Category: The Future of Tunneling
The Changing Face of the Tunneling Industry: The Role of the ITA, Partnership, and Innovation
Martin Knights graduated with a degree in Civil Engineering in 1970 and joined the Second River Mersey Road tunnel project as a site engineer in Liverpool, UK as his first TBM project. The major feature of this 2.5 mile long twin tunnel project was the refurbished 35 ft diameter Robbins TBM, which had previously driven a number of water supply tunnels at the Mangla Dam in Pakistan. Knights worked in several consultancy firms on a number of high profile tunnelling projects over several decades, most recently as the Managing Director and Sr. Vice President for CH2M/Halcrow. He was also president of the International Tunnelling Association (ITA) from 2007-2010. He is currently an independent consultant with his own company, Martin Knights Consulting.
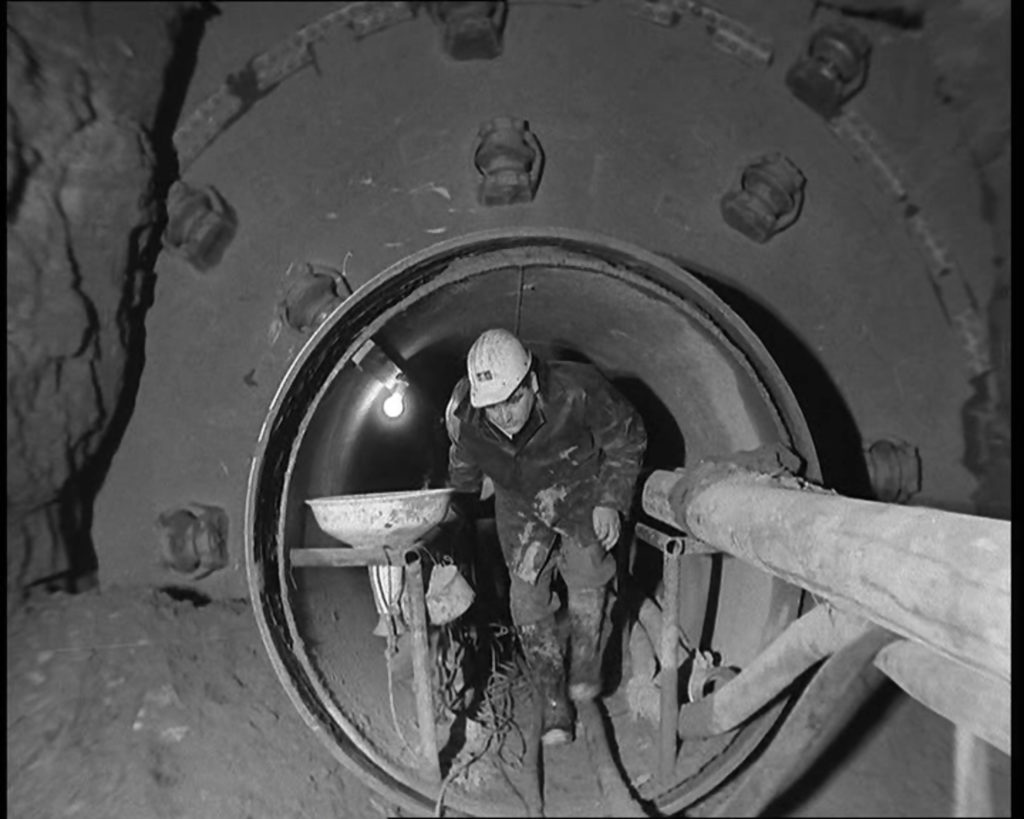
A worker exits the rebuilt Robbins TBM used on the Mersey Road Tunnel Project in the UK. The Second Mersey Road Tunnel was Knights’ first project after graduating in 1970. Image Credit: British Pathé
At the recent ITA Training Course in Bergen, Norway, which preceded the World Tunnel Congress, I gave a lecture about the development of Soft Ground TBMs from Victorian times until now. It took a bit of research: I trawled through reference books and talked to experts in the TBM world. During the research I looked at project specifications for big projects carried out in the past 40 or so years, and was struck by the level of technical detail and requirements that engineers stipulated in the contract documents: there seemed to be a tendency for over-specification that imprisoned the contractor and his equipment suppliers to past tried-and-tested practices. Where was the opportunity to innovate and trial new ideas by those best suited to introduce best and new practices?
