Sin categorizar
Fueled by Vietnamese Coffee: My Epic Adventure at Thuong Kon Tum
Traveling in the tunneling industry is basically a regular commute for some. A lot of us don’t think twice about the destination, we just do it with a mission in mind. My mission as Robbins Marketing Manager was this: a small conference in Ho Chi Minh City. Okay, easy! As the date approached, about a month before, I kept hearing about how well our Main Beam TBM was doing in Vietnam, at the Thuong Kon Tum Hydroelectric project, despite a gauntlet of challenges. I talked to some project engineers and field service personnel who told me it was in a remote location in Kon Tum Province. And then I heard more about traveling to that site: a 6-hour drive from Da Nang, through nauseating windy, narrow roads, climbing elevations with no speed limits to speak of. But that’s cool, I thought, glad I don’t have to go on that ride.
“Wait, why not just go to the jobsite for a video and photo shoot? We can have it ready for the breakthrough in October,” says Desiree Willis, Robbins PR manager a couple weeks later. What!? A few days after that, it was all planned. Ron, our videographer, Ken, our photographer, and Keri Lin, our marketing manager from Robbins China, set off with me on a last-minute adventure. The 17.4 km long Thuong Kon Tum HEPP tunnel will be the country’s longest once complete. A 4.5 m diameter Robbins Main Beam TBM and continuous conveyor system were supplied to bore a section of the tunnel.
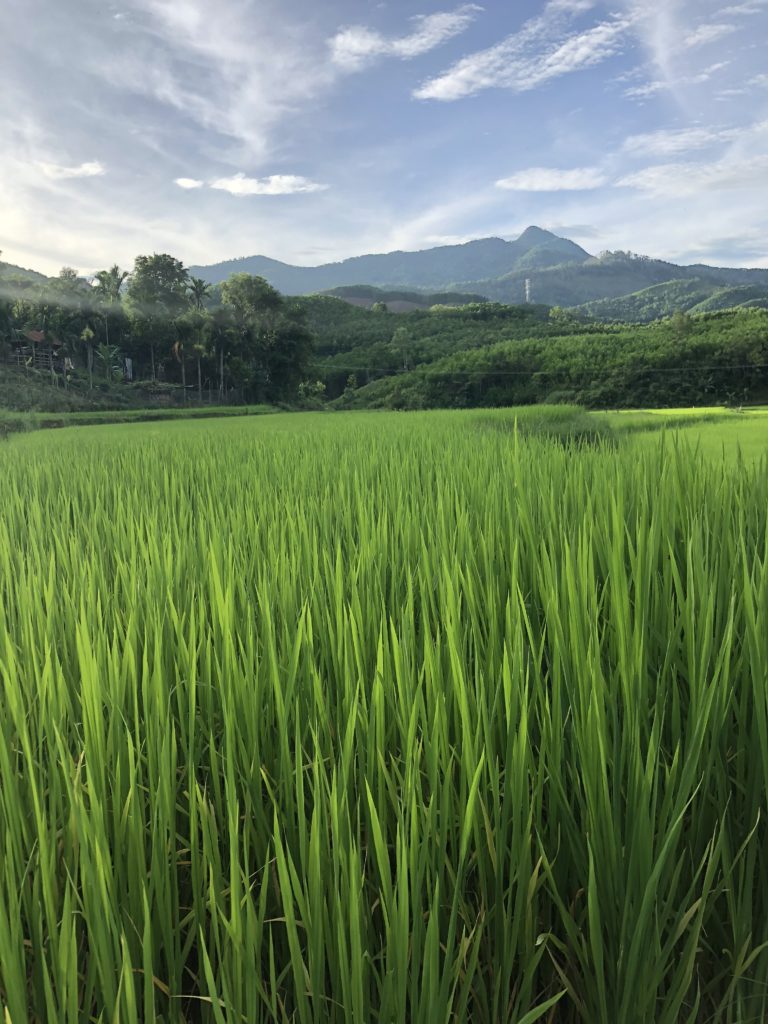
A terraced rice paddy with a beautiful mountain backdrop, so typical of what is synonymous with the sights of Vietnam.
