Year: 2011
There are Urgent Projects…and Then There’s Emisor Oriente
After visiting Mexico City’s Emisor Oriente Wastewater Tunnel, I realized something: there are urgent projects, and then there are URGENT PROJECTS. Túnel Emisor Oriente, often abbreviated to TEO by those involved, is the latter. We visited the site in 2011 to see the assembly of an EPB and learn about why the project is so important.
Day 1
On a good day with light traffic, the jobsite is about an hour’s drive away from the Distrito Federal, the downtown zone of Mexico’s capital city. Our first day, I noticed how the high rise buildings and restaurants slowly dissolved into ramshackle huts as we drove further from the city to an area known as Ecatepec. Approaching the site, we crossed a bridge in our SUV that spanned an extremely slow moving grayish brown river (more about this soon).
It was a warm day in June, Mexico’s rainy season, which is quite different from the rain in my home town of Seattle in the U.S. Each day during the rainy season, the morning dawns sunny and warm–but by 4:00 in the afternoon a torrential downpour begins. The water floods city streets throughout Mexico City, whose storm drains can’t handle the sudden inundation. Sometimes the rain only lasts a few minutes, and sometimes it goes for longer. The water eventually runs into rivers like the one we crossed by the jobsite, creating flooding risks.
We exited our SUV at the Lot 1 shaft and were greeted by several Robbins Field Service guys, including our Field Service Manager for the Americas, Jeremy Pinkham. I was excited to learn more about the TEO project, where we have three EPB machines among six TBMs that are excavating an epic 62 km (39 mi) long wastewater tunnel. The tunnel will feed into the country’s largest water treatment plant, which is currently being built.
As Jeremy and the group walked towards the shaft to be lowered down the elevator, I was struck by a smell—something akin to a vast field of poorly maintained port-a-potties. I asked Jeremy about the Robbins machine, which was originally intended for Lot 5 but had been fast tracked to bore part of the tunnel section at Lot 1. I was wondering why this particular section had been deemed top priority. “Did you see that river just a few meters away from our jobsite?” he asked. “Most rivers, when you throw a stone in, it splashes or skips and then sinks. This one, you throw a stone in and it just goes ‘plop’, then sits there.” It was only then that I realized that this “river” was El Gran Canal, Mexico City’s infamous open sewer originally commissioned in 1910 by President Porfirio Díaz.
The Robbins guys as well as engineers from the Lot 1 contractor Ingenieros Civiles Asociados (ICA) then explained to me that the canal in this section, lined with shacks, was prone to flooding during each rainy season due to a loss of its slope. The effects on the people and infrastructure were severe, so the National Water Commission (CONAGUA) had fast-tracked Lot 1. A pumping station would be put in and the first section of tunnel sealed off so that wastewater from this area could be pumped into a section of the canal downstream that still maintained its negative slope. I was beginning to realize the importance and urgency of this project!
The guys gave us a tour of the TBM being assembled at the bottom of the shaft, which was specially designed for high pressure conditions under the water table.
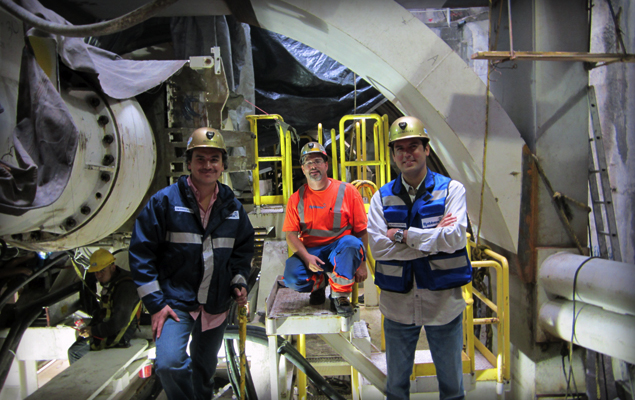
Robbins employees on the Lot 1 EPB. From left to right: Andrei Olivares, Robbins Project Engineer; Jeremy Pinkham, Field Service Manager – The Americas; Roberto Gonzalez, General Manager, Robbins Mexico
On the ride home that day we were hit by a particularly nasty rainstorm that went on for several hours. I learned via the local news later on that the very roads we had driven on to get to the jobsite were now flooded with wastewater and impassable—apparently a regular yet extremely concerning event.
Day 2
The next day we went to CONAGUA’s offices to speak with José Miguel Guevara, General Supply Coordinator for Potable Water and Sanitation. He spoke with us about the massive scope of Emisor Oriente—a project that could improve the lives of over 20 million people in the area by increasing wastewater capacity by 20% during each rainy season. The new pipeline will bolster current wastewater lines (both El Gran Canal and Emisor Central—a pipeline built in 1964) that have lost their slope due to Mexico City’s sinking lake clays.
While Guevara was optimistic, he admitted that health problems caused by El Gran Canal were numerous for the people living on its banks. When asked about future plans, he expressed grave concern that funds were not currently sufficient for a covered option to the open waterway. “At this moment,” said Guevara, “The Valley of Mexico is vulnerable. Our new treatment plant will treat 60% of the area’s water, but we need more alternatives as well. We are working on pieces to the problem, but the problem is not solved yet.”
