Author: Keri Lin
罗宾斯掘进机开挖格勒瑞德嘉鲁洞穴
一台翻新的罗宾斯直径3.5米的主梁式隧道掘进机立下另一个里程碑,以增加其传奇的掘进生涯:遇到一个意想不到的洞穴,并成功通过。
承包商Eiffage土木工程部正在操作这台机器,该机器于2017年在法国拉西奥塔特的格勒瑞德嘉鲁项目(Galerie des Janots)中启动。该洞穴布满钟乳石和石笋,大小为8000立方米,在隧道作业的左侧被磨破。工作人员将该洞穴命名为“哥塔· 玛丽·莱西姆”(Grotte Marie Lesimple)以他们的现场地质学家的名字命名。
“我们撞到了它的拐角处。为了穿过它,我们必须建造一堵4米高的混凝土墙,这样隧道掘进机就有东西可以顶住,” Eiffage格勒瑞德嘉鲁项目项目总监Marc Dhiersat解释说,“一扇小门允许进入洞内,洞内自然形成于地表以下60米处。掘进机启动后,能够成功地在8次行程中驶出洞穴,而不会出现明显的停机时间。
“这当然是不寻常的,遇到一个如此大小和意义的洞穴。罗宾斯欧洲销售经理Detlef Jordan说:“这与地质学有一定关系,岩溶和火山岩地层最有可能形成地下洞穴。”在掘进过程中,溶洞是一种已知的风险,但沿路线从地表进行的垂直钻孔报告中未显示溶洞。
在完成2.8公里的隧道之前,还需要再挖1.8公里的隧道。“可能还有更多未知洞穴。我们在机器上有一个隧道掘进电子前方探测系统(BEAM),正在单独轮班进行探钻、喷射混凝土和维护。” Dhiersat说。隧道掘进电子前方探测系统是一种利用聚焦电致极化探测隧道掘进机前方异常的地质预测技术。
工作人员在早期掘进遇到了困难的地质条件,包括石灰岩和粉状粘土。“当机器正在掘进时,它会很好地工作。我们有很好的生产,这是一个很好的硬岩石机器。但有时我们遇到的不是硬岩石,” Dhiersat说。“软弱的岩石和粘土条件需要围岩支护,包括安装树脂锚栓和不良地面的环梁,顶部是10到15厘米厚的喷射混凝土层。”尽管5个月的地质条件较差,但Eiffage仍乐观地认为,条件将得到改善,隧道将在未来4至5个月内完工。
格勒瑞德嘉鲁隧道是14个旨在节约水资源和保护资源的工程之一,这系列工程由艾克斯 – 马赛 – 普罗旺斯大都会,罗纳地中海科西嘉水务局和州政府执行。格勒瑞德嘉鲁隧道开通后,将取代目前位于铁路隧道中的现有管道 – 这些原始管道存在严重缺陷,导致每年估计水损失量为500,000立方米。。
完工的隧道将穿过Le Parc National des Calanques,埋深范围在15至180米之间,以替换目前用于供水网络的管道。“目前的管道输送能力限制在每秒330升,这在夏季是远远不够的。该工程的目标是确保生产线的安全,并将生产能力提高到每秒440升。” Dhiersat说道
国际排水灌溉委员会会议
Event Name: International Commission on Irrigation on Drainage (ICID) Conference
Dates: May 2-4, 2018
Location: Kathmandu, Nepal
The Robbins Company hopes that you will join us in Kathmandu, Nepal from May 2 through 4, for the International Commission on Irrigation and Drainage (ICID) Conference. Stop by our booth to speak with one of our knowledgeable associates about projects running worldwide.
2018智利矿业展
Event Name: EXPOMIN
Dates: April 23-27, 2018
Location: Santiago, Chile
Venue: Espacio Riesco Convention Center
The Robbins Company is looking forward to exhibiting at EXPOMIN in Santiago, Chile from April 23 through 27. We hope that you will join us at booth C27 during exhibition hours to learn more about projects in the area, such as Los Condores II, which is currently underway in the Andes Mountains, as well as other boring projects around the world.
你现在处境艰难吗?从我们在一些隧道工程世界上最困难的项目中所经历的磨难中学习
Squeezing Ground, Fault Zones, Water Inflows, and More
True story: In a mountain range, crews worked on a shielded TBM more than 500 m below the surface. The TBM had excavated several kilometers in worsening conditions. The crew encountered karstic aquifers filled with mud and water. Personnel were pumping polyurethane through the cutting face to staunch the water inflows.
Suddenly, water inrushes climbed to a rate of 1,500 liters/second, creating a knee-deep underground river and causing the machine to become stuck. Thankfully, the crew was able to exit the tunnel, unharmed. The massive inrush created a damming effect with enough pressure to crush the TBM shields and send cylinders catapulting into the back-up.
As quickly as it had started, the machine ground to a halt, deep underground.
