Year: 2018
Twin Robbins Crossover TBMs to bore on Mumbai Metro Line 3
On June 11, 2018, a Robbins Crossover XRE destined for Line 3 of India’s Mumbai Metro arrived in Mumbai port following a successful factory acceptance test in April. The machine, combining features of a hard rock Single Shield TBM and an Earth Pressure Balance Machine, is one of two 6.65 m (21.8 ft) Crossover machines that will bore under contract UGC-01. Operation of these two machines will be carried out by Larsen & Toubro, part of the Larsen & Toubro -Shanghai Tunnel Engineering Co Joint Venture (L&T-STEC JV). The Robbins Company will provide key personnel for the initial boring phase. “During the factory acceptance testing, we observed that the machine and back-up system are robust enough for hard rock tunneling,” stated Palwinder Singh, Head of Tunnel Operations for L&T-STEC JV.
During the bores, consisting of parallel 2.8 km (1.7 mi long) tunnels, geologic conditions will include mixed ground and possible water pressures up to 2 bar. According to Singh, “A Crossover XRE was chosen because of the expected geology,” which includes basalt rock and transition zones consisting of black carbonaceous shale, tuff, and breccia. Rock strengths are anticipated to range between 15 MPa and 125 MPa (2,200 and 18,100 psi) UCS. The machines will bore with only 15 to 20 m (50 to 70 ft) of cover above the tunnel and the structure will be lined with reinforced concrete segments in a 5+1 arrangement.
The metro tunnels will run between the Cuffe Parade Station and Hutatma Chowk station, passing through the Vidhan Bhavan and Church Stations. Both Crossover machines will be launched from the same 25 m (82 ft) deep by 22 m (72 ft) long shaft at the Cuffe Parade Station. “The limited length of the shaft requires running the TBMs for the first 100 m (328 ft) with some or all the back-up decks at the surface,” said JP Bayart, Robbins Project Engineer. “The TBMs and back-up systems are connected with umbilical cables and hoses.”
The TBMs will begin their excavation in hard rock mode. “Each cutterhead is optimized for operation in rock, as this is what is expected. The machines can also operate in soft ground thanks to the screw conveyor with bulkhead gate and discharge gate,” said Bayart. “The Robbins Torque-Shift System, consisting of two-speed shifting gearboxes coupled to the main drive motors, allows for the high cutterhead torque required for soft ground operation.” The face of each machine is equipped with six muck buckets and six large internal muck loading plates. This design, in combination with the screw conveyor located at the centerline of each machine, will allow for the option of fully emptying the cutterhead chamber, resulting in minimal wear when EPB mode is not required. Muck will be removed from the tunnels via muck cars.
Assembly and launch preparations for the first XRE TBM began on 20 June and are estimated to take about six weeks. The second Robbins XRE TBM underwent factory acceptance testing at the end of May and will arrive at the jobsite at the end of July for its assembly. “Our target is to achieve an average of 250 m (820 ft) of boring per month,” said Jim Clark, Robbins Projects Manager India. “The target to complete the boring operations is 20 months, which includes the additional time required for the short start-up using umbilicals on the initial drives, dragging the machines and re-launching through three stations.” Contractor L&T plans to work crews on double shifts to cover a full day of operations in order to keep to this timeline. The machines will join two Robbins Slurry machines boring a separate contract of the Mumbai Metro Line 3. The first of those machines will be launching in August 2018. The Metro Line 3 project as a whole is estimated to be completed by 2021.
The Risks Associated with TBM Procurement and the Next Steps Towards Industry Change
Risk management in the world of TBM tunneling is, in itself, a risky business. The underground often presents obstacles and complex projects spanning miles of tunnel multiply those risks. However, there are ways to manage and reduce risk in our industry; i.e., by ensuring that thorough geotechnical studies are done and that contingency plans are in place. The TBM itself can be designed with risk reduction in mind, using tools that expand visualization of the ground around the machine and arm the contractor with ways to get through challenging ground conditions with minimal delays. This paper explores risk in TBM tunneling from the viewpoints of the consultant, the contractor, and the equipment manufacturer. It also seeks to make recommendations as to how risk can be better managed in today’s tunneling industry.
