Year: 2022
World Tunnel Congress 2022
Event Name: ITA-AITES World Tunnel Congress
Dates: September 2-8, 2022
Location: Copenhagen, Denmark
Stand: E-11B
Come join us September 2-8 in Copenhagen, Denmark for the ITA-AITES World Tunnel Congress, the premiere event for tunneling and underground construction. More than 160 exhibitors will convene, and hundreds of technical papers will be presented on the latest topics of interest. Stop by our stand E-11B to converse with our expert international team, and find out the latest about our products, projects, and talks at the conference.
Technical Presentation:
Wednesday September 7
Track 4, Mechanized Tunnelling 6
Hard Rock TBM Tunnelling Session, Room Wed6
11:30 – 11:50 AM
Rock Tunnels at High Water Pressure: Non-Continuous Pressurized Tunneling vs. Slurry Tunneling
Presented by Lok Home, Robbins President
Poster Presentations:
Tuesday September 6
1:10 – 1:30 PM
Hall C, Station 10
A Clean Solution for Renewable Energy: Small Diameter Hydro Tunneling
Presented by Detlef Jordan, Sales Manager Europe
Tuesday September 6
1:30 – 1:50 PM
Hall C, Station 6
A Novel, Non-Circular Tunnel Boring Machine for Underground Mine Development
Presented by Brad Grothen, Technical Director
Four Things You Need to Know about Probe Drilling and Pre-Grouting
This blog was originally published in 2017 and updated in 2022.
While probe drilling and pre-grouting have a long and successful history in drill and blast applications, their adoption for TBM technology has been more tenuous. Continuous probe drilling and pre-grouting was first pioneered in Norwegian hard rock D&B tunnels, where they have since been used with great success to detect ground conditions and consolidate weak rock ahead of the excavation face. If these methods have great potential to allow TBMs to excavate in difficult conditions, then there must be a knowledge gap. Here, we highlight four key things to know in order to get the most out of probe drilling and pre-grouting.
Number 1: There are always Pros and Cons
Much of the reluctance to adopt probing and grouting is based on a belief that the overall impact on the project schedule and TBM advance does not usually make up for the benefits provided. However, the benefits can be dramatic when compared to alternatives such as stuck TBMs, bypass tunnels, and other costly delays to the project schedule. The ability of a grout curtain to cut off or reduce water ingress and stabilize weak zones is unique to the method. This result has also been proven on hundreds of D&B projects over decades. When tunnel projects such as India’s Tapovan-Vishnugad Hydroelectric Project are considered, where a Double Shield TBM was brought to a halt following a massive influx of mud and water, the benefits seem clear.
There are other barriers towards industry acceptance besides time, however, and that is the perception of cost (both of course being related). In particular, in mountainous conditions or when tunneling downhill, probing may be the only practical approach towards risk mitigation, and pre-grouting may be the best possible option to control water inflows. When the cost of a stuck TBM is considered as the alternative, continuous probe drilling is looking pretty good.
Number 2: The Right Program and Machine Design can make all the Difference
Though the industry view of probing and pre-grouting tends toward the conservative, there are multiple ways to reduce impact to time and budgets while maximizing the benefits:
Plan and optimize the downtime for maintenance and cutter changes to minimize the downtime caused by probing and grouting
Proper scheduling may be one of the easiest ways to reduce downtime compared with current industry standards. To efficiently perform probe drilling and potentially pre-grouting in a TBM process, it is essential to plan the interventions and remove them from the critical path of the TBM process. Detailed planning should be done to coordinate the maintenance and cutter changing stops to the probing intervals. As an example a daily maintenance shift could be sufficient time to complete a grouting umbrella, with the correct TBM set up.
Analyze the drilling performance in detail
To get the most out of probe drilling and pre-grouting, detailed measurements of the advance rates of the probe drilling and the grouting pressure should be done. These measurements enable proper prediction of the ground ahead of the TBM. The drilling could be measured manually or automatically with Measurement While Drilling (MWD) systems, which are commonly used in D&B applications. The MWD system is used to analyze the rock in detail (hardness, water content, rock mass properties, etc.) and can be used to generate 3D-models of the rock mass in order to decide on the rock support or for documentation purposes.
Choose the right TBM Design
Ultimately, choosing the right TBM type can significantly cut time and cost. A customized machine, whether shielded or open-type, can be designed for accurate and continuous probe drilling. While it might seem that a shield machine would have limited drilling trajectories, machines like the Single Shield TBM for New York’s Delaware Aqueduct Repair offer 360-degree probe drilling paths using multiple drills, as well as probe drilling under pressure using down-the-hole hammers through ports sealed with ball joints. No matter what is needed, planning during the TBM design phase will most certainly cut downtime and costs later on.
Number 3: It has been Successful on Difficult TBM Projects
Though 100% probe drilling and pre-grouting has not yet been used extensively on TBM projects, successful examples can be found worldwide. At Canada’s Seymour Capilano Water Filtration Tunnels, using two Robbins Main Beam TBMs, 100% probe drilling (with minimum overlap) and pre-excavation grouting were specified as part of the twin down drives of the Seymour Capilano tunnel project. This was due to the down gradient of the tunnel under high cover where there was a moderate risk of encountering significant inflows. Fortunately the actual groundwater inflows were much less than originally anticipated and so very limited pre-excavation grouting was required. Probe drilling was continuously carried out during TBM excavation, and while it had an impact on progress in the early days, once the crews became familiar with the equipment and procedures the work activity became efficient, and was successfully implemented with minimum impact to progress. Success stories like this are common in deep rock tunnels around the world.
Number 4: Knowledge Level is Key to Success
As with many developments in the tunneling industry, probe drilling and pre-grouting are seen from the view of risk sharing. Risk sharing could entail clearly defined specifications and payment provisions that allow for fair compensation to the contractor so they will not be reluctant to accept the approach, for example. Clear design and environmental criteria need to be established, so the execution of probe drilling and pre-excavation grouting involve the opinion of the contractor, the design engineer, and equipment supplier. In some cases, for example, the contractor may choose to accept moderate inflows that are manageable and do not impact excavation progress.