What happens when you encounter an unforeseen condition? A severe water inflow, fault zone, or squeezing ground? A geological feature that seems like it might stall your tunneling operation altogether? Some of our most difficult challenges—spanning from New York to Peru to the Republic of Georgia—are detailed below. These case studies are meant to pass on our knowledge and experiences to help you overcome obstacles, unforeseen or otherwise.
How to Overcome an Epic Flood: New York’s Harbor Siphons project
Sometimes an unforeseen condition requires a rescue effort to overcome. In October 2012, a storm was coming to New York City’s Harbor Siphons Project on the shores of Staten Island. The undersea tunnel and its 3.6 m CAT EPB ground to a halt when hit by Superstorm Sandy. The monstrous hurricane battered the eastern seaboard of the U.S. with winds of 145 kph.
The launch shaft was inundated with seawater despite contractor Tully/OHL’s best efforts. Flood water entered the tunnel and stopped the TBM just 460 m into its 2.9 km long drive. A 2013 post-storm survey of the tunnel showed a damaged machine extensively corroded by saltwater. All electrical components needed to be replaced.
Contractor OHL turned to Robbins for help. During the downtime, the original TBM manufacturer had exited the tunneling industry. Robbins worked with the contractor to come up with a multi-pronged approach to bring the TBM back to life.
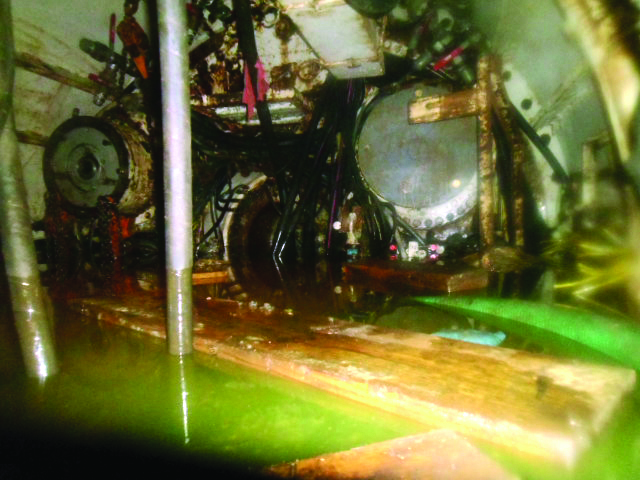
Flooded TBM: A view of the initial inspection after the flood, looking at the machine’s drive motors submerged in seawater.
Hiring a Dedicated Team
Per the scope of work, defined jointly by OHL and Robbins, crews temporarily excluded the cutterhead and main bearing of the TBM for refurbishment, as they were under earth pressure and not accessible. The Robbins team would need to complete the refurbishment taking into account unknowns, such as the condition of the cutterhead. The segmented concrete tunnel lining would not permit the removal of many of the larger TBM components, so these would have to be refurbished onsite.
The Robbins crew was contracted to guide onsite personnel in replacing corroded hydraulic components and installing all new electrical components. Variable Frequency Drives, PLCs, and wiring were replaced inside the small tunnel under atmospheric pressure of 3 bar. Crews constantly monitored earth pressure during the refurbishment. The machine had been stopped with its thrust cylinders in, and thus the crew could not replace or evaluate certain components before the machine started up.
Reverse-Engineering Electrical Components
By mid-December 2013, Robbins PLC technicians were reverse engineering the TBM’s control system. The team understood early on that the previous control programming would be unusable given the PLC change. The technicians had only limited assembly drawings from the CAT manual, so much of the refurbishment, including the PLC system, had to be built from the ground up. The team at site understood how the machine should work and therefore were able to build the correct PLC system.
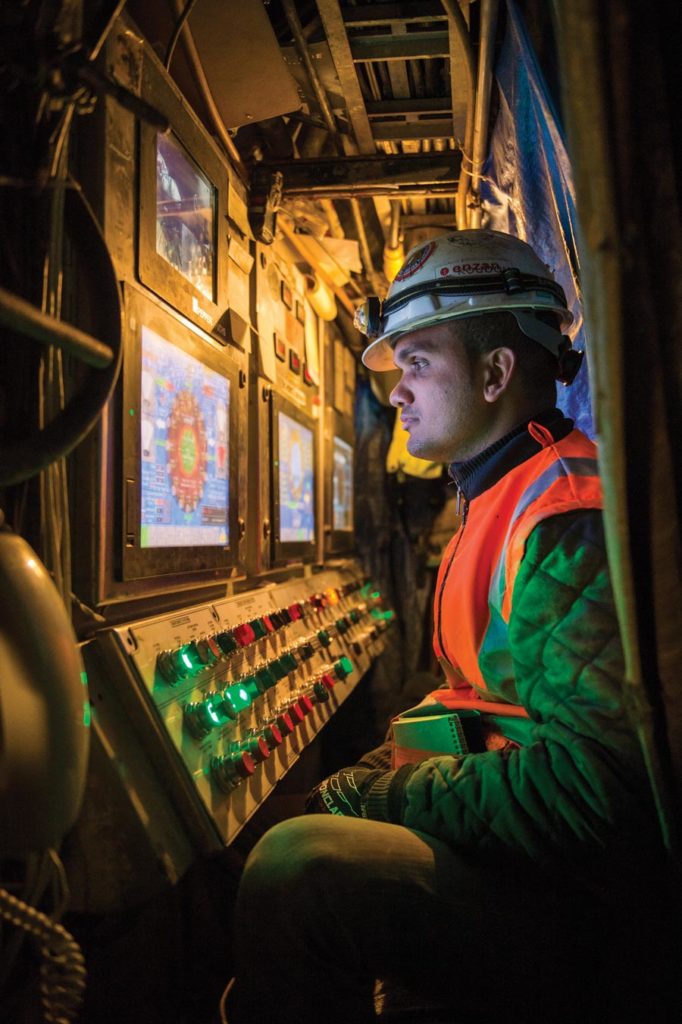
Reworked Electronics: The Harbor Siphons TBM required all new electronic systems.
