Author: Keri Lin
您在操作掘进机开挖困难地质5项可以做的事
Difficult Ground Solutions (DGS) is a suite of options that can be added to a shielded hard rock machine or Crossover machine to better enable advance when conditions are unknown or difficult conditions are anticipated. While each of these items is not new, the concept of installing them on a machine from the start, and of using them in concert to provide better visualization and performance in the most challenging ground, is. The uses and advantages of DGS are various and wide-reaching.
Number 1: DGS can act like risk insurance.
Yes, risk insurance. While one can argue that risk insurance is not needed—and of course if a tunnel were in entirely homogeneous, medium strength, self-supporting rock, under a medium amount of cover, I would tend to agree—there is a problem with this argument. That scenario exists only very rarely. At Robbins, we are seeing more tunnels being planned in mountainous, remote regions where an accurate GBR cannot be obtained. More tunnels planned through multiple fault zones and mixed face conditions. More tunnels planned in suspected karst conditions and in rock where large water inflows may occur. It is a trend we’ve observed arcing upward, and with these high-risk projects it seems prudent that an equipment manufacturer should strongly recommend risk insurance. We’ve done that the only way we know how: by calling on our extensive experience to develop, test, and provide various solutions that can be added to a TBM at the beginning of the project. These features mitigate the risk of getting stuck in unforeseen (or foreseen) challenges that might come up in a tunnel drive.
This risk insurance works like any other type of insurance—it must be purchased before the actual event happens. Waiting until a machine encounters a given challenge—where it may become damaged, stuck, or irretrievable—is not an adequate plan for difficult conditions. Sure, some of these options can be added in the tunnel, but such an operation is far from ideal. Risk insurance is best purchased during the TBM design phase, long before the machine is built and launched.
Number 2: DGS can get your TBM through a fault zone or squeezing ground where it might otherwise become stuck.
If fault zones or squeezing ground are known or suspected, or if there is even a possibility of encountering them, this can greatly affect your TBM operation. Shielded hard rock machines protect your crew from the surrounding ground, and they can bore and line a tunnel efficiently, but in fault zones and converging material they need some of the features of an EPB machine to keep advancing. Avoiding a stuck machine is paramount to project success. Luckily, DGS uses several ways to avoid the problem of a machine becoming stuck. The first of these is multi-speed cutterhead drives. These drives effectively give the machine multiple modes of operation—high speed, low torque for hard rock, and low speed, high torque for difficult ground. Designing a machine with high-torque, continuous boring capabilities allows that machine’s cutterhead to restart with break-out torque in difficult ground. The net effect is that the machine can keep boring in the event of a face collapse and can effectively bore through fault zones and running ground where the potential for cutterhead jamming exists. Going one step further, multi-speed gearboxes give the machine the ideal EPB-type torque if larger sections of soft ground are anticipated.
Secondly, TBMs can get through squeezing ground and faults using Continuous Shield Advance. This design utilizes a stepped shield configuration—where each successive shield is slightly smaller in diameter—to avoid becoming stuck in converging ground. External shield lubrication is an added insurance against becoming stuck, using a series of radial ports that can pump Bentonite into the annular space to act as a lubricant in squeezing material.
