Author: Robbins
Record-Setting Large Diameter Mixed Ground Tunneling in Turkey: The Eşme-Salihli Railway Tunnel
Large diameter tunneling has historically been seen as a challenge. Add into the equation mixed ground conditions, and it becomes a task that may seem insurmountable. How-ever, a recently completed tunnel in Turkey is a flagbearer for changing the mindset towards these challenging tunneling scenarios that are becoming more frequent. A 13.77 m diameter mixed ground Rock/EPB TBM bored the Eşme-Salihli Railway Tunnel at rates of up to 721.8 m in one month, making it the fastest TBM ever recorded over 13 m in diameter. The machine began its bore in altered gneiss, then passed through mélange consisting of gneiss, sandstone, claystone, mudstone, quartz, and silt. By the end of the bore the machine was excavating in mainly mudstone. Core drillings were taken every 200 m prior to boring.
In this paper, we detail the project as well as analyze factors contributing to the fast advance rates. The factors include TBM choice and system design, ground conditions, TBM utilization rates and downtimes, as well as maintenance practices, crew expertise and technical support, all of which have a part to play in the overall advance rates and successful outcome. Recommendations are made as to best practices in order to achieve good advance rates on similar large diameter, mixed ground tunnels.
Lessons Learned During Excavation of the Incredibly Challenging Yin Han Ji Wei Water Diversion Tunnel
The 2022 breakthrough of an 8 m diameter Main Beam TBM at China’s Yin Han Ji Wei project was a triumph of technology and perseverance – crews at the 17.5 km long tunnel encountered over 14,000 rock bursts, some with energy as high as 4,080 kJ. The rock, consisting of mainly quartzite and granite, was estimated to have a rock hardness of between 107 and 309 MPa UCS, with high abrasivity and a maximum quartz content of 92.6%. The incredibly challenging tunnel also experienced at times severe water inflows, with one particular event exceeding 20,000 m3 of water in one day from a single point. In-tunnel ambient temperatures peaked at 40 degrees Celsius and 90% humidity. Throughout the challenges, the crew and support teams found ways to persevere – whether through unique ground support, or increased monitoring and analysis. In this paper, we will examine the successes and lessons learned in the incredibly challenging ground conditions, determining what worked best to confront each condition as it came up. Recommendations will be made towards what could be used successfully on future projects that en-counter these geological features.
Record-Setting Tunnel Boring Below Lake Ontario at the Ashbridges Bay Outfall Tunnel
The 3.5 km long Ashbridges Bay Outfall in Toronto, Ontario, Canada was a challenging drive set below Lake Ontario. After a remote machine acceptance due to the global pandemic, an 8 m diameter Single Shield machine launched in March 2021 from an 85 m deep shaft and began its bore in shale with limestone, siltstone and sandstone. During excavation, the TBM and its crew bored a city-wide record of 30 rings in one day, or 47 m of advance. This paper will cover the unique project, from TBM acceptance through to launch, tunneling in difficult conditions, and completion in 2022.
Enhanced Probe Drilling & Pre-Grouting on Hard Rock TBMs
While probe drills are not strictly necessary for all projects, the incorporation and use of probe drills and pre-grouting adds capability and insurance to boring operations. Water ingress and unstable ground can be resolved before becoming a problem and resulting in costly delays through the use of enhanced, 360-degree probe drilling setups. To do this, proper design of the array of drill ports in the shield, matched to the possible ground conditions, is critical. For ground with exceptional water and instabilities expected, additional probing locations are low-cost additions that can lower risk and increase efficiency. In this paper we will look at recent and ongoing projects including the Lower Meramec Tunnel and Jefferson Barracks Phase 2. We will detail the design of those probe drill arrangements, and our overall recommendations for probing/grouting systems that best suit challenging ground conditions and keep projects running smoothly.
Tunneling in Turkey: The Esme Salihli Railway
Large diameter tunneling in mixed ground has historically been seen as a challenge, but a recently completed tunnel in Turkey has changed the conversation. A 13.77 m diameter Crossover XRE TBM bored the Esme Salihli Railway Tunnel at world-record-setting rates of up to 721.8 m in one month, making it the fastest TBM over 13 m in diameter. What allowed the project to achieve such high advance rates?
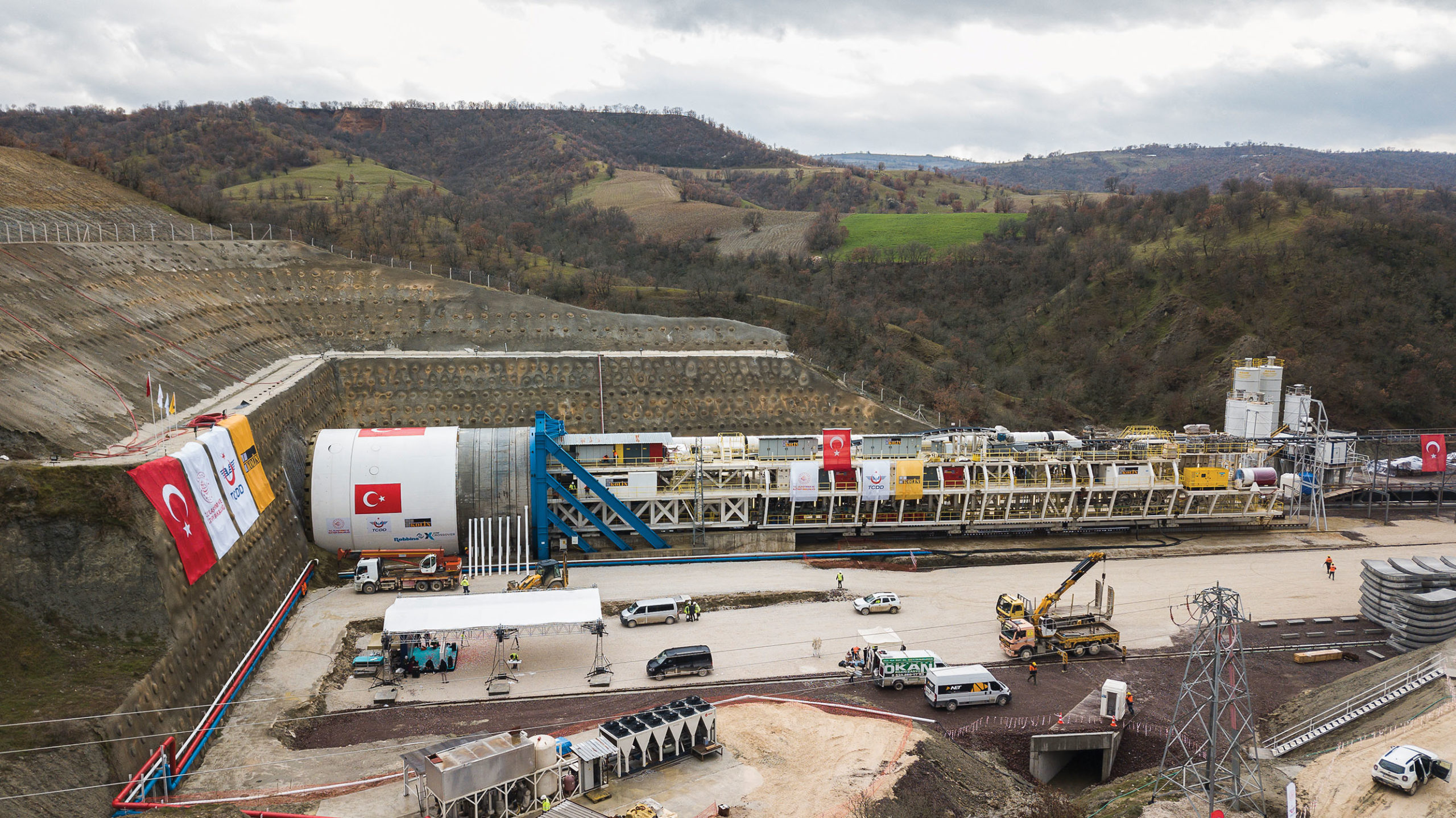
A Robbins Crossover machine that bored Turkey’s 3.05 km (1.90 mi) Eşme-Salihli Railway Tunnel through mixed conditions including sandstone, gravelstone, claystone, and siltstone for contractor Kolin Construction.
Machine Design for Variable Geology
The Eşme-Salihli Railway Tunnel is a short section of high-speed railway, measuring 3.05 km (1.90 mi) through mixed conditions. Contractor Kolin Construction conducted 15 core drillings at 200 m intervals prior to the start of construction, with results predicting occasional groundwater and weak rock between 5 to 9 MPa (720 to 1,300 psi) UCS, with the potential for a gassy environment. Rock and soil types included sections of gneiss, sandstone, claystone, mudstone, quartzite, and silt.
