Author: Keri Lin
2018破岩峰会
Event Name: Cutting Edge 2018
Dates: October 29-31, 2018
Location: Atlanta, Georgia
Venue: Lowes Atlanta Hotel
The Robbins Company is heading south for Cutting Edge, which is being held this year in Atlanta, Georgia from October 29 through 31. Visit table 7 between presentations, including a panel discussion with Robbins President Lok Home and a presentation by Robbins Director of Engineering Brad Grothen, to discuss current projects and tunneling techniques.
困难地质资料册
即使是在计划最周密的项目中,也可能出现困难的情况。从挤压地质到断层带,再到水和泥浆的突然涌入,所有的一切都会大大延迟你的项目。了解我们的现场服务团队如何处理全球最具挑战性的情况。
带你看看:现在罗宾斯世界各地的工地都在忙什么
At any given time, Robbins TBMs are operating at dozens of jobsites around the world. Our dedicated Field Service personnel take video and pictures of the TBM progress often, so we’ve decided to offer a periodic roundup of what’s going on in a picture-based blog–from assembly of a massive Slurry TBM in Japan, to machine assembly for India’s Mumbai Metro to extremely hard rock encountered in Vietnam. Read on to found out the latest.
MEGA TBM ASSEMBLY IN HIROSHIMA, JAPAN
Onsite First Time Assembly (OFTA) of a 13.67 m (44.8 ft) diameter Robbins Slurry TBM is underway for Hiroshima, Japan’s Expressway Line 5 project. The geology of the 1.4 km (0.9 mi) long tunnel is predicted to include maximum 190 MPa (28,000 psi) UCS granite with high water pressure of up to 13 bar. The Robbins Field Service crew is nearing assembly completion and will begin testing of the equipment in August.
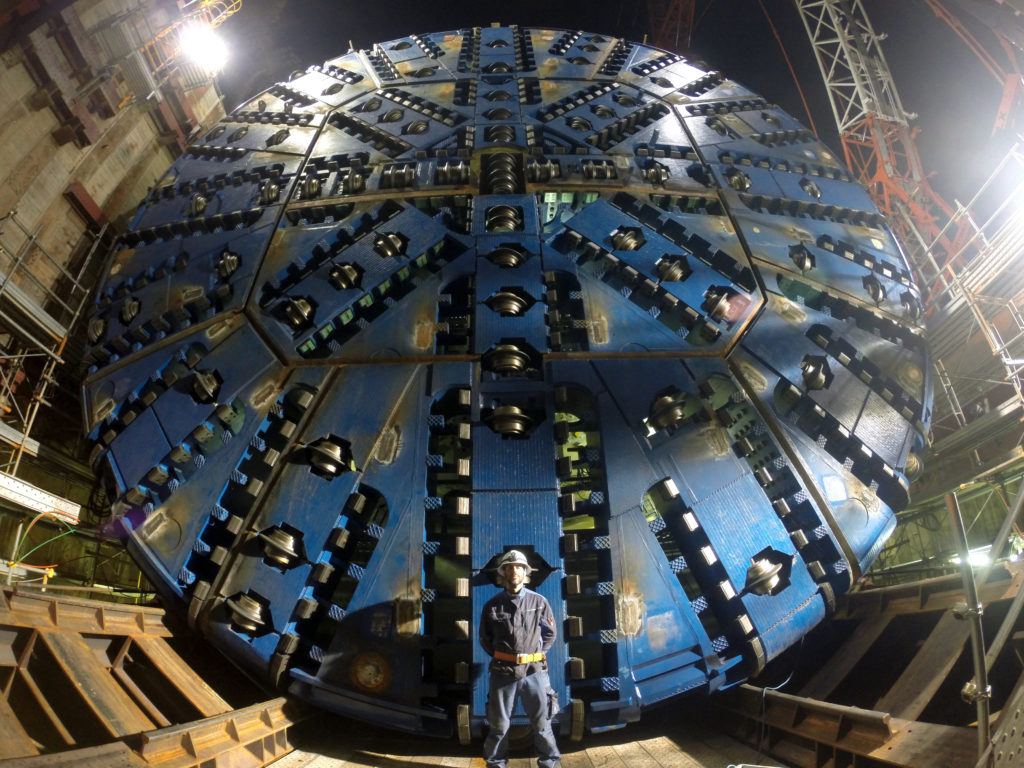
A full view of the 13.67 m (44.8 ft) Robbins Slurry TBM for the Hiroshima Expressway Line 5. Photo: Mario Recena Areces
SIMULTANEOUS BUILDS FOR MUMBAI METRO
Mumbai, India’s massive Metro Line 3 project requires multiple TBMs on various contracts. A total of four Robbins TBMs will bore on two separate contracts–two 6.65 m (21.8 ft) Crossover (XRE) TBMs for contract UGC-01, and two 6.65 m (21.8 ft) Slurry TBMs for contract UGC-03. Assembly of the first Crossover TBM and the first Slurry TBM on each contract are occurring simultaneously, and are being overseen by our experienced Field Service crews.
