Без категории
Tunneling in Turkey: The Esme Salihli Railway
Large diameter tunneling in mixed ground has historically been seen as a challenge, but a recently completed tunnel in Turkey has changed the conversation. A 13.77 m diameter Crossover XRE TBM bored the Esme Salihli Railway Tunnel at world-record-setting rates of up to 721.8 m in one month, making it the fastest TBM over 13 m in diameter. What allowed the project to achieve such high advance rates?
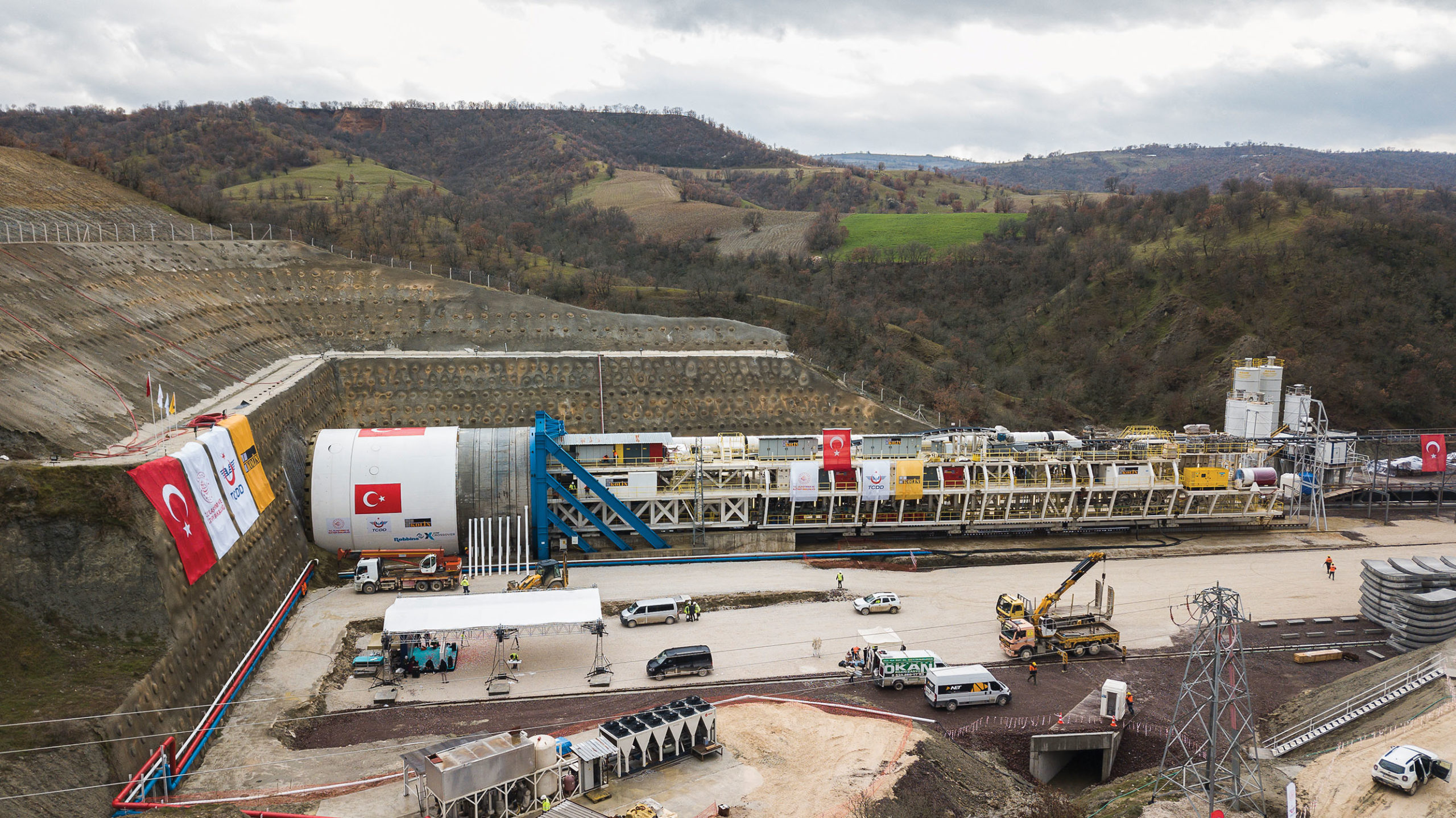
A Robbins Crossover machine that bored Turkey’s 3.05 km (1.90 mi) Eşme-Salihli Railway Tunnel through mixed conditions including sandstone, gravelstone, claystone, and siltstone for contractor Kolin Construction.