A dual mode rock/EPB TBM design was created for the project, in which no design elements were sacrificed in the engineering: The machine was fully capable of operating in 100% EPB mode or 100% Hard Rock Single Shield Mode. The TBM was designed for sections of hard rock and mixed ground, in highly variable conditions. For details on the design, check out this technical paper.
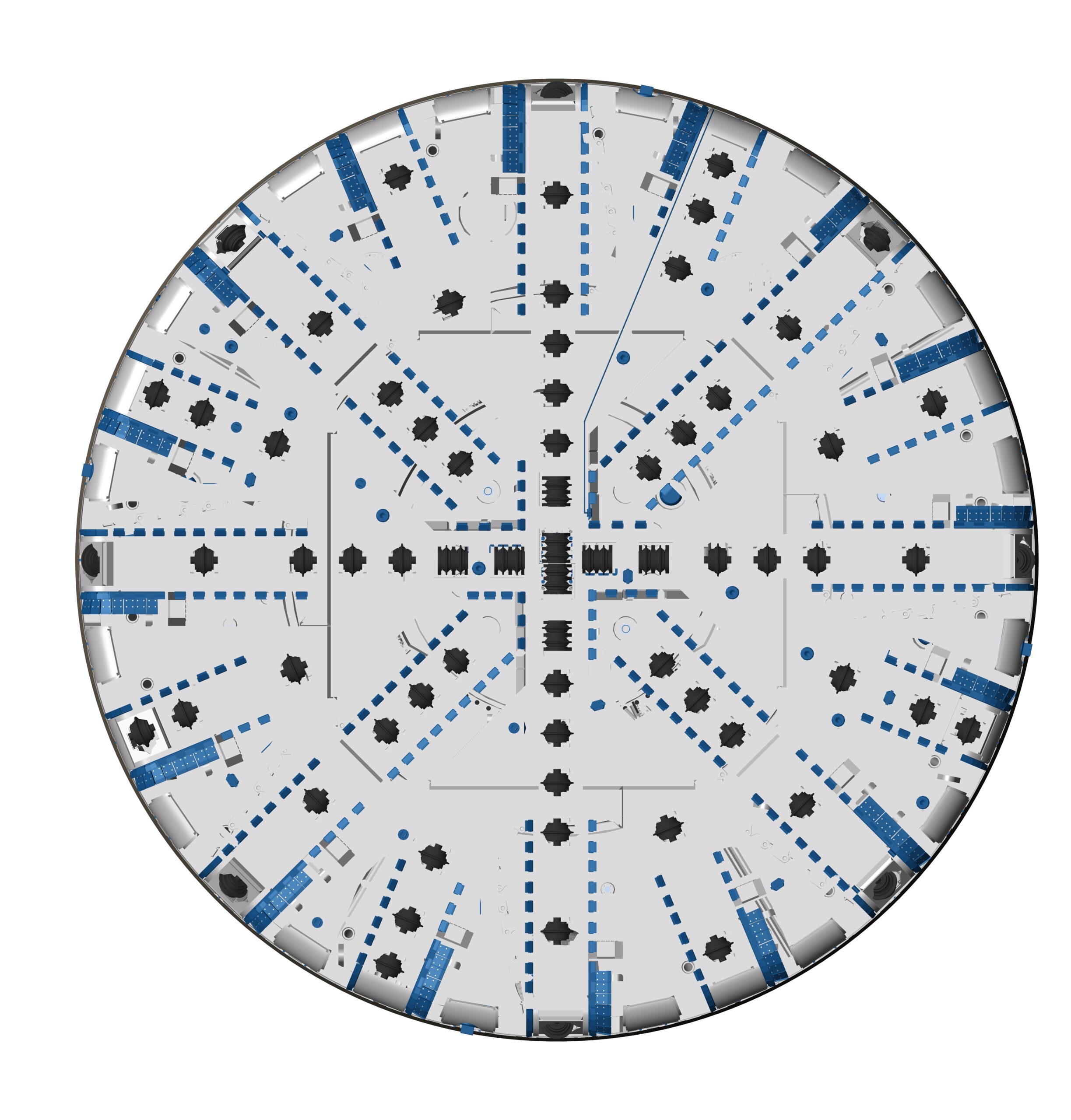
The cutterhead in hard rock mode.
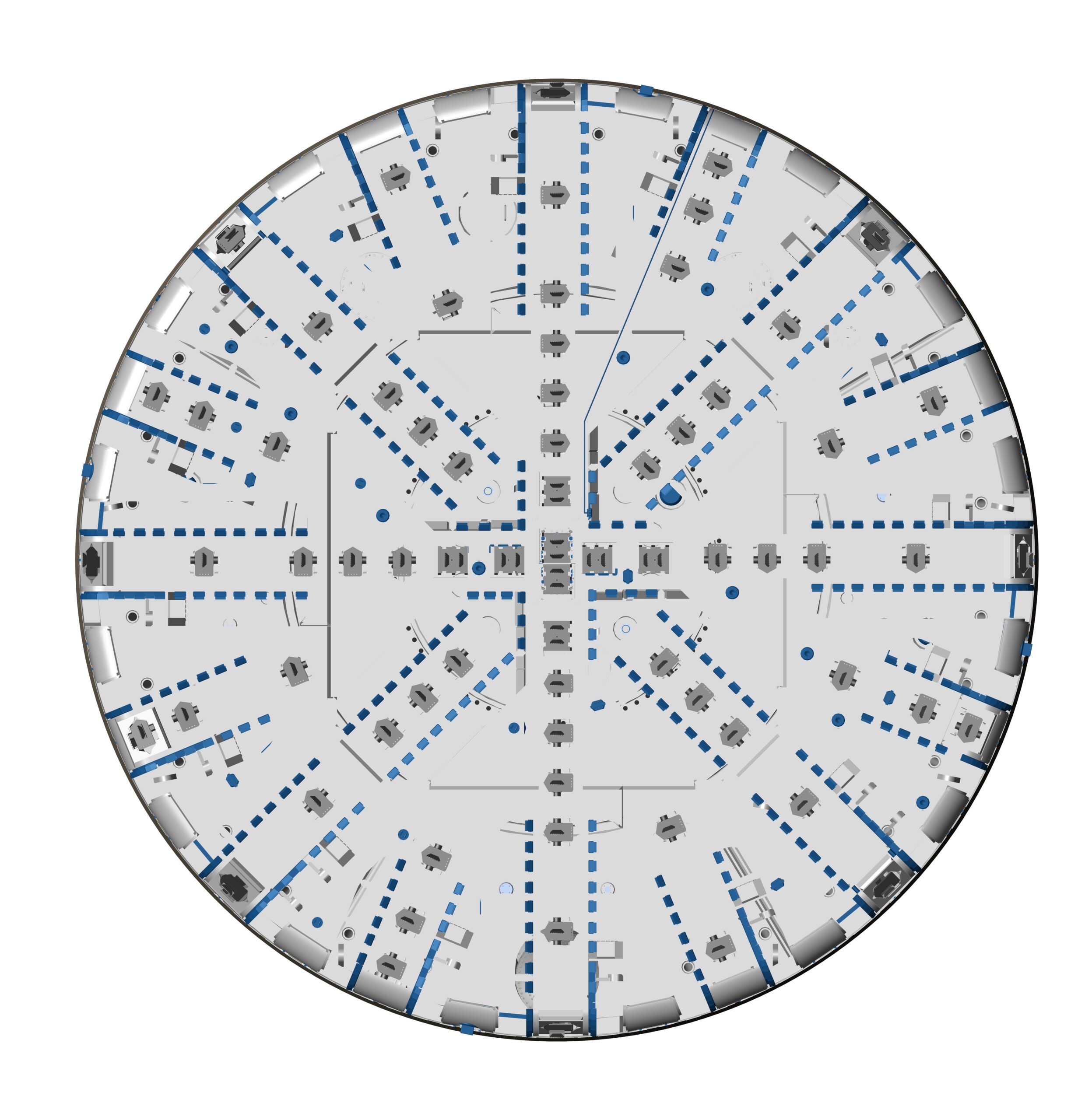
The cutterhead in EPB mode.
Epic Results
The 13.77 m Crossover XRE machine launched on its 3.05 km (1.90 mi) bore at the end of March 2021. While some of the crossover features proved beneficial the TBM was able to utilize the screw conveyor for mucking for the complete tunnel drive, which was a further benefit for the project’s overall schedule.