Training in the operations of probe drilling and pre-grouting will also necessarily lead to greater acceptance. While there is some training available at colleges that offer mining and tunneling degree programs, much of the training for such operations is necessarily hands-on and experience based. With an experienced workforce, the negatives of probe drilling and pre-grouting are greatly reduced. Such hands-on training is currently being provided by Robbins on several projects using a combination of classroom instruction and jobsite operation for crews who are not familiar with the methods.
Ultimately, the adoption of probe drilling and pre-grouting on TBMs is something that must be recognized as an overall benefit to the industry in difficult ground conditions. The technology is well developed in D&B tunneling, and it has been field-tested for decades. It is, in our opinion, the best method of accurately detecting and treating poor ground conditions in front of the TBM.
Robbins TBM takes on Karstic Limestone below St. Louis
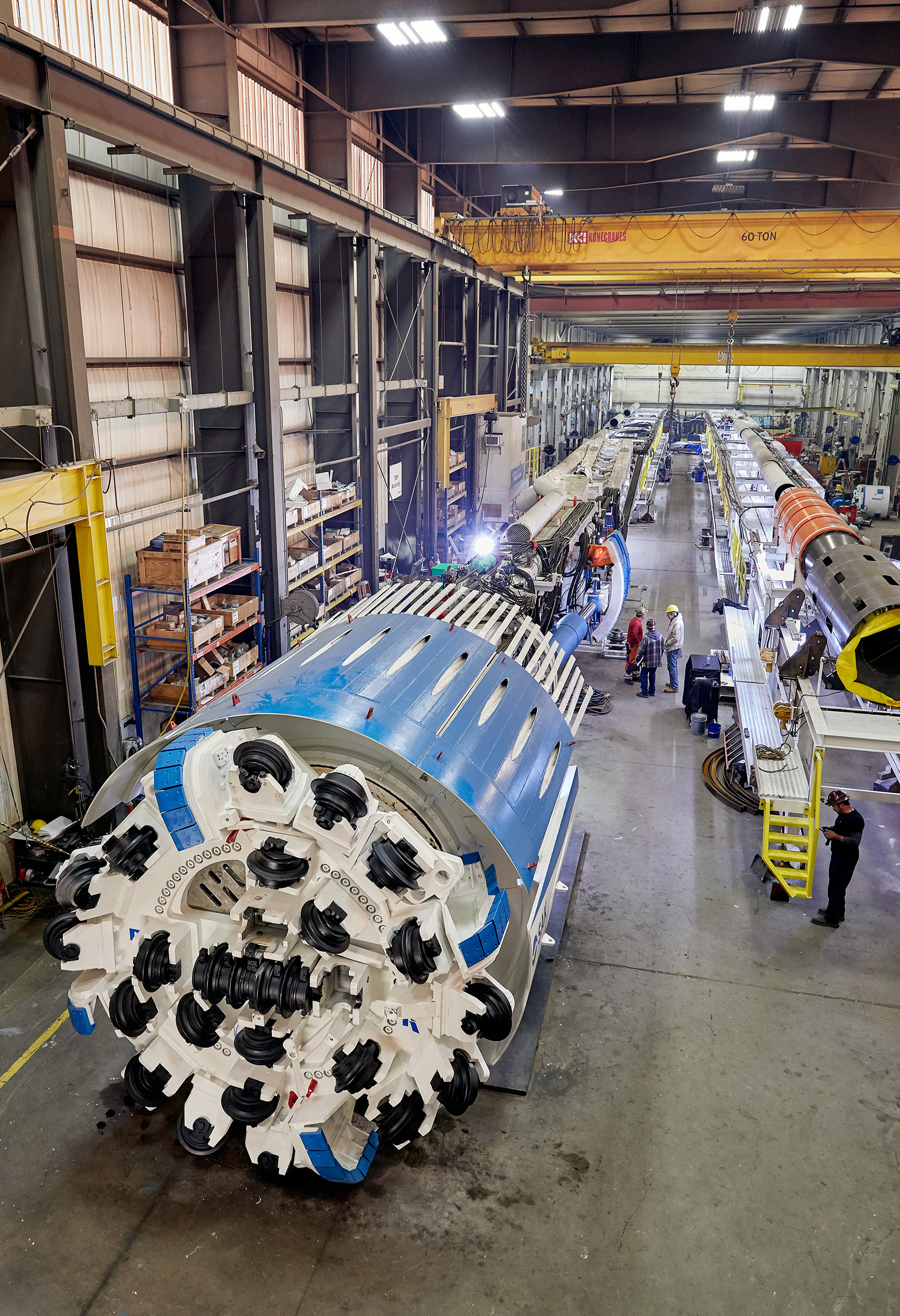
The Robbins Main Beam is boring well so far, advancing 21 m (70 ft) in its first two shifts after launch.
In Spring 2022, a specialized Robbins 4.1 m (13.5 ft) diameter Main Beam TBM launched in St. Louis, Missouri, USA, to complete a critical infrastructure tunnel for contractor SAK Construction. The machine, named “Mrs. Vera”, is boring Phase 2 of the Jefferson Barracks tunnel, a 3,050 m (10,000 ft) long tunnel in karstic limestone. Designed to detect karst and other underground features, the unique machine comes equipped with enhanced 360-degree probe drilling capabilities, as well as versatile ground support options including McNally crown support, wire mesh, ring beam erector and roof drills.
“The overall design of the machine is a good fit for our project, not only for the mining aspect but also for the capability to run two probe drills in multiple locations around the TBM,” said Brotherman Bragg, Project Superintendent for SAK Construction. “The challenges I anticipate during tunneling are mostly related to ground conditions. The area that we are tunneling in has a potential for karst features. The probe drills are our lifeline and with the two probe drills on the machine, I believe that we will find out what’s in front of us before we get there, giving us the ability to take care of potential problems.”