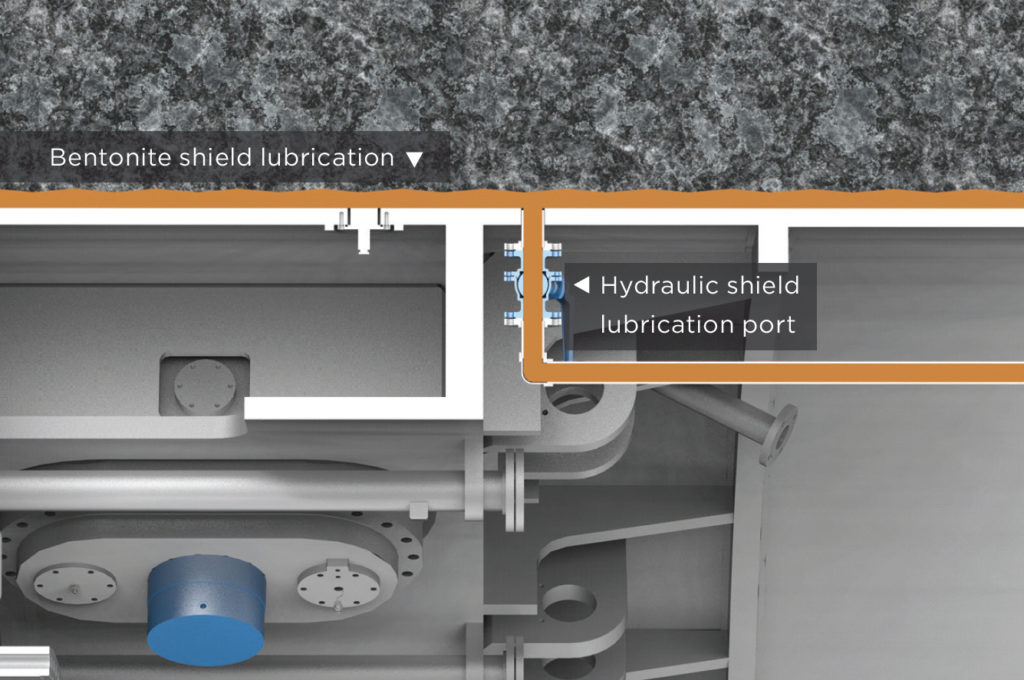
Hydraulic shield lubrication allows for Bentonite (orange) to be pumped into the annular gap.
As a last effort, if a machine has already become stuck the TBM can utilize augmented, or “super” thrust. Additional thrust jacks can be added to supply an extra boost in a short stroke, generating enough force to break loose a trapped shield.
Number 3: DGS can keep your crew safe and save your TBM in the event of a massive inrush of water.
Water is an ever-present part of tunneling underground, but unexpected large inflows can damage a machine and grind a TBM operation to a halt.
In the event of a large inrush of water, a guillotine gate on the muck chute can effectively seal off the muck chamber of a Single Shield TBM to keep the crew safe as well as keep the machine from becoming flooded out. This system is termed “passive” water protection because the TBM is stopped in place (not actively operating). During that time the crew can then work to grout off water inflows and dewater the chamber to control the flow before they begin boring again. The grouting crew also have the added assistance of back pressure to assist in grouting.
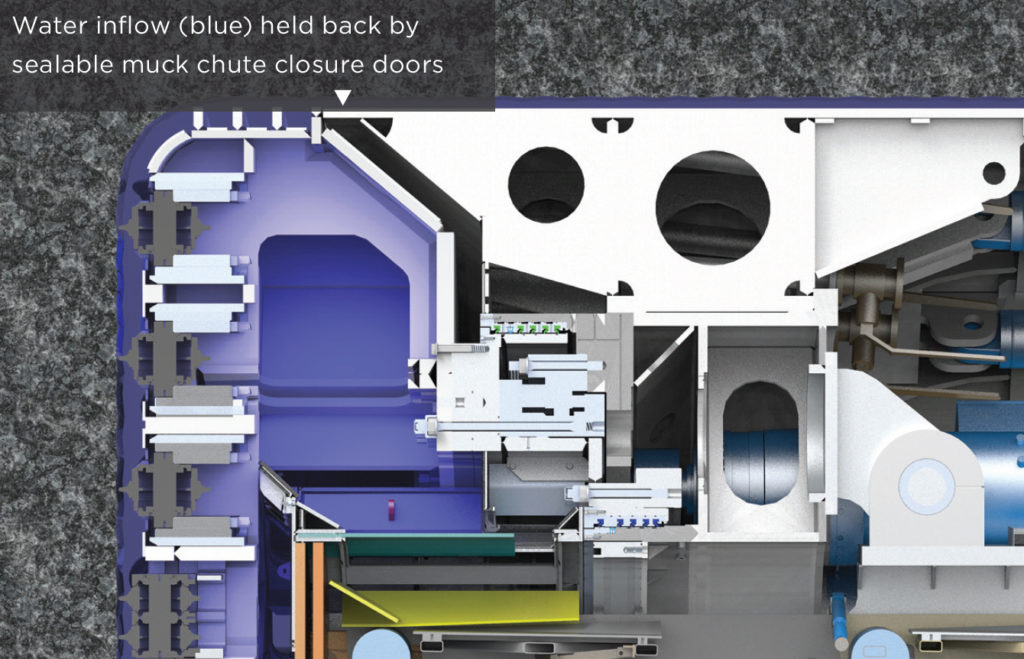
Water Inflow Control can passively seal a Single Shield TBM against water (blue) via a guillotine gate.