Machine Design for Variable Geology
The Eşme-Salihli Railway Tunnel is a short section of high-speed railway, measuring 3.05 km (1.90 mi) through mixed conditions. Contractor Kolin Construction conducted 15 core drillings at 200 m intervals prior to the start of construction, with results predicting occasional groundwater and weak rock between 5 to 9 MPa (720 to 1,300 psi) UCS, with the potential for a gassy environment. Rock and soil types included sections of gneiss, sandstone, claystone, mudstone, quartzite, and silt.
A dual mode rock/EPB TBM design was created for the project, in which no design elements were sacrificed in the engineering: The machine was fully capable of operating in 100% EPB mode or 100% Hard Rock Single Shield Mode. The TBM was designed for sections of hard rock and mixed ground, in highly variable conditions. For details on the design, check out this technical paper.
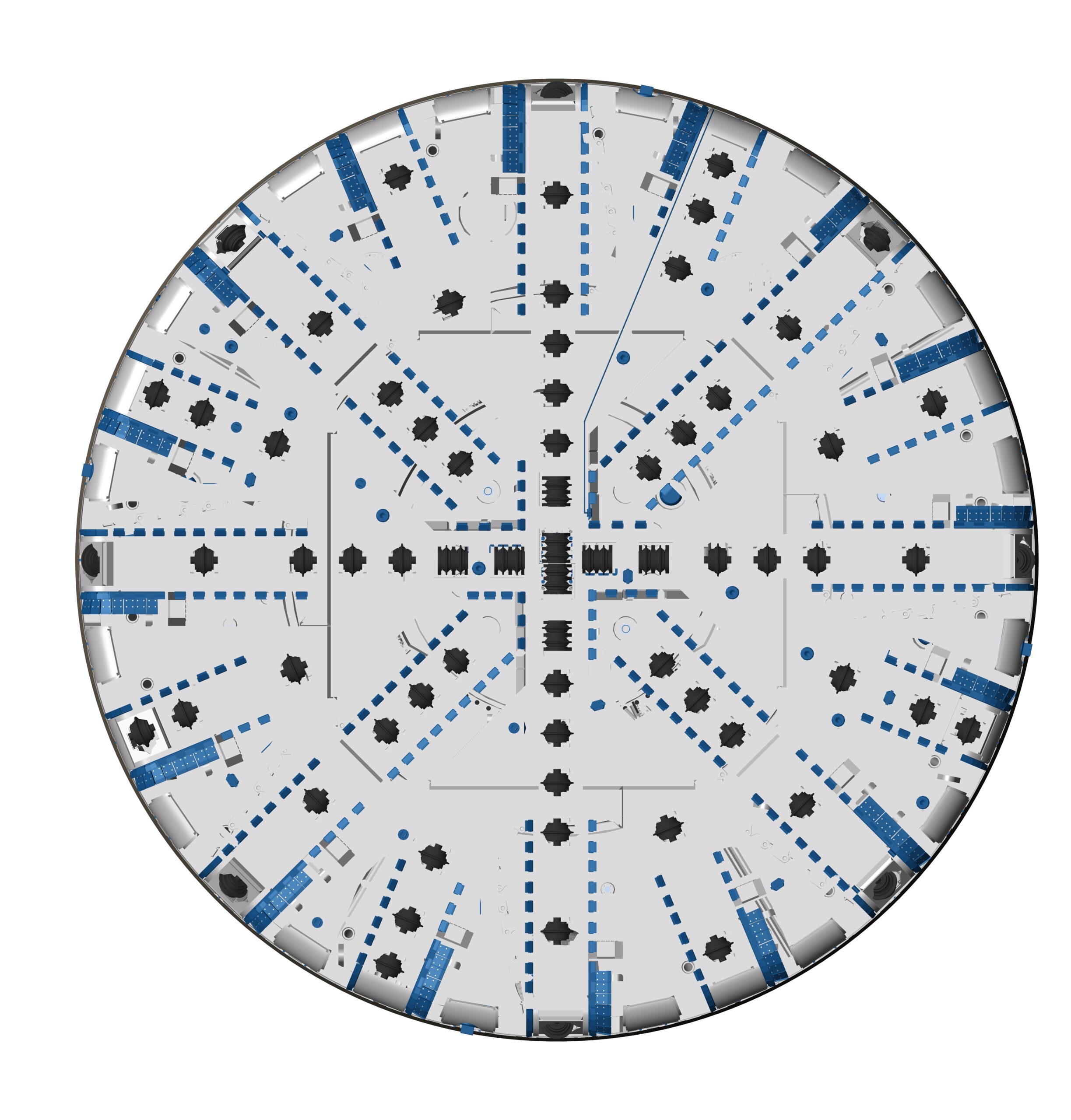
The cutterhead in hard rock mode.
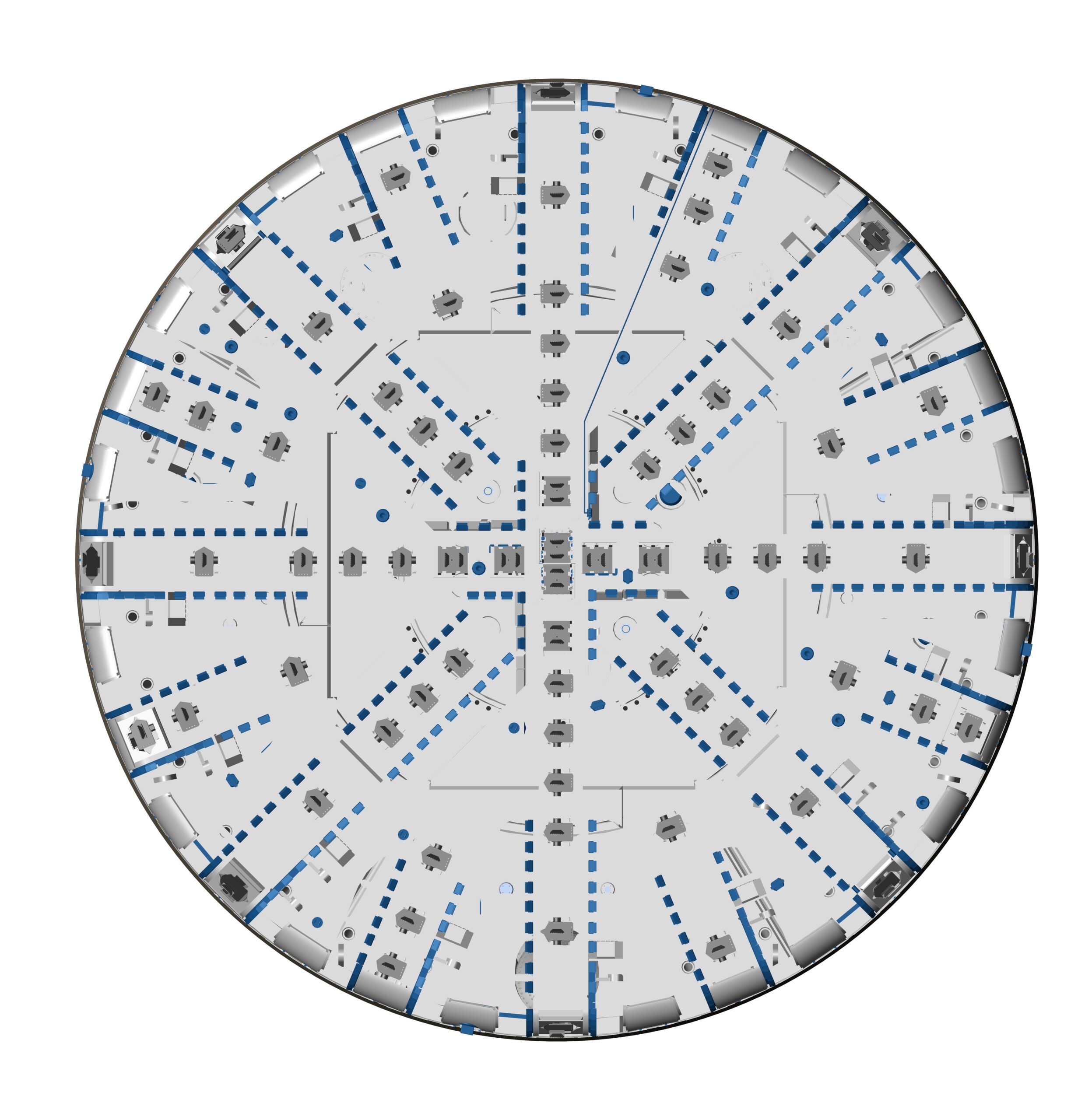
The cutterhead in EPB mode.
Epic Results
