Year: 2017
Robbins Slurry TBM ramps up for Mumbai Metro Line 3
The first of two Slurry TBMs, a rebuilt 6.65 m (21.8 ft) diameter machine, passed its factory acceptance on September 4, 2017 in Singapore. The machine, fitted with a Robbins cutterhead and outer shields, is destined for the Mumbai Metro Line 3 under contract UGC03 for the Dogus-Soma JV (DSJV), and will begin excavation in late 2017. The factory acceptance for a second 6.65 m (21.8 ft) diameter Slurry TBM will be conducted by the end of 2017.
The on-time delivery of the first machine is just the beginning of partnership that will span years. “There are few companies in the international arena that are as professional as Robbins. Robbins has been very helpful to DSJV since the inception of the project and will be our partners until the end of the contract. Robbins’ presence in India including field service crews will be a great help for us in future,” said Mr. DV Raju, Senior Vice President for SOMA.
The two machines will excavate parallel 3.5 km (2.2 mi) long tunnels between Mumbai Central and Worli station sites, passing through three intermediate cut and cover stations on the way. Ground conditions consist of fresh to weathered basalt and breccia up to 100 MPa UCS with water pressures up to 3 bar.
The JV selected Slurry machines for their contract due to the challenging ground conditions expected. “I have worked with Slurry TBMs on similar geology globally. Slurry TBMs have real power and will suit the hard rock geology of our Mumbai Metro contract 3. The water table and variable geology, especially basalt of higher hardness, can be easily tackled by Slurry TBMs,” said Mr. Tamay Sayin, Project Manager for DSJV. The cutterheads of the machines are fitted with wear protection, wear detection bits, and Robbins 17-inch disc cutters for the conditions. Grizzly bars will limit the size of boulders that can enter the cutterhead to 250 mm (9.8 in). The slurry systems includes rock crushers as well as abrasion-resistant plating in high-wear areas.
The two TBMs are the first of a total of four machines being provided by Robbins for the Mumbai Metro Line 3. Another two 6.65 m (21.8 ft) diameter Crossover XRE machines will bore parallel 2.8 km (1.7 mi) tunnels on a separate contract in 2018. “Mumbai Metro is one of the most prestigious metro works in the country, and Robbins’ involvement in providing suitable machines and associated services is an honor,” said Kapil Bhati, Managing Director for Robbins India.
The 33.5 km (20.8 mi) long Line 3 of Mumbai Metro being constructed by the Mumbai Metro Rail Corporation (MMRC) will consist of 26 underground stations and one at-grade station that will reduce heavy traffic and rail congestion between Bandra and Churchgate areas of the city. A total of 17 TBMs are being procured to bore various sections of the tunnels, which will be excavated at average depths of 15 to 25 m below the city. The entire line is expected to be operational by 2021.
The Changing Face of the Tunneling Industry: The Role of the ITA, Partnership, and Innovation
Martin Knights graduated with a degree in Civil Engineering in 1970 and joined the Second River Mersey Road tunnel project as a site engineer in Liverpool, UK as his first TBM project. The major feature of this 2.5 mile long twin tunnel project was the refurbished 35 ft diameter Robbins TBM, which had previously driven a number of water supply tunnels at the Mangla Dam in Pakistan. Knights worked in several consultancy firms on a number of high profile tunnelling projects over several decades, most recently as the Managing Director and Sr. Vice President for CH2M/Halcrow. He was also president of the International Tunnelling Association (ITA) from 2007-2010. He is currently an independent consultant with his own company, Martin Knights Consulting.