Number 4: DGS can improve your visualization of the ground around the TBM.
Probe drilling is an essential part of visualization, and, combined with grouting, it can also fall under the heading of water control. We’ve learned that, in difficult ground, more is better. Multiple probe drills, and more drill ports in a 360-degree radius, are always going to give an advantage. We’ve taken this lesson to heart, and have installed multiple probe drills on many of our new shielded machines, with ports to provide probing patterns in a 360-degree radius. High-pressure grout injection can be done through these same ports to stabilize ground up to 40 m ahead of the face (or more if using specialized drills). The type of grout injected can also be specialized—for example chemical or polymer grout can be used to seal off groundwater. Lastly, a rotary forepole drill can be installed behind the cutterhead support to allow for ground consolidation around the shield periphery. The forepole drill is of particular use in fractured rock and fault zones. These drills are the mainframe of a visualization plan that can ultimately create an in-tunnel GBR as the machine advances: of particular use when no accurate GBR can be created due to topography, high cover, etc.
But what if you suspect the ground around your TBM is converging? What if you want to get a look at the actual rock face in the safest possible manner? There are DGS options for these types of visualization as well. For squeezing ground detection, a hydraulic cylinder can be mounted on top of the shield and connected to the TBM’s PLC. It measures the shield gap in the tunnel crown, so that if squeezing or collapsing ground is detected the crew can take countermeasures. These measures include using bentonite lubrication, crown or face rock conditioning, or planning ahead to use another system in the area before the machine can become stuck. For getting a better look at conditions ahead of the machine, a cutterhead inspection camera can be used to remotely inspect the boring cavity without intervention, and to check water levels ahead of the TBM. While these cameras have been used to monitor mixing chambers and perform cutterhead inspections in soft ground TBMs, their use in hard rock machines has been much more limited. In the new ground investigation system, the probe and injection holes in the cutterhead and front shield are specifically designed to accept these cameras.
Number 5: DGS can save you time and money.
The old adage “the best-laid plans can go astray” applies particularly well to tunneling. There are many unknowns, even with an adequate GBR in hand. Making an initial investment on DGS features when your TBM is still in the shop is far less costly than installing them in the tunnel after a major stoppage. These features can mean the difference between a successful operation and a stuck TBM requiring a bypass tunnel or worse. TBMs with DGS features also produce better advance rates in adverse conditions such as fault zones (see our recent projects Kargi and TEP II as good examples of this). Better advance rates mean your project is more likely to stay on schedule and on budget. And who wouldn’t want that?
Want to find out more about DGS and its successful use in the field?
Check out these white papers:
Difficult Ground Solutions: New TBM Solutions carve a path to Success
免费网络研讨会:降低风险如何管理掘进机隧道中的未知状况
让我们面对现实吧:隧道工程本身就具有风险。即使经过严格的测试,即使是一家高资质的咨询公司创建了岩土基线报告,实际的地质情况也可能存在不可预见的情况。在掘进机掘进的隧道中,机器和操作机器的人员是风险管理策略的关键组成部分。那么,我们如何才能确保隧道作业尽可能地有效地进行呢?