What allowed the machine to perform at high rates of advance? Utilization charts reveal that 38% of the total time was spent on excavation, 27% on ring assembly, 21% on planned downtime such as maintenance, and 14% on unplanned downtime.
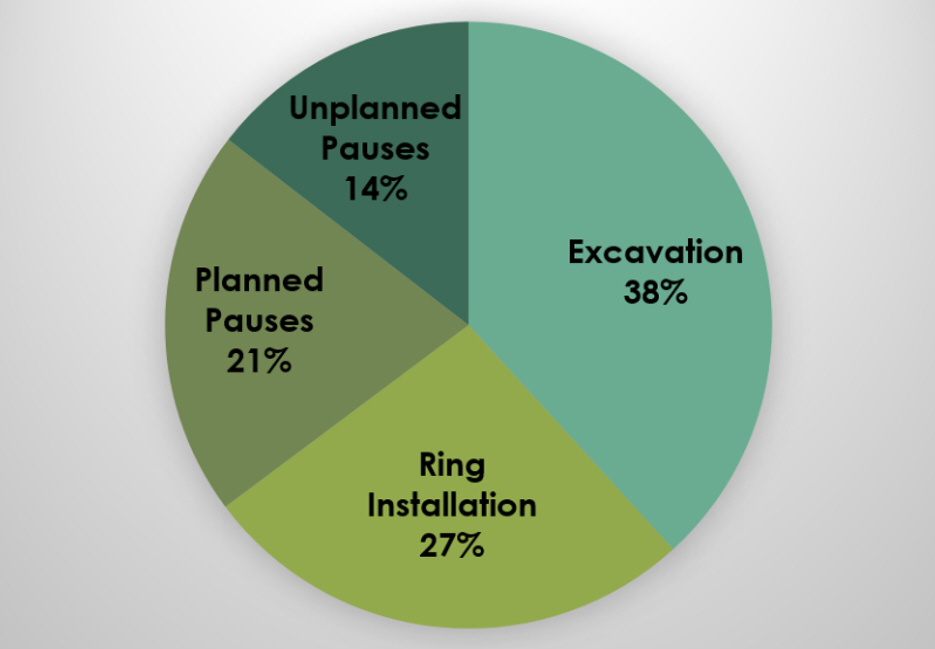
Productivity pie chart.
When looking at planned downtime, the most time was spent on cutterhead maintenance at 28%, followed by crew breaks at 22%. An average machine push took 60 minutes, while ring builds averaged 42 minutes.
Delays caused by mechanical, hydraulic or electrical failures were very low. The contractor cited the main reasons for minimal downtime, and thus high advance rates, as regular planned maintenance, cleaning, an experienced team, and an adequate supply of spare parts. Ultimately the tunnel was completed in just 6.5 months.
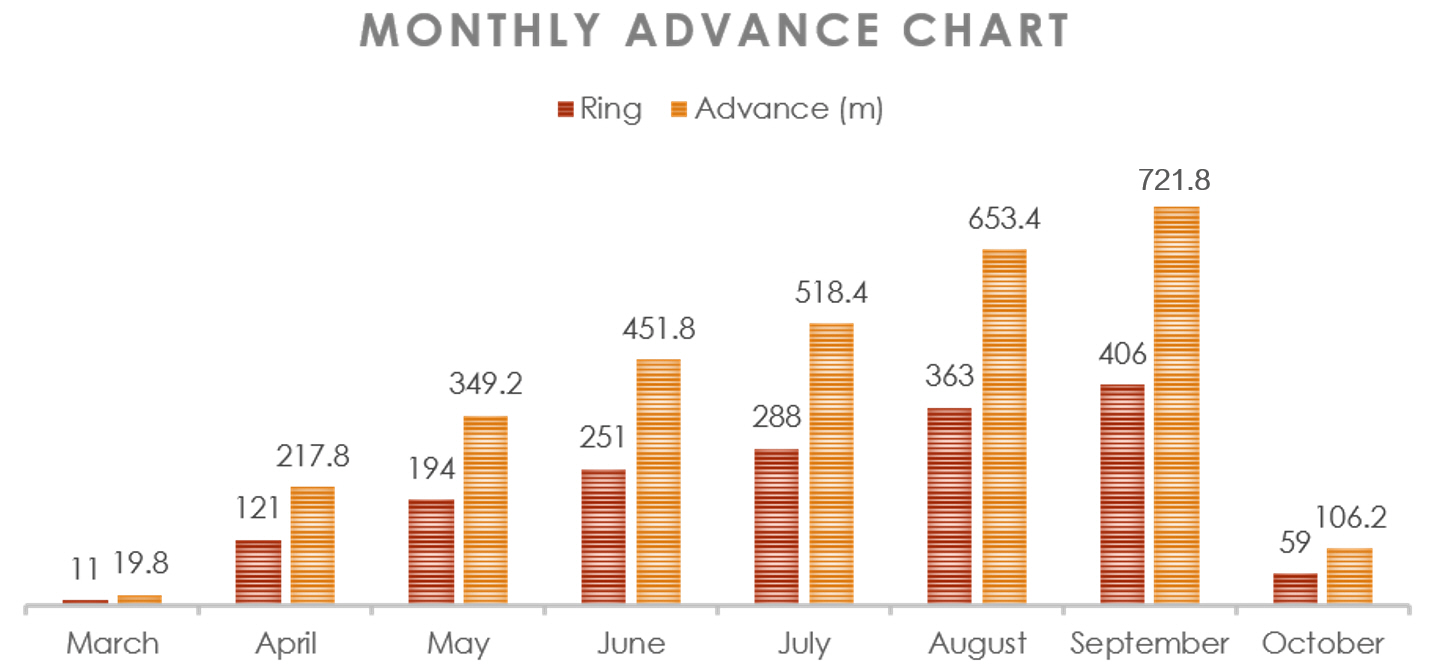
Monthly advance rate chart in meters bored and rings built.
In Conclusion
Large diameter, dual mode rock/EPB machines can and will excavate mixed ground conditions efficiently – even at world record rates. While similar projects in Turkish geology have met with challenges, the Esme-Salihli tunnel shows that with proper maintenance and a knowledgeable crew, equipment downtime can be kept to a minimum and advance rates can remain high.
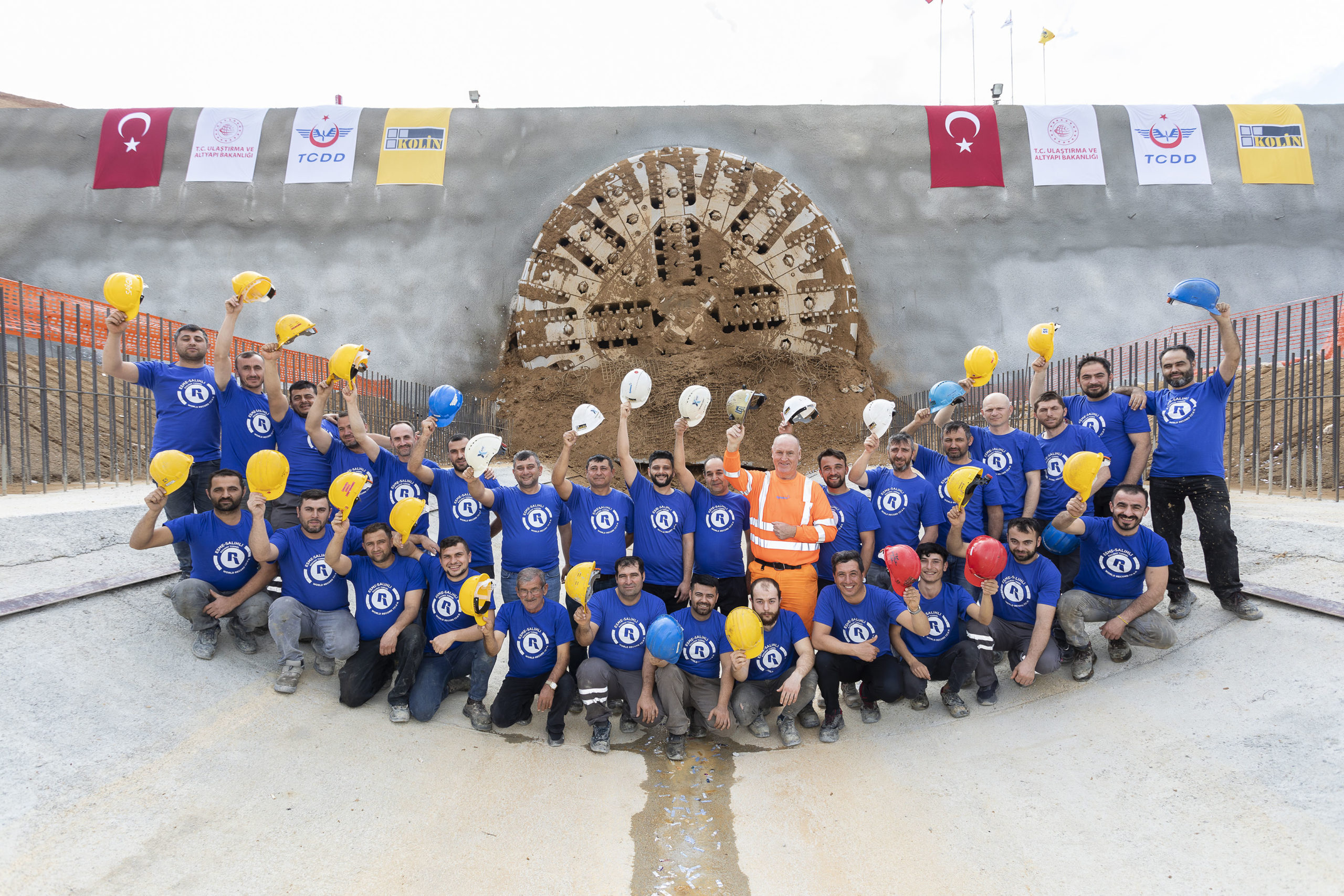
Personnel from contractor Kolin Construction and Robbins celebrate the breakthrough of a Crossover (XRE) TBM after it completed Turkey’s Esme Salihli Railway Tunnel.