That reminded me of Lok Home’s [Robbins president] challenge to me in November 2009 at the Hamburg, Germany STUVA Exhibition and Conference. Lok and l, and other colleagues in ITA and the tunnelling world, took part in an industry round table talk. I was President of ITA then and the two-hour discussion concluded with Lok asking me, “So, Martin, what can I and the industry do for ITA? We provide sponsorship to ITA, like other leading tunnelling companies; we fill the exhibition halls; we host social gatherings during ITA conferences, and we give lectures promoting new products. But we as equipment manufacturers and suppliers want to play a bigger technical role.”
Stung by the realisation that ITA had, by default, missed a trick, and was, in effect, excluding the very talent that provided innovation in tunnelling, I set about forming the then-new ITA technical forum ITAtech. I say “I”, but in fact myself, Lok, Tom Melbye of Normet, Felix Amberg of Amberg Engineering, and colleagues from Herrenknecht, Mapei, Atlas Copco, and others set out over three months to prepare the ground to launch ITAtech as a premier promoter within ITA of technology and innovation. Our purpose was to prepare independent and commonly-agreed technical guidelines and evidence endorsed by the whole international tunnelling industry, which is what ITAtech continues to do. It provides manufacturing, installation, equipment and materials guidelines for Contractors and Designers and creates confidence for tunnel owners that the “brand” of the ITA is overseeing this important knowledge transfer.
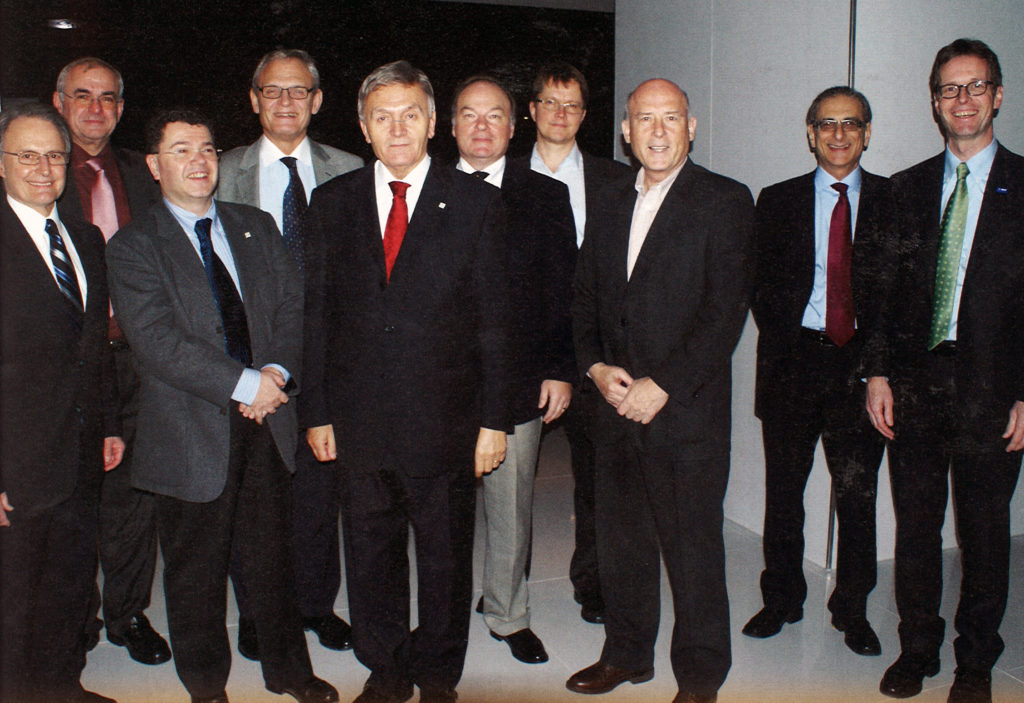
The initial 2009 meeting that led to the ITAtech forum. Left to right: Bill Hansmire, Gerhard Robeller, Olivier Vion, Gunnar Nord, Martin Knights, Brian Fulcher, Pekka Nieminen, Lok Home, David Caiden, Daniel Ruckstuhl
As I talked to the Bergen delegates this year, it was obvious to me that soft ground urban tunnelling owes a debt to the development of TBMs over the past 40 years…and particularly to the past 10 years. We can now do things that were too difficult to do way back then. It’s no coincidence that the innovations in the last 50 years were led by TBM companies like Robbins, Lovat, Seli, Herrenknecht, etc. The leadership and pioneering spirit could have only been driven by the individual passion that comes from a “family run” business. With time, growth and ownership has been passed on, but the stewardship and spirit of innovation in tunnelling lives on. ITAtech has tried to capture that spirit. Membership of its Steering Board and Activity groups relies on that desire of industry to educate, improve and share.