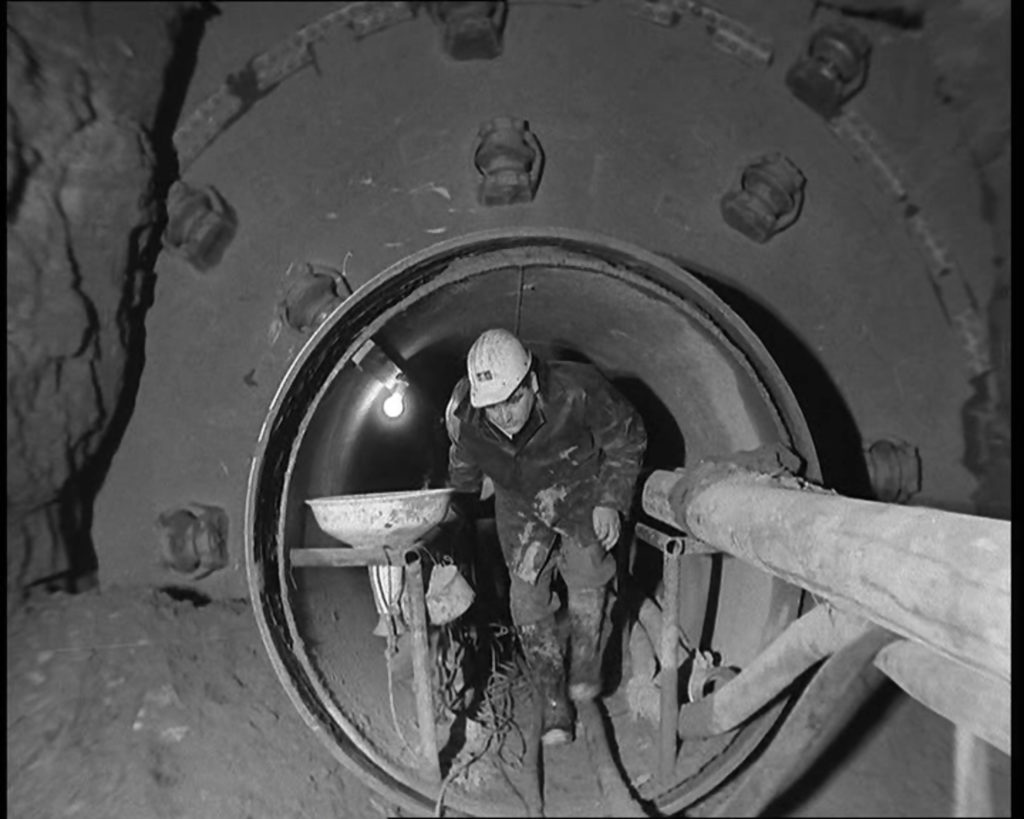
A worker exits the rebuilt Robbins TBM used on the Mersey Road Tunnel Project in the UK. The Second Mersey Road Tunnel was Knights’ first project after graduating in 1970. Image Credit: British Pathé
At the recent ITA Training Course in Bergen, Norway, which preceded the World Tunnel Congress, I gave a lecture about the development of Soft Ground TBMs from Victorian times until now. It took a bit of research: I trawled through reference books and talked to experts in the TBM world. During the research I looked at project specifications for big projects carried out in the past 40 or so years, and was struck by the level of technical detail and requirements that engineers stipulated in the contract documents: there seemed to be a tendency for over-specification that imprisoned the contractor and his equipment suppliers to past tried-and-tested practices. Where was the opportunity to innovate and trial new ideas by those best suited to introduce best and new practices?
That reminded me of Lok Home’s [Robbins president] challenge to me in November 2009 at the Hamburg, Germany STUVA Exhibition and Conference. Lok and l, and other colleagues in ITA and the tunnelling world, took part in an industry round table talk. I was President of ITA then and the two-hour discussion concluded with Lok asking me, “So, Martin, what can I and the industry do for ITA? We provide sponsorship to ITA, like other leading tunnelling companies; we fill the exhibition halls; we host social gatherings during ITA conferences, and we give lectures promoting new products. But we as equipment manufacturers and suppliers want to play a bigger technical role.”
Stung by the realisation that ITA had, by default, missed a trick, and was, in effect, excluding the very talent that provided innovation in tunnelling, I set about forming the then-new ITA technical forum ITAtech. I say “I”, but in fact myself, Lok, Tom Melbye of Normet, Felix Amberg of Amberg Engineering, and colleagues from Herrenknecht, Mapei, Atlas Copco, and others set out over three months to prepare the ground to launch ITAtech as a premier promoter within ITA of technology and innovation. Our purpose was to prepare independent and commonly-agreed technical guidelines and evidence endorsed by the whole international tunnelling industry, which is what ITAtech continues to do. It provides manufacturing, installation, equipment and materials guidelines for Contractors and Designers and creates confidence for tunnel owners that the “brand” of the ITA is overseeing this important knowledge transfer.
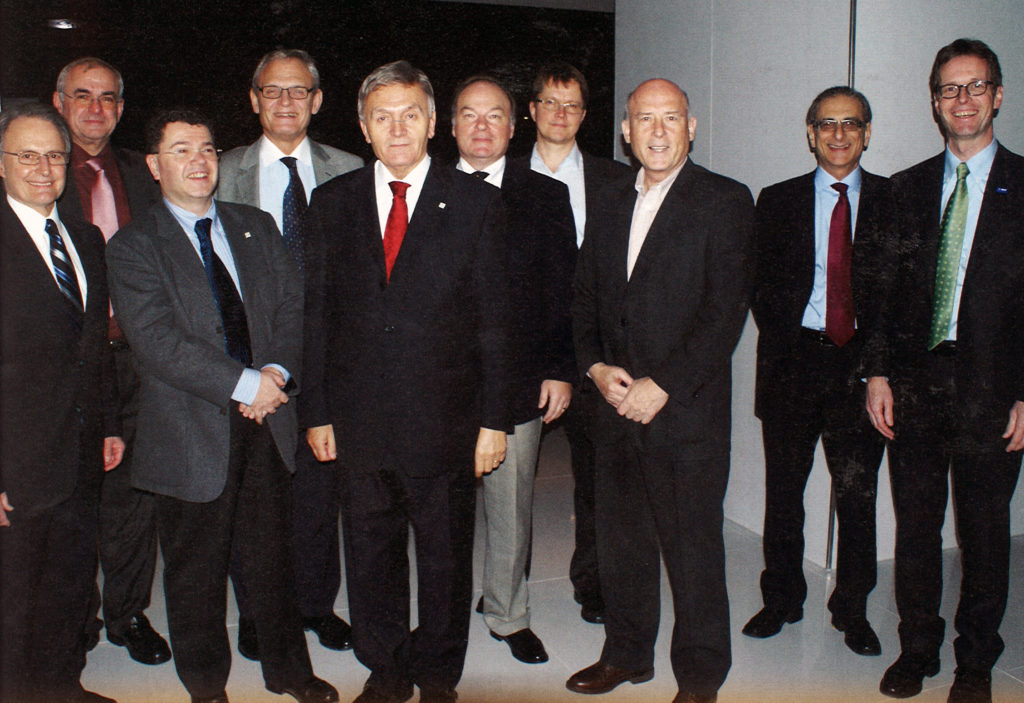
The initial 2009 meeting that led to the ITAtech forum. Left to right: Bill Hansmire, Gerhard Robeller, Olivier Vion, Gunnar Nord, Martin Knights, Brian Fulcher, Pekka Nieminen, Lok Home, David Caiden, Daniel Ruckstuhl
As I talked to the Bergen delegates this year, it was obvious to me that soft ground urban tunnelling owes a debt to the development of TBMs over the past 40 years…and particularly to the past 10 years. We can now do things that were too difficult to do way back then. It’s no coincidence that the innovations in the last 50 years were led by TBM companies like Robbins, Lovat, Seli, Herrenknecht, etc. The leadership and pioneering spirit could have only been driven by the individual passion that comes from a “family run” business. With time, growth and ownership has been passed on, but the stewardship and spirit of innovation in tunnelling lives on. ITAtech has tried to capture that spirit. Membership of its Steering Board and Activity groups relies on that desire of industry to educate, improve and share.