During Phase 1 of Jefferson Barracks, a rebuilt 3.35 m (11.0 ft) diameter Robbins Main Beam TBM hit challenging conditions about 2,400 m (7,900 ft) into tunneling. The machine encountered a large vertical feature along with flowing and unstable ground that required the TBM to remain in place. While various options including ground freezing were considered, they were ultimately deemed infeasible.
A 62 m (205 ft) deep recovery shaft and 60 m (200 ft) long adit were built to stabilize the area and remove the machine in what would be an intensive and ultimately successful undertaking. After recovery of the machine, SAK Construction turned to Robbins for a solution to bore the remaining tunnel in what would become Phase 2 of the project.
SAK and Robbins agreed to do extensive in-shop testing of the new, larger TBM to ensure there would be no unnecessary delays on site. The TBM was ultimately delivered a couple months late due to both COVID-related matters and the additional in-shop testing. SAK operational personnel and Robbins personnel were heavily involved in final assembly and testing procedures.
After arriving in St. Louis, the TBM was swiftly assembled and launched from the recovery shaft. “The Robbins Field Service techs have been excellent in their support, helping us assemble the machine, and troubleshoot the machine. Our challenges during the assembly and launch from the shaft were minimal – this is the fastest and most efficient assembly we’ve ever had on a machine. We assembled the TBM in four weeks, which was a huge hurdle,” said Bragg.
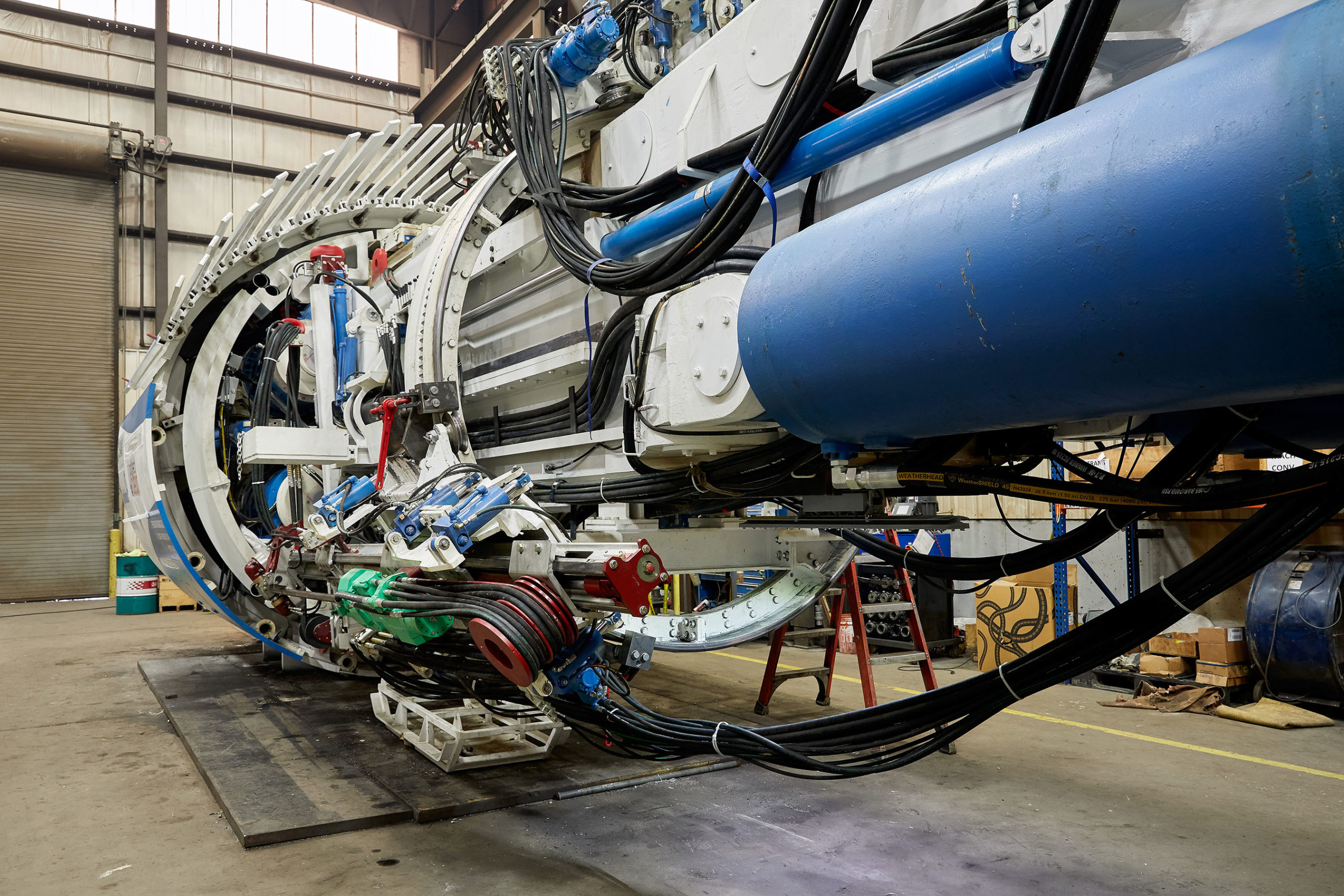
Designed to detect karst and other underground features, the unique machine comes equipped with enhanced 360-degree probe drilling capabilities, as well as versatile ground support options.
“The overall design [of the TBM] is very functional and thus far in the early stages it seems to be mining very well,” continued Bragg. “So far, I’m very pleased with the machine and with the technicians.” Early indications were good, with the machine advancing 21 m (70 ft) in its first two shifts after launch.