Maybe because I was bracing myself for the worst as far as the drive goes, I didn’t feel like it was that bad. The scenery was jaw dropping with lush jungle, rice paddies and scenic villages, and so many distractions on the sides of the road that I just completely avoided looking ahead. Problem solved! The coolest distractions were the scooters driving on these mountain roads: what they were carrying, how many people were on them, their driving technique. My favorite site was seeing a whole family of people—a 5-year old kid in the front, the dad driving, the mom in the back and a toddler sandwiched in between the parents—on a run-down 125 cc scooter. Then there’s the animals: a litter of stray dogs, adorable black piglets making road crossings that almost made me swear off bacon, herds of cows, goats, etc.
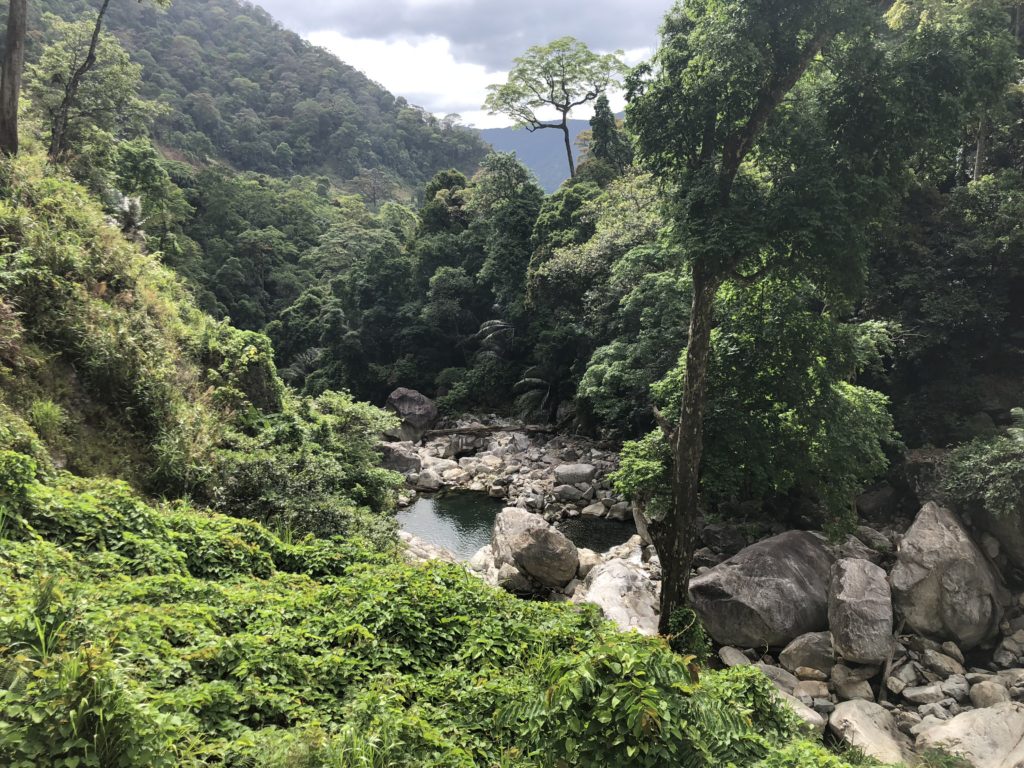
This was about a half hour away from the jobsite in Kon Tum province. The picture doesn’t truly depict how beautiful it was in person.
But how the heck did they get the machine, assembled by Onsite First Time Assembly (OFTA), to the site? Apparently, the previous contractor built portions of the roadway to the jobsite while components were staged at the port site. Several bridges, previously built only for light traffic with scooters and carts, were rebuilt or reinforced in order to carry the heavy TBM components. In a road conditions survey report by logistics firm SDV Vietnam Company Ltd., the original bridges were described as “having no shoulder”, and as having “blind corners and sharp curves”. The OFTA process allows a TBM to be assembled on location, saving time and money in terms of shipping costs and project schedule. The machine had successfully made it to the site, as it had launched in 2012.
