Year: 2018
Complimentary Webinar: Achieve Steady Results in Unsteady Ground
If you’re tunneling in mixed face conditions, where any combination of rock and soil may be present in the tunnel cross section, you expect the project to be a challenge. When variability is a constant, things like surface settlement, abrasive wear on your TBM, and the proper ground conditioning are a concern. Despite these variables, your project can still be a success. With the right technology, crew, and operating methods, consistent TBM advance rates are achievable in even the most variable conditions.
In this complimentary 60-minute webinar, Robbins Vice President Doug Harding and Engineer Greg Michaelson will explore mixed face conditions, delving into recent case studies of EPB and Crossover TBMs in the field. Harding and Michaelson will make recommendations based on proven designs and methods, drawing from the experience of our knowledgeable field service personnel. Whether you’re a contractor operating the TBM, a consultant specifying the equipment, or an owner with an upcoming project, consistent excavation is possible in variable geology.
CLICK TO VIEW RECORDING OF WEBINAR
Fueled by Vietnamese Coffee: My Epic Adventure at Thuong Kon Tum
Traveling in the tunneling industry is basically a regular commute for some. A lot of us don’t think twice about the destination, we just do it with a mission in mind. My mission as Robbins Marketing Manager was this: a small conference in Ho Chi Minh City. Okay, easy! As the date approached, about a month before, I kept hearing about how well our Main Beam TBM was doing in Vietnam, at the Thuong Kon Tum Hydroelectric project, despite a gauntlet of challenges. I talked to some project engineers and field service personnel who told me it was in a remote location in Kon Tum Province. And then I heard more about traveling to that site: a 6-hour drive from Da Nang, through nauseating windy, narrow roads, climbing elevations with no speed limits to speak of. But that’s cool, I thought, glad I don’t have to go on that ride.
“Wait, why not just go to the jobsite for a video and photo shoot? We can have it ready for the breakthrough in October,” says Desiree Willis, Robbins PR manager a couple weeks later. What!? A few days after that, it was all planned. Ron, our videographer, Ken, our photographer, and Keri Lin, our marketing manager from Robbins China, set off with me on a last-minute adventure. The 17.4 km long Thuong Kon Tum HEPP tunnel will be the country’s longest once complete. A 4.5 m diameter Robbins Main Beam TBM and continuous conveyor system were supplied to bore a section of the tunnel.
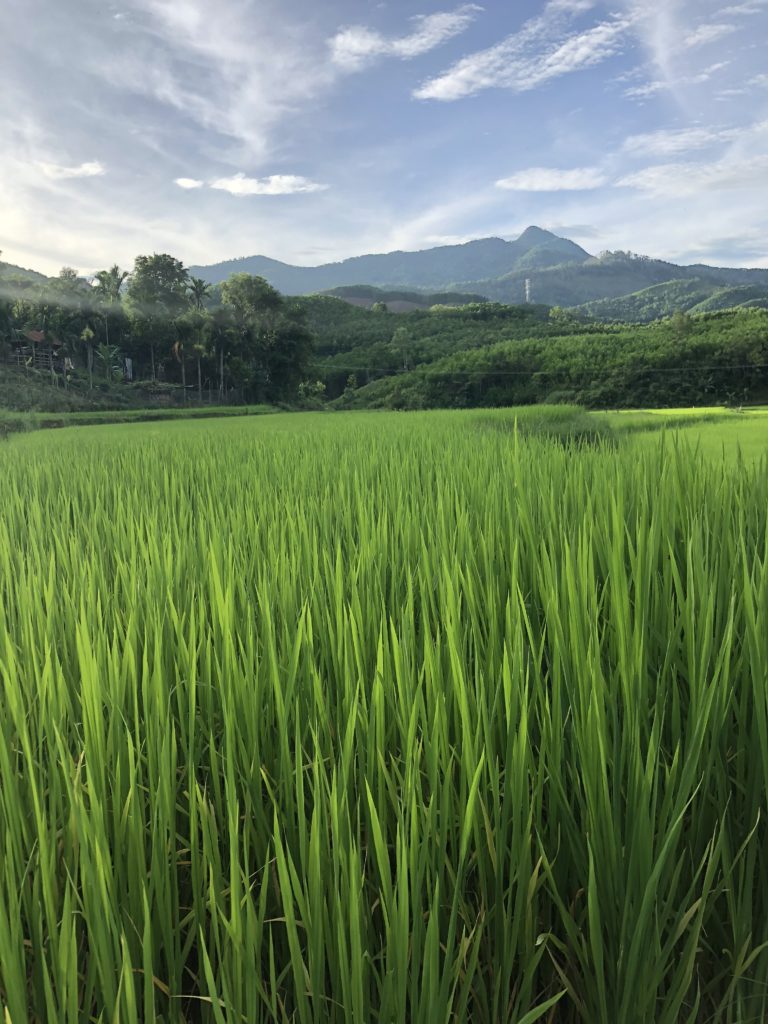
A terraced rice paddy with a beautiful mountain backdrop, so typical of what is synonymous with the sights of Vietnam.
Maybe because I was bracing myself for the worst as far as the drive goes, I didn’t feel like it was that bad. The scenery was jaw dropping with lush jungle, rice paddies and scenic villages, and so many distractions on the sides of the road that I just completely avoided looking ahead. Problem solved! The coolest distractions were the scooters driving on these mountain roads: what they were carrying, how many people were on them, their driving technique. My favorite site was seeing a whole family of people—a 5-year old kid in the front, the dad driving, the mom in the back and a toddler sandwiched in between the parents—on a run-down 125 cc scooter. Then there’s the animals: a litter of stray dogs, adorable black piglets making road crossings that almost made me swear off bacon, herds of cows, goats, etc.
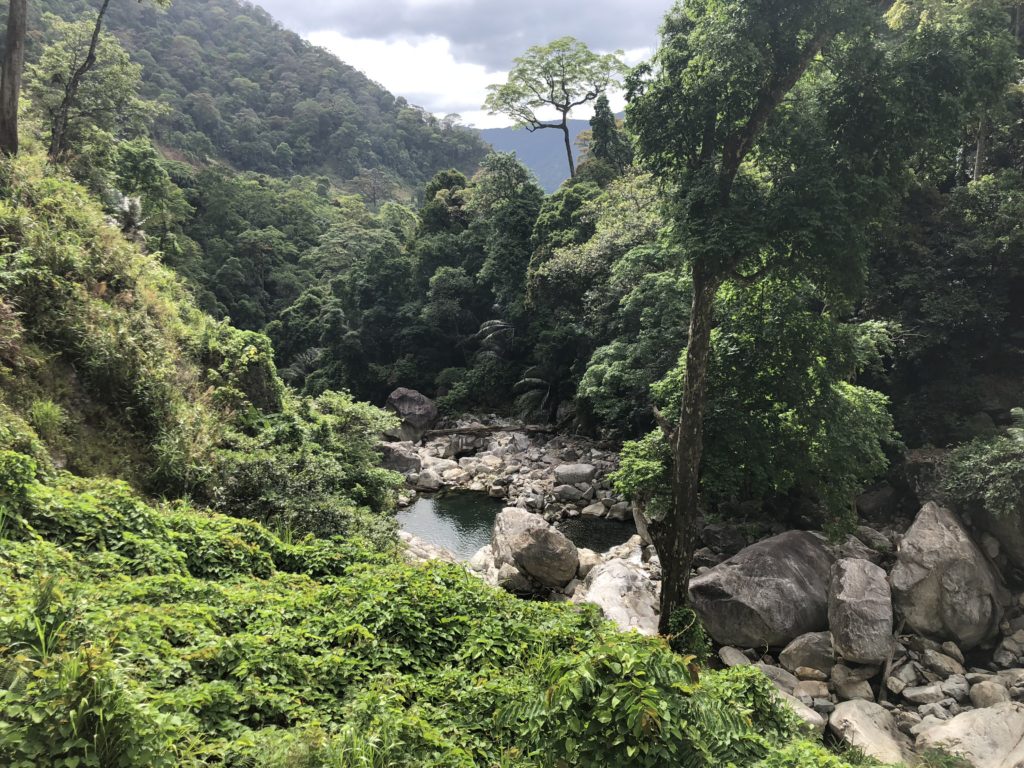
This was about a half hour away from the jobsite in Kon Tum province. The picture doesn’t truly depict how beautiful it was in person.