A recent President of the UK Institution of Civil Engineers compared our fragmented industry processes with the manufacturing, aircraft and car industry. In effect he said “Why–unlike those industries–do we separate inception, planning, and design from assembly, installation and construction?” The infrastructure and mining industries rely on so many processes and partnerships to deliver projects precisely because they are so fragmented and siloed.
Contemporary procurement encourages more partnerships, but this doesn’t make it any less convoluted. We see the rise of the dreaded words “industry supply chain” and “second and third tier partners”, where it strikes me that we’re airbrushing out the identity of the very “tier” of industry that has to innovate and provide the substance that nourishes the technical solutions that feature in new infrastructure developments.
I suggest that owners and clients get better access to and value from these innovating “tiers”—in many cases the equipment manufacturers and suppliers. In so many cases I have seen technical solutions get misinterpreted as ideas and solutions move up and down the so-called supply chain, begging for recognition, understanding and realisation of value.
I’m sure that this is not intended…but it happens. By validating and bringing innovations to the forefront through organizations like the ITAtech, we can improve some of the convoluted procurement and technical approval processes. However if we want to continue to see advancements like we’ve seen in urban soft ground tunnelling in recent decades, we should seek to streamline manufacturing and procurement, and to work closely with all “tiers” involved—second, third, and on up.
5 Things DGS can do for your TBM Operation in Difficult Ground
Difficult Ground Solutions (DGS) is a suite of options that can be added to a shielded hard rock machine or Crossover machine to better enable advance when conditions are unknown or difficult conditions are anticipated. While each of these items is not new, the concept of installing them on a machine from the start, and of using them in concert to provide better visualization and performance in the most challenging ground, is. The uses and advantages of DGS are various and wide-reaching.
Number 1: DGS can act like risk insurance.
Yes, risk insurance. While one can argue that risk insurance is not needed—and of course if a tunnel were in entirely homogeneous, medium strength, self-supporting rock, under a medium amount of cover, I would tend to agree—there is a problem with this argument. That scenario exists only very rarely. At Robbins, we are seeing more tunnels being planned in mountainous, remote regions where an accurate GBR cannot be obtained. More tunnels planned through multiple fault zones and mixed face conditions. More tunnels planned in suspected karst conditions and in rock where large water inflows may occur. It is a trend we’ve observed arcing upward, and with these high-risk projects it seems prudent that an equipment manufacturer should strongly recommend risk insurance. We’ve done that the only way we know how: by calling on our extensive experience to develop, test, and provide various solutions that can be added to a TBM at the beginning of the project. These features mitigate the risk of getting stuck in unforeseen (or foreseen) challenges that might come up in a tunnel drive.
This risk insurance works like any other type of insurance—it must be purchased before the actual event happens. Waiting until a machine encounters a given challenge—where it may become damaged, stuck, or irretrievable—is not an adequate plan for difficult conditions. Sure, some of these options can be added in the tunnel, but such an operation is far from ideal. Risk insurance is best purchased during the TBM design phase, long before the machine is built and launched.
Number 2: DGS can get your TBM through a fault zone or squeezing ground where it might otherwise become stuck.