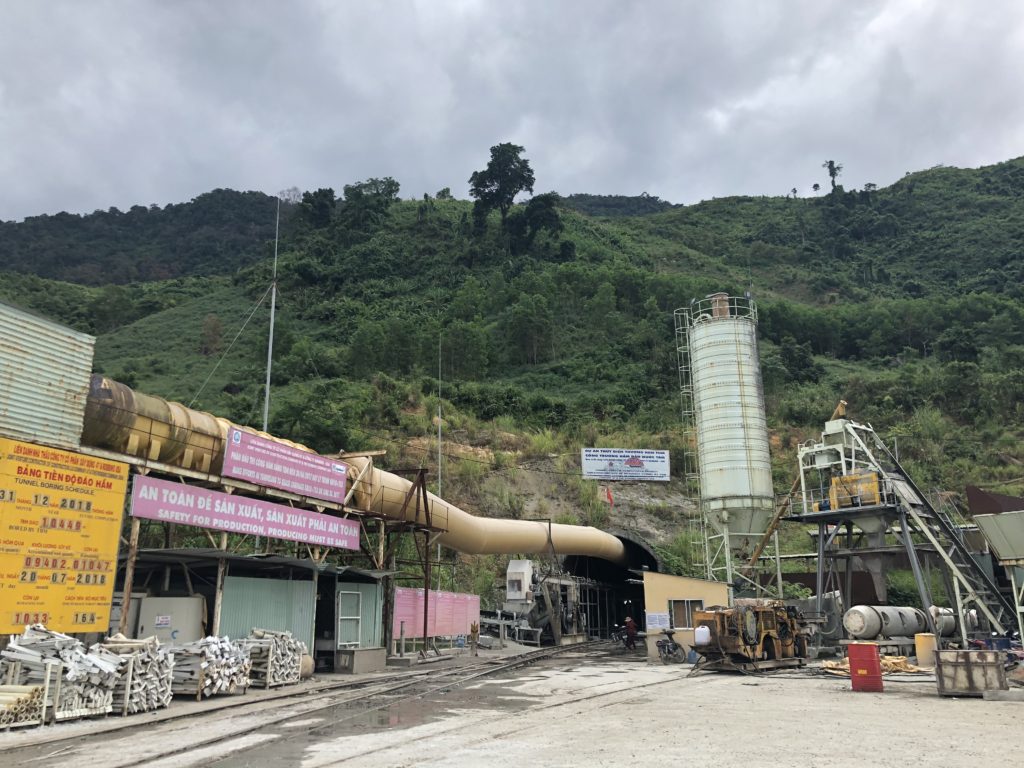
Not pictured: the litters of stray dogs and chickens roaming around the jobsite. Oddly enough, I never saw any stray cats here.
Upon arriving at the jobsite, I was immediately impressed with the site and the surroundings, especially after hearing about all of the challenges the project had back when the TBM was launched, under a different contractor. The TBM launched into complex rocky conditions that turned out to be quite different than in the original geological study. The machine sat abandoned 2.6 km into the tunnel with equipment sitting idle for months, waiting for a change in circumstances. In 2015, Robbins signed a contract with the project’s new contractor CC47 to supply full refurbishment and to operate the equipment with a full Field Service team. Since then, Robbins Field Service has generally been kicking butt.
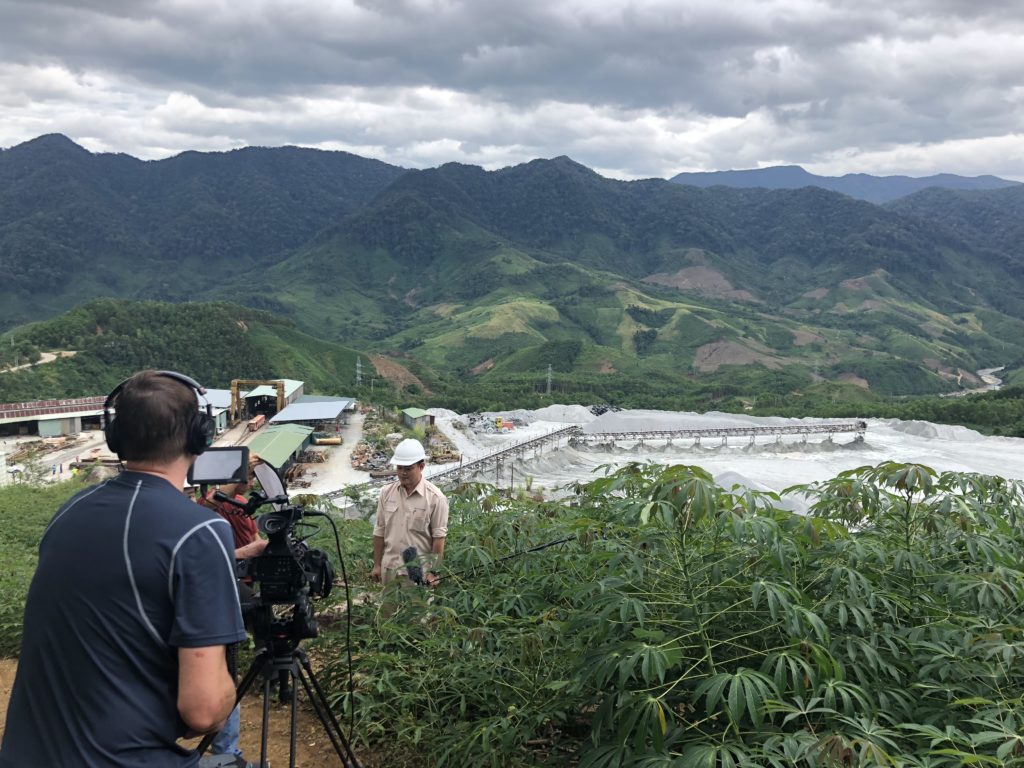
We hiked up a mountain to get this panoramic shot of the project site. I think it was worth it!
