Year: 2019
罗宾斯盾构机最后标段贯通顺利结束62公里墨西哥TEO污水隧道的施工
2019年5月23日,举行了一场庆祝活动:6台直径为8.93米的土压平衡盾构机中的最后一台在墨西哥城的伊米苏. 奥连特隧道(Emisor Oriente,简称TEO)的第4标段完成了挖掘工作,这一壮举标志着历时10年、长62.1公里的隧道施工顺利竣工。“我们为成功完成挖掘工作感到自豪,尽管我们经历了各种困难,例如大量的涌水、液压负荷和不断变化的地质。我们通过对没段地质类型进行调整挖掘模式来解决这些问题,”第4标段包承包商Carso Infrastructura y Construcción(Carso)的机械经理Hector Arturo Carrillo说。
尽管碰到了诸多挑战,但设备掘进速度依然达到日掘进30米和月进尺528米的项目记录。对于这个作业表现Carrillo说,这与用于清除渣土的连续输送系统有很大关系:“应该注意的是,我们的掘进速度归功于优秀的罗宾斯输送机设计。隧道输送机由增压器、垂直带、曲线托辊、推进尾件等部件以及地面部件组成。就我个人而言,我认为这是一个优秀的、令人信赖的系统,帮助我们实现了掘进机的优异的进尺。”
这一项目的贯通是土压平衡盾构机在应急污水项目中所遇到的一些最困难地质问题,最新和最重大的里程碑。10.2公里长的4号标段,从17号竖井延伸至13号竖井,深度达85米,地质包括玄武岩段,中间夹杂着高水压的渗透性砂。“我们的机器必须攻克最恶劣的地质条件,但它们是为挑战这些困难而设计的,”负责第3、4和5号标段三台罗宾斯土压平衡盾构机和连续输送机系统的罗宾斯墨西哥总经理Roberto Gonzalez Ramirez说
所有的机器都是设计可承受4到6巴的水压,配备了复合地质背装式刀盘以应对各种地质条件。根据地质情况,高压碳化钨刀具可与直径17英寸的碳化钨滚刀互换。其他设计包括人仓和物料仓可承受高达7巴的压力,重新设计的铲斗,和用于加固螺旋输送机的悍达耐磨板以及可拆卸的耐磨板,以进一步加强每个螺旋输送机运作。旋转活动接头经过重新设计,以提高在刀盘干预期间的换刀时间,而新的刮刀设计给予刀盘在岩石复合地质条件下提供更大的抗冲击性。
第4标段的掘进机在17号始发井内组装,并于2012年8月投入使用,龙门架和所有的后配套支架位于地面。2012年10月,在设备推进150米后,机器及其后配套系统在隧道内完成了组装。一个月后,连续输送系统也完成安装并启动运行。
在挖掘了405米之后,岩石、刮刀、搅拌杆的一部分和其他磨损材料,促使施工队进行刀盘检查。在高达3.5巴的压力下,项目决定需要进行高压干预。在2013年6月2日,施工队通过隧道中的盾构机进行了第一次高压干预。然而,这些干预措施费用很高,并且证明是耗时的。在大约50次高压干预后,项目的其余部分干预都是大气模式下进行的。 “在大气模式下进行的干预是最大的挑战。因为我们在倾斜隧道上开挖,大量涌入水量测试了到达极限。在所有这些干预措施中,我们必须在盾构机和输送机轴上实施双泵系统,“Carrillo说。尽管每次操作都存在挑战,如抽水量高达每秒180升以及清除隧道中的砂石,但大气模式下干预的成本仍然低于高压下的干预,并且速度更快。
尽管条件很恶劣,Carrillo认为罗宾斯的现场服务都给予整个施工作业很好的支持:“罗宾斯一直为我们提供方案,从不吝啬用他们所有的经验为我们解决问题。举一个最近的例子,在本项目即将结束时,设备的盾体遇到了阻碍,无法前进。必需增加液压系统的压力,把28台推力油缸的压力范围提升到596巴的范围。罗宾斯的现场技术人员都全程和我们一起,帮助我们一起冲破这个障碍。”
当掘进遇到困境:越南昆嵩水力发电隧道项目
与罗宾斯一起前往越南风景如画的昆嵩隧道项目,在该项目中,直径4.5 米的主梁式硬岩掘进机已经完成掘进。在高湿度和地下水中放置14个月后,由罗宾斯和承包商CC47介入并扭转该项目。观看视频,了解罗宾斯团队如何处理多个断层带和主要的涌水,同时保持设备所需的掘进速度。
罗宾斯掘进机在尼泊尔提前一年贯通
2019年4月,罗宾斯双护盾隧道掘进机成功挑战喜马拉雅山公认的困难地质条件,总体项目计划提前约一年和隧道掘进计划提前七个月贯通。尼泊尔的第一台隧道掘进机,直径5.06米,在两个不同的情况下,月进尺超过1,000米。 该机器完成了尼泊尔政府灌溉部(DOI)和承包商中国海外工程集团有限公司尼泊尔分公司(COVEC NEPAL)的12.2公里的巴瑞巴贝引水多用途项目(BBDMP)。
尼泊尔总理毕马沙尔马·奥利(KP Sharma Oli)在仪式上发表了演讲,他称赞了该项目及这个项目对尼泊尔未来TBM项目成功的影响。“这不仅是新技术进入尼泊尔,而且是一个巨大的收获。政府还计划实施各种其他多用途项目,如萨科希马林引水工程( Sunkoshi-Marin Diversion Project)。