Incredible India: Machines on the Move in Agra and Delhi
India’s metro network has undergone extensive growth in recent years, and is showing no signs of slowing. Multiple Robbins machines are part of tunneling work in cities across India, including Agra and Delhi.
Agra Metro: From First Site Acceptance…
On February 16, 2023 the Robbins crew and contractor SAM India celebrated the site acceptance test for the first of two 6.65 m diameter EPB TBMs at Agra Metro. The machine began boring a 1.3 km long tunnel in soft soils, for Uttar Pradesh Metro Rail Corporation Ltd.
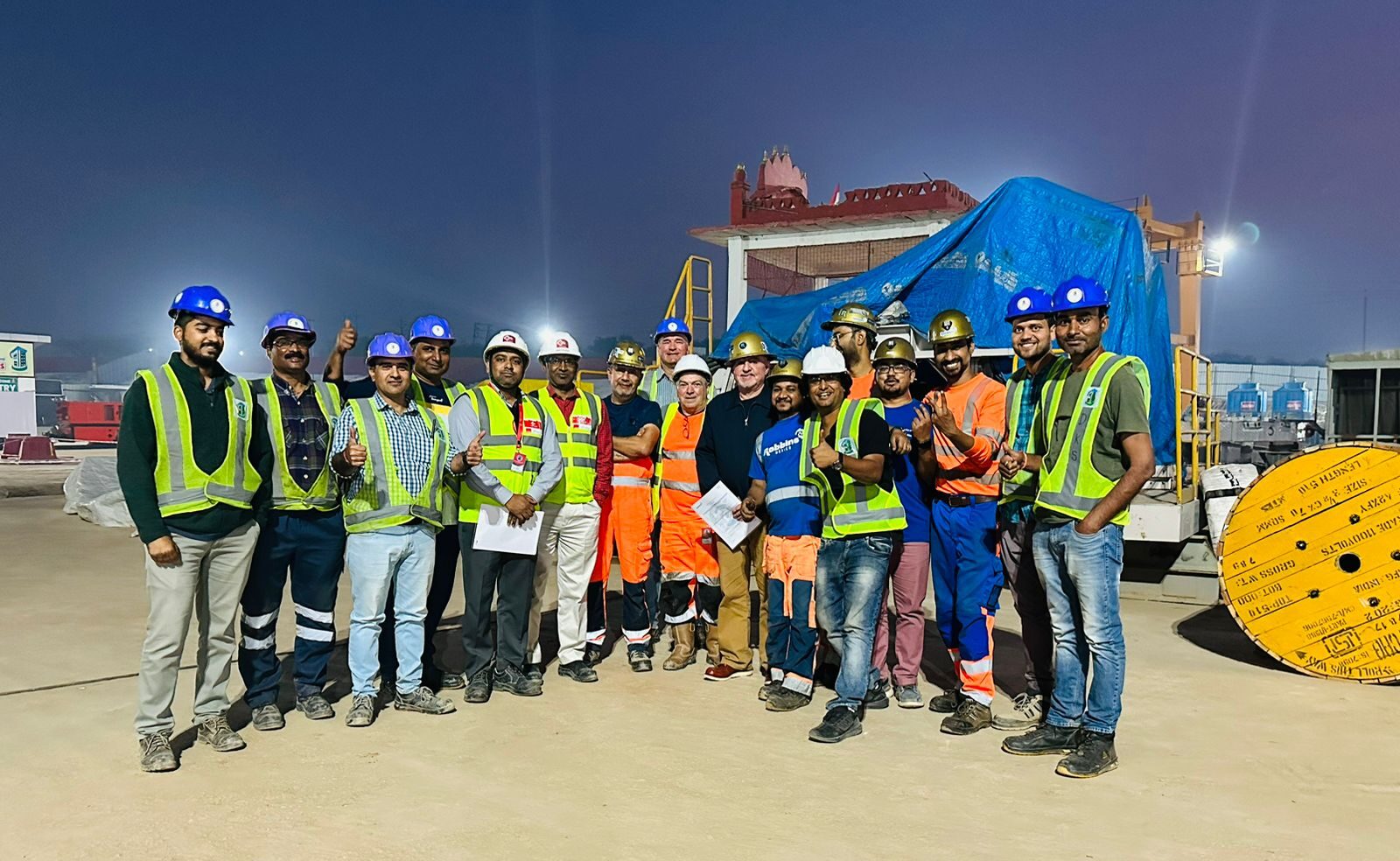
The Robbins team celebrates a successful site acceptance test for the first of two Robbins EPBs at Agra Metro.
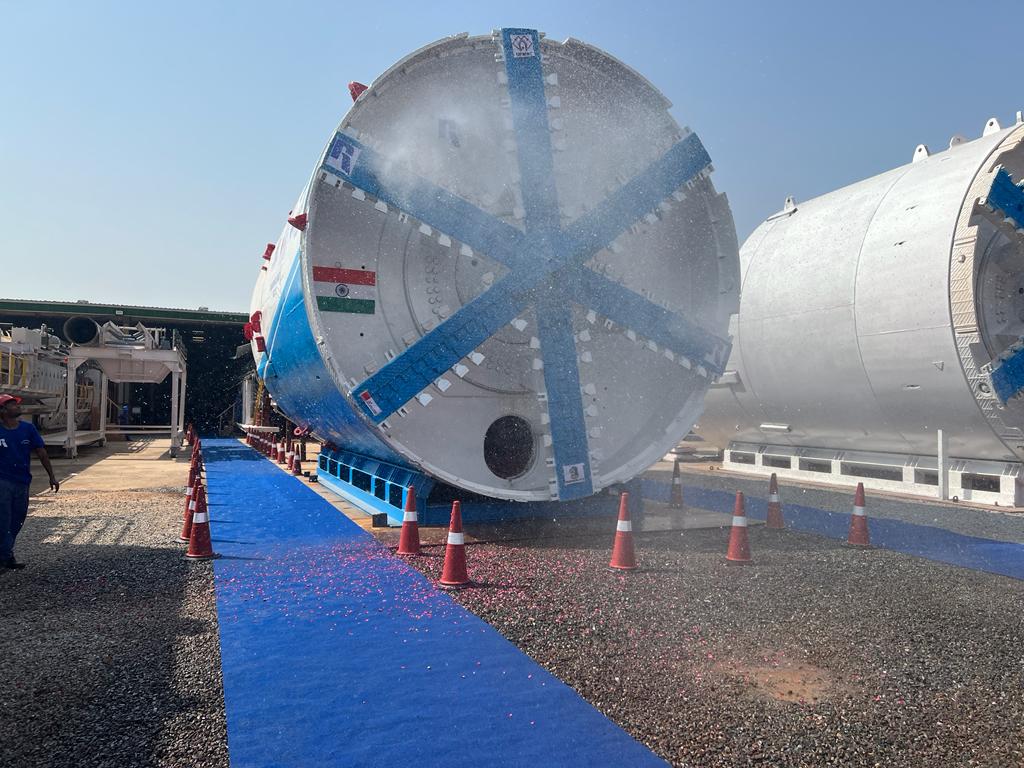
The Robbins EPBs, seen during their Factory Acceptance, are designed for soft soils.
