Author: Keri Lin
2018地下施工技术峰会
Event Name: Underground Construction Technology (UCT) 2018
Dates: January 30-February 1, 2018
Location: New Orleans, LA, USA
Venue: Ernest N. Morial Convention Center
The Robbins Company will be attending Underground Construction Technology 2018 January 30 through February 1. Be sure to visit our booth to learn more about Robbins Small Boring Units (SBUs)—the most cost effective and time efficient way to bore through hard rock.
这一季度世界各地的工地发生了什么?
At any given time, Robbins TBMs are operating at dozens of jobsites around the world. Our dedicated Field Service personnel take video and pictures of the TBM progress often, so we’ve decided to offer a quarterly roundup of what’s going on in picture and video format–from deep TBM assembly in New York, USA to an epic TBM launch in the Himalayan mountains of Nepal. Read on to found out the latest.
TBM Assembly in a Deep Shaft in New York, USA
A 6.8 m (22.3 ft) Robbins Single Shield TBM, designed for water pressures up to 20 bar, is undergoing assembly and testing at the Delaware Aqueduct Repair Project. The TBM will be launched from a starter tunnel at the bottom of a 274 m (900 ft) deep shaft.
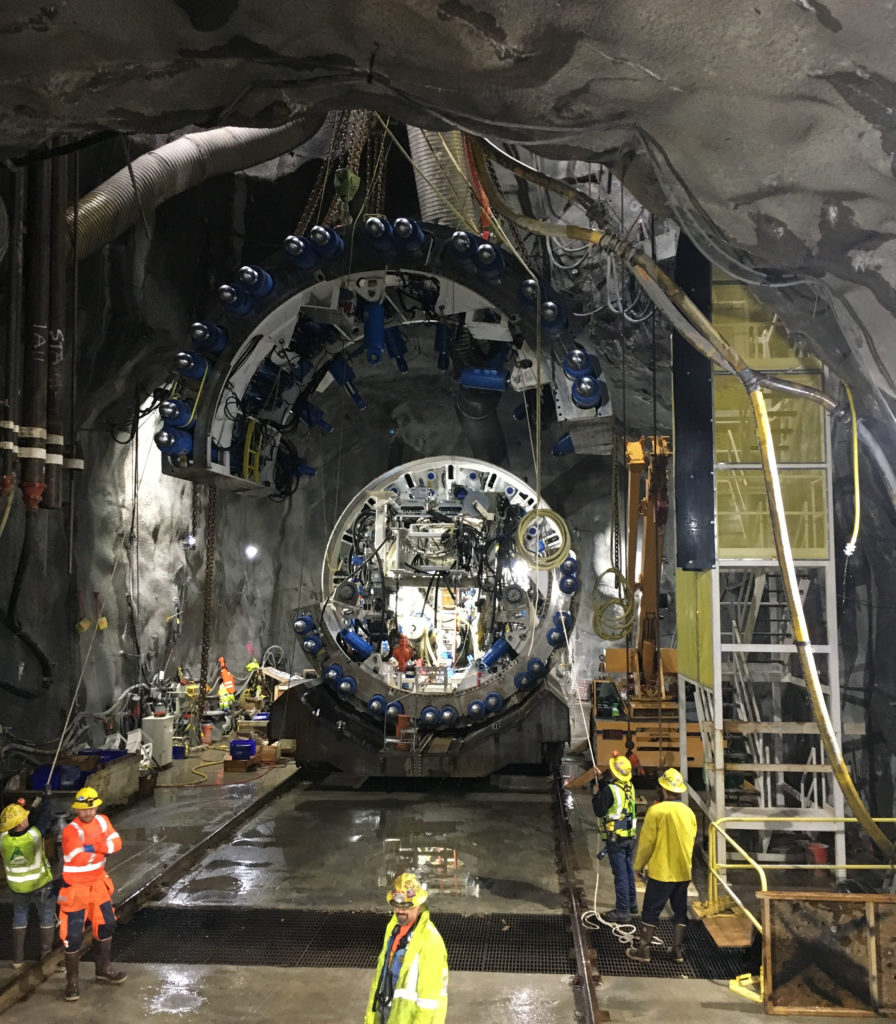
TBM Assembly at the Delaware Aqueduct Repair in Newburgh, New York, USA. The shaft is an incredible 274 m (900 ft) deep.