Boring Hard, Abrasive Gneiss with a Main Beam TBM at the Atlanta Water Supply Program
Atlanta, Georgia’s water supply program is a priority project involving a 5.0-mile long tunnel connecting up with the Chattahoochee River, which will establish an emergency water supply for the city. A 12.5 ft diameter Main Beam TBM is boring the area’s deepest tunnel through hard, abrasive Gneiss rock at rates of up to 100 ft per day. This paper examines the project specifics and design, as well as the performance of the TBM. It also draws conclusions as to the optimal TBM design for excavation in the area’s exceedingly hard geology based on this project and past projects in the area.
TBM Tool Wear Analysis for Cutterhead Configuration and Resource Planning in Glacial Geology
The abrasive nature of glacial geology generally results in Tunnel Boring Machine (TBM) cutting tool inspection and replacement needs that may require hyperbaric interventions and are a cost and risk factor. Correlation analysis of geotechnical conditions, TBM operational parameters, and tool wear measurements is a proven way to gain insight into the wear system behavior. This paper presents findings from various TBM drives in the Seattle and Vancouver, B.C. metropolitan areas on the performance of disc cutters and ripper-type tools in glacial and inter-glacial deposits. The authors provide recommendations for cutterhead configurations, tool management strategies, and the use of monitoring technology.
Logistics and Performance of a Large-Diameter Crossover TBM for the Akron Ohio Canal Interceptor Tunnel
The Ohio Canal Interceptor Tunnel (OCIT) below the city of Akron is utilizing the first large diameter Dual Mode, “Crossover” type TBM in the United States. The 30.4 ft diameter machine is excavating in variable conditions including soft ground and shale rock. Due to the unique conditions, the TBM has been designed with features including a flexible cutterhead design and abrasion-resistant plating on the cutterhead and screw conveyor. As part of a predictive maintenance plan, measurements for the screw conveyor’s exposed features will be taken along the drive to report on the wear rate of these components in shale. This paper concentrates on the logistics and process of the TBM launch, and component wear and performance at the jobsite in variable ground conditions.
Let’s Be Clear: Transparency is a Boon, not a Bust, for the Tunneling Industry
The idea of transparency is one that we most often hear touted in politics and policies. But transparency is a concept that applies to our underground industry as well. Widespread knowledge sharing can and should be the policy in our industry, but all too often jobsite politics, confidentiality agreements, and fear of poor public opinion limit what is ultimately divulged. I argue that transparency in tunneling is a help, not a hindrance, and we can make steps today towards clearer communication.
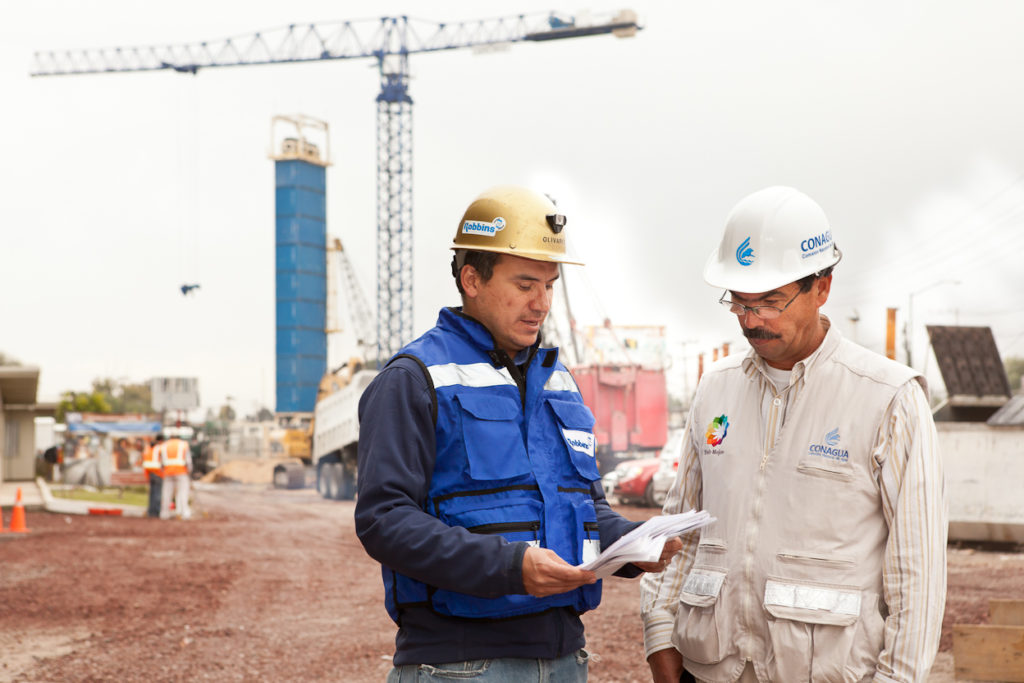
Transparency, achieved through better communication among all stakeholders, is the key to continued success in our industry.