To Second Site Acceptance…
With the first TBM well into tunneling, a second 6.65 m Robbins EPB underwent site acceptance on April 13, 2023 to bore a parallel 1.3 km long tunnel in soft soils. The crew gathered for a ceremony before sending the TBM on its way.
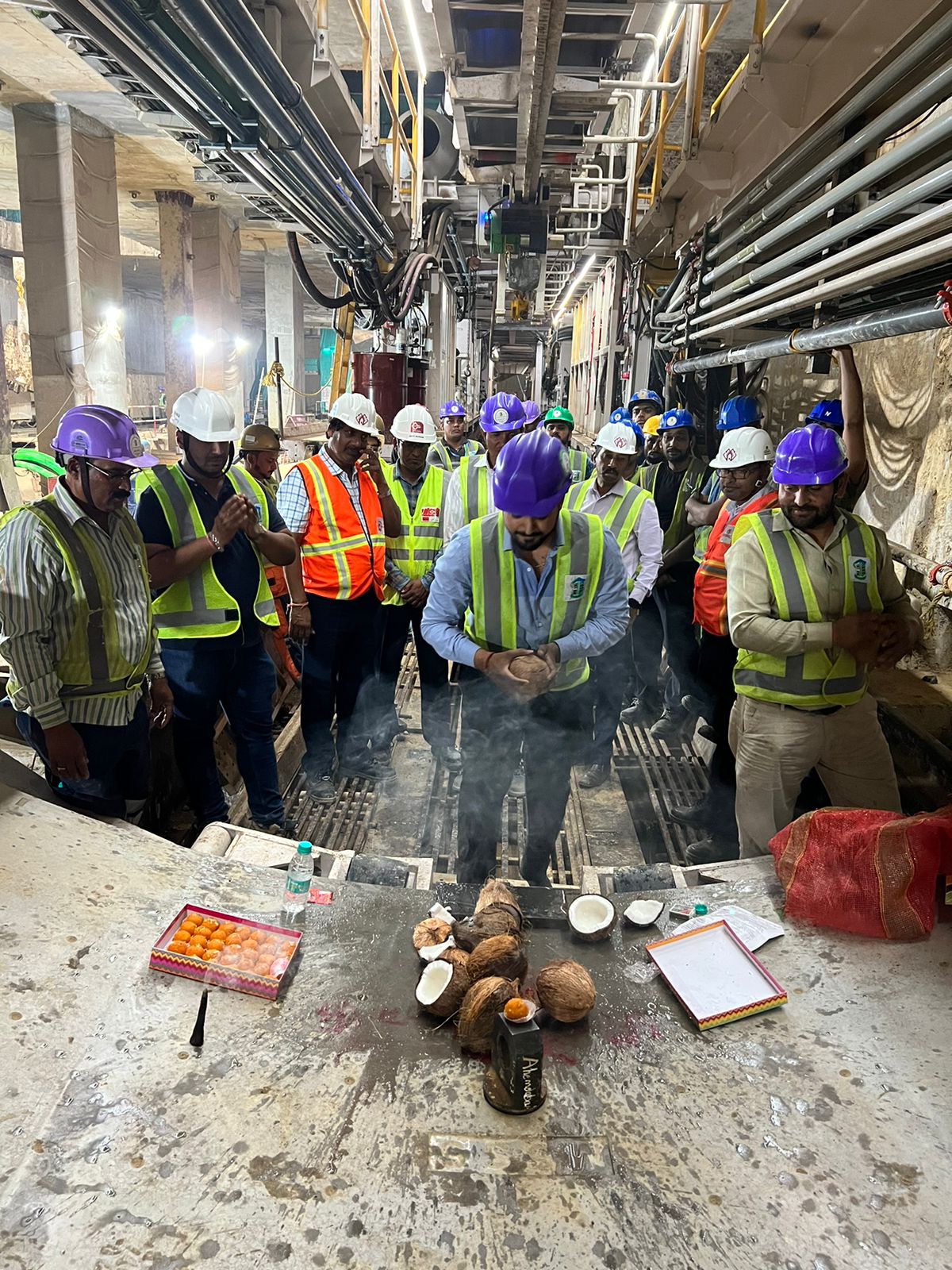
The crew gathers for the site acceptance ceremony of the second Agra metro EPB.
To First Breakthrough!
Just a few days later on April 26, 2023 the first machine made an intermediate breakthrough into a station site, completing the Jama Masjid to Agra Fort stretch of the metro. The machine bored a total of 345 m in sand and clay, and broke through to a celebration by the crew and project teams.
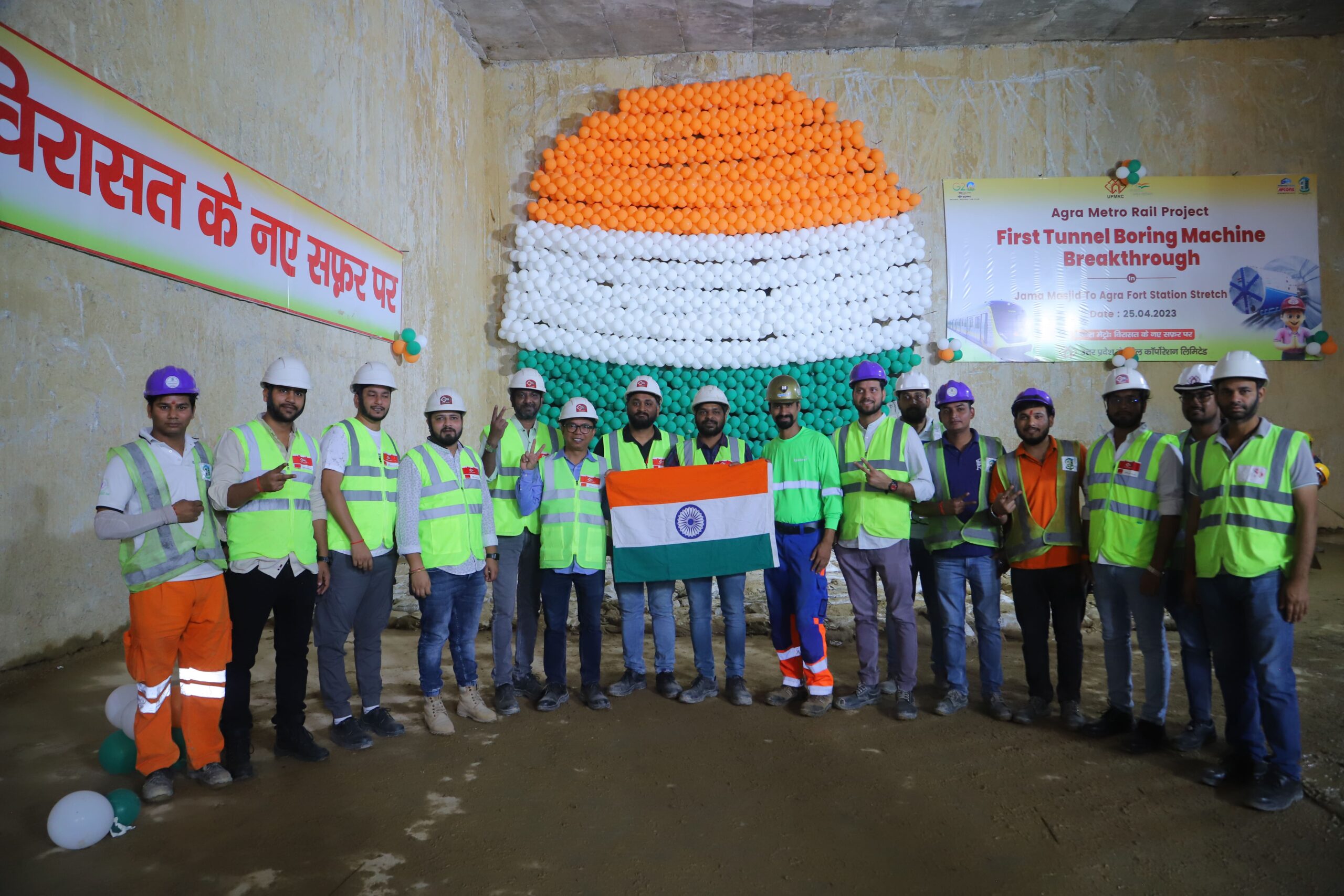
The crew anticipate the first breakthrough of the Robbins EPB at Agra Metro.
