Year: 2017
运用刀具仪器技术的智能滚刀监测系统
在机械化隧道施工中,掌子面的连续地质信息是必不可少的。刀具仪器的最终目标是实时监测单个刀具的操作,获得更真实的刀盘推力值,并在刀盘前方获得更好的地质信息。对这些信息的分析可以为机械挖掘提供深入的了解。刀具操作信息具有直接和间接的优点:它有助于更好地预测和监控刀具使用率,并且可以降低计划外刀具或更换环的成本,从而更好地规划库存、人力和翻修刀具需求。
目前滚刀刀具仪器技术被设计成一个方便安装的仪器包,用于监测单个刀具的转速、磨损、温度和振动。数据记录器服务使用低功率无线电技术无线接收刀具信息,并实时显示刀具状况。使用刀具仪器,操作员持续监控刀具状况,从而提高效率、降低停机时间,并防止意外的环磨损相关损坏导致轴承和刀座进一步损坏。在罗宾斯岩石掘进机上进行了刀具检测技术的试验,并给出了以往和近期的试验结果。讨论了延长寿命和提高可靠性的设计改进。
安第斯山脉高埋深掘进机隧道——智利两个具有挑战性的隧道项目的比较研究
从地质学角度来说,安第斯山脉是世界上最年轻、最复杂的山脉之一。隧道工程,尤其是水力发电和输水工程,对该范围来说并不新鲜,但其过去的历史取得了好坏参半的成功。两个新项目利用非常不同的隧道掘进机和挖掘策略,现在为智利安第斯山脉的现代地下施工设备提供了试验场。
本文将分析在智利两个项目:阿尔托梅坡(Alto Maipo)和秃鹰(Los Condores)水电站项目,位于安第斯山脉,相距约100公里。将详细分析所采用的两种策略,一种是使用开放式主梁式掘进机加上广泛的地面支撑,另一种是使用双护盾掘进机和分段衬砌。作者将研究两个隧道中遇到的隧道掘进机性能和地质条件,以及隧道掘进机的选择和围岩支护策略对每个隧道作业的影响。
墨西哥城TEP二期污水隧道的成功开挖,采用跨模式掘进机在具有挑战性的地质条件下掘进
墨西哥城的历史与地理位置问题密不可分。在过去的100年里,墨西哥城下沉了将近12米,因此,墨西哥城的建筑、主要街道、污水系统等遭到了严重破坏。
到2015年7月,一台跨模式掘进机市场的启动标志着墨西哥城下一个具有挑战性的EP二期污水隧道项目的开始。在5.5公里长的隧道将穿越深170米的山和8米之上的住宅建筑,地质条件也同样不同。地质由安山岩和英安岩组成,带有凝灰岩带和断层带,以及隧道终点处的一段软土。
本文将详细介绍为应对挑战条件而设计的独特直径为8.7米的跨模式隧道掘进机,以及通过断层带、软土地基等成功挖掘机器。将分析挖掘策略、提前率和停机时间。由于机器可以在隧道中从硬岩模式转换为土压平衡模式,作者还将研究转换过程以及两种模式如何在广泛变化的地质条件下进行挖掘。
亚克朗俄亥俄州运河拦截隧道大直径跨模式隧道掘进机的设计与实现
俄亥俄州运河拦截隧道(OCIT)项目涉及建造运输和储存隧道系统,以控制亚克朗市中心地区几个监管机构的综合下水道溢流。将使用罗宾斯跨模式掘进机XRE,兼并硬岩和土压平衡作业模式,开挖直径为9.26米的隧道并安装预制节段衬砌。
罗宾斯跨模式掘进机XRE,兼并硬岩和土压平衡作业模式。以便在岩石和混合地质中进行有效开挖,例如,灵活的刀盘设计,能够在岩石和混合地质下进行开挖,可在硬岩中以超速模式调节主驱动速度,以及特殊的螺旋输送机磨损保护系统。本文介绍了这些设计特点、制造工艺和现场施工情况。
采矿业新趋势:采矿业的掘进机设备
TBMs have become well accepted in civil construction tunneling and excavate a high percentage of civil construction projects each year. But each year in the mining industry, far more kilometers of tunnels are excavated for mining purposes than for civil purposes. The amount of tunnels needed for mining operations is staggering.
Some examples from metal mines:
- A large, deep gold mine has over 800 km of tunnels. That is a single mine!