But how the heck did they get the machine, assembled by Onsite First Time Assembly (OFTA), to the site? Apparently, the previous contractor built portions of the roadway to the jobsite while components were staged at the port site. Several bridges, previously built only for light traffic with scooters and carts, were rebuilt or reinforced in order to carry the heavy TBM components. In a road conditions survey report by logistics firm SDV Vietnam Company Ltd., the original bridges were described as “having no shoulder”, and as having “blind corners and sharp curves”. The OFTA process allows a TBM to be assembled on location, saving time and money in terms of shipping costs and project schedule. The machine had successfully made it to the site, as it had launched in 2012.
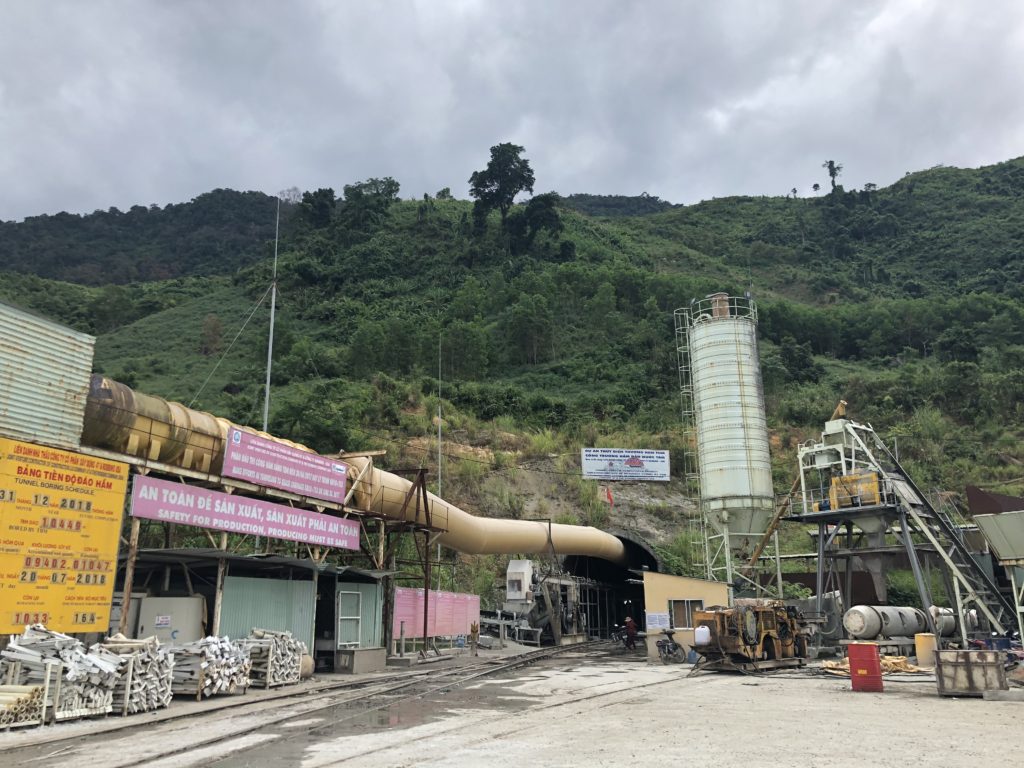
Not pictured: the litters of stray dogs and chickens roaming around the jobsite. Oddly enough, I never saw any stray cats here.
Upon arriving at the jobsite, I was immediately impressed with the site and the surroundings, especially after hearing about all of the challenges the project had back when the TBM was launched, under a different contractor. The TBM launched into complex rocky conditions that turned out to be quite different than in the original geological study. The machine sat abandoned 2.6 km into the tunnel with equipment sitting idle for months, waiting for a change in circumstances. In 2015, Robbins signed a contract with the project’s new contractor CC47 to supply full refurbishment and to operate the equipment with a full Field Service team. Since then, Robbins Field Service has generally been kicking butt.
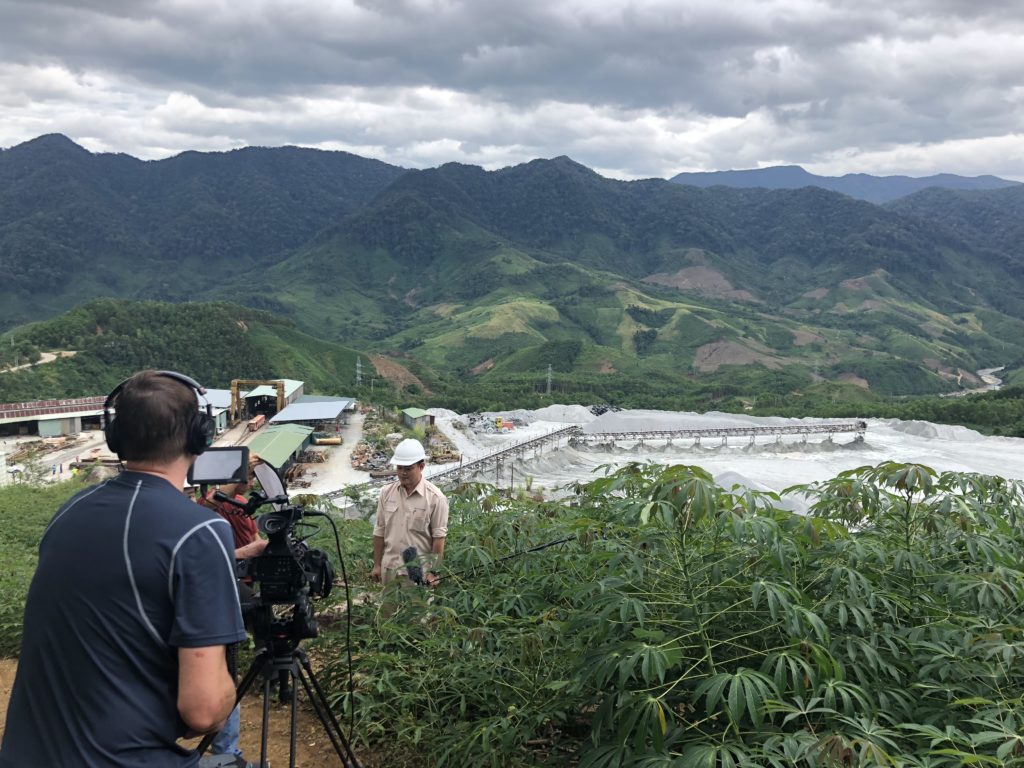
We hiked up a mountain to get this panoramic shot of the project site. I think it was worth it!