施工商的施工进度十分喜人,这台机器仅用17个月就完成了隧道建设,比内政部要求在2020年3月28日完成隧道建设的最后期限提前了近一年。“突破性的仪式很棒。中国海外工程集团有限公司尼泊尔分公司项目经理胡天然说:“我们为我们终于做到了这一点而感到骄傲,而且我们的总体进度比原计划提前了近一年。”
可行性研究表明隧道的钻爆开挖法可能需要12年的时间,但作为国家“国家骄傲项目”之一的BBDMP项目需要加快完成。灌溉部需要一个更快的选项,他们在隧道工法中找到了全断面隧道掘进机。他们开始与当地罗宾斯的代表商量将把尼泊尔有史以来的第一台隧道掘进机引进入该国。内政部花费了七年,通过国际竞争性招标获得项目资金和选择了承包商。从2007年到2015年,项目正式启动。罗宾斯驻尼泊尔的代表Prajwal Man Shrestha说:“我们很荣幸成功地引进了掘进机技术。尽管过程有障碍和阻力,我们最终还是引进了这项技术,打破了尼泊尔所有的隧道施工记录。该国已受到国际关注,来自世界各地的施工商和开发商目前正在考虑尼泊尔未来的TBM项目。”
隧道位于喜马拉雅山脉南部西瓦利克山脉,地质主要由砂岩、泥岩和砾岩组成。“采用掘进机法代替传统的钻爆法是该项目成功的关键因素。它为尼泊尔未来水、能源、运输项目中大量类似隧道的实施树立了良好的榜样。我认为,在尼泊尔应用掘进机技术有着很好的前景,”胡天然继续说道。
为了确保最佳的掘进机性能并防止停机,机器维护每天都在固定的时间进行。地质工程师每天分析两次地质情况,以便在需要时调整隧道参数。精心部署的开挖施工奏效了:经验丰富的施工团队穿越了一个位于隧道5.8公里处危险的巴瑞断裂带,并通过5天内修建了一条旁通道脱困了一次卡机。为了应对这种情况,罗宾斯的掘进机设计配备了困难的地质解决方案(DGS),一套功能包括增强版超前钻探和前驱能力,以及一个阶梯式机器盾体和流畅的刀盘设计,以避免卡在坍塌的地面上。
项目经理胡天然表示,机器快速挖掘的秘密在于良好的规划:“由于承包商和设备供应商在初步阶段共同进行了深入的研究和详细设计,因此掘进机与项目的各种条件相匹配。结合罗宾斯公司在硬岩施工方面的优势,我们在该项目上取得了卓越的掘进机性能。”
BBDMP一旦竣工投入使用,将在尼泊尔南部地区灌溉5.1万公顷土地,并提供48兆瓦的年发电量。它将使用一个15米高的大坝,每秒将42立方米的水从巴瑞河引到150米头下的巴贝河,为周围的Banke和Bardia地区提供全年灌溉。预计尼泊尔卢比每年的灌溉效益为29亿美元,水力发电效益为43亿美元,一旦项目启动,总收益为72亿尼泊尔卢比(约6400万美元)。
主梁式在法国格勒瑞德嘉鲁完成艰难的法国隧道
2019年4月3日,罗宾斯一台直径3.5米的主梁式掘进机贯通后进入洞穴,完成了2.8公里长的引水隧道。这不是机器第一次遇到洞穴:在隧道掘进过程中,设备两次碰到了未知的洞穴,其中最大的洞穴大小达到惊人的8000立方米。
“克服障碍取得最近的贯通是一个重大的成就,” Marc Dhiersat说,他是承包商埃法日土建施工公司格勒瑞德嘉鲁隧道(Galerie des Janots)的项目总监。“我们很荣幸带领一支积极、认真的团队到达隧道尽头,尽管遇到了许多技术难题,但他们做的很好,没有发生事故。”
引水隧道位于法国卡西斯社区的下方,是一个以地下水,岩溶洞和空洞而闻名的石灰岩地区。设备于2017年3月始发,在含有石灰石与粉状粘土相结合地质下进行挖掘。在1,035米处,我们的工作人员在掘进机的左侧碰到了一个洞穴。洞穴中镶嵌着钟乳石和石笋,被掘进机的盾体磨破。工作人员不得不建一个4米高的混凝土墙,以便掘进机有东西可以顶住。然后再次启动掘进机,并且能够在八次冲程中成功导航出洞穴,并且期间没有停机 – 该过程耗时约两周。尽管存在这些挑战,但Dhiersat在整个考验中都对掘进机给予了积极的评价:“能应对这些所有的地质困难,这是最出色的设备。”
第一个洞穴虽然最大,但并不是遇到的最困难的空洞。在清理第一个洞穴后,机器平均每天向前推进20至22米,并有一个专门的夜班进行维护。在挖掘过程中,结合超前钻机和地质土梁调查(一种使用电致极化来检测掘进机前方异样的调查)。工作人员每周进行五天的挖掘,一个月内完成400米以上。这表现一直持续到2157米处,当时机器又磨破了一个延伸到隧道通道深处的另一个未知洞穴的顶部。该洞穴长22米,宽15米,深14米,约4500立方米。
工作人员在刀盘前探测并开始用泡沫和混凝土稳定和固定洞穴,并挖掘旁路隧道。 “在填充了大部分洞穴(1,500 平方米)后,我们最大的困难是确保支撑住机器:我们需要六个旁路隧道和四个月的工期完成这一挑战,” Dhiersat说。对于最后600米的隧道,“我们终于处于良好的岩石地质,”他强调说。该项目的总体平均日掘进为18米,两班制,并最高日掘进达到25米。
“和Marc及他的团队在现场的合作非常好,我们始终享受他们对项目和任务的专业精神和承诺。毫无疑问,这是我们取得成功的关键,“罗宾斯欧洲业务经理Detlef Jordan说道。 “对于我们来说,通过共同努力、通力合作,可以实现最佳和最成功的结果,这是令人满意和鼓舞的。几十年来,这一承诺一直是隧道行业成功的核心,但在最近的其他项目中并不总是如此。“
