Author: Keri Lin
连续输送机在盾构机上的应用
免费网络研讨会: 了解您前方面对的是什么。
无论挑战是深埋深、挤压地质、断层带还是涌水,您的项目都必须继续前进。新的地面调查和处理方案可以为您提供工具,以克服您所面临的问题,同时最大限度地提高掘进机性能和安全性。
在这场免费的60分钟网络研讨会上,罗宾斯首席工程师Dennis Ofiara将讨论困难的地质解决方案(DGS),这是一套可用于盾式硬岩石和跨模式掘进机的选项,可使机器在长隧道、深埋深和具有挑战性的地质特征中移动。DGS是关于可视化的:机器的盾体不必阻挡你对周围地面的观察。有了360度长距离超前钻机、收敛测量传感器(提醒操作员挤压地质)和拱顶钻机(用于加固地质)等一系列功能,您可以清楚知道下一个冲程您会遇到什么挑战。
点击观看视频
罗宾斯单护盾参与修复世界最长隧道
罗宾斯已经完成了一台独特的隧道掘进机机的制造和测试,该设备将用于修复世界上最长的连续隧道。掘进机将用于翻修纽约市特拉华渡槽的一段,这是一条长137公里的隧道,每天提供约50%的城市饮用水。在2月份的两天时间里,来自业主纽约环境保护部(NYDEP)、咨询公司麦克米伦·雅各布斯(McMillen Jacobs,简称MJ)和合资公司承包商基威特·谢赫(Kiewit-Shea Constructors,简称KSC)的代表前往俄亥俄州索隆的罗宾斯工厂,见证这台定制掘进机的工厂验收测试。
罗宾斯单护盾隧道掘进机将开挖一条隧道,以取代3.8公里长的特拉华渡槽。特拉华渡槽目前每天向哈德逊河泄漏约7500万升的水。对特拉华渡槽的调查可以追溯到十多年前,发现隧道衬砌出现裂缝。虽然使用自动水下运载工具进行的几次检查表明这些裂缝是稳定的,但确定它们不能从现有隧道内修复。纽约市随后决定在河下修建一条新的隧道以绕过渗漏。
径为6.8 米的单护盾硬岩掘进机,以安全密封压力高达30巴,并在各种坚硬岩石条件下运行。特拉华渡槽于1944年完工。在最初的施工过程中,工作人员记录了每天75至1500万升的地下水流入量。由于这段隧道位于哈德逊河(Hudson River)下方183 米处,因此,流入的水受到巨大的水头压力,因此需要独特的隧道技术。
由于渡槽修复所带来的挑战,例如地质困难和大量的水涌入,因此必须相应地设计掘进机。困难的地质解决方案(DGS)功能,包括强大的钻机、注浆和涌水控制系统已纳入机器的设计中,以克服预期的挑战。“这种隧道掘进机的一个独特特点是可关闭的铲斗,这使得铲斗仓可以被封闭,” KSC隧道经理Niels Kofoed说。“我们预计,如果隧道开挖部分的地下水流量(分流)导致环空注浆冲刷,这将是一个关键特征。一旦隔离墙关闭,地下水流停止,可对预制衬砌进行二次注浆,有效切断分流水流的流动路径。”
罗宾斯项目经理Martino Scialpi进一步指出,“掘进机的设计排水能力为9500升/分钟。机器在盾体中配备两个钻机,用于在16个不同位置钻探,在管片安装器上配备第三个钻机,用于在盾体另外14个位置钻探。钻探和开挖前灌浆将是控制和减少水流入的常规工作。“此外,水力驱动的高压下孔锤将允许,在需要的时候,可以在机器前方60至100 米、高达20巴压力下钻探。
为了提供始发和回收隧道设备的通道,在纽约纽堡和瓦平格镇建造了两个深井,两个深井将是旁通隧道的入口和出口。由于可用空间有限,项目现场本身对设备的组装和始发也构成了挑战。
罗宾斯与KSC密切合作,确保设备部件的设计和尺寸,以便所有部件都能用承包商的起重机可以承受,并安放在270米深的窄窄的洞室里。机器组装完成后,预计将于2017年秋季开始掘进。
从风险规避到风险降低:伊隆·馬斯克如何开创隧道掘进的新纪元
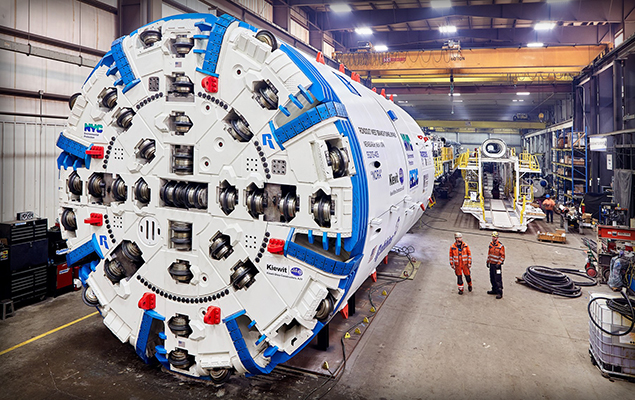
Tunnel boring machines like the one here, for New York’s Delaware Aqueduct Repair, are turning risk aversion on its head.
It has been some time since I have written on the Robbins blog page, but I am inspired to do so by the announcement that Elon Musk is entering our business—the tunnel boring business. It is great to see people with a vision of an improved world enter our industry. I agree with Musk that the advance rate of tunnels can be significantly improved if development money comes into the industry. Development money in tunneling, however, is at best minimal and is more often essentially nonexistent. Nearly all tunnels are heavily specified to