Year: 2013
A Tradition of Innovation: The 2013 Muir Wood Lecture takes a cue from Robbins’ Long History
When asked about his most memorable tunneling project, Dick Robbins narrowed it down to two: The Channel Tunnel and the Paris RER Metro. The former company president and CEO from 1958 to 1993 has seen hundreds of tunneling projects in his career, and should know. The Channel Tunnel, with its hybrid machines capable of operating under 10 bar water pressure, was challenging to say the least. But the Paris RER Metro in 1964 resulted in a radically unique machine design: “We created the world’s first below-water, pressure bulkhead shielded machine using air pressure. All future slurry and EPB designs had their genesis in this machine,” said Robbins. A sealing system using steel fingers back-supported with foam kept the gap between the machine shield and segments airtight. Wire brush seals with grease were not developed until later projects (see below).
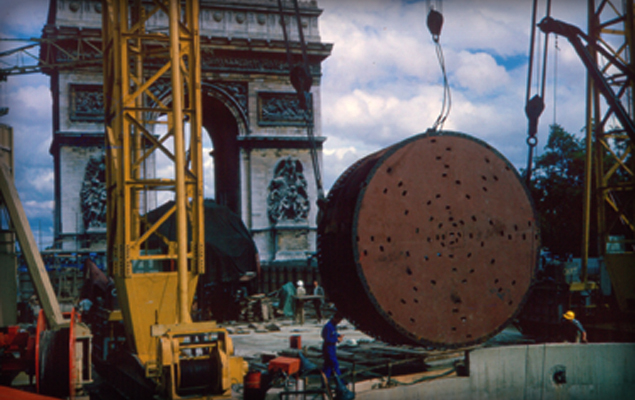
The central section of the Robbins machine at the Paris RER metro, with the Arc de Triomphe in the background.
These two projects are just a few of the highlights Dick Robbins is set to touch on during his 2013 Sir Alan Muir Wood Lecture, honoring the late tunneling statesman who initiated and served as the first president of the International Tunneling Association (ITA).
The talk, titled “A Tradition of Innovation: The Next Push for Machine Tunneling” will cover everything from the beginnings of mechanized tunneling to the era of modern tunneling when his father James S. Robbins came up with the idea of developing full-face TBMs (see picture below). Discussion will then move to modern-day marvels like the world’s largest TBM set to bore the Highway 99 Viaduct Replacement tunnel. Robbins will make the case that a culture of innovation is needed in greater force in order to push for new leaps in design that will accelerate the advancement of the industry.
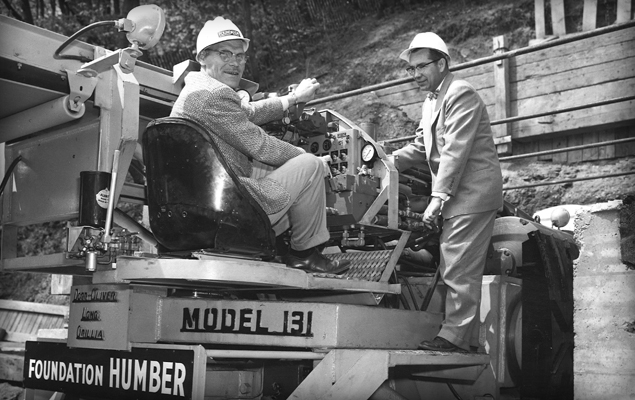
James S. Robbins (in driver’s seat), Robbins founder, at the launch of the Humber River Sewer TBM in 1956. The machine was the first ever to exclusively use rolling disc cutters.
See the Talk:
ITA-AITES World Tunnel Congress
Geneva, Switzerland
Opening Ceremony & Sir Alan Muir Wood Lecture
Monday June 3
9:00 AM to 10:30 AM
For more information on Robbins’ long history, check out the lecture Dick Robbins and colleagues made when he received the 2009 Benjamin Franklin Medal.
Robbins Small Boring Units: A Closer Look at the SBU-M
Learn more about the Robbins Motorized Small Boring Unit (SBU-M) in this 3D animation. With continuous steering capabilities and an in-shield drive motor, the SBU-M can make the grade on long gravity sewers and other line and grade sensitive utility tunnels.
