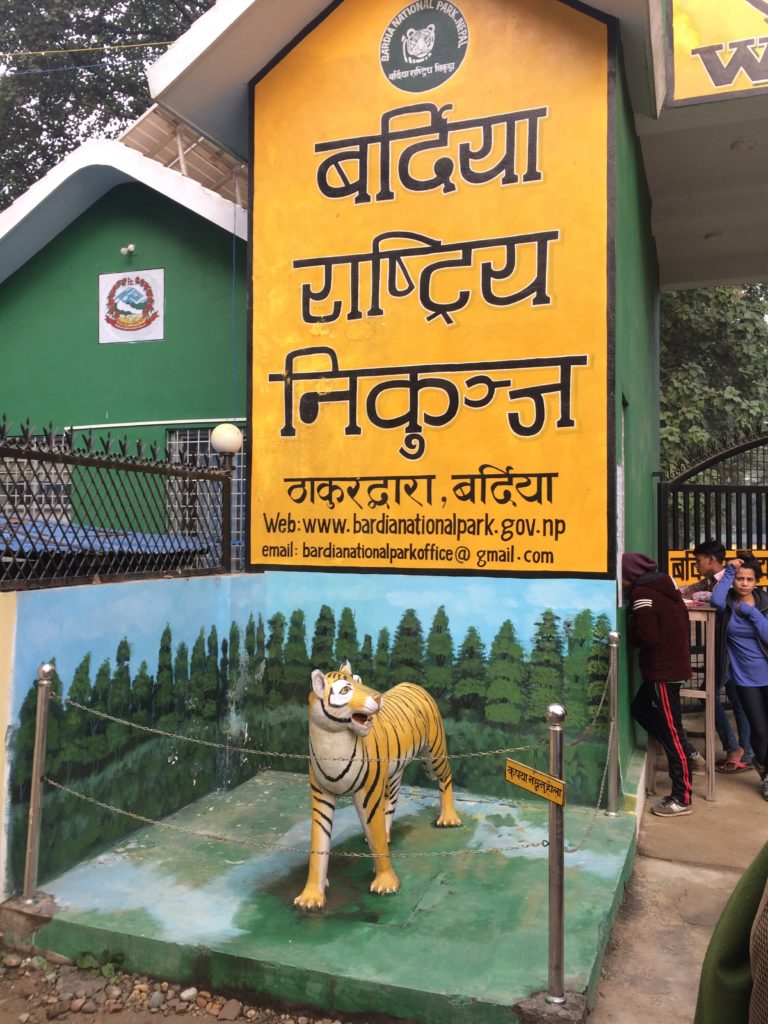
…we spotted our one and only tiger for the day.
A Lesson Learned
After traversing a tunnel, traipsing through the forest, and some swift sight-seeing in Kathmandu on our last day, I felt I had come full circle. I was ready to head home, but with an eye towards future opportunities to return to Nepal, whether for business or vacation. I will be back. But next time, you can rest assured, I will only bring what I can fit in my carry-on.
Fueled by Vietnamese Coffee: My Epic Adventure at Thuong Kon Tum
Traveling in the tunneling industry is basically a regular commute for some. A lot of us don’t think twice about the destination, we just do it with a mission in mind. My mission as Robbins Marketing Manager was this: a small conference in Ho Chi Minh City. Okay, easy! As the date approached, about a month before, I kept hearing about how well our Main Beam TBM was doing in Vietnam, at the Thuong Kon Tum Hydroelectric project, despite a gauntlet of challenges. I talked to some project engineers and field service personnel who told me it was in a remote location in Kon Tum Province. And then I heard more about traveling to that site: a 6-hour drive from Da Nang, through nauseating windy, narrow roads, climbing elevations with no speed limits to speak of. But that’s cool, I thought, glad I don’t have to go on that ride.
“Wait, why not just go to the jobsite for a video and photo shoot? We can have it ready for the breakthrough in October,” says Desiree Willis, Robbins PR manager a couple weeks later. What!? A few days after that, it was all planned. Ron, our videographer, Ken, our photographer, and Keri Lin, our marketing manager from Robbins China, set off with me on a last-minute adventure. The 17.4 km long Thuong Kon Tum HEPP tunnel will be the country’s longest once complete. A 4.5 m diameter Robbins Main Beam TBM and continuous conveyor system were supplied to bore a section of the tunnel.
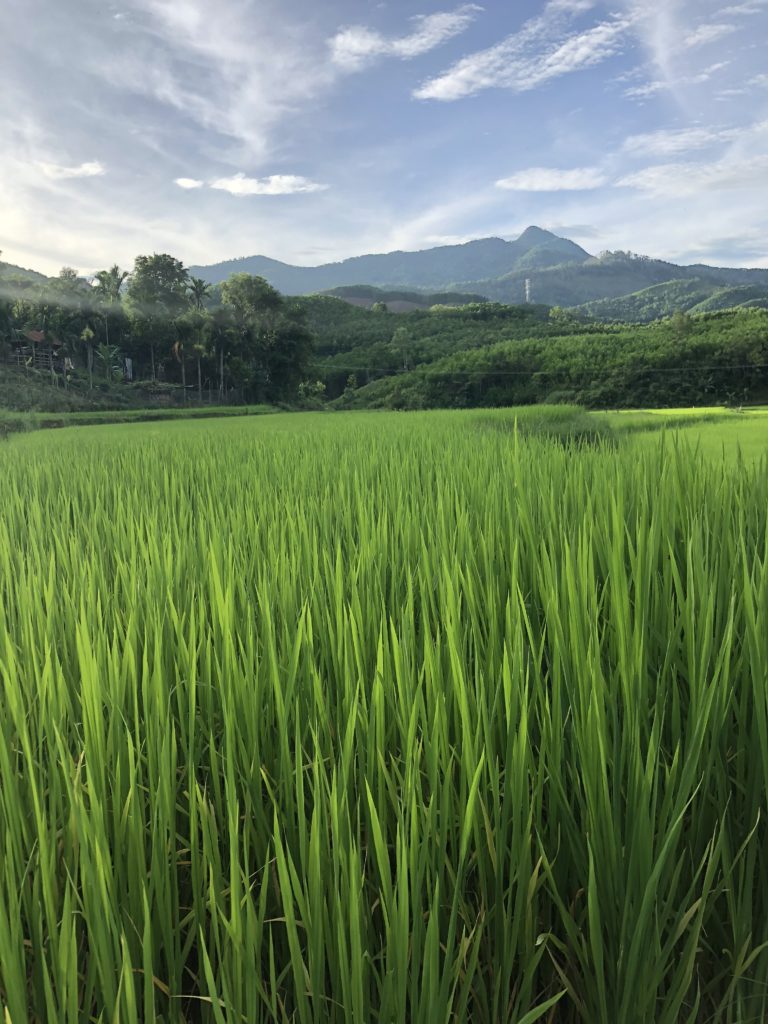
A terraced rice paddy with a beautiful mountain backdrop, so typical of what is synonymous with the sights of Vietnam.
Maybe because I was bracing myself for the worst as far as the drive goes, I didn’t feel like it was that bad. The scenery was jaw dropping with lush jungle, rice paddies and scenic villages, and so many distractions on the sides of the road that I just completely avoided looking ahead. Problem solved! The coolest distractions were the scooters driving on these mountain roads: what they were carrying, how many people were on them, their driving technique. My favorite site was seeing a whole family of people—a 5-year old kid in the front, the dad driving, the mom in the back and a toddler sandwiched in between the parents—on a run-down 125 cc scooter. Then there’s the animals: a litter of stray dogs, adorable black piglets making road crossings that almost made me swear off bacon, herds of cows, goats, etc.
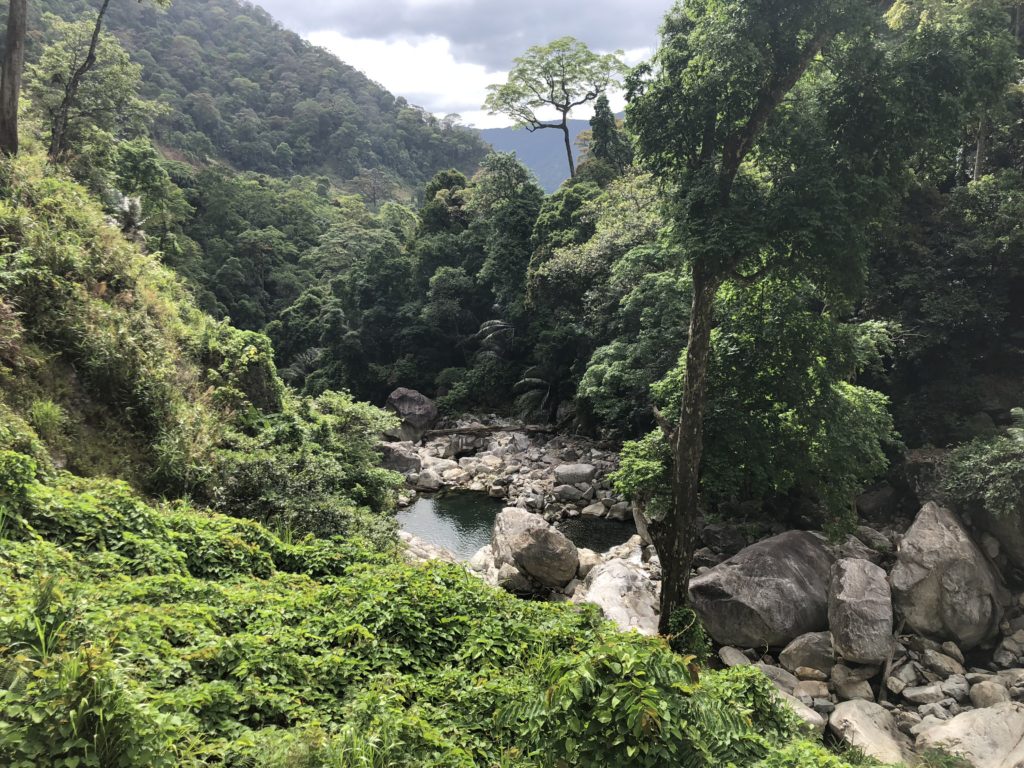
This was about a half hour away from the jobsite in Kon Tum province. The picture doesn’t truly depict how beautiful it was in person.
But how the heck did they get the machine, assembled by Onsite First Time Assembly (OFTA), to the site? Apparently, the previous contractor built portions of the roadway to the jobsite while components were staged at the port site. Several bridges, previously built only for light traffic with scooters and carts, were rebuilt or reinforced in order to carry the heavy TBM components. In a road conditions survey report by logistics firm SDV Vietnam Company Ltd., the original bridges were described as “having no shoulder”, and as having “blind corners and sharp curves”. The OFTA process allows a TBM to be assembled on location, saving time and money in terms of shipping costs and project schedule. The machine had successfully made it to the site, as it had launched in 2012.