The machine was running as expected, so filming interviews and the machine went smoothly. I learned a lot from the interviews, mainly from the Robbins guys we interviewed—PN Madhan, Robbins Engineering Geologist, and Greg Adams, Robbins Field Service Manager. “It’s a workhorse of a machine and still in great condition, considering all of the difficult ground it’s been through,” Greg mentioned. Massive granitic rock wasn’t the only challenge they faced—the team also endured a handful of major fault zones requiring rock bolting and the use of the McNally Roof Support System, as well as some huge water inflows.
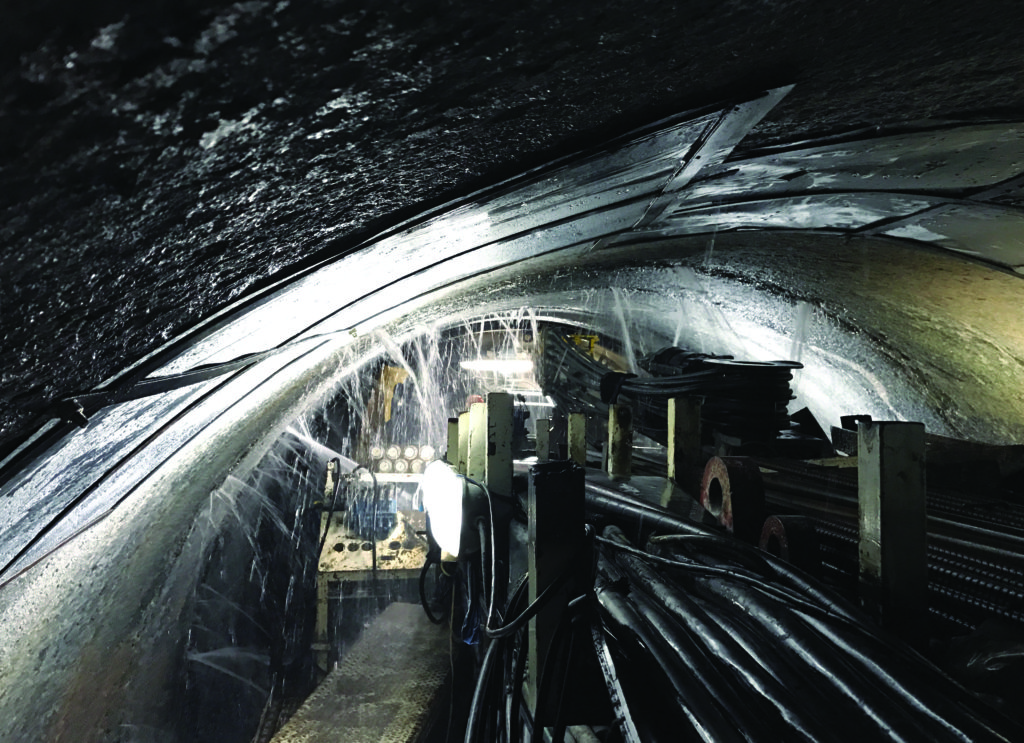
Water inflows were up to 600 liters per second—that’s nearly enough to fill an Olympic-sized swimming pool every hour!
Greg did warn our photographer and videographer that they were going to face heat with extremely high humidity. When John McNally, Robbins Field Service Manager-Asia, took over the project site, he managed refurbishment of much of the equipment inside the tunnel along with the camp’s living quarters. This included adding a ventilation tube, keeping the tunnel at a cool 34°C. That’s the temperature AFTER installing the ventilation. Read more about the challenges here.