The machine was running as expected, so filming interviews and the machine went smoothly. I learned a lot from the interviews, mainly from the Robbins guys we interviewed—PN Madhan, Robbins Engineering Geologist, and Greg Adams, Robbins Field Service Manager. “It’s a workhorse of a machine and still in great condition, considering all of the difficult ground it’s been through,” Greg mentioned. Massive granitic rock wasn’t the only challenge they faced—the team also endured a handful of major fault zones requiring rock bolting and the use of the McNally Roof Support System, as well as some huge water inflows.
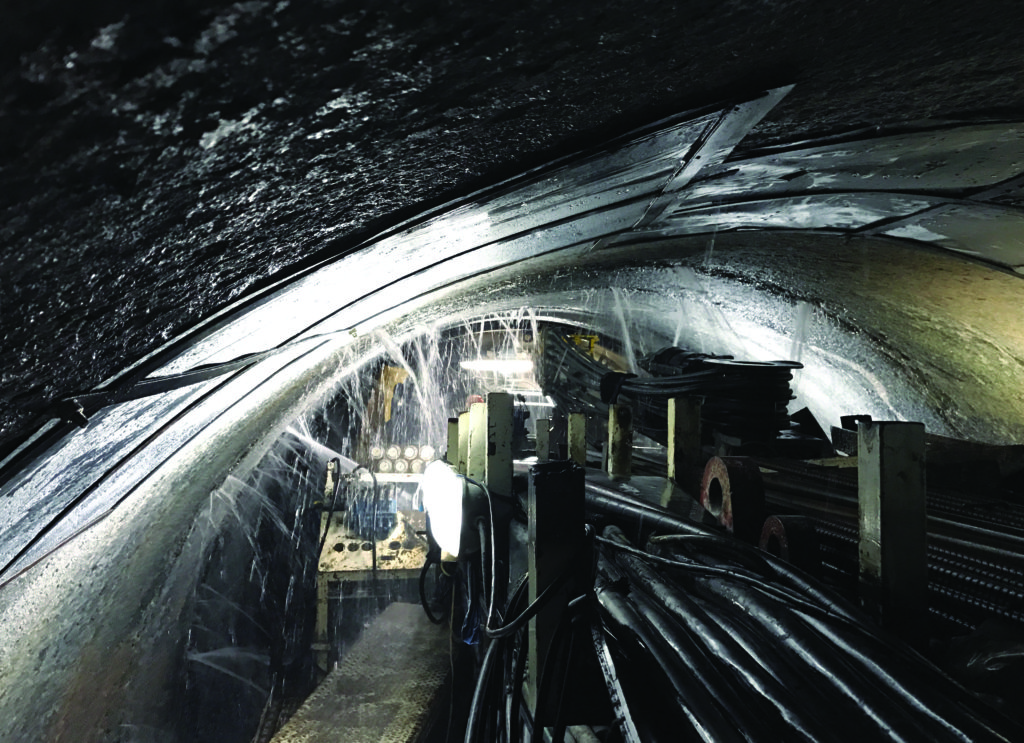
Water inflows were up to 600 liters per second—that’s nearly enough to fill an Olympic-sized swimming pool every hour!
Greg did warn our photographer and videographer that they were going to face heat with extremely high humidity. When John McNally, Robbins Field Service Manager-Asia, took over the project site, he managed refurbishment of much of the equipment inside the tunnel along with the camp’s living quarters. This included adding a ventilation tube, keeping the tunnel at a cool 34°C. That’s the temperature AFTER installing the ventilation. Read more about the challenges here.
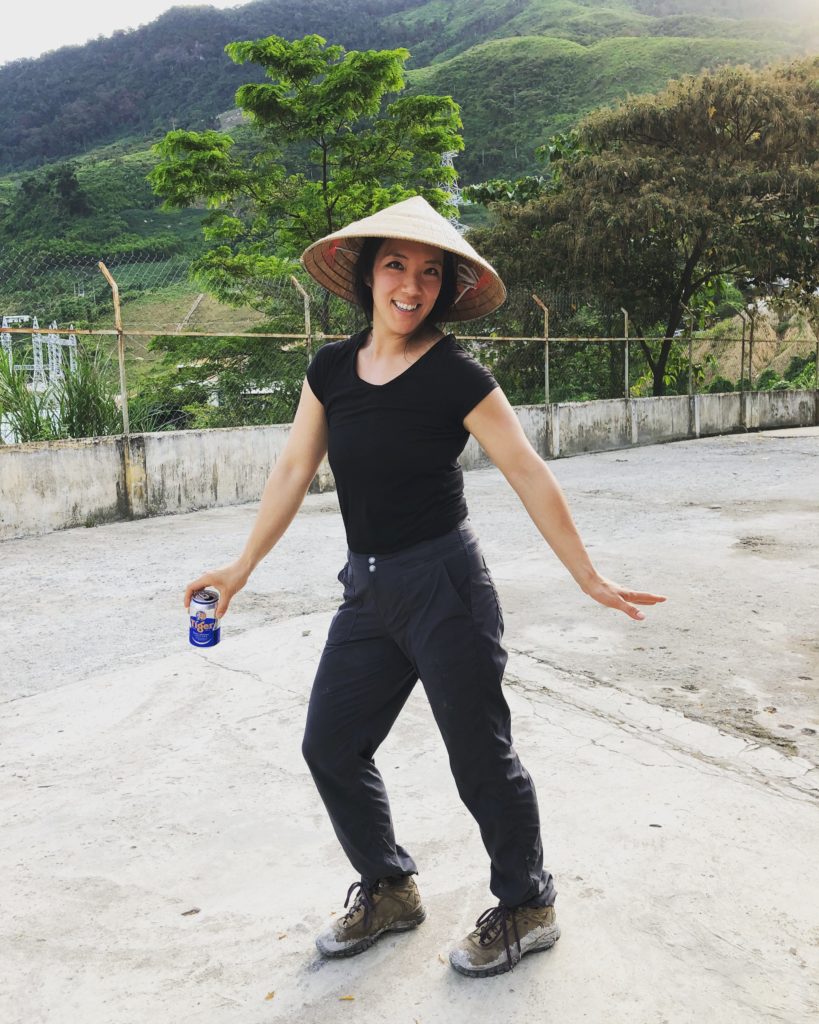
While waiting for dinner, I got posing tips from Keri Lin and our photographer for my next career as an Instagram model. A refreshing beverage and the typical Vietnamese farmer hat were absolutely necessary for the scorching hot day at the site.