The 13.77 m Crossover XRE machine launched on its 3.05 km (1.90 mi) bore at the end of March 2021. While some of the crossover features proved beneficial the TBM was able to utilize the screw conveyor for mucking for the complete tunnel drive, which was a further benefit for the project’s overall schedule.
What allowed the machine to perform at high rates of advance? Utilization charts reveal that 38% of the total time was spent on excavation, 27% on ring assembly, 21% on planned downtime such as maintenance, and 14% on unplanned downtime.
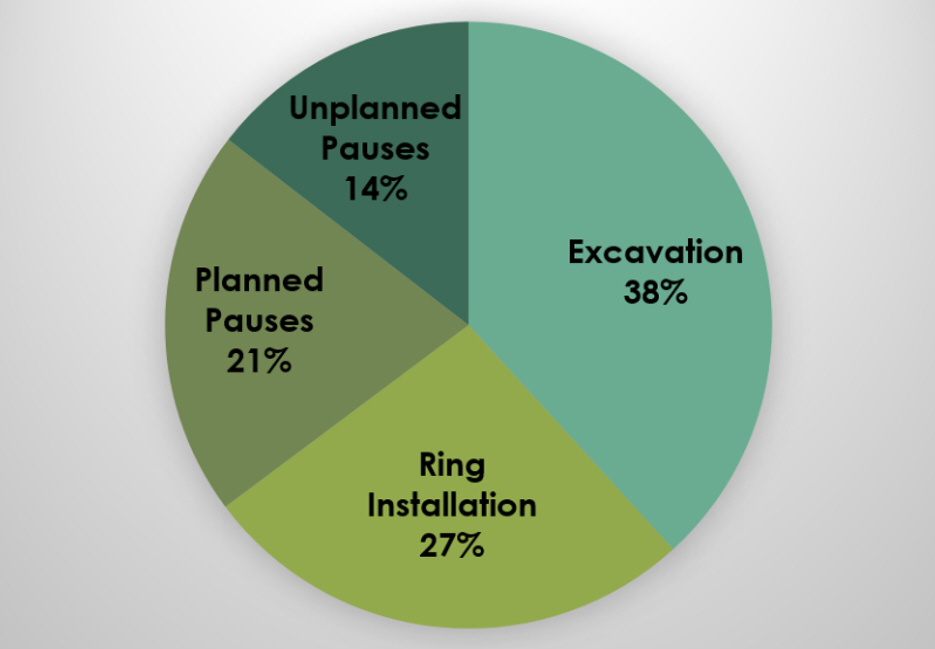
Productivity pie chart.