TBM Assembly Time Lapse
Epic TBM Launch in the Himalayan Mountains
In the Siwalik Range of the southern Himalayan Mountains of Nepal, a 5.06 m (16.6 ft) Robbins Double Shield embarked to bore the Bheri Babai Diversion Multipurpose Project (BBDMP). The TBM launched on October 14. See the drone footage taken by our own Field Service TBM Mechanic Thomas Fuchs:
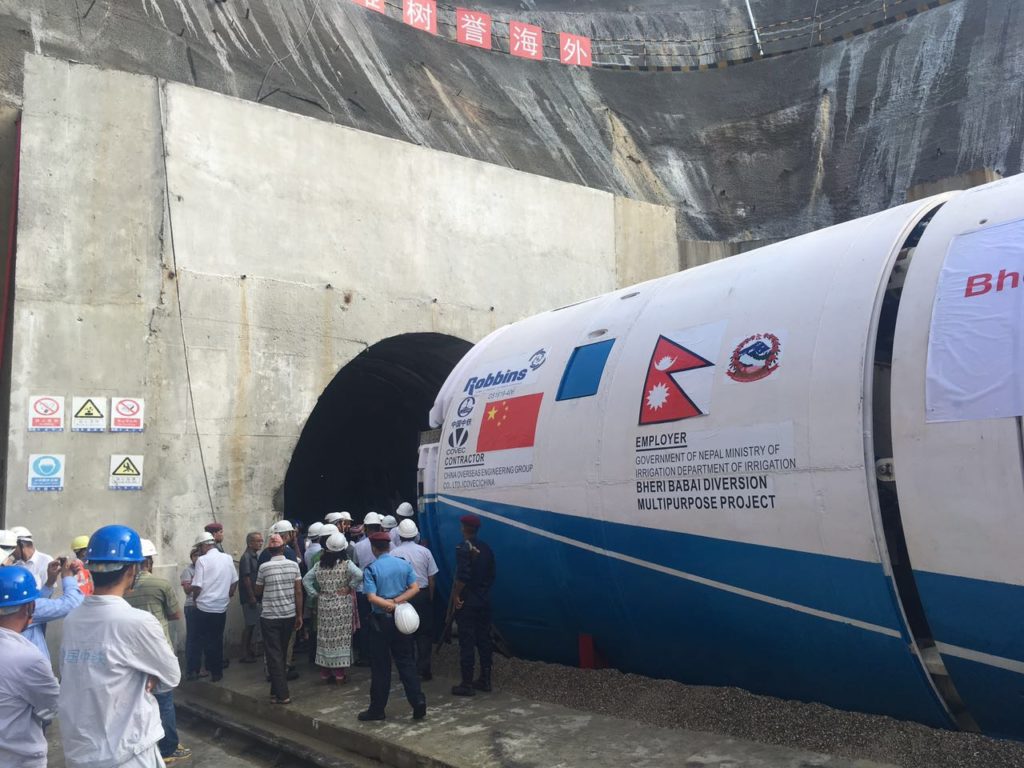
Launch of the Robbins Double Shield at Nepal’s BBDMP on October 14.
Crossover Machine Startup in Akron, Ohio
On October 19, a Robbins 9.26 m (30.4 ft) diameter Crossover (XRE) TBM launched below Akron, Ohio, USA to bore the OCIT tunnel. The machine is excavating in soft soils that will transition into mixed face and then full face shale. Before its launch, personnel at the jobsite filmed the cutterhead testing in a unique way. Watch the video below for more:
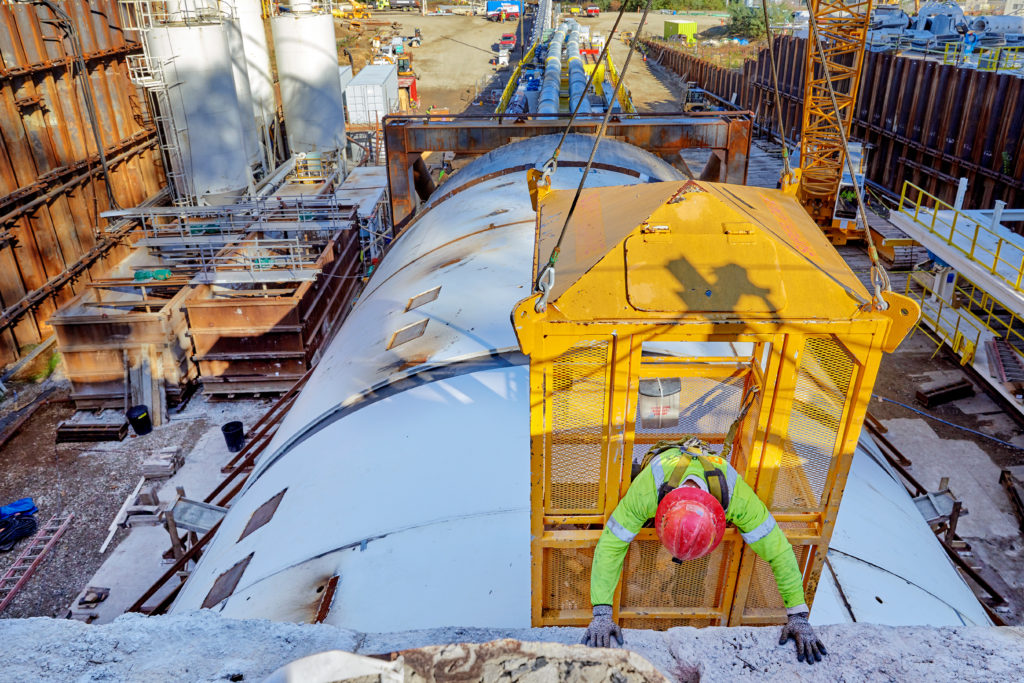
A worker surveys the TBM prior to its launch on the Akron OCIT October 19.