格勒瑞德嘉鲁隧道是14个旨在节约水资源和保护资源的工程之一,这系列工程由艾克斯 – 马赛 – 普罗旺斯大都会,罗纳地中海科西嘉水务局和州政府执行。格勒瑞德嘉鲁隧道开通后,将取代目前位于铁路隧道中的现有管道 – 这些原始管道存在严重缺陷,导致每年估计水损失量为500,000立方米。新隧道将容量增加到每秒440升。
6个史诗性项目|国际劳动节迎来罗宾斯世界各地的一系列贯通
几十个罗宾斯掘进机在世界各地的工地同时作业是很平常的事。但这个五月很特别,我们迎来了一次贯通的盛会。2019年4月,6个项目贯通的捷报纷纷传来,相信还有更多贯通接踵而来。
法国格勒瑞德嘉鲁项目(Galerie des Janots)
2019年4月3日,罗宾斯一台直径3.5米的主梁式掘进机贯通后进入洞穴,完成了2.8公里长的引水隧道。这不是机器第一次遇到洞穴:在隧道掘进过程中,设备两次碰到了未知的洞穴,其中最大的洞穴大小达到惊人的8,000立方米。
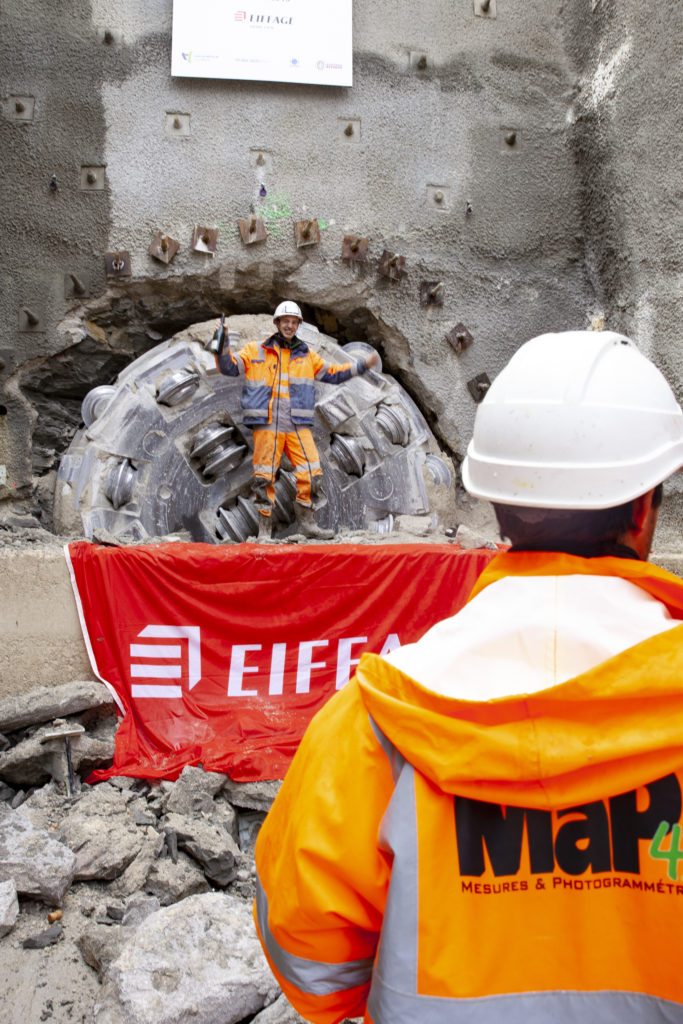
4月3日,承包商Eiffage土建施工在法国卡西斯庆祝罗宾斯掘进机的贯通
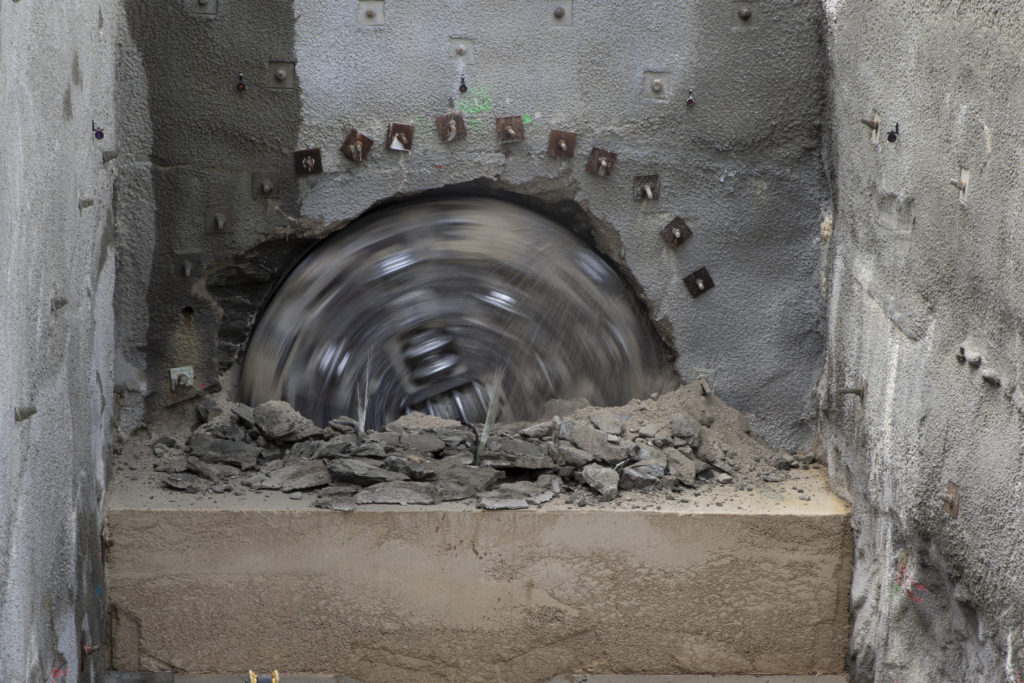
尽管在含有粉状粘土和岩溶石灰岩这样难以置信的地质条件下作业,罗宾斯隧道掘进机每天都能实现高达25米的掘进速度
2019年4月8日,两台直径6.5米的罗宾斯双护盾硬岩掘进机中的第一台完成了奥地利Gemeinschaftskraftwerk Inn(GKI)项目的作业,实现贯通。这条在高山小镇Pfunds附近长22公里的引水隧道,在片岩的高埋深(最大埋深高达1,200米)地质下作业。第二台双护盾掘进机预计也将在今年晚些时候实现贯通。
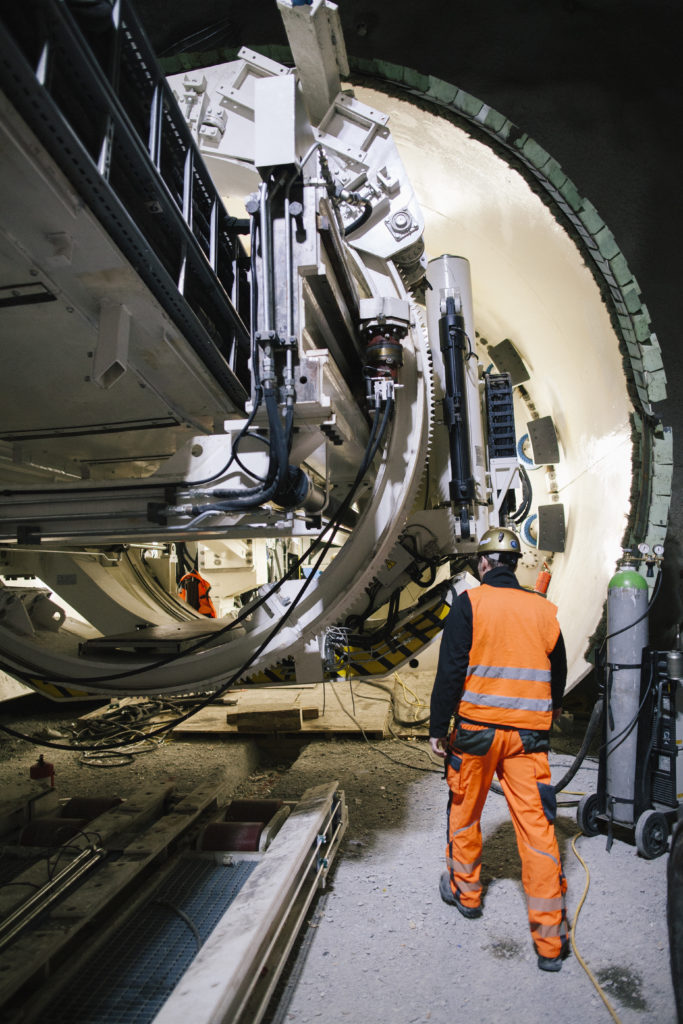
4月8日贯通的这台双护盾掘进机始发时的情景
美国迪津迪隧道系统
2019年4月10日,罗宾斯掘进机完成了美国印第安纳波利斯迪津迪隧道项目(Digindy)中的两个隧道段,即白河(White River)和低洼浦兹(Lower Pogues)隧道。这台36岁、直径6.2 米的翻新罗宾斯主梁式掘进机于2013年在印第安纳波利斯始发,并且表现得非常好。在这项作业中,打破了6至7米直径范围内的多项世界纪录,包括“最高日掘进”(124.9米)、“最高周掘进”(515.1米)和“最高月掘进”(1,754米)。整个项目中,隧道掘进机将计划开挖超过40公里长的隧道。
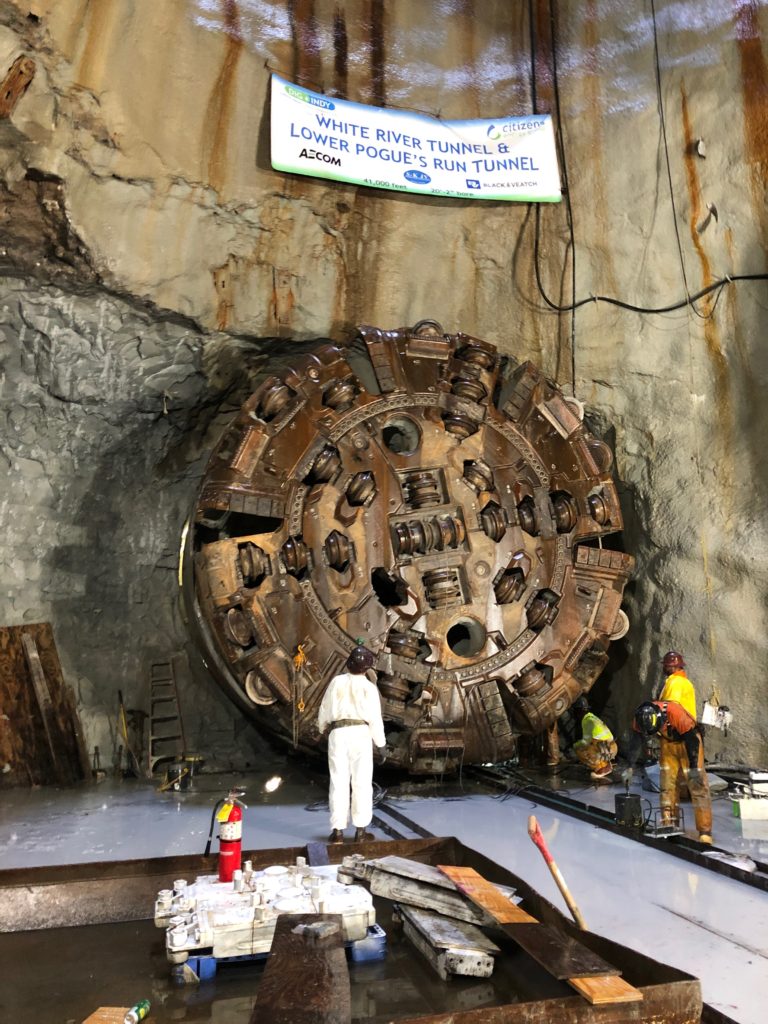
作为迪津迪隧道系统的一部分,罗宾斯主梁式掘进机完成了两个隧道的掘进任务
尼泊尔巴瑞巴贝引水综合项目
2019年4月16日,尼泊尔总理和其他政府官员、承包商COVEC以及罗宾斯齐聚一堂,共同庆祝尼泊尔国家骄傲工程—巴瑞巴贝引水隧道的贯通。这台罗宾斯掘进机不单是首台在尼泊尔国内使用的全断面掘进机,更是全球史上第一台穿越喜马拉雅山脉的全断面双护盾硬岩掘进机。在月掘进超过1,000米的表现下,这台设备比计划提前了7个多月完成掘进。

罗宾斯直径5.09米的双护盾硬岩掘进机穿过砂岩和泥岩,在18个月内完成12.2公里长的行程
2019年4月18日,两台直径6.65米罗宾斯跨模式掘进机 (XRE)中的第一台在孟买地铁三号线上首次实现了中段贯通。这台设备完成了从克夫普瑞(Cuffe Parade)到维旦巴文(Vidhan Bhawan)站长1.2公里的隧道挖掘后,现在也已经准备就绪开始挖掘长2.8公里的第二段隧道。
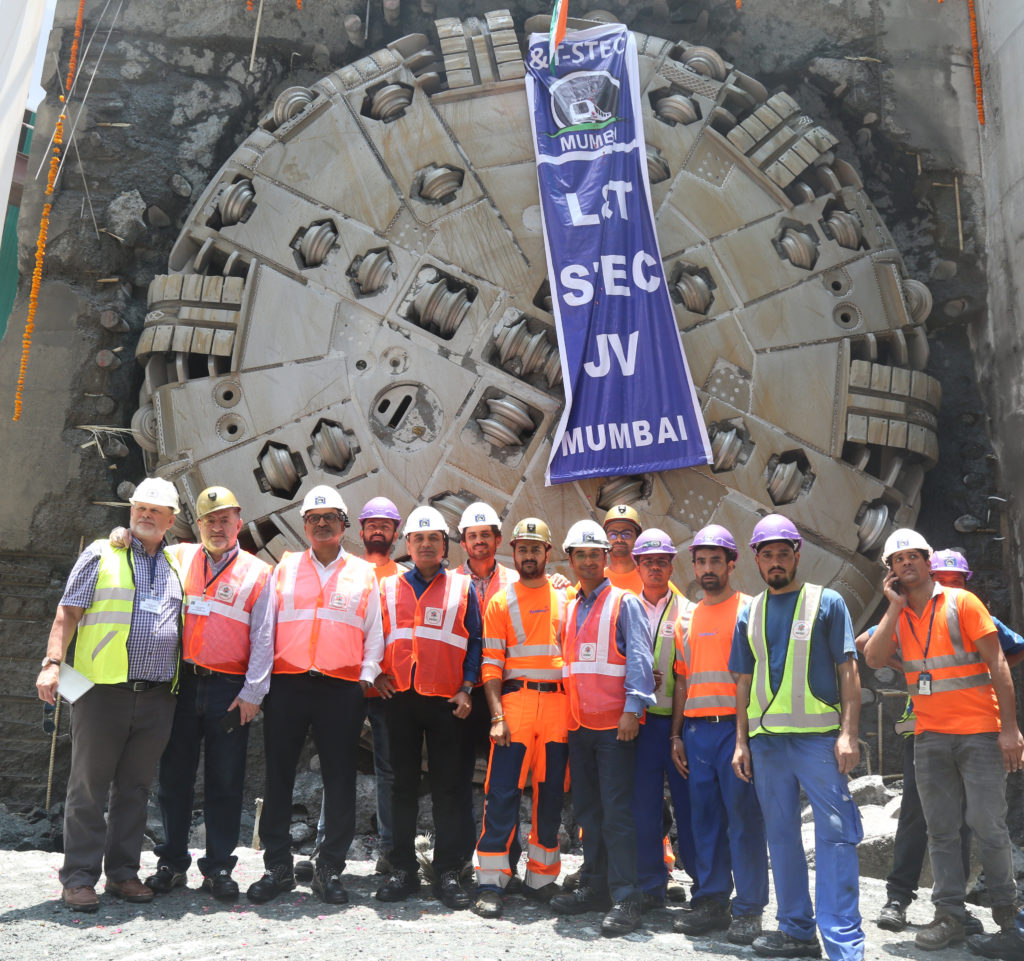
承包商Larsen&Toubro和上海隧道工程公司合资企业(L&T-STEC JV)于4月18日与罗宾斯人员共同庆祝跨模式掘进机的贯通
2019年4月25日,直径4.56米的罗宾斯双护盾掘进机完成了为智利毛利地区(Maule)秃鹰水力发电项目(Los Condores HEPP)建造的一条长12公里的引水隧道。承包商Ferrovial Agroman克服了高埋深混合岩土和高涌水的困难地质条件贯通了隧道。第二台直径4.56米的罗宾斯跨模式掘进机(XRE)将在今年晚些时候开挖另一段隧道
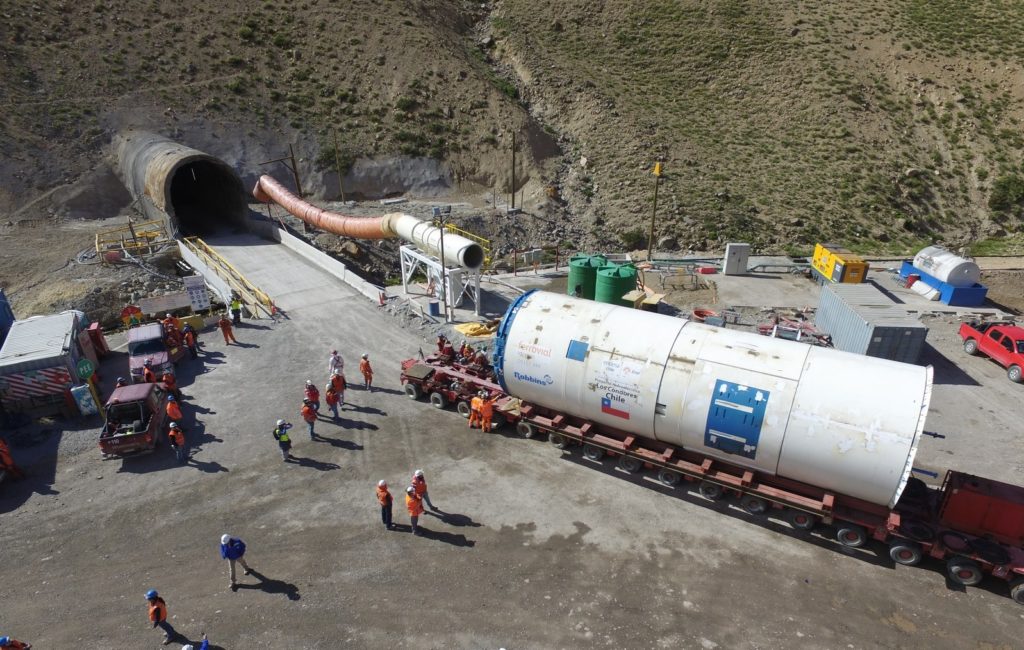
4月25日完成12公里引水隧道的罗宾斯双护盾掘进机始发时的情景
跨模式掘进三维动画: 罗宾斯跨模式掘进机XRE
罗宾斯跨模式隧道掘进机是世界上最具挑战性的隧道项目的适应性解决方案。这个视频解释了罗宾隧跨模式掘进机XRE,一个兼并的硬岩和土压平衡开挖模式的掘进机,为什么他们是在世界各地解决混合地质隧道的最佳方案。
罗宾斯盾构机和输送机完成复杂的TEO第五标段
2019年2月28日举行了一场仪式,以庆祝在软土和硬岩历经考验的设备的贯通。直径为8.93米的罗宾斯盾构机和连续输送机系统完成了复杂的伊米苏. 奥连特隧道(Emisor Oriente,简称TEO)中最困难的一段隧道,这条长达62公里的长管道将为2120万的墨西哥城居民改造废水处理。
