Author: Keri Lin
“Namaste”尼泊尔:我如何学会慢生活,感恩隧道
In Nepal, the greeting ‘Namaste’, while pressing both palms together in front of the chest, signifies both ‘hello’ and ‘goodbye’. It implies a circular concept of time that I rather like—I certainly think I will be coming back to this country of high mountains, valley forests, and yes, tunnels.
The Adventure Begins
When I first learned that I would be visiting Nepal to see a swift-moving tunnel project making an impact in a local community, I was pretty jazzed. I also took it upon myself to overpack. The Bheri Babai Diversion Multipurpose Project (or BBDMP for short) is a 12 km long tunnel that travels below protected forest considered part of the Bardia National Wildlife Reserve. This is an area home to tigers, rhinos, Asian elephants, leopards, and more. And, most worryingly for me, mosquitoes.

The BBDMP portal. Note the trees: perfect mosquito territory.
Mosquitoes love me. I’m not entirely sure why they love me so much, but let’s just say that if there’s a mosquito within a 2 km radius it will find me. Thus, I decided to be prudent and go all out when packing. I purchased a whole new set of safari clothes, the most potent bug spray I could find in copious amounts, and much, much more. I stuffed everything into two suitcases and set off on my journey.
A full 24 hours of traveling later (the journey from Seattle, USA to Kathmandu is no joke, folks), and I arrived in the Kathmandu airport…with no checked luggage. Through a gross miscalculation (what a way to learn a lesson!) I also had not packed hardly anything in my carry-on bag. I had no clothing with me, and more importantly, no bug spray. What was I to do?
Rolling with It
After discovering that my bags were several days away, I decided to forego any hope of reuniting with them during my trip. Instead, I rolled with it. After a one-hour local flight from Kathmandu to Nepalgunj, we arrived at our destination. Nepalgunj is a frenetic, dusty town located around 8 km from the Indian border and one hour from the BBDMP site. The culture is heavily influenced by India, and we had many meals of delicious spicy curry and fried bread. The streets were lined with small shops and marketplace stalls, but to my dismay, no department stores.
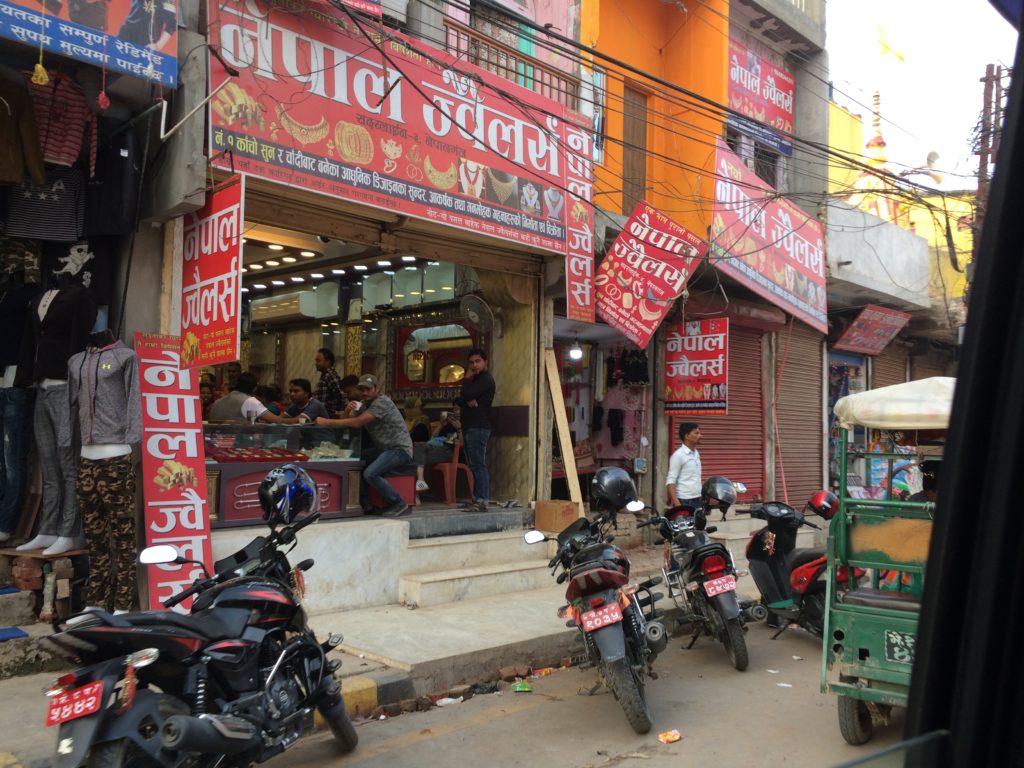
The crowded marketplace in Nepalgunj.
After a quick Google search my coworkers and our guests with us for the site visit headed to the nearest approximation, known as Rani Mart (Rani means ‘queen’ in Hindi). To my surprise, I purchased a whole new wardrobe and everything I needed for 1/10th of the price I would have paid for it in the U.S. (though the sizing on the tags was quite a bit larger!) I was feeling very pleased with myself.
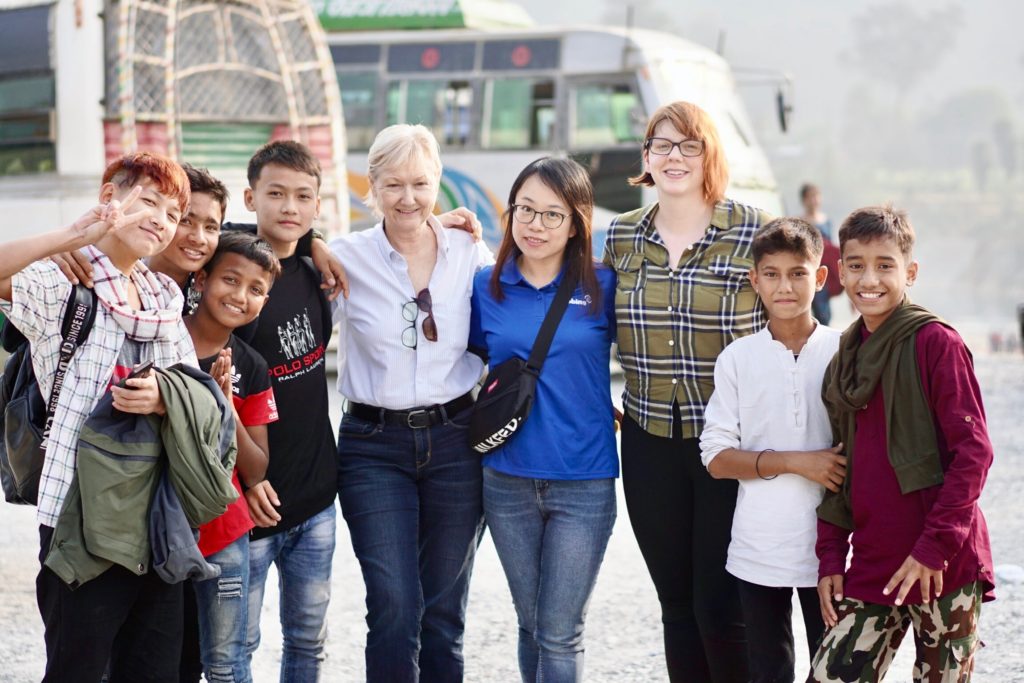
We took pictures with the local kids next to the BBDMP site. I’m the one rocking the green plaid shirt—the latest fashion from Rani Mart.
A Little Perspective
The next day we were ready to visit the jobsite. I couldn’t help but notice the rolling blackouts that plagued the city and the vast stretches of farmland requiring huge water resources. The people in the surrounding area make do with limited resources in ingenious ways—I was intrigued to see, for example, that every outlet requires you to flip an on-switch before the current becomes available. Perhaps we Americans could save significant energy if we made a setup like this a national standard. Local hotels, including one we stayed at, use solar panels for their power and air conditioning, and harvest rain water in order to reduce their usage.