Why It’s Needed
- Learn from Experiences in the Field: Tunneling professionals deserve full access to the successes and the problems that have been encountered in the field. If we were to employ universal knowledge sharing, tunneling operations themselves could become safer and more efficient and overall project costs could be reduced.
- Improve Tunneling Technology: Knowledge of advance rates, performance in specific ground conditions, wear rates for cutters and other surfaces in contact with the cutting face, performance of ground conditioners and foams, and many other types of info are imperative to improving technology. Tunnel boring could be made faster, safer, and more cost effective with such knowledge. It could also improve willingness to try new and emerging technologies in the industry, which benefits all stakeholders. With a good knowledge of TBM performances in specific ground conditions, TBM specifications could also be written to greater accuracy and result in using the most cost effective solutions.
- Improve Risk Sharing: Risk is often apportioned unfairly on today’s tunneling projects. In many cases the TBM supplier is required to shoulder a larger part of that burden than their potential returns. With a better understanding of the risks through knowledge of past projects, as well as knowledge of past risk sharing strategies, this problem can be resolved.
- Ensure Fair Financial Practices: With transparency in terms of contractual pricing and project spending, payments for work performed, etc. and other unsavory practices can be lessened.
- Reduce Litigiousness: Claims in tunneling projects are on the rise worldwide. Recent projects have resulted in separate and duplicate claims against different parties, such as the equipment manufacturer and the owner, for the same issues and without their mutual knowledge. Such claims are unfair, and through transparency and equal access by all parties to a Dispute Review Board, the frequency and extent of lawsuits in our industry could be reduced.
From the Equipment Supplier Perspective
As equipment suppliers, we strive to share the information that is available to us. We’ve opened up about stuck TBMs, challenging drives, and how we’ve overcome those issues. We’ve also tried to share whenever possible why we think fast advance rates and good efficiency were achieved on various projects.
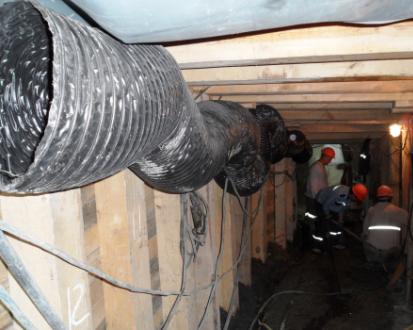
A bypass tunnel at Turkey’s ultimately successful Kargi project, where we shared information on seven such tunnels built in the first 2 km of tunneling.
Unfortunately knowledge is sometimes not shared even within parties on the same project, such as the contractor, project owner, owner’s representative, and equipment supplier. Time and again we see that communication between all parties is key to overcoming challenging conditions. The road to transparency starts here: with clear communication between all coordinating parties on a given project.
Not Without Precedent
Transparency is not an untested idea in our industry. A great recent example is that of the U.K.’s Crossrail project. The project follows governmental codes of practice for data transparency and the country’s Freedom of Information Act. Details such as project and equipment costs, spending budgets and records, safety records, and more are available for download on their website, and special requests can be made for additional data. Multiple reports have also been up front about TBM performance, advance rates, and other experiences on the project. The Crossrail project was highly successful and, arguably, transparency played a large part in that. Crossrail is also just one example of transparency at work in the U.K.—governmental programs such as Transport for London’s Transparency Strategy aim to give clear and consistent information to the public about all road and public transit spending.