Coordinating Success
Despite all of the challenges, the refurbishment project was a success. Crews had gone from a shipwrecked TBM—rusted, corroded, and abandoned in the tunnel—to a successful tunneling operation. It was a monumental task, scheduled to be completed in four months, and finished on schedule.
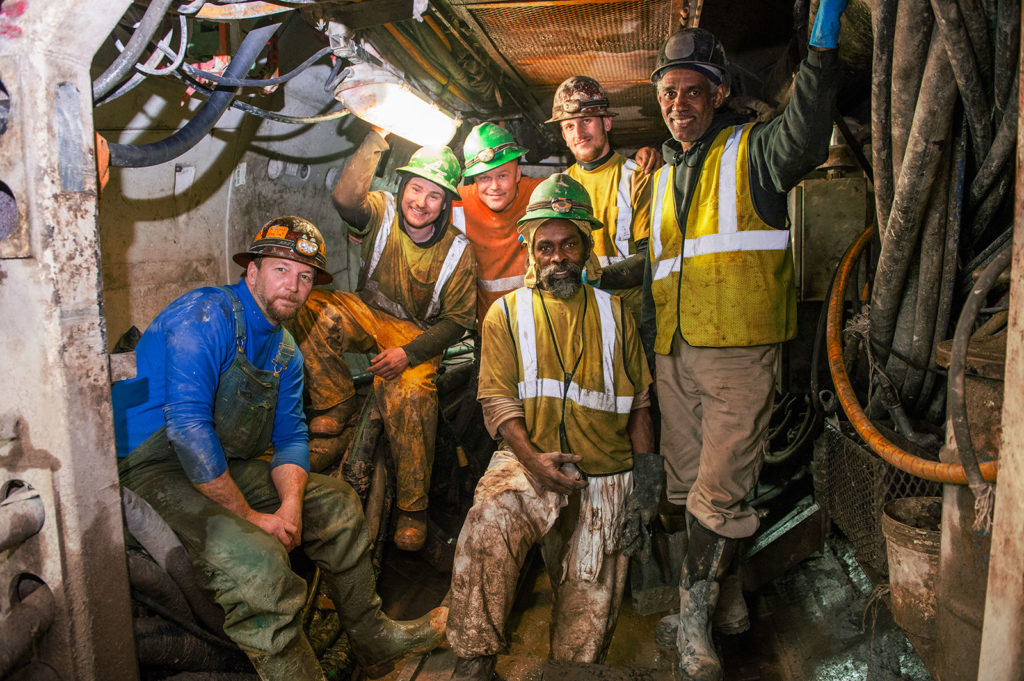
A Good Result: The happy crew during TBM boring, after the full refurbishment.
In the final phase of the refurbishment, a Robbins PLC technician was able to complete the commissioning of the TBM and on April 14, 2014 the machine officially returned to mining. The machine successfully completed its tunnel in February 2015.
Read more in the white paper here.
Make Rock Bursting Conditions Safe for Your Crew: The Olmos Trans-Andean Tunnel
If 16,000 recorded rock bursting events in the world’s second deepest tunnel weren’t enough, the crew at Peru’s Olmos Trans-Andean Tunnel had another problem. As the machine progressed and the cover grew higher—up to 2,000 m at the highest point—the rock bursts became more violent. Crews experienced large over-breaks and cathedralling in fractured and unstable ground. Teams of personnel had to inject concrete into large cavities that had formed during stress-relieving activities and stabilize these cavities with spiling. Then, several kilometers into the tunnel, a major rock bursting event occurred that twisted ring beams and caused damage in 45 m of lined tunnel. Damage was extensive to the TBM gripper, which was ballooned and blown off its mountings. Damage also occurred to other hydraulic cylinders. Thankfully crew members were not harmed, but downtime for repairs would be substantial.