All of this made me realize how much the BBDMP will impact the surrounding areas. This was confirmed in a meeting we had with Nepal’s Department of Irrigation (DOI), the project’s contractor China Overseas Engineering Group Co. Ltd. (COVEC), and consultant Geodata. The tunnel is sourcing water from the Bheri River to the Babai River, traveling through mountainous Himalayan geology known as the Siwalik Range. The water, as the project’s name suggests, is for multiple purposes. The estimated annual benefit in Nepalese Rupees is $2.9 billion for irrigation, and $4.3 billion for hydropower, making a total of $7.2 billion in benefits once the project becomes active.
The completed tunnel will irrigate 51,000 Ha of land and provide 48 MW annual generating capacity. That’s not to mention the environmental benefits: The Babai River currently swells each monsoon season and then runs extremely low in drier seasons. It is connected directly to the groundwater table, which is being aggressively depleted. With a regulated flow during all seasons, the groundwater table will see less depletion year-round.
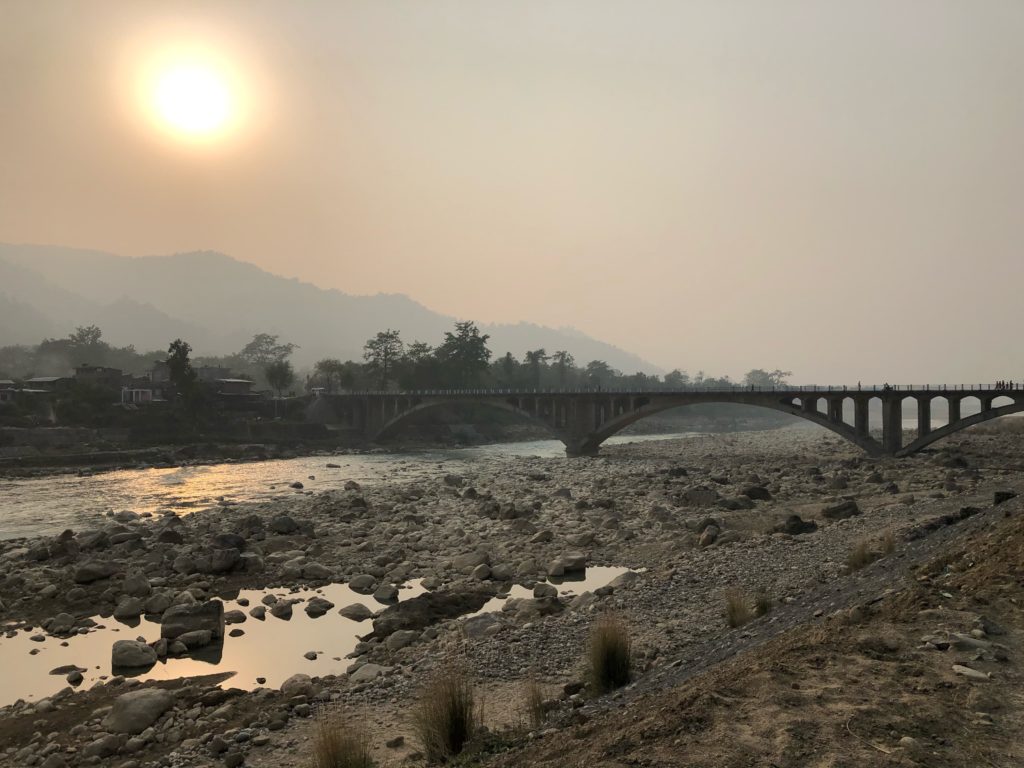
We crossed the Babai River on the way to the jobsite, seen here at low water levels.
The impact, in other words, is huge. Learning all of this made my obsession with my missing luggage seem inconsequential in comparison. I had my bug spray and some clothes. That was all I needed.
The First Nepalese TBM
With such a landmark project for the region, its proponents were willing to look to the latest technology during the planning phase. Our local representatives, MOSH Tunnelling, had been working since the 1990’s to bring a TBM to Nepal, a country known for its Drill & Blast tunneling. While TBMs had been considered multiple times, each time conventional tunneling had been chosen.
When the BBDMP was fast-tracked as one of the country’s “National Pride Projects” feasibility studies showed that Drill & Blast excavation could take as long as 12 years. The DOI needed a faster option, and they found it in TBMs. They began working with MOSH Tunnelling and Robbins to bring what would be the first Nepalese TBM ever into the country—a 5.06 m diameter Robbins Double Shield. The process for the DOI to acquire funding for the project and select a contractor through international competitive bidding took seven years, spanning from 2007 to 2015, when project commencement officially began.
Fast forward to our site visit in November 2018 and the project is far exceeding expectations. Tunneling has topped out at 1,202 m in one month with an average of around 740 m per month. The knowledgeable COVEC team have traversed a major fault zone, the Bheri Thrust, with no problems, and overcome a stuck TBM shield with a bypass tunnel constructed in just five days. Overall, the TBM is far ahead of schedule and the results are of national importance.
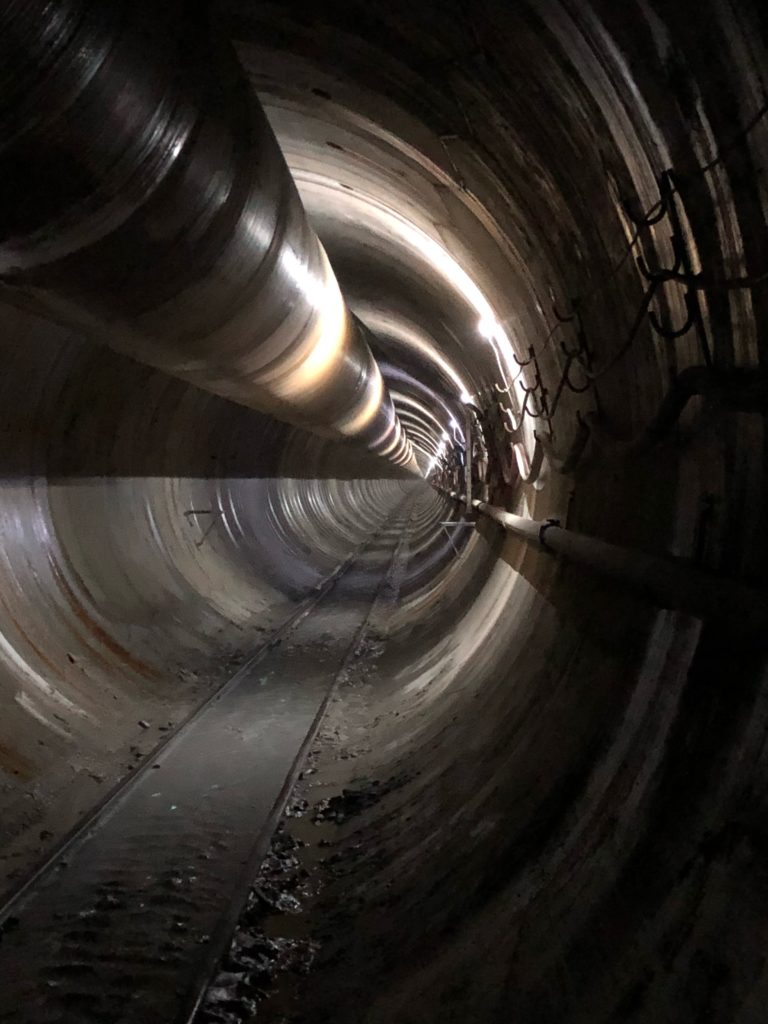
The tunnel is lined with hexagonal segments for rapid excavation.
The local community, national media, and government are all watching how the TBM excavation plays out at BBDMP. Given the strong performance, they are now considering TBMs for a host of future multipurpose water projects. It’s the kind of result that opens up a whole new marketplace.
Into the Forest
After a great site visit, we chose to relax for one day at a spectacular local lodge that offered jeep safaris into the Bardia Wildlife Reserve. Currently home to nearly 90 tigers (a number that is rapidly increasing through conservation efforts) we were hopeful of perhaps seeing one of the striped cats in the forest. Our guide was knowledgeable, our jeep sturdy and our driver adept as we traversed bumpy roads and forded a few streams on our safari drive. We saw mischievous macaques, tree-dwelling langurs, a host of brightly colored birds, and various deer. We saw several enticing tiger prints…but the tiger itself remained elusive. Obviously, this means that I must go back!
