Year: 2018
BTS 2018
Event Name: The British Tunneling Society (BTS) Conference
Dates: October 9-10, 2018
Location: Westminster, London
Venue: QEII Conference Centre
The Robbins Company looks forward to seeing you in Westminster, London for the 2018 British Tunnelling Society (BTS) Conference. Join us on October 9 and 10 at stand B26 to learn more about current projects and recent innovations.
ICID Conference
Event Name: International Commission on Irrigation on Drainage (ICID) Conference
Dates: May 2-4, 2018
Location: Kathmandu, Nepal
The Robbins Company hopes that you will join us in Kathmandu, Nepal from May 2 through 4, for the International Commission on Irrigation and Drainage (ICID) Conference. Stop by our booth to speak with one of our knowledgeable associates about projects running worldwide.
EXPOMIN 2018
Event Name: EXPOMIN
Dates: April 23-27, 2018
Location: Santiago, Chile
Venue: Espacio Riesco Convention Center
The Robbins Company is looking forward to exhibiting at EXPOMIN in Santiago, Chile from April 23 through 27. We hope that you will join us at booth C27 during exhibition hours to learn more about projects in the area, such as Los Condores II, which is currently underway in the Andes Mountains, as well as other boring projects around the world.
Are You in Tough Ground? Learn from our Trials and Tribulations in some of the Tunneling World’s Most Difficult Projects
Squeezing Ground, Fault Zones, Water Inflows, and More
True story: In a mountain range, crews worked on a shielded TBM more than 500 m below the surface. The TBM had excavated several kilometers in worsening conditions. The crew encountered karstic aquifers filled with mud and water. Personnel were pumping polyurethane through the cutting face to staunch the water inflows.
Suddenly, water inrushes climbed to a rate of 1,500 liters/second, creating a knee-deep underground river and causing the machine to become stuck. Thankfully, the crew was able to exit the tunnel, unharmed. The massive inrush created a damming effect with enough pressure to crush the TBM shields and send cylinders catapulting into the back-up.
As quickly as it had started, the machine ground to a halt, deep underground.
What happens when you encounter an unforeseen condition? A severe water inflow, fault zone, or squeezing ground? A geological feature that seems like it might stall your tunneling operation altogether? Some of our most difficult challenges—spanning from New York to Peru to the Republic of Georgia—are detailed below. These case studies are meant to pass on our knowledge and experiences to help you overcome obstacles, unforeseen or otherwise.
How to Overcome an Epic Flood: New York’s Harbor Siphons project
Sometimes an unforeseen condition requires a rescue effort to overcome. In October 2012, a storm was coming to New York City’s Harbor Siphons Project on the shores of Staten Island. The undersea tunnel and its 3.6 m CAT EPB ground to a halt when hit by Superstorm Sandy. The monstrous hurricane battered the eastern seaboard of the U.S. with winds of 145 kph.
The launch shaft was inundated with seawater despite contractor Tully/OHL’s best efforts. Flood water entered the tunnel and stopped the TBM just 460 m into its 2.9 km long drive. A 2013 post-storm survey of the tunnel showed a damaged machine extensively corroded by saltwater. All electrical components needed to be replaced.
Contractor OHL turned to Robbins for help. During the downtime, the original TBM manufacturer had exited the tunneling industry. Robbins worked with the contractor to come up with a multi-pronged approach to bring the TBM back to life.
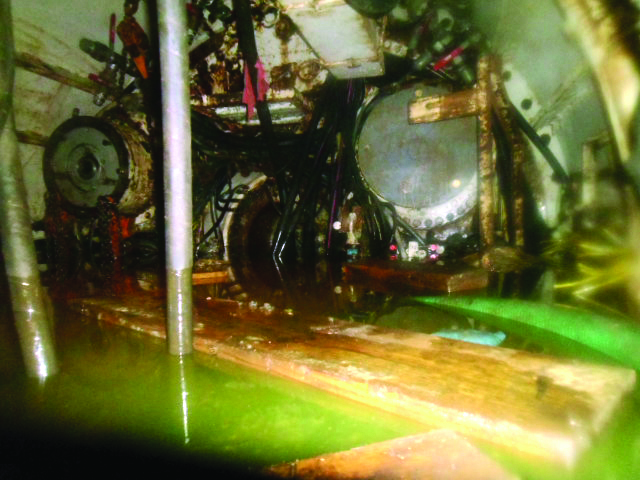
Flooded TBM: A view of the initial inspection after the flood, looking at the machine’s drive motors submerged in seawater.