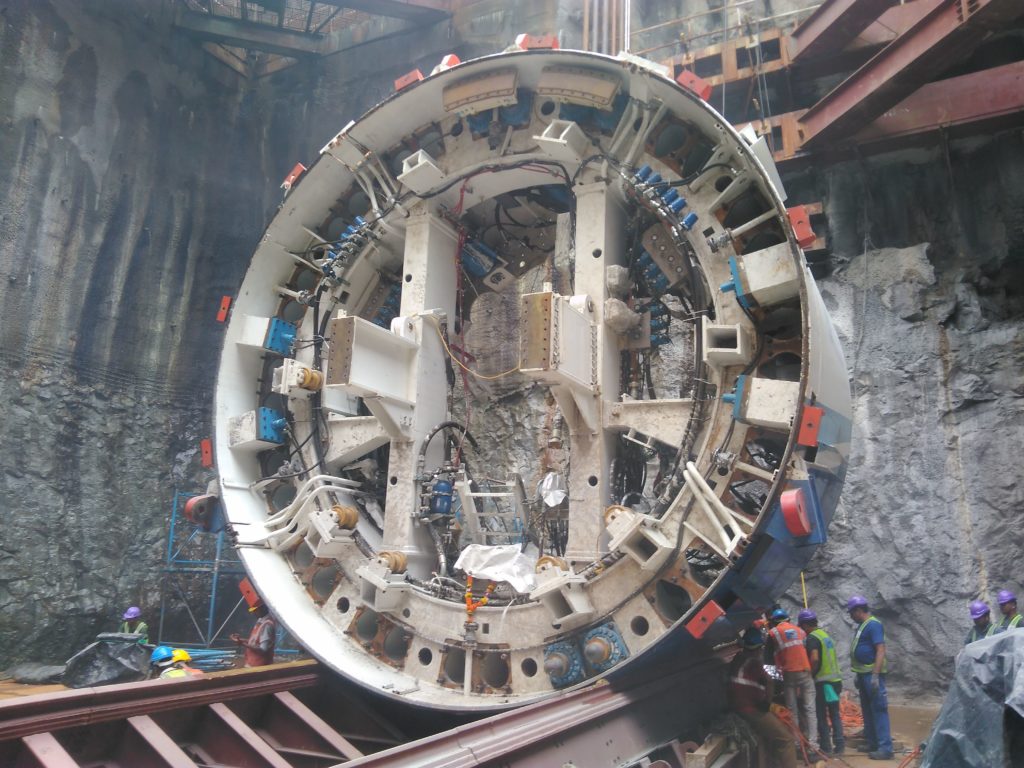
Crews position a section of the first of two Crossover (XRE) TBMs for the Mumbai Metro Line 3. Photo: Colin Ferguson
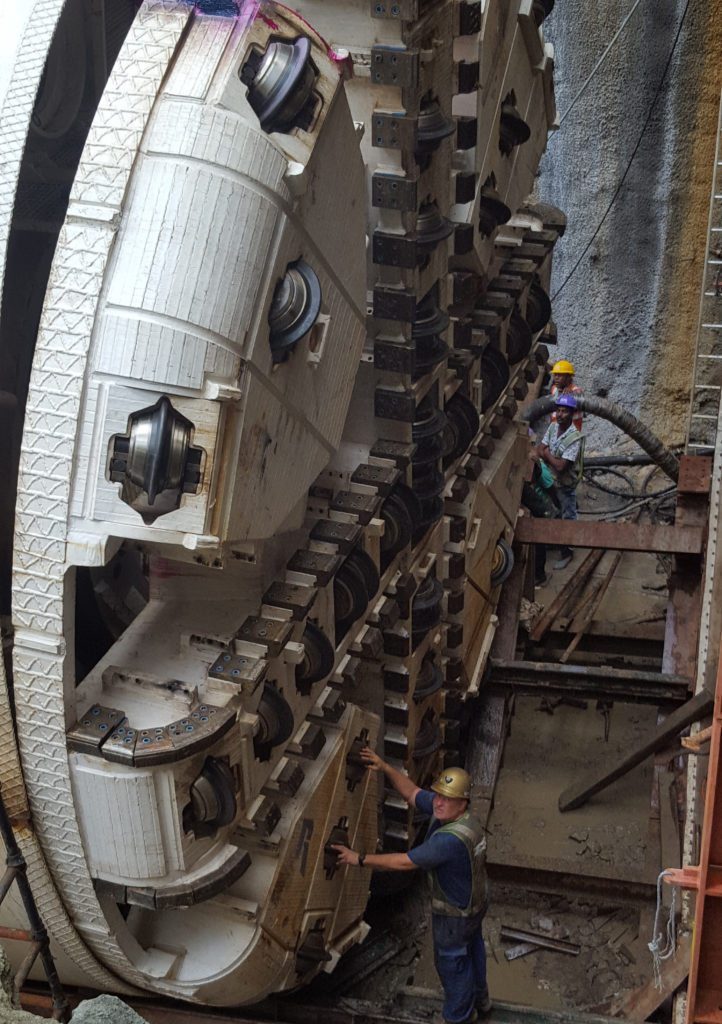
Crews assemble a Slurry TBM for the Mumbai Metro Line 3, and inspect the cutterhead. Photo: Colin Ferguson
EXTREME HARD ROCK IN VIETNAM