A Call for Clarity
Transparency is possible in the tunneling industry, but it may require things like international regulations, or at the very least certifications that could be provided by an international organization like the ITA. Such a certificate would be highly beneficial to all stakeholders: It could certify corruption-free practices, and guarantee knowledge sharing. Transparency is not an easy thing to achieve, and there are certainly barriers to the process in various areas of the world. But we can start with transparency requirements within projects, and then move outward. To be clear: knowledge sharing is something that can only benefit our industry. It is our recommendation we start today.
Record-Setting Robbins TBM breaks through at China’s Jilin project
In mid-May 2018 the national-record-setting 7.9 m (26 ft) Robbins Main Beam TBM at the Jilin Lot 3 Tunnel broke through. A formal ceremony followed to commemorate the stellar performance of the tunneling operation and its early completion. “I have participated in this project from the beginning. The project broke through 147 days earlier than scheduled. The project has achieved the fastest monthly advance rate record–1423.5 m/4,670 ft—for 7 to 8 m (23 to 26 ft) diameter TBMs in China. And the machine has reached over 1000 m (3,280 ft) per month for three consecutive months. I am so proud of these achievements,” said Mr. Wu Zhi Yong, Vice Chief Engineer and Jilin Yinsong Project Vice General Manager for contractor Beijing Vibroflotation Engineering Co. Ltd. (BVEC).
The completion of the 24.3 km (15 mi) tunnel nearly five months ahead of schedule is a monumental achievement considering the difficult ground conditions encountered. Rock types ranged from tuff to granite, sandstone, and andesite with multiple fault zones—conditions requiring nearly continuous ground support. Rock strengths varied widely from 35 to 206 MPa UCS (5,100 to 30,000 psi). The contractor cited a number of factors that contributed to the swift advance rates: “It is the stable and reliable performance of the Robbins machine, and the professional technical skills of the service technicians. The Robbins crew coordination, reasonable working progress arrangements and the sophisticated technology all allowed the project to make the fast advance rate,” said Mr. Wu.
The Robbins Main Beam TBM bored through a total of 24 fault zones utilizing a unique combination of steel McNally slats (extruded through pockets in the TBM roof shield to prevent movement of loose rock), wire mesh, and shotcrete. The TBM was specifically designed to tackle the tough conditions. “Under the variable ground conditions, especially weak, soft, and fractured rock, the optimized system and reasonable design of the machine ensured effective tunneling progress. Robbins’ unique gripper system, continuous propel system, hydraulic drives, roof support and stable cutterhead reduced the wear of cutters.The efficient belt conveyor inside the main beam allowed quick muck removal from the cutterhead to the back of the machine, which ensured the good progress of the TBM,” said Mr. Wu.
The Jilin Lot 3 tunnel is part of the Jilin Yinsong Water Supply Project, which at 736.3 km (457.5 mi) is China’s largest scale water diversion project to date. Once operational the water lines will divert the water from Fengman Reservoir at the upper reaches of Di’er Songhua River to central regions of Jilin Province experiencing chronic water shortages. These regions include the cities of Changchun and Siping, eight surrounding counties, and 26 villages and towns under their jurisdiction. The project will optimize water resource distribution, improve regional eco-systems, and ensure better food production and water safety for the people of Jilin Province.
ATC 2018
Event Name: Australian Tunneling Conference
Dates: October 15-16, 2018
Location: Sydney, Australia
Venue: SMC Conference & Function Centre
Meet us down under in Sydney, Australia as we attend the Australian Tunneling Conference from October 15 through 16. Stop by stand 11 to discuss current techniques being used on Robbins projects throughout the world.
Ho Chi Minh City MRT Lines Infrastructure Projects Conference 2018
Event Name: Ho Chi Minh City MRT Lines Infrastructure Projects Conference 2018
Dates: July 24-26, 2018
Location: Ho Chi Minh City, Vietnam
Venue: Sheraton Saigon Hotel & Towers
The Robbins Company looks forward to attending the Ho Chi Minh City MRT Lines Infrastructure Projects Conference in Ho Chi Minh City Vietnam. Meet us at our table between July 24 through 26 to discuss projects operating nearby, such as the Thuong Kon Tum project, or others world-wide.