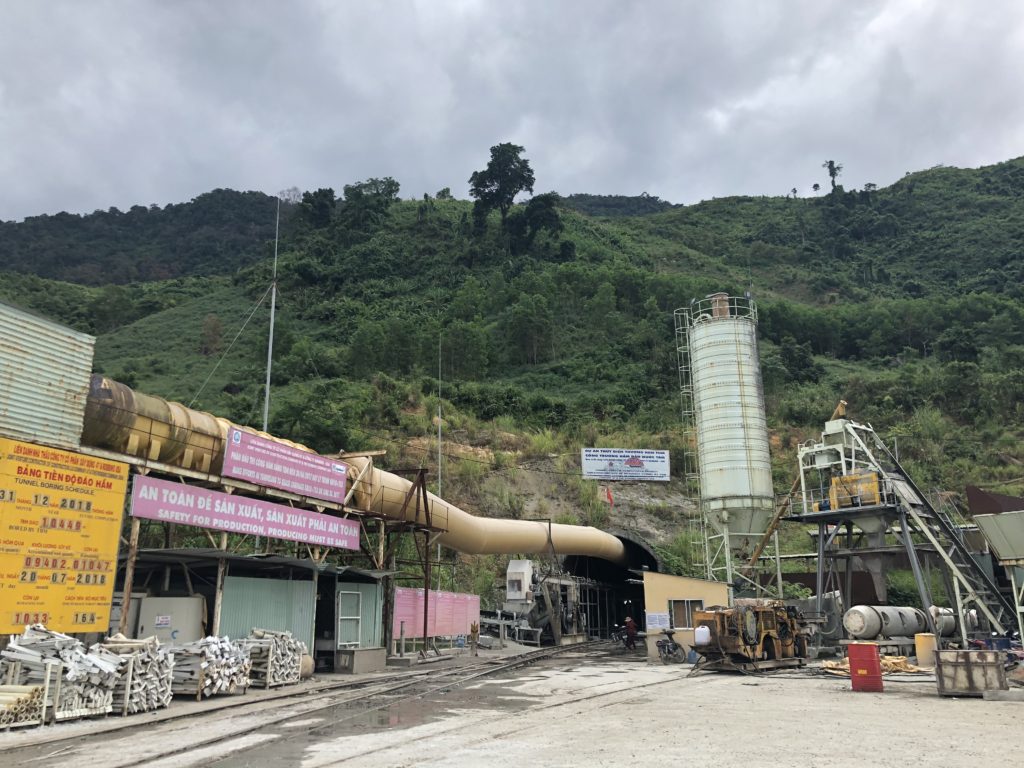
Not pictured: the litters of stray dogs and chickens roaming around the jobsite. Oddly enough, I never saw any stray cats here.
Upon arriving at the jobsite, I was immediately impressed with the site and the surroundings, especially after hearing about all of the challenges the project had back when the TBM was launched, under a different contractor. The TBM launched into complex rocky conditions that turned out to be quite different than in the original geological study. The machine sat abandoned 2.6 km into the tunnel with equipment sitting idle for months, waiting for a change in circumstances. In 2015, Robbins signed a contract with the project’s new contractor CC47 to supply full refurbishment and to operate the equipment with a full Field Service team. Since then, Robbins Field Service has generally been kicking butt.
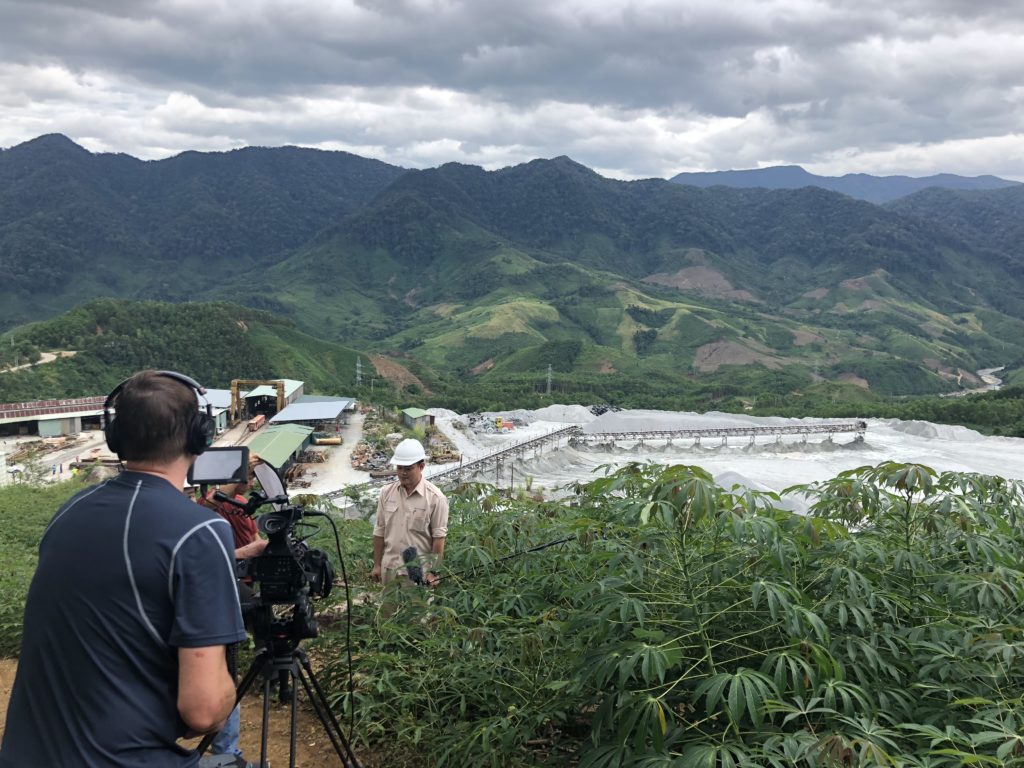
We hiked up a mountain to get this panoramic shot of the project site. I think it was worth it!
The machine was running as expected, so filming interviews and the machine went smoothly. I learned a lot from the interviews, mainly from the Robbins guys we interviewed—PN Madhan, Robbins Engineering Geologist, and Greg Adams, Robbins Field Service Manager. “It’s a workhorse of a machine and still in great condition, considering all of the difficult ground it’s been through,” Greg mentioned. Massive granitic rock wasn’t the only challenge they faced—the team also endured a handful of major fault zones requiring rock bolting and the use of the McNally Roof Support System, as well as some huge water inflows.
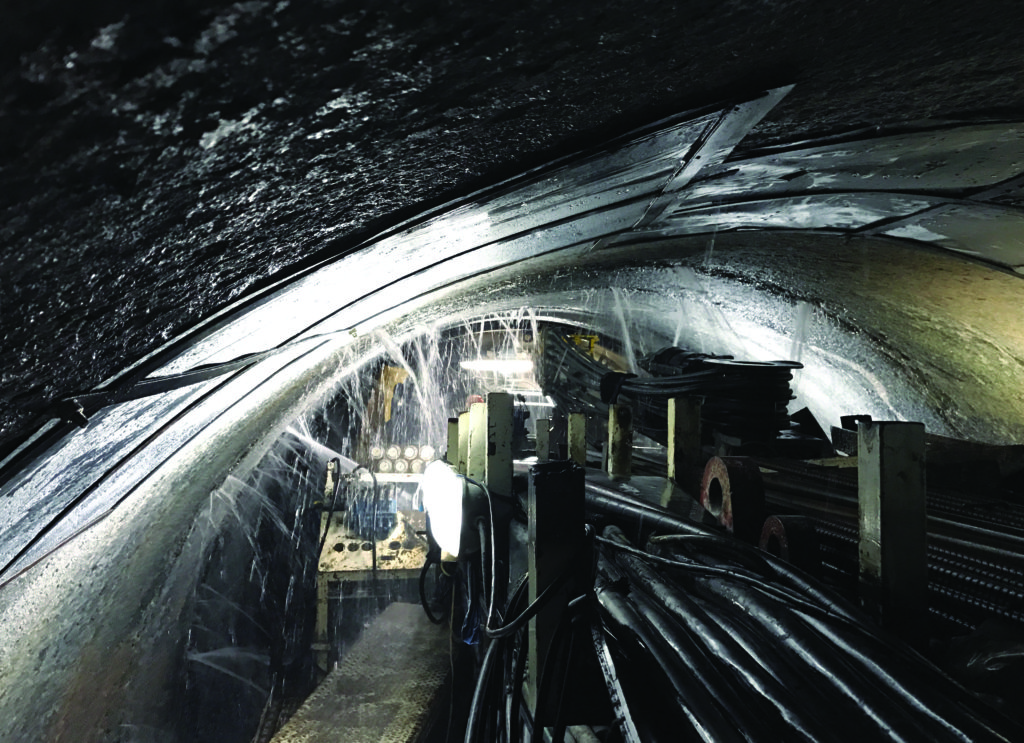
Water inflows were up to 600 liters per second—that’s nearly enough to fill an Olympic-sized swimming pool every hour!
Greg did warn our photographer and videographer that they were going to face heat with extremely high humidity. When John McNally, Robbins Field Service Manager-Asia, took over the project site, he managed refurbishment of much of the equipment inside the tunnel along with the camp’s living quarters. This included adding a ventilation tube, keeping the tunnel at a cool 34°C. That’s the temperature AFTER installing the ventilation. Read more about the challenges here.
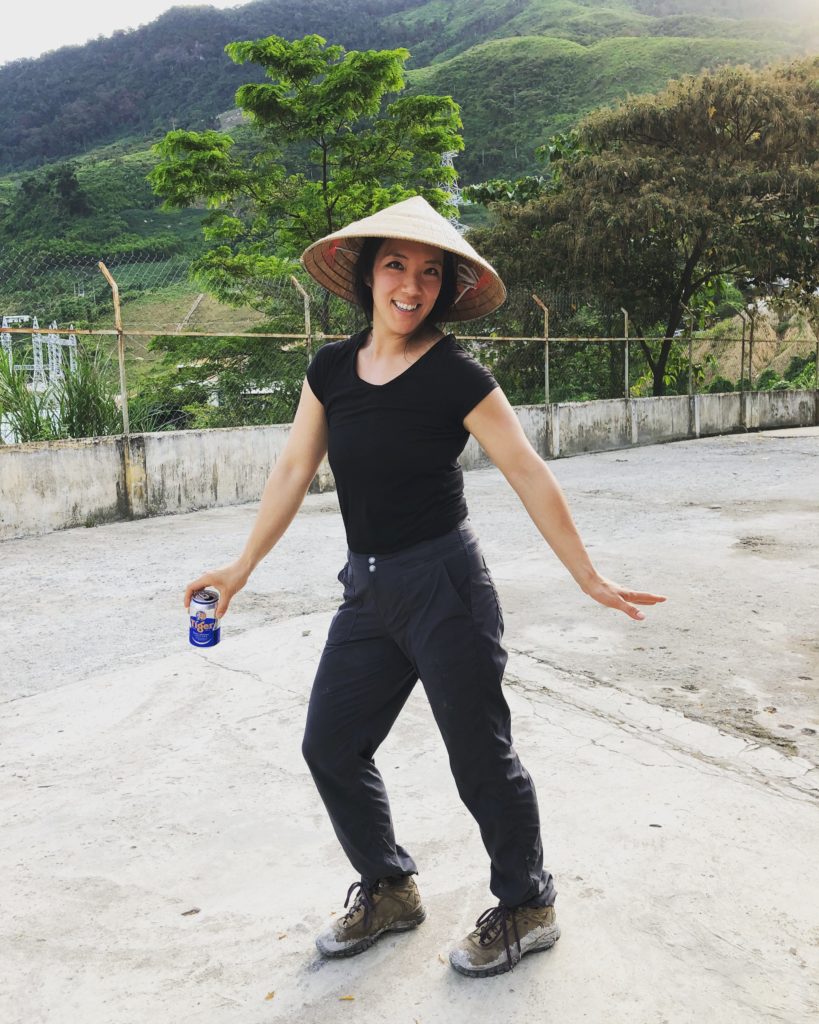
While waiting for dinner, I got posing tips from Keri Lin and our photographer for my next career as an Instagram model. A refreshing beverage and the typical Vietnamese farmer hat were absolutely necessary for the scorching hot day at the site.