坚固的罗宾斯盾构机为金奈地铁项目完成第三次开挖
2017年10月31,直径6.65米罗宾斯盾构机贯通了钦奈地铁隧道,这是这台机器为承包商Afcons基础设施有限公司在这个项目中贯通的第三段隧道。采用这台盾构机开挖三段独立的隧道是一个增长趋势,许多罗宾斯盾构机重复使用于多个项目都有十分好的性能表现。罗宾斯盾构机比市场上其他盾构机重量多重1/3倍,其设计的使用寿命为10,000小时。这让他们成为在可以开挖许多公里数的理想设备。“罗宾斯的设备也以适用性强闻名,”承包商Afcons高级经理Gopal Dey说道。“为这个项目,我们需要的机器,具体来说是为项目的地质条件从粘土到混合地质到硬岩地质量是定制的。罗宾斯盾构机有独特为地质优化的设计特点。”
在完成其原来的两条隧道后,盾构机进行了翻新,准备开挖其最新的长1.8公里路段。在翻新过程中,内密封润滑系统由自动切换到手动模式,并对泡沫喷嘴系统进行了改造。这些变化使机器在前两个隧道遇到的高度可变的混合面条件下进行了优化。
这台盾构机于今年早些时候于2月3日始发。根据承包商AFCONS的说法,这台机器面临着一个巨大的挑战。AFCONS总监Manivannan先生说:“当掘进机从始发井出来时,安装了几个环,然后机器必须穿过一条带电的铁路轨道,这意味着有可能发生地表沉降。在这一阶段,我们必须密切监测掘进机的工作面压力,以均匀的速度推进机器,以确保适当的一次注浆。”掘进的地质主要由粘土砂和大约60米的混合地质组成。
Dey说:“我们(AFCONS)之所以选择这台机器是因为钦奈的地下地质情况不断地从土壤变为混合地质。我们还喜欢罗宾斯盾构机的主动铰接系统设计,使机器能够轻松转动或转向。”在主动铰接下,推力油缸对隧道衬砌的整个圆周均匀作用,即使是在曲线隧道,这种设计消除了隧道衬砌变形的问题。”这一特性使机器能够在良好的控制条件下穿越隧道,” Manivannan补充说。
在开挖所有三条隧道中,罗宾斯现场服务人员都在现场,根据需要提供协助和支持。在每次掘进过程中,罗宾斯都会向AFCON建议如何在具有挑战性的地面上进行最佳操作,并为机器操作提供指导。正如罗宾斯和AFCON在整个合同中所说,承包商和制造商的良好合作能力对良好的掘进率至关重要。其结果是一个强大的机器,在具有挑战性的条件下以每分钟80毫米的速度前进。
这条最新的隧道连接了地铁沿线的多个车站,从Washermenpet到Sir Theagaraya和Kurukpet。金奈地铁项目将为快速发展的城市提供急需的交通工具。
2017土耳其隧道展
Event Name: Tunnel Turkey 2017
Dates: December 2-3, 2017
Location: Istanbul, Turkey
Venue: Wyndham Grand Istanbul Levent Hotel
The Robbins Company will be exhibiting at the 2017 International Tunneling Symposium, also known as Tunnel Turkey, in Istanbul December 2-3. In keeping with this year’s theme, “Challenges in Tunneling,” stop by stand S-4 to learn more about how Robbins overcomes our own challenging projects.
During the conference, be sure to attend, “Use of dual mode, crossover TBM to excavate challenging geology at Mexico City’s Emisor Poniente II Waste Water Tunnel” presented by Robbins Public Relations Manager, Desiree Willis. The presentation will take place on Saturday, December 2 at 2:00 pm.