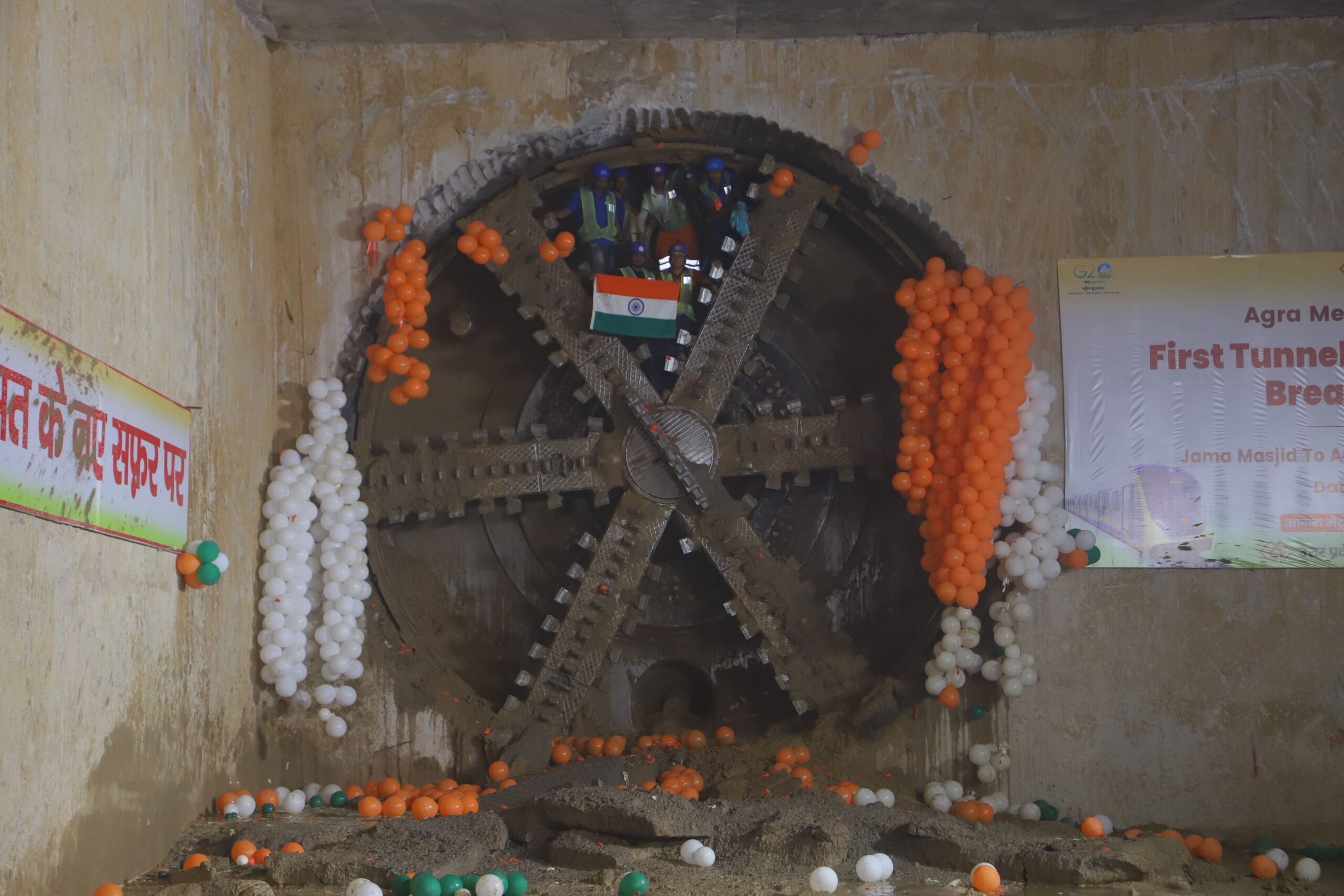
The Robbins EPB breaks through to much fanfare at Agra Metro.
New Delhi Metro: Machines Ramping Up
On February 27, 2023 the first of two 6.65 m diameter EPBs for the Delhi Metro (owner is Delhi Metro Rail Corporation) was completed in the Robbins Gurgaon, India facility. The mixed ground machine will bore a 3 km long tunnel through rock with some gravel, sand, silt and clay for contractor Afcons Infrastructure Ltd.
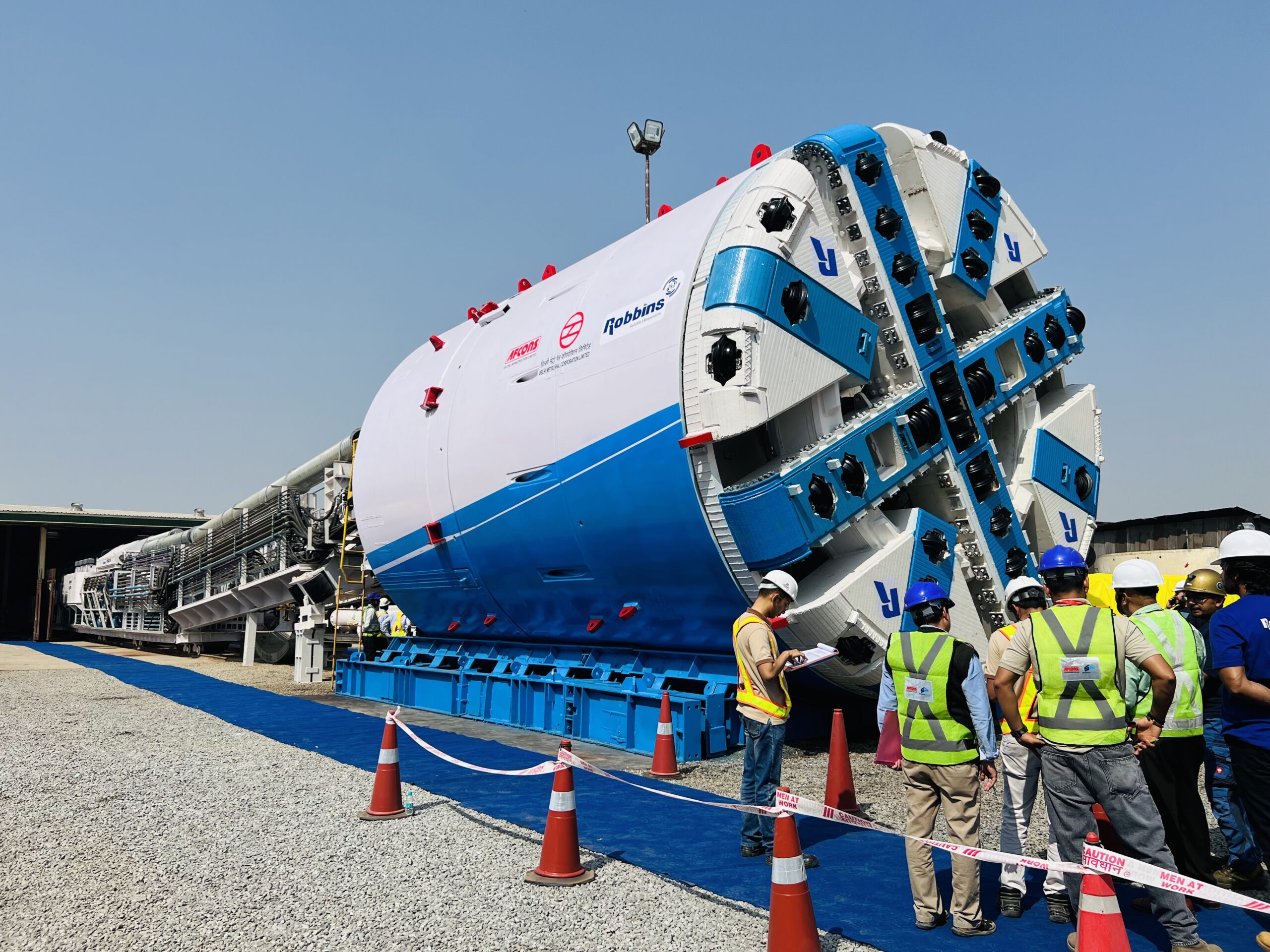
The first of two TBMs set to bore in mixed ground at Delhi Metro, during the factory acceptance in February 2023.