The Jefferson Barracks project is a key component of MSD Project Clear, a massive USD $6 billion program undertaken by the Metropolitan St. Louis Water District to target water quality and wastewater concerns in the city and surrounding areas. The 5,400 m (17,800 ft) long, 2 m (7 ft) internal diameter Jefferson Barracks tunnel runs parallel to the Mississippi River and extends to the Lemay Wastewater Treatment Plant located at the confluence of the River des Peres and the Mississippi. The tunnel is slated for completion in Autumn 2023.
Robbins Main Beam Triumphs on Challenging China Drive
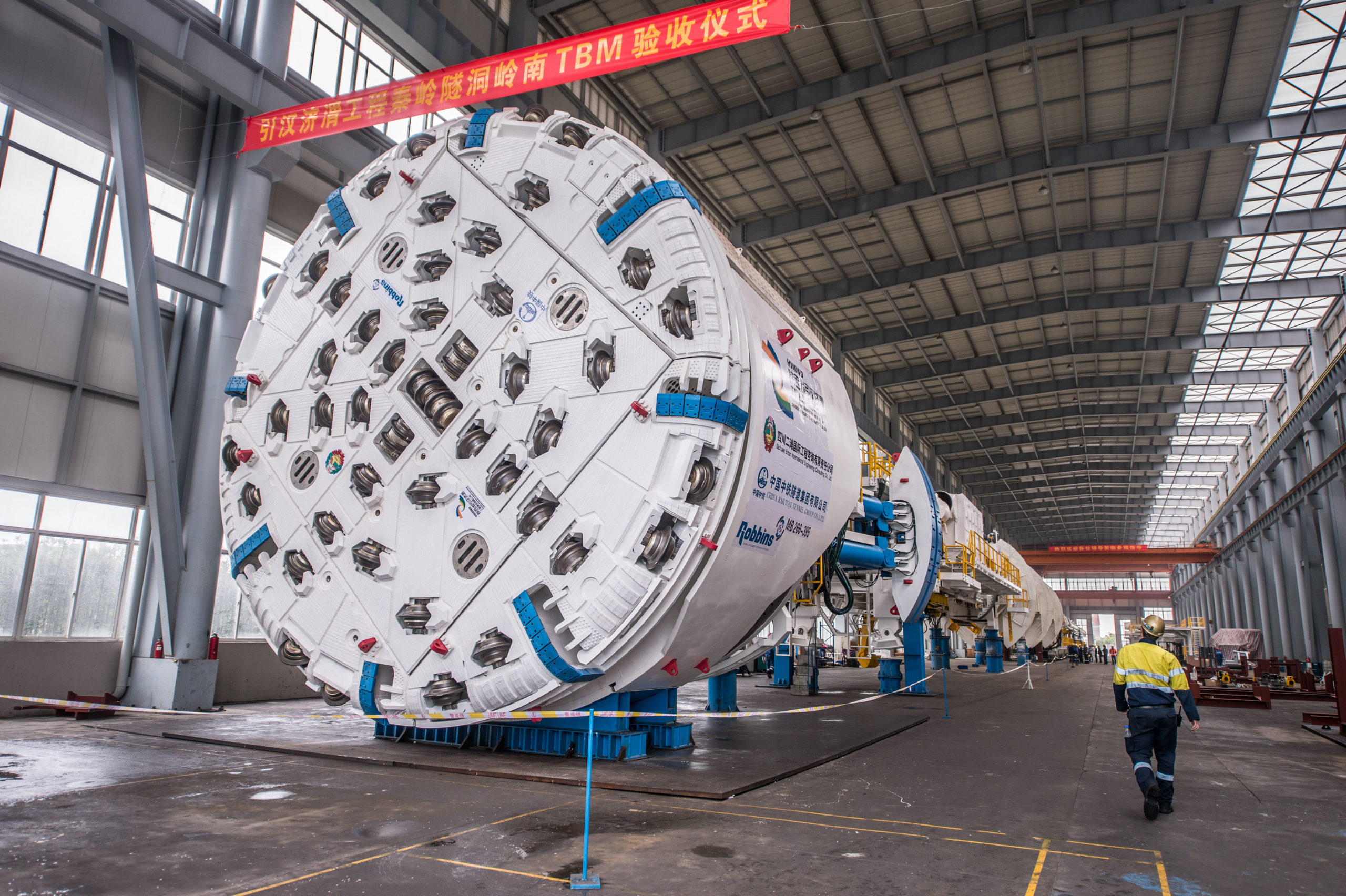
The Robbins TBM and experienced crew were able to overcome difficult conditions including severe water inflows, abrasive rock with a maximum quartz content of 92.6%, high energy rock bursts, and more.
The breakthrough of an 8 m (26.2 ft) diameter Robbins Main Beam TBM at China’s Yin Han Ji Wei project is not only a cause for celebration, but also a triumph of technology and perseverance. The machine overcame 17.5 km (10.9 mi) of tunnel in some of the most difficult geology ever encountered, breaking through in the first quarter of 2022. The water diversion tunnel traverses the Qinling Mountains of Shaanxi Province, with up to 2,000 m (1.2 mi) of cover.
“Every day was full of challenges. We are most proud of our teamwork and unyielding spirit,” said a representative for tunnel contractor China Railway Tunnel Group (CRTG). The ground, consisting of mainly quartzite and granite, was estimated to have a rock hardness of between 107 and 309 MPa (15,500 to 45,000 psi) UCS, with high abrasivity and a maximum quartz content of 92.6%.
“This was in my opinion the most challenging project ever completed by TBMs, and it proves TBMs are up to overcoming even the most difficult conditions. I have great respect for the CRTG crews and management, and I thank them for moving TBM technology to a new level,” said Robbins President Lok Home.
During tunneling, crews encountered over 14,000 rock bursts, some with energy as high as 4,080 kJ. “Robbins’ overall equipment performance was excellent from the beginning to the end of breakthrough, and during seven years of excavation. This is despite the super hard rock with high quartz content, strong rock bursts, and substantial water inrushes,” said the CRTG representative.