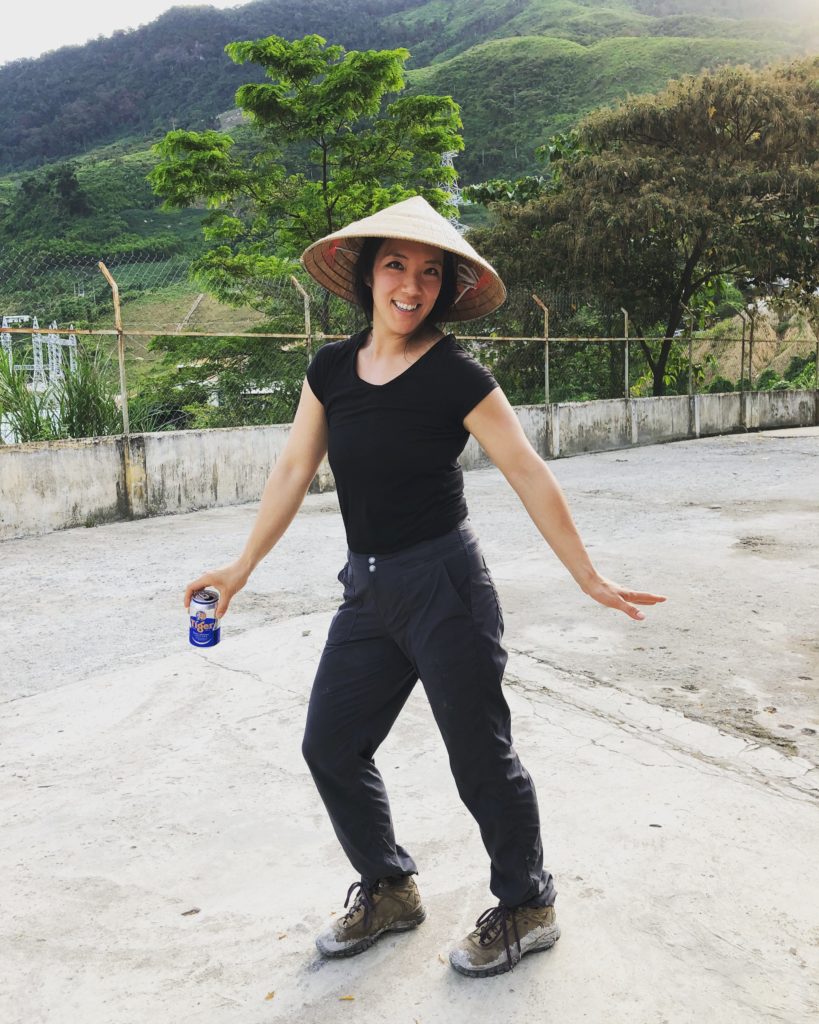
While waiting for dinner, I got posing tips from Keri Lin and our photographer for my next career as an Instagram model. A refreshing beverage and the typical Vietnamese farmer hat were absolutely necessary for the scorching hot day at the site.
The crew at the camp quarters, and the jobsite in general, were very welcoming. Greg and Taylor Hwang, Robbins project manager, arranged for a special dinner just for us on the first night—steak and French fries, an American staple! The crew on site mainly consists of English-speaking expats, Chinese, Thai, Vietnamese, Indian and Philippine guys, so the cuisine varied every day. We hung around that night for a while, listening to stories from some of the field service crew. This is while we were fawning over the pet falcon that one of the field service guys owned. I think the falcon liked living there, because his string wasn’t even tied to the perch at one point. Taylor told us that there were some families and children of the crew living there, who had to find ways to pass the time in this little remote village. He even told us they had pet monkeys at one point. I peeked into a living quarter and saw a drum set made with those Danish butter cookie tins that you get at Christmas. That’s one way to pass the time! Before we were about to leave, some of the Thai people at the site had brought in a bucket with a cover over it. I was curious and went to take a peek, because they started adding salt to the buckets. It was about 30 river snakes (possibly river eels, but they called them snakes) writhing violently because of the sodium touching their skin. Then they started preparing them one-by-one, sticking a nail into their heads and gutting them. It was quite mesmerizing, really.