The crew at the camp quarters, and the jobsite in general, were very welcoming. Greg and Taylor Hwang, Robbins project manager, arranged for a special dinner just for us on the first night—steak and French fries, an American staple! The crew on site mainly consists of English-speaking expats, Chinese, Thai, Vietnamese, Indian and Philippine guys, so the cuisine varied every day. We hung around that night for a while, listening to stories from some of the field service crew. This is while we were fawning over the pet falcon that one of the field service guys owned. I think the falcon liked living there, because his string wasn’t even tied to the perch at one point. Taylor told us that there were some families and children of the crew living there, who had to find ways to pass the time in this little remote village. He even told us they had pet monkeys at one point. I peeked into a living quarter and saw a drum set made with those Danish butter cookie tins that you get at Christmas. That’s one way to pass the time! Before we were about to leave, some of the Thai people at the site had brought in a bucket with a cover over it. I was curious and went to take a peek, because they started adding salt to the buckets. It was about 30 river snakes (possibly river eels, but they called them snakes) writhing violently because of the sodium touching their skin. Then they started preparing them one-by-one, sticking a nail into their heads and gutting them. It was quite mesmerizing, really.
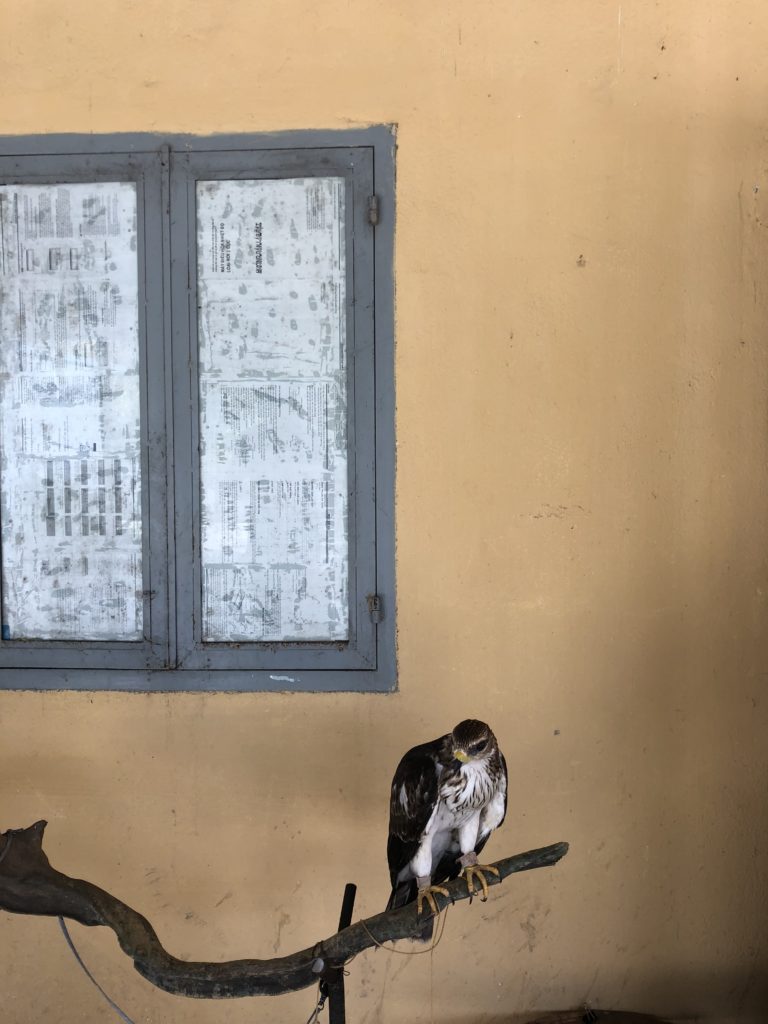
The camp’s pet falcon.
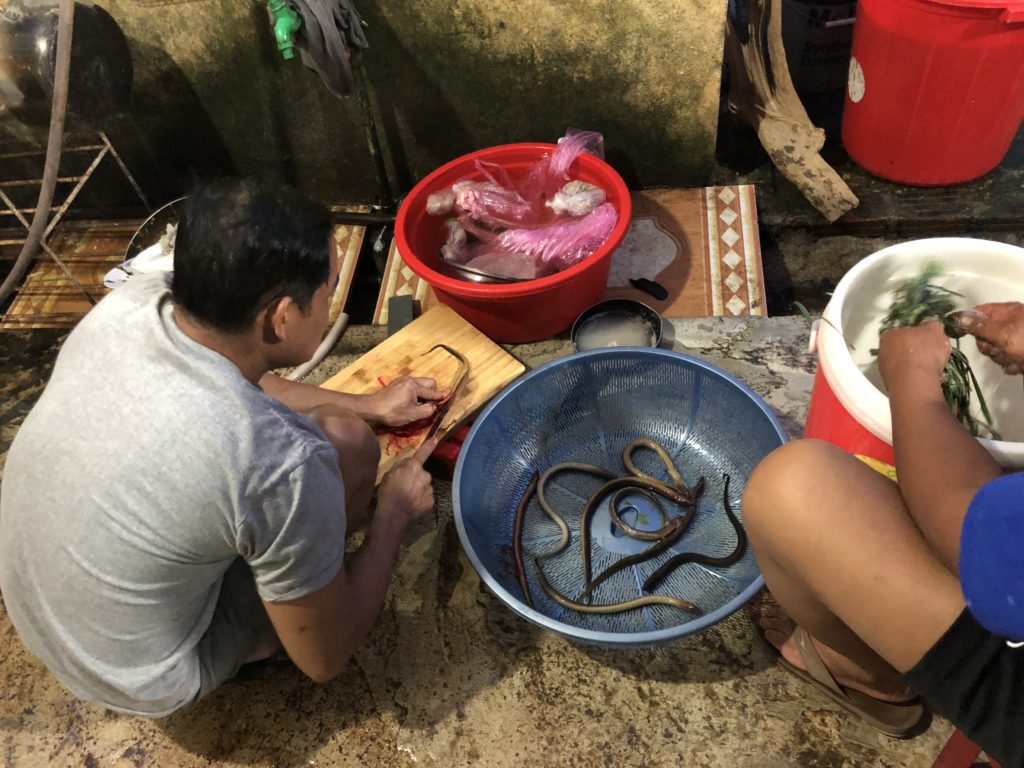
Not sure if this is the regional cuisine but the snakes were caught at a river close by the camp.
We only had two full days of shooting video and photos. Before the 6-hour drive back to Danang, all of us got caffeine-drunk on two strong Vietnamese coffees served with condensed milk each. I suspect it’s the perfect combination of the tenaciously strong espresso dripped into a puddle of pure sugar syrup (condensed milk) that singlehandedly causes adult ADHD from the first sip. During the drive down (which was much worse, I didn’t realize how much elevation we climbed going up), we were already reminiscing about the stories and experiences shared at the jobsite. When talking to the field service crew, they were all excited for the coming breakthrough later this year, but it seemed they were just a bit melancholy too. They were at this site for years, in a tiny remote village in the mountains of Vietnam, building friendships and routines. With only a handful of meters left to go on the tunnel, they’ll soon be off to the different parts of the world where they came from. I’m fortunate to have experienced everything I did on this trip and can’t wait to come back to this beautiful country.