- One small underground metal mine excavates over 13 km of tunnel each year
- In the Sudbury, Ontario mining district, there are over 5000 km of mine tunnels
If tunnels for coal mining were included, the statistics would be even more dramatic. But all these tunnels hold a little-known secret.
The Lack of Mechanized Tunneling
How many of the above thousands of kilometers of mine tunnels do you think have been excavated by TBM? The answer is “Nada”. Compare that to the thousands of kilometers of civil construction tunnels built over the last decades, which required hundreds of TBMs. Why such a great disparity when the objective in both industries is to excavate underground openings as rapidly, economically, and as safely as possible? What are the differences in these industries?
In TBM civil construction, the TBM crew members that know how to make things happen underground, that know how to drive the machines, how to lift heavy components and repair the equipment, how to get the trains in and out to remove the muck and to bring in supplies, are known by a special name. They are known as the “miners”. Yet the only thing they are mining is the muck, no coal, no minerals. But “miners” is a term of reverence for someone who knows how to excavate a tunnel rapidly and efficiently. When a civil tunnel is progressing well, they say “now we’re mining”. (Well, sometimes they also say this sarcastically sometimes when things are going poorly underground.) Why aren’t such talented miners, who know how to make a TBM perform, using their TBMs to excavate thousands of kilometers of mine tunnels each year? What are the differences between civil tunneling and mine tunneling?
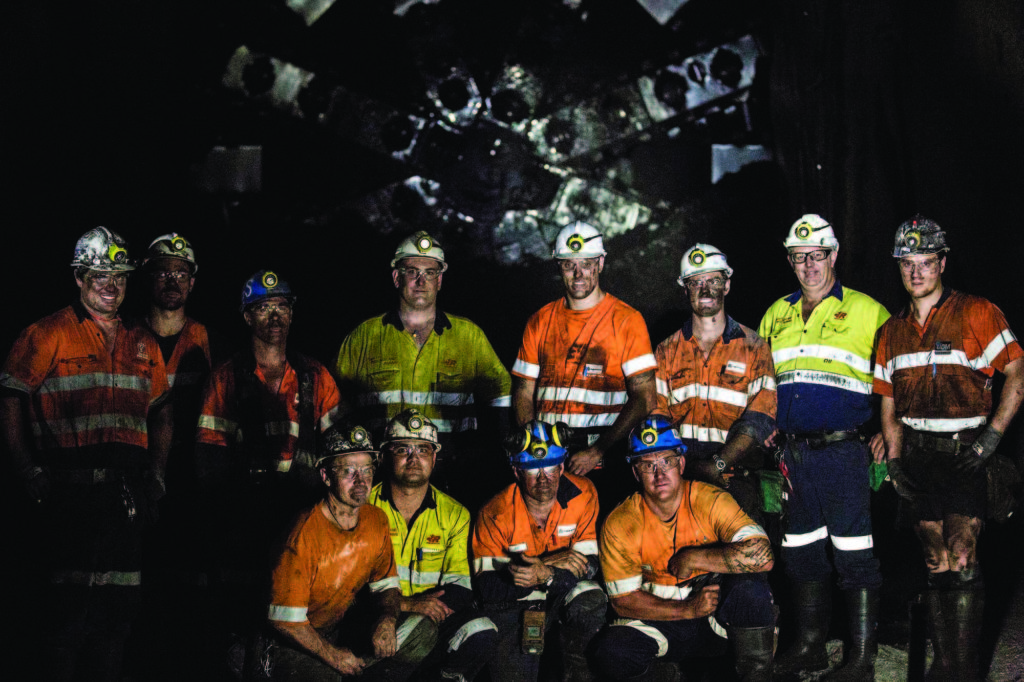
A group of talented miners at Australia’s Anglo American Coal Mine, where a Robbins Crossover TBM excavated two drifts for haulage and personnel access.
TBMs for Civil Tunnels
TBMs have become well accepted for civil tunneling. TBMs designs have become widely adapted for different ground conditions or specialized applications: Hard rock, soft ground, mixed face, pressurized face. Various types of ground support can be installed, according to current geological conditions. More current “hybrid” or “Crossover” TBM designs can handle widely different geological conditions, with the TBM adaptable to cope as conditions change.