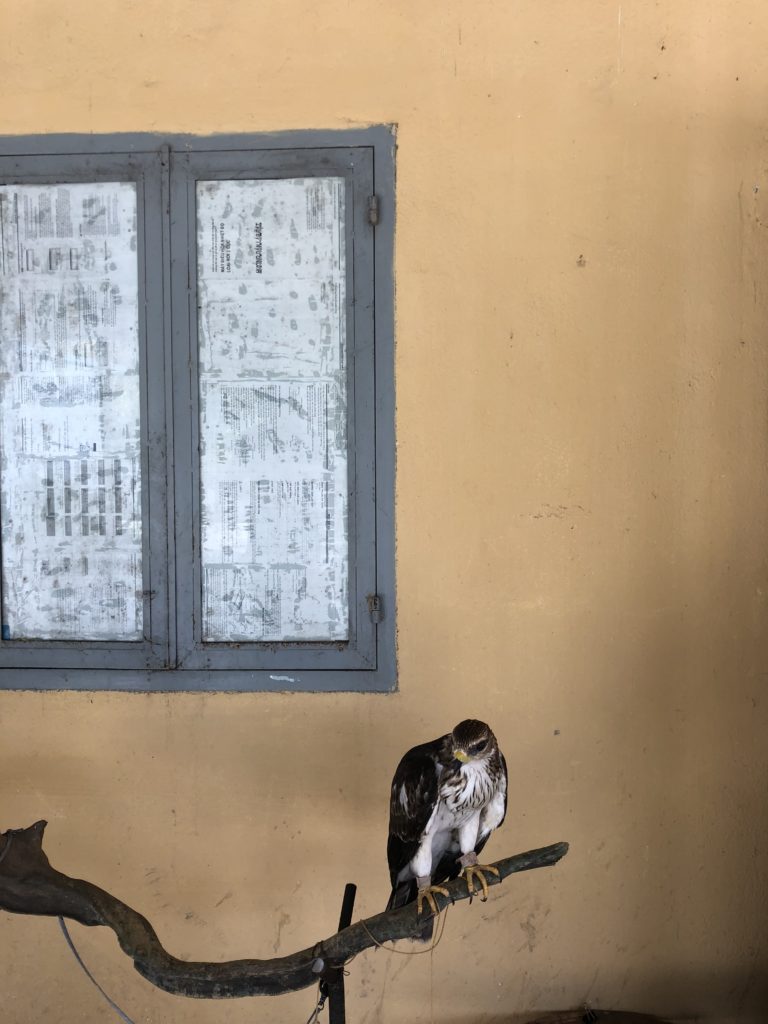
The camp’s pet falcon.
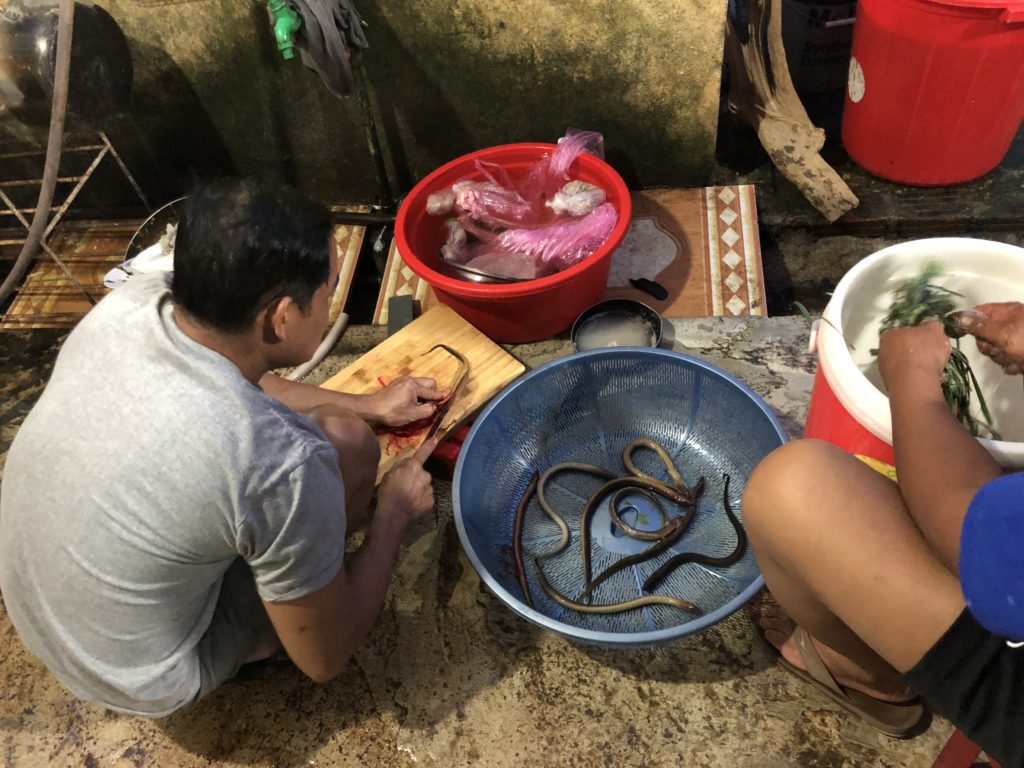
Not sure if this is the regional cuisine but the snakes were caught at a river close by the camp.