A Century-Long Effort
The Olmos tunnel is a 12.5 km long water transfer tunnel that was bored through the Andes Mountains to bring irrigation to drought-ridden areas on the pacific coast. The project was more than 100 years in the making, with several attempts being made and thwarted by incredibly difficult geology as recently as the 1950s.
In 2007, with Odebrecht as the main contractor, the tunnel was finally completed using a 5.3 m diameter Robbins Main Beam TBM after other attempts with conventional methods failed. The route is the world’s second deepest civil works tunnel with overburden of up to 2,000 m. The tunnel alignment traverses complex geology consisting of quartz porphyry, andesite, and tuff with rock strengths ranging from 60 to 225 MPa UCS. The machine crossed over 400 fault lines including two major faults of approximately 50 m wide.
A Rocky Start
The machine was launched in March 2007, in ground conditions that immediately became more complex than anticipated. As the height of the overburden increased, long stretches of extremely loose, blocky ground were encountered. TBM utilization was as low as 18.7% of working time because rock support installation was requiring a very high 43.5% of the working time.
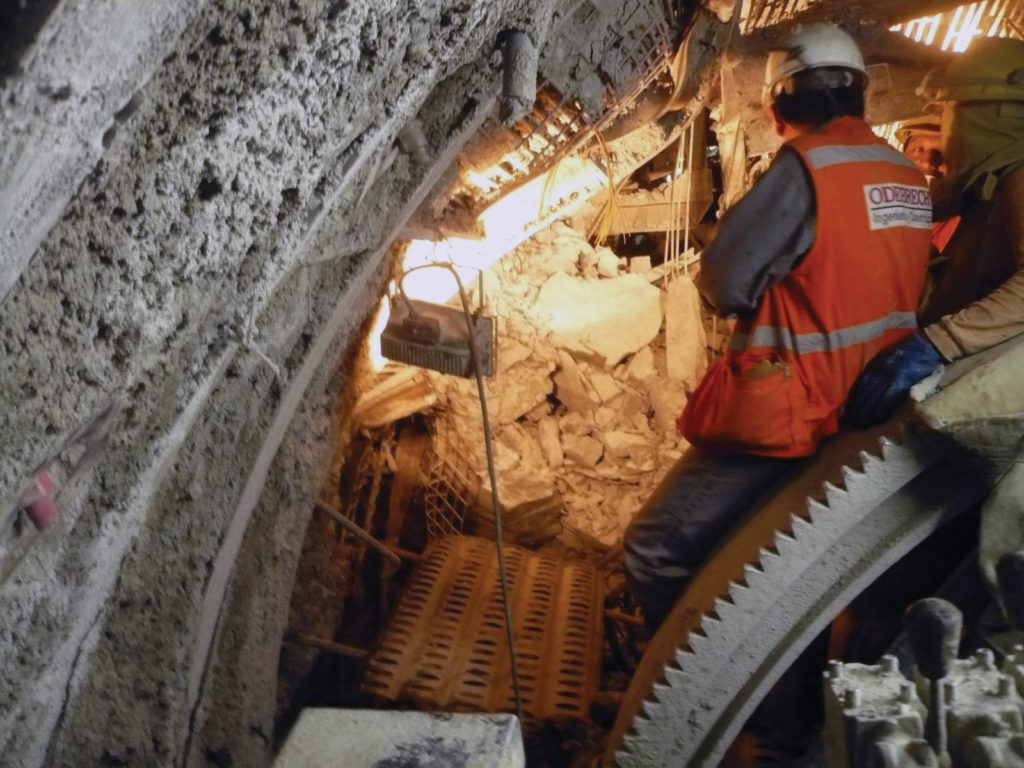
A rocky start: Rock bursting conditions at Olmos prompted a major overhaul of the TBM in the tunnel.
One of the main problems faced was ground deterioration and the resulting falls of blocky ground. The majority of these events occurred during the time taken for the newly excavated bore to pass behind the rear fingers of the roof shield, where ring beams and mesh were installed.
Modifying the Machine in the Tunnel
During consultations between Robbins and Odebrecht, a decision was made to modify the machine in the tunnel. The TBM would be reworked to use the McNally roof support system, which allows support to be installed directly behind the main roof shield. Crews removed the roof shield fingers and installed a series of rectangular pockets in their place. The pockets ran from the rear side of the cutterhead to the trailing edge of the roof support. These pockets were designed to be used with rebar, which is part of the McNally Roof Support System. At a later stage when the ground conditions worsened these pockets were extended to cover the sides of the TBM as well.