With Emisor Oriente scheduled to be complete in 2014, I am hopeful that at least some of those problems will be alleviated. This is a great example of the magnitude that civil engineering works have on societies. I for one am proud that Robbins has a part in this monumental solution to an age old problem.After visiting Mexico City’s Emisor Oriente Wastewater Tunnel, I realized something: there are urgent projects, and then there are URGENT PROJECTS. Túnel Emisor Oriente, often abbreviated to TEO by those involved, is the latter.
Day 1
On a good day with light traffic, the jobsite is about an hour’s drive away from the Distrito Federal, the downtown zone of Mexico’s capital city. Our first day, I noticed how the high rise buildings and restaurants slowly dissolved into ramshackle huts as we drove further from the city to an area known as Ecatepec. Approaching the site, we crossed a bridge in our SUV that spanned an extremely slow moving grayish brown river (more about this soon).
It was a warm day in June, Mexico’s rainy season, which is quite different from the rain in my home town of Seattle in the U.S. Each day during the rainy season, the morning dawns sunny and warm–but by 4:00 in the afternoon a torrential downpour begins. The water floods city streets throughout Mexico City, whose storm drains can’t handle the sudden inundation. Sometimes the rain only lasts a few minutes, and sometimes it goes for longer. The water eventually runs into rivers like the one we crossed by the jobsite, creating flooding risks.
We exited our SUV at the Lot 1 shaft and were greeted by several Robbins Field Service guys, including our Field Service Manager for the Americas, Jeremy Pinkham. I was excited to learn more about the TEO project, where we have three EPB machines among six TBMs that are excavating an epic 62 km (39 mi) long wastewater tunnel. The tunnel will feed into the country’s largest water treatment plant, which is currently being built.
As Jeremy and the group walked towards the shaft to be lowered down the elevator, I was struck by a smell—something akin to a vast field of poorly maintained port-a-potties. I asked Jeremy about the Robbins machine, which was originally intended for Lot 5 but had been fast tracked to bore part of the tunnel section at Lot 1. I was wondering why this particular section had been deemed top priority. “Did you see that river just a few meters away from our jobsite?” he asked. “Most rivers, when you throw a stone in, it splashes or skips and then sinks. This one, you throw a stone in and it just goes ‘plop’, then sits there.” It was only then that I realized that this “river” was El Gran Canal, Mexico City’s infamous open sewer originally commissioned in 1910 by President Porfirio Díaz.
The Robbins guys as well as engineers from the Lot 1 contractor Ingenieros Civiles Asociados (ICA) then explained to me that the canal in this section, lined with shacks, was prone to flooding during each rainy season due to a loss of its slope. The effects on the people and infrastructure were severe, so the National Water Commission (CONAGUA) had fast-tracked Lot 1. A pumping station would be put in and the first section of tunnel sealed off so that wastewater from this area could be pumped into a section of the canal downstream that still maintained its negative slope. I was beginning to realize the importance and urgency of this project!
The guys gave us a tour of the TBM being assembled at the bottom of the shaft, which was specially designed for high pressure conditions under the water table.
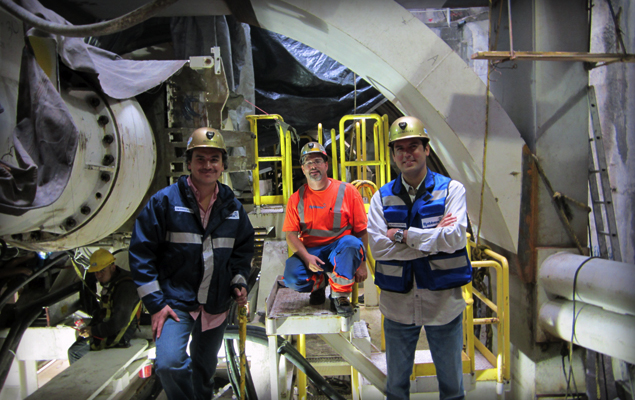
Robbins employees on the Lot 1 EPB. From left to right: Andrei Olivares, Robbins Project Engineer; Jeremy Pinkham, Field Service Manager – The Americas; Roberto Gonzalez, General Manager, Robbins Mexico
On the ride home that day we were hit by a particularly nasty rainstorm that went on for several hours. I learned via the local news later on that the very roads we had driven on to get to the jobsite were now flooded with wastewater and impassable—apparently a regular yet extremely concerning event.
Day 2
The next day we went to CONAGUA’s offices to speak with José Miguel Guevara, General Supply Coordinator for Potable Water and Sanitation. He spoke with us about the massive scope of Emisor Oriente—a project that could improve the lives of over 20 million people in the area by increasing wastewater capacity by 20% during each rainy season. The new pipeline will bolster current wastewater lines (both El Gran Canal and Emisor Central—a pipeline built in 1964) that have lost their slope due to Mexico City’s sinking lake clays.
