新闻及资讯
Breakthrough Robbins “Crossover” Machine Breaks Through
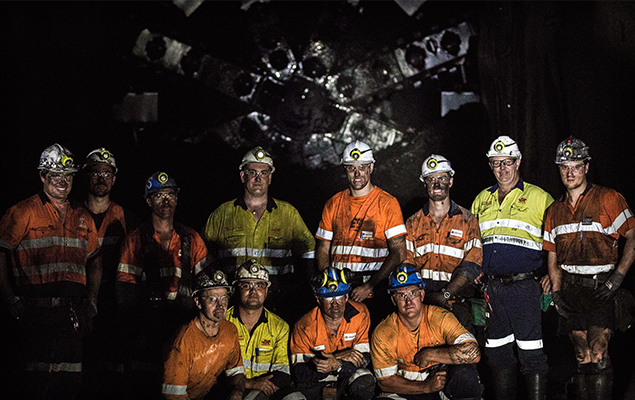
Workers from owner Anglo American celebrate the breakthrough of the Robbins Crossover Rock/EPB machine on February 9, 2015. Image courtesy of Anglo American.
The News in Brief:
- The Grosvenor Decline tunnel marks the first method of a TBM being used in a coal mine in Queensland.
- The unique Crossover Rock/EPB TBM features design aspects from both hard rock Single Shield and soft ground EPB TBMs to bore through a variety of ground.
- The “Crossover” designation is new for Robbins, and will going forward be the designation for all types of Dual Mode TBMs.
- The Crossover TBM for Grosvenor was uniquely designed for excavation in conditions that included the potential for methane gas. It was designed as Class 1, Division 2 Coal Mine Compliant.
- The TBM excavated at rates fourteen times that of a traditional roadheader operation (70 m per week on average vs. 5 m per week).
- The TBM broke through into an active section of the coal mine on February 9, 2015, completing excavation of two mine access tunnels.
Full Press Release:
A ground-breaking TBM brought a mining operation one step closer to first coal on February 9, 2015. The Robbins Dual Mode “Crossover” Rock/EPB TBM completed tunneling at Anglo American’s Grosvenor Project in Queensland, Australia. The “Crossover” designation is new for Robbins Dual Mode TBMs, and will be used for all such projects going forward. The efficient type of TBM used at Grosvenor is now known as an XRE, standing for Crossover between Rock/EPB. Other types of machines are designated the XSE (Crossover between Slurry/EPB) and the XRS (Crossover between Rock/Slurry).
The Grosvenor Mine, a Greenfield coal operation, was the first to utilize TBM technology for mining tunnels in Queensland. Mine owner Anglo American Coal chose the 8.0 m (26.2 ft) machine for two decline access tunnels at grades of 1:6 and 1:8, one for conveyors and another for people and equipment.
The XRE TBM was picked over the traditionally-used roadheader method for several reasons, including excavation speed and tunnel maintenance. The choice proved prescient with the machine excavating at a rate approximately ten to fourteen times faster than a roadheader™bout 70 m per week for the TBM vs. 5 m per week for a roadheader. In addition, the final tunnels have a smooth profile and are segment-lined, requiring minimal upkeep during the planned 40-year life of the mine. “In the coal mining community, and certainly in Queensland, companies are aware of the Grosvenor project and how it has set a benchmark for underground access drift construction,” said Glen Maynard, Robbins Field Service Site Supervisor at Grosvenor.
The machine’s Crossover capabilities enabled it to operate in both hard rock and mixed ground. In addition, the TBM was required to operate during gaseous conditions. The unique TBM design included a cutterhead capable of interchanging hard rock and soft ground cutting tools, a two-stage center-mounted screw conveyor, a “quick removal” shield system, and flame-proof machine components due to the possibility of methane gas in the underground environment.
The TBM was optimized for hard rock and mixed ground excavation in geology ranging from soft clay and soil to sandstone and basalt. The two-stage screw conveyor worked in both ground conditions to draw muck from the tunnel face. Two sets of shields were built for the TBM’s “Quick Removal” system, and were detached from the machine at the end of each blind tunnel to be left in the ground for constant support, a requirement in Australian tunnels. The inner core components of the TBM were then retracted out of the segment-lined tunnels on specially designed transport dollies.
The machine began boring the conveyor tunnel in December 2013, and after completion in May 2014 was successfully retracted and transported to the second tunnel site. The machine was then re-commissioned for the people and equipment tunnel in November 2014 with a new set of shields. Once excavation commenced, boring was completed in 88 days at an average of 10.9 m per day, with a best day of 25.2 m. The bore itself was similar to the first, with few challenges encountered other than elevated methane gas levels that required several temporary stoppages in order to safely remove the gas from the tunnel. “The machine performed very well and had high reliability. The cutting tools, in particular the knife edge bits, were exceptional. The bits were required for most of the drive and one complete set lasted 650 meters,” said Maynard.
The team is now preparing the machine for its final retraction and roll-out, and it will be on the surface in less than two months. The TBM will then be stored onsite for future Anglo American mining projects.
Once the longwall mine is operational in 2016, Grosvenor is expected to produce five million tonnes of coal per year over the next 26 years.