从制造商的角度来看,罗宾斯的首席工程师Dennis Ofiara和项目工程师Elisa Comis将在这60分钟的免费网络研讨会上探讨这个问题,深入探讨合同结构、掘进机设计、案例研究等,以找到答案。无论你是一个操作掘进机的承包商,一个指定设备的顾问,还是即将进行项目的业主,即使是最复杂的隧道也有可能降低风险。
点击观看视频
罗宾斯双护盾为尼泊尔首个掘进机项目开挖隧道
尼泊尔将在这个夏天迎接国内第一台的全断面隧道掘进机,一台直径5.06米的双护盾掘进机为巴瑞巴贝综合引水项目(BBDMP)开挖隧道。2017年7月这台罗宾斯掘进机在其工厂通过测试验收,现在正被运送到喜马拉雅山脉的南部克亚山脉(Siwalik Range)的工地,施工前,包括碎石路和敷设到农村饮用水井的开挖已完成,为掘进机的始发做好准备。
BBDMP是尼泊尔11个民族自豪感项目之一,这是尼泊尔政府批准的进一步发展主要农村国家的优先计划。该项目将在尼泊尔南部地区灌溉60,000公顷的土地,预计将惠及30,000户家庭。它将使用一个15米高的大坝,每秒从巴瑞河向巴贝河转移40立方米的水,水头150米,为周围的班克(Banke)和巴迪亚(Bardia)地区提供全年灌溉。该水还将用于水力发电,发电量为48兆瓦,每年有20亿尼泊尔卢比(月2,000万美元)惠及该国。
承包商中国海外工程集团有限公司尼泊尔分公司(中海工程尼泊尔分公司)负责建造这条引水隧道,并了解在恶劣地质条件下进行隧道施工所面临的挑战。“罗宾斯隧道掘进机的设计很好,尤其是双护盾隧道掘进机,” BBDMP项目经理胡天然说。西瓦利克山脉预计主要由砂岩、泥岩和砾岩组成,需要一个能够开挖挤压地质、不稳定岩石、可能高涌水和断层带的掘进机。隧道上方的最大埋深范围为820米。
由于喜马拉雅山年轻地质的挑战,在机器的设计中加入了困难的地质解决方案(DGS)。一个阶梯式的防护罩被设计用来穿过挤压地质。罗宾斯项目工程师Missy Isaman谈到了包含在掘进机中的DGS功能:“在后部有一个超前钻机,可以从撑靴盾14个位置伸出探测地质。我们在前面的护盾上也加了一些孔以便钻探。圆周上有8个孔用于人工钻探。还有6个孔位于前向上100度的护盾顶部。“她进一步指出,没有为前盾订购任何钻探设备,但现在更护盾中添加钻孔,以防后期在掘进中需要更全面的地质钻探。其他机器改装包括用于可能过度切割直径35 mm的量具切割,以及用于排水的前盾附加排水端口。
渣土清除将由渣土车完成。罗宾斯将提供现场服务,以支持前500米的机器安装、测试、调试和掘进。隧道将采用六角形预制混凝土段进行衬砌。
项目业主尼泊尔灌溉部(MOI)政府选择了一种掘进机,而不是传统的钻爆法,因为机械化采矿提供了更快的动员和推进速度。“为该项目选择掘进机的原因是,使用钻爆法方法至少需要12年才能完成项目。这是因为单头掘进不可能使用平洞进行多个作业,”罗宾斯尼泊尔总经理Prajwal Man Shrestha说。更一般地说,Shrestha先生认为该项目是一种证明掘进机确实可以承受复杂喜马拉雅岩石的方法。“由于喜马拉雅山脉的地质学还很年轻,而且还没有对其进行太多的调查,因此人们对新技术的使用略有担忧。只要有几个掘进机项目和更多的调查,将会表明掘进机技术将适用于喜马拉雅山脉。”
BBDMP是一个民族自豪感项目,它的成功对国家和掘进机行业都至关重要。预计将通过提高尼泊尔中西部地区的农业产量和促进该地区的社会经济发展,帮助缓解粮食危机。为这长12.2公里隧道作业的罗宾斯掘进机计划于2017年11月始发。
2017法国隧道施工及地下空间协会国际峰会
Event Name: AFTES International Congress 2017
Dates: November 13-15, 2017
Location: Paris, France
Venue: Palais des Congrès
The Robbins Company will be joining NFM at this year’s French Tunnelling and Underground Space Association International Congress in Paris, France. Visit our shared booth from November 13-15, to discuss current projects and innovations within the industry.