The crew at the camp quarters, and the jobsite in general, were very welcoming. Greg and Taylor Hwang, Robbins project manager, arranged for a special dinner just for us on the first night—steak and French fries, an American staple! The crew on site mainly consists of English-speaking expats, Chinese, Thai, Vietnamese, Indian and Philippine guys, so the cuisine varied every day. We hung around that night for a while, listening to stories from some of the field service crew. This is while we were fawning over the pet falcon that one of the field service guys owned. I think the falcon liked living there, because his string wasn’t even tied to the perch at one point. Taylor told us that there were some families and children of the crew living there, who had to find ways to pass the time in this little remote village. He even told us they had pet monkeys at one point. I peeked into a living quarter and saw a drum set made with those Danish butter cookie tins that you get at Christmas. That’s one way to pass the time! Before we were about to leave, some of the Thai people at the site had brought in a bucket with a cover over it. I was curious and went to take a peek, because they started adding salt to the buckets. It was about 30 river snakes (possibly river eels, but they called them snakes) writhing violently because of the sodium touching their skin. Then they started preparing them one-by-one, sticking a nail into their heads and gutting them. It was quite mesmerizing, really.
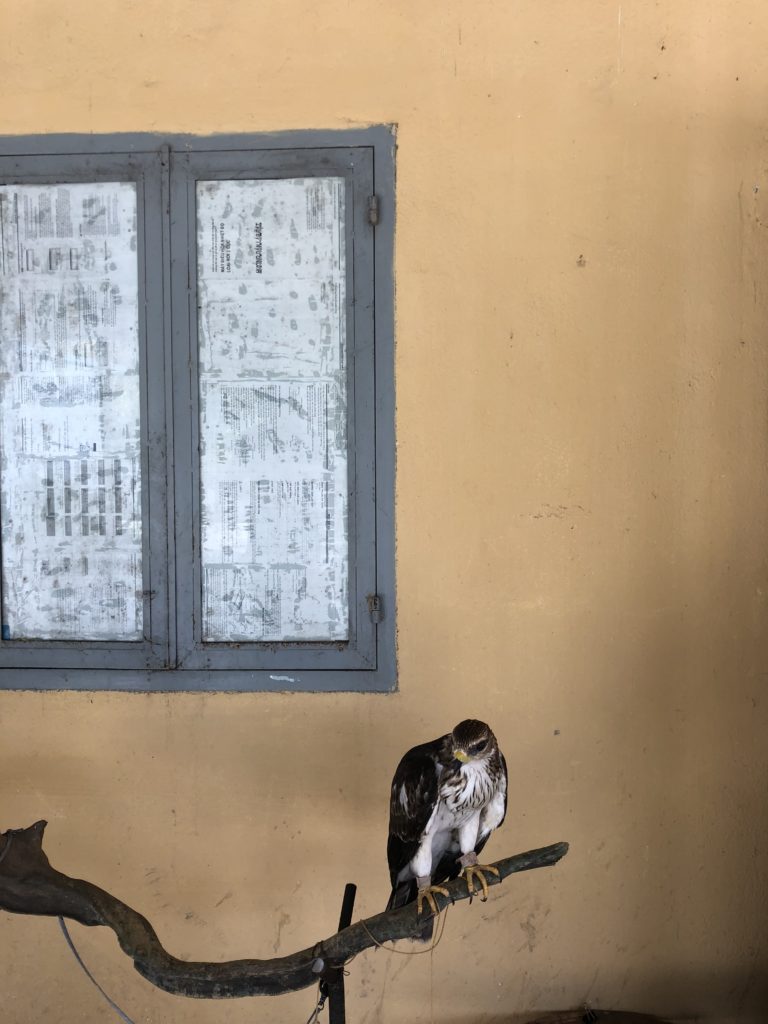
The camp’s pet falcon.
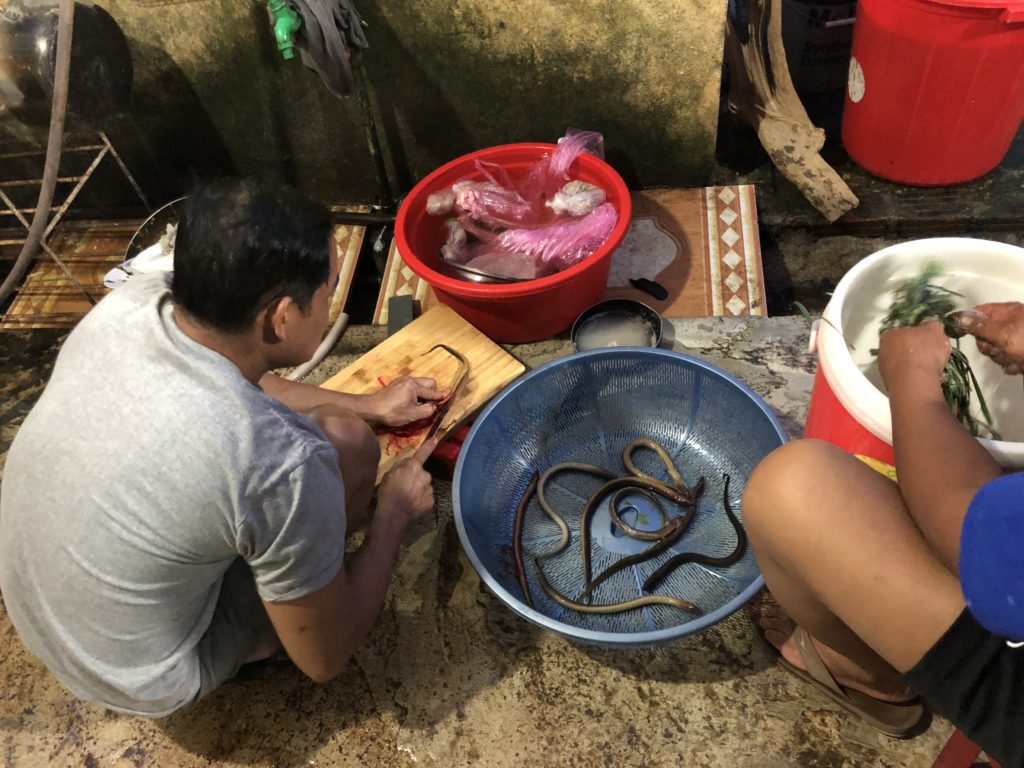
Not sure if this is the regional cuisine but the snakes were caught at a river close by the camp.
We only had two full days of shooting video and photos. Before the 6-hour drive back to Danang, all of us got caffeine-drunk on two strong Vietnamese coffees served with condensed milk each. I suspect it’s the perfect combination of the tenaciously strong espresso dripped into a puddle of pure sugar syrup (condensed milk) that singlehandedly causes adult ADHD from the first sip. During the drive down (which was much worse, I didn’t realize how much elevation we climbed going up), we were already reminiscing about the stories and experiences shared at the jobsite. When talking to the field service crew, they were all excited for the coming breakthrough later this year, but it seemed they were just a bit melancholy too. They were at this site for years, in a tiny remote village in the mountains of Vietnam, building friendships and routines. With only a handful of meters left to go on the tunnel, they’ll soon be off to the different parts of the world where they came from. I’m fortunate to have experienced everything I did on this trip and can’t wait to come back to this beautiful country.
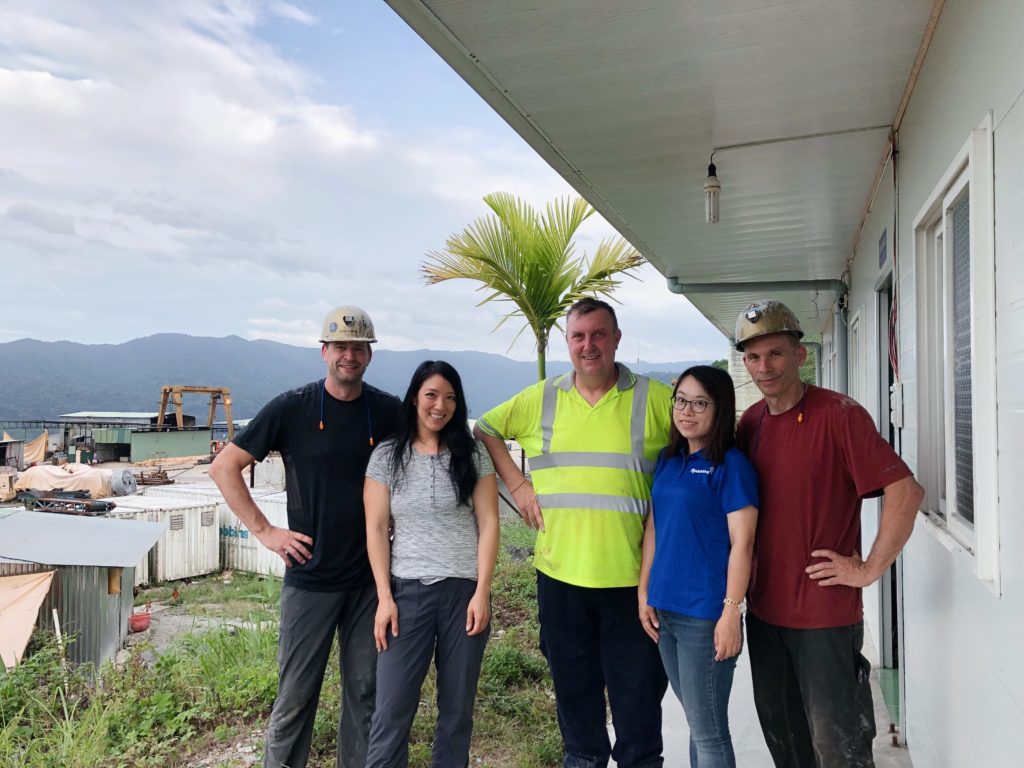
(From left): Ron (videographer), me, Greg Adams (Field Service Manager), Keri Lin (Marketing Manager for Robbins China), and Ken (Photographer) at the end of the shoot.