A second machine factory acceptance followed in April 2023. Both machines are scheduled to launch on parallel tunnels this summer.
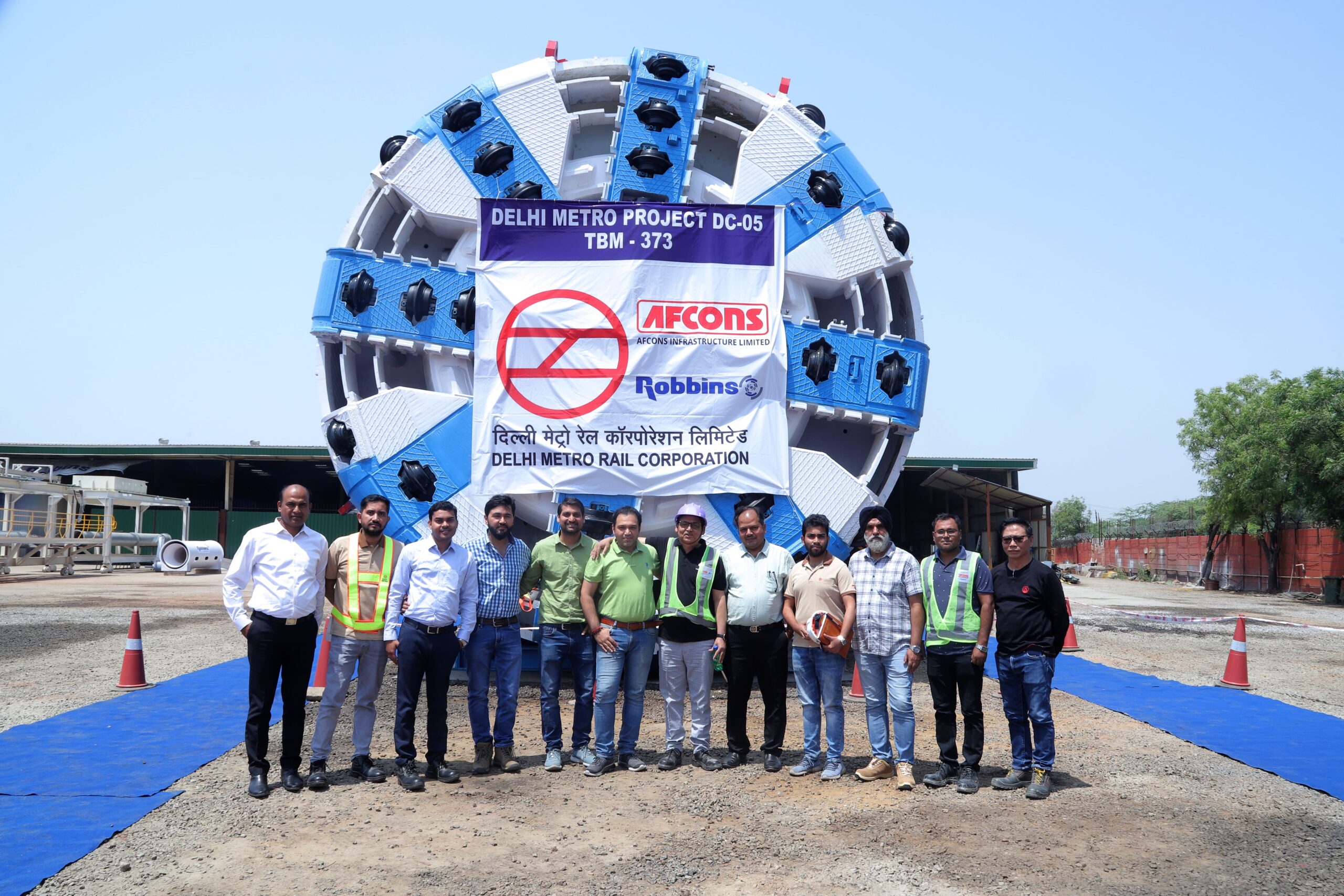
The second Delhi Metro EPB, designed to bore in mixed ground conditions.
RETC 2023
Event Name: RETC 2023
Dates: June 11-14
Location: Boston, MA, USA
Venue: Sheraton Boston Hotel
Booth No: 409
The Rapid Excavation and Tunneling Conference (RETC) is sponsored by the Society for Mining, Metallurgy & Exploration (SME). The show focuses on developments, technology, trends, and innovations that directly affect the tunneling and underground construction industry through a wide variety of technical presentations. Stop by the Robbins booth #409 to meet with our expert staff and find out the latest about our products and projects. Be sure to check out our technical presentations as well:
Monday June 12
Hard Rock TBMs and Tunnels Session
9:30-10:00 AM
Enhanced Probe Drilling and Pre–Grouting Design and Recommendations on Hard Rock TBMs
Presented by Stryker Magnuson, Robbins Design Engineer
10:30-11:00 AM
Record-Setting Tunnel Boring Below Lake Ontario at the Ashbridges Bay Outfall Tunnel
Presented by Doug Harding, Robbins Vice President
WTC 2023
Event Name: ITA-AITES World Tunnel Congress
Dates: May 12-18, 2023
Location: Athens, Greece
Venue: Megaron Athens International Conference Centre (MAICC)
Stand: 59
Come join us May 12-18 in Athens, Greece for the ITA-AITES World Tunnel Congress, the premiere event for tunneling and underground construction. More than 2,000 professionals are set to take part in the world’s top-attended tunneling conference, where hundreds of technical papers will be presented on the latest topics of interest. Stop by our stand 59 to converse with our expert international team, and find out the latest about our products, projects, and talks at the conference.
Technical Presentations:
Tuesday May 16
Track 2, Theme 4 Mechanized Tunneling
4:30 – 4:50 PM
Mitropoulos Hall
Record-Setting Large Diameter Mixed Ground Tunneling in Turkey: The Eşme-Salihli Railway Tunnel
Presented by Detlef Jordan, Sales Manager Europe
Wednesday May 17
Track 4, Theme 6 Tunneling in Challenging Conditions: Case Histories and Lessons Learned
12:40 – 1:00 PM
MC2 Hall
Lessons Learned During Excavation of the Incredibly Challenging Yin Han Ji Wei Water Diversion Tunnel
Presented by Lok Home, Robbins President
NASTT No-Dig
Event Name: NASTT No-Dig 2025
Dates: April 30-May 4, 2023
Location: Denver, Colorado
Booth: 441
Join experienced Robbins staff at the largest trenchless technology conference in the world, NASTT No-Dig in Denver, Colorado. Find out more about our line of Robbins Small Boring Units (SBUs) —game changers in the trenchless industry, saving you time and money on your next hard rock or mixed ground utility tunnel.