If fault zones or squeezing ground are known or suspected, or if there is even a possibility of encountering them, this can greatly affect your TBM operation. Shielded hard rock machines protect your crew from the surrounding ground, and they can bore and line a tunnel efficiently, but in fault zones and converging material they need some of the features of an EPB machine to keep advancing. Avoiding a stuck machine is paramount to project success. Luckily, DGS uses several ways to avoid the problem of a machine becoming stuck. The first of these is multi-speed cutterhead drives. These drives effectively give the machine multiple modes of operation—high speed, low torque for hard rock, and low speed, high torque for difficult ground. Designing a machine with high-torque, continuous boring capabilities allows that machine’s cutterhead to restart with break-out torque in difficult ground. The net effect is that the machine can keep boring in the event of a face collapse and can effectively bore through fault zones and running ground where the potential for cutterhead jamming exists. Going one step further, multi-speed gearboxes give the machine the ideal EPB-type torque if larger sections of soft ground are anticipated.
Secondly, TBMs can get through squeezing ground and faults using Continuous Shield Advance. This design utilizes a stepped shield configuration—where each successive shield is slightly smaller in diameter—to avoid becoming stuck in converging ground. External shield lubrication is an added insurance against becoming stuck, using a series of radial ports that can pump Bentonite into the annular space to act as a lubricant in squeezing material.
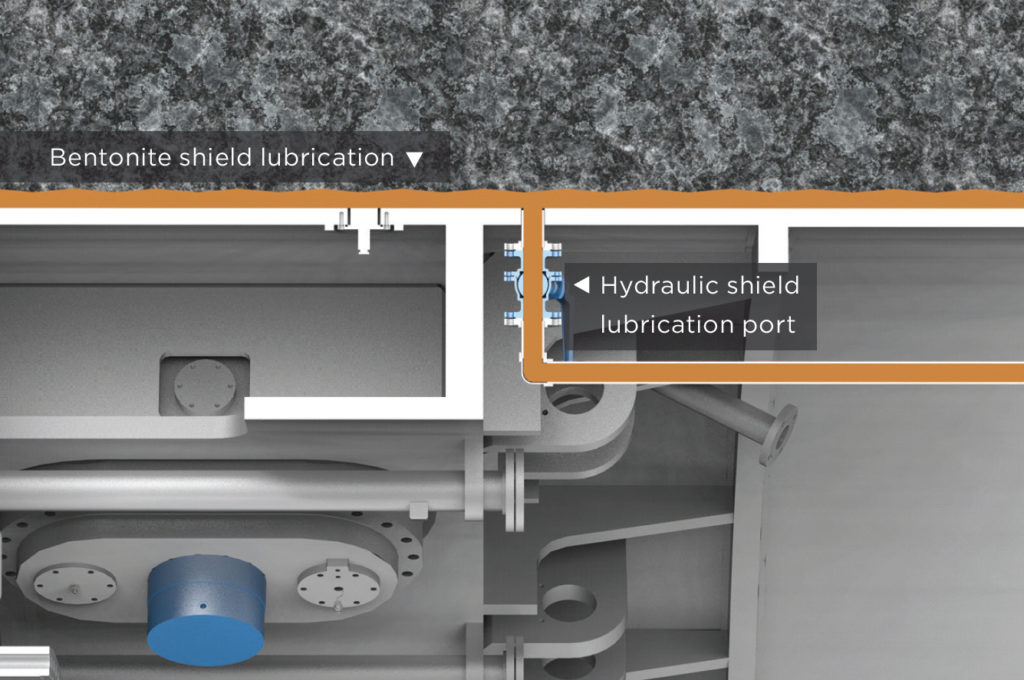
Hydraulic shield lubrication allows for Bentonite (orange) to be pumped into the annular gap.
As a last effort, if a machine has already become stuck the TBM can utilize augmented, or “super” thrust. Additional thrust jacks can be added to supply an extra boost in a short stroke, generating enough force to break loose a trapped shield.
Number 3: DGS can keep your crew safe and save your TBM in the event of a massive inrush of water.
Water is an ever-present part of tunneling underground, but unexpected large inflows can damage a machine and grind a TBM operation to a halt.
In the event of a large inrush of water, a guillotine gate on the muck chute can effectively seal off the muck chamber of a Single Shield TBM to keep the crew safe as well as keep the machine from becoming flooded out. This system is termed “passive” water protection because the TBM is stopped in place (not actively operating). During that time the crew can then work to grout off water inflows and dewater the chamber to control the flow before they begin boring again. The grouting crew also have the added assistance of back pressure to assist in grouting.
