Year: 2020
BTS Evening Meeting
Event Name: BTS Evening Meeting with Lok Home
Location: Virtual Event
Attend the upcoming BTS Evening Meeting, a complimentary event for members and non-members alike. The talk and Q&A will be streamed live on YouTube.
Meeting Info
Three Great Challenges: Experiences from TBM Tunneling in Difficult Ground
When boring through the earth, even extensive Geotechnical Baseline Reports can miss fault lines, water inflows, squeezing ground, mixed face conditions, rock bursting and other geological challenges. That reality is compounded when tunnels are extremely long, in remote locations, or under high cover.
In this lecture, Robbins’ President Lok Home will discuss three of the most challenging projects in recent memory: The 43.5 km long AMR Water Tunnel, the geologically diverse Sleemanabad Carrier Canal (both in India), and China’s Yin Han Ji Wei project in challenging rock bursting conditions.
Encountering Caverns in France: TBM Tunneling in Karst Conditions
France’s recently completed Galerie des Janots featured some unexpected challenges: Karst cavities large and small were found throughout the bore as well as two large, uncharted caverns. During excavation with a Main Beam TBM, crews encountered an 8,000 cubic meter cavern studded with stalagmites and a 4,500 cubic meter cavity directly below the bore path. How did the crew overcome the conditions and continue past the voids?
Tunneling in Karst: Your Questions Answered
On November 18, 2020 we held a webinar on a unique recent project, France’s Galerie des Janots. Crews utilized a 3.5 m diameter Robbins Main Beam TBM to bore a 2.8 km long tunnel through limestone with karstic features, with some surprises: Two uncharted caverns up to 8,000 cubic meters per size in the bore path of the TBM. To find out how the crew overcame the challenges, watch the video here:
We held a question and answer session during our event that was not recorded and wanted to share some selected Q & A with you below.
Question and Answer Session
Q: What type of karst was predominant along the alignment?
A: The karst was a kind of weak limestone formation. Very soft with a tendency to get pasty – like chalk in water.
Q: Could another type of TBM have been used in the geological conditions (limestone with karst)?
A: It was a rather small diameter tunnel and the less structure you have with the machine, the better. A shielded machine with segments at this diameter can work – but when in bad rock and you need to do something, the shield can become an obstacle to access the rock. We think the Main Beam machine was the best option and provided full access to the tunnel walls and strata.
Q: Do you think an EPB or Slurry machine could have been used in this tunnel?
A: I do not think so. When in rock, you will struggle with EPB or Slurry TBMs–producing conditioned muck or building up a filter cake and pressurizing the chamber will be very difficult to make happen in these conditions. However, our Crossover type machines do provide for operation in various modes and can run from rock into soft material.
Q: One of the typical challenges faced with karst is high water ingress. Can an open face machine deal with that?
A: Here we did not have water ingress, and did not have karstic aquifers either, so it was sufficient to employ normal water pumping. An open machine provides full access to the tunnel walls and the face. So, you can inject and fight the water ingress better compared to a shielded machine.
Q: In the Middle East, we had a project that, during pilot tunnel drilling in front of the cutterhead, resulted in sudden inrush of water ,which led to flooding inside the TBM. What types of mitigations measures do you recommend to overcome flooding risk?
A: A TBM can be furnished with doors and chutes at the relevant points to stop water ingress. A very appropriate tool is a so-called Guillotine Door, which is assembled to the muck chute above the TBM conveyor and allows for quick closing. Also, TBM conveyors can be furnished with a water-tight plug door, which can seal the machine when pulling back the conveyor. For sure, submersible pumps are needed, and to stop the water ingress, injection grouting should be used.
Q: What is BEAM Technology and was it able to successfully predict any real detected cavities before the TBM excavation?
A: BEAM Technology stands for Bore-tunneling Electrical Ahead Monitoring. BEAM is a ground prediction technique using focused electricity-induced polarization to detect anomalies ahead of the TBM. Yes, they were able to predict a cavity using BEAM on this TBM, see drawing below courtesy of Geo Exploration Technologies. The red spot spot in the colored band clearly indicates the location of the cavity, and the picture verifies that it was found at that location.