Water ingress occurred a total of 69 times during the drive, with some inflows extremely high – exceeding 20,000 m3 (700,000 ft3) of water in one day from a single point. In-tunnel ambient temperatures peaked at 40 degrees Celsius and 90% humidity.
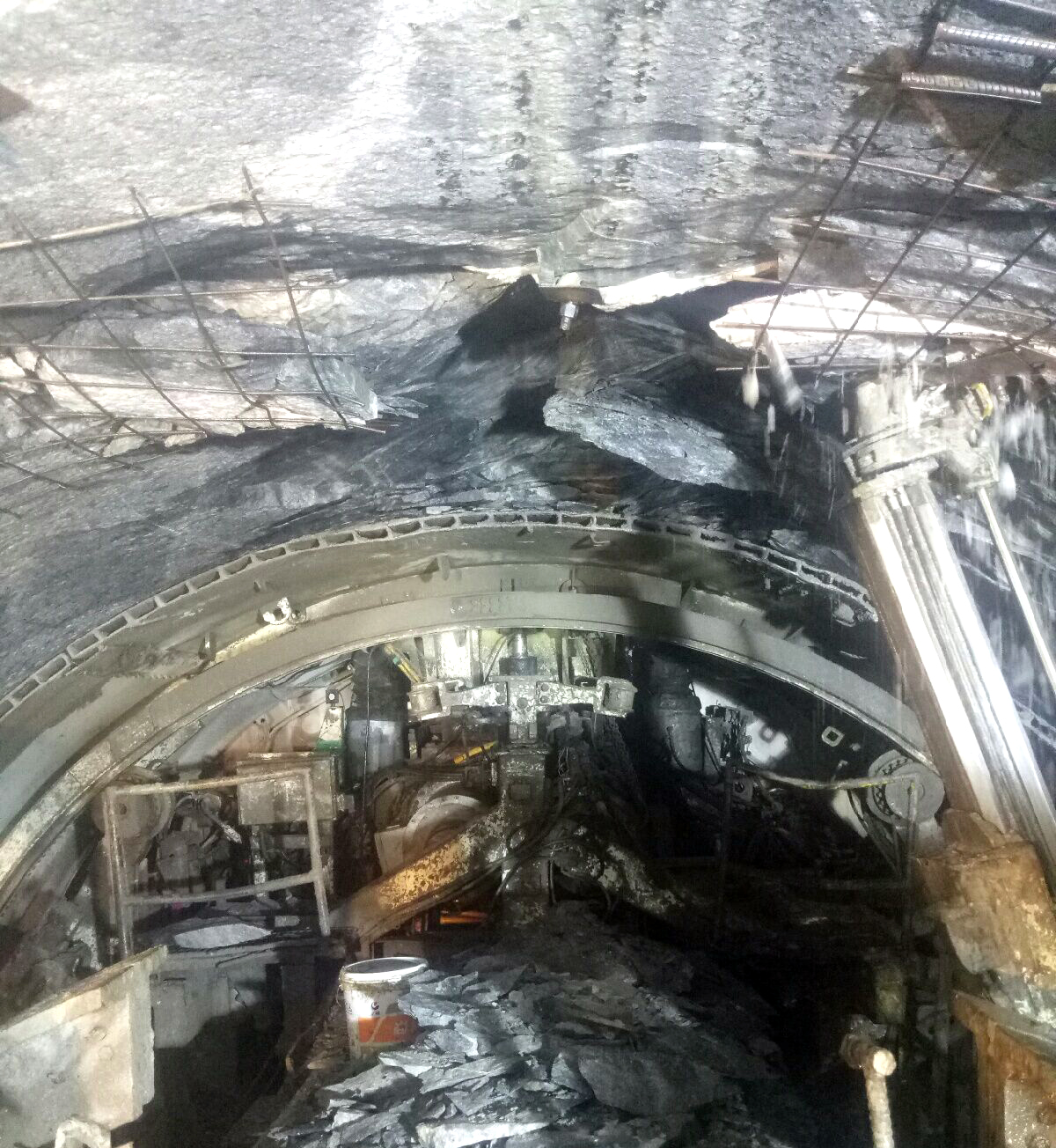
During tunneling, crews encountered over 14,000 rock bursts, some with energy as high as 4,080 kJ.
Throughout the challenges, the crew found ways to persevere. Rock bursting was controlled using steel slats in conjunction with the McNally crown support system, while zones of stress were predicted using a micro-seismic monitoring system. The micro-seismic system records rock stresses in a borehole 20 m (65 ft) ahead of the face and predicts the potential for rock bursting following comparative analysis with similar rockburst data from other projects, as well as from nearby sections of tunnel in the Qinling Mountains.
Water ingress was controlled by dramatically increasing pumping capacity in the tunnel to 41,000 m3 (1.4 million ft3) per day. Systematic probing ahead of the TBM was also used to detect water, as well as rock bursting. When ingress exceeded 70 percent of the in-tunnel pumping capacity, crews then carried out grout injections.
The abrasive, hard rock was another challenge, addressed by Robbins through the use of Extra Heavy Duty (XHD) 20-inch disc cutters that showed long cutter life and lower wear compared to standard 20-inch discs. The crew also optimized TBM operation with at times lower production rates where needed. “Especially with such a huge challenge, a strong cutterhead is required to ensure production. The quality of Robbins’ cutterhead has been proven. The cutterhead can still work properly after the tunnel breakthrough,” said the CRTG representative.
With TBM tunneling complete, the route will become part of two other sections of an altogether 82 km (51 mi) long tunnel that will link up the Hanjiang and Weihe Rivers in Shaanxi province. The completed tunnel, for owner Hanjiang-to-Weihe River Valley Water Diversion Project Construction Company, will secure a water supply for towns and agricultural areas in Central China, while also generating hydroelectricity.