avoid risk taking by owners (therefore discouraging new development). Nearly all tunnels go to the low bidder and low bidders try to buy the TBMs at the lowest price; a further discouragement of development. The industry has therefore been slow to improve advance rates, but with Musk bringing the issue into the spotlight, perhaps things will change.
Risk Aversion and How to Reverse it
There are some exceptions to this practice of risk aversion for new technology, and one is the Delaware Aqueduct Repair. This tunnel corrects heavy water leakage occurring from the 1940’s-built aqueduct tunnel for New York City. We are just completing Factory Acceptance in our plant in Solon, Ohio of this unique Single Shield TBM. The tunnel is at significant depth (approximately 300 m / 900 ft) with the distinct possibility of encountering very high water pressure (up to 30 bars). The contractor JV of Kiewit/Shea have shown their willingness to move forward with several new developments for this project. The concept of grouting off high water pressure as the primary means to allow advance in such conditions, rather than use an EPB or Slurry TBM, is in my view a significant step forward for our industry. Granted there have been halfway attempts with a combination of grouting and pressurized tunneling at recent projects like the Arrowhead Tunnels and Lake Mead Intake No. 3, but these have come at high cost and sometimes long delays. The Delaware Aqueduct TBM, by contrast, is designed to hold up to 30 bars of pressure while grouting occurs. Boring and cutter changes are done in atmospheric pressure.
Chemical grouting and grouting technology in general have advanced multifold in recent years, and it is commendable to see it used extensively on several aspects of the Delaware Aqueduct Project. It’s a great example of what can be done when a contractor is willing to use new technology to address potential risks—it appears it can actually reduce risk in the long run. It is a great honor to be working with the capable Kiewit/Shea JV team to be a part of advancing technology.
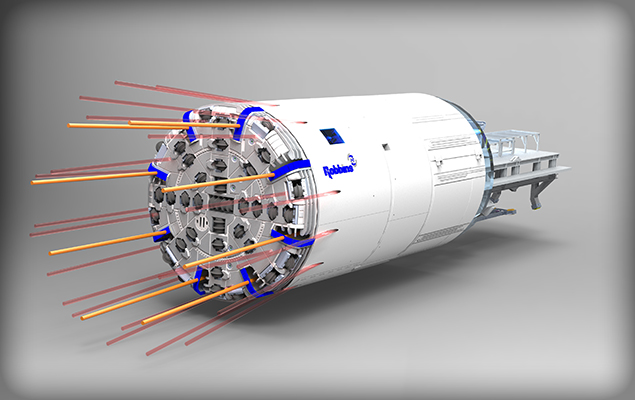
The enhanced probe drilling and grouting capabilities as seen in trajectories (orange and red) on the Delaware Aqueduct TBM 3D model.