6公里长的第五标段是TEO隧道的六个地段中的一个,需要罗宾斯设备从墨西哥最深的土建工程井始发,深150米,挖掘含磨蚀性玄武岩岩石的混合面地质。 “我很自豪能够成功完成隧道挖掘,因为这是这个项目埋深最深的部分,” José Adolfo Méndez Colorado,承包商Ingenieros Civiles Asociados(ICA)的工地主管说。 “罗宾斯现场服务为这个项目的成功贯通做出了重要贡献。机器操作至关重要:现场服务人员知道如何准确操作设备以获得很好的表现。他们发现问题的速度帮助减少停机时间。”
地面条件的复杂性,Méndez继续说道,需要正确的聚合物浓度和选择,这本身就是一个很大的挑战。现场服务协助了我们解决其他问题以及设备相关的操作:“螺旋输送机在混合地质下输送渣土以及铰接系统存在一些问题,这些问题通过现场服务经验得以克服。他们还知道连续输送系统的正确操作,这使我们的作业能够达到预期的表现。”
罗宾斯墨西哥公司总经理Roberto Gonzalez说:“我们为这台机器在两个截然不同的世界中的运行感到骄傲。”2011年,最初为第五标段设计的机器被提前开挖了3.9公里长的第1B标段,这是该线路的一个关键部分,需要立即投入运行,以防止长期季节性洪水。“盾构机采用输送机系统在墨西哥城粘性粘土作业中证明了自己的能力,黏土含水率非常高,高达400%。”该机器在一个月内实现了掘进高达592.5米的速度,被认为是该项目中使用的六台盾构机(其中三台为罗宾斯)中的一项最高纪录。在15个月内完成掘进后,机器被送到第五标段现场,在那里针对一段混合和岩石地质进行了改良。
改良包括一个能够承受7巴的高压工作仓、添加到螺旋输送机的碳化铬耐磨板、以及添加到刀盘上的灰色杆和重型切削刀具。
该机器在始发井底部长28米组装仓内组装,并于2014年8月投入使用,要求所有的后配套龙门架保持在地面上。两个月后的2014年10月,在推进了150米后,机器及其后配套龙门架完全组装在隧道中。一个月后,连续输送系统安装并运行。“第五标段盾构机的装配记录是墨西哥掘进机最深的装配纪录。装配工作需要ICA工程师、大容量起重机和人力资源的高度配合,以保持10周的装配进度完成,” Gonzalez说。
随着第五标段的隧道工程正式结束,在TEO线路完工之前还有一个贯通:在第四标段作业的直径8.93米罗宾斯盾构机也计划于今年春天破土动工。第三台在第三标段作业的罗宾斯盾构机在2018年已完成了隧道建设。
TEO隧道是墨西哥城100多年来因湖床排水和地下水位普遍下降而下沉的解决方案。当时,墨西哥城的建筑物、主要街道和其他建筑已经下沉超过12米,而且该地区的大部分地区很容易受到洪水的影响。与此同时,该地区的重力供水污水管道已经失去了坡度,严重不足。
隧道施工一旦竣工,TEO隧道将扩大向墨西哥谷系统增加150立方米/秒的输水量,并减轻关键区域的洪水风险。它还将把废水输送到墨西哥最大的污水处理厂。这条巨大的隧道包括24个竖井,深度从23米到150米,有通向希达尔戈州阿托尼科市的污水处理厂的出口。
罗宾斯跨模式完成土耳其最长的输水隧道
2018年12月18日,土耳其有史以来最长的引水隧道工程竣工了,这条隧道就是长31.6公里的格雷德(Gerede)引水隧道。为了贯通这条隧道,负责开挖隧道的罗宾斯直径5.56米跨模式掘进机(XRE-兼并硬岩和土压平衡作业模式)和施工商Kolin-Limak合资公司的施工队伍,克服了几十个主要断层带和高达26巴水压的高难度地质条件。这条贯通的国家首级供水线将于2019年3月投入使用。
由于土耳其首都安卡拉长期严重干旱,格雷德引水隧道成为一个迫在眉睫的引水隧道工程。格雷德引水隧道的最后一段是一条长9.0公里、地质极其困难的隧道段。地质由砂岩附聚物、石灰岩和凝灰岩组成。这条9公里的隧道段被广泛认为是土耳其隧道施工中最具挑战性的隧道。“自20世纪80年代以来,我有机会学习和参观土耳其的大部分机械化隧道工程。格雷德引水项目是其中最具挑战性的项目之一。”伊斯坦布尔技术大学矿山与隧道机械化教授、土耳其隧道学会主席Nuh Bilgin博士说。
在罗宾斯公司参与这个项目之前,其他的掘进机制造商提供了三台标准双护盾硬岩掘进机试图攻克隧道,但其中两台在遇到大量淤泥、碎岩和涌水后被困在隧道里无法挽救,隧道处于停滞状态。鉴于意外的困难地质条件,施工商Kolin-Limak合资公司制定新战略,联系了罗宾斯公司。罗宾斯提议采用跨模式(XRE)掘进机开挖这段困难的隧道段。 “跨模式掘进机在整个项目施工中,为应对经常变化的地质条件提供了极大地便利性和灵活性。掘进机同时配备了增加推力、双速减速箱和标准螺旋输送机等功能。让我们贯通隧道实现目标最重要的关键点是,设备能够应对在不同地质条件下的开挖作业。” Kolin-Limak合资公司项目经理Barış Duman说道。