What's Going On? A Worldwide Roundup of Robbins Jobsites
At any given time, Robbins TBMs are operating at dozens of jobsites around the world. Our dedicated Field Service personnel take video and pictures of the TBM progress often, so we’ve decided to offer a periodic roundup of what’s going on in a picture-based blog–from machine assembly for India’s Mumbai Metro to extremely hard rock encountered in Vietnam. Read on to found out the latest.
SIMULTANEOUS BUILDS FOR MUMBAI METRO
Mumbai, India’s massive Metro Line 3 project requires multiple TBMs on various contracts. A total of four Robbins TBMs will bore on two separate contracts–two 6.65 m (21.8 ft) Crossover (XRE) TBMs for contract UGC-01, and two 6.65 m (21.8 ft) Slurry TBMs for contract UGC-03. Assembly of the first Crossover TBM and the first Slurry TBM on each contract are occurring simultaneously, and are being overseen by our experienced Field Service crews.
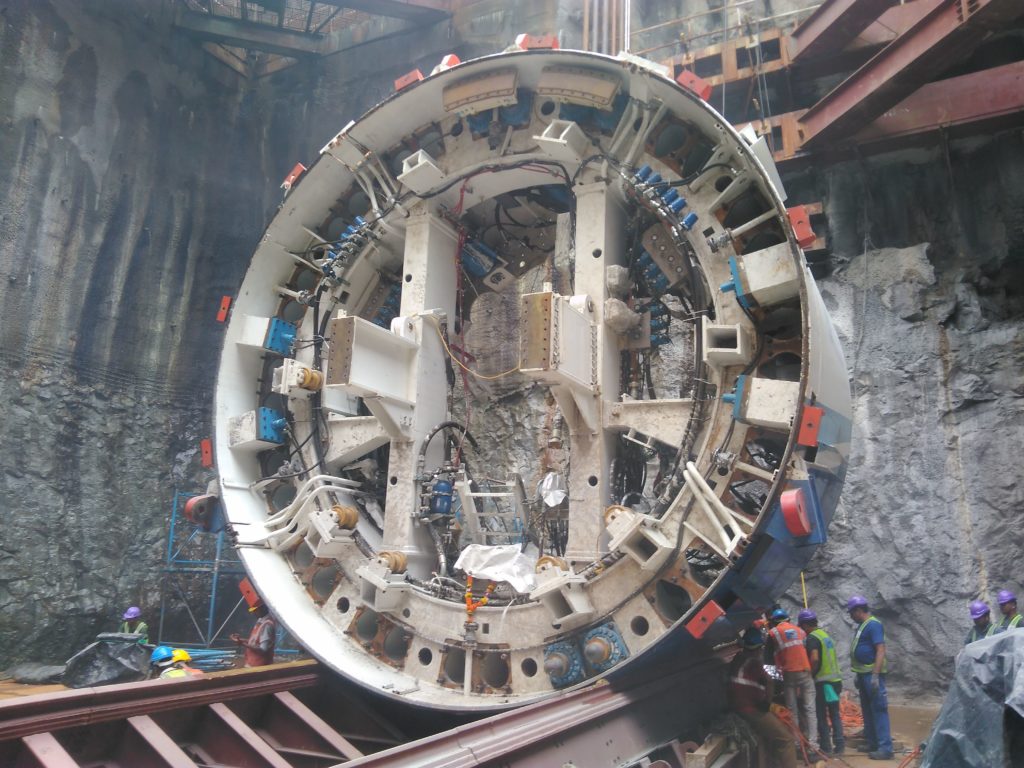
Crews position a section of the first of two Crossover (XRE) TBMs for the Mumbai Metro Line 3. Photo: Colin Ferguson
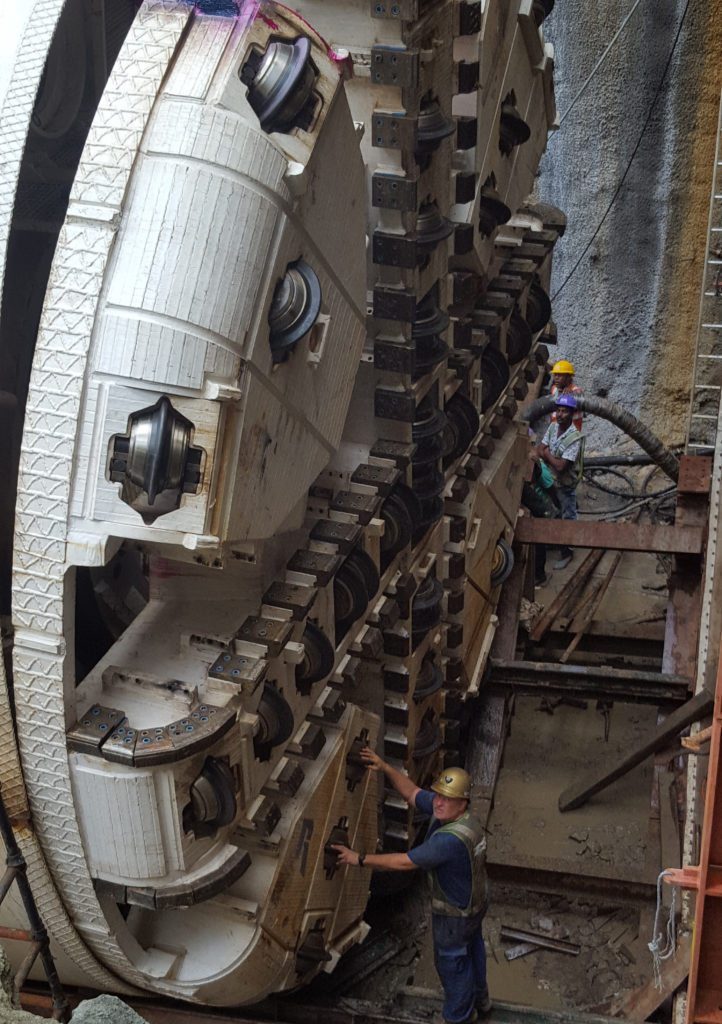
Crews assemble a Slurry TBM for the Mumbai Metro Line 3, and inspect the cutterhead. Photo: Colin Ferguson
EXTREME HARD ROCK IN VIETNAM
Robbins Field Service crews operating the Main Beam TBM at Vietnam’s Thuong Kon Tum HEPP have encountered granitic rock exceeding 300 MPa UCS and high water inflows. Despite the challenges the tunnel is more than 85% complete.
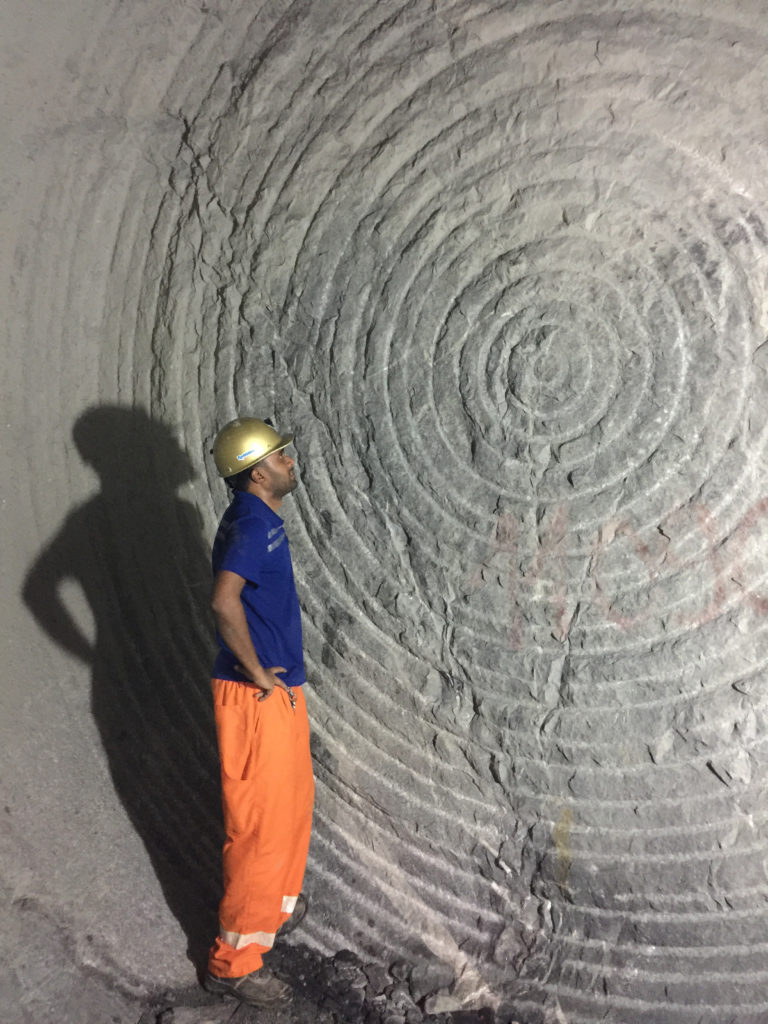
Robbins Engineering Geologist for Field Service, PN Madhan, inspects the massive granitic rock ahead of the TBM at Vietnam’s Thuong Kon Tum HEPP.
AN EPIC PROJECT IN MEXICO
With one of three Robbins lots completed at Mexico City’s massive 62 km (39 mi) Emisor Oriente tunnel, Field Service efforts are focused on completing Lots 4 and 5 in difficult mixed ground conditions. The customized EPB TBMs are boring through some of the most challenging conditions in the world, from abrasive basalt to watery clays and boulders.
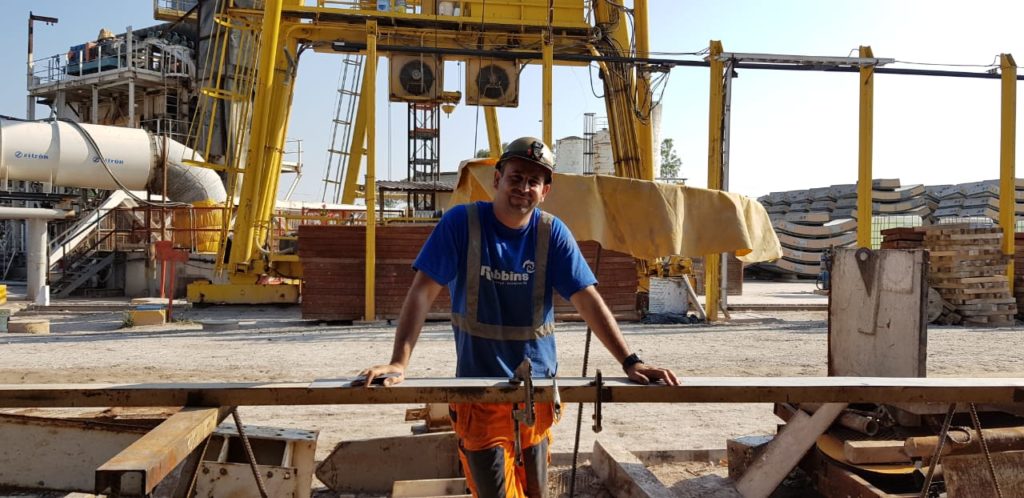
Alfredo Garrido Baena is part of the dedicated Field Service crew focusing efforts on completing Lots 4 and 5 in challenging conditions at Mexico City’s Emisor Oriente tunnel.