Areas Ripe for Change
The Delaware Aqueduct Repair project is a flagship project for what I hope will become more common in the industry: instead of low bidding with the cheapest possible machine, offering a reasonable bid with a specialized TBM that has a higher initial investment, but ultimately a lower cost overall. The project’s use of technology is wide-reaching, particularly atmospheric cutter changes and chemical grouting, which have the potential to reduce downtime and increase safety. I do not see the future of rock tunneling under high water pressure being left to divers to change cutters and repair the cutterhead. We all know it is not cost effective to send divers to work in confined spaces over 10 bars. It should be noted that the long-duration Hallandsås Tunnel, for example, finished the majority of its TBM advance by relying on effectively this technique of grouting and advance after failing with a Slurry System. There are lots of tunnels to be built with above 10 bars pressure that will use this technology. The industry needs to automate cutter and bit changes as much as possible, and increase the integration of chemical grouting in tunneling.
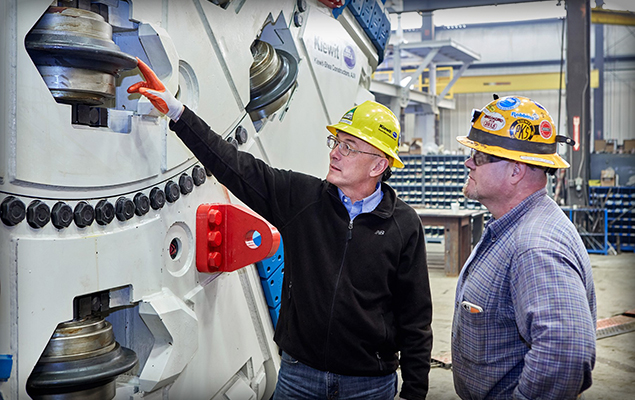
Niels Kofoed and Danny Smith of contractor Kiewit examine the cutterhead and cutters of the Delaware Aqueduct TBM. The machine can bore and cutters can be changed at atmospheric pressure.
Certainly there are many areas for advancement in our industry, and major public figures like Musk drawing attention to it is ultimately a good thing. After all, getting the general public to think about solving traffic by going underground is no easy feat. Even more so, getting the tunneling industry to think about its own risk-averse practices has a big potential benefit. Hopefully all of this attention will result in more tunnels, more business, and better infrastructure. Musk’s willingness to take a risk aimed at making the underground construction industry potentially faster and more stable is a good bet to take.