罗宾斯第一百台连续输送机
2017年10月18日,为美国俄亥俄州开挖阿克伦俄亥俄运河拦截隧道(Akron OCIT)的一台直径为9.26米的大直径跨模式掘进机始发。但这个始发并不是唯一的里程碑。在跨模式掘进机后运行用于出渣的,是第100台罗宾斯连续输送系统。侧置式输送机是一种设计标准,但它的里程碑意义重大:“这台输送机的诞生,让我们成为供应输送机数量最多的掘进机输送机供应商,”罗宾斯输送机、刀具及小型掘进机分布总裁Dean Workman说道。Workman补充说,罗宾斯按订单计算输送机的数量,包括准备发货的,数字现在已经超过了100台。
Akron OCIT输送机系统包括皮带+主驱动、插接机架、存储部件,以及前进尾件,通过几条曲线运行,配备具有专利的自调式曲惰轮,根据不同的皮带张力和皮带负荷进行校正运行。该系统会把渣土排放到定制的地面输送机,然后再把渣土送往入口附近的一个大型堆场。这条输送带设计用于处理多变地质,从软土到部分面岩,最后是全段面页岩。
在罗宾斯几十年来不断完善和改良,第100台输送系统已经被翻新和定制。“我们设计的输送机系统可以工作5到10年,但很多都工作了几十年。”我们有系统采用已经运行了30年的组件。我们的许多系统还没有达到一个极限——例如,我们很特别的输送机系统,十多年前为澳大利亚悉尼的Parramatta铁路连接隧道上制造。这些组件在佐治亚州亚特兰大的项目得到了翻新,现在他们又在印第安纳州印第安纳波利斯的挖掘隧道中使用。这些都是很长很有挑战性的隧道驱动器,组件都是由它决定的。虽然Akron OCIT输送机刚刚开始运输淤泥,但在整个项目的不同地面条件下,它肯定会受益。
在阿克伦的输送机也是罗宾斯输送带的历史的一部分,这个产品是第一台在掘进机后使用的连续输送系统。该原型机由创始人詹姆斯·S·罗宾斯(James S. Robbins)于1963年发明,在当时被称为西巴基斯坦的曼格拉大坝项目中成功地在直径11.2米的主梁式掘进机中使用。虽然输送带在发明后来的多年没有被作为一种标准的出渣方法,但这个项目为未来的成功奠定了基础。
今天的输送机系统可以跨越几十公里,运输量达1800吨(2000吨)一个小时或更多。Workman认为这个历史遗产会继续发扬光大:“这是我与罗宾斯的第20年,我还记得我们开始我们着手记录传送机的名单。看着所有的付出和成果,真是太棒了。看到这些系统完成不同的项目任务真是太棒了。
在蓝山下掘进:世界最快的掘进机的内幕故事
Over 20 years ago, a Robbins open-type machine set three world records while tunneling in the picturesque Blue Mountains in Australia. You may be asking yourself, why is this significant? Why drudge up a project that is surely outdated at this point in our industry’s history? The fact of the matter is, two decades have passed and the Robbins open-type TBM chosen for this project is still considered to be the world’s fastest TBM.
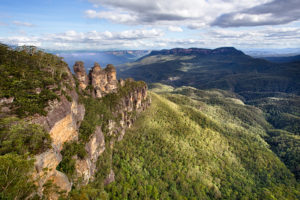
The picturesque Blue Mountains in New South Wales, Australia.
Project Background
In 1993, the 3.4 m (11 ft) diameter TBM was chosen to bore two sewage tunnels in the Blue Mountains near Sydney, Australia. At the time, there had been a rapid expansion of urban developments within the Blue Mountain National Park, causing an influx of pollution to enter streams as the result of septic tank runoff and outdated sewage treatment plants.
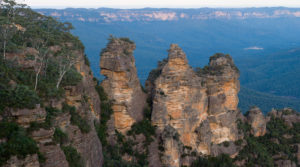
A closer look at the Three Sisters, a unique rock formation in the Blue Mountains.
The Blue Mountains Sewage Transfer Project comprised of approximately 40 km (25 mi) of tunnels, two of which were TBM-driven using the Robbins machine. The first, the Katoomba Carrier tunnel, was 13.4 km (8.3 mi) long and the second, the Lawson Carrier, was 3.5 km (2.1 mi) long. While the Lawson Carrier tunnel was finished five weeks prior to the expected completion date, it was during the Katoomba Carrier tunnel that all three records were set. During excavation the machine set the following world records: best day of 172.4 m (565.6 ft), best week of 702.8 m (2,305.7 ft), and a best monthly average of 1,189 m (39,000 ft) within its size range of 3 to 4 m (9.8 to 13.1 ft) diameter machine. Two of those records—the best day and best week—are the fastest ever recorded and have yet to be surpassed by any TBM of any size.
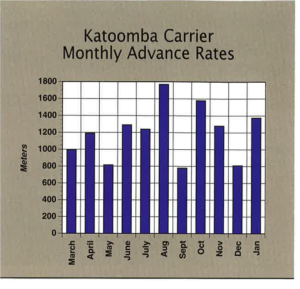
The 3.4 m (11 ft) diameter TBM set three world records while boring the Katoomba Carrier tunnel. Photo credit: tunneltalk.com
Custom Machine Design
There were many factors that played into this machine’s success—the system utilized on this project required a well-planned design, careful operation, and regular maintenance. As many people involved in tunneling know, choosing the right equipment for the geology can make or break a project. Detailed empirical data allowed the contractor to accurately predict what kind of ground they would encounter and prepare accordingly. The National Park is located within the Triassic Sydney Sedimentary Basin and is comprised primarily of sandstones and claystones. Anticipating this geology, the 3.4 m (11 ft) diameter machine’s cutterhead was dressed with 25 Robbins 17-inch diameter disc cutters designed for soft yet abrasive rock formations.