Hiring a Dedicated Team
Per the scope of work, defined jointly by OHL and Robbins, crews temporarily excluded the cutterhead and main bearing of the TBM for refurbishment, as they were under earth pressure and not accessible. The Robbins team would need to complete the refurbishment taking into account unknowns, such as the condition of the cutterhead. The segmented concrete tunnel lining would not permit the removal of many of the larger TBM components, so these would have to be refurbished onsite.
The Robbins crew was contracted to guide onsite personnel in replacing corroded hydraulic components and installing all new electrical components. Variable Frequency Drives, PLCs, and wiring were replaced inside the small tunnel under atmospheric pressure of 3 bar. Crews constantly monitored earth pressure during the refurbishment. The machine had been stopped with its thrust cylinders in, and thus the crew could not replace or evaluate certain components before the machine started up.
Reverse-Engineering Electrical Components
By mid-December 2013, Robbins PLC technicians were reverse engineering the TBM’s control system. The team understood early on that the previous control programming would be unusable given the PLC change. The technicians had only limited assembly drawings from the CAT manual, so much of the refurbishment, including the PLC system, had to be built from the ground up. The team at site understood how the machine should work and therefore were able to build the correct PLC system.
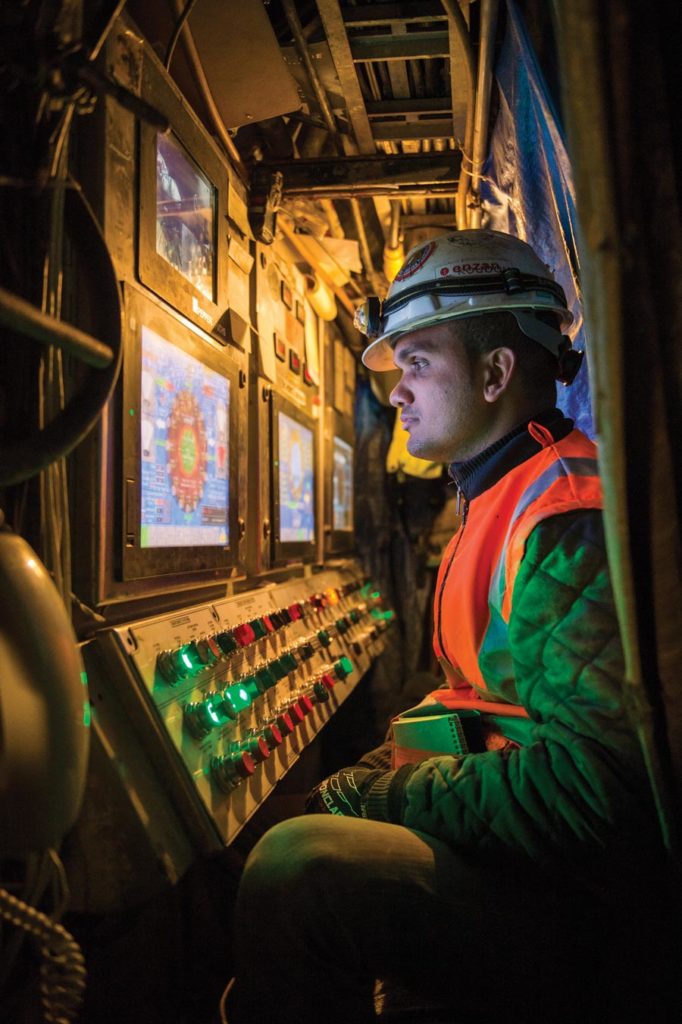
Reworked Electronics: The Harbor Siphons TBM required all new electronic systems.
Coordinating Success
Despite all of the challenges, the refurbishment project was a success. Crews had gone from a shipwrecked TBM—rusted, corroded, and abandoned in the tunnel—to a successful tunneling operation. It was a monumental task, scheduled to be completed in four months, and finished on schedule.