Robbins Field Service crews operating the Main Beam TBM at Vietnam’s Thuong Kon Tum HEPP have encountered granitic rock exceeding 300 MPa UCS and high water inflows. Despite the challenges the tunnel is more than 85% complete.
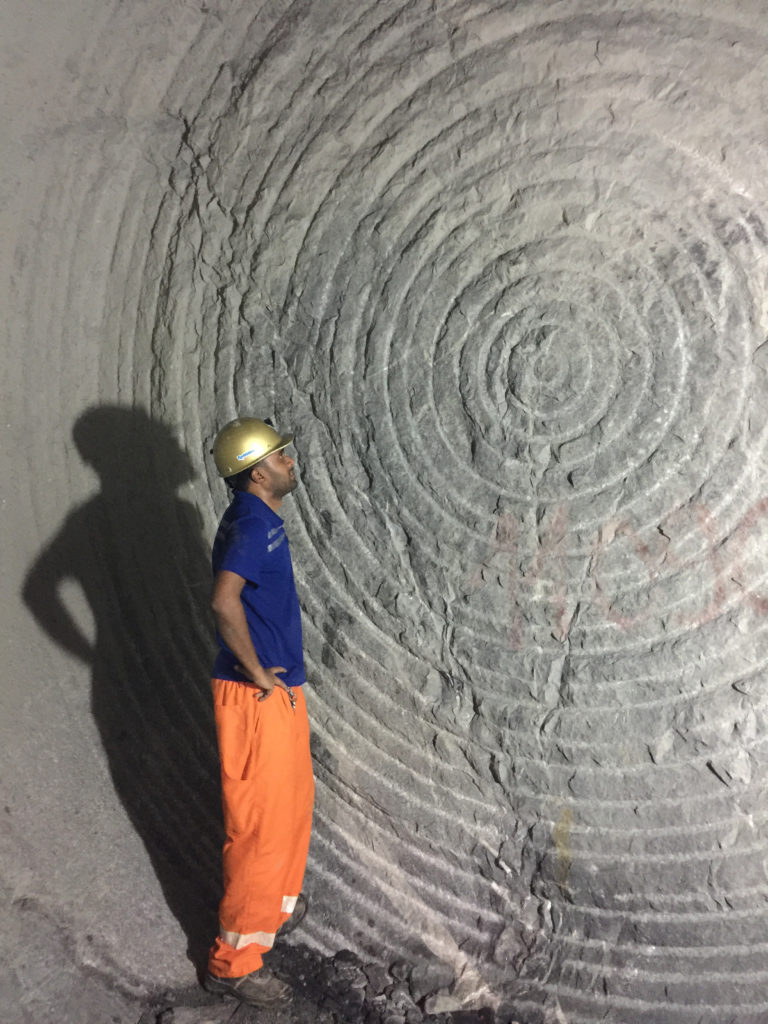
Robbins Engineering Geologist for Field Service, PN Madhan, inspects the massive granitic rock ahead of the TBM at Vietnam’s Thuong Kon Tum HEPP.