Civil tunnels are generally long tunnels, where the efficiency of TBM excavation offsets the longer mobilization and demobilization times. And civil tunnels are generally designed with equipment mobilization/demobilization in mind. Suitable sized shafts are located to allow relatively simple introduction or retrieval of the TBM equipment. The most efficient type of TBM is the full face, rotary type TBM, which produces a circular tunnel profile. The circular profile is nearly universally accepted for civil construction. It is the optimum profile for fluid flow for fresh water, waste water, or hydro tunnels. It is also widely accepted for vehicular civil tunnels that need a flat roadbed. A flat roadway is constructed within the circular tunnel profile and the remainder of the profile within the circle is used for ventilation, services, escapeways, etc.
Some efforts have been made to develop non-circular profile TBMs for the civil sector. These machines include the Mini-Fullfacer, the Mobile Miner, and horseshoe shaped shields with excavator boom or roadheader. Such machines may produce a non-circular profile that is better for that specific job. But usually, there is a penalty in production rate compared to full face, circular TBMs.
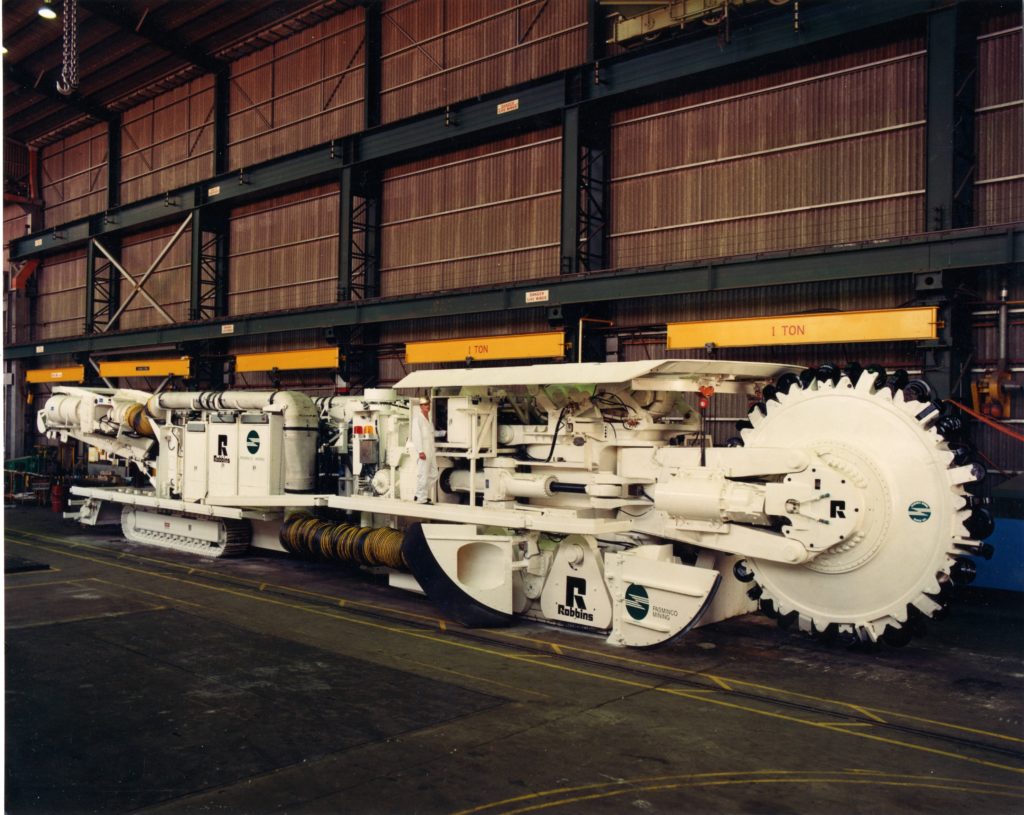
The mobile miner, a non-circular profile TBM developed by Robbins.
TBMs for Mine Tunnels
There have been some notable successes to the application of circular profile “civil type” TBMs for mining projects. Benefits have been lower costs, quicker access, and improved safety. Some examples include:
- Magma Copper, San Manuel Tunnels
- Stillwater Mines (four TBMs used)
- Grosvenor Coal Mine, Two Inclined Access Drifts to the coal seam
However, application of TBMs for mine tunnel construction has remained surprisingly limited. Why is this? Tunnels for mining are often not so long, or a developed in shorter phases, with the excavation front moved from place to place within the mine. TBMs and their constituent components are large and heavy. It is not easy to mobilize a TBM deep underground in a mine at a remote face. Better efforts must be made to make TBM transport and mobilization within the mine practical. This includes considerations for steep ramp roads and other restricted cross sections within the mine.