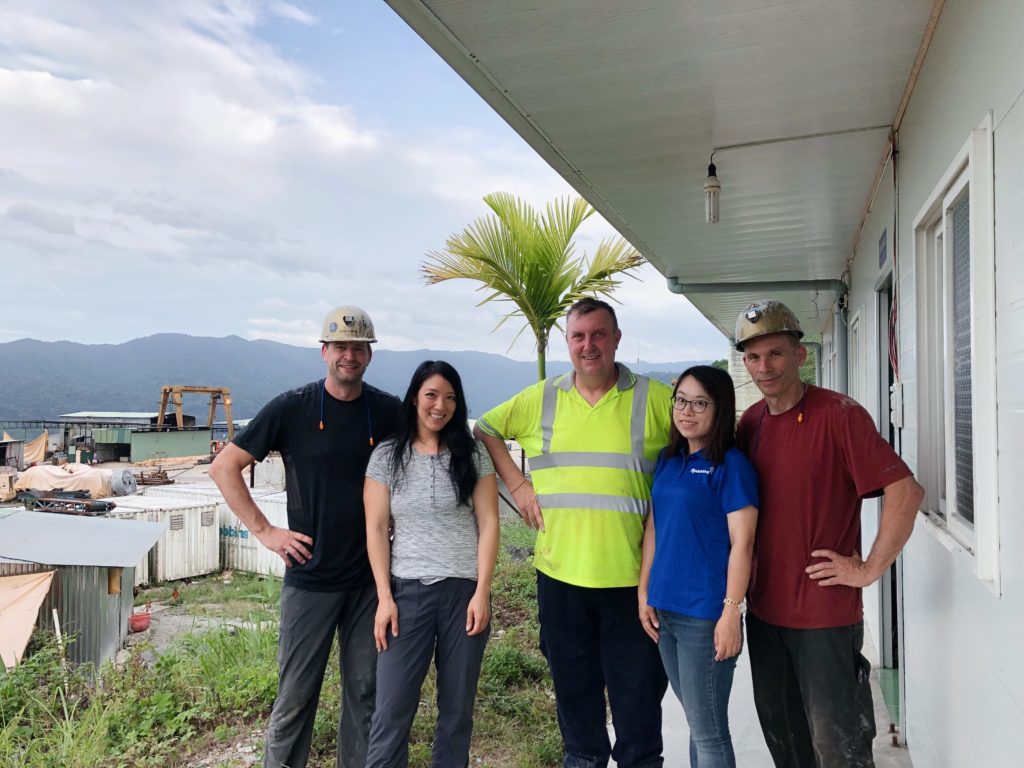
(From left): Ron (videographer), me, Greg Adams (Field Service Manager), Keri Lin (Marketing Manager for Robbins China), and Ken (Photographer) at the end of the shoot.
Robbins Crossover TBM “Rosie” Makes Breakthrough at Akron OCIT
On August 29, 2018, a 9.26 m (30.4 ft) diameter Robbins Crossover (XRE) TBM crossed the finish line at the Akron Ohio Canal Interceptor Tunnel (OCIT). A press day followed on September 5, where companies and members of the media were invited to view the giant machine. The machine—dubbed “Rosie” in honor of Rosie the Riveter, an icon representing American women who worked in factories and shipyards during World War II—overcame tough ground conditions during the bore.
“One of the most challenging aspects of this job was that we launched right into the most difficult part. We had 60 m (200 ft) of soft ground, a very short reach, and then from there we went right into a mixed face for 180 m (600 ft),” said David Chastka, Project Manager for Kenny Construction, a joint venture contractor on the project with Obayashi. “It took everybody we had in the industry, everybody from Robbins, to fight through that first 240 m (800 ft).”
The TBM was designed for the project’s geology, which transitioned from soil to partial face shale to full face shale rock. The Crossover XRE included features of both EPB and Hard Rock Single Shield TBM types, with a versatile cutterhead that could be configured for hard rock or soft ground conditions. While in soft ground and mixed face conditions the machine operated in closed mode, but once it hit solid rock crews switched excavation to open mode.“The machine had the power to get to the other side and made advance rates we never thought we were going to get. It was very successful in hard rock,” said Chastka. Advance rates once in full-face shale rock reached a high of 34 m (111 ft) in one day (two 10-hour shifts). Muck removal was achieved using a Robbins continuous conveyor, and conveyor availability remained high throughout the project.
“I am most proud of the team that I have had the pleasure of being a part of,” said Don Smida, Robbins Field Service Technician. “The overall scope of a project of this scale is immense, and the amount of daily cooperation & hard work that has been asked of The Robbins Company, the local unions, city staff, and Kenny-Obayashi is extremely important in reaching our common goals. I think we should all be proud of our teamwork going forward from a successful completion of the tunnel and into a successful disassembly of Rosie.”
Now that tunneling is complete, the machine will be disassembled and removed from its retrieval shaft this autumn. “The Ohio Canal Interceptor Tunnel is the largest public improvement project in our City’s history and a significant investment in our environment and infrastructure that will benefit Akron residents and businesses for generations to come,” said the City of Akron’s Mayor Daniel Horrigan. “Projects of this kind are inherently dangerous, and I am incredibly proud that the tunneling portion was completed without any major injuries, thanks to a dedicated team of professionals. And although Robbins is an international company with worldwide impact, we were pleased to be able to work with a local Northeast Ohio firm on this significant project.”
The OCIT Project for the City of Akron, Ohio, USA consists of the construction of a conveyance and storage tunnel system to control Combined Sewer Overflows (CSOs) for several regulators in the downtown Akron area. The EPA-mandated project includes the 1.89 km (1.17 mi) conveyance and storage tunnel, as well as drop shafts, diversion structures, consolidation sewers, and related structures.
Moving Projects Forward: Ohio Canal Interceptor Tunnel
Robbins and joint venture contractor Kenny/Obayashi worked together to achieve a short startup schedule at the Akron Ohio Canal Interceptor Tunnel. Field Service personnel assisted in TBM assembly and trained crews to achieve a smooth startup. Watch this short for a quick word from Kenny Construction’s Project Manager David Chastka on working with Robbins Field Service.
Overcoming Tough Ground: Akron Ohio Canal Interceptor Tunnel
In this short video, David Chastka, Kenny Construction Project Manager, discusses how Robbins Field Service and his team surmounted the challenge of launching immediately into difficult ground at the Akron Ohio Canal Interceptor Tunnel.
TAC/NASTT-NW Tunnelling & Trenchless Conference
Event Name: TAC/NASTT-NW Tunnelling & Trenchless Conference
Dates: November 8-9
Location: Edmonton, AB, Canada
Venue: Fantasyland Hotel at the West Edmonton Mall
Robbins Utility Tunneling Manager, Tom Fuerst, will be presenting “Lessons Learned at Montreal’s Rue Jarry Project: Overcoming Flooding and Rebuilding a TBM to Finish on Schedule,” at this year’s TAC/NASTT-NW Tunneling & Trenchless Conference. The show will be held on November 8 and 9 in Edmonton, Alberta.