AN EPIC PROJECT IN MEXICO
With one of three Robbins lots completed at Mexico City’s massive 62 km (39 mi) Emisor Oriente tunnel, Field Service efforts are focused on completing Lots 4 and 5 in difficult mixed ground conditions. The customized EPB TBMs are boring through some of the most challenging conditions in the world, from abrasive basalt to watery clays and boulders.
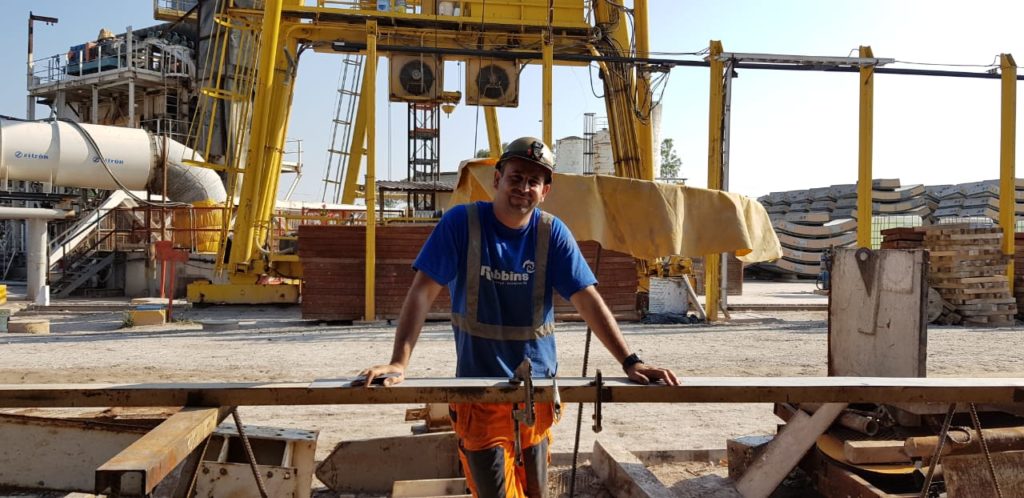
Alfredo Garrido Baena is part of the dedicated Field Service crew focusing efforts on completing Lots 4 and 5 in challenging conditions at Mexico City’s Emisor Oriente tunnel.
A JOB WELL DONE IN ALBANIA
TBM assembly and breakthrough is often discussed, but disassembly can be just as complicated. Following the recent breakthrough of the Crossover (XRE) TBM in Albania (the first machine of its kind in Europe) for the Moglicë Headrace Tunnel, Field Service crews are working to disassemble the machine in an underground launch chamber.
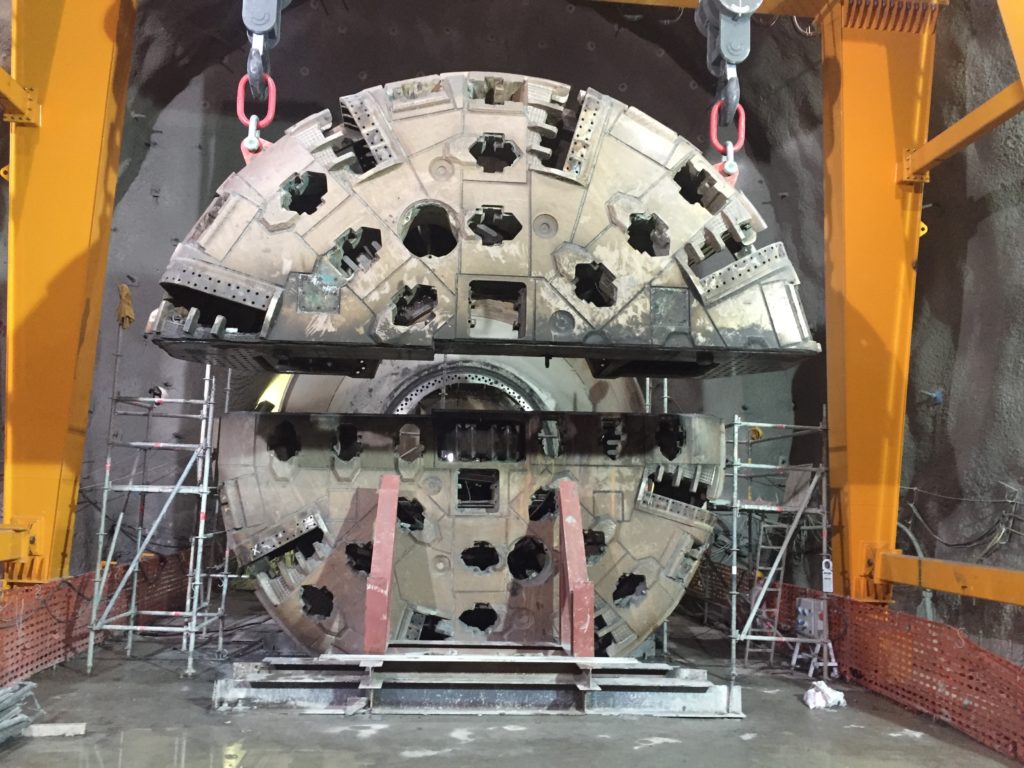
Crews separate the cutterhead of the Crossover TBM in an underground chamber in Devoll, Albania. Photo: Andy Birch
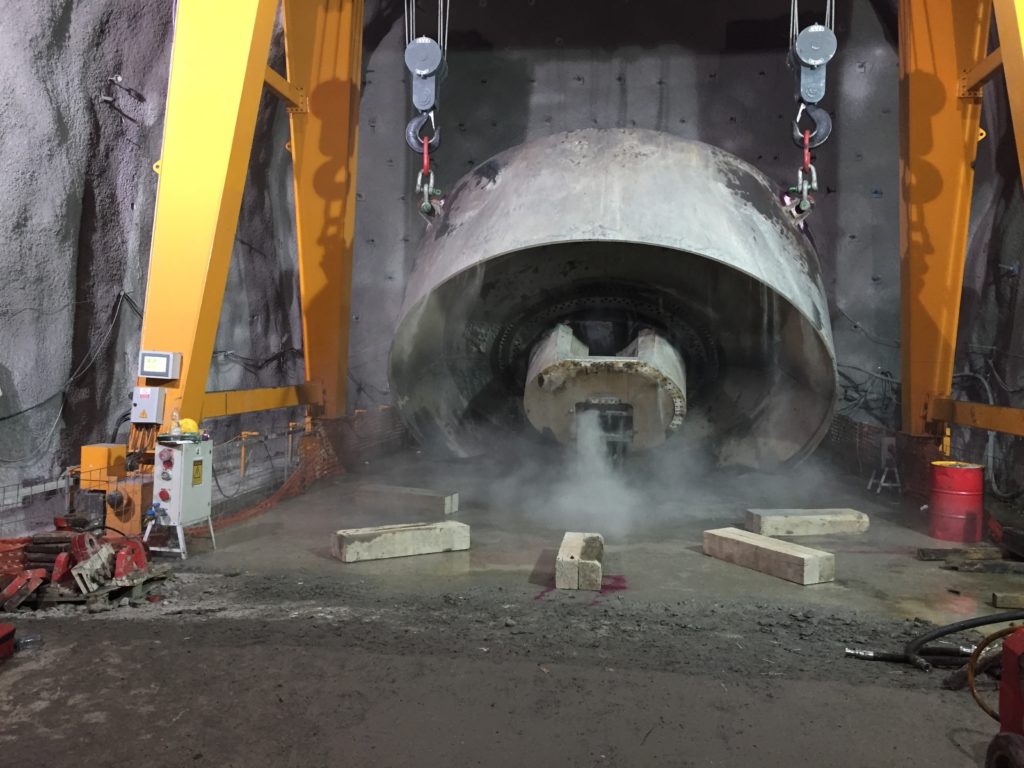