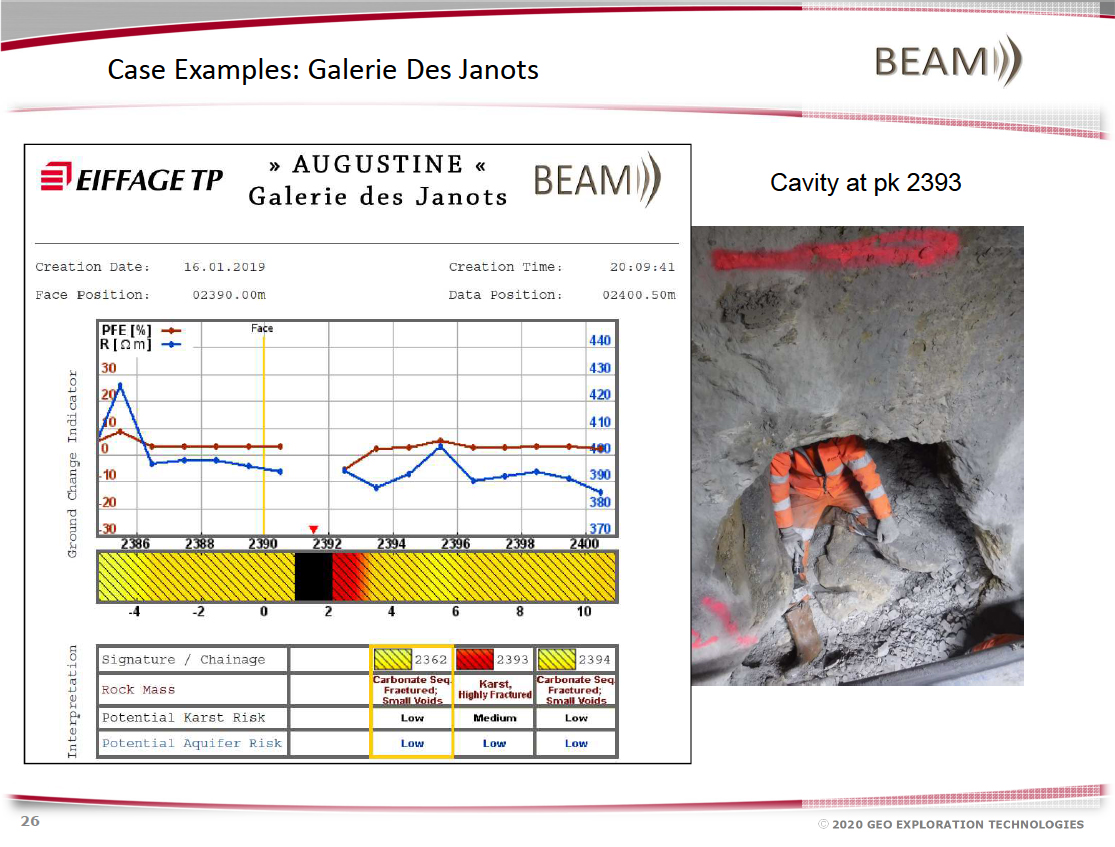
Detection of a cavity using BEAM at Galerie des Janots.
Q: What type of material did you use to fill the cavities?
A: It was mainly concrete reinforced with steel mesh and wood structures.
Q: How did they move past the first cavern and did ground support change during tunneling?
A: To cross the cavern space, crews erected a 4 m high wall of concrete so the TBM would have something to grip against (see picture below). The TBM was started up and was able to successfully navigate out of the cavern in eight strokes without significant downtime to the operation. Shotcrete was also employed – as long as necessary. Rock conditions changed often in this tunnel.