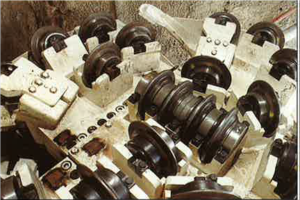
A close-up of the 17-inch cutters.
Logistics
The 13.4 km (8.3 mi) long Katoomba Carrier tunnel was originally planned to comprise of multiple short tunnels, several kilometers in length each, with intermittent portals to shorten drives. Ultimately it was decided to make the project one continuous tunnel, which led to higher advance rates and deemed it—at the time—the longest single-drive TBM tunnel. Not only did this change save time, but it also allowed boring to be less disruptive to the landscape.
Continuous Conveyor
In addition, the project was the first in Australia to utilize a continuous conveyor system. Due to the length of the tunnel, the use of traditional muck cars for muck removal would have taken too much time and were seen as an inadequate solution. The 106-m (347.8 ft) long system boosted production rates, with a best day of 1,565 m³ (55,267 ft³) of in-situ material removed from the Katoomba tunnel.
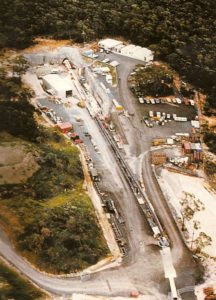
The Blue Mountains project was the first TBM-driven tunnel in Australia to utilize a continuous conveyor system.
Good Geology
Ground support throughout the tunnel comprised of a combination of resin grouted bolts, mesh, steel straps and steel sets. In the sturdier sandstone, however, the tunnel was left largely unlined and instead shotcrete was applied to areas of poorer, softer rock.
As boring progressed, the sandstone proved to be softer than expected. Instead of the predicted average of 80 MPa ranging from 20 MPa to 150 MPa, it averaged 40 MPa to 50 MPa with a range of 10 MPa to 100 MPa. This ideal material could also have contributed to the Robbins machine’s record breaking results and its early breakthrough, which occurred nine months ahead of schedule.
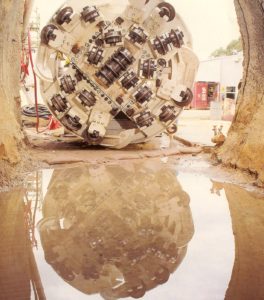
The machine’s record breaking boring enabled the project as a whole to finish 17 months ahead of schedule.
Exceeding Expectations
The Robbins Mk 12C’s performance on the tunnel boring portion of the project substantially surpassed all expectations. Not only did it set the previously mentioned world tunneling records, but it also helped the project as a whole finish 17 months ahead of schedule, saving not only on time but on significant financial costs.
您在操作掘进机开挖困难地质5项可以做的事
Difficult Ground Solutions (DGS) is a suite of options that can be added to a shielded hard rock machine or Crossover machine to better enable advance when conditions are unknown or difficult conditions are anticipated. While each of these items is not new, the concept of installing them on a machine from the start, and of using them in concert to provide better visualization and performance in the most challenging ground, is. The uses and advantages of DGS are various and wide-reaching.
Number 1: DGS can act like risk insurance.
Yes, risk insurance. While one can argue that risk insurance is not needed—and of course if a tunnel were in entirely homogeneous, medium strength, self-supporting rock, under a medium amount of cover, I would tend to agree—there is a problem with this argument. That scenario exists only very rarely. At Robbins, we are seeing more tunnels being planned in mountainous, remote regions where an accurate GBR cannot be obtained. More tunnels planned through multiple fault zones and mixed face conditions. More tunnels planned in suspected karst conditions and in rock where large water inflows may occur. It is a trend we’ve observed arcing upward, and with these high-risk projects it seems prudent that an equipment manufacturer should strongly recommend risk insurance. We’ve done that the only way we know how: by calling on our extensive experience to develop, test, and provide various solutions that can be added to a TBM at the beginning of the project. These features mitigate the risk of getting stuck in unforeseen (or foreseen) challenges that might come up in a tunnel drive.
This risk insurance works like any other type of insurance—it must be purchased before the actual event happens. Waiting until a machine encounters a given challenge—where it may become damaged, stuck, or irretrievable—is not an adequate plan for difficult conditions. Sure, some of these options can be added in the tunnel, but such an operation is far from ideal. Risk insurance is best purchased during the TBM design phase, long before the machine is built and launched.
Number 2: DGS can get your TBM through a fault zone or squeezing ground where it might otherwise become stuck.