罗宾斯土耳其代表处负责人Yunus Alpagut说:“对我们来说,最具挑战性的是设计和制造出可以完成格雷德隧道这段困难隧道段开挖工作的掘进机,而其他两个竞争对手的掘进机也失败了。” 20巴的静态水压,这是标准双护盾掘进机不具备的应急保护性能 。掘进机设计采用可转换刀盘,便于在硬岩和土压平衡掘进模式之间进行转换,并且刀座可以安装滚刀或盾构碳化钨刀具。为了应对困难的地质,这台掘进机还配备扭矩切换系统,双速减速器使设备能够在土压平衡或硬岩模式下灵活作业。这个功能通过添加一级减速器来实现——重型小齿轮和大齿轮可在低速作业时提供高扭矩,使机器能够顺利穿过断层地带和复合软土地段,不会被困。
2016年春季,施工人员在其中一台被困双护盾掘进机的一侧开挖了一条旁路隧道后,这台跨模式掘进机就在这个地下装配室进行组装。这个地下装配室让设备可以在隧道内采用现场首次安装调试方案(OFTA)来实现组装。“把设备部件运送到既有隧道里是最具挑战性的。装配室距隧道入口7公里。159加仑/秒的涌水让物料运送到设备变得十分困难。”罗宾斯现场服务经理Glen Maynard说。
尽管面临挑战,但设备仍然在2016年的夏天顺利始发掘进,并且在最初的50米掘进就成功穿越了原来被困双护盾掘进机的隧道段。设备需要采用土压平衡模式作业,来应对水压高达26巴和含有冲积层、流动土层、粘土的地质,共48个断层带;通过尾盾预留的超前钻孔排出地下水来降低水压,钻孔配有常闭球阀;定期采用超前钻探进行探测地质,以便顺利通过困难地质。
“我们遇到许多具有挑战性的区域,如高达26巴的高压突涌水和含有冲积物的断层带。地压力作用在盾体导致盾体在粘土地质中受到挤压变形。在这些困难区域,我们能够通过将掘进机的掘进速度、刀盘转速和螺旋输送机转速保持在理想水平来实现快速开挖。最后,我们认为我们选择跨模式掘进机的决定是非常正确的。” Duman 继续说道。
随着隧道的贯通,这条供水隧道也将于2019年3月投入使用。这条格雷德隧道将会把从格雷德河的水引入卡里德瑞大坝(Çamlıdere Dam),为安卡拉市的供水系统提供饮用水。
免费网络研讨会:如何加快隧道掘进
快速挖掘被许多人认为是隧道掘进机的最终目标,它可以可靠地按时(或提前)完成项目,无论条件如何,都能以更快的推进速度完成项目。然而,加快项目进度并不像推动机器、延长工作时间或增加人员规模那么简单。必须考虑整个项目进度,从最初的调查到设计过程。
罗宾斯设计总监Brad Grothen和Elisa Comis(McMillen Jacobs的合伙人)在这篇简洁、免费的40分钟演讲中,分享了快速挖掘在该领域的实际情况,包括掘进设计的案例研究和项目调度的实际示例。
快速开挖7个关键点的简史
Rapid Excavation: It’s a term bandied about throughout our industry, but what does it mean? It’s considered by many to be the ultimate goal in TBM tunneling—machines that reliably complete projects on time (or early) with faster rates of excavation, regardless of conditions. However, speeding up a project schedule is not as straightforward as pushing a machine harder, working longer hours, or increasing your crew size. The issue is complex, and we’ve put together 7 key points to help you navigate it.
1. Consider the Entire Project Schedule
First of all, consider that increasing the excavation rate may not be the only way—and indeed may not be the best way—to speed up a project schedule. The generalized graphic below illustrates my point: TBM excavation often makes up around 25% or less of the total time to complete a public works tunnel. In fact this is a conservative value as by many estimations the total project time is often 15 years. Even if we were to increase the excavation rate by several times what TBMs are currently capable of, it wouldn’t significantly speed up project delivery.