A JOB WELL DONE IN ALBANIA
TBM assembly and breakthrough is often discussed, but disassembly can be just as complicated. Following the recent breakthrough of the Crossover (XRE) TBM in Albania (the first machine of its kind in Europe) for the Moglicë Headrace Tunnel, Field Service crews are working to disassemble the machine in an underground launch chamber.
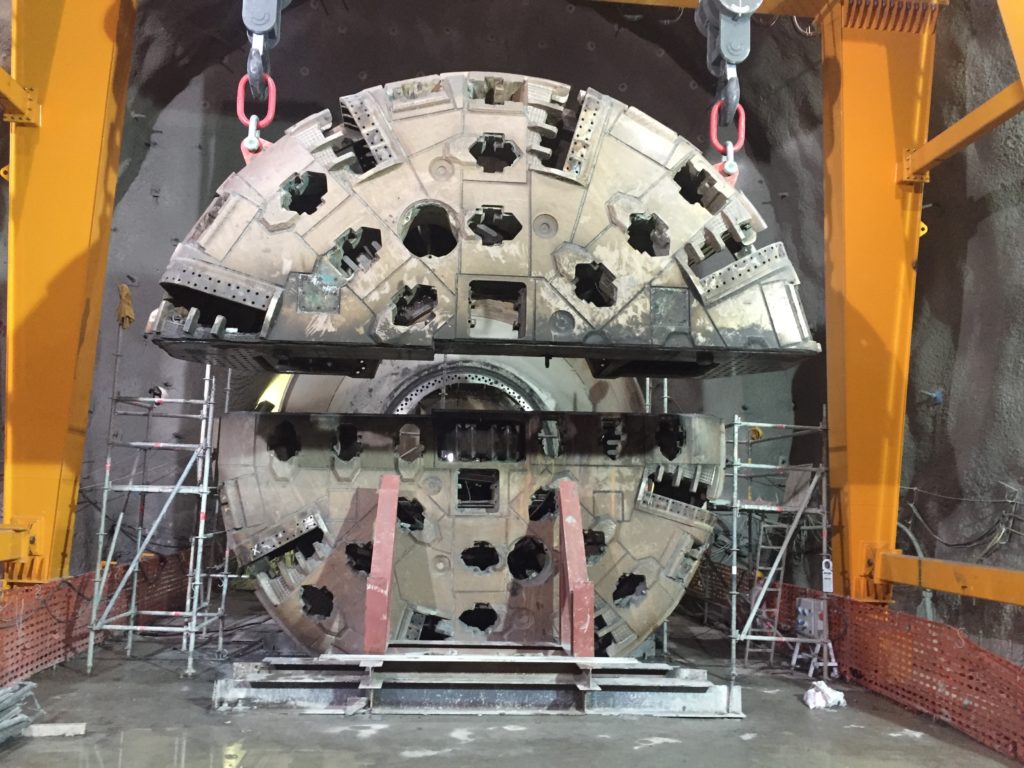
Crews separate the cutterhead of the Crossover TBM in an underground chamber in Devoll, Albania. Photo: Andy Birch
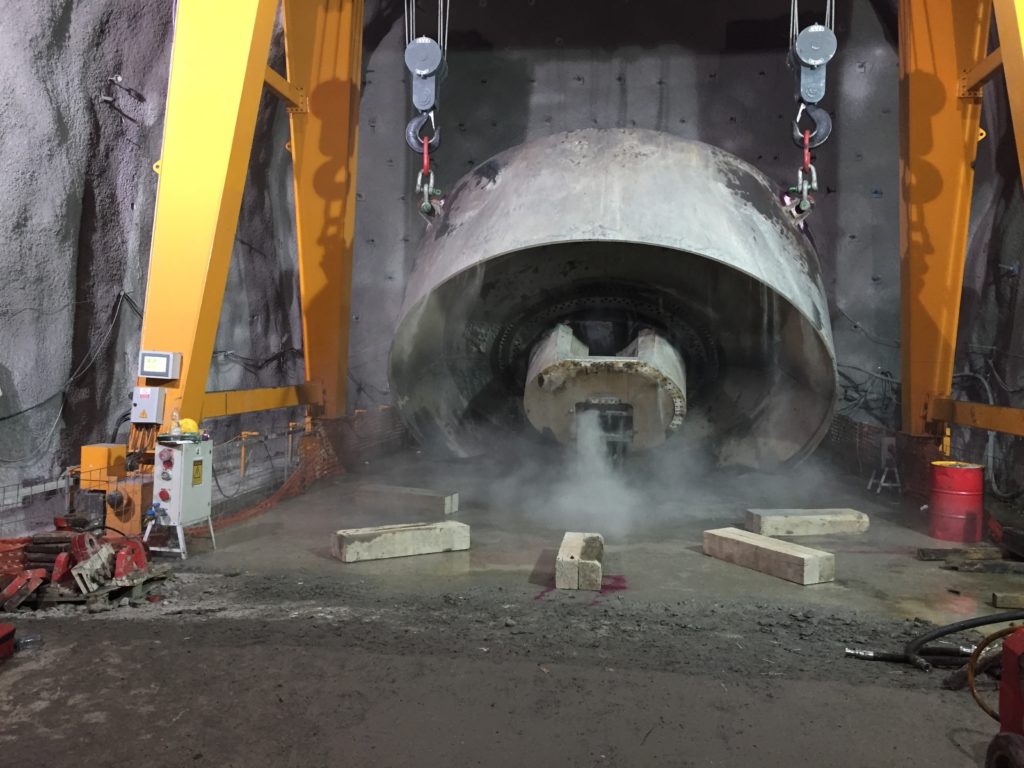
The forward shield is turned during disassembly of the TBM, which broke through in May of this year. Photo: Andy Birch
Let’s Be Clear: Transparency is a Boon, not a Bust, for the Tunneling Industry
The idea of transparency is one that we most often hear touted in politics and policies. But transparency is a concept that applies to our underground industry as well. Widespread knowledge sharing can and should be the policy in our industry, but all too often jobsite politics, confidentiality agreements, and fear of poor public opinion limit what is ultimately divulged. I argue that transparency in tunneling is a help, not a hindrance, and we can make steps today towards clearer communication.
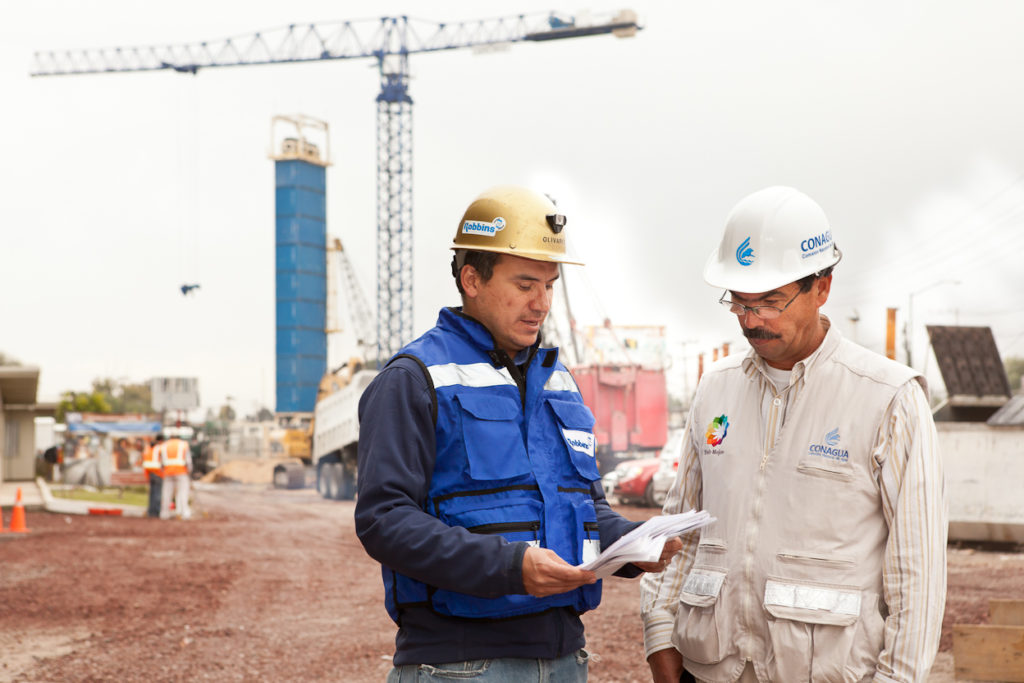
Transparency, achieved through better communication among all stakeholders, is the key to continued success in our industry.
Why It’s Needed
- Learn from Experiences in the Field: Tunneling professionals deserve full access to the successes and the problems that have been encountered in the field. If we were to employ universal knowledge sharing, tunneling operations themselves could become safer and more efficient and overall project costs could be reduced.
- Improve Tunneling Technology: Knowledge of advance rates, performance in specific ground conditions, wear rates for cutters and other surfaces in contact with the cutting face, performance of ground conditioners and foams, and many other types of info are imperative to improving technology. Tunnel boring could be made faster, safer, and more cost effective with such knowledge. It could also improve willingness to try new and emerging technologies in the industry, which benefits all stakeholders. With a good knowledge of TBM performances in specific ground conditions, TBM specifications could also be written to greater accuracy and result in using the most cost effective solutions.
- Improve Risk Sharing: Risk is often apportioned unfairly on today’s tunneling projects. In many cases the TBM supplier is required to shoulder a larger part of that burden than their potential returns. With a better understanding of the risks through knowledge of past projects, as well as knowledge of past risk sharing strategies, this problem can be resolved.
- Ensure Fair Financial Practices: With transparency in terms of contractual pricing and project spending, payments for work performed, etc. and other unsavory practices can be lessened.
- Reduce Litigiousness: Claims in tunneling projects are on the rise worldwide. Recent projects have resulted in separate and duplicate claims against different parties, such as the equipment manufacturer and the owner, for the same issues and without their mutual knowledge. Such claims are unfair, and through transparency and equal access by all parties to a Dispute Review Board, the frequency and extent of lawsuits in our industry could be reduced.