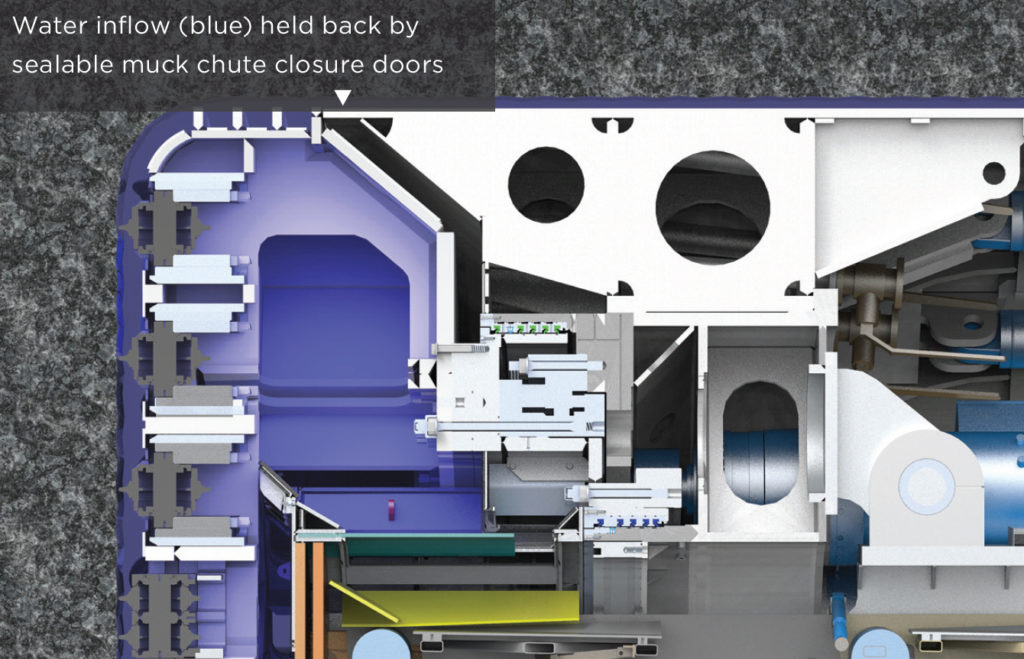
Water Inflow Control can passively seal a Single Shield TBM against water (blue) via a guillotine gate.
Number 4: DGS can improve your visualization of the ground around the TBM.
Probe drilling is an essential part of visualization, and, combined with grouting, it can also fall under the heading of water control. We’ve learned that, in difficult ground, more is better. Multiple probe drills, and more drill ports in a 360-degree radius, are always going to give an advantage. We’ve taken this lesson to heart, and have installed multiple probe drills on many of our new shielded machines, with ports to provide probing patterns in a 360-degree radius. High-pressure grout injection can be done through these same ports to stabilize ground up to 40 m ahead of the face (or more if using specialized drills). The type of grout injected can also be specialized—for example chemical or polymer grout can be used to seal off groundwater. Lastly, a rotary forepole drill can be installed behind the cutterhead support to allow for ground consolidation around the shield periphery. The forepole drill is of particular use in fractured rock and fault zones. These drills are the mainframe of a visualization plan that can ultimately create an in-tunnel GBR as the machine advances: of particular use when no accurate GBR can be created due to topography, high cover, etc.
But what if you suspect the ground around your TBM is converging? What if you want to get a look at the actual rock face in the safest possible manner? There are DGS options for these types of visualization as well. For squeezing ground detection, a hydraulic cylinder can be mounted on top of the shield and connected to the TBM’s PLC. It measures the shield gap in the tunnel crown, so that if squeezing or collapsing ground is detected the crew can take countermeasures. These measures include using bentonite lubrication, crown or face rock conditioning, or planning ahead to use another system in the area before the machine can become stuck. For getting a better look at conditions ahead of the machine, a cutterhead inspection camera can be used to remotely inspect the boring cavity without intervention, and to check water levels ahead of the TBM. While these cameras have been used to monitor mixing chambers and perform cutterhead inspections in soft ground TBMs, their use in hard rock machines has been much more limited. In the new ground investigation system, the probe and injection holes in the cutterhead and front shield are specifically designed to accept these cameras.
Number 5: DGS can save you time and money.
The old adage “the best-laid plans can go astray” applies particularly well to tunneling. There are many unknowns, even with an adequate GBR in hand. Making an initial investment on DGS features when your TBM is still in the shop is far less costly than installing them in the tunnel after a major stoppage. These features can mean the difference between a successful operation and a stuck TBM requiring a bypass tunnel or worse. TBMs with DGS features also produce better advance rates in adverse conditions such as fault zones (see our recent projects Kargi and TEP II as good examples of this). Better advance rates mean your project is more likely to stay on schedule and on budget. And who wouldn’t want that?
Want to find out more about DGS and its successful use in the field?
Check out these white papers:
Difficult Ground Solutions: New TBM Solutions carve a path to Success
Complimentary Webinar: Reducing Risk—How to Manage the Unknown in TBM Tunneling
Let’s face it: tunneling projects are inherently risky. The actual geology can harbor unforeseen conditions even with rigorous testing, and even when a highly-qualified consulting company creates the Geotechnical Baseline Report. In TBM-driven tunnels, the machine and the crew operating it are key components of the risk management strategy. So, how can we ensure that the tunneling operation is done effectively as often as possible?
In this complimentary 60-minute webinar from the manufacturer perspective, Robbins Chief Engineer Dennis Ofiara and Project Engineer Elisa Comis will explore that question, delving into contract structure, TBM design, case studies, and more to find the answer. Whether you’re a contractor operating the TBM, a consultant specifying the equipment, or an owner with an upcoming project, risk reduction is possible in even the most complex tunnels.