When looking at planned downtime, the most time was spent on cutterhead maintenance at 28%, followed by crew breaks at 22%. An average machine push took 60 minutes, while ring builds averaged 42 minutes.
Delays caused by mechanical, hydraulic or electrical failures were very low. The contractor cited the main reasons for minimal downtime, and thus high advance rates, as regular planned maintenance, cleaning, an experienced team, and an adequate supply of spare parts. Ultimately the tunnel was completed in just 6.5 months.
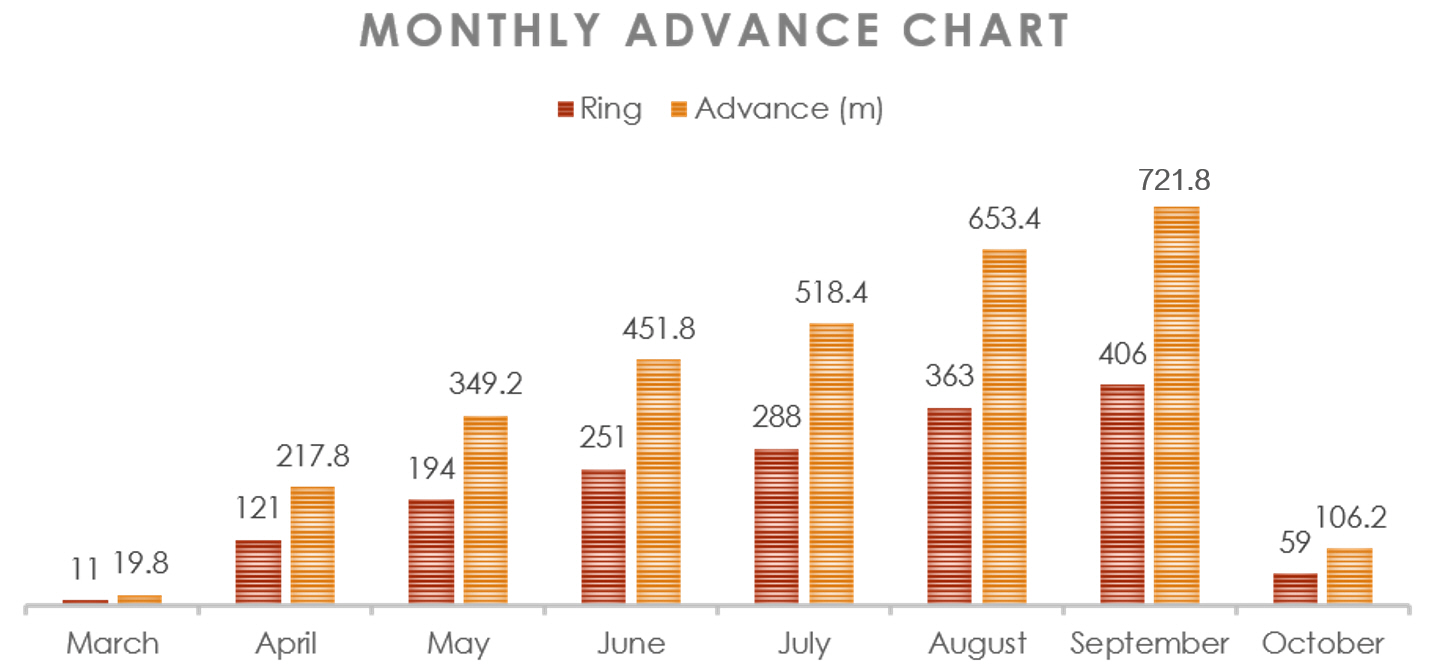
Monthly advance rate chart in meters bored and rings built.
In Conclusion
Large diameter, dual mode rock/EPB machines can and will excavate mixed ground conditions efficiently – even at world record rates. While similar projects in Turkish geology have met with challenges, the Esme-Salihli tunnel shows that with proper maintenance and a knowledgeable crew, equipment downtime can be kept to a minimum and advance rates can remain high.