From the Equipment Supplier Perspective
As equipment suppliers, we strive to share the information that is available to us. We’ve opened up about stuck TBMs, challenging drives, and how we’ve overcome those issues. We’ve also tried to share whenever possible why we think fast advance rates and good efficiency were achieved on various projects.
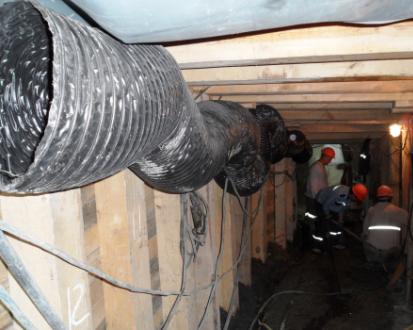
A bypass tunnel at Turkey’s ultimately successful Kargi project, where we shared information on seven such tunnels built in the first 2 km of tunneling.
Unfortunately knowledge is sometimes not shared even within parties on the same project, such as the contractor, project owner, owner’s representative, and equipment supplier. Time and again we see that communication between all parties is key to overcoming challenging conditions. The road to transparency starts here: with clear communication between all coordinating parties on a given project.
Not Without Precedent
Transparency is not an untested idea in our industry. A great recent example is that of the U.K.’s Crossrail project. The project follows governmental codes of practice for data transparency and the country’s Freedom of Information Act. Details such as project and equipment costs, spending budgets and records, safety records, and more are available for download on their website, and special requests can be made for additional data. Multiple reports have also been up front about TBM performance, advance rates, and other experiences on the project. The Crossrail project was highly successful and, arguably, transparency played a large part in that. Crossrail is also just one example of transparency at work in the U.K.—governmental programs such as Transport for London’s Transparency Strategy aim to give clear and consistent information to the public about all road and public transit spending.
A Call for Clarity
Transparency is possible in the tunneling industry, but it may require things like international regulations, or at the very least certifications that could be provided by an international organization like the ITA. Such a certificate would be highly beneficial to all stakeholders: It could certify corruption-free practices, and guarantee knowledge sharing. Transparency is not an easy thing to achieve, and there are certainly barriers to the process in various areas of the world. But we can start with transparency requirements within projects, and then move outward. To be clear: knowledge sharing is something that can only benefit our industry. It is our recommendation we start today.
Rescuing and Refurbishing TBMs: Experiences at Bangalore’s Namma Metro
In this blog, Robbins and guest blogger Barrie Willis, Manager Tunneling & Civil for iPS, share their experiences rebuilding and relaunching TBMs in the field.
TBM maintenance: it’s one of the most important factors predicting project success, but it is often glossed over. Experience shows, however, that maintenance plays just as much a part in the excavation rates as the proper TBM design. Regular maintenance can keep future rebuild costs low and keep equipment efficiency high while maximizing advance rates.
Conversely, a lack of maintenance, improper operation, and/or severe ground conditions can result in undue wear and slow advance rates. In a worst case scenario, it can even require rescuing and refurbishing a TBM. Such a case occurred at Bangalore, India’s Namma Metro, where several TBMs required recovery and refurbishment after operating in abrasive ground. Teams from both Robbins and iPS were called in to evaluate and rescue TBMs on separate sections of the tunnel.
The Robbins Experience
Two European-manufactured EPB TBMs “Krishna” and “Kaveri” were launched from the South Ramp station at the Namma Metro project in October and November of 2012, and were slated to bore three sections of metro tunnel each, totaling 1,550 m. While the first 400 m long drive from South Ramp to City Market station went well, the TBMs encountered severe ground conditions on the second, 432 m long drive from City Market to Chickpet Station.
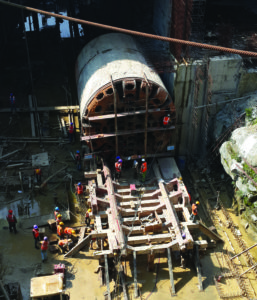
Robbins refurbished the two EPBs but did not change any of the machine design features.
Difficult Conditions
The drives took 12 and 22 months, respectively, and were hampered by a mixed face comprising hard granite and soil with high groundwater levels. Tunneling took place near fragile, historic building foundations in some cases hundreds of years old. The TBMs in this section encountered large boulders as well as reinforced blocks of concrete that seriously damaged the TBM cutterheads. These challenges required regular cutterhead interventions but at the same time there was an inability to grout unstable areas from the surface due to congested residential areas.
It was at this point that the contractor, along with owner Bangalore Metro Rail Corporation Ltd. (BMRCL), approached Robbins and asked them to take over the operations of the TBMs—the critical path tunnels needed to be brought back up to speed. The last 750 m drive between Chickpet and Majestic stations was all that stood in the way of opening a substantial section of Namma Metro’s Phase 1.
Robbins Signs On
After obtaining agreement from the project owner and the contractor, Robbins took over the responsibility for all aspects of the underground operations. A team of over 60 staff including TBM operators, TBM technicians, ring builders, a grouting team, and others began work. Robbins was also responsible for running surface installations and equipment such as the grout batching plant, gantry cranes and power supply. The contractor provided a team of people including surveyors, QC engineers, and loco operators who reported directly to the Robbins site management team.
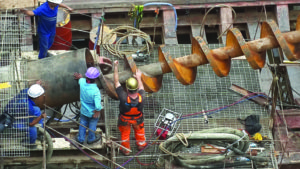
Robbins Field Service guided the refurbishment and assembly of the two competitor-manufactured EPBs.
The Robbins crew carried out refurbishment of the two TBMs, keeping the designs of the machines in tact while installing Robbins cutting tools in both cutterheads. In particular TBM “Krishna” underwent 112 days of repairs and testing. The refurbishment, and subsequent assembly and launch of the two machines, was carried out even as the Chickpet station was being constructed in order to mitigate any further delays. The two TBMs were re-launched in 2015 on their last drive—in March for TBM “Kaveri” and in December for TBM “Krishna”.
Challenging Ground Continues
Difficult conditions were encountered during the bore: the initial 160 meters of the drive was found to consist of residual soil, gradually transitioning into a mixed face of soil and highly weathered granite over the following 100 m. The mixed face conditions then gave way to a full face of fresh granite in the last 50 meters of boring.
The zones of transition were particularly difficult, with soil occasionally falling in due to the vibrations during tunneling. The conditions also made it impossible to maintain hyperbaric air pressure during cutterhead interventions. This problem was overcome by pumping a weak-mix grout solution into the ground surrounding the TBM. The solution permeated into existing voids and effectively prevented air from percolating through to the surface. A period of approximately 36 hours was initially required for curing of the grout solution. However, on-site trials with various additives enabled the standing time to be reduced to 12 hours.
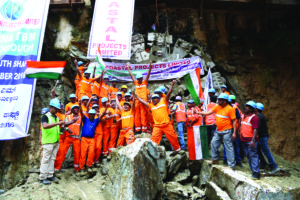
Robbins and crews celebrate the breakthrough of TBM “Kaveri”.
A Resounding Success
Despite the challenges, the TBMs were able to achieve advance rates of 50 mm per minute in highly weathered rock and 22 mm per minute in sections of competent hard rock. TBM “Kaveri” completed its final breakthrough in June 2016. The second TBM “Krishna” had the advantage of known geology and completed its excavation in about nine months on September 28, 2016.
The iPS Experience

When the TBM emerged from the rescue shaft most cutters and grill bars were worn away.
On another section of the recently completed Namma Metro, iPS rescued and refurbished a stuck TBM from another European manufacturer, and then operated it for owner Bangalore Metro Rail Corporation (BMRC) alongside the project’s original contractor.
Initial Inspection
iPS found severe wear—the cutterhead was essentially bare, and the cutters, disc boxes, cutter mountings and grill bars had been worn away. On inspection a serious crack in the screw conveyor was found and the flights had been severely worn. The TBM had been operating for 12 months and had bored 300 m of abrasive ground with insufficiently thorough maintenance. Geology consisted of weathered granite with a high quartz and feldspar content, 130 MPa UCS, and was often mixed with softer soils. It came to a standstill below the main railway lines at a major Bangalore metro station.
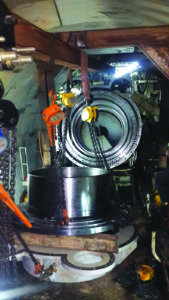
iPS crews had to rebuild the machine inside the tunnel.
Rebuild & Recovery Plan
iPS was able to build an intermediate shaft and refurbish the TBM to the point that it could advance into that shaft for further rebuild work including a replacement cutterhead. But the rebuild work itself was not easy—sourcing parts in India was a challenge, with smaller parts being brought in from Germany and other countries. A new cutterhead was shipped to the site by air freight. Crews dismantled the TBM to inspect and repair the screw conveyor, hydraulic system, PLC, and main drive. The TBM was relaunched in August 2015.
A Second Chance
Once the TBM had started up again, iPS then trained the crew on the importance of maintenance and inspections. They went over cutterhead interventions, what to look for, and how to prevent significant damage.
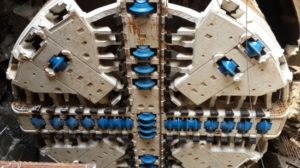
The cutterhead shown was shipped to the site by air freight, as sourcing parts was a challenge.
The training and TBM rebuild were a success—despite continued abrasive geology and mixed face conditions the machine completed the remaining 630 m of its drive in seven months. Frequent interventions were undertaken to maintain and inspect the machine. Breakthrough occurred on April 19, 2016.
Key Takeaways
Like any piece of machinery, it is essential to consider the total life cycle and to take steps to maximize the efficiency and life of the equipment through good operation and maintenance. Contractors should work with equipment suppliers to learn of the maintenance that is required—both scheduled and in response to changing geology.
When a project begins, err on the side of caution: do too many inspections, more than you think are necessary, to get a feel for how the machine reacts in different geologies. Geological surveys are extremely important, but they don’t always reveal every feature, so in the event the machine encounters unexpected geology, even more inspections will be necessary than normal. Above all, avoid complacency: just because a TBM is a large steel machine with a metal cutterhead and cutters doesn’t mean that nothing can damage it.
The proof is in the multitude of successful projects around the world: TBMs can and have shown their ability to excavate projects at world-class rates of advance even in very difficult conditions. With proper maintenance and operation, a TBM can last over many kilometers of tunnel and years of use.
9 Things to Consider When Choosing a TBM: A Checklist
Purchasing a Tunnel Boring Machine is no small consideration. Many factors are equally important to the price, and they can mean the difference between project success and significant downtime. Download our complimentary checklist to learn about the nine most important things to consider:
Learn more! Download the checklist for choosing a TBM here.
Are You in Tough Ground? Learn from our Trials and Tribulations in some of the Tunneling World’s Most Difficult Projects
Squeezing Ground, Fault Zones, Water Inflows, and More
True story: In a mountain range, crews worked on a shielded TBM more than 500 m below the surface. The TBM had excavated several kilometers in worsening conditions. The crew encountered karstic aquifers filled with mud and water. Personnel were pumping polyurethane through the cutting face to staunch the water inflows.