If fault zones or squeezing ground are known or suspected, or if there is even a possibility of encountering them, this can greatly affect your TBM operation. Shielded hard rock machines protect your crew from the surrounding ground, and they can bore and line a tunnel efficiently, but in fault zones and converging material they need some of the features of an EPB machine to keep advancing. Avoiding a stuck machine is paramount to project success. Luckily, DGS uses several ways to avoid the problem of a machine becoming stuck. The first of these is multi-speed cutterhead drives. These drives effectively give the machine multiple modes of operation—high speed, low torque for hard rock, and low speed, high torque for difficult ground. Designing a machine with high-torque, continuous boring capabilities allows that machine’s cutterhead to restart with break-out torque in difficult ground. The net effect is that the machine can keep boring in the event of a face collapse and can effectively bore through fault zones and running ground where the potential for cutterhead jamming exists. Going one step further, multi-speed gearboxes give the machine the ideal EPB-type torque if larger sections of soft ground are anticipated.
Secondly, TBMs can get through squeezing ground and faults using Continuous Shield Advance. This design utilizes a stepped shield configuration—where each successive shield is slightly smaller in diameter—to avoid becoming stuck in converging ground. External shield lubrication is an added insurance against becoming stuck, using a series of radial ports that can pump Bentonite into the annular space to act as a lubricant in squeezing material.
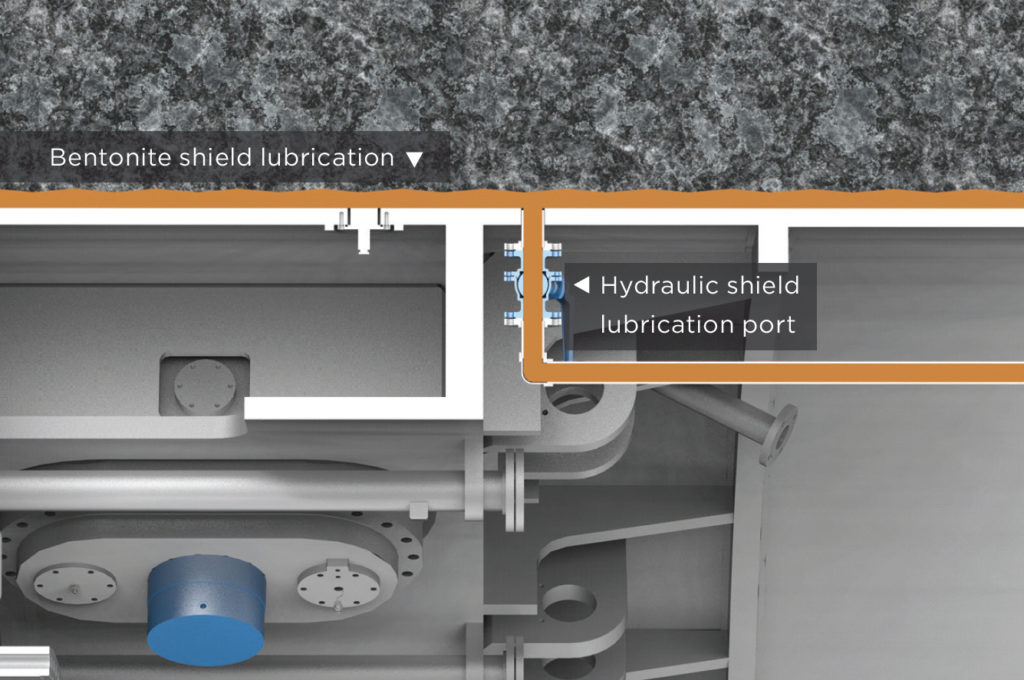
Hydraulic shield lubrication allows for Bentonite (orange) to be pumped into the annular gap.
As a last effort, if a machine has already become stuck the TBM can utilize augmented, or “super” thrust. Additional thrust jacks can be added to supply an extra boost in a short stroke, generating enough force to break loose a trapped shield.
Number 3: DGS can keep your crew safe and save your TBM in the event of a massive inrush of water.
Water is an ever-present part of tunneling underground, but unexpected large inflows can damage a machine and grind a TBM operation to a halt.
In the event of a large inrush of water, a guillotine gate on the muck chute can effectively seal off the muck chamber of a Single Shield TBM to keep the crew safe as well as keep the machine from becoming flooded out. This system is termed “passive” water protection because the TBM is stopped in place (not actively operating). During that time the crew can then work to grout off water inflows and dewater the chamber to control the flow before they begin boring again. The grouting crew also have the added assistance of back pressure to assist in grouting.