The forward shield is turned during disassembly of the TBM, which broke through in May of this year. Photo: Andy Birch
尼泊尔首台隧道掘进机月掘进超1,000米
2018年年末,尼泊尔首台隧道掘进机——直径5.06米的罗宾斯双护盾硬岩掘进机不负众望,实现了13个月掘进突破1万米,完成了隧道总长过度的82%,比预期目标提前了6个月。这台双护盾于2017年11月正式始发,到2018年4月,设备的月进尺超过1,000米,平均月掘进达800米,被尼泊尔媒体誉为工程史上的奇迹。
为了确保最佳的掘进机性能并防止停机,机器维护每天都在固定的时间进行。每天派地质工程师对地面情况进行两次分析,以便预测地质变化时,施工人员调整隧道参数,做好辅助措施的准备。在创纪录月的挖掘过程中,所开挖的部分主要由砂岩和泥岩组成,随后是长5.8公里、被称为巴瑞逆冲带的主要断层带。掘进机在2018年夏天成功贯通了宽400~600米的区域。
中海外尼泊尔分公司已经为这些条件做好了准备,并制定了有效的隧道物流,以减少停工时间。“隧道和分段架设的两个工作程序是在双盾构隧道模式下同时进行的,一般情况下,分段环的架设时间为15分钟,”王玉水继续说。“在单护盾构法施工模式下,分段支护是在连续施工后进行的,但分段支护时间仍在15分钟左右。”为了进一步减少时间,在日常维护中,应提前进行固结灌浆,以避免灌浆停工对整体施工进度的影响。
两台罗宾斯跨模式为孟买地铁三号线作业
2018年6月11日,在4月工厂成功后,一台罗宾斯跨模式掘进机XRE抵达孟买港,目的地为印度孟买地铁三号线开挖隧道。该机器结合了硬岩单护盾构和土压平衡盾构作业模式的特点,是将为合同UGC-01开挖隧道的两台直径6.65 米的跨模式掘进机其中一台。这两台机器的将由Larsen & Toubro使用,她是Larsen & Toubro和上海隧道工程有限公司(L&T-STEC合资公司)的一部分。罗宾斯公司将为初始掘进阶段提供关键人员。L&T-STEC合资公司的隧道运营主管Palwinder Singh表示:“在工厂验收试验期间,我们发现机器和后配套系统足以进行硬岩隧道施工。”
掘进期间,包括平行的长2.8公里隧道,地质条件将包括混合地质和可能出现的2巴水压。据Singh称,“由于预期的地质条件,选择了跨模式掘进机XRE”,包括玄武岩和由黑色碳质页岩、凝灰岩和角砾岩组成的过渡带。岩石强度预计在15兆帕至125兆帕之间。这些机器将在覆盖层仅15至20 米下掘进,并且隧道结构将以5+1的布置内衬钢筋混管片。