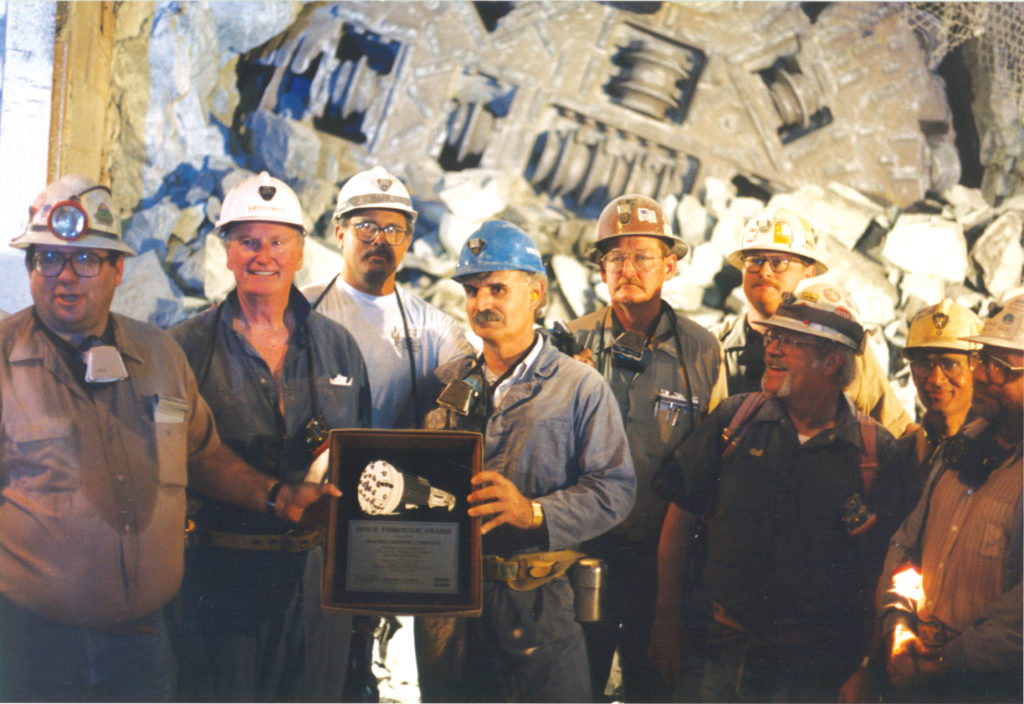
Breakthrough at the Magma Copper Mine in the 1990s.
Efficient TBMs are highly productive, but require a lot of power, ventilation, cooling, and support services. These need to be part of the mining plan so that the TBM has the necessary support and can provide the full benefit. Operating personnel with proper skills are also essential. If a TBM is introduced into a mining environment, either the mine personnel need proper TBM training or motivation, or the TBM drive must be isolated as a “stand alone” operation within the mine and be given proper priority of skilled personnel and the necessary services so the full benefit can be realized.
Mines often do not accept the circular profile produced by the most efficient, full face rotary TBMs. Mine tunnels are usually designed with a flat invert to allow for passage of rubber tired vehicles during the production phase of the mine tunnel. Many efforts have been made to provide TBM type equipment that produces a flat invert. Some have been relatively successful. But generally these machines do not provide the same productivity of efficient, full face circular profile TBMs. Rail bound mining vehicles can be used in the circular tunnel to take advantage of this TBM efficiency. Or, precast invert slabs, poured in place concrete, or partial invert filling can be used in a circular tunnel to provide a flat roadway. The cost/benefits must be analyzed and presented to the industry for a change to occur.
Mining plans often have tunnels with steep gradients and sharp radius curves. On steep gradients (up to 12-15 degrees), the most efficient haulage is usually by belt conveyor. However, the belt system is not effective if there are sharp radius curves. And typical TBM curve ability is limited. Special TBM designs can be made that allow for excavation in sharp curves, but there is a compromise in reduced TBM performance.