While Guevara was optimistic, he admitted that health problems caused by El Gran Canal were numerous for the people living on its banks. When asked about future plans, he expressed grave concern that funds were not currently sufficient for a covered option to the open waterway. “At this moment,” said Guevara, “The Valley of Mexico is vulnerable. Our new treatment plant will treat 60% of the area’s water, but we need more alternatives as well. We are working on pieces to the problem, but the problem is not solved yet.”
With Emisor Oriente scheduled to be complete in 2014, I am hopeful that at least some of those problems will be alleviated. This is a great example of the magnitude that civil engineering works have on societies. I for one am proud to have a part in discussing this monumental solution to an age old problem.
Research and Development: A Sneak Peek at the Next Generation of Disc Cutters
R & D is important in any industry, and it is no less true for the tunneling industry. Evolution, even if it is incremental, is where most research and development successes are made. Such improvement forms part of the competitiveness among manufacturers and thus begets further improvements. I also believe it is our obligation, as equipment manufacturers, to assist the market in driving down the costs of tunneling in general by improved product performance and product life.
Take, for example the research and development going on with our disc cutters: Robbins disc cutters have improved dramatically since the 1950s when they achieved their first success at 11 inches in diameter in crystalline limestone of 190 MPa (28,000 psi) UCS. Today’s disc cutters do reach 20 inches in diameter and cost-effectively excavate rock strengths of 400 MPa (60,000 psi) UCS, all while lasting much longer than their predecessors.
That being said, we believe there is always room for improvement. We are working hard right now to develop customized cutters for EPB tunneling in soft and mixed ground, and to optimize those designs so they can excavate under high pressure. In hard rock, we are researching and testing new steels, and developing monitoring systems to allow contractors to plan cutter changes.
Here’s a snapshot of what research and development is going on in the cutter department, both in the lab and in the field:
Improved Metallurgy
Working with the University of Trondheim and the Norwegian government, we are commencing a program of laboratory and field testing to improve the materials making up the disc ring itself. We are always testing new materials in order to find the most durable materials based on the ground conditions. An example of past cutter research in the lab can be seen below:
Pressure Compensated Disc Cutters
We are currently developing improved disc cutters specifically for use on EPB and Slurry TBMs at high pressures of plus 10 bars, using a testing module in our Kent, Washington facility. The module duplicates a pressurized operational environment so that we can analyze how the cutter seals perform under pressure—the design is in its 3rd or 4th generation with continuous improvements being made.
Remote Cutter Monitoring
Our remote cutter monitoring system is a breakthrough that we have been field testing for four years. The system is now undergoing full scale testing on three Main Beam TBMs at Malaysia’s Pahang Selangor Raw Water Tunnel. The setup allows crews to more closely monitor the actual working conditions and cutter wear. We project, through this system, to increase the TBM utilization of each machine by 3 to 4% and to reduce cutter cost by 10%.
We’re also working on expanding this wireless system to EPB and Slurry machines, so that monitoring of cutter wear and rotation can be used while those machines are in closed mode. This would be a highly beneficial development, because under pressure the detection of tool wear is difficult. Our goal here is to reduce or better plan interventions because of tool wear.
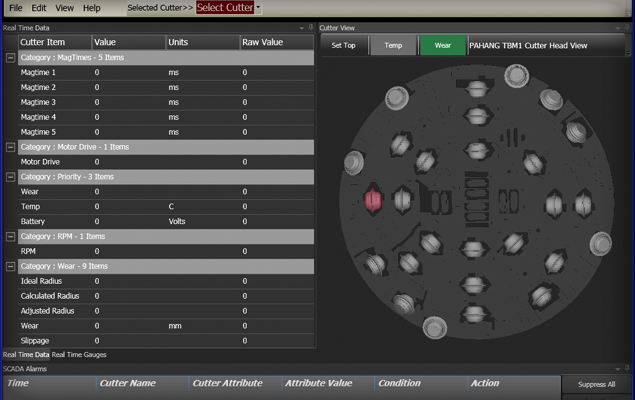
Sample screenshot of the Robbins remote cutter monitoring systems. Failed cutters are highlighted by a color on the screen.
Robbins Atmospheric Cutter Change System (RACCS)
Finally, we are developing a system to allow cutter changes at atmospheric pressure on large diameter EPBs. This atmospheric cutter change system is superior to other systems on the market because it allows muck to flow through. Other systems on the market are very prone to clogging. Each spoke of an EPB cutterhead will contain a chamber at atmospheric pressure. Cutters can be rotated from the pressure zone into the chamber to allow for efficient and relatively fast cutter changes.
The development is also significant because a huge cost of operating large diameter EPBs is associated with intervention for cutter inspection and change. We are currently building a large test fixture for this system, which will analyze how RACCS reacts in sand, gravel, boulders, clay, and mud conditions under pressure.
Conclusions
These research and development projects are all aimed at solving a particular problem or shortfall—with the objective to bore more meters per month. It is not the only area where we have research and development underway, as we have similar programs to investigate improvements of the probe drilling and lube systems on our TBMs. The process is usually rigorous, as designs need to be tested and re-tested in both the lab and the field.