A recent President of the UK Institution of Civil Engineers compared our fragmented industry processes with the manufacturing, aircraft and car industry. In effect he said “Why–unlike those industries–do we separate inception, planning, and design from assembly, installation and construction?” The infrastructure and mining industries rely on so many processes and partnerships to deliver projects precisely because they are so fragmented and siloed.
Contemporary procurement encourages more partnerships, but this doesn’t make it any less convoluted. We see the rise of the dreaded words “industry supply chain” and “second and third tier partners”, where it strikes me that we’re airbrushing out the identity of the very “tier” of industry that has to innovate and provide the substance that nourishes the technical solutions that feature in new infrastructure developments.
I suggest that owners and clients get better access to and value from these innovating “tiers”—in many cases the equipment manufacturers and suppliers. In so many cases I have seen technical solutions get misinterpreted as ideas and solutions move up and down the so-called supply chain, begging for recognition, understanding and realisation of value.
I’m sure that this is not intended…but it happens. By validating and bringing innovations to the forefront through organizations like the ITAtech, we can improve some of the convoluted procurement and technical approval processes. However if we want to continue to see advancements like we’ve seen in urban soft ground tunnelling in recent decades, we should seek to streamline manufacturing and procurement, and to work closely with all “tiers” involved—second, third, and on up.
What’s New, What’s Next: TBM Equipment for the Mining Industry
TBMs have become well accepted in civil construction tunneling and excavate a high percentage of civil construction projects each year. But each year in the mining industry, far more kilometers of tunnels are excavated for mining purposes than for civil purposes. The amount of tunnels needed for mining operations is staggering.
Some examples from metal mines:
- A large, deep gold mine has over 800 km of tunnels. That is a single mine!
- One small underground metal mine excavates over 13 km of tunnel each year
- In the Sudbury, Ontario mining district, there are over 5000 km of mine tunnels
If tunnels for coal mining were included, the statistics would be even more dramatic. But all these tunnels hold a little-known secret.
The Lack of Mechanized Tunneling
How many of the above thousands of kilometers of mine tunnels do you think have been excavated by TBM? The answer is “Nada”. Compare that to the thousands of kilometers of civil construction tunnels built over the last decades, which required hundreds of TBMs. Why such a great disparity when the objective in both industries is to excavate underground openings as rapidly, economically, and as safely as possible? What are the differences in these industries?
In TBM civil construction, the TBM crew members that know how to make things happen underground, that know how to drive the machines, how to lift heavy components and repair the equipment, how to get the trains in and out to remove the muck and to bring in supplies, are known by a special name. They are known as the “miners”. Yet the only thing they are mining is the muck, no coal, no minerals. But “miners” is a term of reverence for someone who knows how to excavate a tunnel rapidly and efficiently. When a civil tunnel is progressing well, they say “now we’re mining”. (Well, sometimes they also say this sarcastically sometimes when things are going poorly underground.) Why aren’t such talented miners, who know how to make a TBM perform, using their TBMs to excavate thousands of kilometers of mine tunnels each year? What are the differences between civil tunneling and mine tunneling?