Rescuing and Refurbishing TBMs: Experiences at Bangalore’s Namma Metro
In this blog, Robbins and guest blogger Barrie Willis, Manager Tunneling & Civil for iPS, share their experiences rebuilding and relaunching TBMs in the field.
TBM maintenance: it’s one of the most important factors predicting project success, but it is often glossed over. Experience shows, however, that maintenance plays just as much a part in the excavation rates as the proper TBM design. Regular maintenance can keep future rebuild costs low and keep equipment efficiency high while maximizing advance rates.
Conversely, a lack of maintenance, improper operation, and/or severe ground conditions can result in undue wear and slow advance rates. In a worst case scenario, it can even require rescuing and refurbishing a TBM. Such a case occurred at Bangalore, India’s Namma Metro, where several TBMs required recovery and refurbishment after operating in abrasive ground. Teams from both Robbins and iPS were called in to evaluate and rescue TBMs on separate sections of the tunnel.
The Robbins Experience
Two European-manufactured EPB TBMs “Krishna” and “Kaveri” were launched from the South Ramp station at the Namma Metro project in October and November of 2012, and were slated to bore three sections of metro tunnel each, totaling 1,550 m. While the first 400 m long drive from South Ramp to City Market station went well, the TBMs encountered severe ground conditions on the second, 432 m long drive from City Market to Chickpet Station.
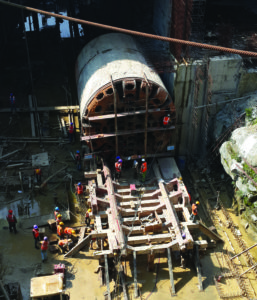
Robbins refurbished the two EPBs but did not change any of the machine design features.
Difficult Conditions
The drives took 12 and 22 months, respectively, and were hampered by a mixed face comprising hard granite and soil with high groundwater levels. Tunneling took place near fragile, historic building foundations in some cases hundreds of years old. The TBMs in this section encountered large boulders as well as reinforced blocks of concrete that seriously damaged the TBM cutterheads. These challenges required regular cutterhead interventions but at the same time there was an inability to grout unstable areas from the surface due to congested residential areas.
It was at this point that the contractor, along with owner Bangalore Metro Rail Corporation Ltd. (BMRCL), approached Robbins and asked them to take over the operations of the TBMs—the critical path tunnels needed to be brought back up to speed. The last 750 m drive between Chickpet and Majestic stations was all that stood in the way of opening a substantial section of Namma Metro’s Phase 1.
Robbins Signs On
After obtaining agreement from the project owner and the contractor, Robbins took over the responsibility for all aspects of the underground operations. A team of over 60 staff including TBM operators, TBM technicians, ring builders, a grouting team, and others began work. Robbins was also responsible for running surface installations and equipment such as the grout batching plant, gantry cranes and power supply. The contractor provided a team of people including surveyors, QC engineers, and loco operators who reported directly to the Robbins site management team.
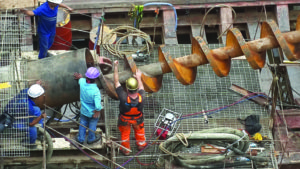
Robbins Field Service guided the refurbishment and assembly of the two competitor-manufactured EPBs.
The Robbins crew carried out refurbishment of the two TBMs, keeping the designs of the machines in tact while installing Robbins cutting tools in both cutterheads. In particular TBM “Krishna” underwent 112 days of repairs and testing. The refurbishment, and subsequent assembly and launch of the two machines, was carried out even as the Chickpet station was being constructed in order to mitigate any further delays. The two TBMs were re-launched in 2015 on their last drive—in March for TBM “Kaveri” and in December for TBM “Krishna”.
Challenging Ground Continues
Difficult conditions were encountered during the bore: the initial 160 meters of the drive was found to consist of residual soil, gradually transitioning into a mixed face of soil and highly weathered granite over the following 100 m. The mixed face conditions then gave way to a full face of fresh granite in the last 50 meters of boring.