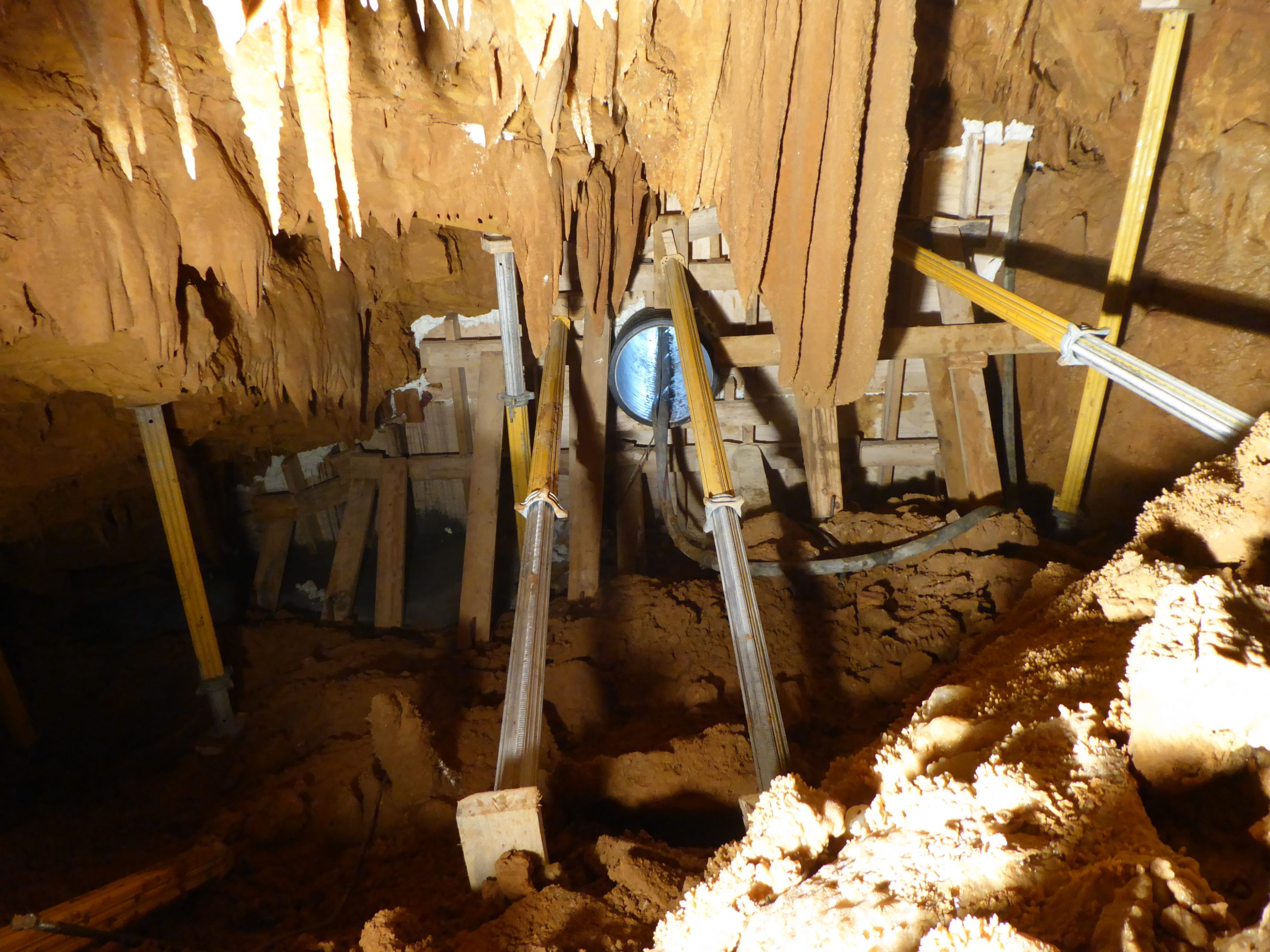
Reinforcement of the first cavern at Galerie des Janots.
NASTT No-Dig
Event Name: NASTT No-Dig
Dates: April 5-June 30
Location: Virtual Event
Booth: 2015
Come join us for some (virtual) fun in the sun at NASTT No-Dig’s virtual exhibit hall. Stop by the Robbins booth to meet with our expert staff and found out the latest about our SBU products and projects.
ITA Tunnelling Awards
Event Name: ITA Tunnelling Awards
Dates: December 3-4
Location: Virtual Event
Register for the ITA Tunnelling Awards, a complimentary event to learn about and celebrate the industry’s innovative projects and products worldwide. Stop by the Robbins booth for a live chat with our in-booth experts over video or IM, and get the latest updates on our offerings and events. The virtual exhibition is open during the entire event. We hope to see you there!