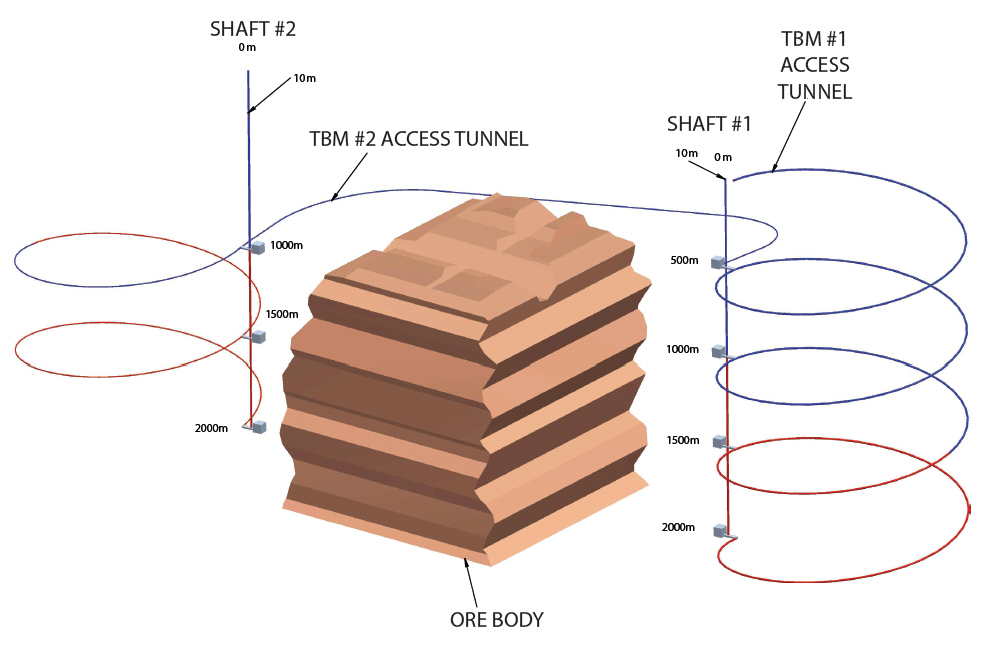
An example of a mine access and haulage plan to reach a deep ore body.
Mines need Versatile TBMs
It seems the mining industry needs the benefits that TBMs can provide. Open pit mines are becoming depleted, and mining activities are reaching deeper. Longer access tunnels are needed. Safety and speed of development are paramount. TBMs can offer these advantages, but have limitations. Special TBMs can be developed that meet special requirements, but usually there is a penalty in reduced TBM performance. The mine planners and the TBM equipment designers must work together at an early stage in the mine planning to determine the optimum compromise between most desirable mine plan, and most beneficial application of TBM equipment. A good partnering approach is necessary in the planning stage, as well as the operating stage, to allow for the most efficient application of TBM equipment to the needs of the mine.
By Dennis Ofiara, Chief Engineer
跨模式的诞生
The Real Field Experiences that Resulted in a Versatile Design
This blog is the first in a series called “Hidden Underfoot”, exploring the little-known history and behind-the-scenes happenings of the tunneling industry.
Many technological breakthroughs have been the direct result of the necessity to solve a problem; the creation of the first Crossover TBM was no exception. While much has been written about Central Turkey’s Kargi Kizilirmak Hydroelectric Project, we interviewed Field Service personnel who were there working in the conditions every day to get the untold story behind the genesis of the versatile Crossover TBM.
Behind the Scenes
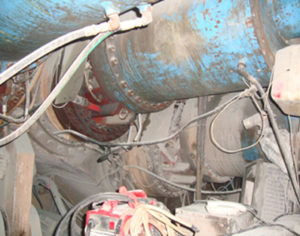
Custom-made gear reducers retrofitted to the motors in the tunnel.
The Kargi HEPP, now complete, generates 470 Gwh of power annually for project owner Statkraft, and supplies an estimated 150,000 homes.
Robbins supplied a 9.84 meter (32 ft) diameter Double Shield TBM and continuous conveyor system to Turkish contractor Gülermak for the project. The machine was to bore an 11.8 km (7.3 mi) headrace tunnel to divert water from the dam to powerhouse. Initial geological reports predicted softer ground for the first 2.5 km (1.6 mi), which would be lined with pre-cast concrete segments. The remainder of the tunnel was to be supported by a combination of shotcrete, rock bolts, and wire mesh in more competent rock.