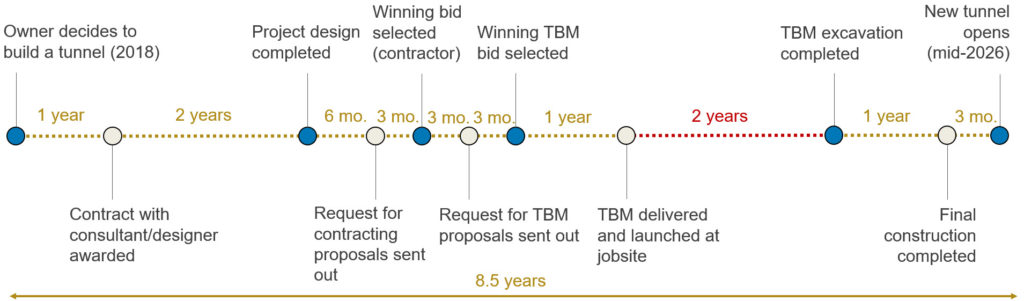
Figure 1. Generalized process of delivering a public works tunnel. TBM excavation show in red.
Shortening the decision-making process or the design and consulting process is much more feasible than creating a “super-fast TBM” and would have a bigger impact on the project schedule as well.
2. Know the Facts about TBMs
TBMs are fast, and they’ve been fast for decades. In fact, 50% of all known TBM world records were set more than two decades ago. Much of the seeming lack of progress is illusory–it has to do with the fact that modern tunnels are being built in ever more difficult geology, while more stringent health and safety standards put necessary limits on the excavation process, among other things. Today’s TBMs are capable of boring in harder rock, in higher water pressures, in mixed ground conditions and a host of other environments that would have been impossible in the 1970s and 1980s. And they do it while performing well; indeed, at much higher rates than conventional excavation. The below chart is a good illustration of just how far TBMs have come in recent years.
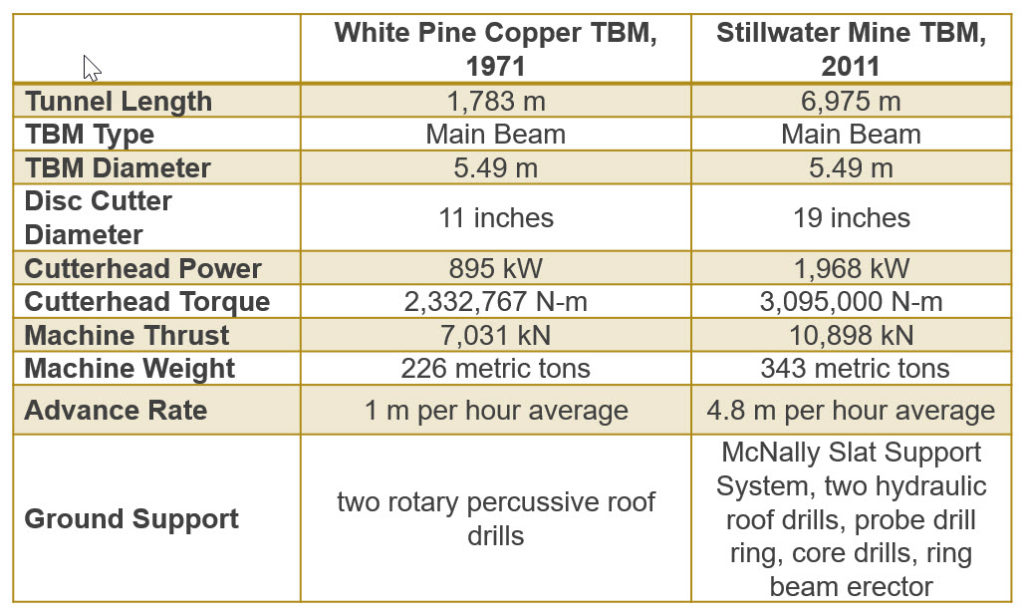
Figure 2. The long way that TBMs have come since the 1970s.
3. Know That Productivity Has Vastly Improved
There have been some recent articles looking at decreasing productivity in the construction industry overall, such as this article in The Economist. While the productivity of the overall construction industry is up for debate, productivity is not decreasing in the tunneling industry. Moreover, productivity is incredibly reliant on each project’s limitations and requirements. When considering productivity, think about logistics, geology, and data.
Based on decades of field data, we’ve found that a typical TBM heading is two to three times faster than a drill & blast heading. This effect is more pronounced the longer the tunnel drive, and more than makes up for the typically longer lead time to acquire and mobilize a TBM.