罗宾斯双护盾在安第斯山脉下掘进
智利的秃鹰水电站(Los Condores)是一个高深埋、坚硬岩石的挑战,隧道上方有500米的岩石,海拔2,500米的高空作业现场。截至2017年1月,直径4.56 米双护盾隧道掘进机已完成900米长的进水口隧道的开挖,并正在顺利进行引水隧道第一段的开挖工作。该机器于2016年5月27日开始其旅程,自那时起,已总共挖掘1,300米以上的隧道。
机器启动的过程非常艰难,需要在未铺路面的山区道路上运输掘进机部件和车辆。承包商Ferrovial Agroman负责秃鹰水电站项目的进水口隧道,并充分意识到与机器始发相关的挑战:“工作地点是由于其崎岖的地形和安第斯山脉的地理位置,这是一个很大的限制。由于这些挑战,我们迫切希望以高效的方式开展工作,”Ferrovial Agroman的隧道生产经理Pello Idigoras说。
该工地位于智利圣地亚哥以南360公里,是一个新的150兆瓦发电厂和进水口隧道的一部分。罗宾斯双护盾掘进机正在对两段进水口隧道进行开挖,第一段长度为6公里,第二段长度为4.4公里)。两条隧道之间的一段将通过机械掘进和爆破进行开挖,以连接两条隧道,使进水口隧道的长度约为12公里。该项目增加了该国的能源生产,从而有助于全面改善该国公民的福利,” Idigoras说,已完成的水电项目将对周边地区产生影响。
该隧道位于智利莫勒山区,目前正在两种岩石中掘进:沉积岩和火山岩。岩石在强度高达100兆帕的下进行了测试,其中至少有两个断层带,第一个断层带已经在流纹岩、安山岩、凝灰岩和角砾岩中穿过。对于Idigoras,条件非常适合双护盾隧道掘进机:“我们有质量良好的中硬岩石,适合采用双护盾开挖。”他说。尽管如此,一些具有挑战性的领域仍然存在。为了应对这些条件,包括稳步增加水流入率高达3500 升/分钟,承包商正在使用水泥灌浆和化学灌浆聚氨酯和泡沫。预计会采用此类地质处理技术,罗宾斯双护盾旨在有效应用这些技术。
随着隧道掘进机的开挖,隧道采用250 毫米厚、1.2 米长的混凝土管片,采用4+1布置。这台机器目前正在以每20小时掘进25个环的速度进行。工作人员分两个10小时轮班,一个4小时轮班专门负责维护。Idigoras 认为隧道掘进机的性能和入口隧道的完工视为巨大的项目里程碑,尽管还有很多工作要做。”经过数月的工程、制造、安装和调试,我们很高兴看到这个结果。到目前为止,不可能说出所有参与该项目的人的名字,但作为一个整体,他们已经设法使掘进机开始挖掘和钻井。”
免费网络研讨会: 拥有一台掘进机的总成本?
Subject: What is the Total Cost of Owning a TBM?
Date: September 24, 2015
Time: 07:00 PST, 10:00 EST, 15:00 BST
Hosted By: Robbins
Register Now, Limited Spaces Available!
Tunnel Boring Machines exist today that have excavated over 50 km (31 mi) of tunnel, and have been in operation for nearly 50 years. These workhorses have been built and rebuilt to satisfy requirements of various tunnels while their durable steel structure endures.
Today’s underground construction contractors often face a higher capital cost during the initial investment for a TBM, but what is the total cost of owning a TBM? Much more than the initial price tag must be taken into account: while a heavier TBM with durable steel structure may cost more initially, reusing it on multiple tunnels will ultimately result in substantial savings. Paying for a custom-designed machine often results in increased efficiency and faster advance rates, with the end result that the tunnel is completed on or even ahead of schedule.
In this complimentary 60-minute webinar, Robbins Vice President-Sales Doug Harding will explore the true cost of owning a TBM, considering the entire lifespan of the machine. He will draw on real project data and cost estimates to demonstrate that a machine designed for multiple tunnels will pay for itself over time.
We invite you to submit your questions beforehand webinars@robbinstbm.com to get a thoughtful and well-researched answer from Doug during the Q&A session at the end of the webinar.
跨越式掘进机贯通澳洲格罗夫纳煤矿斜井隧道
这段视频展示了罗宾斯跨模式掘进机在澳大利亚莫兰巴为格罗夫纳煤矿贯通斜井隧道。
免费网络研讨会: 采用机械化掘进机技术加速您的采矿步伐
Subject: Fast-Track Your Mine with Proven TBM Technology
Date: June 24, 2015
Time: 13:00 PST, 16:00 EST, 06:00 AEST
Hosted By: Robbins
Register Now, Limited Spaces Available!
Second Option: Pre-Recorded Broadcast
Date: June 25, 2015
Time: 07:00 PST, 10:00 EST, 15:00 BST, 16:00 CEST
Hosted By: Robbins
Register Now, Limited Spaces Available!