地铁隧道将在克夫普瑞站(Cuffe Parade)和胡特马昼克站(Hutatma Chowk)之间穿过维旦巴文站(Vidhan Bhavan)和教堂站。两台跨模式将从同一个25米深,22米长的竖井在卡夫游行站始发。罗宾斯项目工程师JP Bayart说:“竖井的有限长度要求在顶部100米处运行掘进机,部分或所有的后配套台车存放在地面。掘进机和后配套系统通过脐带电缆和软管连接。”
掘进机将在硬岩模式下开始挖掘。“每个刀盘都针对岩石作业进行了优化,因为这是预期的。由于螺旋输送机带有铲斗闸门和卸料闸门,这些机器也可以在软土地基上运行。“罗宾斯扭矩换档系统由两个与主驱动电机相连的变速箱组成,允许软土地质操作所需的高刀盘扭矩。”每台机器的表面配备六个渣土仓和六个大型内部渣土装载板。这种设计与位于每台机器中心线的螺旋输送机相结合,将允许完全排空刀盘土仓,从而在不需要土压平衡模式时,产生最小磨损。渣土将通过渣土车从隧道中运出。
第一台跨模式掘进机的组装和始发准备工作于6月20日开始,预计大约需要6周时间。第二台罗宾斯跨模式掘进机于5月底进行工厂验收测试,并将于7月底到达工地进行组装。“我们的目标是实现平均每月250米的掘进,”罗宾斯印度项目经理Jim Clark说。“完成掘进作业的目标工期是20个月,其中包括在初始驱动装置上使用脐带缆进行短启动、拖动机器和通过三个站点重新启动所需的额外时间。”承包商L&T计划两个轮班工作,以覆盖一整天的作业,以保持按工期完成。这两台跨模式将连接两台罗宾斯泥水盾构机,分别为孟买地铁三号线开挖隧道。这些机器中的第一台将于2018年8月始发。孟买地铁三号线工程预计于2021年竣工。
与掘进机采购相关的风险以及行业变革的下一步
掘进机隧道工程领域的风险管理本身就是一项风险业务。地下往往会出现障碍,跨越数英里隧道的复杂项目会增加这些风险。然而,在我们的行业中有管理和降低风险的方法,即通过确保进行彻底的岩土工程研究并制定应急计划。掘进机本身可以在设计时考虑到降低风险,使用扩大机器周围地面可视化的工具,并为承包商提供以最小延迟通过具有挑战性的地面条件的方法。本文从顾问、承包商和设备制造商的角度探讨了隧道掘进的风险。它还试图就如何更好地管理当今隧道行业的风险提出建议。
在亚特兰大供水项目中用主梁式掘进机在坚硬的磨蚀片麻岩下掘进
佐治亚州亚特兰大市的供水项目是一个优先项目,其中包括一条5.0英里长的隧道,连接查塔胡奇河(Chattahoochee),该河将为该市建立一个应急供水系统。一个直径12.5英尺的主梁掘进机正在以每天高达100英尺的速度开挖该地区最深的隧道,穿过坚硬、磨蚀的片麻岩。本文研究了该项目的具体设计,以及掘进机的性能。根据本工程和该地区以往的工程,得出了该地区极硬地质条件下开挖的掘进机优化设计结论。