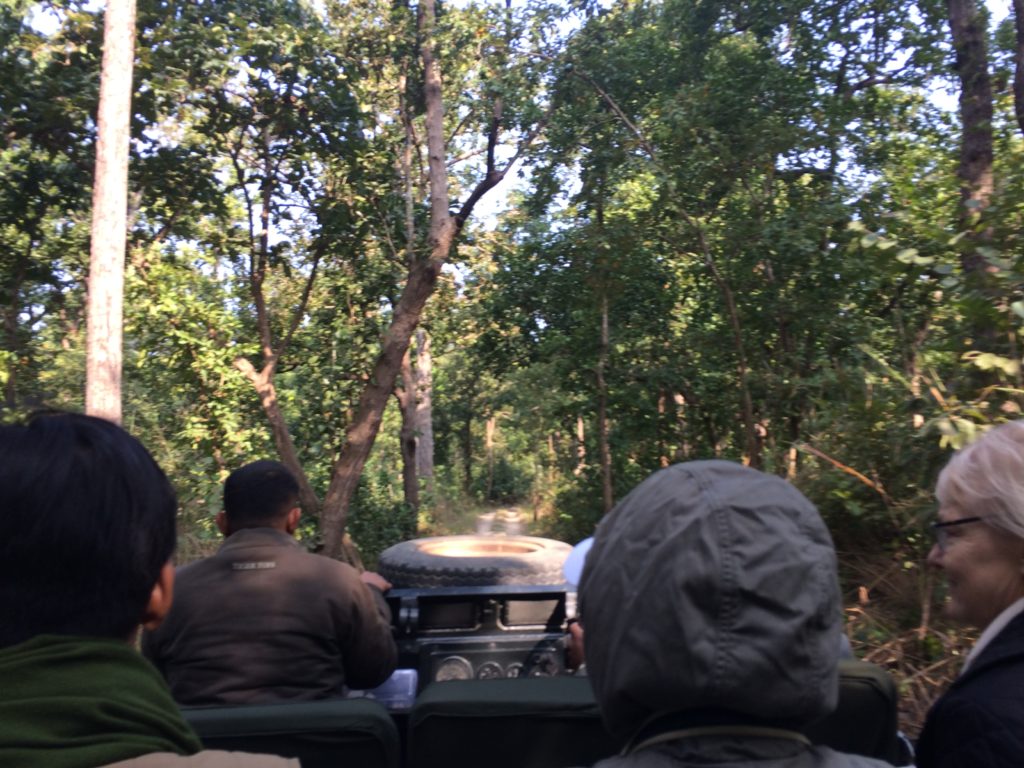
Over the river and through the woods…
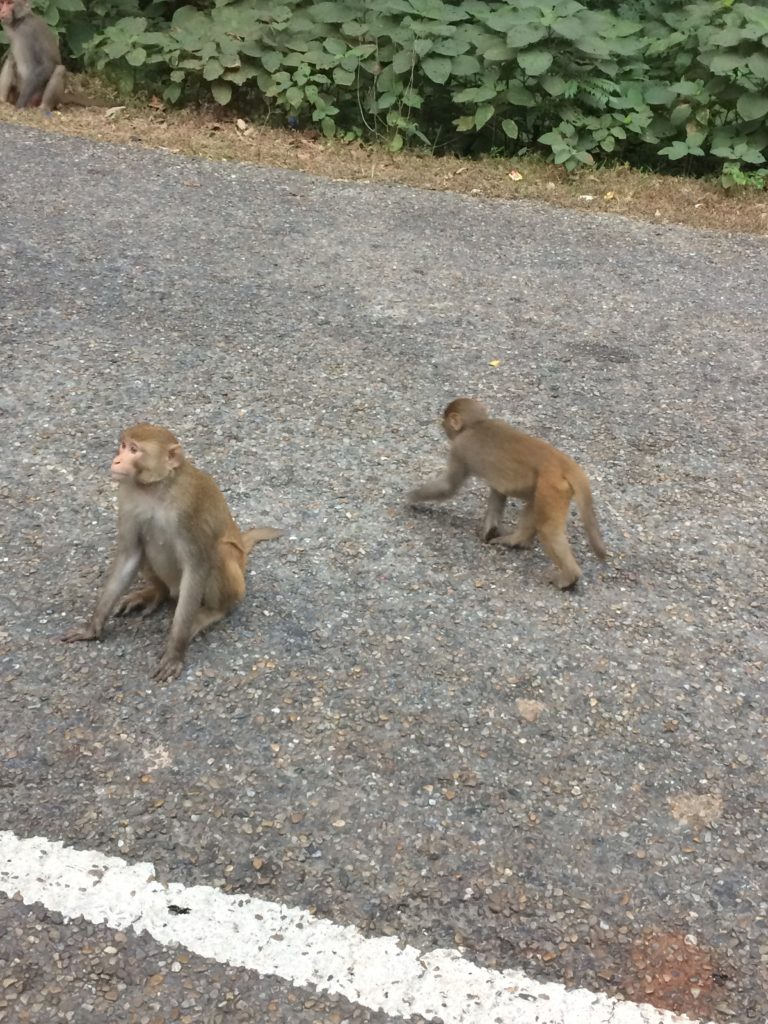
…past mischievous macaques waiting for food from tourists…
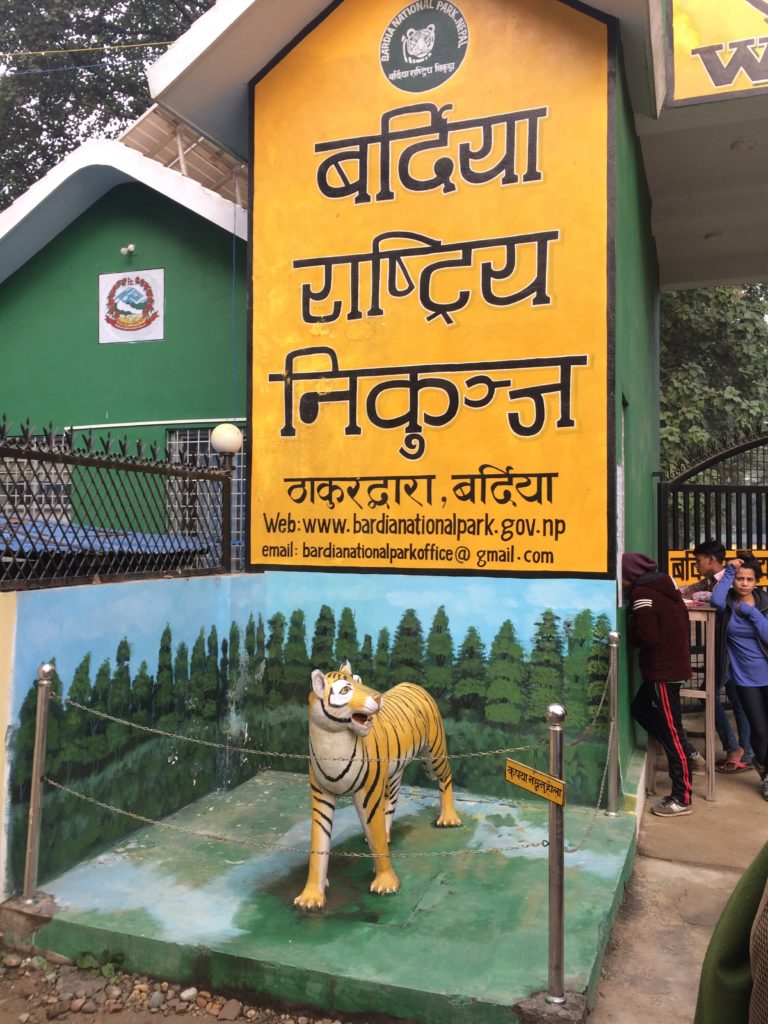
…we spotted our one and only tiger for the day.