I am not a big believer in “Big Step” research and development as was tried in earlier days at Robbins with the Mobile Miner and the Bore Pack. Such “Big Step” research and development usually leads to disappointment and heavy cost for the client and the company.
However, improvements like the 19” cutters and the cutter monitoring systems are and will be big wins for the contractors and for Robbins.
R & D is important in any industry, and it is no less true for the tunneling industry. Evolution, even if it is incremental, is where most research and development successes are made. Such improvement forms part of the competitiveness among manufacturers and thus begets further improvements. I also believe it is our obligation, as equipment manufacturers, to assist the market in driving down the costs of tunneling in general by improved product performance and product life.
Take, for example the research and development going on with our disc cutters: Robbins disc cutters have improved dramatically since the 1950s when they achieved their first success at 11 inches in diameter in crystalline limestone of 190 MPa (28,000 psi) UCS. Today’s disc cutters do reach 20 inches in diameter and cost-effectively excavate rock strengths of 400 MPa (60,000 psi) UCS, all while lasting much longer than their predecessors.
[Photo of a disc cutter]
That being said, we believe there is always room for improvement. We are working hard right now to develop customized cutters for EPB tunneling in soft and mixed ground, and to optimize those designs so they can excavate under high pressure. In hard rock, we are researching and testing new steels, and developing monitoring systems to allow contractors to plan cutter changes.
Here’s a snapshot of what research and development is going on in the cutter department, both in the lab and in the field:
Improved Metallurgy
Working with the University of Trondheim and the Norwegian government, we are commencing a program of laboratory and field testing to improve the materials making up the disc ring itself. We are always testing new materials in order to find the most durable materials based on the ground conditions. An example of past cutter research in the lab can be seen below:
Pressure Compensated Disc Cutters
We are currently developing improved disc cutters specifically for use on EPB and Slurry TBMs at high pressures of plus 10 bars, using a testing module in our Kent, Washington facility. The module duplicates a pressurized operational environment so that we can analyze how the cutter seals perform under pressure—the design is in its 3rd or 4th generation with continuous improvements being made. [Photo of testing facility?]
Remote Cutter Monitoring
Our remote cutter monitoring system is a breakthrough that we have been field testing for four years. The system is now undergoing full scale testing on three Main Beam TBMs at Malaysia’s Pahang Selangor Raw Water Tunnel. The setup allows crews to more closely monitor the actual working conditions and cutter wear. We project, through this system, to increase the TBM utilization of each machine by 3 to 4% and to reduce cutter cost by 10%.
We’re also working on expanding this wireless system to EPB and Slurry machines, so that monitoring of cutter wear and rotation can be used while those machines are in closed mode. This would be a highly beneficial development, because under pressure the detection of tool wear is difficult. Our goal here is to reduce or better plan interventions because of tool wear.
[Show screen shot of monitoring system]
Robbins Atmospheric Cutter Change System (RACCS)
Finally, we are developing a system to allow cutter changes at atmospheric pressure on large diameter EPBs. This atmospheric cutter change system is superior to other systems on the market because it allows muck to flow through. Other systems on the market are very prone to clogging. Each spoke of an EPB cutterhead will contain a chamber at atmospheric pressure. Cutters can be rotated from the pressure zone into the chamber to allow for efficient and relatively fast cutter changes.
The development is also significant because a huge cost of operating large diameter EPBs is associated with intervention for cutter inspection and change. We are currently building a large test fixture for this system, which will analyze how RACCS reacts in sand, gravel, boulders, clay, and mud conditions under pressure.
Conclusions
These research and development projects are all aimed at solving a particular problem or shortfall—with the objective to bore more meters per month. It is not the only area where we have research and development underway, as we have similar programs to investigate improvements of the probe drilling and lube systems on our TBMs. The process is usually rigorous, as designs need to be tested and re-tested in both the lab and the field.
I am not a big believer in “Big Step” research and development as was tried in earlier days at Robbins with the Mobile Miner and the Bore Pack. Such “Big Step” research and development usually leads to disappointment and heavy cost for the client and the company.
However, improvements like the 19” cutters and the cutter monitoring systems are and will be big wins for the contractors and for Robbins.
Adventure at West Qinling:Treacherous Roads, Spicy Food, and TBMs
A few months ago one of my colleagues and yours truly presented a two day seminar to the Dongah Geological Company of South Korea on Robbins Hard Rock TBMs. The following is our story of the ensuing trip: Fueled by copious amounts of South Korean hospitality known as Soju (for those of you who don’t know Soju or Shōchū is a Japanese distilled beverage. It is usually distilled from barley, sweet potatoes, or rice. Typically, shōchū contains 25% alcohol by volume. It’s weaker than whiskey or standard-strength vodka but stronger than wine and sake. It does actually taste like weak vodka, at least the first one or two do, after that…well you should get the picture!) our agent Mr. Kim in South Korea suggested that we should further develop our relationship with our hosts and provide some on-site practical training for our hosts.