Live Awards Ceremony
2 PM CET
TBM Tunneling in Karst Conditions
France’s recently completed Galerie des Janots was the scene of some unforeseen challenges. During excavation with a Main Beam TBM, crews encountered a stalagmite studded 8,000 cubic meter cavern, and also a 4,500 cubic meter cavity directly under the bore path. In addition to the two large and uncharted caverns, there were also karst cavities of a multitude of sizes found throughout boring. What exactly did the crew do to beat the odds and power through?
For the answer, be sure to listen in as Detlef Jordan, Robbins Sales Manager Europe, goes into detail about the obstacles, lessons learned, and recommendations for future tunnels in karst conditions.
Watch the Recording
The Next Push: Robbins TBMs on the Move Around the Globe
Robbins machines continue to advance in 2020, with essential projects ongoing and starting up the world over. From a proven Main Beam starting its fifth tunnel in Switzerland to a triumphant small diameter breakthrough in Norway to continued Crossover success in India, we’ve got all the tunneling highlights below.
ASSEMBLY UNDERWAY IN TORONTO
Assembly is underway on a Single Shield TBM for the Ashbridges Bay Treatment Outfall in Toronto, ON, Canada. The 7.95 m (26.0 ft) diameter machine and Robbins continuous conveyor will bore a tunnel to replace a 70 yr old existing outfall. The video below shows the machine acceptance in Mexico before being shipped to Canada. Due to coronavirus protocol, this was the first all-remote machine acceptance that Robbins has conducted.
SMALL DIAMETER TRIUMPH IN NORWAY