A Lesson Learned
After traversing a tunnel, traipsing through the forest, and some swift sight-seeing in Kathmandu on our last day, I felt I had come full circle. I was ready to head home, but with an eye towards future opportunities to return to Nepal, whether for business or vacation. I will be back. But next time, you can rest assured, I will only bring what I can fit in my carry-on.
顽强的掘进机和团队克服困难贯通亚特兰大供水隧道
2018年10月4日,见证了直径3.8米的罗宾斯主梁式硬岩掘进机完成了它的史诗之旅。在当地说唱歌手和活动家“杀手迈克”之后,被称为“Driller Mike”的掘进机克服了沿着弯曲的8.0公里隧道的极其坚硬的岩石条件,以支持美国佐治亚州亚特兰大市的供水。
新隧道使亚特兰大供水计划更接近于将城市的水容量提高到30至90天,具体取决于日常使用情况。 “我们的项目进度非常激进,但项目团队一直在努力克服与隧道开挖相关的问题,”PC Russell合资公司的项目负责人兼风险施工经理(CMAR) Bob Rie表示 。
尽管面临挑战,但项目团队的独特结构仍然归功于项目的整体成功。 “我为我们的团队感到自豪。他们有障碍,挑战和挑战,但他们团结在一起并没有放弃,他们取得了成功。 PC Russell JV的隧道负责人Larry Weslowski表示,团队有很好的领导和监督。
该项目仅是美国第三个使用CMAR结构的大型施工项目。 PC 施工 / HJ Russell合资公司被选为该项目的CMAR,然后为该隧道采购了罗宾斯主梁式掘进机。设计施工包括隧道和竖井的设计方是由Stantec,PRAD 集团公司和River 2 Tap公司组成的JP2,指定了项目采用硬岩掘进机掘进。然后将掘进机的操作和组装分包给Atkinson / Technique 合资公司。
在罗宾斯的帮助下,在大型贝尔沃采石场(Bellwood Quarry)工地使用现场首次安装调试方案(OFTA)组装了坚硬的掘进机。 “工作人员按照规范组建所有部件,以使工程保持进度。这是一个挑战,但在此过程中没有消极性,“Weslowski说。尽管夏季气温达到43摄氏度和100%湿度,但掘进机已在2016年10月前蓄势待发。
硬质花岗岩从一开始就挑战了19英寸滚刀。 “地质非常坚硬,需要8个小时才推进1.5米。单轴抗压强度介于117和310 兆帕之间。掘进一开始就非常艰难。” Weslowski表示,但他补充说,一旦学习难关得到克服,“他们就开始打破项目纪录。我们取得了最佳日掘进38.4米。这个速度还在不断加快。” 其他挑战包括隧道掘进过程中遇到的涌水。 “我们确实遇到了需要修复的地下水污染。这项补救工作顺利完成,“ Huie说。
随着隧道工程的完工,亚特兰大市流域管理部3亿美元的项目正在进行中,以满足其2019年9月的计划总完工日期。该项目将把闲置的贝尔沃采石场变成一个91亿升的原水储存设施,连接查塔胡奇河和各种水处理设施。
超大直径泥水盾构为日本广岛开新路
2018年9月18日,一台直径13.7米的罗宾斯超大直径泥水平衡盾构机,为日本广岛高速公路5号线项目,始发掘进,开挖坚硬的岩石地质隧道。 这台盾构机在这个狭窄的城市工地始发,全靠采用现场首次安装调试的方案(OFTA)。施工商大林大成广成建设工事合资公司对工期的要求十分严格,在机器组装上只给予8个月的工期。”这个组装工期非常重要。在掘进机组装完成后,我认为OFTA方案很适用于这个项目。” 大林大成广成建设工事合资公司项目副经理赤井亮太说道。
为了满足城市内的运输管理要求,项目工地在运输上也存在限制。掘进机必须拆分为小型、可移动的重量和尺寸,然后组装在一个仅30米宽、60米长的小型工地里。这台重达2,400公吨的机器将为总长1.8公里的隧道,开挖1.4公里长的隧道段。项目一旦竣工,将显著改善广岛的交通状况。
根据地质条件,机器设计为可以应付20巴的水压,坚固的刀盘配有直径为20英寸和17英寸的压力补偿刀具。该刀具采用专利设计,可在高压下有效工作。作为机器维护的一部分,施工商打算在掘进期间更换10次滚刀。
在整个设备组装和始发过程中,施工商的工作人员与罗宾斯的现场主管紧密合作,罗宾斯负责协助并提供指导。“罗宾斯的工作人员经验丰富,尽管我们之间存在语言障碍,但并不妨碍他们每天全力帮助我们。我很感激他们。” 赤井亮太继续说。
新的高速公路5号线隧道将直接连接广岛市区和一个主要的国家公路网,预计将大大缩短市区到广岛机场的交通时间。隧道计划于2020年竣工。
克服断层带和涌水:越南昆嵩水电站项目
在这个简短的片段中,罗宾斯现场服务人员分享了他们如何处理越南昆嵩水电站项目中的硬岩、断层带和进水钻孔。
免费网络研讨会:在不稳定的地质下获得稳定的掘进
如果在混合地质条件下进行隧道施工,隧道横截面上可能存在任何岩土组合,那么您预计该项目将是一个挑战。当变异性是一个常数时,诸如地表沉降、掘进机上的磨损和适当的地质加固是一个问题。尽管存在这些变量,您的项目仍然可以成功。采用正确的技术、人员和操作方法,即使在最可变的地质条件下,也可以实现持续的良好掘进率。
罗宾斯副总裁Doug Harding和工程师Greg Michaelson将在这场免费的60分钟网络研讨会上探讨混合地质的情况,深入研究盾构机和跨模式掘进机在该领域的最新案例研究。Harding和Michaelson将根据我们众多现场服务人员的经验,根据成熟的设计和方法提出建议。无论你是一个操作掘进机的承包商,一个指定设备的顾问,还是一个即将开始的项目的业主,在不同的地质条件下,持续良好的挖掘都是可能实现的。
点击观看视频
能量提升的越南咖啡:我在昆嵩的冒险之旅
Traveling in the tunneling industry is basically a regular commute for some. A lot of us don’t think twice about the destination, we just do it with a mission in mind. My mission as Robbins Marketing Manager was this: a small conference in Ho Chi Minh City. Okay, easy! As the date approached, about a month before, I kept hearing about how well our Main Beam TBM was doing in Vietnam, at the Thuong Kon Tum Hydroelectric project, despite a gauntlet of challenges. I talked to some project engineers and field service personnel who told me it was in a remote location in Kon Tum Province. And then I heard more about traveling to that site: a 6-hour drive from Da Nang, through nauseating windy, narrow roads, climbing elevations with no speed limits to speak of. But that’s cool, I thought, glad I don’t have to go on that ride.
“Wait, why not just go to the jobsite for a video and photo shoot? We can have it ready for the breakthrough in October,” says Desiree Willis, Robbins PR manager a couple weeks later. What!? A few days after that, it was all planned. Ron, our videographer, Ken, our photographer, and Keri Lin, our marketing manager from Robbins China, set off with me on a last-minute adventure. The 17.4 km long Thuong Kon Tum HEPP tunnel will be the country’s longest once complete. A 4.5 m diameter Robbins Main Beam TBM and continuous conveyor system were supplied to bore a section of the tunnel.