We needed to find a project that would be similar to the potential project in South Korea–similar meaning, similar in purpose, design and diameter. The machines in South Korea we learned could be up to 12m in diameter and possibly larger. Someone, I am not sure who, volunteered the West Qinling project in Gansu Province, China as the project most similar to the ones in South Korea.
Robbins currently has two 10m diameter hard rock main beam type machines in operation there. With the Soju in full effect we all thought this was a great idea and it was decided that West Qinling would be our next port of call. (For more on this project, view our news release and case study).
After a day or two of recovery and not expecting to hear anything more (Soju has that affect on you) there followed a flurry of E-mails, a few phone calls and before you knew it we had arranged a trip to the West Qinling project.
Gansu province is located in the northwest of the People’s Republic of China. It lies between the Tibetan and Huangtu plateaus. The landscape in Gansu is very mountainous in the South and flat in the North. The mountains in the South are part of the Qilian mountain range. At 5,547 meters high, Qilian Shan Mountain is Gansu’s highest elevation. The West Qinling Project is located in the mountainous region to the South. Similar to the great expedition in 1845, it’s only about 500km (310miles) from Chengdu to the jobsite.
I have been to the West Qinling site before; there is no way to get there other than by a four wheel drive vehicle. You have to drive; the nearest airport was severely damaged by the deadly 7.8 earthquake in the region in 2008. On a good day the drive could take 8 hours. Generally it takes at least 10 hours. On my first trip it took over 13 hours. If it rains you can expect landslides and mudslides, it has taken some field service personnel nearly two days to get off the mountain and back to Chengdu. In a weak attempt to dissuade Mr. Kim from actually going ahead with the visit to the jobsite, we tried to paint as black a picture of the journey as we could. No matter what we told him he always replied “Guk-jung-ha-jee-ma!” which in Korean literally means “No worries!” or “Don’t worry!” To which we replied, “But Mr. Kim are you aware that this is the rainy season?” And to that we got the same answer “Guk-jung-ha-jee-ma!”
After meeting and greeting our party of seven guests, accompanied by Mr. Kim from South Korea, at Chengdu Airport on the evening of 12th May we held a briefing on the same evening about the journey and the schedule for the days ahead. Arrangements were made to meet in the hotel lobby the next morning. “Any questions?” I asked. “Guk-jung-ha-jee-ma!” was the now familiar reply.
8am Friday 13th May:
I thought I wasn’t superstitious, but setting off on Friday 13th on a 10-hour journey in the rain to a remote jobsite in the mountains gets you thinking a little. So with Mike (our field service training supervisor), Andy (the Robbins China project manager for the project) and myself in the lead vehicle we set off in convoy, 4 vehicles in total, for West Qinling. Four hours into the journey and lunchtime is approaching. As some of you will be aware meal times are sacred in China–the drivers are getting short tempered and need to stop. We’re driving through Sichuan province and we’re close to the last major town before we hit the mountains and dirt roads.
The majority of food in Sichuan is spicy. The locals love nothing more than Chilies of any and all kinds with their food. We stop at a local restaurant in Baolun, (this is one of the small number of places where you will see few, if any, American style fast food joints, a rarity in itself these days). Andy orders food and leaves instructions ‘not too spicy’ with our smiling waitress. It seems as though something got lost in translation and most of the food is spicy. There are a few newcomers in our group to this part of China and the last thing you need on a long road trip into the mountains is to be looking for restrooms. Even some of the more experienced travelers have been known to get caught out once or twice (myself included).
In the more remote parts of non-Westernized countries or parts of countries that have had limited exposure to Westerners or “lao wai” (foreigners in China) you shouldn’t expect Western style facilities either; a hole in the floor type convenience would be the norm…if you’re lucky.
We set off again after lunch, the first few hours are on black top. Although the road is winding up and over the first mountain range it’s a relatively smooth ride and the views are spectacular. We enter Gansu province around 3:30pm in the afternoon.
Relative to the food we’ve eaten and the roads we’re traveling on, the condition of the digestive system is, in weather related terms, (refer to the Beaufort Scale) around Force 7: ‘High Wind, moderate gale, near gale.’”
Again for those of you who don’t know, The Beaufort Scale (pronounced bou–fart, need I say more) is an empirical measure for describing wind speed based mainly on observed sea conditions (on land it is categorized by the physical effects it has on vegetation and structures). Its full name is the Beaufort Wind Force Scale.
Not long after we’re on the dirt roads, top speed is roughly 20km/h (12mph) about an hour in we stop at a small village, where wind speed for some of the group has increased to force 8 (gale, fresh gale), and all of our guests need a pit stop. We find a ‘restroom’ in a small village, the wind dies down and we set off again.
We pass through an area that has just been cleared of a landslide (see photo below), which had closed the road for 2 days prior to us travelling. If the landslide had not been cleared we would have had a four hour 150km detour to endure.