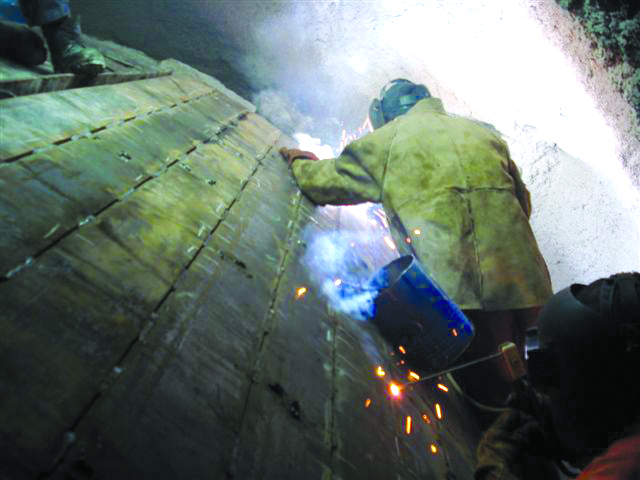
TBM Modifications: The crew add McNally pockets to the TBM roof shield in the tunnel.
The McNally Support System
One big advantage of the McNally support system is that it is possible to install ground support closer to the face than other ground support methods used on TBMs. It holds loose rock in place, which in turn helps to activate the strength of the rock mass and maintain the inherent strength of the tunnel arch. When used correctly the system can significantly reduce the time taken to provide adequate support. It can also offer reductions in the level of support required, and contain rock bursts and collapsing ground. The greatest benefit of the system, by far, is its ability to provide a much safer work area.
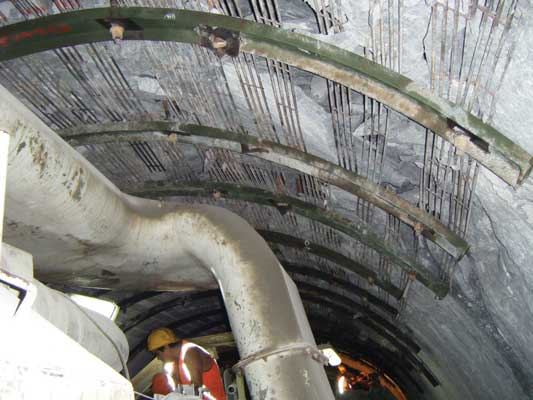
Crown Control: McNally slat installation at the Olmos Trans-Andean Tunnel.
Incorporation of the McNally support system and various other modifications to the TBM resulted in a steady increase in production rates in spite of continuous rock bursting events. The machine broke though in December 2011 having achieved production rates in excess of 670 m a month.
Read more about the McNally Support System here.
Make short work of an unforeseen cavern: The MKTVARI project
The Republic of Georgia’s Mktvari Hydropower Plant Construction project, along the river of the same name, was a challenge from the outset. The initial contractor used drill and blast for the 9.5 km long headrace tunnel through hard rock, but after 1.5 years they had only advanced about 200 m. The new contractor took over a previously-ordered non-Robbins hard rock machine but enlisted Robbins to help with the TBM assembly. They also wanted Robbins to be available if problems occurred. The machine did well at the outset, boring up to 900 m per month. But then, the machine hit bad ground.
Cavernous Conditions
Crews hit an unforeseen cavern above the TBM and were unsure of how to proceed through mixed layers of breccia, andesite, and bands of clay with light water inflows. A Robbins Field Service Manager was sent to the site, where he determined that the cavern was part of a fault zone consisting of unstable material that fell onto the cutterhead. At the time of his arrival, the TBM had passed through most of the fault zone but huge voids were left behind the segments.
Using pea gravel pumped through holes drilled in the segments, combined with cementitious grout, the crew was able to stabilize the existing segments and safely advance through the cavern in about 10 additional segments. There was also a probe drill onsite that had not been used; the Robbins manager persuaded the crew to install the probe drill and conduct systematic probing ahead of the machine, in case a larger section of clay was encountered.
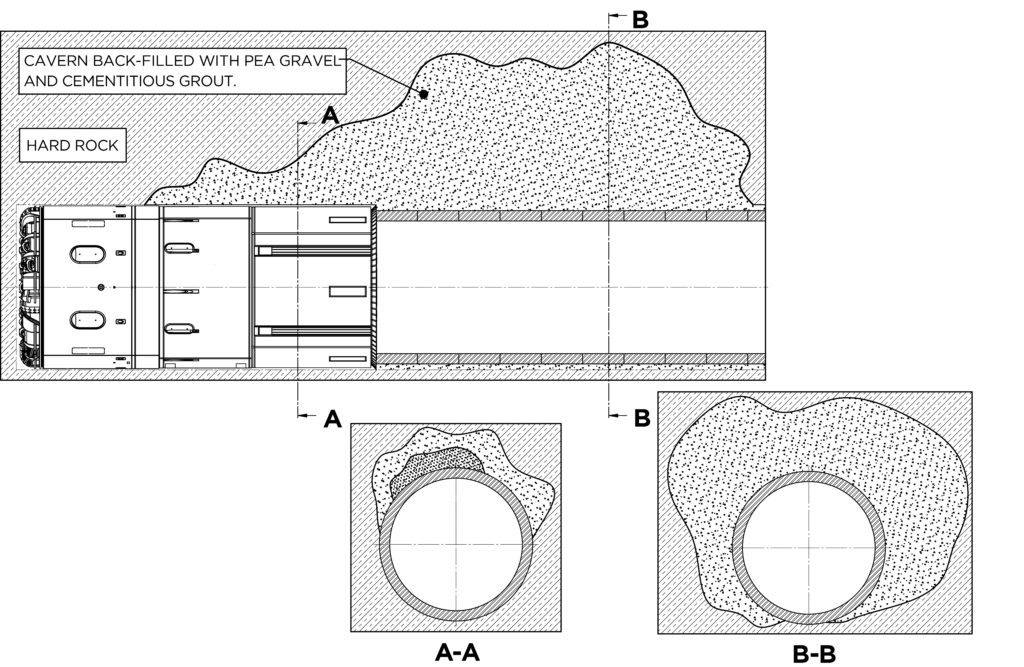
Crossing the Void: Robbins worked with the contractor to backfill the cavern, enabling the crew to advance out of the void in 10 additional segment rings.