The zones of transition were particularly difficult, with soil occasionally falling in due to the vibrations during tunneling. The conditions also made it impossible to maintain hyperbaric air pressure during cutterhead interventions. This problem was overcome by pumping a weak-mix grout solution into the ground surrounding the TBM. The solution permeated into existing voids and effectively prevented air from percolating through to the surface. A period of approximately 36 hours was initially required for curing of the grout solution. However, on-site trials with various additives enabled the standing time to be reduced to 12 hours.
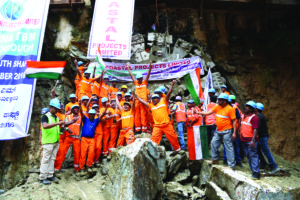
Robbins and crews celebrate the breakthrough of TBM “Kaveri”.
A Resounding Success
Despite the challenges, the TBMs were able to achieve advance rates of 50 mm per minute in highly weathered rock and 22 mm per minute in sections of competent hard rock. TBM “Kaveri” completed its final breakthrough in June 2016. The second TBM “Krishna” had the advantage of known geology and completed its excavation in about nine months on September 28, 2016.
The iPS Experience

When the TBM emerged from the rescue shaft most cutters and grill bars were worn away.
On another section of the recently completed Namma Metro, iPS rescued and refurbished a stuck TBM from another European manufacturer, and then operated it for owner Bangalore Metro Rail Corporation (BMRC) alongside the project’s original contractor.
Initial Inspection
iPS found severe wear—the cutterhead was essentially bare, and the cutters, disc boxes, cutter mountings and grill bars had been worn away. On inspection a serious crack in the screw conveyor was found and the flights had been severely worn. The TBM had been operating for 12 months and had bored 300 m of abrasive ground with insufficiently thorough maintenance. Geology consisted of weathered granite with a high quartz and feldspar content, 130 MPa UCS, and was often mixed with softer soils. It came to a standstill below the main railway lines at a major Bangalore metro station.
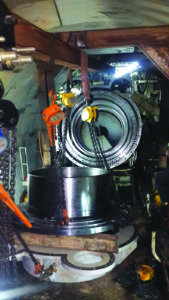
iPS crews had to rebuild the machine inside the tunnel.
Rebuild & Recovery Plan
iPS was able to build an intermediate shaft and refurbish the TBM to the point that it could advance into that shaft for further rebuild work including a replacement cutterhead. But the rebuild work itself was not easy—sourcing parts in India was a challenge, with smaller parts being brought in from Germany and other countries. A new cutterhead was shipped to the site by air freight. Crews dismantled the TBM to inspect and repair the screw conveyor, hydraulic system, PLC, and main drive. The TBM was relaunched in August 2015.
A Second Chance
Once the TBM had started up again, iPS then trained the crew on the importance of maintenance and inspections. They went over cutterhead interventions, what to look for, and how to prevent significant damage.
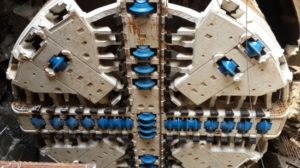
The cutterhead shown was shipped to the site by air freight, as sourcing parts was a challenge.
The training and TBM rebuild were a success—despite continued abrasive geology and mixed face conditions the machine completed the remaining 630 m of its drive in seven months. Frequent interventions were undertaken to maintain and inspect the machine. Breakthrough occurred on April 19, 2016.
Key Takeaways
Like any piece of machinery, it is essential to consider the total life cycle and to take steps to maximize the efficiency and life of the equipment through good operation and maintenance. Contractors should work with equipment suppliers to learn of the maintenance that is required—both scheduled and in response to changing geology.
When a project begins, err on the side of caution: do too many inspections, more than you think are necessary, to get a feel for how the machine reacts in different geologies. Geological surveys are extremely important, but they don’t always reveal every feature, so in the event the machine encounters unexpected geology, even more inspections will be necessary than normal. Above all, avoid complacency: just because a TBM is a large steel machine with a metal cutterhead and cutters doesn’t mean that nothing can damage it.
The proof is in the multitude of successful projects around the world: TBMs can and have shown their ability to excavate projects at world-class rates of advance even in very difficult conditions. With proper maintenance and operation, a TBM can last over many kilometers of tunnel and years of use.