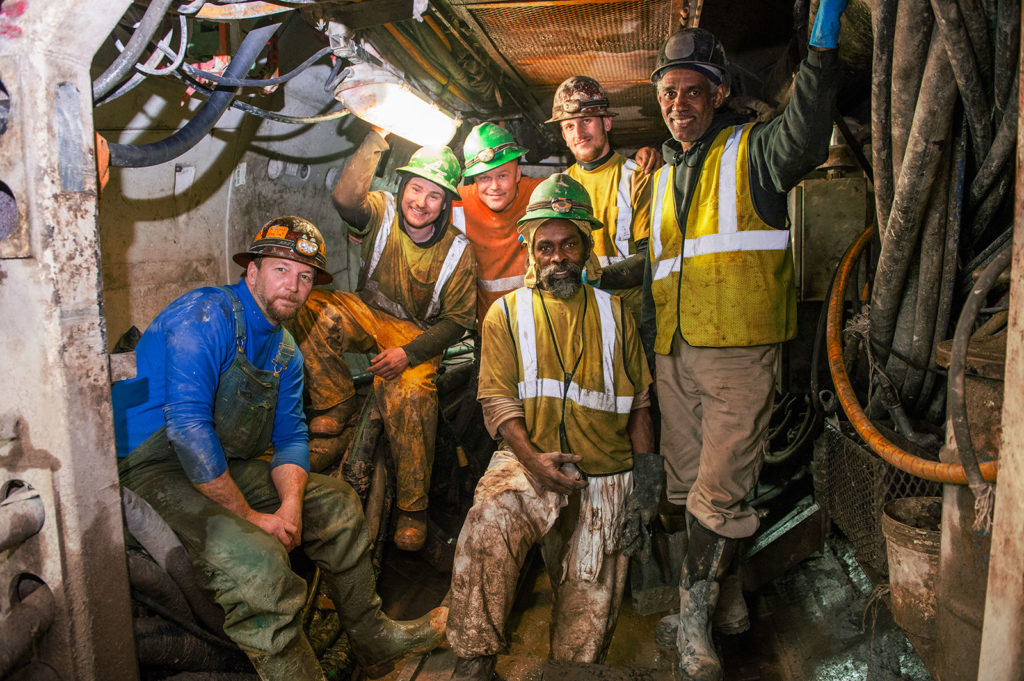
A Good Result: The happy crew during TBM boring, after the full refurbishment.
In the final phase of the refurbishment, a Robbins PLC technician was able to complete the commissioning of the TBM and on April 14, 2014 the machine officially returned to mining. The machine successfully completed its tunnel in February 2015.
Read more in the white paper here.
Make Rock Bursting Conditions Safe for Your Crew: The Olmos Trans-Andean Tunnel
If 16,000 recorded rock bursting events in the world’s second deepest tunnel weren’t enough, the crew at Peru’s Olmos Trans-Andean Tunnel had another problem. As the machine progressed and the cover grew higher—up to 2,000 m at the highest point—the rock bursts became more violent. Crews experienced large over-breaks and cathedralling in fractured and unstable ground. Teams of personnel had to inject concrete into large cavities that had formed during stress-relieving activities and stabilize these cavities with spiling. Then, several kilometers into the tunnel, a major rock bursting event occurred that twisted ring beams and caused damage in 45 m of lined tunnel. Damage was extensive to the TBM gripper, which was ballooned and blown off its mountings. Damage also occurred to other hydraulic cylinders. Thankfully crew members were not harmed, but downtime for repairs would be substantial.
A Century-Long Effort
The Olmos tunnel is a 12.5 km long water transfer tunnel that was bored through the Andes Mountains to bring irrigation to drought-ridden areas on the pacific coast. The project was more than 100 years in the making, with several attempts being made and thwarted by incredibly difficult geology as recently as the 1950s.
In 2007, with Odebrecht as the main contractor, the tunnel was finally completed using a 5.3 m diameter Robbins Main Beam TBM after other attempts with conventional methods failed. The route is the world’s second deepest civil works tunnel with overburden of up to 2,000 m. The tunnel alignment traverses complex geology consisting of quartz porphyry, andesite, and tuff with rock strengths ranging from 60 to 225 MPa UCS. The machine crossed over 400 fault lines including two major faults of approximately 50 m wide.
A Rocky Start
The machine was launched in March 2007, in ground conditions that immediately became more complex than anticipated. As the height of the overburden increased, long stretches of extremely loose, blocky ground were encountered. TBM utilization was as low as 18.7% of working time because rock support installation was requiring a very high 43.5% of the working time.