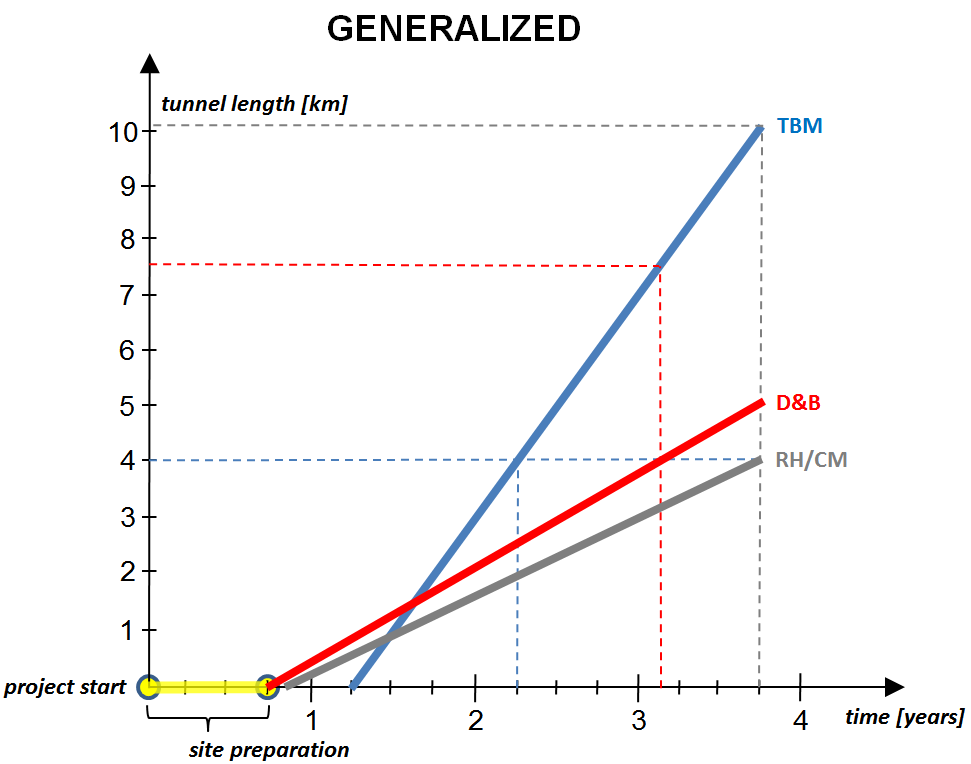
Figure 3. TBMs are two to three times faster on average than drill & blast and multiple times faster than a roadheader.
So it’s safe to say that TBMs are the way to go for more productive tunneling in all but the shortest tunnels. Logistics is the other key: scheduling of crew and materials, particularly in long tunnels, is so important. This is doubly so if using muck cars. For this reason, using continuous conveyors for muck removal is more efficient, as the removal process does not need to stop for personnel and material movements. In fact at least 75% of all TBM world records were set while using a continuous conveyor for muck removal.
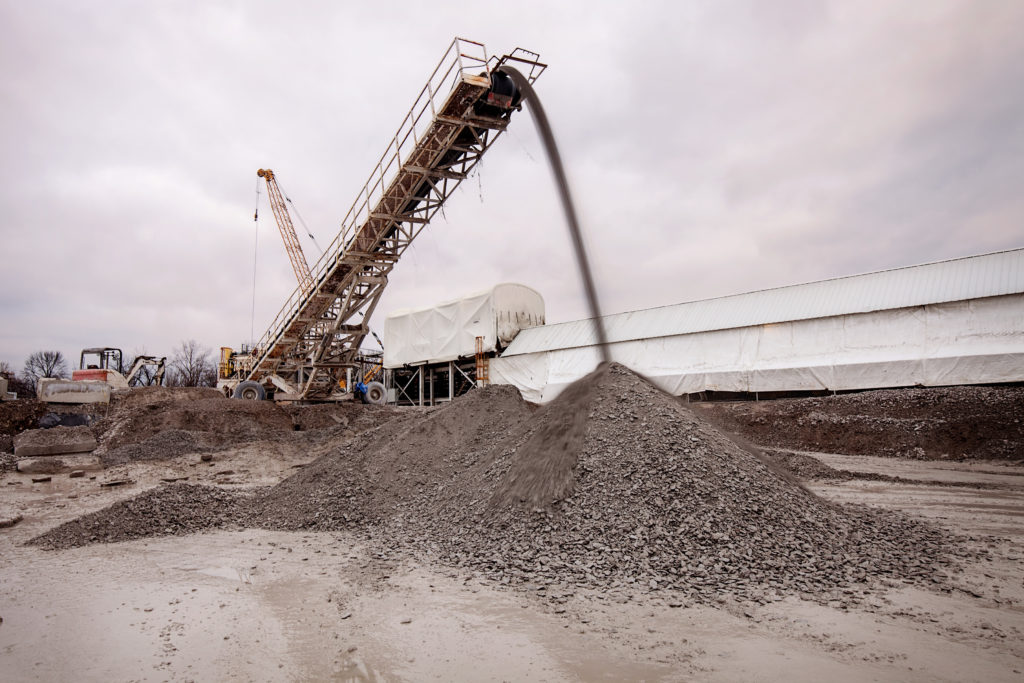
Figure 4. Today’s conveyors are capable of hauling 1,800 metric tons per hour or more.
Lastly, consider geology when planning the construction schedule. Even a customized machine with streamlined logistics will bore more slowly in fractured volcanic rock with significant fault zones than in competent sandstone. Setting the excavation schedule requires a close look at geology and the excavation rates of recent projects in those conditions.
4. Identify the Bottlenecks
The bottlenecks must be identified and alleviated if productivity is to be increased. Think about the operations that can be done simultaneous with boring that are now done separately:
- Applying a Concrete Lining: Continuous concrete lining can be done concurrent with boring in many cases. This type of lining eliminates the separate operation of lining a tunnel with segments. Waterproofing membrane can be applied with a membrane gantry if needed
- Increasing Automation: Processes such as cutter changes and segment erection can and are being fully automated on research projects in the industry. Full automation could significantly reduce downtime
- Eliminate re-grip time: When setting segments and thrusting off rings, elimination of re-grip time could be key to increasing advance rates. New innovations such as helical segments are promising to do this through a simple change in segment architecture
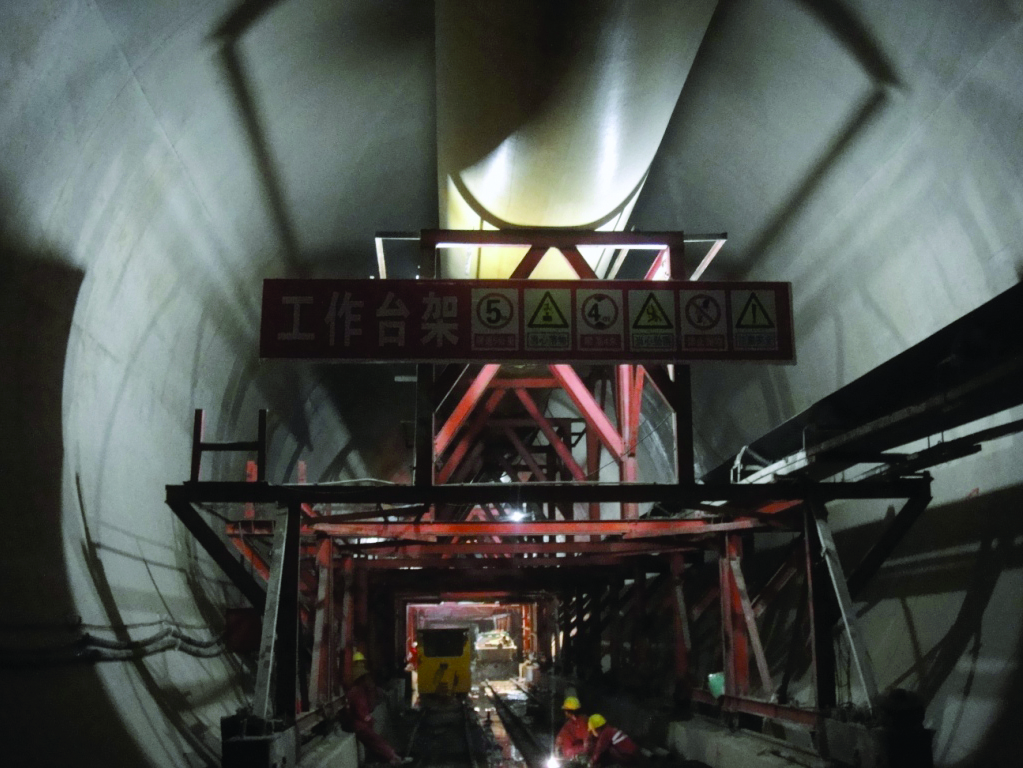
Figure 5. Continuous concrete lining applied behind a Main Beam TBM.