Suddenly, water inrushes climbed to a rate of 1,500 liters/second, creating a knee-deep underground river and causing the machine to become stuck. Thankfully, the crew was able to exit the tunnel, unharmed. The massive inrush created a damming effect with enough pressure to crush the TBM shields and send cylinders catapulting into the back-up.
As quickly as it had started, the machine ground to a halt, deep underground.
What happens when you encounter an unforeseen condition? A severe water inflow, fault zone, or squeezing ground? A geological feature that seems like it might stall your tunneling operation altogether? Some of our most difficult challenges—spanning from New York to Peru to the Republic of Georgia—are detailed below. These case studies are meant to pass on our knowledge and experiences to help you overcome obstacles, unforeseen or otherwise.
How to Overcome an Epic Flood: New York’s Harbor Siphons project
Sometimes an unforeseen condition requires a rescue effort to overcome. In October 2012, a storm was coming to New York City’s Harbor Siphons Project on the shores of Staten Island. The undersea tunnel and its 3.6 m CAT EPB ground to a halt when hit by Superstorm Sandy. The monstrous hurricane battered the eastern seaboard of the U.S. with winds of 145 kph.
The launch shaft was inundated with seawater despite contractor Tully/OHL’s best efforts. Flood water entered the tunnel and stopped the TBM just 460 m into its 2.9 km long drive. A 2013 post-storm survey of the tunnel showed a damaged machine extensively corroded by saltwater. All electrical components needed to be replaced.
Contractor OHL turned to Robbins for help. During the downtime, the original TBM manufacturer had exited the tunneling industry. Robbins worked with the contractor to come up with a multi-pronged approach to bring the TBM back to life.
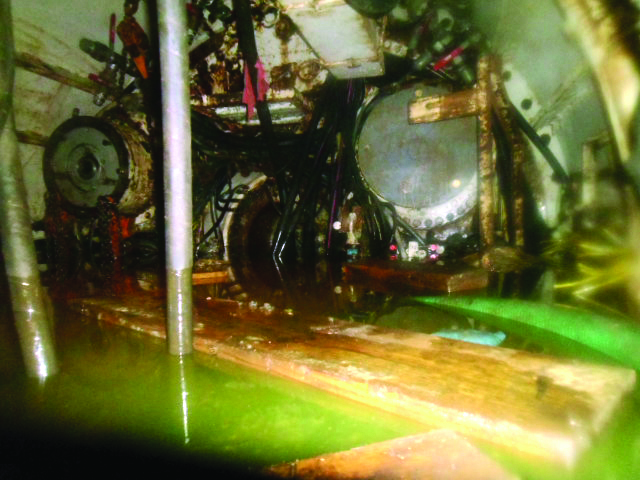
Flooded TBM: A view of the initial inspection after the flood, looking at the machine’s drive motors submerged in seawater.
Hiring a Dedicated Team
Per the scope of work, defined jointly by OHL and Robbins, crews temporarily excluded the cutterhead and main bearing of the TBM for refurbishment, as they were under earth pressure and not accessible. The Robbins team would need to complete the refurbishment taking into account unknowns, such as the condition of the cutterhead. The segmented concrete tunnel lining would not permit the removal of many of the larger TBM components, so these would have to be refurbished onsite.
The Robbins crew was contracted to guide onsite personnel in replacing corroded hydraulic components and installing all new electrical components. Variable Frequency Drives, PLCs, and wiring were replaced inside the small tunnel under atmospheric pressure of 3 bar. Crews constantly monitored earth pressure during the refurbishment. The machine had been stopped with its thrust cylinders in, and thus the crew could not replace or evaluate certain components before the machine started up.
Reverse-Engineering Electrical Components
By mid-December 2013, Robbins PLC technicians were reverse engineering the TBM’s control system. The team understood early on that the previous control programming would be unusable given the PLC change. The technicians had only limited assembly drawings from the CAT manual, so much of the refurbishment, including the PLC system, had to be built from the ground up. The team at site understood how the machine should work and therefore were able to build the correct PLC system.
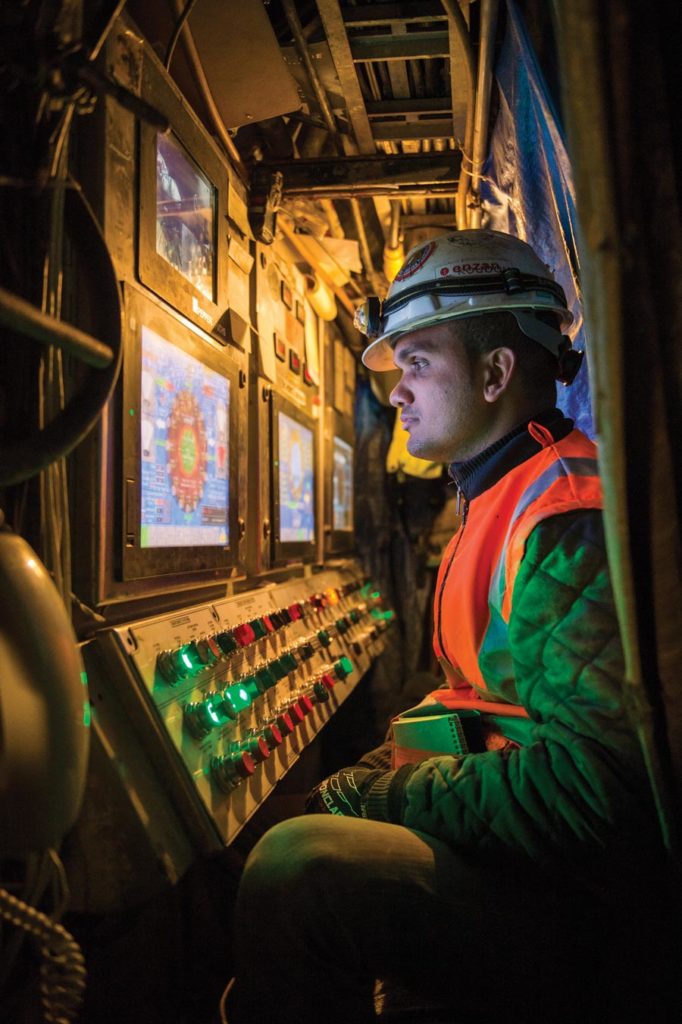
Reworked Electronics: The Harbor Siphons TBM required all new electronic systems.
Coordinating Success
Despite all of the challenges, the refurbishment project was a success. Crews had gone from a shipwrecked TBM—rusted, corroded, and abandoned in the tunnel—to a successful tunneling operation. It was a monumental task, scheduled to be completed in four months, and finished on schedule.
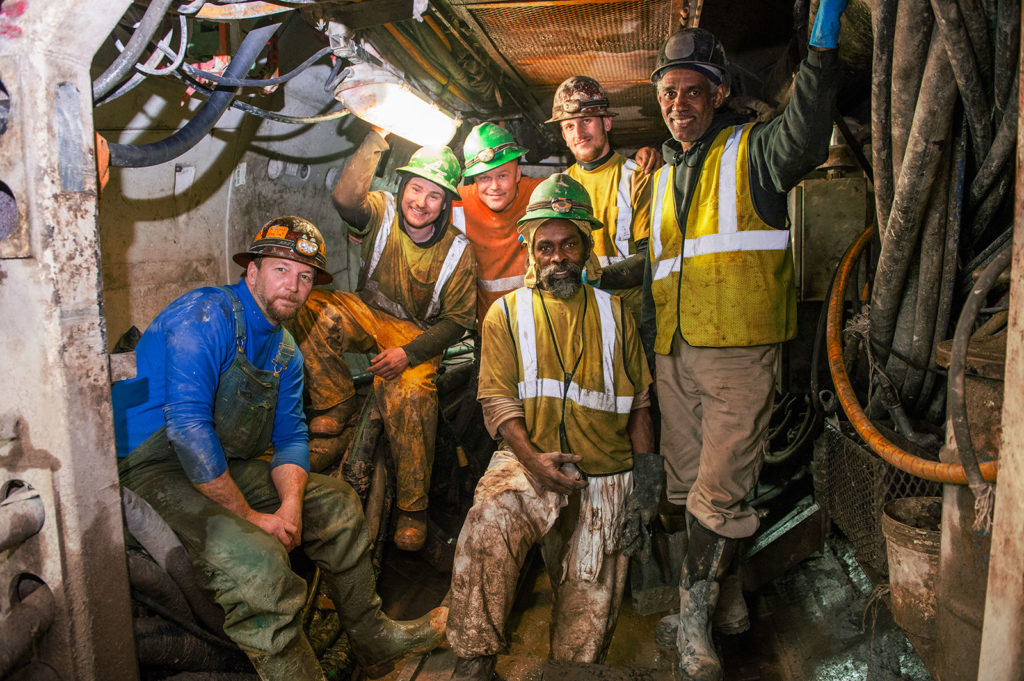
A Good Result: The happy crew during TBM boring, after the full refurbishment.
In the final phase of the refurbishment, a Robbins PLC technician was able to complete the commissioning of the TBM and on April 14, 2014 the machine officially returned to mining. The machine successfully completed its tunnel in February 2015.
Read more in the white paper here.
Make Rock Bursting Conditions Safe for Your Crew: The Olmos Trans-Andean Tunnel
If 16,000 recorded rock bursting events in the world’s second deepest tunnel weren’t enough, the crew at Peru’s Olmos Trans-Andean Tunnel had another problem. As the machine progressed and the cover grew higher—up to 2,000 m at the highest point—the rock bursts became more violent. Crews experienced large over-breaks and cathedralling in fractured and unstable ground. Teams of personnel had to inject concrete into large cavities that had formed during stress-relieving activities and stabilize these cavities with spiling. Then, several kilometers into the tunnel, a major rock bursting event occurred that twisted ring beams and caused damage in 45 m of lined tunnel. Damage was extensive to the TBM gripper, which was ballooned and blown off its mountings. Damage also occurred to other hydraulic cylinders. Thankfully crew members were not harmed, but downtime for repairs would be substantial.
A Century-Long Effort
The Olmos tunnel is a 12.5 km long water transfer tunnel that was bored through the Andes Mountains to bring irrigation to drought-ridden areas on the pacific coast. The project was more than 100 years in the making, with several attempts being made and thwarted by incredibly difficult geology as recently as the 1950s.
In 2007, with Odebrecht as the main contractor, the tunnel was finally completed using a 5.3 m diameter Robbins Main Beam TBM after other attempts with conventional methods failed. The route is the world’s second deepest civil works tunnel with overburden of up to 2,000 m. The tunnel alignment traverses complex geology consisting of quartz porphyry, andesite, and tuff with rock strengths ranging from 60 to 225 MPa UCS. The machine crossed over 400 fault lines including two major faults of approximately 50 m wide.