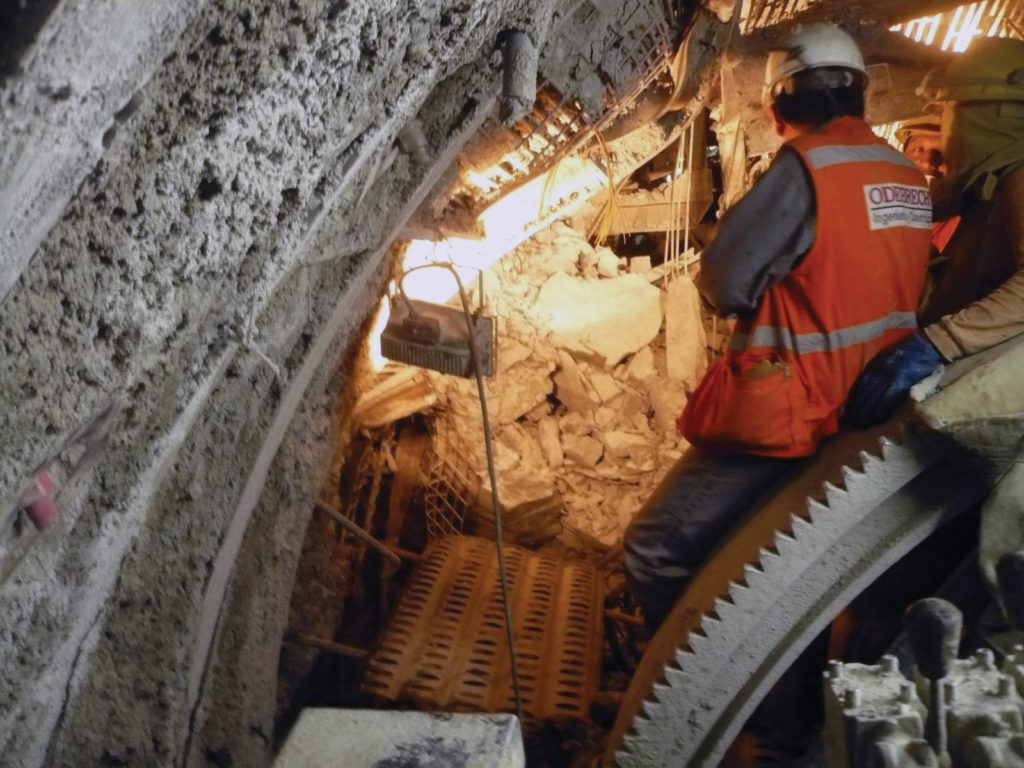
A rocky start: Rock bursting conditions at Olmos prompted a major overhaul of the TBM in the tunnel.
One of the main problems faced was ground deterioration and the resulting falls of blocky ground. The majority of these events occurred during the time taken for the newly excavated bore to pass behind the rear fingers of the roof shield, where ring beams and mesh were installed.
Modifying the Machine in the Tunnel
During consultations between Robbins and Odebrecht, a decision was made to modify the machine in the tunnel. The TBM would be reworked to use the McNally roof support system, which allows support to be installed directly behind the main roof shield. Crews removed the roof shield fingers and installed a series of rectangular pockets in their place. The pockets ran from the rear side of the cutterhead to the trailing edge of the roof support. These pockets were designed to be used with rebar, which is part of the McNally Roof Support System. At a later stage when the ground conditions worsened these pockets were extended to cover the sides of the TBM as well.
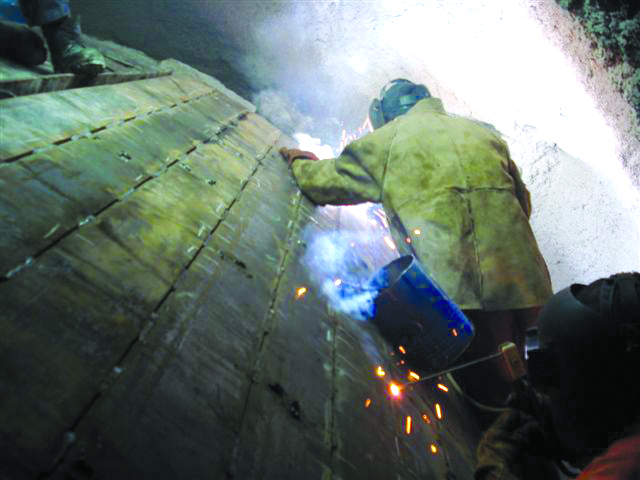
TBM Modifications: The crew add McNally pockets to the TBM roof shield in the tunnel.
The McNally Support System
One big advantage of the McNally support system is that it is possible to install ground support closer to the face than other ground support methods used on TBMs. It holds loose rock in place, which in turn helps to activate the strength of the rock mass and maintain the inherent strength of the tunnel arch. When used correctly the system can significantly reduce the time taken to provide adequate support. It can also offer reductions in the level of support required, and contain rock bursts and collapsing ground. The greatest benefit of the system, by far, is its ability to provide a much safer work area.