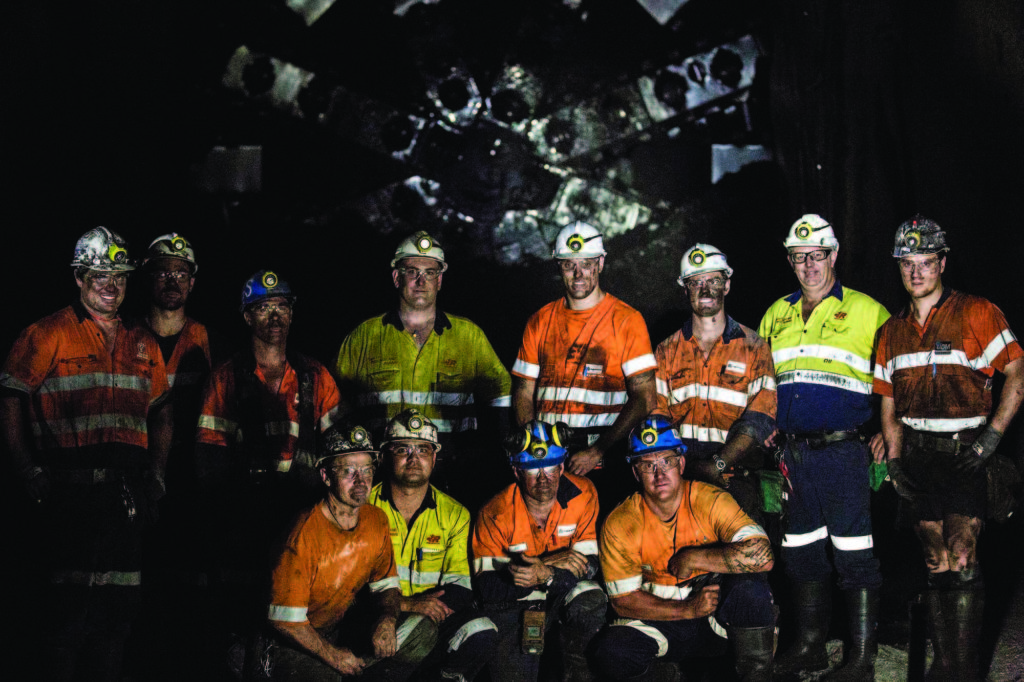
A group of talented miners at Australia’s Anglo American Coal Mine, where a Robbins Crossover TBM excavated two drifts for haulage and personnel access.
TBMs for Civil Tunnels
TBMs have become well accepted for civil tunneling. TBMs designs have become widely adapted for different ground conditions or specialized applications: Hard rock, soft ground, mixed face, pressurized face. Various types of ground support can be installed, according to current geological conditions. More current “hybrid” or “Crossover” TBM designs can handle widely different geological conditions, with the TBM adaptable to cope as conditions change.
Civil tunnels are generally long tunnels, where the efficiency of TBM excavation offsets the longer mobilization and demobilization times. And civil tunnels are generally designed with equipment mobilization/demobilization in mind. Suitable sized shafts are located to allow relatively simple introduction or retrieval of the TBM equipment. The most efficient type of TBM is the full face, rotary type TBM, which produces a circular tunnel profile. The circular profile is nearly universally accepted for civil construction. It is the optimum profile for fluid flow for fresh water, waste water, or hydro tunnels. It is also widely accepted for vehicular civil tunnels that need a flat roadbed. A flat roadway is constructed within the circular tunnel profile and the remainder of the profile within the circle is used for ventilation, services, escapeways, etc.
Some efforts have been made to develop non-circular profile TBMs for the civil sector. These machines include the Mini-Fullfacer, the Mobile Miner, and horseshoe shaped shields with excavator boom or roadheader. Such machines may produce a non-circular profile that is better for that specific job. But usually, there is a penalty in production rate compared to full face, circular TBMs.