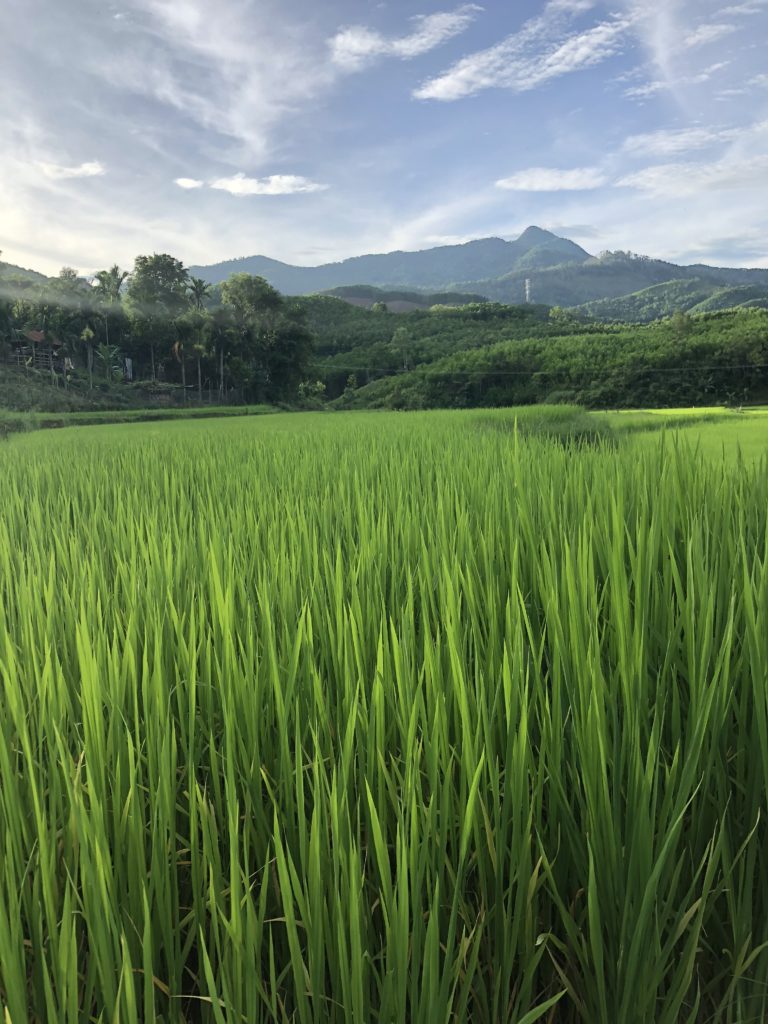
A terraced rice paddy with a beautiful mountain backdrop, so typical of what is synonymous with the sights of Vietnam.
Maybe because I was bracing myself for the worst as far as the drive goes, I didn’t feel like it was that bad. The scenery was jaw dropping with lush jungle, rice paddies and scenic villages, and so many distractions on the sides of the road that I just completely avoided looking ahead. Problem solved! The coolest distractions were the scooters driving on these mountain roads: what they were carrying, how many people were on them, their driving technique. My favorite site was seeing a whole family of people—a 5-year old kid in the front, the dad driving, the mom in the back and a toddler sandwiched in between the parents—on a run-down 125 cc scooter. Then there’s the animals: a litter of stray dogs, adorable black piglets making road crossings that almost made me swear off bacon, herds of cows, goats, etc.
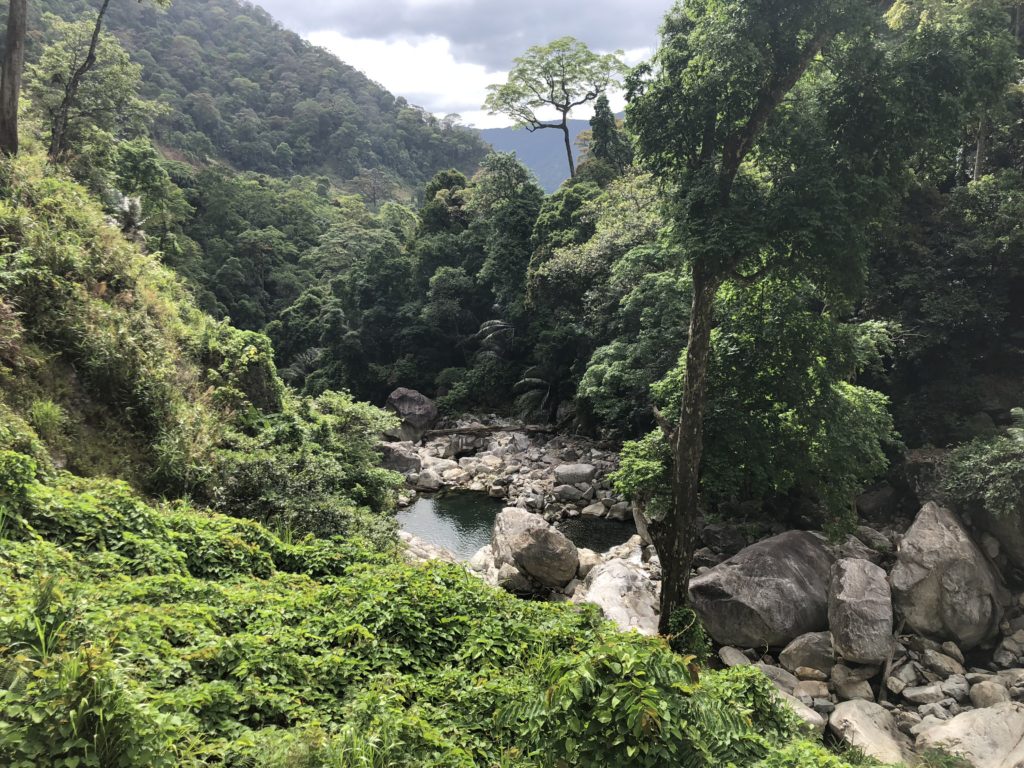
This was about a half hour away from the jobsite in Kon Tum province. The picture doesn’t truly depict how beautiful it was in person.
But how the heck did they get the machine, assembled by Onsite First Time Assembly (OFTA), to the site? Apparently, the previous contractor built portions of the roadway to the jobsite while components were staged at the port site. Several bridges, previously built only for light traffic with scooters and carts, were rebuilt or reinforced in order to carry the heavy TBM components. In a road conditions survey report by logistics firm SDV Vietnam Company Ltd., the original bridges were described as “having no shoulder”, and as having “blind corners and sharp curves”. The OFTA process allows a TBM to be assembled on location, saving time and money in terms of shipping costs and project schedule. The machine had successfully made it to the site, as it had launched in 2012.
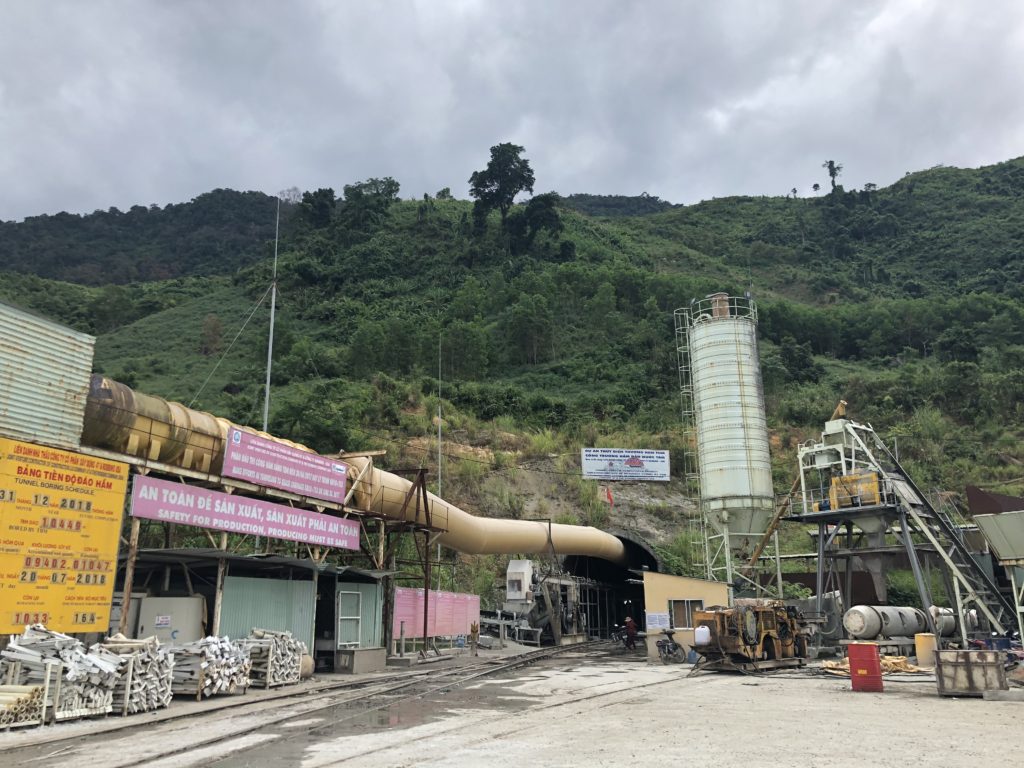
Not pictured: the litters of stray dogs and chickens roaming around the jobsite. Oddly enough, I never saw any stray cats here.