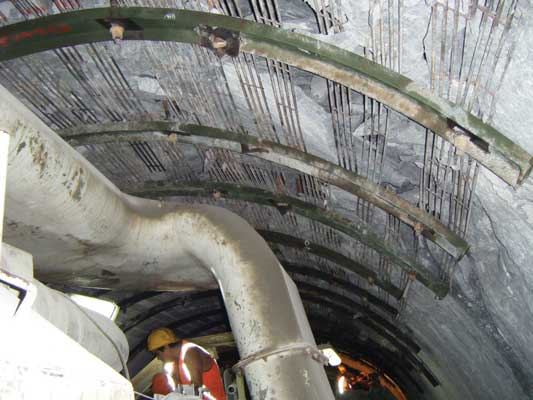
Crown Control: McNally slat installation at the Olmos Trans-Andean Tunnel.
Incorporation of the McNally support system and various other modifications to the TBM resulted in a steady increase in production rates in spite of continuous rock bursting events. The machine broke though in December 2011 having achieved production rates in excess of 670 m a month.
Read more about the McNally Support System here.
Make short work of an unforeseen cavern: The MKTVARI project
The Republic of Georgia’s Mktvari Hydropower Plant Construction project, along the river of the same name, was a challenge from the outset. The initial contractor used drill and blast for the 9.5 km long headrace tunnel through hard rock, but after 1.5 years they had only advanced about 200 m. The new contractor took over a previously-ordered non-Robbins hard rock machine but enlisted Robbins to help with the TBM assembly. They also wanted Robbins to be available if problems occurred. The machine did well at the outset, boring up to 900 m per month. But then, the machine hit bad ground.
Cavernous Conditions
Crews hit an unforeseen cavern above the TBM and were unsure of how to proceed through mixed layers of breccia, andesite, and bands of clay with light water inflows. A Robbins Field Service Manager was sent to the site, where he determined that the cavern was part of a fault zone consisting of unstable material that fell onto the cutterhead. At the time of his arrival, the TBM had passed through most of the fault zone but huge voids were left behind the segments.
Using pea gravel pumped through holes drilled in the segments, combined with cementitious grout, the crew was able to stabilize the existing segments and safely advance through the cavern in about 10 additional segments. There was also a probe drill onsite that had not been used; the Robbins manager persuaded the crew to install the probe drill and conduct systematic probing ahead of the machine, in case a larger section of clay was encountered.
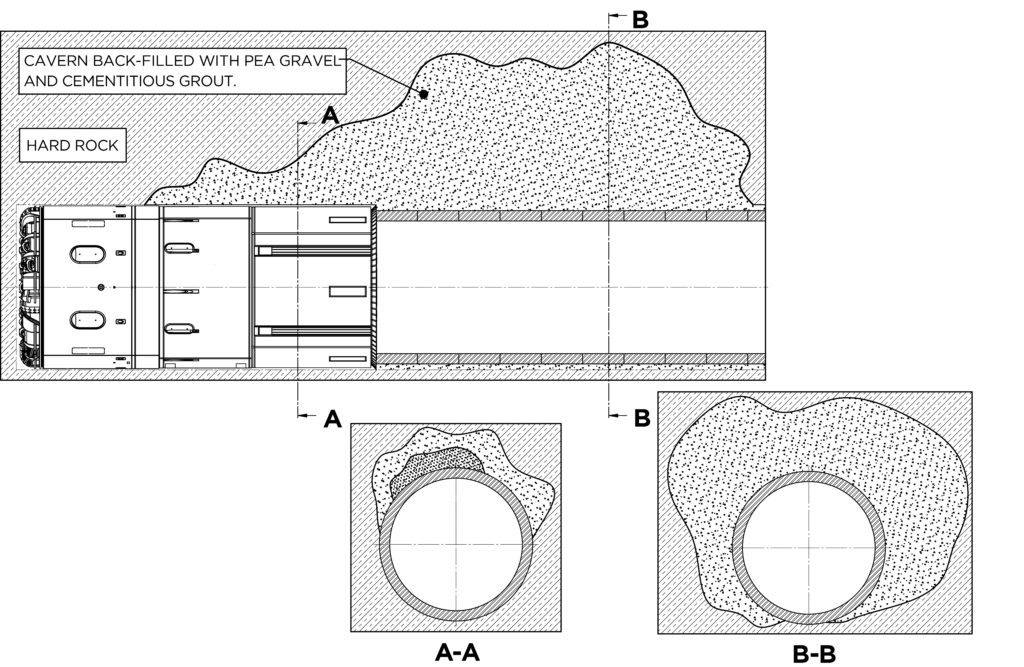
Crossing the Void: Robbins worked with the contractor to backfill the cavern, enabling the crew to advance out of the void in 10 additional segment rings.