2017隧道协会颁奖大会
Event Name: ITA Tunneling Awards 2017
Date: November 15, 2017
Location: Paris, France
Venue: Salle Wagram
The Robbins Company is excited to announce that the recently completed Túnel Emisor Poniente (TEP) II has been nominated as an ITA Tunneling Awards finalist for Project of the Year. Winners will be announced at the ITA Tunneling Awards that will take place during the AFTES Congress in Paris, France on November 15.
The Robbins XRE TBM and its Robbins continuous conveyor system were built on location using Onsite First Time Assembly (OFTA), and featured components like a convertible cutterhead with interchangeable cutting tools, interchangeable TBM belt conveyor and screw conveyor, and multi-speed gearboxes to increase torque for tunneling through difficult ground. The 8.7 m (28.5 ft) diameter Robbins Crossover TBM bored a 5.8 km (3.6 mi) long wastewater tunnel, setting two national records in the process. The completed project will prevent flooding in urban areas and benefit the lives of 2.1 million people.
混合盾构、跨模式或更多,到底这些命名是什么机器类型?
For underground construction professionals and manufacturers, there is some confusion about the current TBM designations and what they really mean, and for what applications they are to be considered. This is especially noted when it comes to soft and mixed ground type shield machines and if they are to operate in “open” mode, “closed” mode or “semi-open/closed” mode conditions.
The term “open mode” defines defines a mode of TBM operation where no pressure is required to stabilize the boring face; the geology is self-standing and ground settlement will not occur.
The term “closed mode” defines tha mode of TBM operation where face pressure needs to be constantly applied in order to maintain face support. Should the face pressure not be maintained as determined by the geology, under-pressurization will cause ground settlement, over-pressurization can cause surface heaving.
The term “semi-open/closed mode” defines a mode of TBM operation in varying geology where the TBM has the ability to control the face.
The various machine types in question are Mixshield, Hybrid and the Robbins “Crossover”. Are they the same? If not, what is the difference? This blog seeks to clarify and explore those definitions.
Mixshield
Mixshield is a terminology introduced by German manufacturer Herrenknecht for what is essentially a Slurry TBM that uses an air bubble to control and support pressure at the face. The air bubble acts like an accumulator with the belief that this offers better pressure control. This type of machine operates only in “closed mode”. Mixshields are not meant to go from high pressure soft ground to significant rocky conditions with great efficiency, hence the name “Mixshield” is somewhat of a misnomer. They can excavate mixed face conditions, but the machine configuration is not changed so it is a different thing entirely than to excavate significant sections of differing geology. In order to change the configuration to allow more efficient operation in different sections of geology, a Hybrid machine is needed.
Hybrid, etc.
“Hybrid”, “Dual Mode”, and “Multi-Mode” are names developed by the industry to try and define machines that feature components of two different machine types. The most common types is a multi-mode between EPB with a screw conveyor (for operation in “closed mode” or “semi-closed mode”) and conversion to Rock Mode with the installation of a belt conveyor (for use in “open mode” operation). Typically, the only changes made to the machine are components such as cutting tools and muck removal method that can be switched out in the tunnel depending on ground conditions. The machines are used for large sections of vastly different geology in one tunnel, such as a section of clay followed by as significant section of rock. However these types of machines are typically designed as EPB machines and then converted, making them not very efficient for use in rock geology.