冰川地质下刀盘配置和资源规划的掘进机刀具磨损分析
冰川地质的磨蚀性通常导致隧道掘进机刀具检查和更换需要,这可能需要高压干预,是成本和风险因素。岩土条件、掘进机运行参数和刀具磨损测量的相关性分析是深入了解磨损系统行为的一种行之有效的方法。本文介绍了在西雅图和温哥华,不列颠哥伦比亚省大城市地区的各种掘进机驱动装置对冰川和冰川间沉积物中滚刀和刮刀类型刀具性能的研究结果。作者对刀盘结构、刀具管理策略和监控技术的使用提出了建议。
俄亥俄运河拦截隧道项目大直径跨模式掘进机的物流和表现
在亚克朗下面开挖的俄亥俄运河拦截隧道(OCIT)是美国第一次采用大直径跨模式掘进机的项目。该机是在30.4英尺直径可变的条件下开挖软岩和页岩等。由于独特的条件,隧道掘进机具有灵活设计和功能的特点,包括刀盘设计、配备耐磨板的刀盘的和螺旋输送机。预测性维护计划的一部分,测量的螺旋输送机的暴露特点将被考虑进驱动报告分析在页岩中的磨损率。本论文主要集中分析项目在物流和掘进机始发过程和组件的耐磨性能,在现场和在地质下的变量。
让我们明确一下:对于隧道行业来说,透明度是一种恩惠,而不是破坏。
The idea of transparency is one that we most often hear touted in politics and policies. But transparency is a concept that applies to our underground industry as well. Widespread knowledge sharing can and should be the policy in our industry, but all too often jobsite politics, confidentiality agreements, and fear of poor public opinion limit what is ultimately divulged. I argue that transparency in tunneling is a help, not a hindrance, and we can make steps today towards clearer communication.
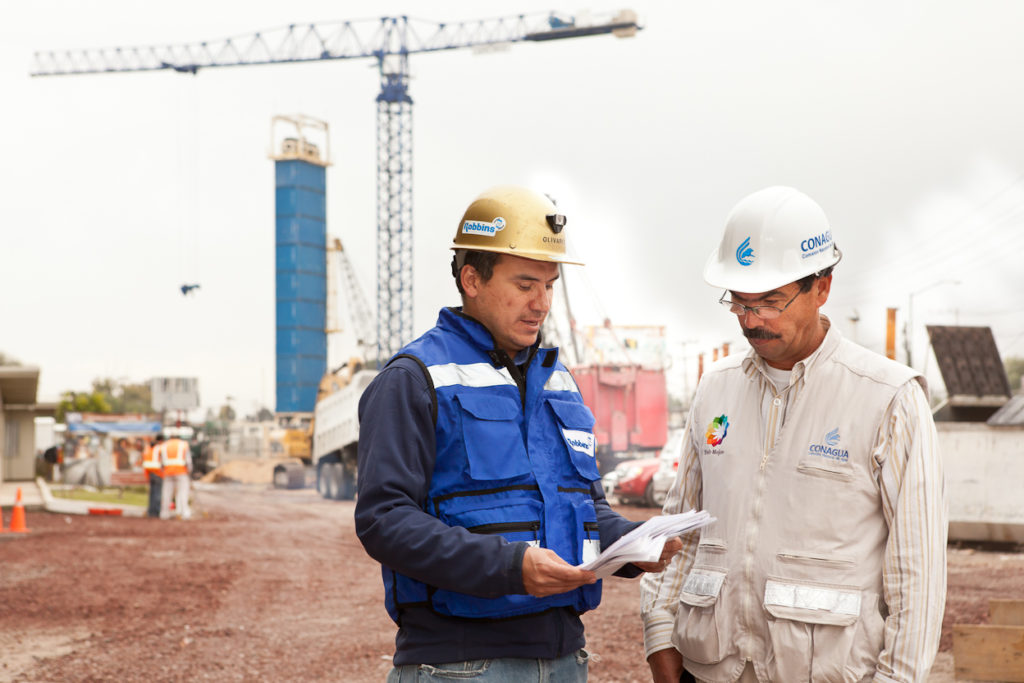
Transparency, achieved through better communication among all stakeholders, is the key to continued success in our industry.