Upon arriving at the jobsite, I was immediately impressed with the site and the surroundings, especially after hearing about all of the challenges the project had back when the TBM was launched, under a different contractor. The TBM launched into complex rocky conditions that turned out to be quite different than in the original geological study. The machine sat abandoned 2.6 km into the tunnel with equipment sitting idle for months, waiting for a change in circumstances. In 2015, Robbins signed a contract with the project’s new contractor CC47 to supply full refurbishment and to operate the equipment with a full Field Service team. Since then, Robbins Field Service has generally been kicking butt.
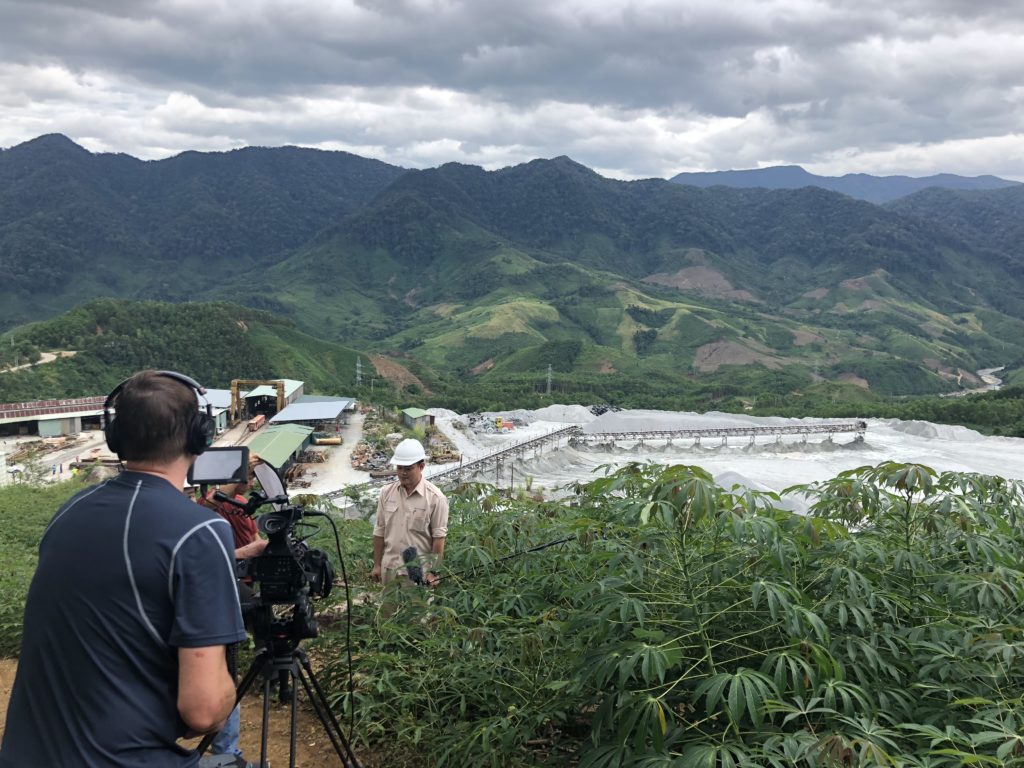
We hiked up a mountain to get this panoramic shot of the project site. I think it was worth it!
The machine was running as expected, so filming interviews and the machine went smoothly. I learned a lot from the interviews, mainly from the Robbins guys we interviewed—PN Madhan, Robbins Engineering Geologist, and Greg Adams, Robbins Field Service Manager. “It’s a workhorse of a machine and still in great condition, considering all of the difficult ground it’s been through,” Greg mentioned. Massive granitic rock wasn’t the only challenge they faced—the team also endured a handful of major fault zones requiring rock bolting and the use of the McNally Roof Support System, as well as some huge water inflows.
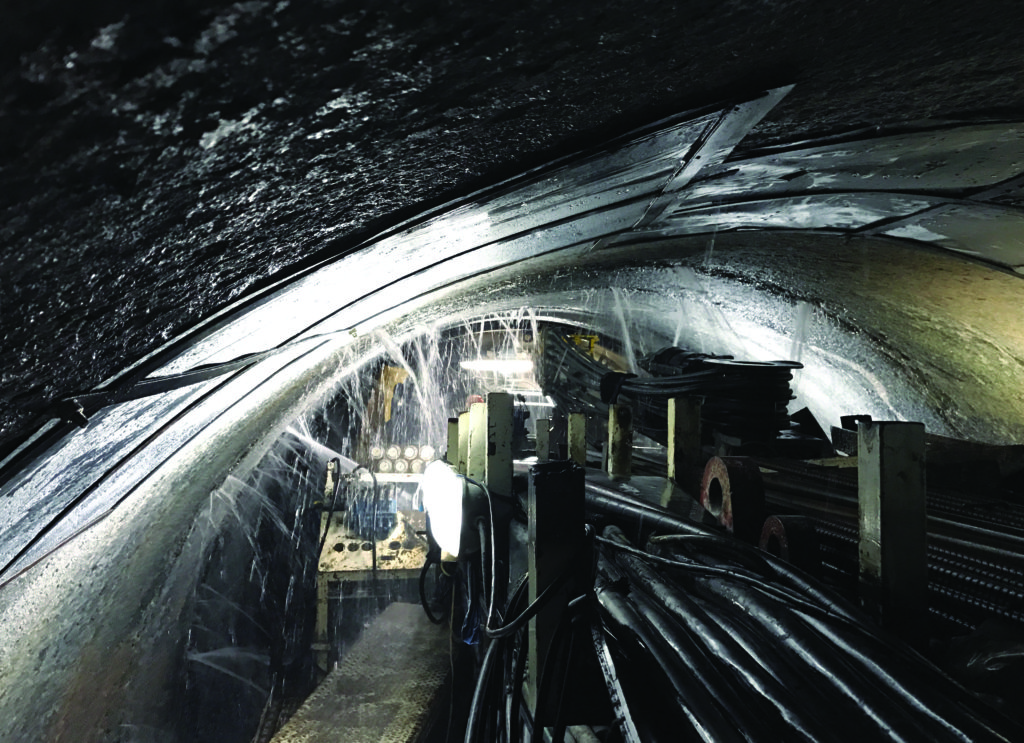
Water inflows were up to 600 liters per second—that’s nearly enough to fill an Olympic-sized swimming pool every hour!
Greg did warn our photographer and videographer that they were going to face heat with extremely high humidity. When John McNally, Robbins Field Service Manager-Asia, took over the project site, he managed refurbishment of much of the equipment inside the tunnel along with the camp’s living quarters. This included adding a ventilation tube, keeping the tunnel at a cool 34°C. That’s the temperature AFTER installing the ventilation. Read more about the challenges here.