Robbins Single Shield completes Canada’s Largest Outfall
On March 3, 2022, a 7.95 m (26.1 ft) diameter Robbins Single Shield TBM completed a record-setting run below Lake Ontario. The machine, for the Southland/Astaldi JV, bored 3.5 km (2.2 mi) in sedimentary rock for the Ashbridges Bay Outfall in Toronto, Ontario, Canada.
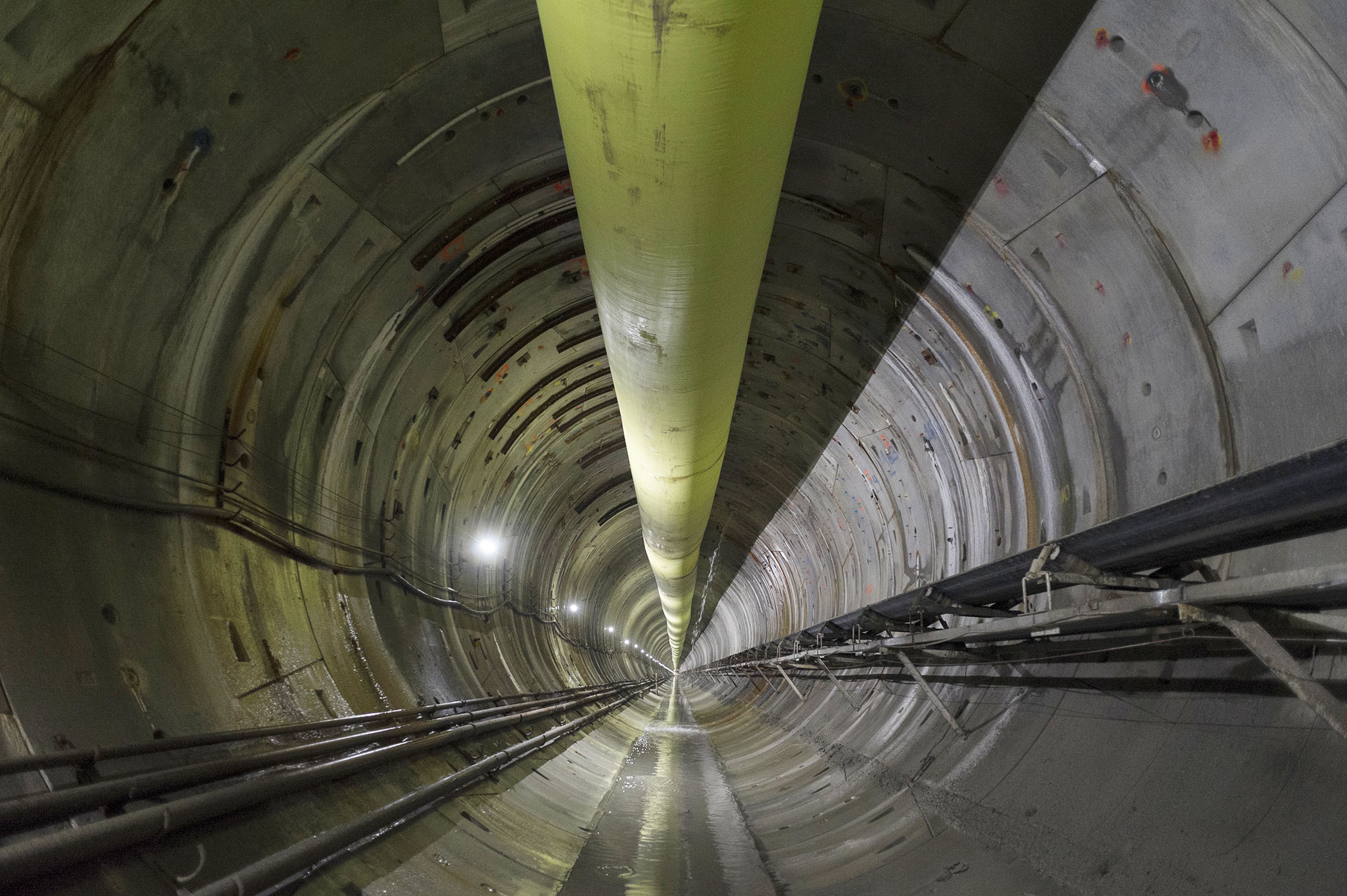
The 3.5 km (2.2 mi) long Ashbridges Bay Outfall Tunnel is Canada’s largest outfall and connects to 50 risers in Lake Ontario.
The machine launched in March 2021 from an 85 m (280 ft) deep, 16 m (53 ft) diameter shaft and began its bore in predominantly shale, with limestone, siltstone and sandstone. During its excavation, the TBM and its experienced crew bored a city-wide record of 30 rings in one day, or about 47 m (154 ft) of advance. The machine and crew surpassed a previous best day of 21 rings at a project with similar specifications. “We are proud to have completed another successful tunnel with Robbins and greatly appreciate their field service support,” said Joe Savage, Project Manager for Southland.
“This is a wonderful type of geology for our machines. During the entire excavation, a total of 7 cutters were changed. The wear behavior is incredible, between 2 and 5 mm, and everyone is amazed by the cutter performance,” said Alfredo Garrido of Robbins Field Service.
The crew had been operating the machine in two shifts of 12 hours from Monday to Friday. A Robbins continuous conveyor system including vertical conveyor transported muck behind the machine. “Every 25 machine cycles, it was necessary to stop the excavation to probe drill hole in front of the cutterhead to check for possible water. This drilling was done basically every day, stopping the machine for a few hours, but it was very necessary,” said Garrido.
The last kilometer of tunnel, bored below a series of 50 risers under Lake Ontario, was challenging but ultimately successful. “The team really worked together to overcome some tough ground conditions and high water inflows in the tunnel,” said Savage.