Unexpectedly the wind starts to increase again, Mike is feeling it the worst, without warning we (he) experiences Force 11 (Violent storm) – we need to stop immediately!
Luckily we’re not far off another camp about 2 hours from our destination. We pull in and Mike calms the storm. There’s a lot of curiosity when we arrive at this camp. It’s not often you see four vehicles in convoy travelling these roads. Add to this the fact that we’re all ‘lao wai’ and pretty soon we’re surrounded by curious onlookers. A bit of ‘Chinglish’ (Chinese English) with the crowd, they hand out cigarettes to those who want them, we have a laugh and joke (‘laugh and joke’ by the way is cockney rhyming slang (slang mainly used in London in the UK) for ‘smoke’, and head on up the mountain.
We arrive at the camp at around 6:30pm, where we’re greeted by our host from MOR18, Mr Wang. Everyone is shown to their rooms. We throw the bags in, wash up and head for a welcome dinner. We’re all weary after the long journey, a few beers take the edge off and the expedition team starts to relax.
Saturday May 14th:
First day of training, we split up into two groups. Mike takes a group for some classroom study, Andy & I with the other group head into the tunnel. First of all we explain some general rules on safety and what to watch out for when we’re in the tunnel. “Any questions?” – same answer: “Guk-jung-ha-jee-ma!”
When we were on site the previous year we were there to assemble, test and commission the machines. Due to bad ground at the start of the tunnel we had to walk the machines some 2.5km from the portal to the starting point of the bored tunnel. Since then the machine we’re visiting has advanced another 4.5km. Average production on the machines is close to 500m per month. Considering the location and the logistical nightmare that this project is, this is an excellent achievement. By anyone’s standards 500m per month on a 10m main beam machine is good going.
These tunnels form part of a massive project that will eventually cut rail transportation times between two major cities in the region from 12 hours to roughly 4 hours.
It takes us an hour on the loco to get to the machine, along the way we see several slip forms that are used by the contractor to complete the final lining of the tunnel. There are two rail tracks all the way to the back of the machine. There are currently nine rail switches at roughly 500m distance throughout the tunnel, and we constantly switch from the left line to the right line as we progress towards the machine to prevent any hold ups to the works.
On this project excavation, preliminary ground support consisting of rock bolts, mesh, ring beams and shotcrete is done at the machine and the final lining using the slip forms is carried out simultaneously in both tunnels. The excavated material is transported out of the tunnel on a continuous conveyor also supplied and installed by us.
We spend the whole morning on the machine and our guests get to see a lot of activities being carried out, ask a lot of good questions and get a good feel for hard rock tunnel boring. We manage to get into the cutterhead and witness a cutter inspection. For most of our guests it is the first time they have seen a hard rock boring machine in action. In South Korea tunnels in hard rock have typically been excavated by drill and blast methods and metro tunnels have been excavated by EPB machines. I think everyone is taken aback by the sheer size of the machine, the heat and noise and the amount of activities being carried out in the tunnel.
We see first-hand the machine boring whilst the crew installs ring beams and mesh and drill for rock bolts. Behind us in the L2 zone shotcreting is ongoing.
Around 1pm we’re out of the tunnel. After a light lunch Mike and I swap teams and once again we head back into the machine with the second group. More questions, more explanations and all in all a productive educational day.
We have two machines on this project that are boring parallel tunnels, we’ve been on the left side machine all day, due to the way the project is organized this is actually the right line machine. This machine is operated by MOR18, our other machine is operated by CRTG. We think it only proper that we visit both machines. Two different contractors, two different ways of working, it’s good for our guests to see & understand that there are many different ways to approach this kind of work.
Saturday evening we get invited to dinner by CRTG, Mr. Dai is our host and knows how to throw a good reception. The food is excellent: Mike and myself demolish a large plate of bull frogs (tastes and looks just like Chicken) our guests however don’t seem too fond of them. They are washed down with Mr. Dai’s special Baijiu. Baijiu is almost the Chinese version of Korean Soju but around 50% stronger. Literally translated Baijiu means ‘white liquor’. For the most part Baijiu is an acquired taste; it kind of percolates out of you for around 3 days after you’ve been drinking it. Mr Dai has a special Baijiu that contains herbs and spices that make it good for the health, or so they say (and who am I to argue). I don’t want to upset our host and join with him in several toasts to the health of our guests — there’s no need for translation this evening. Baijiu is a wonderful translation tool — it’s funny how we can all understand each other so well. Our guests reciprocate with several toasts of their own, we sleep well that night!
Sunday May 15th:
Sunday morning is spent looking around the jobsites as a group. We visit the segment plant (all segments are fabricated on site), the ring beam plant, the wire mesh plant, the cutter workshop and the three batching plants. Three batching plants are needed as the invert segments, the shotcrete and the final lining concrete all require different quantities of sand, cement and aggregates for each application.