On June 16, 2020, crews wrapped up tunneling at the Salvasskardelva Hydroelectric Power Project (HEPP), located far above the Arctic Circle at 68.7 degrees north latitude near Bardufoss, Norway. The site may well be the world’s northernmost TBM-driven tunnel. The 2.8 m (9.2 ft) diameter specialized Main Beam TBM known as “Snøhvit”, or “Snow White”, was provided to contractor Norsk Grønnkraft for use on several of their hydroelectric tunnels. A continuous conveyor was also provided. The small hydro tunnels featured moderate to steep positive gradients up to 25 percent. The TBM was able to achieve rates of up to 44 m (144 ft) in 24 hours.

A small diameter Robbins Main Beam TBM broke through in June 2020 in Northern Norway.
PROVEN MACHINE RAMPS UP FOR 5TH BORE
In Oberwalden, Switzerland a 6.50 m (21.3 ft) diameter Robbins Main Beam TBM, originally built in 1993, is ramping up to begin boring in December 2020. The machine, rebuilt by Swiss contractor Marti, will bore the 6.4 km (4.0 mi) long Sarnen Stormwater Relief Tunnel through hard rock. As the bore proceeds, wire mesh, shotcrete, and invert segments will be installed.
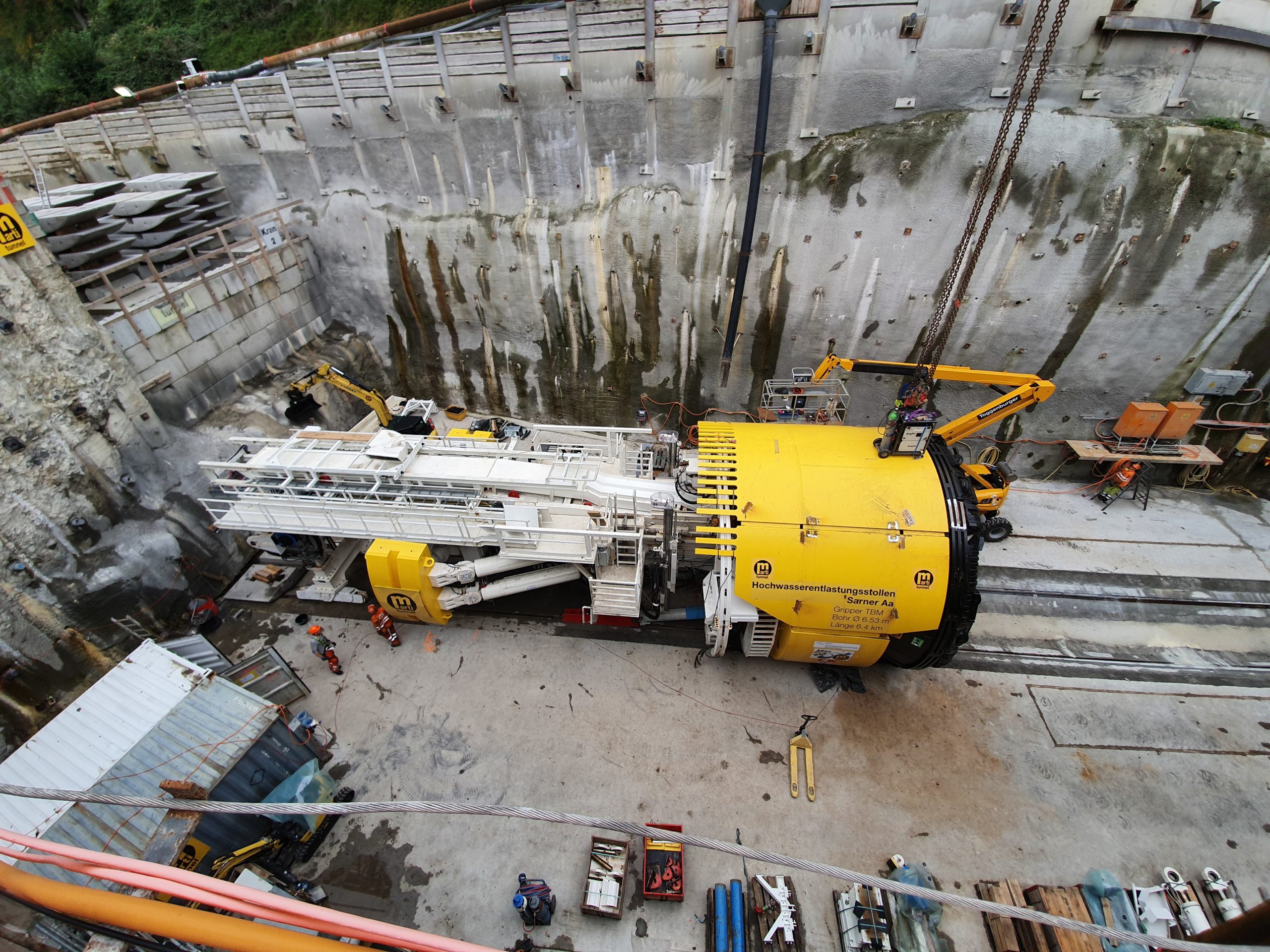
The 6.50 m Robbins Main Beam TBM will begin boring in December 2020 in Oberwalden, Switzerland.
UNIQUE CONVEYOR SYSTEM FOR NEUTRINO FACILITY
In Lead, South Dakota, a unique Robbins conveyor system is gearing up to begin hauling muck. The conveyor system will be used to build the Long Baseline Neutrino Facility (LBNF) for Fermilab. Contractor Kiewit will renovate a disused gold mine into a world-class neutrino research facility. Two caverns will be excavated by drill & blast and roadheader deep below the surface. Rock will be transported by cable hoist up a 1.5 km (0.9 mi) deep mine shaft to a rock crusher at the surface using much of the original but refurbished mining equipment, and from there will be transported via conveyors. The Robbins conveyor systems are designed for the unique application, and include the longest overland conveyor Robbins has ever provided (550 m/1,800 ft), which travels over a main road and city park and near a residential area.