Salamanders, Pseudo Scorpions, and Quartz Crystals: How my Recent Site Visit proved that TBM Tunneling is the Greenest Way to Go
The Balcones Canyonlands just north of Austin, Texas, USA is a protected wildlife preserve, and it’s not open to the public. So when the city of Austin opted to build a 10.5 km (6.5 mi) long water line directly below it, there was understandably some concern—but not for humans. The inhabitants of the Canyonlands include some of the state’s most endangered species, from tiny, blind cave spiders to songbirds to the green-speckled Jollyville Plateau Salamander. And don’t forget the pseudo scorpions. The Jollyville Transmission Main, a pipeline planned to bring drinking water to the drought-ridden city, was designed deep below protected aquifers in chalk, up to 106 m (350 ft) down in limestone rock. This made tunneling the only option. But even so, how could the project avoid impacting such a sensitive environment?
When I visited the site in Autumn 2012, I got my answer. The contractor, Southland/Mole JV, is taking every precaution to mitigate impact, and they’ve been very successful thus far. An environmental consultant from the city is on the site daily, and routine inspections ensure that the minimally invasive tunnel is not encroaching on the habitat of the endangered animals.
Our guides for the visit, Kent Vest and John Arciszewski of Southland Contracting, took us to the 82 m (270 ft) deep Four Points Shaft first, which has been partially reinforced with liner plates. Kent and John explained that during excavation, water inflow from the aquifer had been high enough that the city opted to grout behind the liner plates to prevent further dewatering. Gravel in the annular space between the liner plates and shaft walls would keep any groundwater pathways intact.
As we descended into the unlined tunnel where a 3.25 m (10.7 ft) Robbins Main Beam TBM was averaging 55 m (180 ft) per day, we talked ground support—or the lack thereof. Three TBMs are being used to excavate portions of the tunnel in competent limestone. Southland is not permitted to do either pre-excavation drilling or grouting because of the possibility of karst cavities and groundwater pathways—areas where endangered aquatic species might live. While they plan to install wire mesh and rock bolts if it’s needed, the rock quality has so far been very good with little ground water. We took a few photos while in this tunnel (see below), and then moved on to the next site.
Our last site visit of the day was the deepest—the 106 m (350 ft) Jollyville shaft next to the similarly named Jollyville Reservoir in a much more urban location. Once we’d been lowered down the shaft, we found a small, unlined tunnel in competent limestone. A 3.0 m (9.8 ft), contractor-owned Double Shield TBM was tunneling this reach, after having been refurbished by Robbins in Solon, Ohio. Similarly, the machine was getting some fast advance rates of 46 m (150 ft) per day on average.
What I immediately noticed in this tunnel was the multitude of small, mostly dry karst cavities down the tunnel walls. These cavities could potentially be home to the blind cave spiders, though none had been found during tunneling and it was likely they wouldn’t live in such small voids. We noticed, during our ride on the muck train towards the machine, sparks of light emitting from these cavities. Once we stopped John reached into a cavity and pulled out a handful of quartz crystals. “These are all over, in all these cavities. You can take some with you,” he said. As I am part-pirate (my genealogy traces back to Sir Francis Drake on my mother’s side!), I decided to stuff my pockets with the sparkly crystals (i.e., treasure!). I had never seen anything like this before, but John explained that the minerals in the perched water in many of the pockets caused the crystals to grow. Since the pockets were small, they weren’t filled in or isolated and we could pluck quartz crystals to our heart’s content.
On a more serious note, Southland does have a plan of action if large cavities are found or if a groundwater pathway is very open and linked to the aquifer. In this case, large voids would be isolated and sealed off to protect the habitat within. If ground water inflows are severe they will install steel liner plates and grout behind them to stop the flow. But, says Southland, they don’t expect to encounter either of these since the tunnels are so far below the aquifer. In fact, one reach of the tunnel, already complete at the time of our visit, had encountered almost no groundwater in 1,300 m (4,400 ft) of tunneling.
Once back on the surface, it became clear to me that this well-designed project proved that tunneling, particularly TBM tunneling, could be used safely in even the most sensitive environments. The foresight, planning, and execution by the designers and contractors was impressive. The salamanders and pseudo scorpions thank you.