Cutting Edge 2018
Event Name: Cutting Edge 2018
Dates: October 29-31, 2018
Location: Atlanta, Georgia
Venue: Lowes Atlanta Hotel
The Robbins Company is heading south for Cutting Edge, which is being held this year in Atlanta, Georgia from October 29 through 31. Visit table 7 between presentations, including a panel discussion with Robbins President Lok Home and a presentation by Robbins Director of Engineering Brad Grothen, to discuss current projects and tunneling techniques.
Difficult Ground Brochure
Even in the most well-planned projects, tough conditions can come up. Everything from squeezing ground to fault zones to sudden inflows of water and mud can delay your project significantly. Find out how our field service teams have dealt with the most challenging
conditions worldwide.
What's Going On? A Worldwide Roundup of Robbins Jobsites
At any given time, Robbins TBMs are operating at dozens of jobsites around the world. Our dedicated Field Service personnel take video and pictures of the TBM progress often, so we’ve decided to offer a periodic roundup of what’s going on in a picture-based blog–from machine assembly for India’s Mumbai Metro to extremely hard rock encountered in Vietnam. Read on to found out the latest.
SIMULTANEOUS BUILDS FOR MUMBAI METRO
Mumbai, India’s massive Metro Line 3 project requires multiple TBMs on various contracts. A total of four Robbins TBMs will bore on two separate contracts–two 6.65 m (21.8 ft) Crossover (XRE) TBMs for contract UGC-01, and two 6.65 m (21.8 ft) Slurry TBMs for contract UGC-03. Assembly of the first Crossover TBM and the first Slurry TBM on each contract are occurring simultaneously, and are being overseen by our experienced Field Service crews.
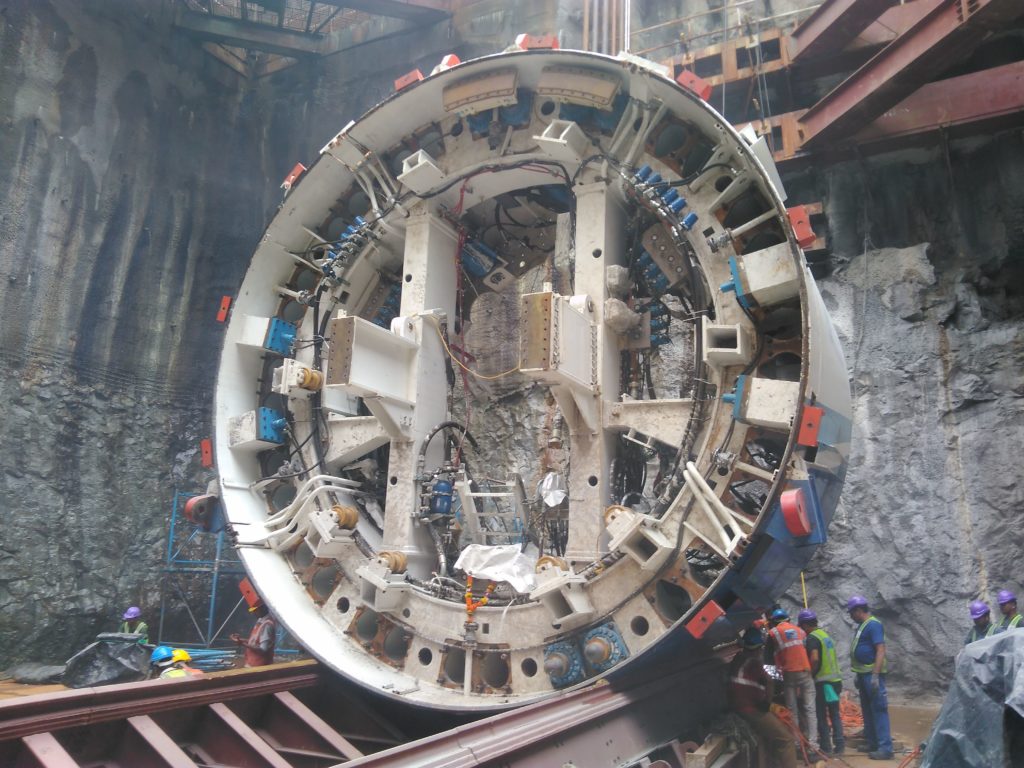
Crews position a section of the first of two Crossover (XRE) TBMs for the Mumbai Metro Line 3. Photo: Colin Ferguson
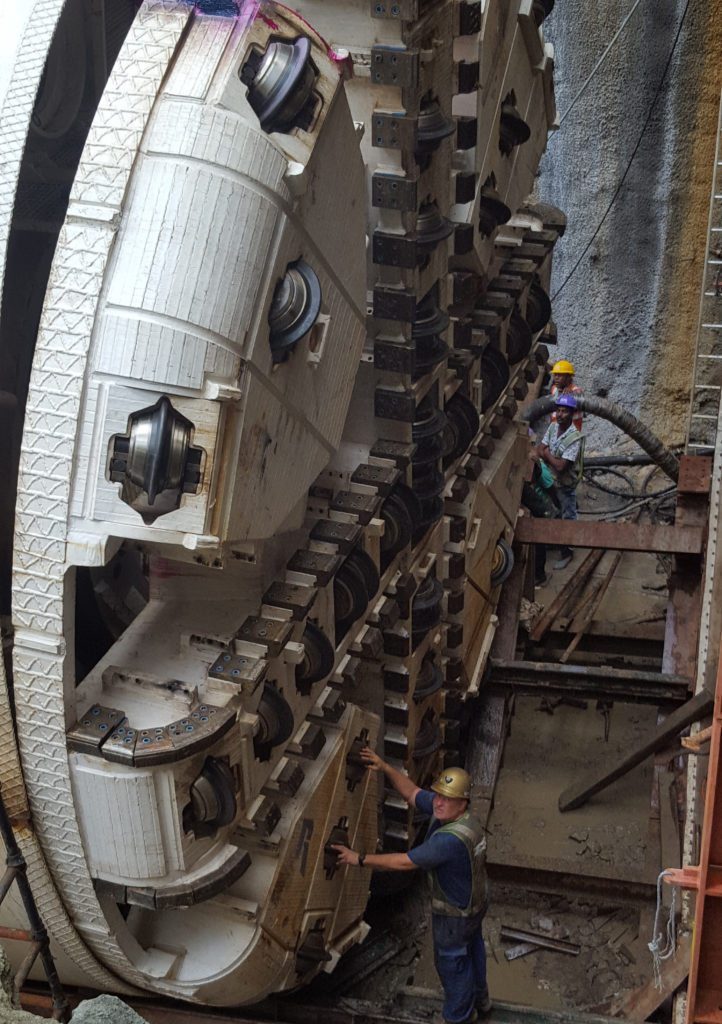
Crews assemble a Slurry TBM for the Mumbai Metro Line 3, and inspect the cutterhead. Photo: Colin Ferguson
EXTREME HARD ROCK IN VIETNAM
Robbins Field Service crews operating the Main Beam TBM at Vietnam’s Thuong Kon Tum HEPP have encountered granitic rock exceeding 300 MPa UCS and high water inflows. Despite the challenges the tunnel is more than 85% complete.