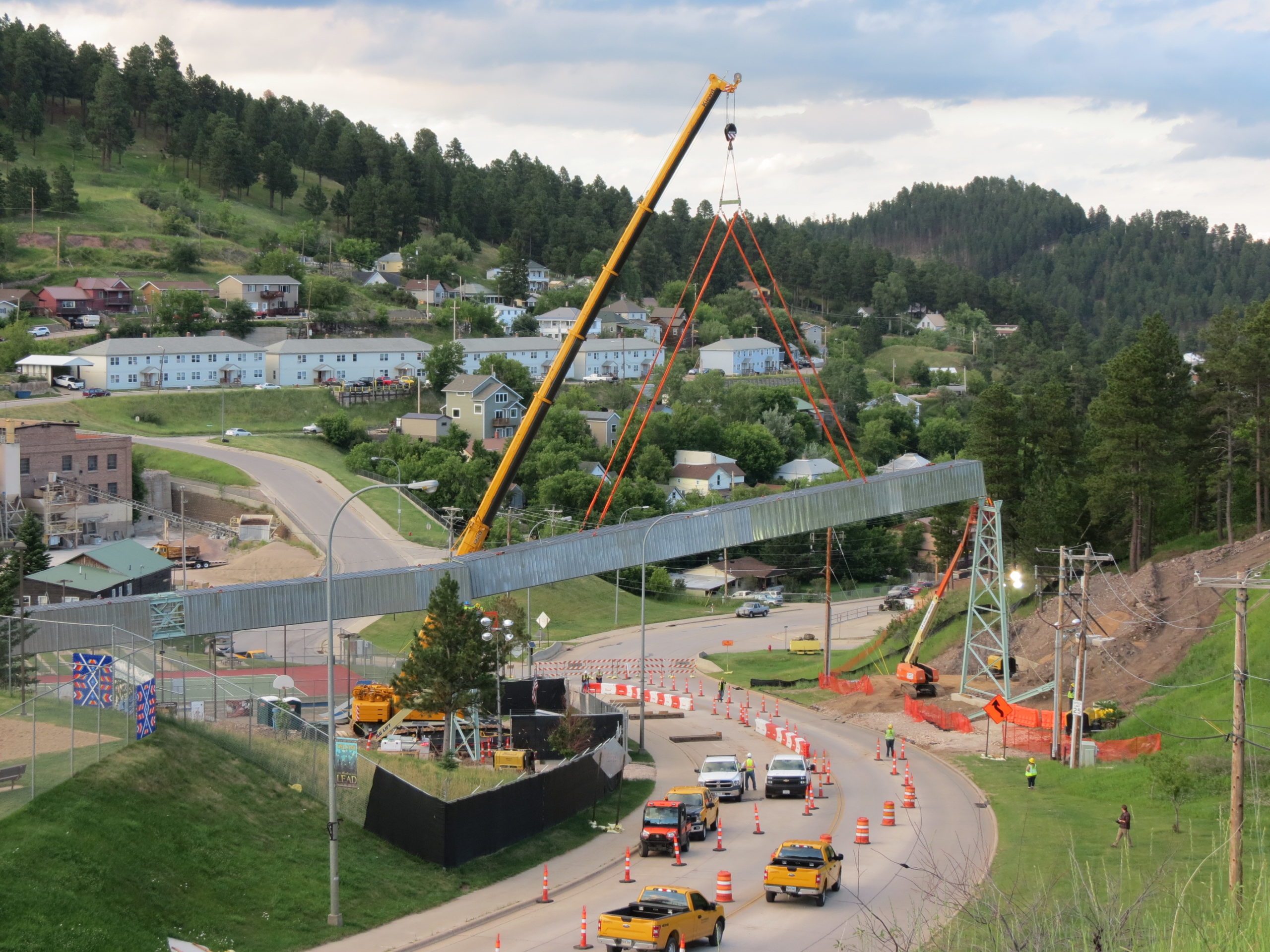
Crews install the completely enclosed box truss for the overland conveyor, which will traverse a roadway and other features.
CROSSOVERS CONTINUE BELOW MUMBAI
Tunneling continues on the Mumbai Metro Line 3, where two 6.65 m (21.8 ft) diameter Crossover XRE TBMs are on their third drives for the L&T/STEC JV. TBM 1 has bored 2,178 m (7,146 ft) with another 765 m (2,500 ft) left to bore. TBM 2 has bored 2,352 m (7,716 ft) with another 592 m (1,942 ft) left to bore, and is scheduled to bore fourth drive later this year. Two 6.65 m (21.8 ft) Robbins Slurry TBMs are also boring for the Dogus-Soma JV with one machine starting its second drive after boring 2,181 m (7,155 ft), and the other being reading for its second drive after boring 2,100 m (6,890 ft).