The project became arduous soon after startup, when the machine encountered blocky rock, sand, and clays that were not initially predicted. “We realized modifications needed to be made as soon as we started experiencing flowing materials and squeezing ground,” said Glen Maynard, Robbins Site Manager, who worked on the project throughout the challenging conditions. Maynard’s prognosis was apt, as 80 meters (262 ft) into the bore the TBM became trapped in a section of collapsed ground. “The machine faced serious blockages,” added Maynard, “there was no one fix, each problem needed its own solution. Thrust, cutterhead, and ground support all needed adjustment.” The machine was freed but continued to struggle, requiring not just one but seven bypass tunnels to free it each time it encountered collapsing ground.
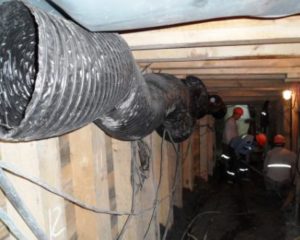
Construction of one of several bypass tunnels at Kargi.
Concerns that the machine would need to be buried were quickly mollified. Robbins President Lok Home told the Kargi team to build a “wish list” of all the materials they would need to modify the machine and get it moving again. Robbins and Gülermak worked together to determine what changes would need to be made, and parts were shipped to the jobsite as quickly as possible. This of course, was not the first time a machine had required modifications while in the tunnel, and Robbins engineers were able to pull from past projects in order to know what needed to be done.
In-Tunnel Effort
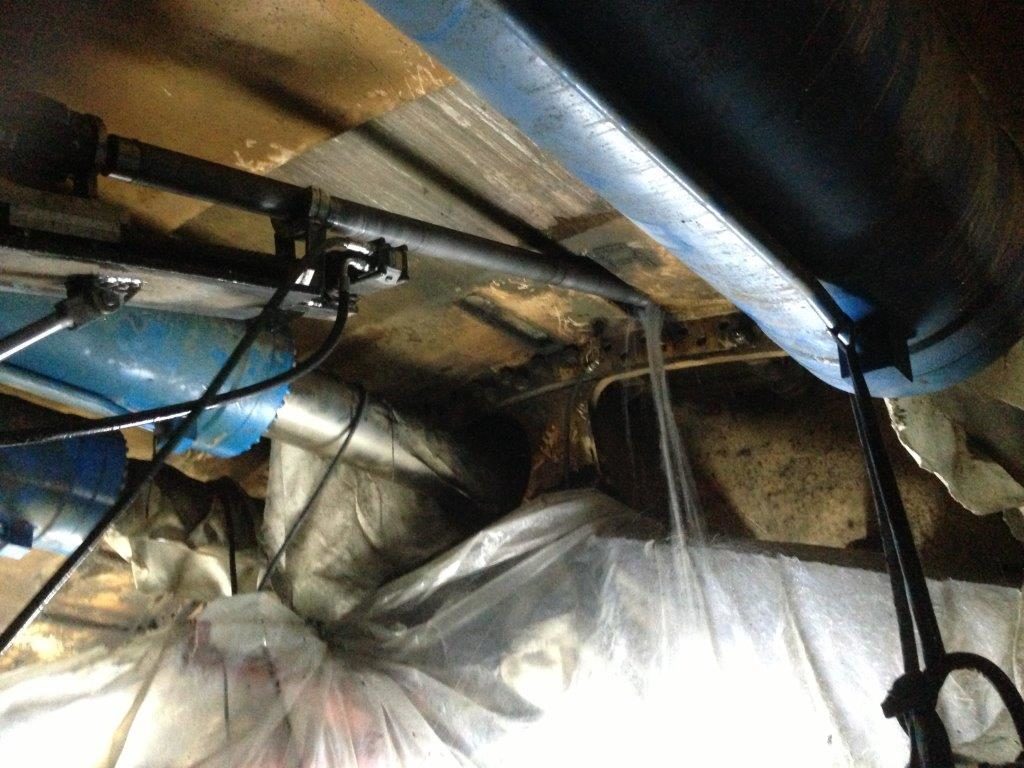
Canopy drill installed in the tunnel.