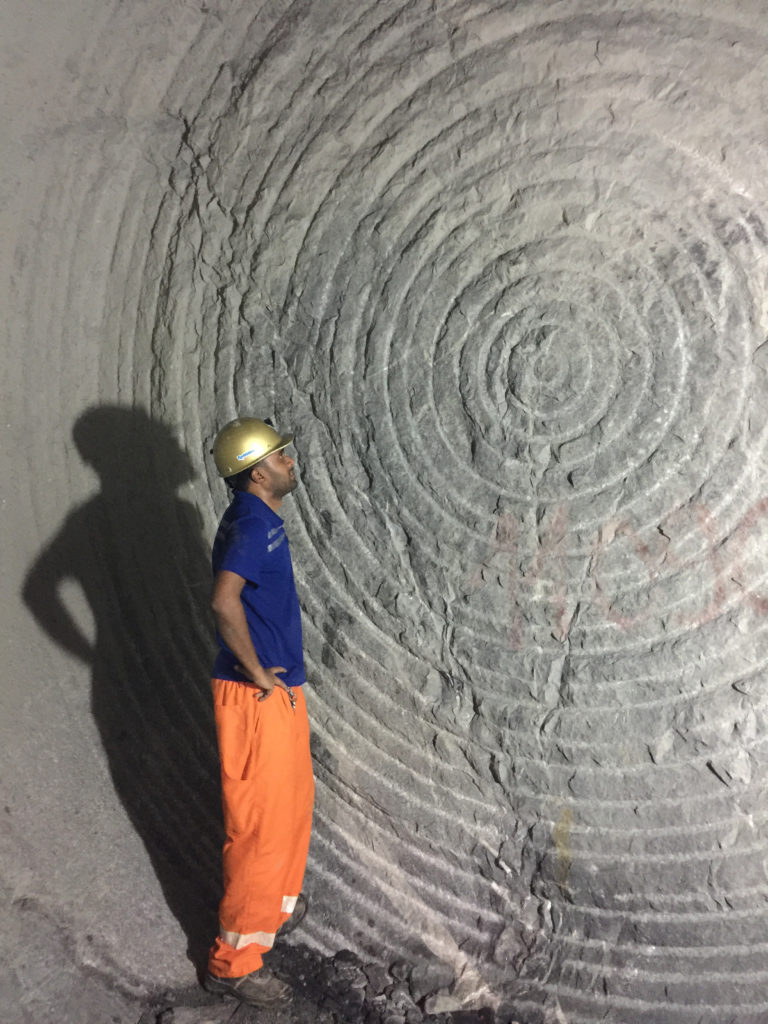
Robbins Engineering Geologist for Field Service, PN Madhan, inspects the massive granitic rock ahead of the TBM at Vietnam’s Thuong Kon Tum HEPP.
AN EPIC PROJECT IN MEXICO
With one of three Robbins lots completed at Mexico City’s massive 62 km (39 mi) Emisor Oriente tunnel, Field Service efforts are focused on completing Lots 4 and 5 in difficult mixed ground conditions. The customized EPB TBMs are boring through some of the most challenging conditions in the world, from abrasive basalt to watery clays and boulders.
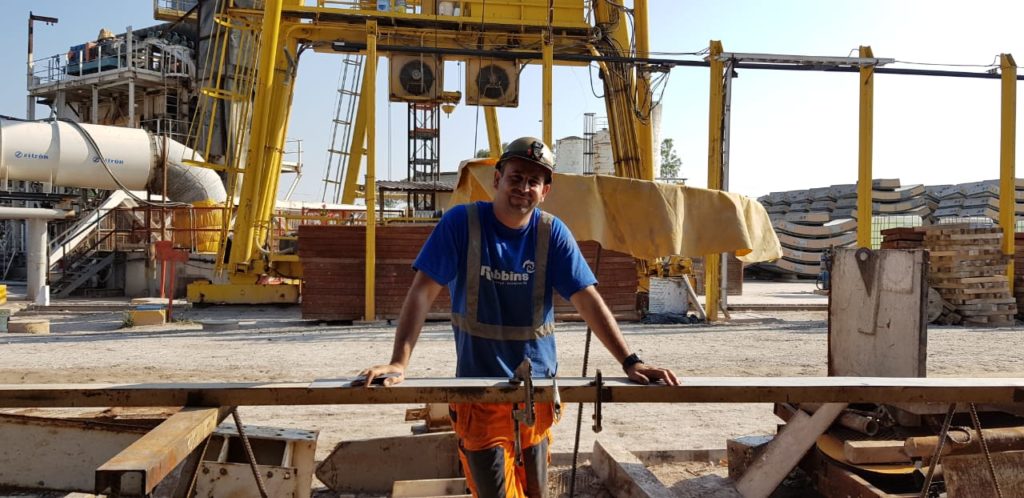
Alfredo Garrido Baena is part of the dedicated Field Service crew focusing efforts on completing Lots 4 and 5 in challenging conditions at Mexico City’s Emisor Oriente tunnel.
A JOB WELL DONE IN ALBANIA
TBM assembly and breakthrough is often discussed, but disassembly can be just as complicated. Following the recent breakthrough of the Crossover (XRE) TBM in Albania (the first machine of its kind in Europe) for the Moglicë Headrace Tunnel, Field Service crews are working to disassemble the machine in an underground launch chamber.