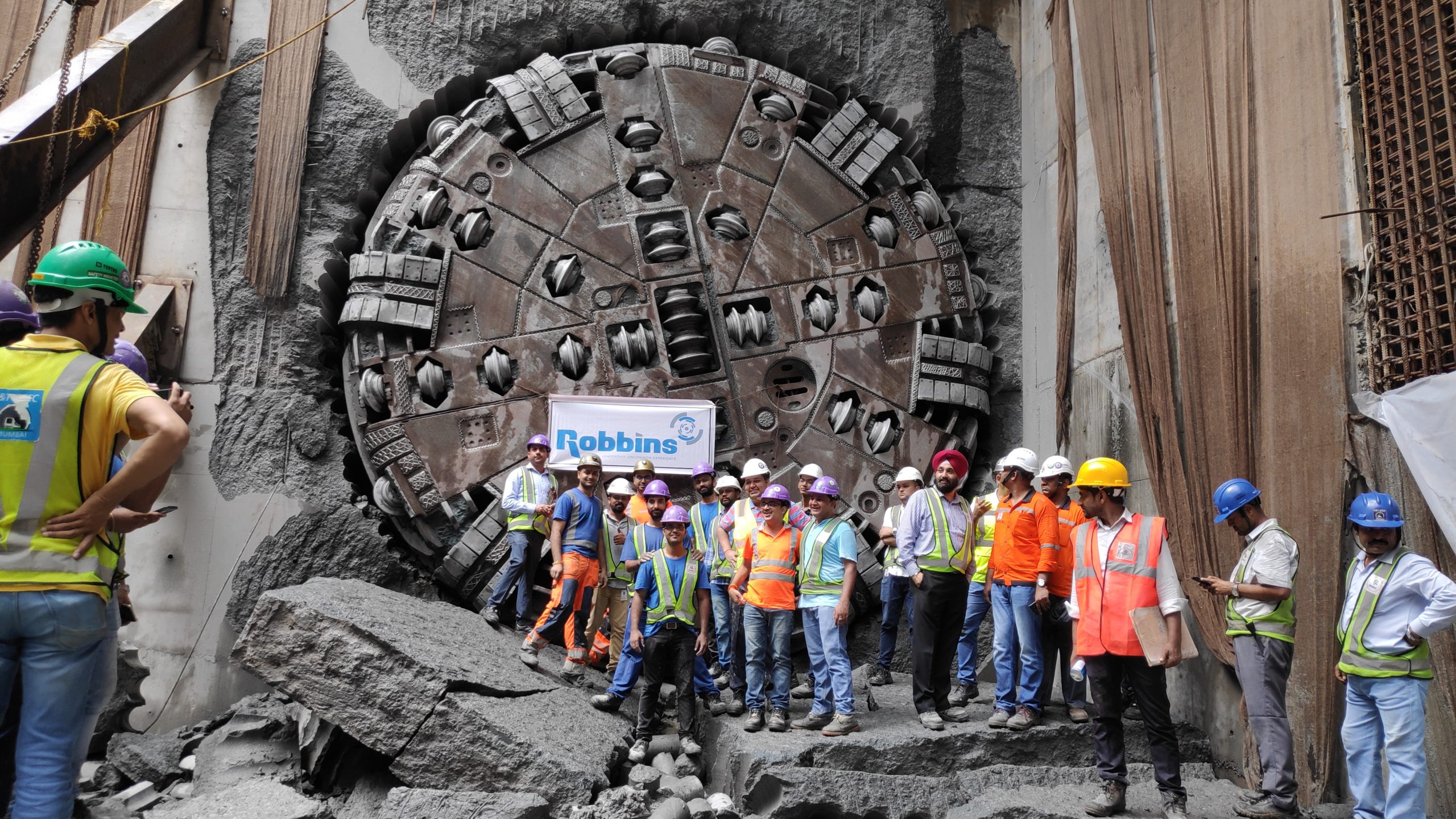
One of two 6.65 m (21.8 ft) Robbins Crossover XRE TBMs at India’s Mumbai Metro during a recent breakthrough.
48 Fault Zones and 26 Bar Pressure: Boring Turkey's Gerede Water Transmission Tunnel
Difficult ground doesn’t begin to describe the challenges overcome at a recent tunnel in central Turkey. The breakthrough of a 5.5 m diameter Robbins Crossover XRE TBM at the Gerede Water Transmission Tunnel was a feat of modern construction.