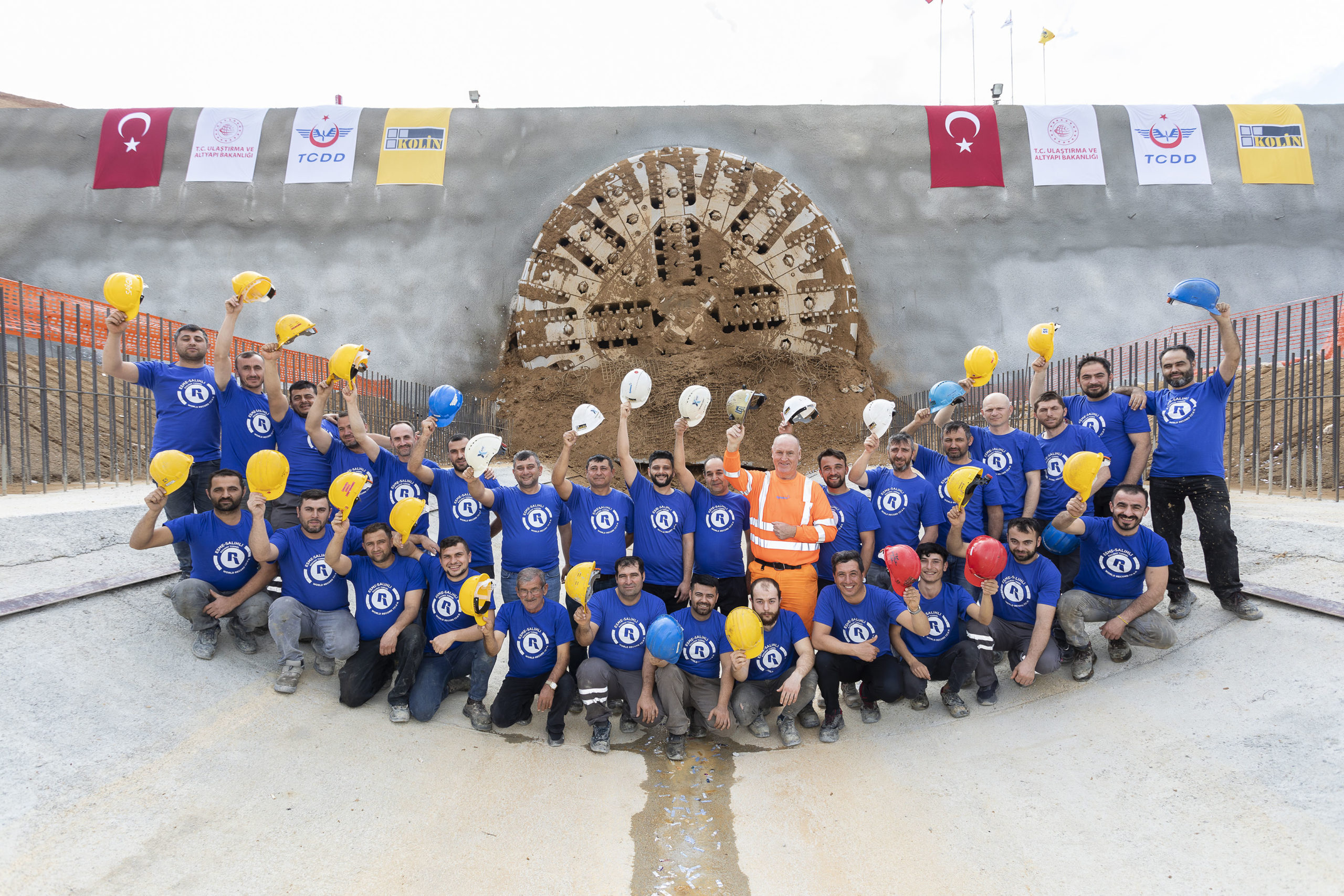
Personnel from contractor Kolin Construction and Robbins celebrate the breakthrough of a Crossover (XRE) TBM after it completed Turkey’s Esme Salihli Railway Tunnel.