Key Takeaways
As can be seen in these examples, planning is key. But, even the best-laid plans can go awry. When conditions go from bad to worse, having an expert team of personnel on your side is by far the most valuable tool and the most positive predictor of a project’s ultimate success. That true story I started off with certainly wasn’t the first such incident in the tunneling world, and it won’t be the last. Be prepared by arming yourself with knowledge, and with a knowledgeable team.
Information at your Fingertips
Learn more about our vast experience in difficult ground conditions. Our selection of white papers covers some of the world’s most challenging projects, while our Project Solutions section offers many examples of past successes.
老罗宾斯掘进机在防洪做贡献
在美国伊利诺伊州芝加哥市,肯尼建筑公司建造(KennyConstruction)的奥尔巴尼公园雨水导流隧道即将完工。该项目由芝加哥交通部所有,将从奥尔巴尼公园附近调水,奥尔巴尼公园附近长期受洪水困扰。隧道计划于2013年开始实施,洪水条件变得如此恶劣,居民不得不乘船撤离该地区。预计该隧道将于2018年4月投入使用。
2017年8月底,罗宾斯主梁式硬岩隧道掘进机在隧道内开挖隧道并贯通,使该项目更接近完工。这台掘进机,也被称为“Keri”,自20世纪90年代以来一直为项目承包商肯尼建筑公司所有,以前曾用于多个项目。肯尼建筑公司的项目经理Clay Spellman说:“这台机器掘入了进水井。我们挖掘了竖井作为项目的一部分。此后,机器已被拆卸和运走。”
在奥尔巴尼公园项目中,Keri是由肯尼建筑公司翻新的,由罗宾斯设计。罗宾斯取了一个现有的刀盘,对其进行了修复,然后增加了一些部件,把刀盘从直径5.2米改为6.2米。 Spellman补充说:“在地下对机器进行了广泛的改造,使其能够安装岩石定位销钉,并将环钢置于顶盾下。”
“翻新和改造掘进机一直是罗宾斯业务的核心部分。大多数客户都会立即意识到,一台经过改造的具有更新系统的机器可以在不增加风险的情况下提供卓越的价值,而一台经过改造的机器通常可以更快地交付,”罗宾斯工程经理 Steve Smading说。“虽然财务和进度优势明显,但所用设备的灵活性可能不太明显。我们可以增大或减小掘进机的掘进直径,甚至可以更改机器构造。例如,可以将单护盾掘进机重新改造为双护盾,反之亦然,并且可以将开放主梁式掘进机重新改造为护盾式掘进机。复合软土地面机器可以为不同的地质重新改造,可以设置为泥水平衡或土压平衡。”
罗宾斯公司生产的所有主梁式掘进机中,有超过50%用于三个或更多的项目。令人难以置信的是,许多已用于多个项目的罗宾斯隧道掘进机的使用里程已接近50公里。在被肯尼建筑公司拥有之前,Keri已经在多米尼加共和国、沙特阿拉伯、纽约和芝加哥成功地开挖了总长度至少19.5公里的隧道。
由于项目地点位于居民区,因此对机器的运行时间和每天允许开挖的频率有限制。尽管存在这些限制,但隧道掘进机的最佳日掘进为39.5米,最佳周掘进(5天)为146.4米。这台机器开挖白云石,平均抗压强度为64兆帕。 Spellman说:“在掘进过程中,我们遇到了大约30.4米的断裂地面,这些地面必须由轧制的槽钢、钢带和19个全圆钢圈支撑。”
排水隧道始于尤金公园(Eugene Park),在福斯特大道下延伸约一英里至北岸航道。当芝加哥河的水位达到超过2米的洪水位时,隧道将使65立方米的水流每秒转向,避开奥尔巴尼公园,然后将其沉积到河道中。这条隧道将基本上把水转移到原本会结束的地方,而不会破坏居民区或对河流的野生动物造成不利影响。
罗宾斯主梁式在中国刷纪录
在中国东北三省之一的吉林省,一台直径7.9米的罗宾斯硬岩主梁式掘进机在一个月以1,423.5米刷新了7至8米直径类别掘进机的全国纪录。这一记录刷新了同一项目在2017年早些时候取得的创纪录成就,当时掘进机在一个月内以1,336.8米的速度前进。
这个直径类型的世界纪录是由另一台罗宾斯机器保持的,这台机器是20多年前在美国伊利诺伊州芝加哥的隧道和水库计划(TARP)上创下的,一个月内达到1,482米。然而,鉴于岩石条件的差异,吉林项目的记录非常重要。在油布中,岩石是相对均匀的白云岩灰岩,平均强度达145兆帕,偶尔有岩石锚杆;在吉林,岩石类型为35至206兆帕,包括有凝灰岩、花岗岩、砂岩和安山岩,具有多个断层带地质条件,几乎需要连续的围岩支护。