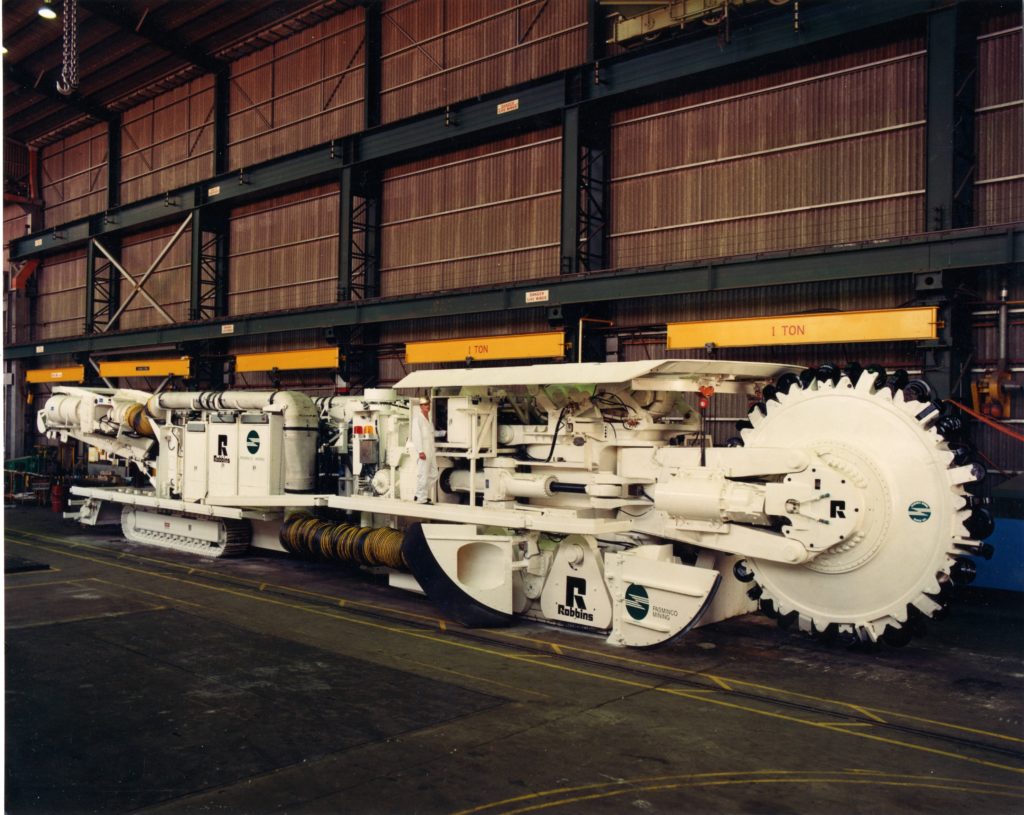
The mobile miner, a non-circular profile TBM developed by Robbins.
TBMs for Mine Tunnels
There have been some notable successes to the application of circular profile “civil type” TBMs for mining projects. Benefits have been lower costs, quicker access, and improved safety. Some examples include:
- Magma Copper, San Manuel Tunnels
- Stillwater Mines (four TBMs used)
- Grosvenor Coal Mine, Two Inclined Access Drifts to the coal seam
However, application of TBMs for mine tunnel construction has remained surprisingly limited. Why is this? Tunnels for mining are often not so long, or a developed in shorter phases, with the excavation front moved from place to place within the mine. TBMs and their constituent components are large and heavy. It is not easy to mobilize a TBM deep underground in a mine at a remote face. Better efforts must be made to make TBM transport and mobilization within the mine practical. This includes considerations for steep ramp roads and other restricted cross sections within the mine.