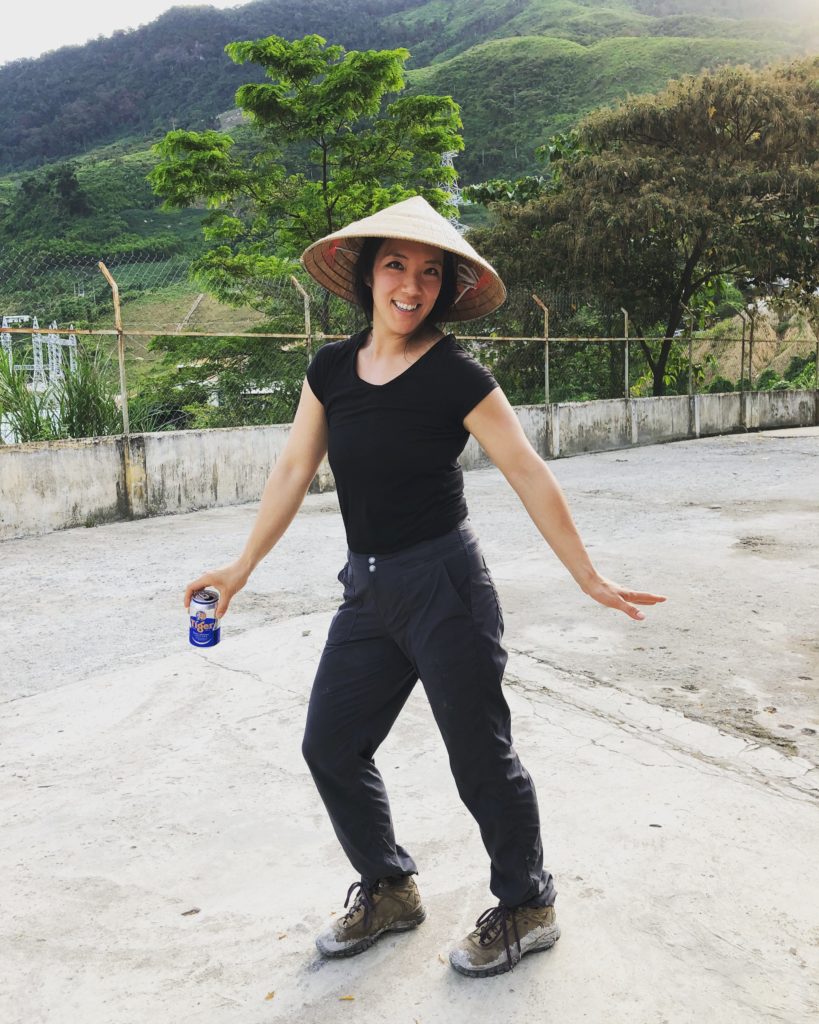
While waiting for dinner, I got posing tips from Keri Lin and our photographer for my next career as an Instagram model. A refreshing beverage and the typical Vietnamese farmer hat were absolutely necessary for the scorching hot day at the site.
The crew at the camp quarters, and the jobsite in general, were very welcoming. Greg and Taylor Hwang, Robbins project manager, arranged for a special dinner just for us on the first night—steak and French fries, an American staple! The crew on site mainly consists of English-speaking expats, Chinese, Thai, Vietnamese, Indian and Philippine guys, so the cuisine varied every day. We hung around that night for a while, listening to stories from some of the field service crew. This is while we were fawning over the pet falcon that one of the field service guys owned. I think the falcon liked living there, because his string wasn’t even tied to the perch at one point. Taylor told us that there were some families and children of the crew living there, who had to find ways to pass the time in this little remote village. He even told us they had pet monkeys at one point. I peeked into a living quarter and saw a drum set made with those Danish butter cookie tins that you get at Christmas. That’s one way to pass the time! Before we were about to leave, some of the Thai people at the site had brought in a bucket with a cover over it. I was curious and went to take a peek, because they started adding salt to the buckets. It was about 30 river snakes (possibly river eels, but they called them snakes) writhing violently because of the sodium touching their skin. Then they started preparing them one-by-one, sticking a nail into their heads and gutting them. It was quite mesmerizing, really.
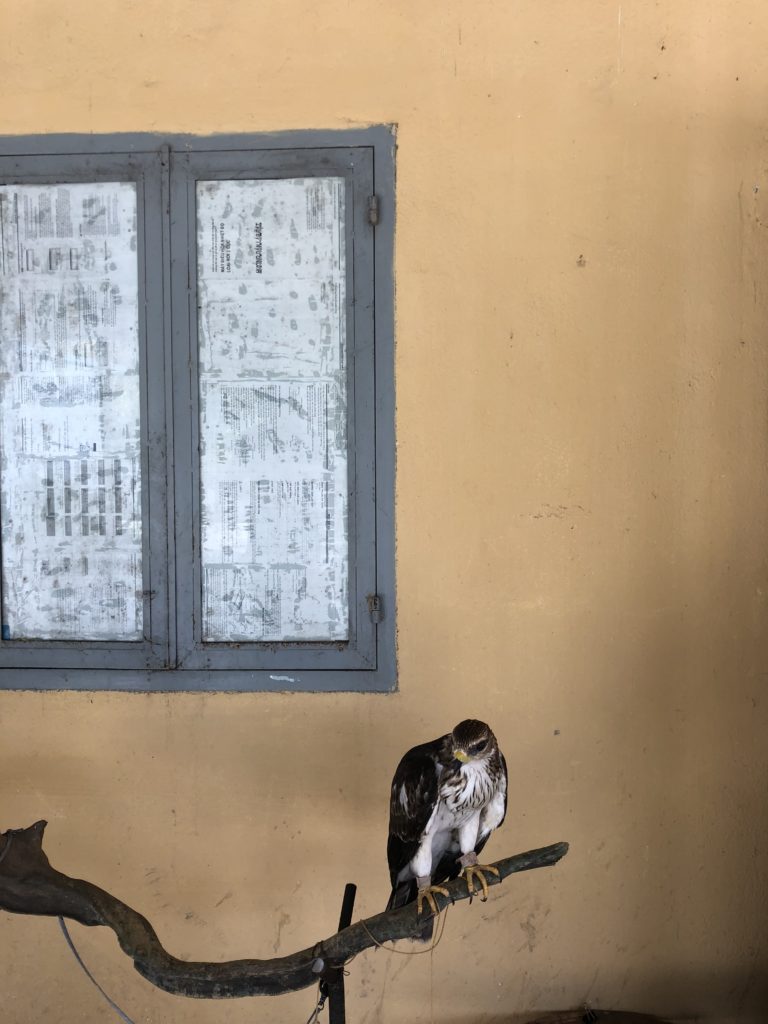
The camp’s pet falcon.
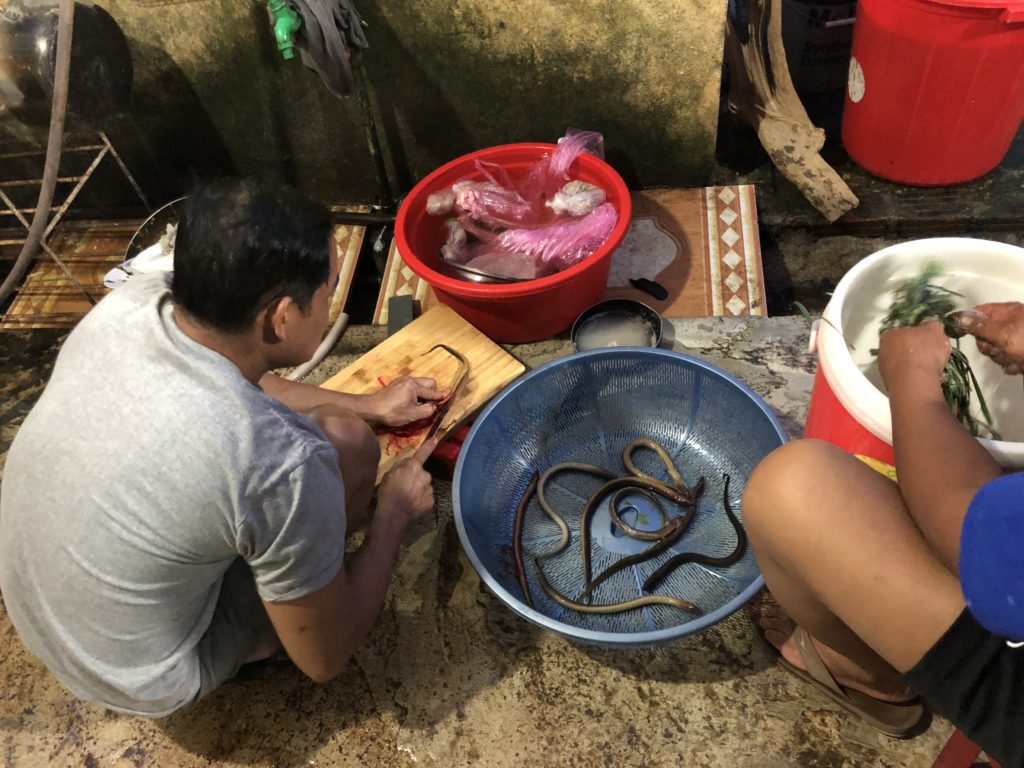
Not sure if this is the regional cuisine but the snakes were caught at a river close by the camp.