Click to View Recording of Webinar
Robbins Double Shield Takes on Nepal’s First TBM Project for Bheri Babai
Nepal will welcome its first TBM ever this summer, a 5.06 m (16.6 ft) diameter Double Shield machine for the Bheri Babai Diversion Multipurpose Project (BBDMP). The Robbins TBM underwent its Factory Acceptance Testing in July 2017 and is currently being shipped to the jobsite in the Siwalik Range, part of the Southern Himalayan Mountains. Pre-construction, including laying gravel onto rural roads and excavating wells for drinking water, has been completed to make way for the TBM and its impending launch.
The BBDMP is one of Nepal’s 11 National Pride Projects–prioritized plans sanctioned by the Government of Nepal to further develop the mainly rural country. This project will irrigate 60,000 hectares (almost 15,000 acres) of land in the southern region of Nepal, benefitting an estimated 30,000 households. It will divert 40 cubic meters of water (1,400 cubic feet) per second from Bheri River to Babai River under a head of 150 m (492 ft) using a 15 m (49 ft) tall dam, providing year-round irrigation in the surrounding Banke and Bardia districts. The water will also be used for hydroelectricity, with a generating capacity of 48 MW benefiting the country with NPR 2 billion (20 million USD) annually.
Contractor China Overseas Engineering Group Co. Ltd. Nepal Branch (COVEC Nepal Branch) is responsible for the headrace tunnel and is aware of the challenges associated with tunneling in tough geology. “The design of Robbins TBMs is good, and in particular Double Shield TBMs,” said Project Manager of BBDMP, Hu Tianran. The Siwalik range is projected to consist of mainly sandstone, mudstone and conglomerate, requiring a TBM that can withstand squeezing ground, rock instability, possibly high ingress of water and fault zones. Maximum cover above the tunnel is 820 m (0.5 mi).
Due to the challenges in the young geology of the Himalayas, Difficult Ground Solutions (DGS) have been incorporated into the machine’s design. A stepped shield has been designed to move through squeezing ground. Robbins Project Engineer Missy Isaman talked about the DGS features incorporated into the TBM: “There is a probe drill in the rear that probes through the gripper shield in 14 places. We added ports in the forward shield for drilling too. There are eight ports around the circumference for hand drilling. There are also six ports in the top 100 degrees of the shield for forepoling.” She further noted that no equipment was ordered for either of the forward shield drilling options, but it’s easier to add the ports to the shield now, in case more comprehensive drilling is needed later in the bore. Other machine modifications included 35 mm (70 mm on the diameter) of possible overcut for gage cutters, and additional ports in the forward shield for dewatering.
Muck removal will be achieved by muck cars. Robbins will provide Field Service to support the machine erection, testing, commissioning and boring of the first 500 m (1,640 ft). The tunnel will be lined with hexagonal precast concrete segments.
The project owner, the Government of Nepal’s Ministry of Irrigation (MOI), has chosen a TBM over the traditional method of Drill & Blast due to the faster mobilization and rate of advance offered by mechanized mining. “The reason a TBM was chosen for this project was because using D&B method could have taken at least 12 years for project completion. This was due to there only being one excavation heading with no possibility of launching multiple operations using adit tunnels,” said Robbins General Manager for Nepal, Prajwal Man Shrestha. More generally, Mr. Shrestha saw the project as a way to prove that TBMs can indeed take on complex Himalayan rock. “Since the Himalayan range has a young geology and not much has been surveyed yet, the use of newer technology is looked upon with slight apprehension. The first few TBM projects and additional surveys will show how suitable TBM technology will be for the Himalayan Range.”
The success of the BBDMP, a national pride project, is paramount for the country as well as the TBM industry. It is expected to help aide the food crisis in the mid-western region of Nepal by increasing agricultural yields and invigorating socio-economic development in the region. The Robbins TBM for the 12.2 km (7.5 mi) tunnel is scheduled to launch in November 2017.
AFTES 2017
Event Name: AFTES International Congress 2017
Dates: November 13-15, 2017
Location: Paris, France
Venue: Palais des Congrès
The Robbins Company will be joining NFM at this year’s French Tunnelling and Underground Space Association International Congress in Paris, France. Visit our shared booth from November 13-15, to discuss current projects and innovations within the industry.
ITA Tunneling Awards 2017
Event Name: ITA Tunneling Awards 2017
Date: November 15, 2017
Location: Paris, France
Venue: Salle Wagram
The Robbins Company is excited to announce that the recently completed Túnel Emisor Poniente (TEP) II has been nominated as an ITA Tunneling Awards finalist for Project of the Year. Winners will be announced at the ITA Tunneling Awards that will take place during the AFTES Congress in Paris, France on November 15.
The Robbins XRE TBM and its Robbins continuous conveyor system were built on location using Onsite First Time Assembly (OFTA), and featured components like a convertible cutterhead with interchangeable cutting tools, interchangeable TBM belt conveyor and screw conveyor, and multi-speed gearboxes to increase torque for tunneling through difficult ground. The 8.7 m (28.5 ft) diameter Robbins Crossover TBM bored a 5.8 km (3.6 mi) long wastewater tunnel, setting two national records in the process. The completed project will prevent flooding in urban areas and benefit the lives of 2.1 million people.