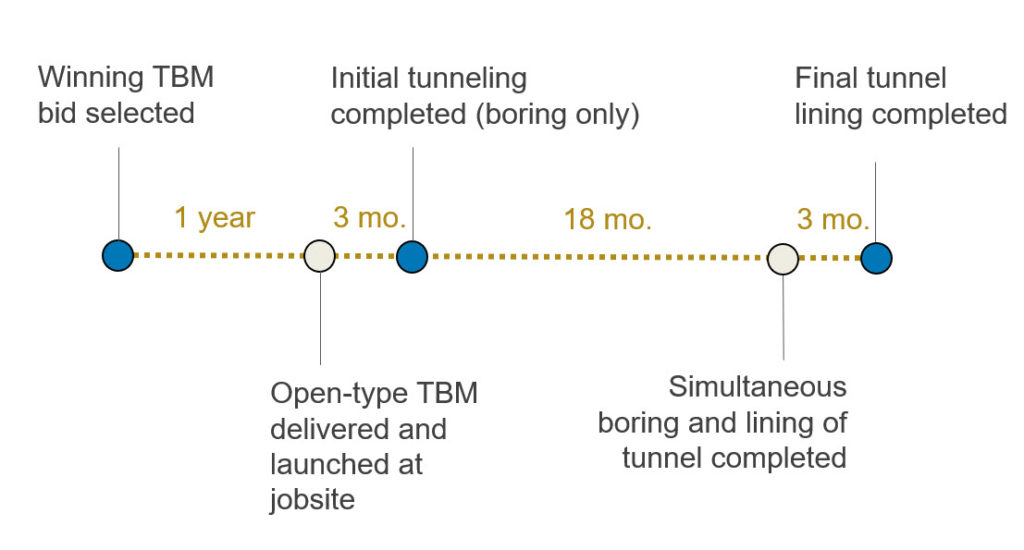
Figure 6. By boring and lining the tunnel simultaneously with a final, continuous concrete liner, a substantial amount of time—perhaps six months—could be shaved off of the excavation schedule (as compared to previous example that showed two years’ excavation time).
5. Understand the Limitations
There has been talk in our industry of making TBMs excavate up to ten times faster. While this is all well and good to aim for, in many cases it may not be realistic. For example, when boring in soft ground using EPB TBMs the penetration rate is limited by material flow and additive permeation. Boring at faster rates could cause heave in front of the TBM followed by subsidence at the surface.
So how could we bore faster in softer ground? It would require a change in the mechanism of excavation—no short order. It would require a better way of holding pressure than the screw conveyor can currently achieve. This is just one of many examples where physical limitations are the barrier to speed, not efficiency.
6. Think Outside the Circle
The possibilities for tunnel construction in the future are intriguing. Consider non-circular tunneling machines, of rectangular, square or other shapes. How much efficiency could be gained by creating a tunnel that requires no back-filling or invert segments to create a flat tunnel invert? Robbins has been exploring these types of machines for decades, with machines such as the Mobile Miner, seen here.
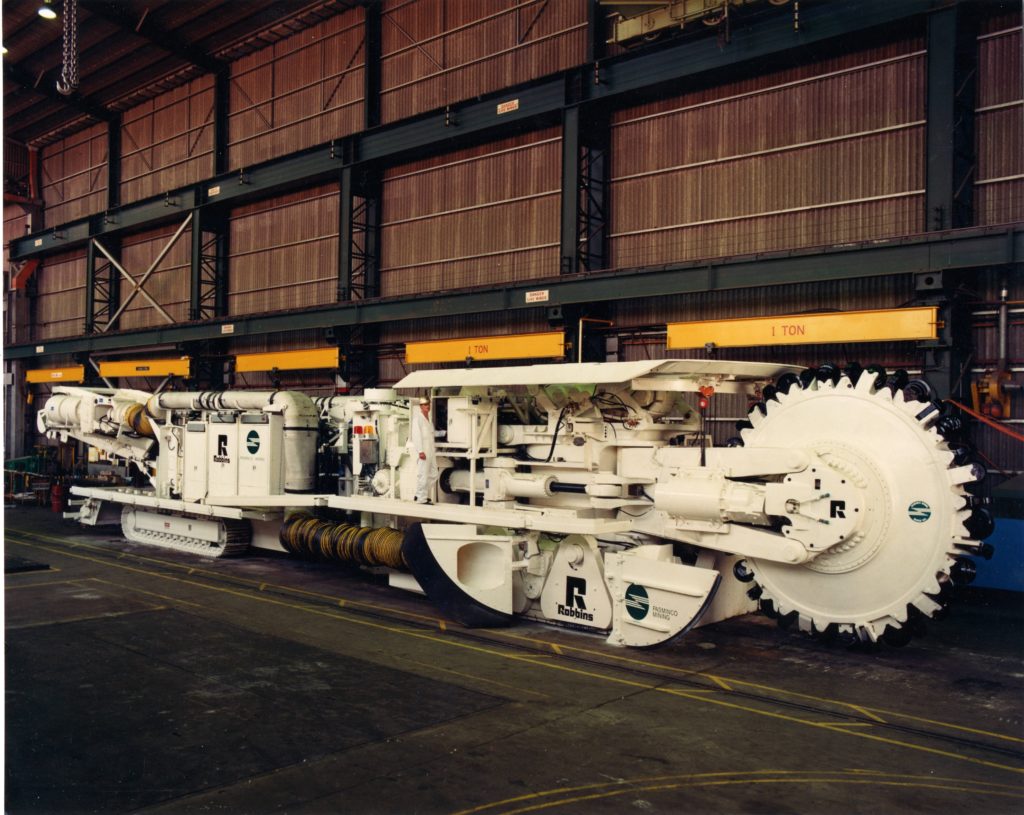
Figure 7. The Mobile Miner was developed in years past to bore non-circular tunnels.
7. Promote Industry R&D
Lastly, there are things all of us in the industry can do to advance technology towards faster and safer tunneling. R&D in our industry is necessarily incremental as technology must be tested for safety and efficacy. But the rate of advancements could be sped up with better funding and closer cooperation between owners, consultants, contractors and TBM suppliers.