Robbins Crossover
The “Crossover Series” of TBMs was developed by Robbins in March 2015 using innovative design concepts to effectively excavate between different geologies. The Crossover Series is Robbins’ version of a Hybrid TBM but with many additional features to allow the TBM to effectively cross between different geology types. Operation of the machine can allow the machine to quickly change from “open mode” to “semi open/closed mode” and “closed mode.” The main types of Crossover TBM include the XRE (Crossover between Hard Rock and EPB), XSE (Crossover between Slurry and EPB) and XRS (Crossover between Hard Rock and Slurry). The features include interchangeable cutting tools; single direction and bi-directional cutterhead muck pick-up; multi-speed, multi-torque cutterhead drive systems; durable, abrasion resistant components on the cutterhead and screw conveyor; emergency thrust; tapered shields to reduce shield entrapment in squeezing ground; integrated probe/grout drill system for ground consolidation; and heavy steel construction with components designed for +12,000 hours of life, just to name a few.
The Crossover Series is suitable for tunnel projects that require the ability to excavate different types of geology efficiently with one machine, based on ground conditions. The TBM design is flexible enough to switch from one mode to another. Ultimately, Crossover Series machines are cost efficient in the long run, since the TBMs require less repair costs than a non-customized machine, and they can be used on multiple projects.
Based on the ground situation (whether it’s self-supporting ground, self-supporting ground with water pressure, or unstable ground), the Crossover is optimized towards “open” mode (as in hard rock shielded TBMs) or “closed” mode (as in compressed air, slurry, and EPB TBMs).
Reliable geological information is therefore critical to the TBM design. An accurate geological report is needed to decide when and where to convert the machine as well. During excavation, adequate probe drilling is further essential to determine the ground conditions ahead of the Crossover TBM.
Below are the features specific to each type of Crossover machine.
Crossover XRE
- Mixed ground cutterhead: with disc cutters & soft ground tools or a combination of tools (interchangeable).
- Two-speed gearboxes: provide high torque at low RPM under soft ground conditions and high RPM under hard rock conditions.
- Cutterhead rotation: Single direction is more efficient in hard ground conditions and bi-directional is more efficient in soft ground to prevent roll.
Crossover XSE
- Equipped with both screw conveyor and slurry system for muck removal.
- Ground conditions: soft ground containing water under pressure (particularly for water pressures > 5 bar).
- The most universal of the Crossover machines, the XSE can bore in most types of ground.
Crossover XRS
- Highly adaptable to variable ground conditions; suitable for rock tunnels with water pressure > 5 bar.
- Hard rock machine with a rock cutterhead and slurry system in place.