A Rocky Start
The machine was launched in March 2007, in ground conditions that immediately became more complex than anticipated. As the height of the overburden increased, long stretches of extremely loose, blocky ground were encountered. TBM utilization was as low as 18.7% of working time because rock support installation was requiring a very high 43.5% of the working time.
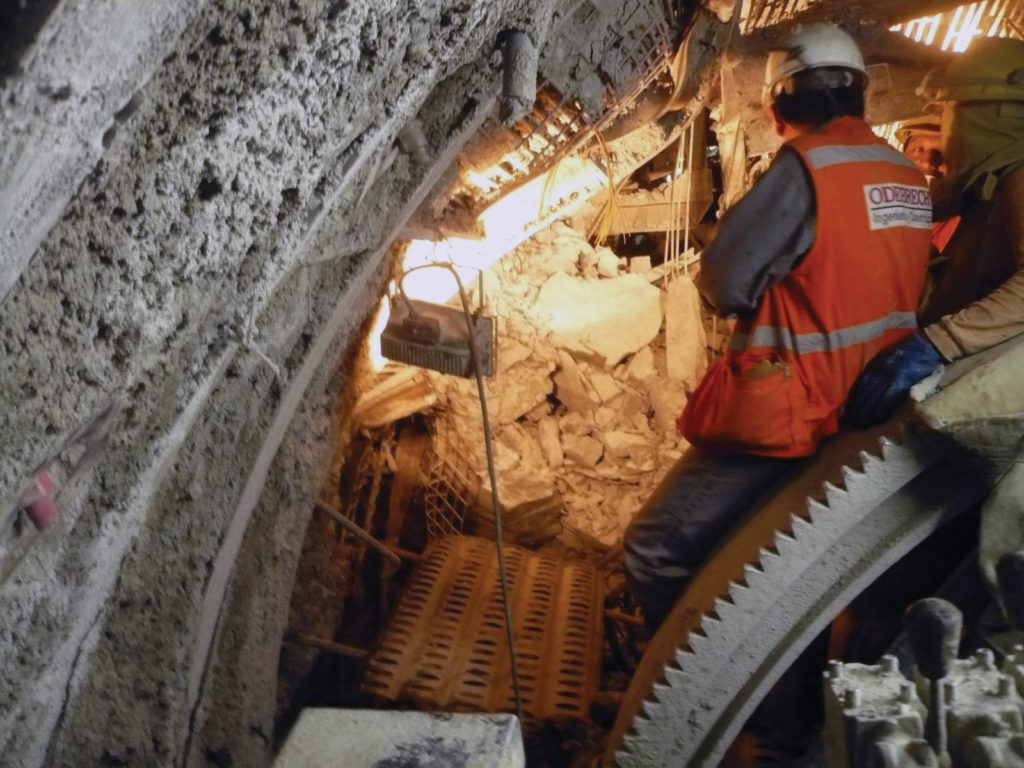
A rocky start: Rock bursting conditions at Olmos prompted a major overhaul of the TBM in the tunnel.
One of the main problems faced was ground deterioration and the resulting falls of blocky ground. The majority of these events occurred during the time taken for the newly excavated bore to pass behind the rear fingers of the roof shield, where ring beams and mesh were installed.
Modifying the Machine in the Tunnel
During consultations between Robbins and Odebrecht, a decision was made to modify the machine in the tunnel. The TBM would be reworked to use the McNally roof support system, which allows support to be installed directly behind the main roof shield. Crews removed the roof shield fingers and installed a series of rectangular pockets in their place. The pockets ran from the rear side of the cutterhead to the trailing edge of the roof support. These pockets were designed to be used with rebar, which is part of the McNally Roof Support System. At a later stage when the ground conditions worsened these pockets were extended to cover the sides of the TBM as well.
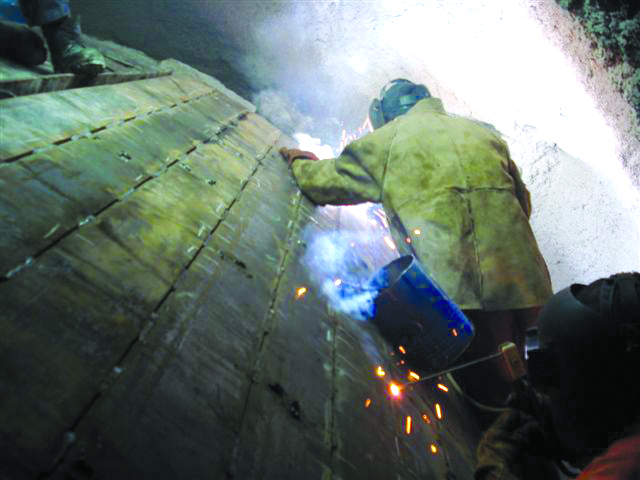
TBM Modifications: The crew add McNally pockets to the TBM roof shield in the tunnel.
The McNally Support System
One big advantage of the McNally support system is that it is possible to install ground support closer to the face than other ground support methods used on TBMs. It holds loose rock in place, which in turn helps to activate the strength of the rock mass and maintain the inherent strength of the tunnel arch. When used correctly the system can significantly reduce the time taken to provide adequate support. It can also offer reductions in the level of support required, and contain rock bursts and collapsing ground. The greatest benefit of the system, by far, is its ability to provide a much safer work area.
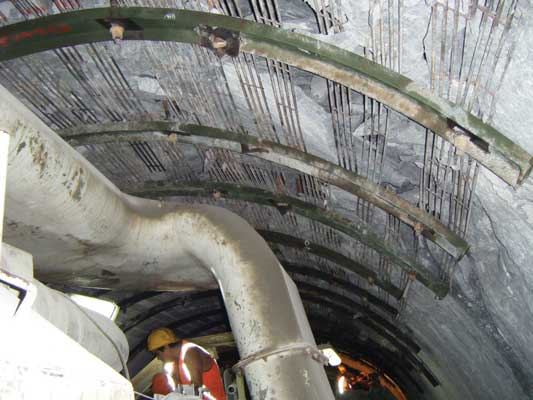
Crown Control: McNally slat installation at the Olmos Trans-Andean Tunnel.
Incorporation of the McNally support system and various other modifications to the TBM resulted in a steady increase in production rates in spite of continuous rock bursting events. The machine broke though in December 2011 having achieved production rates in excess of 670 m a month.
Read more about the McNally Support System here.
Make short work of an unforeseen cavern: The MKTVARI project
The Republic of Georgia’s Mktvari Hydropower Plant Construction project, along the river of the same name, was a challenge from the outset. The initial contractor used drill and blast for the 9.5 km long headrace tunnel through hard rock, but after 1.5 years they had only advanced about 200 m. The new contractor took over a previously-ordered non-Robbins hard rock machine but enlisted Robbins to help with the TBM assembly. They also wanted Robbins to be available if problems occurred. The machine did well at the outset, boring up to 900 m per month. But then, the machine hit bad ground.
Cavernous Conditions
Crews hit an unforeseen cavern above the TBM and were unsure of how to proceed through mixed layers of breccia, andesite, and bands of clay with light water inflows. A Robbins Field Service Manager was sent to the site, where he determined that the cavern was part of a fault zone consisting of unstable material that fell onto the cutterhead. At the time of his arrival, the TBM had passed through most of the fault zone but huge voids were left behind the segments.
Using pea gravel pumped through holes drilled in the segments, combined with cementitious grout, the crew was able to stabilize the existing segments and safely advance through the cavern in about 10 additional segments. There was also a probe drill onsite that had not been used; the Robbins manager persuaded the crew to install the probe drill and conduct systematic probing ahead of the machine, in case a larger section of clay was encountered.
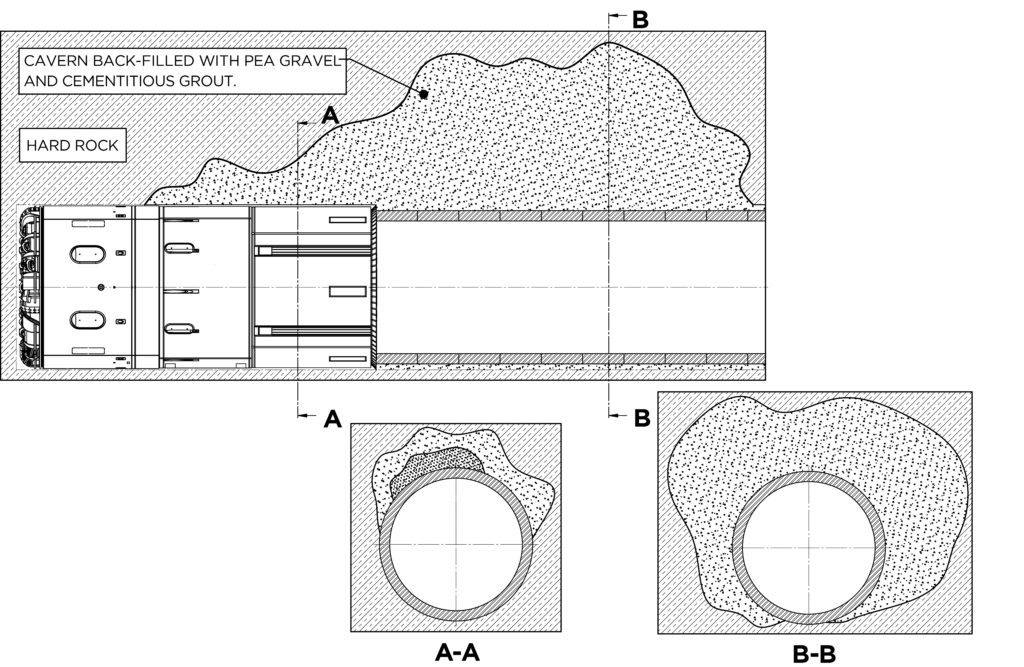
Crossing the Void: Robbins worked with the contractor to backfill the cavern, enabling the crew to advance out of the void in 10 additional segment rings.
Key Takeaways
As can be seen in these examples, planning is key. But, even the best-laid plans can go awry. When conditions go from bad to worse, having an expert team of personnel on your side is by far the most valuable tool and the most positive predictor of a project’s ultimate success. That true story I started off with certainly wasn’t the first such incident in the tunneling world, and it won’t be the last. Be prepared by arming yourself with knowledge, and with a knowledgeable team.
Information at your Fingertips
Learn more about our vast experience in difficult ground conditions. Our selection of white papers covers some of the world’s most challenging projects, while our Project Solutions section offers many examples of past successes.
Recent Posts
- Tunneling in Turkey: The Esme Salihli Railway
- Incredible India: Machines on the Move in Agra and Delhi
- Notice of Retraction and Apology
- Four Things You Need to Know about Probe Drilling and Pre-Grouting
- The Latest Updates: Records in Toronto, the News from Nepal, and More