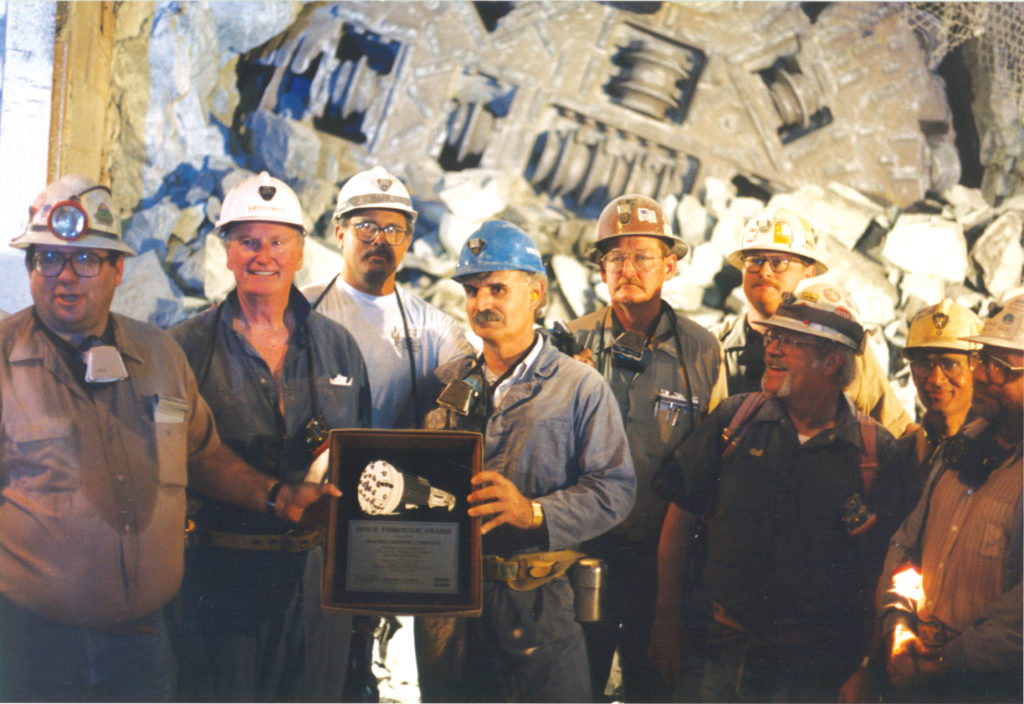
Breakthrough at the Magma Copper Mine in the 1990s.
Efficient TBMs are highly productive, but require a lot of power, ventilation, cooling, and support services. These need to be part of the mining plan so that the TBM has the necessary support and can provide the full benefit. Operating personnel with proper skills are also essential. If a TBM is introduced into a mining environment, either the mine personnel need proper TBM training or motivation, or the TBM drive must be isolated as a “stand alone” operation within the mine and be given proper priority of skilled personnel and the necessary services so the full benefit can be realized.
Mines often do not accept the circular profile produced by the most efficient, full face rotary TBMs. Mine tunnels are usually designed with a flat invert to allow for passage of rubber tired vehicles during the production phase of the mine tunnel. Many efforts have been made to provide TBM type equipment that produces a flat invert. Some have been relatively successful. But generally these machines do not provide the same productivity of efficient, full face circular profile TBMs. Rail bound mining vehicles can be used in the circular tunnel to take advantage of this TBM efficiency. Or, precast invert slabs, poured in place concrete, or partial invert filling can be used in a circular tunnel to provide a flat roadway. The cost/benefits must be analyzed and presented to the industry for a change to occur.
Mining plans often have tunnels with steep gradients and sharp radius curves. On steep gradients (up to 12-15 degrees), the most efficient haulage is usually by belt conveyor. However, the belt system is not effective if there are sharp radius curves. And typical TBM curve ability is limited. Special TBM designs can be made that allow for excavation in sharp curves, but there is a compromise in reduced TBM performance.
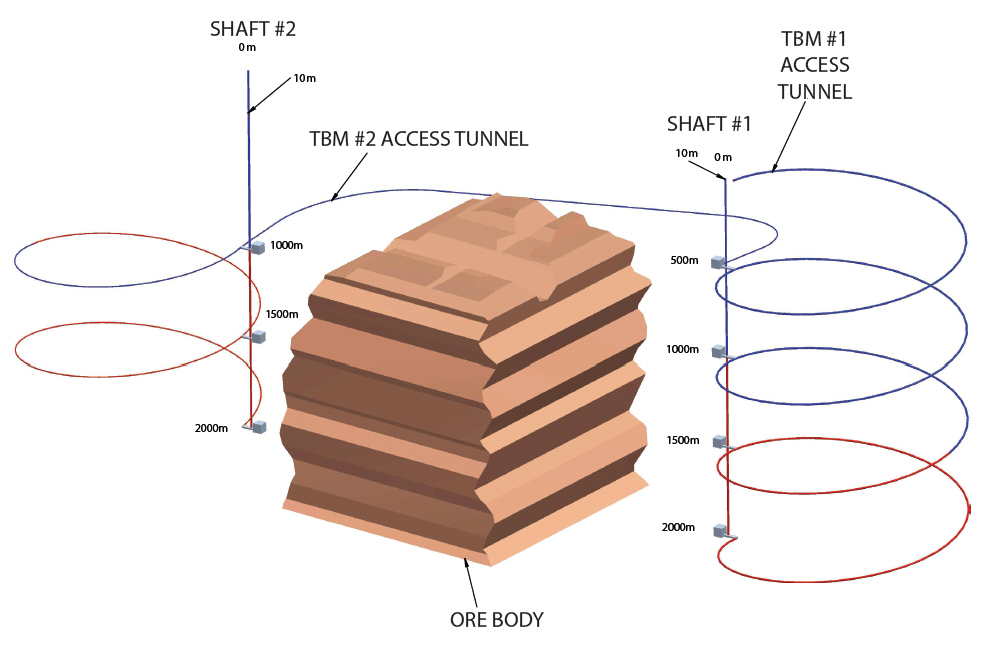
An example of a mine access and haulage plan to reach a deep ore body.