Robbins Double Shield Launches in Nepal
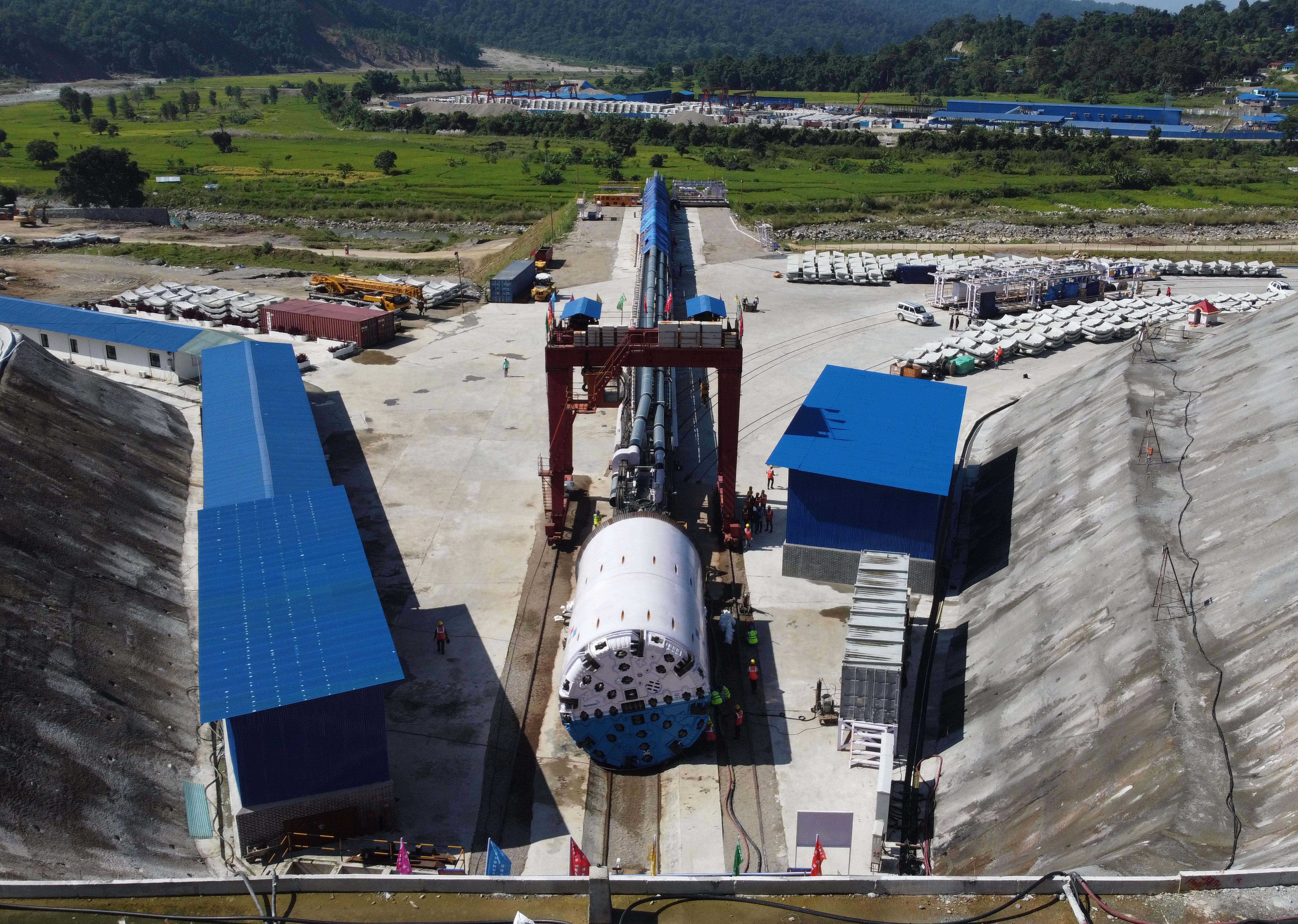
Since the Robbins TBM’s launch, it has bored over 500 m, with a best week of 224.6 m, and a best day of 36.6 m.
In October 2022, China Overseas Engineering Group Co. Ltd and China Railway No. 2 Engineering Group Co Ltd launched a 6.4 m diameter Robbins Double Shield TBM. The TBM is boring the 13.1 km headrace tunnel for the Sunkoshi Marin Diversion Multipurpose Project (SMDMP) located in southern Nepal. The tunnel is connected to a new 28.6 MW surface powerhouse on the Marin River to alleviate the shortage of power supply in the area. It will also be used for farmland irrigation in the districts of Dhanusha, Mahottari, Sarlahi, Rauthat and Bara in the Terai Plain, diverting water from the Sunkoshi River to the Marin River. Since the TBM’s launch, it has bored over 500 m, with a best week of 224.6 m, and a best day of 36.6 m.
The headrace tunnel is being bored through granitic rock with maximum overburden of 1,320 m. Geological conditions may include squeezing ground, fault zones, and water inflows. In particular, a major fault zone is located approximately 4 km into the tunnel at Dhanamana Khola. The machine was customized for the conditions, explains Mr. Liu Fengfan, Project Manager for contractor B-2/COVEC: “The TBM shield is a tapered design to reduce the risk of becoming stuck in squeezing ground; there is an enclosed cutterhead design to reduce the collapse of surrounding rock as well. The TBM has overcut capabilities, and a high thrust. It has also been designed to be equipped with an extra high torque cutterhead drive, as well as strong auxiliary thrust to be used in squeezing ground or weak fault zones to keep the machine from becoming stuck.”
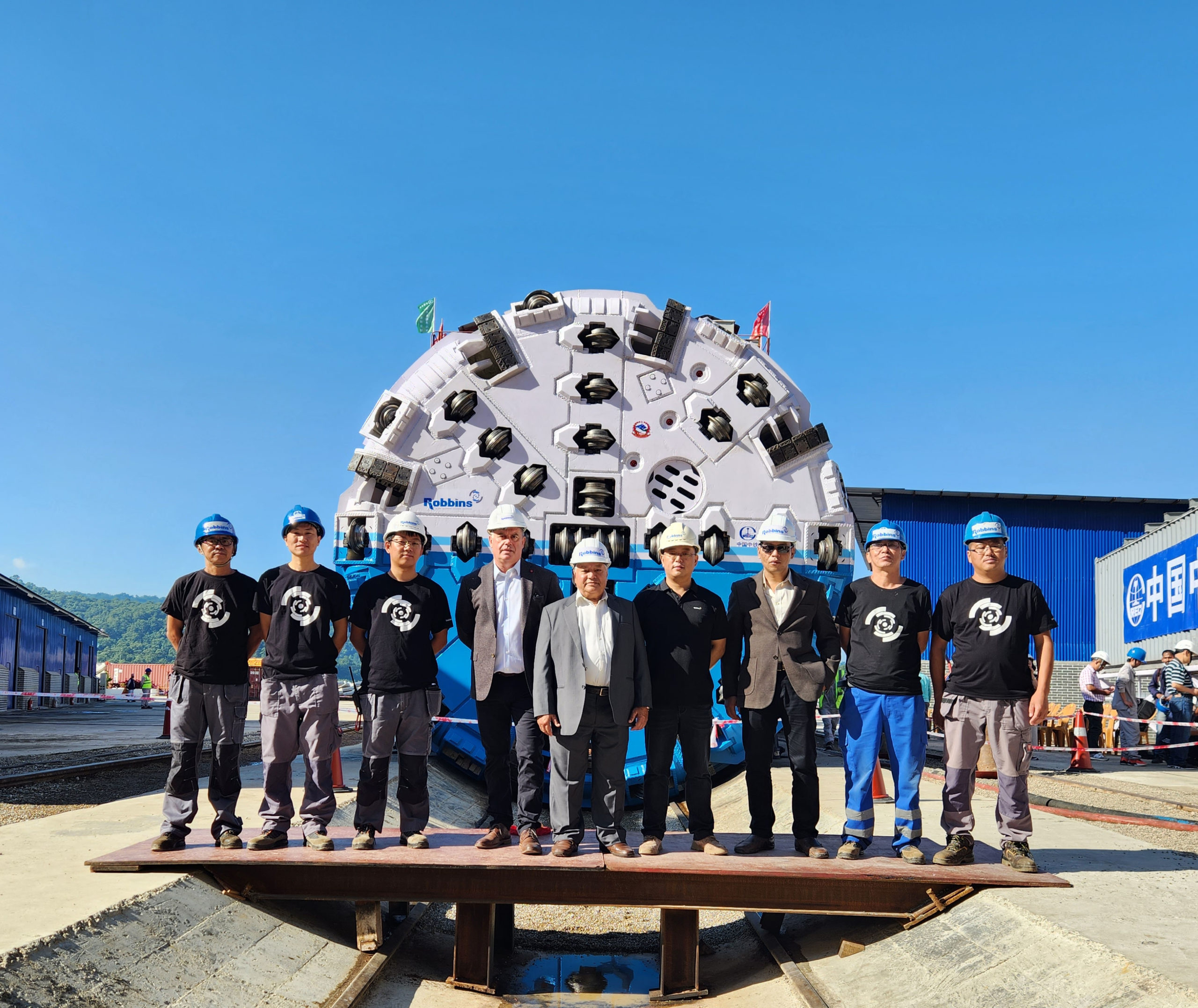
The Robbins Double Shield is engineered for ground conditions including granitic rock with sections of squeezing ground and fault zones with potential water inflows.
As for the major fault zone, to be reached in approximately June 2023, and other zones of concern, Mr. Liu’s plan is well-thought-out: “We have prepared the advance geology forecast along with technical measures and equipment to cope with the extraordinary geological conditions. These include advance drainage holes, pre-excavation grouting (both ordinary and chemical), and other methods based on our experience. When we reach the major fault zone at Dhanamana Khola we will go slow, with more probe drilling while in the fault zone.”
The tunnel is the machine’s second: on its 12.2km first tunnel (the Bheri Babai Diversion Multipurpose Project/BBDMP), the TBM finished nearly one year early and achieved 1,202 m advance in one month. “The Robbins TBM at BBDMP successfully broke through the 12.2 km tunnel and overcame extraordinary geological conditions especially in fault zones. Its stable and excellent performance and function have been verified very well. We have much confidence in the TBM to be used in SMDMP,” said Mr. Liu.