The contractor, with the assistance of the field service team, installed a Robbins custom-built canopy drill and positioner to allow pipe tube support installation through the forward shield. This allowed drilling with a distance of up to 10 m (33 ft) ahead of the cutterhead while 90 mm (3.5 in) diameter pipe tubes provided extra support across the top 120 to 140 degrees at the tunnel crown. Injection of resins and grout protected against collapse at the crown while excavating through soft ground. “There were a lot of risks to the modified machine, but we gave comprehensive instructions on how to operate it to the contractor,” said Maynard. “The contractor team was open to change and had great cooperation. They were a really hard working team.”
To further mitigate the effects of squeezing ground or collapses, custom-made gear reducers were ordered and retrofitted to the cutterhead motors. They were installed between the drive motor and the primary two-stage planetary gearboxes. When the machine encountered loose or squeezing ground the reducers were engaged, which resulted in a reduction in cutterhead RPM and a doubling of the available torque. The net effect of the modifications allowed the Double Shield TBM to operate much like an Earth Pressure Balance Machine in fault zones and squeezing ground with high torque and low RPM—these methods effectively kept the machine from getting stuck. In addition, short stroke thrust jacks were installed between the normal auxiliary thrust to double total thrust capabilities.
The results of the modifications led to astonishing results. An advance rate of 600 m (1,986 ft) in one month was achieved in March 2013 and a project best of approximately 723 m (2,372 ft) was achieved in spring 2014, including a daily best of 39.6 m (130 ft) in April 2014. The TBM bored 7.8 km (4.8 mi) of the tunnel in total, making its final breakthrough in July 2014. The remainder was excavated by drill and blast—of which it is notable that the modified TBM achieved advance rates more than twice that of the traditional mining operation. “It was enjoyable to find a way to overcome this challenge,” added Maynard.
Mixed Ground Legacy
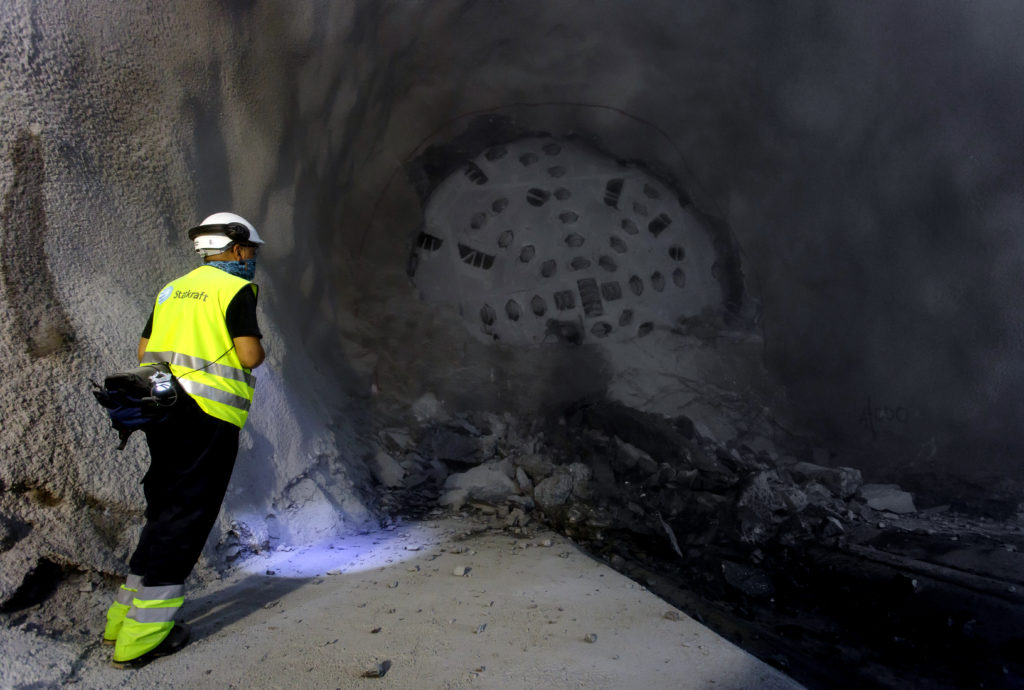
Successful breakthrough in July 2014.
A project that had started out as a disheartening one transformed into one that encouraged others. The insights gained by implementing changes to the Kargi machine were quickly applied to other projects facing mixed ground conditions that would otherwise require multiple tunneling machines. From these creative solutions came the design of a new line of Robbins dual-mode machines—TBMs that contain features of two machine types—termed Crossovers. Everything from multi-speed gearboxes to canopy drills, and emergency thrust are regular features of Crossover machines, and they owe their genesis to the hard work involved at Kargi HEPP.