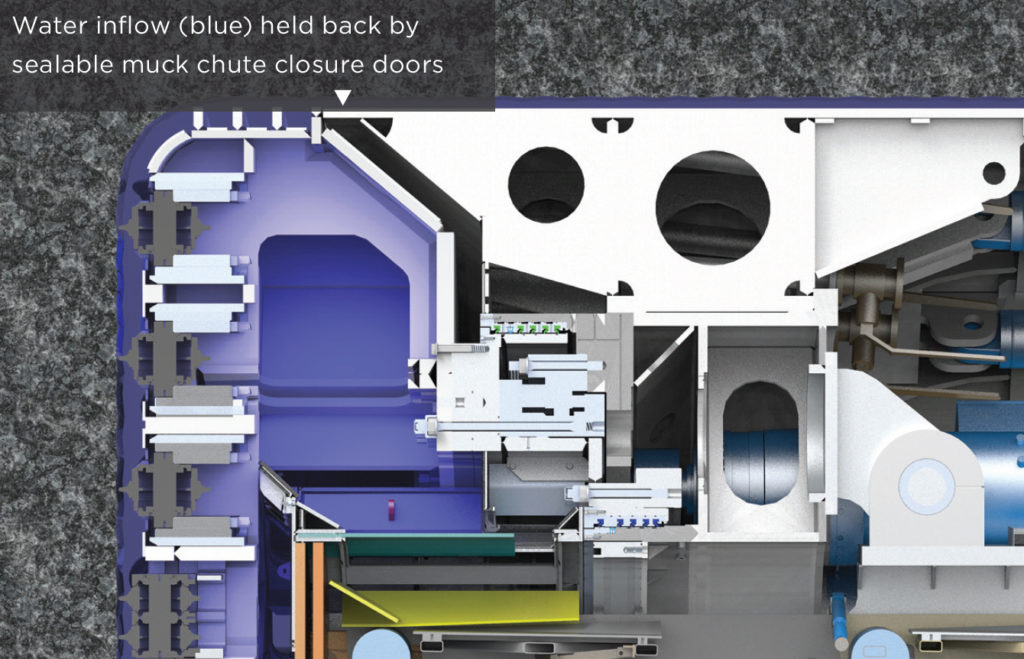
Water Inflow Control can passively seal a Single Shield TBM against water (blue) via a guillotine gate.
Number 4: DGS can improve your visualization of the ground around the TBM.
Probe drilling is an essential part of visualization, and, combined with grouting, it can also fall under the heading of water control. We’ve learned that, in difficult ground, more is better. Multiple probe drills, and more drill ports in a 360-degree radius, are always going to give an advantage. We’ve taken this lesson to heart, and have installed multiple probe drills on many of our new shielded machines, with ports to provide probing patterns in a 360-degree radius. High-pressure grout injection can be done through these same ports to stabilize ground up to 40 m ahead of the face (or more if using specialized drills). The type of grout injected can also be specialized—for example chemical or polymer grout can be used to seal off groundwater. Lastly, a rotary forepole drill can be installed behind the cutterhead support to allow for ground consolidation around the shield periphery. The forepole drill is of particular use in fractured rock and fault zones. These drills are the mainframe of a visualization plan that can ultimately create an in-tunnel GBR as the machine advances: of particular use when no accurate GBR can be created due to topography, high cover, etc.
But what if you suspect the ground around your TBM is converging? What if you want to get a look at the actual rock face in the safest possible manner? There are DGS options for these types of visualization as well. For squeezing ground detection, a hydraulic cylinder can be mounted on top of the shield and connected to the TBM’s PLC. It measures the shield gap in the tunnel crown, so that if squeezing or collapsing ground is detected the crew can take countermeasures. These measures include using bentonite lubrication, crown or face rock conditioning, or planning ahead to use another system in the area before the machine can become stuck. For getting a better look at conditions ahead of the machine, a cutterhead inspection camera can be used to remotely inspect the boring cavity without intervention, and to check water levels ahead of the TBM. While these cameras have been used to monitor mixing chambers and perform cutterhead inspections in soft ground TBMs, their use in hard rock machines has been much more limited. In the new ground investigation system, the probe and injection holes in the cutterhead and front shield are specifically designed to accept these cameras.
Number 5: DGS can save you time and money.
The old adage “the best-laid plans can go astray” applies particularly well to tunneling. There are many unknowns, even with an adequate GBR in hand. Making an initial investment on DGS features when your TBM is still in the shop is far less costly than installing them in the tunnel after a major stoppage. These features can mean the difference between a successful operation and a stuck TBM requiring a bypass tunnel or worse. TBMs with DGS features also produce better advance rates in adverse conditions such as fault zones (see our recent projects Kargi and TEP II as good examples of this). Better advance rates mean your project is more likely to stay on schedule and on budget. And who wouldn’t want that?
Want to find out more about DGS and its successful use in the field?