What’s in a Name? Mixshield, Crossover, Hybrid and More
For underground construction professionals and manufacturers, there is some confusion about the current TBM designations and what they really mean, and for what applications they are to be considered. This is especially noted when it comes to soft and mixed ground type shield machines and if they are to operate in “open” mode, “closed” mode or “semi-open/closed” mode conditions.
The term “open mode” defines defines a mode of TBM operation where no pressure is required to stabilize the boring face; the geology is self-standing and ground settlement will not occur.
The term “closed mode” defines tha mode of TBM operation where face pressure needs to be constantly applied in order to maintain face support. Should the face pressure not be maintained as determined by the geology, under-pressurization will cause ground settlement, over-pressurization can cause surface heaving.
The term “semi-open/closed mode” defines a mode of TBM operation in varying geology where the TBM has the ability to control the face.
The various machine types in question are Mixshield, Hybrid and the Robbins “Crossover”. Are they the same? If not, what is the difference? This blog seeks to clarify and explore those definitions.
Mixshield
Mixshield is a terminology introduced by German manufacturer Herrenknecht for what is essentially a Slurry TBM that uses an air bubble to control and support pressure at the face. The air bubble acts like an accumulator with the belief that this offers better pressure control. This type of machine operates only in “closed mode”. Mixshields are not meant to go from high pressure soft ground to significant rocky conditions with great efficiency, hence the name “Mixshield” is somewhat of a misnomer. They can excavate mixed face conditions, but the machine configuration is not changed so it is a different thing entirely than to excavate significant sections of differing geology. In order to change the configuration to allow more efficient operation in different sections of geology, a Hybrid machine is needed.
Hybrid, etc.
“Hybrid”, “Dual Mode”, and “Multi-Mode” are names developed by the industry to try and define machines that feature components of two different machine types. The most common types is a multi-mode between EPB with a screw conveyor (for operation in “closed mode” or “semi-closed mode”) and conversion to Rock Mode with the installation of a belt conveyor (for use in “open mode” operation). Typically, the only changes made to the machine are components such as cutting tools and muck removal method that can be switched out in the tunnel depending on ground conditions. The machines are used for large sections of vastly different geology in one tunnel, such as a section of clay followed by as significant section of rock. However these types of machines are typically designed as EPB machines and then converted, making them not very efficient for use in rock geology.
Robbins Crossover
The “Crossover Series” of TBMs was developed by Robbins in March 2015 using innovative design concepts to effectively excavate between different geologies. The Crossover Series is Robbins’ version of a Hybrid TBM but with many additional features to allow the TBM to effectively cross between different geology types. Operation of the machine can allow the machine to quickly change from “open mode” to “semi open/closed mode” and “closed mode.” The main types of Crossover TBM include the XRE (Crossover between Hard Rock and EPB), XSE (Crossover between Slurry and EPB) and XRS (Crossover between Hard Rock and Slurry). The features include interchangeable cutting tools; single direction and bi-directional cutterhead muck pick-up; multi-speed, multi-torque cutterhead drive systems; durable, abrasion resistant components on the cutterhead and screw conveyor; emergency thrust; tapered shields to reduce shield entrapment in squeezing ground; integrated probe/grout drill system for ground consolidation; and heavy steel construction with components designed for +12,000 hours of life, just to name a few.
The Crossover Series is suitable for tunnel projects that require the ability to excavate different types of geology efficiently with one machine, based on ground conditions. The TBM design is flexible enough to switch from one mode to another. Ultimately, Crossover Series machines are cost efficient in the long run, since the TBMs require less repair costs than a non-customized machine, and they can be used on multiple projects.
Based on the ground situation (whether it’s self-supporting ground, self-supporting ground with water pressure, or unstable ground), the Crossover is optimized towards “open” mode (as in hard rock shielded TBMs) or “closed” mode (as in compressed air, slurry, and EPB TBMs).
Reliable geological information is therefore critical to the TBM design. An accurate geological report is needed to decide when and where to convert the machine as well. During excavation, adequate probe drilling is further essential to determine the ground conditions ahead of the Crossover TBM.
Below are the features specific to each type of Crossover machine.
Crossover XRE
- Mixed ground cutterhead: with disc cutters & soft ground tools or a combination of tools (interchangeable).
- Two-speed gearboxes: provide high torque at low RPM under soft ground conditions and high RPM under hard rock conditions.
- Cutterhead rotation: Single direction is more efficient in hard ground conditions and bi-directional is more efficient in soft ground to prevent roll.
Crossover XSE
- Equipped with both screw conveyor and slurry system for muck removal.
- Ground conditions: soft ground containing water under pressure (particularly for water pressures > 5 bar).
- The most universal of the Crossover machines, the XSE can bore in most types of ground.
Crossover XRS
- Highly adaptable to variable ground conditions; suitable for rock tunnels with water pressure > 5 bar.
- Hard rock machine with a rock cutterhead and slurry system in place.
- Capable of mining rock through high water pressure without grouting off water flows.