Key Takeaways
As can be seen in these examples, planning is key. But, even the best-laid plans can go awry. When conditions go from bad to worse, having an expert team of personnel on your side is by far the most valuable tool and the most positive predictor of a project’s ultimate success. That true story I started off with certainly wasn’t the first such incident in the tunneling world, and it won’t be the last. Be prepared by arming yourself with knowledge, and with a knowledgeable team.
Information at your Fingertips
Learn more about our vast experience in difficult ground conditions. Our selection of white papers covers some of the world’s most challenging projects, while our Project Solutions section offers many examples of past successes.
Veteran Robbins TBM plays a Main Role in Ending Residential Flooding
In Chicago, Illinois, USA Kenny Construction is nearing completion on the Albany Park Stormwater Diversion Tunnel. The project, owned by the Chicago Department of Transportation, will divert water from the Albany Park neighborhood, which has long been plagued by flooding. Plans for the tunnel began in 2013, after flood conditions became so severe that residents had to be evacuated from the area by boat. The tunnel is expected to be functional by April 2018.
A Robbins Main Beam Hard Rock TBM bored the tunnel and broke through at the end of August 2017, bringing the project one step closer to completion. The TBM, also known as “Keri,” has been owned by project contractor Kenny Construction since the 1990s and has been used on several projects prior. “The machine holed through into the inlet shaft,” said Clay Spellman, Project Manager for Kenny Construction. “We excavated the shaft as part of the project. The machine has since been disassembled and removed.”
For the Albany Park Project, Keri was rebuilt by Kenny Construction with size modifications designed by Robbins. Robbins took an existing cutterhead, repaired it, and then added segments, taking it from 5.2 m (17.2 ft) to 6.2 m (20.4 ft) in diameter. “Extensive modifications were also made underground to the machine to be able to install rock dowels and stand the ring steel under the roof shield,” added Spellman.
“Rebuilding TBMs has always been a core part of Robbins’ business. Most customers immediately recognize that a rebuilt machine with updated systems can offer exceptional value without increasing risk, and a rebuilt machine can usually be delivered faster,” said Robbins Engineering Manager Steve Smading. “While the financial and schedule advantages are obvious, the flexibility of used equipment may be less obvious. Boring diameters can be increased or decreased and machine configurations can even be changed. For example, a Single Shield can be reconfigured as a Double Shield or vice versa, and a Main Beam TBM can be reconfigured as a shielded machine. Soft ground machines can be configured for different geologies and can be set up as either Slurry or EPB.”
Over 50 percent of all Robbins Main Beams ever manufactured have been used on three or more projects. Incredibly, many Robbins TBMs that have been used on multiple projects are approaching over 50 km (31 mi) of use. Prior to its ownership by Kenny, Keri has successfully bored tunnels in the Dominican Republic, Saudi Arabia, New York, and Chicago—totaling at least 19.5 km (12 mi) of tunnel.
Due to the project location in a residential neighborhood, there were restrictions in place as to when the machine could operate and the frequency at which blasting would be allowed per day. Despite these limitations, the TBM achieved a best day of 39.5 m (129.7 ft) and a best week (5 days) of 146.4 m (480.4 ft). The machine bored through dolomite with an average compressive strength of 64 MPa UCS (9,300 psi). “During boring we encountered approximately 30.4 m (100 ft) of fractured ground that had to be supported with rolled channels, straps, and 19 full circle steel rings,” said Spellman.
The drainage tunnel starts in Eugene Park and extends for approximately one mile under Foster Avenue to the North Shore Channel. When the Chicago River’s water levels reach flood stages—exceeding 2 m (7 ft)—the tunnel will divert a flow of 65 cubic meters (2,300 cubic ft) of water per second, avoiding Albany Park, then deposit it into the Channel. The tunnel will essentially be transferring the water where it would have ended up, without damaging the residential area or adversely affecting the river’s wildlife.
Robbins Main Beam Breaks Records in China
In Jilin, one of the three provinces of Northeast China, a 7.9 m (26 ft) diameter Robbins Hard Rock Main Beam TBM has achieved a national record for 7 to 8 meter (23 to 26 ft) machines: 1,423.5 m (4,670 ft) in one month. The record tops a previously-set achievement on the same project from earlier in 2017, when the TBM advanced at a rate of 1,336.8 m (4,386 ft) in one month.