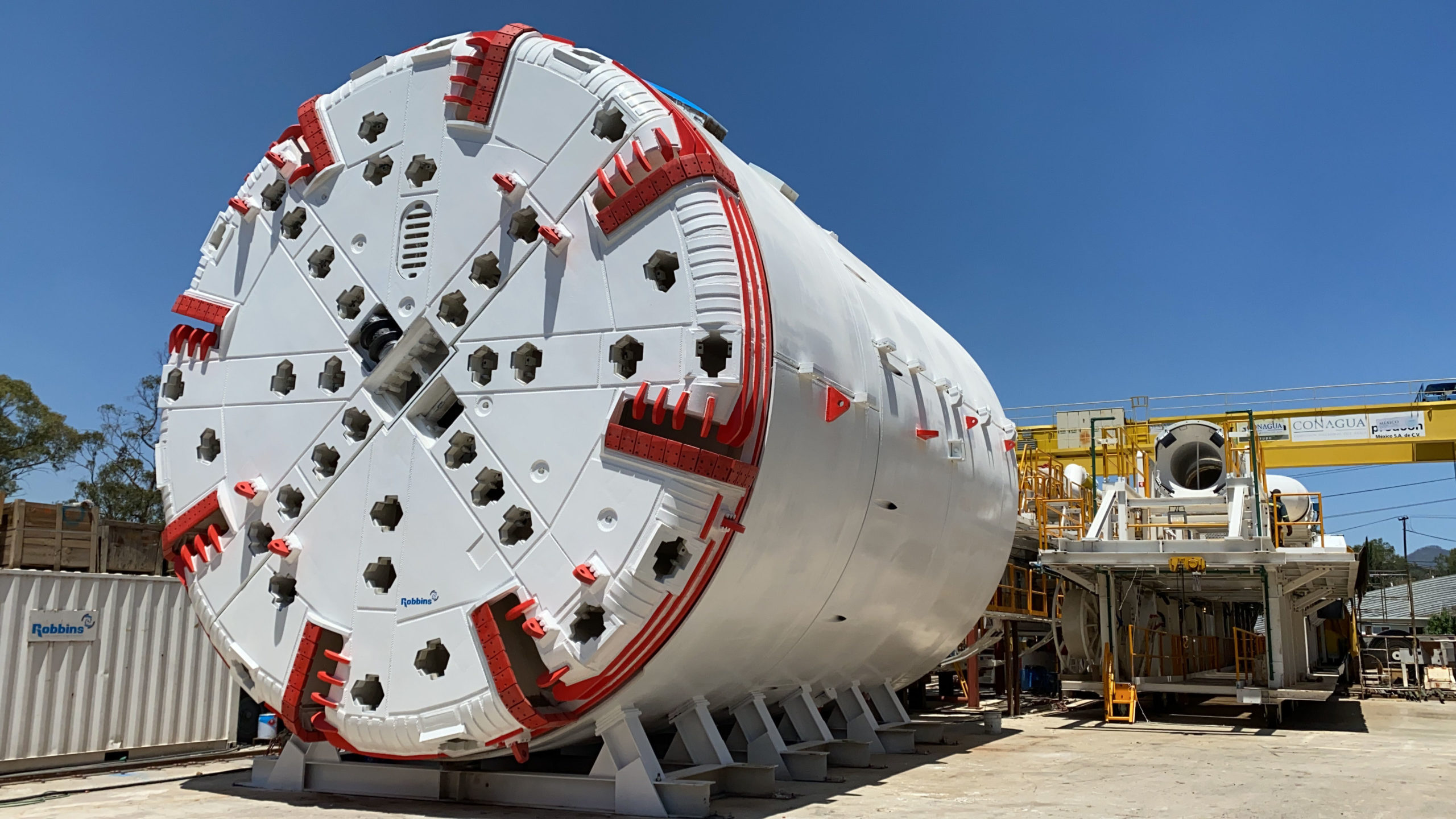
The Ashbridges Bay Outfall won accolades from the Tunnelling Association of Canada (TAC) in late 2021 for its all-remote machine acceptance, the first of its kind, enacted due to the Covid-19 pandemic.
The success of the TBM is just one cause for celebration. The project won accolades from the Tunnelling Association of Canada (TAC) in late 2021 for its all-remote machine acceptance enacted due to the Covid-19 pandemic. The machine acceptance, the first of its kind, enabled communication and confirmation between the machine’s assembly location in Mexico, suppliers in the U.S. and those involved in Canada. “It was a challenge for all the people involved due the pandemic travel restrictions; however, due to good planning and communication we were able to go through the Acceptance Test successfully. I think this might become quite common in the near future,” said Robbins Project Manager Javier Alcala.
The completed outfall will connect to the 50 in-lake risers to enable efficient dispersion of treated effluent over a wide area of the lake, making it the largest outfall in the country. The project for the City of Toronto will improve the city’s shoreline and Lake Ontario’s water quality by replacing a 70-year-old existing outfall.
6º Simposio Internacional de Túneles y Lumbreras en Suelos y Rocas
Join AMITOS, the Mexican Society for engineering of tunnels and underground space, in the sixth symposium on tunnels and shafts in soil and rock. Robbins President Lok Home will kick off the conference with a virtual keynote talk on the industry’s approach to R&D, focusing on a particular innovation: non-circular tunneling in rock.
Keynote Talk Details:
Monday March 29
9:00 – 10:00 AM CT
Non-Circular Tunneling in Rock: A New Way Forward
Presented by Lok Home, Robbins President
CIM 2022
Event Name: CIM Convention
Location: Vancouver, BC, Canada
Dates: May 1-4, 2022
The CIM Convention focuses on the future of mining. Join Robbins at the conference for a presentation with Robbins Technical Director, Brad Grothen, P.E., on new innovations for underground mining in rock. Keep an eye out for Abstract Number 252: Faster Underground Mine Development: Getting to First Ore Quicker using a Novel, Non-Circular Tunneling Machine – date and location coming soon! Find out how to reach your ore body quicker, safer and more cost effectively in this talk.