尽管条件困难,但自2015年3月开始掘进以来,吉林机械的月平均推进率为708.3米,是该项目另一部分钻爆作业月平均推进率的三倍多。“现在很明显,装备精良的开放式主梁掘进机,具有特殊的困难地面特征,能够比传统的掘进方法更快地穿越断层和大的进水量。这一事实,再加上吉林所展示的高性能,降低了在困难地区完成长隧道的成本和时间。” 罗宾斯总裁Lok Home说。
作为一项水利工程的一部分,吉林三标段隧道将在完工时长24.3公里。根据承包商北京振冲工程有限公司(BVEC),截至2018年1月,该机器已挖掘了14公里的隧道。
在整个掘进中,预计主梁将穿过总共24个断层带。隧道掘进机是根据设计的,配备了四个凿岩机、顶盾有麦纳利钢精排储存仓,以便安装麦纳利板条、环形梁安装机和喷射混凝土系统。麦纳利板条用于隧道遇到的困难地质。
吉林TBM的第一个断层带是在掘进了仅87米的后遇到的,需要业主、吉林省水利投资集团有限公司、承包商北京振冲和罗宾斯现场服务部门的合作。在长度为1196 米的路段中,进水和坍塌的地面通过麦纳利支护板条、注浆和机器前方地面加固的组合来解决。围岩支护总体由钢丝网和喷射混凝土组成。隧道反射层析成像(TRT)——一种利用地震波进行地面预测的方法,也被用于探测隧道掘进机前方的变化情况。
尽管存在最初的挑战,但掘进机现在每天的前进速度在40到60米之间。“我和我的同事都认为罗宾斯掘进机非常容易操作。系统的所有组件在操作过程中都工作良好,这确保了我们的良好进展,”北京振冲吉林第三标段掘进机现场经理陶勇说。
吉林三标段隧道是吉林引松供水工程的一部分,该工程将向吉林省中心城市输水。大型跨区域引水工程是吉林省历史上最长的供水线路,全长263.5公里,受益者最多。总工程师。该建设项目将把第二松花江上游的丰满水库的水引至长期缺水的吉林省中部地区。这些地区包括长春市、四平市、周边8个县、所辖26个乡镇。预计2018年底完成隧道施工。
世界第一台输送机系统的诞生
Modern Achievements
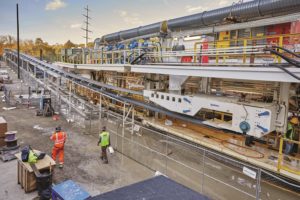
The 100th conveyor system has been refurbished and customized for the job in a process that Robbins has been perfecting for decades.
There are many elements that contribute to the success of a project: having an accurate report of ground conditions, choosing the proper equipment, having a well-trained team operating the tunnel boring machine—and behind it all—the utilization of a high-quality conveyor system. As tunneling machines evolve and bore at continuously faster rates, rapid muck removal becomes more important than ever. Robbins conveyor systems are capable of moving more than two thousand US tons of muck per hour—saving time and money on every project that uses the complete system.
In Akron, Ohio, a major milestone has been reached for Robbins conveyors. Running behind a Robbins 9.26 m (30.4 ft) diameter Crossover TBM is the 100th Robbins Continuous Conveyor System supplied for muck removal—more than any other TBM conveyor supplier has sold. The conveyor in Akron is just one landmark event in the long history of Robbins conveyors, the start of which can be traced back to the first ever documented use of a continuous conveyor system behind a TBM.
Pioneering Muck Removal
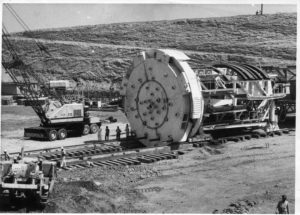
No roads were at the site in West Pakistan so goods were transported by rail car, requiring surveying of hundreds of bridges from the port city of Karachi.