Check out these white papers:
Difficult Ground Solutions: New TBM Solutions carve a path to Success
免费网络研讨会:降低风险如何管理掘进机隧道中的未知状况
让我们面对现实吧:隧道工程本身就具有风险。即使经过严格的测试,即使是一家高资质的咨询公司创建了岩土基线报告,实际的地质情况也可能存在不可预见的情况。在掘进机掘进的隧道中,机器和操作机器的人员是风险管理策略的关键组成部分。那么,我们如何才能确保隧道作业尽可能地有效地进行呢?
从制造商的角度来看,罗宾斯的首席工程师Dennis Ofiara和项目工程师Elisa Comis将在这60分钟的免费网络研讨会上探讨这个问题,深入探讨合同结构、掘进机设计、案例研究等,以找到答案。无论你是一个操作掘进机的承包商,一个指定设备的顾问,还是即将进行项目的业主,即使是最复杂的隧道也有可能降低风险。
点击观看视频
罗宾斯双护盾为尼泊尔首个掘进机项目开挖隧道
尼泊尔将在这个夏天迎接国内第一台的全断面隧道掘进机,一台直径5.06米的双护盾掘进机为巴瑞巴贝综合引水项目(BBDMP)开挖隧道。2017年7月这台罗宾斯掘进机在其工厂通过测试验收,现在正被运送到喜马拉雅山脉的南部克亚山脉(Siwalik Range)的工地,施工前,包括碎石路和敷设到农村饮用水井的开挖已完成,为掘进机的始发做好准备。
BBDMP是尼泊尔11个民族自豪感项目之一,这是尼泊尔政府批准的进一步发展主要农村国家的优先计划。该项目将在尼泊尔南部地区灌溉60,000公顷的土地,预计将惠及30,000户家庭。它将使用一个15米高的大坝,每秒从巴瑞河向巴贝河转移40立方米的水,水头150米,为周围的班克(Banke)和巴迪亚(Bardia)地区提供全年灌溉。该水还将用于水力发电,发电量为48兆瓦,每年有20亿尼泊尔卢比(月2,000万美元)惠及该国。
承包商中国海外工程集团有限公司尼泊尔分公司(中海工程尼泊尔分公司)负责建造这条引水隧道,并了解在恶劣地质条件下进行隧道施工所面临的挑战。“罗宾斯隧道掘进机的设计很好,尤其是双护盾隧道掘进机,” BBDMP项目经理胡天然说。西瓦利克山脉预计主要由砂岩、泥岩和砾岩组成,需要一个能够开挖挤压地质、不稳定岩石、可能高涌水和断层带的掘进机。隧道上方的最大埋深范围为820米。
由于喜马拉雅山年轻地质的挑战,在机器的设计中加入了困难的地质解决方案(DGS)。一个阶梯式的防护罩被设计用来穿过挤压地质。罗宾斯项目工程师Missy Isaman谈到了包含在掘进机中的DGS功能:“在后部有一个超前钻机,可以从撑靴盾14个位置伸出探测地质。我们在前面的护盾上也加了一些孔以便钻探。圆周上有8个孔用于人工钻探。还有6个孔位于前向上100度的护盾顶部。“她进一步指出,没有为前盾订购任何钻探设备,但现在更护盾中添加钻孔,以防后期在掘进中需要更全面的地质钻探。其他机器改装包括用于可能过度切割直径35 mm的量具切割,以及用于排水的前盾附加排水端口。
渣土清除将由渣土车完成。罗宾斯将提供现场服务,以支持前500米的机器安装、测试、调试和掘进。隧道将采用六角形预制混凝土段进行衬砌。
项目业主尼泊尔灌溉部(MOI)政府选择了一种掘进机,而不是传统的钻爆法,因为机械化采矿提供了更快的动员和推进速度。“为该项目选择掘进机的原因是,使用钻爆法方法至少需要12年才能完成项目。这是因为单头掘进不可能使用平洞进行多个作业,”罗宾斯尼泊尔总经理Prajwal Man Shrestha说。更一般地说,Shrestha先生认为该项目是一种证明掘进机确实可以承受复杂喜马拉雅岩石的方法。“由于喜马拉雅山脉的地质学还很年轻,而且还没有对其进行太多的调查,因此人们对新技术的使用略有担忧。只要有几个掘进机项目和更多的调查,将会表明掘进机技术将适用于喜马拉雅山脉。”
BBDMP是一个民族自豪感项目,它的成功对国家和掘进机行业都至关重要。预计将通过提高尼泊尔中西部地区的农业产量和促进该地区的社会经济发展,帮助缓解粮食危机。为这长12.2公里隧道作业的罗宾斯掘进机计划于2017年11月始发。
2017法国隧道施工及地下空间协会国际峰会
Event Name: AFTES International Congress 2017
Dates: November 13-15, 2017
Location: Paris, France
Venue: Palais des Congrès
The Robbins Company will be joining NFM at this year’s French Tunnelling and Underground Space Association International Congress in Paris, France. Visit our shared booth from November 13-15, to discuss current projects and innovations within the industry.