- Capable of mining rock through high water pressure without grouting off water flows.
跨模式掘进在墨西哥城破纪录地贯通
2017年6月8日,包括墨西哥总统 Enrique Peña Nieto在内的一批项目官员庆祝了史诗隧道项目的最终突破。直径8.7米的罗宾斯跨模式掘进机是第一台在北美作业的跨模式掘进机,它完成了伊米苏泊尼特隧道二期 (Túnel Emisor Poniente II,简称TEP II)。这台掘进机兼并硬岩模式和土压平衡模式作业的跨模式掘进机XRE,可以在断层带、可变地面、浅埋深等地质掘进,以日掘进57米、周掘进231米和月掘进702米的速度刷新了的国家纪录。
“XRE具有很大的优势,因为它设计用于开放或封闭土压盾构模式下掘进;允许它在土壤或岩石中挖掘隧道。我们已经证实它的性能是非常有效的。” 业主Conagua,墨西哥国家水委员会TEP二期主管Ing. Juan Alberto Herrera Moro y Castillo说道。
这台独特的机器及其连续输送系统是采用现场首次安装调试的方案(OFTA)组装的,并且是为Aldesem、Provon和Recsa的承包商联合体设计的。罗宾斯跨模式掘进机的特点是,如配备可互换刀具的可转换刀盘,可互换的掘进机带式输送机和螺旋输送机,以及多速变速箱,以增加在困难地质下挖掘隧道时的扭矩。“这种设计的好处在于其卓越的推力和改变刀盘扭矩的便利性。如果机器卡在困难的地质下,这会使整个过程变得更容易,” RECSA隧道部门负责人Alberto Martinez说。
XRE机器于2015年8月启动,用于挖掘5.8公里长的废水隧道。这台机器安装在坚硬的岩石地质中,刀盘配备20英寸的滚刀。2016年初,掘进机撞击了几个接触带中的第一个,这是一条30米宽的断裂带,由破碎和块状岩石构成。虽然通过接触带的挖掘工作进展缓慢,但在更具挑战性的安山岩中,进度再次加快。在2016年3月中段贯通进入80 米深的竖井,随后进行检查和维护后,掘进机继续掘进。
2016年秋季在破碎安山岩中掘进时,隧道掘进机遇到了一个自然形成的洞穴,据信是过渡带中的岩石坠落或侵蚀岩石的古老地下湖体造成的。据估计,该洞穴的大小为90立方米,其中不稳定的地面面积约为57立方米。掘进机被停机,并立即采取措施使机器前的地面用聚氨酯泡沫稳定,然后用豌豆砾石和浆液的混合物填充洞室。
截至2016年10月底,掘进机已达到软土地面最后900米长的隧道段,并在那里转换为土压平衡模式。在最后一段浅埋深的隧道中,隧道顶部到住宅地基的距离低至4 米,地质具有再固结土壤的一致性。为了稳定软土,并将居住区以下的沉降风险降至最低,隧道施工人员从地表开始钻孔,每隔1.0米安装890根微型桩。他解释说:“我们能够做到这一点,而不会对TEP II路径沿途附近地区邻居的财产造成损害,也不会对该地区安装的道路或城市基础设施造成损害。” 承包商Aldesa的TEP II现场经理Francisco Miguel Lopez说。
现在隧道已经贯通,隧道将在投入使用前再灌注一个35厘米厚的二次混凝土衬砌。该污水隧道将对墨西哥城外西部地区的现有系统进行检修,以防止瓦尔多拉多的反复洪水。特别是,隧道将有益于Cuauttal Izcalli、Tlalnpantla和Atizapan de Zaragoza这些城市总共有210万居民。
2017破岩峰会
Event Name: Cutting Edge Conference
Dates: November 13-15, 2017
Location: Seattle, WA, USA
Venue: Renaissance Seattle Hotel
Join The Robbins Company at the Sixth Annual Cutting Edge Conference: Advances in Tunneling Technology November 13-15, in Seattle, WA. Visit our booth to learn more about current techniques being used on Robbins projects throughout the world.
2017国际轨道交通技术展览会
Event Name: STUVA Expo and Conference
Dates: December 6-7, 2017
Location: Messe Stuttgart, Germany
Venue: Messe Stuttgart Trade Fair Centre
With an increasing rate of growth, STUVA-Expo will take place parallel to STUVA-Conference December 6-7 in Messe Stuttgart, Germany. The Robbins Company is looking forward to sharing information about current TBM projects operating world-wide at this ever-growing event.
罗宾斯盾构机斋浦尔标志性城门不足5米下掘进
大陆工程公司(Continental Engineering Corporation ,简称CEC)为斋浦尔地铁项目开挖的隧道临着世界范围内地铁项目通常面临的挑战,包括小场地,以及有关路段和淤泥储存空间等的相关问题。然而,这些挑战相对较简单。与隧道施工所面临的挑战相比。土压平衡盾构机(EPB)需要在极浅的埋深下掘进,以及在几个文化敏感的历史建筑旁边和下面掘进。在考虑隧道引起的地面沉降和振动的可能后果时,这些结构及其施工方法及材料的使用寿命非常令人关注。本文将介绍为确保这些历史建筑不受隧道施工的不利影响而采取的有关隧道掘进和地表监测的措施。
最近要闻
- Long Haul TBM: Use of a Rebuilt Main Beam Machine at the DigIndy Tunnel System in Indianapolis, IN
- Evaluating TBM Design and Performance, 30 Years Apart: The Lesotho Highlands Water Tunnel, Phase 1 and Phase 2
- Use of a Tunnel Boring Machine on Nepal’s First and Second TBM-Driven Tunnels
- Record-Setting Large Diameter Mixed Ground Tunneling in Turkey: The Eşme-Salihli Railway Tunnel
- Lessons Learned During Excavation of the Incredibly Challenging Yin Han Ji Wei Water Diversion Tunnel