The prototype for the conveyor systems we know today was developed by James S. Robbins in 1963 and was built using a Goodman coal-mine conveyor instead of muck cars which were more commonly used during that period. The conveyor ran behind what was, at the time, the largest TBM in the world. The 11.2 m (36.7 ft) diameter Robbins Main Beam was built for the Mangla Dam Project in what was then known as West Pakistan. The 4.3 km (2.7 mi) long tunnel was built to control water flow from the Jhelum River for use in agriculture and hydro-electric power.
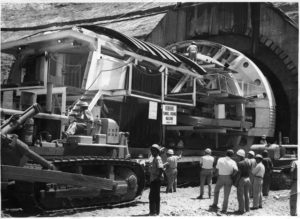
Temperatures at the jobsite climbed up to 53 degrees C (127 degrees F) in the shade.
The conveyor design had originally been used for coal and potash mines and was adapted for use behind the TBM. An extendable belt was side-mounted in the tunnel, leaving room for man-access and rail tracks to carry materials. Belt tension was maintained using a belt cassette. “They were able to operate continuously. It worked like a charm—and then the extensible conveyor was forgotten by the industry because it was perceived by contractors and owners as too much of an investment,” explained Dick Robbins, former President and CEO of The Robbins Company, in a 2013 article for World Tunnelling. It would be another 30 years after the successful completion of the Mangla Dam tunnel until conveyors became a standard means of muck removal in the tunneling industry.
Persistently Moving Forward
Conveyors have come a long way since their first use. Unlike the system used for the Mangla Dam project—which was limited to the use of a straight belt—conveyors can now wrap around curves and bring rock vertically up a shaft to the surface. “The control system, along with monitoring systems, has dramatically improved,” says Dean Workman, Robbins Director of Conveyors, Cutters, and SBUs. “The components have all been enhanced, giving a much longer life to the conveyor system. Contractors are using the same conveyors on multiple projects with minor refurbishments between projects.” While the basic function of a conveyor has stayed the same—muck hauling—the quality of conveyor systems has certainly changed.
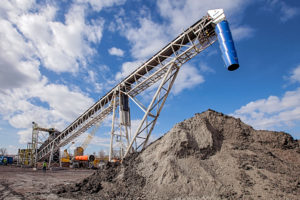
Did You Know: At least 75% of all world records achieved by TBMs were done with a continuous conveyor system for spoils removal rather than muck cars.
In a new design that is being used for the Los Angeles Purple Line Extension, continuous conveyors have gained another ability, they are now able to change direction. The unique system can be flipped to accommodate two machines boring parallel tunnels eastward before being re-launched to bore west. Due to the narrow launch shaft, modular components were designed to save space, and were built using a kit of secondhand parts, showcasing the long-life conveyor systems are capable of. “We are always looking to improve the design and function of the system,” says Workman, “modular components are a benefit to the contractor when installing, maintaining, and shipping the equipment.”
As progress continues and new technology provides advancements for the industry, The Robbins Company continues to uphold the pioneering spirit that James S. Robbins brought to tunneling with his trailblazing developments.
Read More:
Robbins Conveyor Systems
Conveyor Spec Sheet
100th Conveyor
2018世界隧道峰会
Event Name: WTC 2018
Dates: April 21-26, 2018
Location: Dubai, United Arab Emirates
Venue: Dubai World Trade Centre
The Robbins Company will be attending ITA-AITES World Tunnel Congress 2018 in Dubai, United Arab Emirates, April 21 through 26. Be sure to visit us at stand 70-71 between April 23 through 25 to learn more about Robbins TBMs operating world-wide.
Robbins Presentations
Monday, April 23
14:20 – 14:40 Robbins Vice Present Doug Harding, “Excavating Turkey’s Hardest Rock at the Bahce-Nurdag Railway Tunnel”
Wednesday, April 25
9:40 – 10:00 Robbins Director of Engineering Brad Grothen, “Excavating Turkey’s Most Challenging Project – The Gerede Water Transmission Tunnel”
12:15 – 12:35 Robbins Mexico Managing Director Roberto Gonzalez, “Excavating Mexico City’s Mega-Tunnel in Mixed Ground at 150 Meters Deep: Emisor Oriente Wastewater Tunnel Lot 5”
2018北美非开挖技术峰会
Event Name: NASTT’s No-Dig Show 2018
Dates: March 25-29, 2018
Location: Palm Springs, CA, USA
Venue: Palm Springs Convention Center
The Robbins Company is looking forward to seeing you in Palm Springs, CA for NASTT’s No Dig 2018 March 25 through 29. Visit booth 470 during exhibit hours to discover how renting or owning a Robbins Small Boring Unit (SBU) can save you time and money on your next boring project.
墨西哥全国土木工程师大会
Event Name: Congreso Nacional de Ingenieria Civil
Dates: March 1-8, 2018
Location: Mexico City, Mexico
Venue: World Trade Center
Join The Robbins Company at Congreso Nacional de Ingenieria Civil March 1 through 8, in Mexico City, Mexico. Visit our booth to learn more about current techniques being used on Robbins projects throughout the world.