The world record for the size class is held by another Robbins machine, set more than 20 years ago at the Tunnel and Reservoir Plan (TARP) in Chicago, Illinois, USA, for 1,482 m (4,862 ft) in one month. However, given the differences in rock conditions this Jilin project record is very significant. At TARP the rock was relatively homogeneous dolomitic limestone averaging 145 MPa/21,100 psi with occasional rock bolts; at Jilin the rock types were rated from 35 to 206 MPa UCS (5,100 to 30,000 psi), and identified as tuff, granite, sandstone, and andesite with multiple fault zones—conditions requiring nearly continuous ground support.
Despite the difficult conditions, the Jilin machine has achieved an average monthly advance rate of 708.3 m since the start of boring in March 2015—more than three times the average monthly rate of a Drill & Blast operation on another section of the project. “It is now very evident that well-equipped, open-type Main Beam TBMs with specialized features for difficult ground can traverse faults and large water inflows much faster than conventional tunneling methods. This fact, coupled with the high performance capabilities as demonstrated at Jilin, lowers the cost and time to complete long tunnels in difficult ground,” said Robbins President Lok Home.
The Jilin Lot 3 tunnel, which is being bored as part of a water conservation project, will be 24.3 km (15 mi) long when complete. Under contractor Beijing Vibroflotation Engineering Co. Ltd. (BVEC), the machine has excavated 14 km (8.7 mi) of the tunnel as of January 2018.
Throughout its bore, the Main Beam is expected to traverse a total of 24 fault zones. The TBM was designed accordingly, and is equipped with four rock drills, McNally pockets in the roof shield for the ability to install McNally slats, a ring beam erector, and a shotcrete system. The McNally slats were used in difficult ground encountered in the tunnel.
The McNally Roof Support System was designed and patented by C&M McNally and licensed for exclusive use on Robbins TBMs in certain markets. By replacing the roof shield fingers on a Main Beam TBM, the McNally system prevents movement of loose rock in the critical area immediately behind the cutterhead support. The system has been tested and proven on projects worldwide—including the world’s second deepest civil works tunnel, the 2,000 m (1.2 mi) deep Olmos Trans-Andean Tunnel in Peru—to increase advance rates while still maintaining worker safety on Main Beam machines in difficult rock conditions.
The Jilin TBM’s first fault zone was encountered after just 87 m (285 ft) of boring, requiring cooperation between the owner, Jilin Province Water Investment Group Co., Ltd., contractor BVEC, and Robbins field service. Water inflows and collapsing ground in a section measuring 1,196 m (3,926 ft) long were resolved with a combination of McNally slats, grouting, and consolidation of the ground ahead of the machine. Ground support overall consists of wire mesh and shotcrete. Tunnel Reflection Tomography (TRT)—a method of ground prediction using seismic waves—is also being used to detect changing conditions ahead of the TBM.
Despite the initial challenges, the TBM is now achieving between 40 and 60 m (130 to 197 ft) advance per day. “My colleagues and I all feel that the Robbins TBM is very easy to operate. All components of the system work well during operation, which has ensured our good progress,” said by Tao Yong, BVEC Jilin Lot 3 TBM Site Manager.
The Jilin Lot 3 tunnel is part of the Jilin Yinsong Water Supply Project, which will convey water to the central cities of Jilin Province. The large-scale, trans-regional water diversion project is the longest water supply line, measuring 263.5 km (163.7 mi), with the largest number of recipients benefiting from it in the history of Jilin Province. The construction project will divert the water from Fengman Reservoir at the upper reaches of Di’er Songhua River to central regions of Jilin Province experiencing chronic water shortages. These regions include the cities of Changchun and Siping, eight surrounding counties, and 26 villages and towns under their jurisdiction. Tunneling is expected to be complete in late 2018.
2018 Webinars: A Look at This Year's Lineup
Have a taxing project coming up this year? Be sure to keep an eye out for the Robbins 2018 series of complimentary webinars. Over our long history, we’ve seen a variety of grueling tunneling situations from squeezing ground to water inflows to fault zones. Join us as we share our hard earned experience to help you face your own upcoming challenges.
Here’s a sneak peak at what the year will bring:
April: TBMs in Squeezing Ground & Mountainous Conditions
June: Tunneling in Mixed Ground Conditions
October: Water Inflows in Hard Rock Tunneling
Breakthroughs While Breaking Ground: The First TBM Conveyor
Modern Achievements
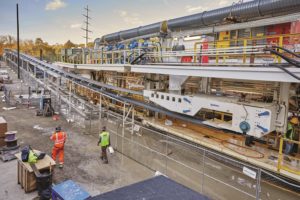
The 100th conveyor system has been refurbished and customized for the job in a process that Robbins has been perfecting for decades.