Large Diameter Crossover TBM: Success in Turkey & Future Applications
Large diameter tunneling in mixed ground has historically been seen as a challenge, but a recently completed tunnel in Turkey has changed the conversation. A 13.77 m diameter Crossover XRE TBM bored the Esme Salihli Railway Tunnel at world-record-setting rates of up to 721.8 m in one month, making it the fastest TBM over 13 m in diameter.
Join tunneling experts Brad Grothen P.E., Robbins Technical Director; Şevket Kılıç, TBM Engineer for contractor Kolin Construction; and Prof. Dr. Nuh Bilgin, Chairman of the executive board of the Turkish Tunnelling Society in this complimentary, 45-minute webinar. We’ll discuss the remarkable advance rates, experiences, and future applications for Crossover machines both within Turkey and worldwide. A live Q&A session will be held at the end where you can get a thorough answer from our expert speakers.
REGISTER HERE
NAT 2022
Event Name: North American Tunneling Conference (NAT)
Dates: June 19-22, 2022
Location: Philadelphia, Pennsylvania
Booth: 205
Come join us in Philadelphia, Pennsylvania, USA June 19-22 at the North American Tunneling Conference, the premier tunneling event focusing on current projects, challenges, and successes in tunneling. Our team of experts will have brochures, technical papers, spec sheets, and the latest updates on our machines. Visit our booth 205 to learn more about our ongoing and successful tunneling projects, and be sure to check out our insightful technical presentations.
Technical Presentations
Monday June 20
TBM Technology Session
Salon G
2:00 – 2:25 PM
Unprecedented In-Tunnel Diameter Conversion of the Largest Hard Rock TBM in the U.S.
Presented by Evan Brinkerhoff, Robbins Field Service Site Manager
2:50 – 3:15 PM
Hard Rock Tunnel Boring in Challenging Conditions at the Jefferson Barracks Tunnel
Presented by Doug Harding, Robbins Sr. Vice President
3:15 – 3:40 PM
The Next Generation of Mixed Ground Tunnel Boring Machines
Presented by Brad Grothen P.E., Robbins Technical Director
Robbins Crossover holes through in the Andes
A Robbins 4.6 m (15.1 ft) diameter Crossover machine holed through in the Andes Mountains of Chile in the last quarter of 2021. The XRE TBM bored a 3.3 km (2.1 mi) long tunnel for Chile’s Los Condores Hydroelectric Power Project (HEPP) and project owner Enel.
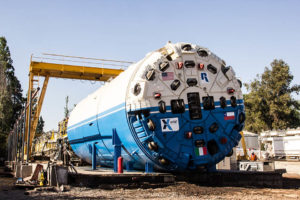
The Robbins Crossover (XRE) TBM bored a 3.3 km (2.1 mi) long tunnel through the Chilean Andes.
A dedicated team, including three Robbins Field Service personnel, guided the machine to breakthrough in conditions including tuff, sandstone, breccia, and conglomerate with sections of high-pressure water inflows. Ground cover reached up to 450 m (nearly 1,500 ft) above the tunnel with rock strengths maxing out at 60 MPa UCS. “Robbins Field Service was an important part of the success of the excavation, evaluating continuous improvements in the machine and correcting faults,” said Ricardo Riveros Puratic, Project Engineer for Enel.
For Riveros Puratic, Crossover machines make sense despite the challenging conditions: “Towards the end, [the TBM] exceeded expectations. Crossover TBMs are suitable for Andean geology of sedimentary and volcanic type, where there is a great range of rock strengths and hydrogeological conditions.” Maximum advance rates topped out at 605.8 m (1,988 ft) in one month and 212.8 m (698.2 ft) in one week.
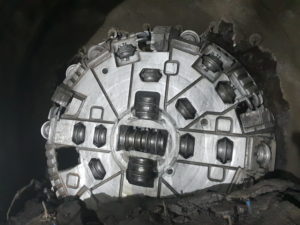
Despite challenging mixed ground and fault zones, the Robbins TBM achieved advance rates of up to 605.8 m (1,988 ft) in one month.
The Crossover machine featured a heavy duty, centrally mounted screw conveyor for the duration of the drive. The TBM remained in a hard rock configuration with muck chute installed, along with paddles, bucket lips, scrapers and disc cutters on the cutterhead. However, “75% of the excavation was performed using the main drive gearboxes in high torque configuration (EPB or low speed mode). We never physically changed the cutterhead or screw conveyor to EPB mode,” said Omar Alvarez, Robbins field service site manager at Los Condores.
High-pressure ground water inflows were the key challenge of the project. “When we started the excavation, we used dewatering hoses to reduce the water into the cutterhead during the excavation,” said Alvarez. Water pressures rose whenever the TBM stopped, however. “During the segment ring installation, we stopped the water from draining through the rear shield drilling ports and we closed the screw conveyor rear gate. We reached 7+ bar in the cutterhead earth sensors.”
“We bored in places with 5,500+ liters (1,500 gal) /min, making back-fill grout injection behind the concrete segments a challenge. We decided not to use the grout injection through the tail shield ports, but instead injected grout directly through the concrete segment with hoses. This approach was more flexible and reduced the need for reinjections,” said Alvarez.
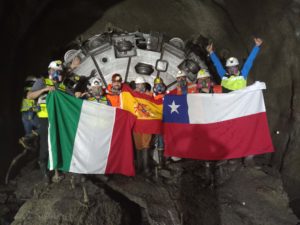
Robbins Field Service and dedicated crew guided the XRE TBM through challenging conditions including water inflows of 5,500+ liters/min.
With multiple triumphs and lessons learned during tunneling, Alvarez reflected on the breakthrough: “I’m proud to be part of a team that finished a tunnel in the Andes Mountains.” Once brought online, the Los Condores HEPP, located in the mountainous southern Maule region, will have an annual generating capacity of 150 MW.