罗宾斯公司: 专注前行
罗宾斯公司60多年来一直是隧道掘进机和地下施工设备的领先制造商。了解罗宾斯员工的公司历史,了解最新的创新和设计理念,使罗宾斯成为行业的思想领袖。
美国第一台作业的跨模式掘进机“罗斯”
2017年5月30日,一辆直径为9.26米的罗宾斯跨模式掘进机在工厂验收。这台巨大的机器最初是在5月25日的新闻发布会上在俄亥俄州罗宾斯的索伦总部亮相的,之后被运往南部40公里的地方,用于在亚克朗建造俄亥俄运河拦截隧道项目(OCIT)。出席会议的有亚克朗市长Daniel Horrigan、罗宾斯首席工程师Dennis Ofiara和承包商肯尼·大林合资公司(Kenny-Obayashi JV)的项目工程师David Chastka。
掘进机具有土压平衡和硬岩单护盾两种作业模式的特点,是美国使用的第一台跨模式掘进机。它将从一个12米深的入口始发,并在软土地质下开挖长68米的第一段隧道区间,在转换为硬岩模式之前,过渡到183米长的部分面页岩区域,然后在全面页岩中继续驱动。超前钻探将使用两个探头钻头连续进行,以决定掘进机应处于哪种模式作业。”罗宾斯提供了一个强大的设计,我们相信将能够处理OCIT项目隧道驱动的所有挑战,”Chastka说。
机器的独特之处包括一个多功能刀盘,该刀盘的配置考虑了硬质岩石中的短软土段和硬岩长段(约占隧道的65%)。如果刀具堵塞,将使用滚刀和刮刀的组合。滚刀所需的滚动扭矩减少了25%,以支持在软土地下顺利旋转。XRE机器的电机已从原来的土压平衡模式配置中进行了调整,以允许驱动的打开模式段在降低扭矩的情况下提高电机转速。
通过一个耐用的螺旋输送机来清除渣滓,其第一段由耐磨板焊接而成。螺旋轴采用交叉舱口式硬面衬里,螺旋输送机外壳采用耐磨板和硬面衬里,整个传动装置都制定了磨损监测系统,以使设备在磨蚀硬岩地质下可以最大限度地提高开挖效率。罗宾斯项目经理Pablo Salazar对于在掘进机施工和设计过程中使用当地生产力感到自豪:“我们已经在俄亥俄州东北部地区制造了机器的大部分。许多部件都是在本地与次级供应商以及我们自己的车间制造的。”
这台机器被称为“罗斯”(“Rosie”),以纪念Rosie the Riveter,这是代表在第二次世界大战期间在工厂和造船厂工作的美国女性的标志。包括亚克朗居民Rose May Jacob在内的数百名在工厂工作的“Rosies”,为盟军的战争努力提供材料和军备。 掘进机将以卡车运输到工地,大型刀盘分为四件。 “整个装配过程允许承包商密切关注机器的测试,因此他们现在非常熟悉掘进机。在工地,我们还将为备件和人员提供即时支持,“Salazar说。 罗宾斯的工地主管将协助掘进机装配和至少前1000米的掘进。隧道掘进计划于今年8月开始。
亚克朗市的OCIT项目包括修建一个运输和储存隧道系统,以控制阿克伦市中心地区几个监管机构的综合下水道溢流(CSO)。环境保护局授权的项目包括1.89公里的运输和储存隧道,以及竖井、引水结构、加固下水道和相关结构。同意令规定,隧道必须在2018年12月31日前投入运营。
跨模式XSE掘进机参数表
如果您的项目含有高通透性的土壤夹杂地透性的地质,跨模式XSE掘进机是您的方案。
跨模式XRE掘进机参数表
无论您的项目地质包括硬岩、软土、巨石,还是一些其他东西,罗宾斯都能为您提供解决方案。并非所有项目都符合特定掘进机类型的参数,在罗宾斯,我们认为您的机器应根据您独特的项目要求进行定制设计。跨模式掘进机XRE提供了兼并土压平衡(EPB)和硬岩单护盾(Rock)作业模式的的最佳功能。