Why It’s Needed
- Learn from Experiences in the Field: Tunneling professionals deserve full access to the successes and the problems that have been encountered in the field. If we were to employ universal knowledge sharing, tunneling operations themselves could become safer and more efficient and overall project costs could be reduced.
- Improve Tunneling Technology: Knowledge of advance rates, performance in specific ground conditions, wear rates for cutters and other surfaces in contact with the cutting face, performance of ground conditioners and foams, and many other types of info are imperative to improving technology. Tunnel boring could be made faster, safer, and more cost effective with such knowledge. It could also improve willingness to try new and emerging technologies in the industry, which benefits all stakeholders. With a good knowledge of TBM performances in specific ground conditions, TBM specifications could also be written to greater accuracy and result in using the most cost effective solutions.
- Improve Risk Sharing: Risk is often apportioned unfairly on today’s tunneling projects. In many cases the TBM supplier is required to shoulder a larger part of that burden than their potential returns. With a better understanding of the risks through knowledge of past projects, as well as knowledge of past risk sharing strategies, this problem can be resolved.
- Ensure Fair Financial Practices: With transparency in terms of contractual pricing and project spending, payments for work performed, etc. and other unsavory practices can be lessened.
- Reduce Litigiousness: Claims in tunneling projects are on the rise worldwide. Recent projects have resulted in separate and duplicate claims against different parties, such as the equipment manufacturer and the owner, for the same issues and without their mutual knowledge. Such claims are unfair, and through transparency and equal access by all parties to a Dispute Review Board, the frequency and extent of lawsuits in our industry could be reduced.
From the Equipment Supplier Perspective
As equipment suppliers, we strive to share the information that is available to us. We’ve opened up about stuck TBMs, challenging drives, and how we’ve overcome those issues. We’ve also tried to share whenever possible why we think fast advance rates and good efficiency were achieved on various projects.
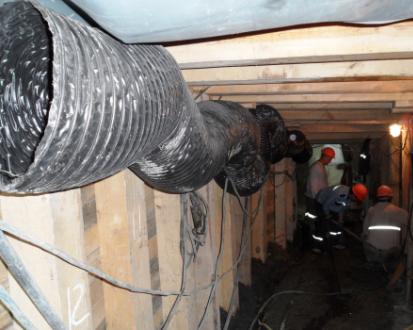
A bypass tunnel at Turkey’s ultimately successful Kargi project, where we shared information on seven such tunnels built in the first 2 km of tunneling.
Unfortunately knowledge is sometimes not shared even within parties on the same project, such as the contractor, project owner, owner’s representative, and equipment supplier. Time and again we see that communication between all parties is key to overcoming challenging conditions. The road to transparency starts here: with clear communication between all coordinating parties on a given project.
Not Without Precedent
Transparency is not an untested idea in our industry. A great recent example is that of the U.K.’s Crossrail project. The project follows governmental codes of practice for data transparency and the country’s Freedom of Information Act. Details such as project and equipment costs, spending budgets and records, safety records, and more are available for download on their website, and special requests can be made for additional data. Multiple reports have also been up front about TBM performance, advance rates, and other experiences on the project. The Crossrail project was highly successful and, arguably, transparency played a large part in that. Crossrail is also just one example of transparency at work in the U.K.—governmental programs such as Transport for London’s Transparency Strategy aim to give clear and consistent information to the public about all road and public transit spending.
A Call for Clarity
Transparency is possible in the tunneling industry, but it may require things like international regulations, or at the very least certifications that could be provided by an international organization like the ITA. Such a certificate would be highly beneficial to all stakeholders: It could certify corruption-free practices, and guarantee knowledge sharing. Transparency is not an easy thing to achieve, and there are certainly barriers to the process in various areas of the world. But we can start with transparency requirements within projects, and then move outward. To be clear: knowledge sharing is something that can only benefit our industry. It is our recommendation we start today.