Today’s mine development projects are no longer being done from the surface. Worldwide, easily accessible ore deposits have been spent, requiring mines to aim for deeper ore bodies, often kilometers underground, to keep operations viable.
This changing mine environment brings a need for access tunnels, first to reach the ore, then to provide long-term muck haulage. Tunnel boring machines provide efficient, safe, and fast access to those ore bodies. Mines around the world are accustomed to methods such as drill & blast, roadheader, and other types of conventional excavation. However, TBMs have been proven on multiple projects to complete tunnels two to three times faster than drill and blast; when considering roadheaders that number is often 10 times faster.
In this complimentary 60-minute webinar, Ryan Gratias, Project Engineer at Robbins and Adam Foulstone, General Manager-Grosvenor for mining company Anglo American, will discuss the changing face of the worldwide mining industry. From machine design to application and real-world examples, Gratias will prove that early adopters of the TBM method will be able to better meet increased demand and extend the life of their mine. Foulstone will discuss the recent use of a Crossover (XRE) TBM at the Grosvenor Decline Tunnel in Australia™ wildly successful use of a TBM that resulted in access tunnels bored 14 times faster than the traditionally-used roadheader method.
We invite you to submit your questions beforehand to webinars@robbinstbm.com to get a well-researched answer during the Q&A session at the end of the webinar.
免费网络研讨会: 总统Lok Home告诉您一个驱散的神话
Subject: A Myth Dispelled: In Difficult Ground, the Time for Drill & Blast Excavation has Passed
Date: April 15, 2015
Time: 10:00 AM EST, 2:00 PM GMT, 2:00 PM WEST
Hosted By: Robbins
Register Now, Limited Spaces Available!
In the modern-day tunneling industry, one outdated perception remains: Traditional, tested methods are always the best. When presented with difficult ground””from fault zones to water inflows to mixed face conditions””many consultants and contractors rely on decades-old field studies and conclude that conventional excavation methods like drill and blast are the best option. With today’s Tunnel Boring Machine (TBM) technology, this assumption couldn’t be further from the truth. Modern TBMs are highly adaptable and capable of offering all of the same ground support and excavation capabilities of their conventional counterparts””most often with a safer setup and faster performance, not to mention at a lower overall cost.
In this complimentary 60-minute webinar, Robbins President Lok Home will analyze recent tunneling projects in difficult ground conditions where TBMs have proven their worth, including Turkey’s Kargi Kizilirmak Hydroelectric Project and Peru’s Olmos Trans-Andean Tunnel. At Kargi, a shielded hard rock TBM overcame incredibly difficult mixed face conditions with the help of in-tunnel machine modifications””ultimately completing the tunnel at an advance rate more than twice that of a drill and blast operation proceeding from the opposite end of the tunnel. At Olmos, the world’s second deepest civil works tunnel, a TBM ultimately succeeded at boring where drill and blast had failed: below 2,000 m of volatile volcanic rock in the Andes Mountains.
We invite you to submit your questions beforehand to marketing@robbinstbm.com to get a well-researched answer during the Q&A session at the end of the webinar.
罗宾斯主梁式为挪威隧道业立下里程碑
了解罗宾斯主梁式如何为挪威Røssåga 水电项目贯通1条7.4公里的隧道,写下20年来,第一台全断面隧道掘进机在挪威贯通隧道的历史。观看现场访谈,深入了解机器在异常坚硬、磨蚀性岩石和偏远现场条件下的作业性能,以及挪威采用机械化掘进机开挖隧道的未来。
最近要闻
- Overcoming Mountainous Geology at Nepal's Sunkoshi Marin Project
- Unprecedented Diameter Change: The Mill Creek Tunnel
- Mine Development Machine: Successful Rectangular Rock Bore in Fresnillo, Mexico
- Encountering Caverns in France: TBM Tunneling in Karst Conditions
- 48 Fault Zones and 26 Bar Pressure: Boring Turkey's Gerede Water Transmission Tunnel