Mines need Versatile TBMs
It seems the mining industry needs the benefits that TBMs can provide. Open pit mines are becoming depleted, and mining activities are reaching deeper. Longer access tunnels are needed. Safety and speed of development are paramount. TBMs can offer these advantages, but have limitations. Special TBMs can be developed that meet special requirements, but usually there is a penalty in reduced TBM performance. The mine planners and the TBM equipment designers must work together at an early stage in the mine planning to determine the optimum compromise between most desirable mine plan, and most beneficial application of TBM equipment. A good partnering approach is necessary in the planning stage, as well as the operating stage, to allow for the most efficient application of TBM equipment to the needs of the mine.
By Dennis Ofiara, Chief Engineer
From Risk Aversion to Risk Reduction: How Elon Musk could usher in a New Era of Tunnel Boring
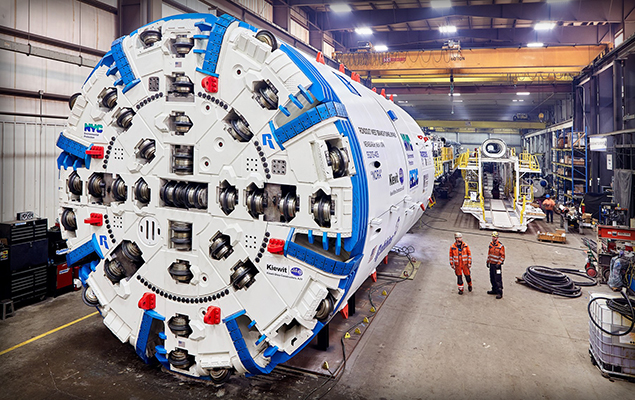
Tunnel boring machines like the one here, for New York’s Delaware Aqueduct Repair, are turning risk aversion on its head.
It has been some time since I have written on the Robbins blog page, but I am inspired to do so by the announcement that Elon Musk is entering our business—the tunnel boring business. It is great to see people with a vision of an improved world enter our industry. I agree with Musk that the advance rate of tunnels can be significantly improved if development money comes into the industry. Development money in tunneling, however, is at best minimal and is more often essentially nonexistent. Nearly all tunnels are heavily specified to avoid risk taking by owners (therefore discouraging new development). Nearly all tunnels go to the low bidder and low bidders try to buy the TBMs at the lowest price; a further discouragement of development. The industry has therefore been slow to improve advance rates, but with Musk bringing the issue into the spotlight, perhaps things will change.
Risk Aversion and How to Reverse it
There are some exceptions to this practice of risk aversion for new technology, and one is the Delaware Aqueduct Repair. This tunnel corrects heavy water leakage occurring from the 1940’s-built aqueduct tunnel for New York City. We are just completing Factory Acceptance in our plant in Solon, Ohio of this unique Single Shield TBM. The tunnel is at significant depth (approximately 300 m / 900 ft) with the distinct possibility of encountering very high water pressure (up to 30 bars). The contractor JV of Kiewit/Shea have shown their willingness to move forward with several new developments for this project. The concept of grouting off high water pressure as the primary means to allow advance in such conditions, rather than use an EPB or Slurry TBM, is in my view a significant step forward for our industry. Granted there have been halfway attempts with a combination of grouting and pressurized tunneling at recent projects like the Arrowhead Tunnels and Lake Mead Intake No. 3, but these have come at high cost and sometimes long delays. The Delaware Aqueduct TBM, by contrast, is designed to hold up to 30 bars of pressure while grouting occurs. Boring and cutter changes are done in atmospheric pressure.