We only had two full days of shooting video and photos. Before the 6-hour drive back to Danang, all of us got caffeine-drunk on two strong Vietnamese coffees served with condensed milk each. I suspect it’s the perfect combination of the tenaciously strong espresso dripped into a puddle of pure sugar syrup (condensed milk) that singlehandedly causes adult ADHD from the first sip. During the drive down (which was much worse, I didn’t realize how much elevation we climbed going up), we were already reminiscing about the stories and experiences shared at the jobsite. When talking to the field service crew, they were all excited for the coming breakthrough later this year, but it seemed they were just a bit melancholy too. They were at this site for years, in a tiny remote village in the mountains of Vietnam, building friendships and routines. With only a handful of meters left to go on the tunnel, they’ll soon be off to the different parts of the world where they came from. I’m fortunate to have experienced everything I did on this trip and can’t wait to come back to this beautiful country.
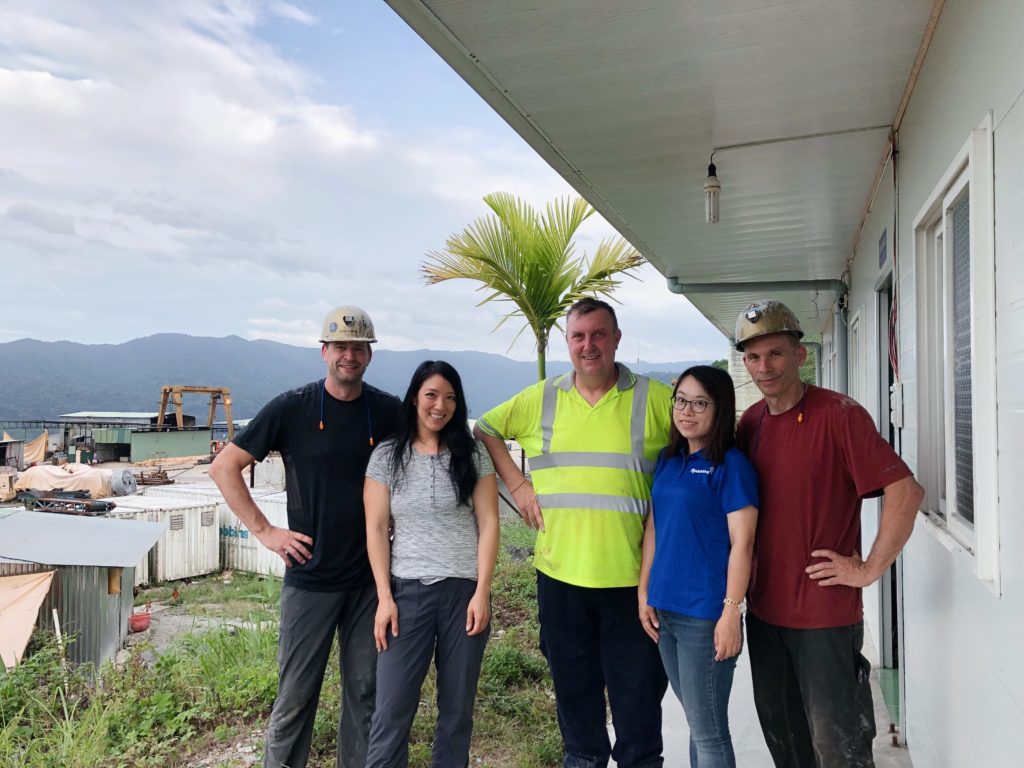
(From left): Ron (videographer), me, Greg Adams (Field Service Manager), Keri Lin (Marketing Manager for Robbins China), and Ken (Photographer) at the end of the shoot.