Robbins Main Beam carves out a win in Louisville
A 6.5 km (4 mi) long tunnel for wastewater storage below Louisville, Kentucky, USA has more to it than meets the eye. “At first glance, this seems like a straightforward project, but it turned out to be much more challenging,” said Shemek Oginski, Project Manager for the contractor, a joint venture of Shea/Traylor. The 6.7 m (22 ft) diameter Robbins Main Beam TBM and conveyor system had to cope with overstress in the crown that resulted in significant rock fallout in seven different areas, as well as methane gas in the tunnel. By the machine’s breakthrough on September 22, 2020, the crew had much to celebrate.
The machine was refurbished and consisted of older components as well as a brand new cutterhead supplied by Robbins and completely rebuilt electrical and hydraulic systems. “This was definitely an older machine—I actually operated it on the DART [Dallas Area Rapid Transit] tunnels in Dallas, Texas in the 1990s, but with many of the components being new we were confident in it,” said Oginski.
The original tunnel was expected to be 4 km (2.5 mi) long, but a change order added to the length by 2.1 km (1.3 mi). The extension was ordered by the owner, Louisville Metropolitan Sewer District (MSD), and its Engineer-of-Record Black & Veatch in order to eliminate four surface CSO storage basins. That included one basin originally located at the site of the TBM breakthrough, explains Oginski: “The original CSO site was located in close proximity to Beargrass Creek and had flooded multiple times. It was decided to extend the tunnel to that site in order to use the tunnel as storage instead, and connect it to the sewer system.” MSD installed a sheeting wall to protect the site from floodwaters while Shea-Traylor installed liner plate in the retrieval shaft, resulting in a site that is in much better shape.
It was in the 2.1 km (1.3 mi) extension, essentially a bifurcation of the main tunnel, where the crew encountered much of the crown overstress. “The longest section of overstress was 700 m (2,300 ft) and took two and a half months to get through,” said Oginski. The crew switched up the prescribed rock bolt pattern of four to six bolts at 1.5 m (5.0 ft) centers, and instead installed six bolts at 1 m (3 ft) centers. “It worked out to two rows per push. When that wasn’t enough, we installed wire mesh in the crown, mine straps, and channels. It definitely took extra time to install steel support, remove loose rock, and deal with the rock coming down so we could install rock support safely.” Overbreak varied from a few inches above the machine to 30 cm (1 ft) or more.
“We also had encountered natural methane gas in the tunnel just shortly before holing through,” said Oginski. The methane was discovered while the crew were probing out 150 ft ahead of the machine—something that the crew did continuously throughout the bore, using one, two or four probe holes depending on the geology. “We were down for about two weeks and were able to contain the methane within the cutterhead, where concentration spiked at 100% LEL. We were able to resume work after systematically ventilating, probing and grouting multiple times.”
Despite the challenges, the TBM was able to achieve up to 658 m (2,159 ft) in one month and 192 m (630 ft) in one week. The Robbins conveyor, including a 68.6 m (225 ft) long vertical belt, made this progress achievable, said Oginski: “The conveyor is definitely the way to go, especially for longer drives. There was quite a difference in performance between the extension tunnel, which we mined with lift-boxes, and mining with the conveyor. Our best month in the extension tunnel with the boxes was 221 m (725 ft), so that is a big difference.”
With tunneling now complete, Oginski is “definitely proud that we got to the end, as this is a challenging project.” The contractor is removing the components of the TBM to be stored in their yard in Mt. Pleasant, PA, and sees future applications for the equipment. “If the right project comes up then yes, it’s likely we would use this machine again.”
HYDRO 2020
Event Name: Hydro 2020
Dates: October 26-28
Location: Virtual Event
Register for the Hydro 2020 online event and get access to the latest information on all things hydropower, include Robbins’ innovative approach to small hydro tunnels at steep inclines using small diameter tunneling machines. Hear Robbins Civil Engineer and Cutter Product Manager Sindre Log speak on the use of three unique machines at up to 45 degree inclines in Norway.
Presentation Details:
Tuesday October 27
Session 22 – Tunnels & Underground Works – 2
11:00AM – 12:30PM CET
Title: Small but Powerful: Compact Hydro Tunneling offers Renewable Energy Solutions