Chemical grouting and grouting technology in general have advanced multifold in recent years, and it is commendable to see it used extensively on several aspects of the Delaware Aqueduct Project. It’s a great example of what can be done when a contractor is willing to use new technology to address potential risks—it appears it can actually reduce risk in the long run. It is a great honor to be working with the capable Kiewit/Shea JV team to be a part of advancing technology.
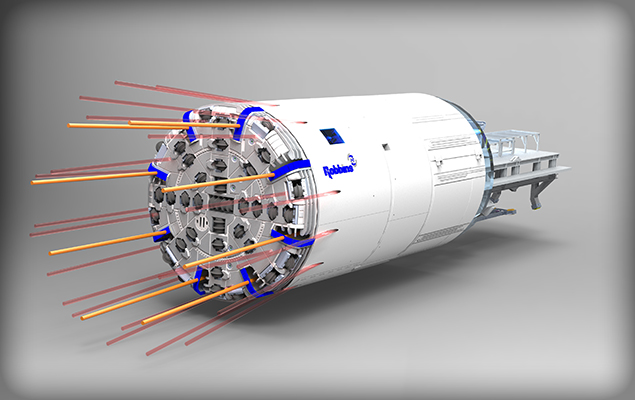
The enhanced probe drilling and grouting capabilities as seen in trajectories (orange and red) on the Delaware Aqueduct TBM 3D model.
Areas Ripe for Change
The Delaware Aqueduct Repair project is a flagship project for what I hope will become more common in the industry: instead of low bidding with the cheapest possible machine, offering a reasonable bid with a specialized TBM that has a higher initial investment, but ultimately a lower cost overall. The project’s use of technology is wide-reaching, particularly atmospheric cutter changes and chemical grouting, which have the potential to reduce downtime and increase safety. I do not see the future of rock tunneling under high water pressure being left to divers to change cutters and repair the cutterhead. We all know it is not cost effective to send divers to work in confined spaces over 10 bars. It should be noted that the long-duration Hallandsås Tunnel, for example, finished the majority of its TBM advance by relying on effectively this technique of grouting and advance after failing with a Slurry System. There are lots of tunnels to be built with above 10 bars pressure that will use this technology. The industry needs to automate cutter and bit changes as much as possible, and increase the integration of chemical grouting in tunneling.
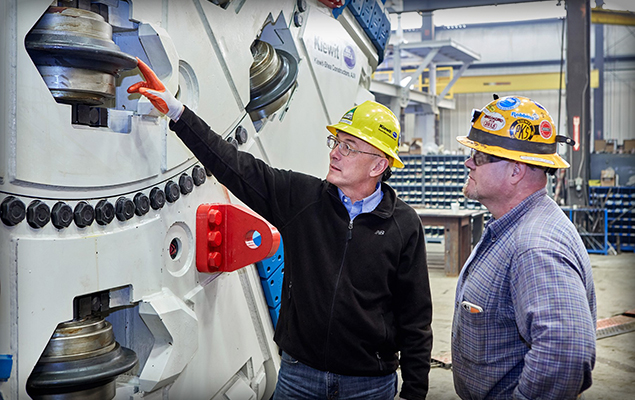
Niels Kofoed and Danny Smith of contractor Kiewit examine the cutterhead and cutters of the Delaware Aqueduct TBM. The machine can bore and cutters can be changed at atmospheric pressure.
Certainly there are many areas for advancement in our industry, and major public figures like Musk drawing attention to it is ultimately a good thing. After all, getting the general public to think about solving traffic by going underground is no easy feat. Even more so, getting the tunneling industry to think about its own risk-averse practices has a big potential benefit. Hopefully all of this attention will result in more tunnels, more business, and better infrastructure. Musk’s willingness to take a risk aimed at making the underground construction industry potentially faster and more stable is a good bet to take.