There are many elements that contribute to the success of a project: having an accurate report of ground conditions, choosing the proper equipment, having a well-trained team operating the tunnel boring machine—and behind it all—the utilization of a high-quality conveyor system. As tunneling machines evolve and bore at continuously faster rates, rapid muck removal becomes more important than ever. Robbins conveyor systems are capable of moving more than two thousand US tons of muck per hour—saving time and money on every project that uses the complete system.
In Akron, Ohio, a major milestone has been reached for Robbins conveyors. Running behind a Robbins 9.26 m (30.4 ft) diameter Crossover TBM is the 100th Robbins Continuous Conveyor System supplied for muck removal—more than any other TBM conveyor supplier has sold. The conveyor in Akron is just one landmark event in the long history of Robbins conveyors, the start of which can be traced back to the first ever documented use of a continuous conveyor system behind a TBM.
Pioneering Muck Removal
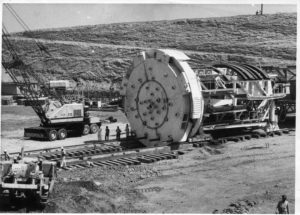
No roads were at the site in West Pakistan so goods were transported by rail car, requiring surveying of hundreds of bridges from the port city of Karachi.
The prototype for the conveyor systems we know today was developed by James S. Robbins in 1963 and was built using a Goodman coal-mine conveyor instead of muck cars which were more commonly used during that period. The conveyor ran behind what was, at the time, the largest TBM in the world. The 11.2 m (36.7 ft) diameter Robbins Main Beam was built for the Mangla Dam Project in what was then known as West Pakistan. The 4.3 km (2.7 mi) long tunnel was built to control water flow from the Jhelum River for use in agriculture and hydro-electric power.
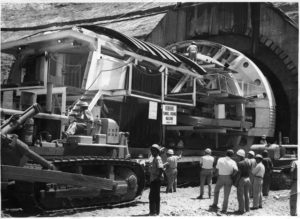
Temperatures at the jobsite climbed up to 53 degrees C (127 degrees F) in the shade.
The conveyor design had originally been used for coal and potash mines and was adapted for use behind the TBM. An extendable belt was side-mounted in the tunnel, leaving room for man-access and rail tracks to carry materials. Belt tension was maintained using a belt cassette. “They were able to operate continuously. It worked like a charm—and then the extensible conveyor was forgotten by the industry because it was perceived by contractors and owners as too much of an investment,” explained Dick Robbins, former President and CEO of The Robbins Company, in a 2013 article for World Tunnelling. It would be another 30 years after the successful completion of the Mangla Dam tunnel until conveyors became a standard means of muck removal in the tunneling industry.
Persistently Moving Forward
Conveyors have come a long way since their first use. Unlike the system used for the Mangla Dam project—which was limited to the use of a straight belt—conveyors can now wrap around curves and bring rock vertically up a shaft to the surface. “The control system, along with monitoring systems, has dramatically improved,” says Dean Workman, Robbins Director of Conveyors, Cutters, and SBUs. “The components have all been enhanced, giving a much longer life to the conveyor system. Contractors are using the same conveyors on multiple projects with minor refurbishments between projects.” While the basic function of a conveyor has stayed the same—muck hauling—the quality of conveyor systems has certainly changed.
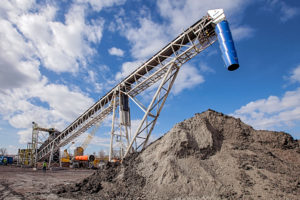
Did You Know: At least 75% of all world records achieved by TBMs were done with a continuous conveyor system for spoils removal rather than muck cars.
In a new design that is being used for the Los Angeles Purple Line Extension, continuous conveyors have gained another ability, they are now able to change direction. The unique system can be flipped to accommodate two machines boring parallel tunnels eastward before being re-launched to bore west. Due to the narrow launch shaft, modular components were designed to save space, and were built using a kit of secondhand parts, showcasing the long-life conveyor systems are capable of. “We are always looking to improve the design and function of the system,” says Workman, “modular components are a benefit to the contractor when installing, maintaining, and shipping the equipment.”
As progress continues and new technology provides advancements for the industry, The Robbins Company continues to uphold the pioneering spirit that James S. Robbins brought to tunneling with his trailblazing developments.
Read More:
Robbins Conveyor Systems
Conveyor Spec Sheet
100th Conveyor