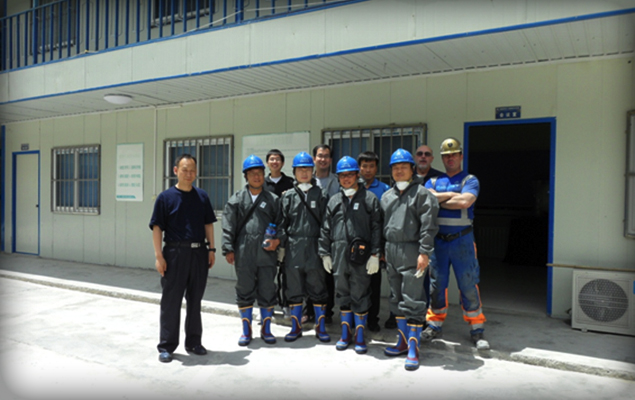
The Expedition team at the MOR18 Camp. (Mr. Kim, our Robbins Korea Agent on the LHS of the picture, Mike (back row) and myself on the right in the Hi-Vis workwear)
We take a look at the continuous conveyor installations and explain to our guests how it all works and ties in with the boring machine.
Sunday afternoon we visit the right side machine (left line), as they have just come off an 800m plus month. We think it’s a record for this size of machine, an outstanding performance.
Later on in the day we’re invited to a question and answer session by the contractors. Our guests get a lot of useful information from them as do we.
We get a weather report for the next few days, not so good, rain is forecast. We need to change plans and decide to make a run for it down the mountain before the rains start. Sunday evening we attend another excellent dinner, this time hosted by Mr. Wang of MOR18. Once again the Baijiu replaces our translators and we communicate in a common language. We need to be cautious though; wind is also forecast for the next morning especially after a large dinner. We don’t need a repeat of our inbound journey!
Monday May 16th
We cannot thank our hosts enough for their hospitality; we have been welcomed with open arms, a great experience for our guests. We set off down the mountain at 7am. Winds are Force 0 – Calm!!
Around 6pm we’re back in Chengdu. A bit of rest and recuperation is in order—a couple of hectic days & hard nights takes its toll on you.
Tuesday May 17th
We pay a visit to one of the workshops in Chengdu. We are currently assembling the 2nd machine for the Chengdu metro project there. It’s an EPB machine and is nearly completely assembled. The shop is impressive and our guests are very interested in the unit. They have a lot of experience with EPB machines and ask a lot of pertinent questions.
Later that morning we stop off at the jobsite and see the sister machine in the workshop being assembled in the pit at site. Most of the back-up is completed, the middle shield is standing up and the site crew are preparing for the arrival of the forward and tail shields.
Monday afternoon is spent taking in all the information from the visit. We have a final question and answer session with our guests and arrange a farewell dinner.
Wednesday morning 5:30am, we put our guests on the bus for the airport. We made it back from the mountains safely and the expedition is over. Mike gets on a plane for the US, Andy flies back to Shanghai; I jump on the high speed train from Chengdu to Chongqing, we have two hard rock single shield machines to build there. The first is about a month away from completion…back to reality, we’re on a tight schedule and there’s work to be done. All of a sudden I get the familiar feeling of a Force 11 (violent storm) coming on, must be something I ate at the farewell dinner. Luckily I’m on the train, there is a decent restroom and the storm is over before we know it. Winds return to Force 0 – Calm!
The Oldest Robbins TBM still in Action? We visit a jobsite in Canada that may be using the World’s Ultimate Workhorse TBM
It’s a long-standing question in the world of tunneling: Which TBM has been operating the longest? What makes it so durable?
In May 2011, I visited the site of the Centennial Parkway Sanitary Sewer Tunnel in Hamilton, Ontario, Canada to find some answers. The rock portion of the tunnel, located in the shale of the Niagara Escarpment, is being bored by a Robbins Main Beam TBM in operation since 1968. The 2.7 m (8.8 ft) diameter machine was first used for a Hydroelectric Tunnel in Tasmania, and is now owned by McNally Construction, who has used it on multiple sewer tunnels in Toronto and Ottawa since 1972.
I arrived at the Centennial Parkway site on a sunny Friday afternoon along with Tunnels & Tunnelling North America editor Nicole Robinson, where we were greeted by McNally Project Sponsor Dave Bax and Field Technician Kenny Baxter.
After giving us some safety instructions, we were handed full rubber suits and boots. “You’re going to need these,” said Kenny. “It’s muddy on the shaft floor, and the material is red. It gets everywhere.” A quick look around the jobsite confirmed his statement—red clay-like material caked nearly everything, from trailers to trucks to boots.
We climbed down a long ladder into the shaft, and were given a tour of the small diameter tunnel. Kenny explained that the ring beams and wooden lagging installed at the tunnel entrance were due to the softer clay material encountered at that point. The rest of the rock portion of tunnel was being supported with rock bolts and steel straps. “The shale material is being recycled to use as brick. The clay was used by a local gun club for berms on their grounds.”
Single track muck cars rolled out as we walked out of the tunnel, carrying more heaps of reddish shale, before they were lifted by a crane and dumped on the surface.