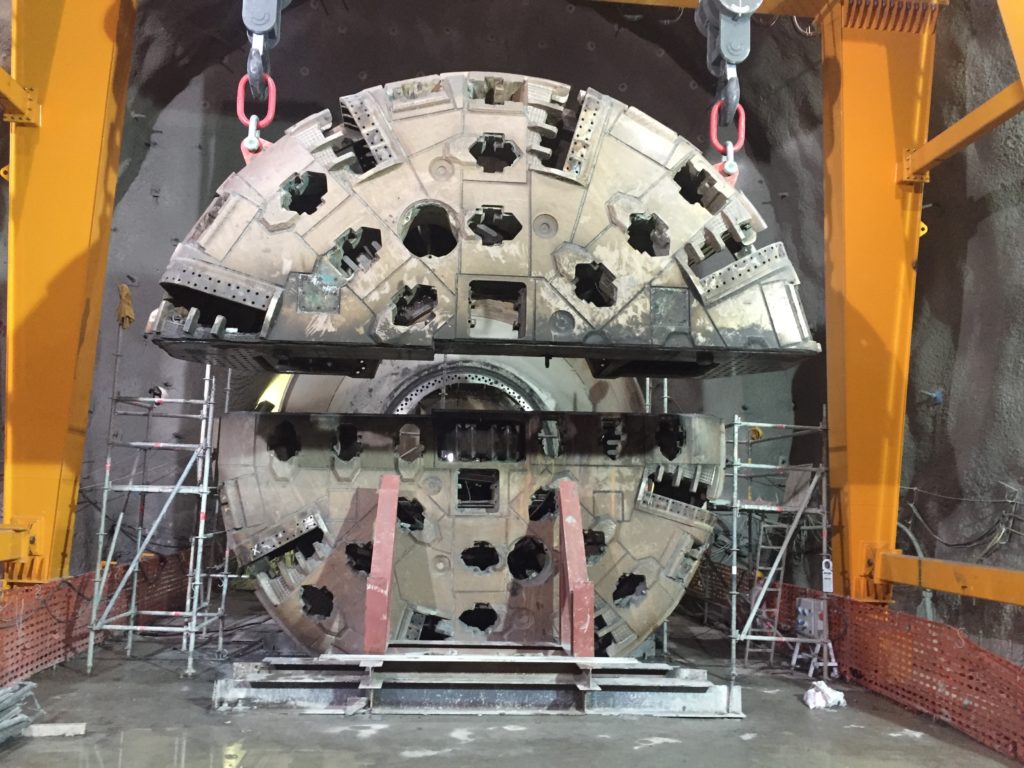
Crews separate the cutterhead of the Crossover TBM in an underground chamber in Devoll, Albania. Photo: Andy Birch
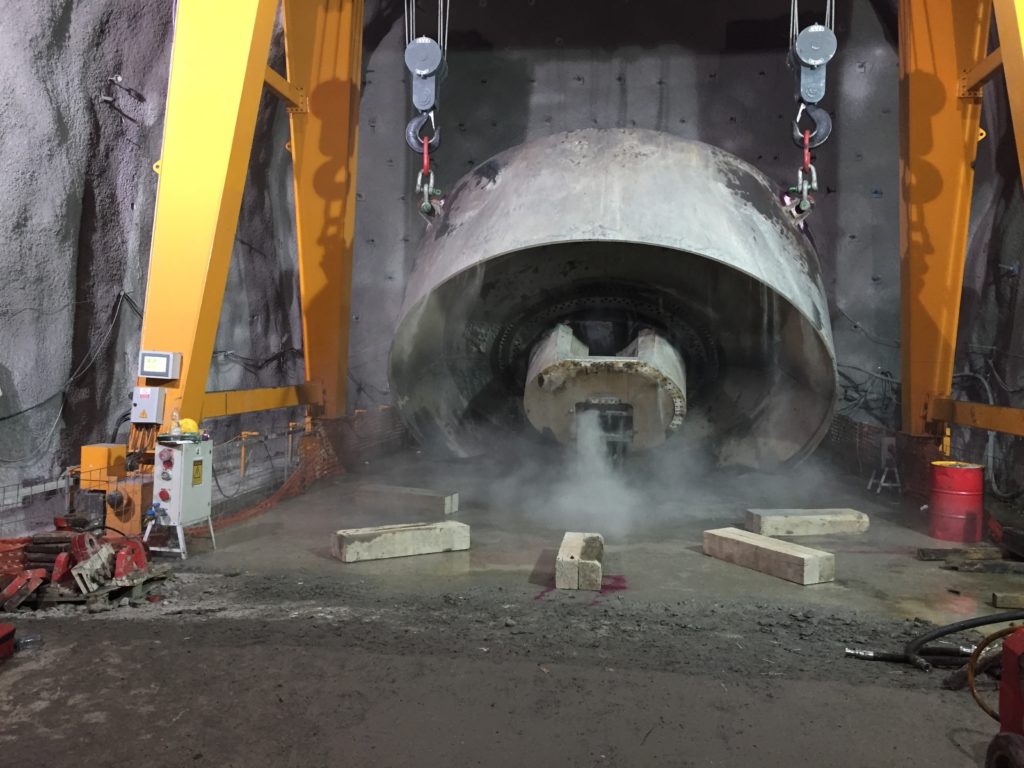
The forward shield is turned during disassembly of the TBM, which broke through in May of this year. Photo: Andy Birch
Nepal’s First TBM bores 1,000 Meters in One Month
Nepal’s first tunnel boring machine, a 5.06 m (16.6 ft) diameter Robbins Double Shield, is living up to the nation’s high expectations. The TBM, supplied in summer 2017 for the Bheri Babai Diversion Multipurpose Project (BBDMP), recently bored over 1,000 m (3,280 ft) in one month and has been averaging an impressive 800 m (2,630 ft) per month. The project is owned by the Government of Nepal’s Department of Irrigation (DOI) and operated by contractor China Overseas Engineering Group Co. Ltd. Nepal Branch (COVEC Nepal).
The decision to use a TBM for the BBDMP project—designated by the government as one of Nepal’s 11 National Pride Projects—was a departure for a nation where drill & blast has long been the preferred tunneling method. Early studies done on the tunnel path predicted that drill & blast excavation of the 12.2 km (7.5 mi) tunnel would take close to 12 years to complete. The tunnel is located in the Siwalik Range, part of the Southern Himalayan Mountains, where geology consists of mainly sandstone, mudstone, and conglomerate.
Mr. Wang Wu Shui, General Manager for COVEC Nepal, cited several factors that have contributed to the good advance rates so far, “In China, there is a proverb about TBM construction: ‘geology is the premise, equipment is the foundation, and talents are the key’. The great advance rates achieved at present mainly lie in preliminary planning, process control, and professional construction personnel.” Shui added that technical training and guidance are provided for each position so that all personnel can fully understand their job and team responsibilities. If unforeseen circumstances arise and there is no operator for a certain position, others have enough training to fill the role.
To ensure the best TBM performance and to prevent downtime, machine maintenance occurs daily at a fixed time. Geological engineers are sent to analyze the ground conditions twice daily so that construction personnel can adjust the tunneling parameters and prepare for auxiliary measures if geological changes are predicted.
The ground conditions during the record-setting month consisted mainly of sandstone and mudstone, but that is set to change. At about the 5.8 km mark, the machine will encounter a major fault zone known as the Bheri Thrust. Clay and water ingress are expected throughout the fault, which is about 400 to 600 m wide.
COVEC Nepal are prepared for the conditions and have worked out efficient tunneling logistics to decrease downtime. “The two working procedures of tunneling and segment erection are carried out simultaneously under the double shield tunneling mode, and the time to erect a ring of segments is 15 minutes in general,” said Shui. “Under the single shield tunneling mode, segment erection comes after tunneling in a sequential process, but the segment erection time is still about 15 minutes.” To further reduce time, consolidation grouting is carried out in advance during daily maintenance to avoid the impact of downtime for grouting on the overall construction progress.
Once complete, the BBDMP will irrigate 60,000 hectares of land in the southern region of Nepal, and benefit an estimated 30,000 households. It will divert 40 cubic meters (1,400 cubic feet) of water per second from Bheri River to Babai River under a head of 150 m (490 ft) using a 15 m (49 ft) tall dam, providing year-round irrigation in the surrounding Banke and Bardia districts. The water will also be used for hydroelectricity, with a generating capacity of 48 MW benefiting the country with NPR 2 billion (20 million USD) annually. The initial success of the TBM operation has already inspired developers and contractors to opt for TBMs over conventional excavation methods on upcoming Nepalese tunnels.