La tuneladora que pulveriza récords en Ciudad de México realiza el cale final
El 8 de julio de 2017, un selecto grupo de autoridades responsables del proyecto, incluido el presidente de México Enrique Peña Nieto, celebró el cale final de un titánico proyecto de construcción de túneles. La TBM Crossover Robbins de 8,7 m de diámetro es la primera de este tipo de máquinas híbridas que se utiliza en Norteamérica y puso el broche final al Túnel Emisor Poniente (TEP) II. La tuneladora, del tipo denominado XRE —un cruce o crossover (X) entre TBM para roca (R) y EPB (E)— logró sortear zonas de fallas, terrenos variables y bajas coberturas, entre otros obstáculos, para lograr un récord nacional de 57 m en un día, así como avances máximos de 231 m en una semana y 702 m en un mes.
«La XRE presenta la gran ventaja de estar diseñada para trabajar en modo abierto o cerrado (EPB), lo cual le permite excavar túneles tanto en suelo como en roca. Hemos comprobado que su rendimiento ha sido muy eficiente», afirmó el ingeniero Juan Alberto Herrera Moro y Castillo, responsable en el TEPII de la Conagua, la Comisión Nacional del Agua, propietaria del proyecto.
Se empleó el método de montaje in situ OFTA para ensamblar en la misma obra esta singular máquina y su sistema de cinta transportadora Robbins, que fueron diseñados para un consorcio contratista formado por Aldesem, Proacón y Recsa. La TBM XRE Robbins incorporaba componentes tales como una cabeza de corte convertible con herramientas de corte intercambiables, transportador de cinta y de tornillo intercambiables y reductoras de velocidad variable para aumentar el par con el fin de perforar túneles en terrenos difíciles. «Las ventajas del diseño residen en su excepcional potencia de empuje y en lo sencillo que resulta variar el par de la cabeza de corte, lo cual facilita mucho el proceso en el caso de que la máquina se quede atascada en un terreno dificultoso», comentó Alberto Martínez, jefe del departamento de construcción de túneles de Recsa.
La tuneladora XRE entró en servicio en agosto de 2015 para perforar el túnel de aguas residuales de 5,8 km de longitud. La máquina estaba configurada para roca dura y montaba cortadores de disco de 20 pulgadas (51 cm) de diámetro. A principios de 2016, la TBM la primera de varias zonas de contacto, una falla de 30 m de anchura de roca fracturada y en bloques. Si bien la excavación se ralentizó al atravesar la zona de contacto, el ritmo de avance se recobró en la roca andesítica, que presentaba una mayor competencia. Tras llevar a cabo un cale intermedio en marzo de 2016 para desembocar en un pozo de 80 metros de profundidad, seguido de un proceso de inspección y mantenimiento, la TBM siguió adelante.
En otoño de 2016, mientras excavaba en roca andesítica fracturada, la TBM se encontró con una caverna natural que, presumiblemente, se había originado por un desprendimiento de rocas en una zona de transición o por un lago subterráneo que había erosionado el material rocoso. La caverna tenía un tamaño estimado de 90 metros cúbicos e incluía una zona de suelo inestable de 57 metros cúbicos. Se detuvo la tuneladora y se adoptaron medidas inmediatas para estabilizar el terreno situado frente a la máquina con espuma de poliuretano antes de rellenar la caverna con una mezcla de gravilla y lechada.
A finales de octubre de 2016, la tuneladora alcanzó un trecho final de 900 m de longitud en terreno blando, donde se pasó al modo EPB. En este último tramo de túnel con baja cobertura, la distancia desde la parte superior del túnel a los cimientos de las viviendas llegaba a reducirse hasta los 4 m y el terreno presentaba la consistencia de un suelo reconsolidado. Para estabilizar los suelos blandos y minimizar el riesgo de que se produjera un asentamiento bajo la zona residencial, el personal de construcción de túnel perforó desde la superficie e instaló 890 micropilotes a intervalos de 1 m. «Fuimos capaces de lograrlo sin causar daños en las propiedades de los vecinos de las zonas aledañas al trazado del TEPII, ni en la carretera, ni en las infraestructuras urbanas instaladas en dicha zona», explicó el ingeniero Francisco Miguel López, jefe de obra en el TEPII del contratista Aldesa.
Con las excavaciones ya concluidas, se procederá a aplicar en el túnel un segundo revestimiento de hormigón con un espesor de 35 cm antes de que entre en servicio. El túnel de aguas residuales servirá para modernizar la actual infraestructura en zonas del extrarradio situadas al oeste de la Ciudad de México y para evitar las periódicas inundaciones en Valle Dorado. El túnel beneficiará especialmente a las ciudades de Cuautitlán Izcalli, Tlalnepantla y Atizapán de Zaragoza, que en conjunto albergan a 2,1 millones de habitantes.
Cutting Edge 2017
Event Name: Cutting Edge Conference
Dates: November 13-15, 2017
Location: Seattle, WA, USA
Venue: Renaissance Seattle Hotel
Join The Robbins Company at the Sixth Annual Cutting Edge Conference: Advances in Tunneling Technology November 13-15, in Seattle, WA. Visit our booth to learn more about current techniques being used on Robbins projects throughout the world.