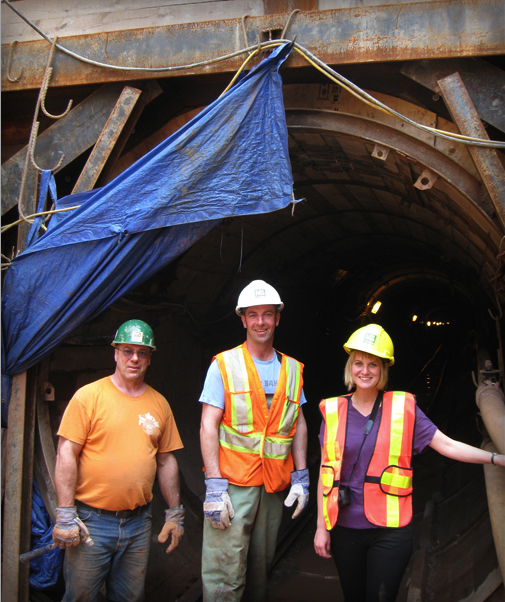
From left to right: Mark Walker, Laborer; Kenny Baxter, Field Technician; Nicole Robinson, T&T N. America, at the tunnel entrance.
Bax and Kenny mentioned that daily maintenance shifts have helped keep the veteran machine in good working order. Crews regularly check the 12-inch (304 mm) diameter disc cutters, and inspect the cutterhead and critical sub-systems. “We are not expecting a lot of wear. Our estimated completion for this tunnel is about two months,” said Bax. At the time of our Centennial visit, the TBM had advanced 200 m, at 1.8 to 2.1 m (6.0 to 7.0 ft) per hour, with no major issues.
The competent shale rock is certainly also a factor in limiting wear to the machine’s cutterhead and main bearing. Robust core components, including the main beam and gripper system, are key in keeping a TBM running for a long time (43 years, in this case).
Overall, the machine looked to be well equipped for its latest tunnel drive, and though it is impossible to know if it’s the world’s oldest working Robbins machine, it is certainly on the list. If you know of a Robbins machine that’s been operating longer, drop us a line in the comments section. We’d be interested to hear about it, and maybe even visit it!
Robbins EPBs in Action: Chengdu Metro
Soft clay soil, an array of boulders, and sharp turns have each added an extra layer of difficulty on the Chengdu Metro Line 2 project. Custom-engineered with active articulation systems, the two Robbins 6.3m EPBs have been carving their paths at speeds up to 180 meters per week.
Hunting Mouse: A lighthearted look at field service communications
Being in Field Service can have some interesting moments, particularly when working overseas and in countries where the English language might not be the first language. We are a department of personnel drawn from all over the world, so we each have our own take on English and the way to speak it. Add to this workers who speak a local dialect, and even communicating with each other can be confusing or comical, to say the least. Read below for some lighthearted moments at field service projects around the world.
Sign Language
Field Service personnel often get by with sign language, drawings on the back of cigarette packets (a rarely used device these days as most of us have quit!) and by any means possible to get a point or question across. In some of the more frustrating conversations we resort to shouting the same question, as it would appear we think people can understand English by raising our voices.
On occasion we could be in a scene from a Monty Python Sketch–A reply to the question “Do we have no cutter wedges?” was met with a positive “yes” answer. “So where are they then?”, “We have none.” It’s all very confusing, but the way the question was asked prompted the answer, so “Yes, we have no cutter wedges,” would appear to be correct when taken literally. A few years ago one of our guys (no names mentioned) was trying to explain to the waitress that we wanted one of those fancy Italian Ice Creams for dessert. Imitating holding the ice cream and moving it to his mouth several times didn’t go down too well, with a somewhat embarrassed waitress as I recall, but it was all taken in good humor (we got the ice cream by the way).
Lost in Translation
When we try to get smart and speak the local language the results are even worse…or better depending on your outlook. In Spain while ordering lunch, Macaroni with Tomato Sauce (Maccarones con tomate) came out as ‘Maricones con tomate’, which turned out to be ‘Gays with Tomatoes’…that brought more than a few smiles to the table and a bewildered look to the waiter’s face. We still talk about it to this day.
During a lunchtime chat between three of our guys, two Americans and a Scottish guy, the topic of conversation came around to hunting. The two American guys mentioned that they had been hunting Moose somewhere in the USA a few years back and that they had needed special ammunition for the rifle. “Hunting Moose!” said the Scotsman in his strong dialect, with a confused look on his face, “Where I come from a Moose (dialect for a Mouse) is only 3 inches long!”
A few months ago we were working in China and came across this sign in Shanghai:
I did as instructed, went down the stairs, turned around and walked backwards… I couldn’t find the restroom or a Policeman??
So as you can see, communication in the field is important. There is no need to shout. Be humble and respectful, and think about the question and the way to ask it–whatever country or situation you’re in. Sometimes what you say or the sign language you use to get your message across can be misinterpreted, often with unexpected results.
As is often said: “When in Rome, do as the Romans do.” And a final word of advice…be careful of any sign language you use, especially when asking for ice cream, more so if you’re in Italy, you’d probably end up with a slap there!!