We only had two full days of shooting video and photos. Before the 6-hour drive back to Danang, all of us got caffeine-drunk on two strong Vietnamese coffees served with condensed milk each. I suspect it’s the perfect combination of the tenaciously strong espresso dripped into a puddle of pure sugar syrup (condensed milk) that singlehandedly causes adult ADHD from the first sip. During the drive down (which was much worse, I didn’t realize how much elevation we climbed going up), we were already reminiscing about the stories and experiences shared at the jobsite. When talking to the field service crew, they were all excited for the coming breakthrough later this year, but it seemed they were just a bit melancholy too. They were at this site for years, in a tiny remote village in the mountains of Vietnam, building friendships and routines. With only a handful of meters left to go on the tunnel, they’ll soon be off to the different parts of the world where they came from. I’m fortunate to have experienced everything I did on this trip and can’t wait to come back to this beautiful country.
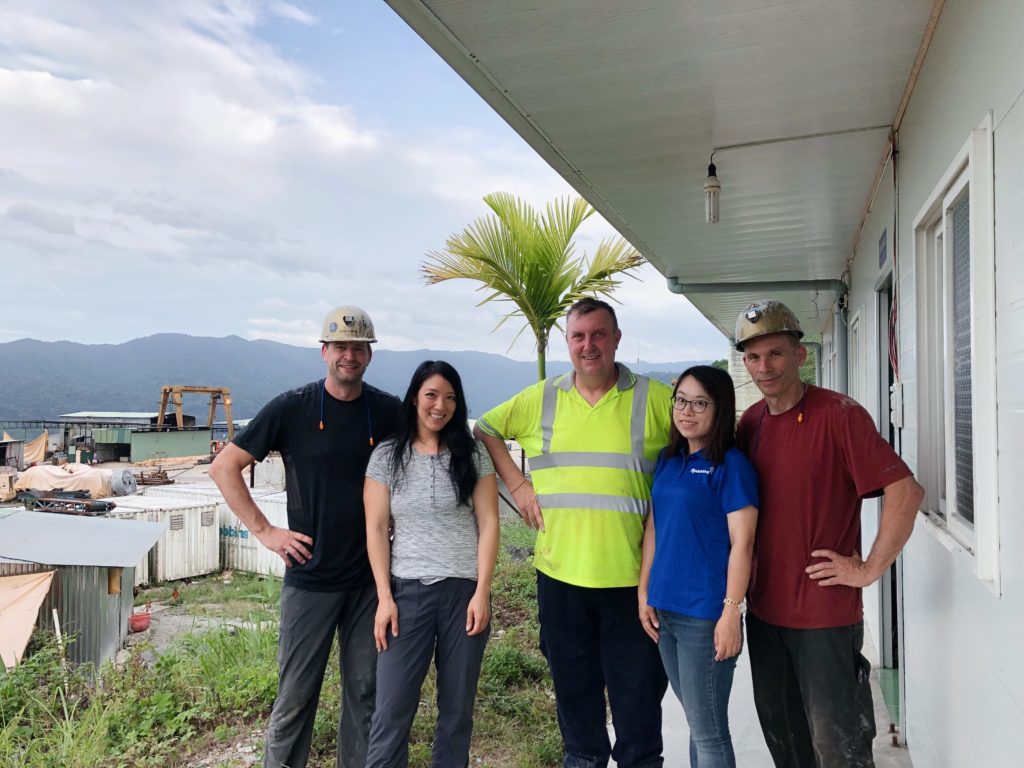
(From left): Ron (videographer), me, Greg Adams (Field Service Manager), Keri Lin (Marketing Manager for Robbins China), and Ken (Photographer) at the end of the shoot.
罗宾斯跨模式“罗斯”为亚克朗贯通运河拦截隧道
近日,一台直径9.26米的罗宾斯跨模式掘进机(XRE) 在美国俄亥俄州亚克朗运河拦截隧道(OCIT) 穿越终点线。跨模式掘进机 (XRE) 兼并硬岩掘进机和土压平衡盾构机的作业模式特点,配备的复合刀盘可以应付硬岩或松软地质。而在松软和混合地质条件下,机器在封闭模式下操作,一旦碰到坚固岩石,工作人员可以切换到开放模式进行挖掘。
这台跨模式掘进机是专门为该项目的地质量身定制的,隧道穿越从土壤到部分页岩层再转变为全页岩层岩石。“这个工程最具挑战性的一点是我们一开始就直接进入了最困难的地质部分。我们遇到长60米软土地质,从一个非常短的范围直接进入长180米混合地质段。”肯尼建筑工程公司(Kenny Construction)的项目经理David Chastka说。“我把我们公司熟悉这个领域的每个人,包括罗宾斯在内的每个人,都一起来攻克这段开始的240米隧道”
这台跨模式掘进机的掘进速度全页岩地质下,日掘进(2班轮次,每班10小时)达到了34米。“这台机器有能力顺利贯通,并取得了我们从未想过的掘进速度。它在硬岩下的掘进施工非常成功。” Chastka说道。排渣通过一台罗宾斯连续输送机完成。根据施工方记录,输送机在项目全程保持良好的使用率。
美国俄亥俄州亚克朗市的OCIT项目由一个运输和存储隧道系统组成,用于控制亚克朗市区多个调节道的下水道溢流(CSOs)。环保局(EPA)委托的项目包括长1.89公里的隧道,以及沉井、引水结构、加固污水管道以及相关结构工程。“俄亥俄州运河拦截隧道是本市历史上最大的公共改善工程,也是对我们的环境和基础设施重大投资,可以让未来亚克朗市居民和企业长久受益。” 亚克朗市市长Daniel Horrigan说。“这种项目本身是有风险的,我感到无比自豪,隧道工程在没有重大人员受伤的情况下圆满完成,多亏了一支专业的特别团队。”
现在隧道工程已经完工,机器将在今年秋天从其回收井上拆卸下来。“俄亥俄州亚克朗运河拦截隧道是我们城市历史上最大的公共改善项目,对我们的环境和基础设施进行了大量投资,这将使亚克朗的居民和企业受益。”亚克朗市市长Daniel Horrigan说。“这类项目本身就具有危险性,我非常自豪的是,由于一支专业团队的帮助,隧道部分完工时没有任何重大事故伤害。虽然罗宾斯是一家具有全球影响力的国际公司,但我们很高兴能够她能与俄亥俄州东北部的一家当地公司合作完成这一重大项目。”
美国俄亥俄州亚克朗市的OCIT项目包括建设一个运输和储存隧道系统,以控制亚克朗市中心区域的几个监管机构的下水道溢流系统(CSO)。美国环保署规定的项目包括长1.89公里的运输和储存隧道,以及下水道、引水结构、加固下水道和相关结构。
推动项目前进: 俄亥俄运河拦截隧道
罗宾斯和合资承包商Kenny/Obayashi共同努力,在亚克朗俄亥俄运河拦截隧道实现了短期启动计划。现场服务人员协助掘进机组装,并培训施工人员,以实现顺利始发。简而言之,Kenny Consturction的项目经理David Chastka就与罗宾斯现场服务团队合作分享感受。
攻克困难地质:亚克朗俄亥俄运河拦截隧道
在这短视频,Kenny Construction的项目经理David Chastka,分享罗宾斯的现场服务和他的团队如何在亚克朗俄亥俄运河拦截隧道项目上,一起攻克挑战与困难。
TAC/NASTT-西北隧道工程和非开挖大会
Event Name: TAC/NASTT-NW Tunnelling & Trenchless Conference
Dates: November 8-9
Location: Edmonton, AB, Canada
Venue: Fantasyland Hotel at the West Edmonton Mall
Robbins Utility Tunneling Manager, Tom Fuerst, will be presenting “Lessons Learned at Montreal’s Rue Jarry Project: Overcoming Flooding and Rebuilding a TBM to Finish on Schedule,” at this year’s TAC/NASTT-NW Tunneling & Trenchless Conference. The show will be held on November 8 and 9 in Edmonton, Alberta.