Project Categories: 跨模式掘进机
盖雷德输水隧道项目
罗宾斯跨模式掘进机在土耳其迄今要求最苛刻的隧道中脱颖而出
项目概况
盖雷德(Gerede)输水隧道大概是世界上最困难的隧道工程之一,数十个断层带和高达20巴的巨大水压仅仅是其中需要克服的两个挑战。在罗宾斯公司参与之前,一家欧洲制造商提供了三台标准双护盾隧道掘进机试图挖掘隧道,但其中的两台在遇到大量的淤泥和碎岩流入后被困住,无法挽救。2016年,一台罗宾斯跨模式XRE隧道掘进机开始挖掘总长31.6公里(19.6英里)的供水隧道中的最后9公里。由于首都安卡拉长期遭受严重干旱,这条输水隧道被认为是土耳其的首当务之急。一旦完成,补给线将从盖雷德河引水,成为土耳其最长的输水隧道。
地质概况
土耳其处于一个地质构造活跃的地区,很大程度上受阿拉伯板块和欧亚板块碰撞的控制。从更详细的层面上来说,一块面积几乎与土耳其相同,被称为“安纳托利亚板块”的大陆地壳正被向西挤压。该板块向东连接着北安纳托利亚断层,向东南连接着东安纳托利亚断层。断层区的地质条件往往非常多变和不稳定。
在该项目中,安纳托利亚断层带的确制造了许多障碍。地质测试和钻孔样本显示,一种由包括凝灰岩、玄武岩和角砾岩在内的火山岩混合物改变成了类似砂岩、页岩和石灰岩的沉积岩形式。所有这些岩层都被包含有粘土和冲积层的断层带所打断。这台交叉隧道掘进机还将面临一个含水层系统,可能引起高达20巴的高压涌水
机器设计
由于地质原因,该项目使用的掘进机需要一个经过优化的可转换式刀盘来对付坚硬的岩石。刀盘在设计上可以轻易在硬岩和土压平衡(EPB)模式之间进行转换,刀盘外罩可以安装在盘形滚刀或硬质合金刀具上。此外,刀盘采用单向操作设计。所有这些用在XRE掘进机上的设置,可以使挖掘效率更高、消耗动力更低、重新研磨的概率更小。为了应付艰难的地层条件,该项目使用的掘进机还配备了特殊的传动装置。
为了保护机器不受到预计的高水压影响,掘进机采用了一个全面的密封系统。在主轴承周围,有6个密封圈组成的外排密封和3个密封圈组成的内排密封。每个密封圈之间的腔内注满润滑脂以确保恒定压力。万一机器停机,涌水来袭,压力传感器就会检测到涌水,并用润滑脂冲击密封系统来持续保护密封装置。铰接接头、支撑和稳定靴也采用同样的方式进行密封
或许在这个项目中使用的隧道掘进机在设计上最重要的部分之一是螺旋输送机。由于存在大量涌水的可能,掘进机必须配有一个密封的螺旋输送机。然而,通过螺旋输送机输送岩石会产生极大的磨损。为了考虑可能的磨损,螺旋输送机在整个输送线上的耐磨板都设计成可更换式,输送机本身也由多个短节组成,如有需要可以拆卸和更换。输送机还设置了多个人孔用于维修耐磨板,而两个大型可拆卸外壳可以容纳整个螺旋输送机的所有短节
由于地质情况难以预料,掘进中要对任何可疑区域进行探测和灌浆封堵,以保护掘进机不受疏松岩体和水压的影响。掘进机使用了一个由12个直径100毫米,7度角的舱门组成的标准阵列,等间距地分布在后护盾周围。每个舱门都由一个球阀密封,直到需要进行探测时才打开。另外,10个同样尺寸的舱门直接通过前护盾分布,用于探测和灌浆。6个额外的舱口安装在掘进机前部台座上,可以配合位于刀盘中部的气动冲钻使用。
隧道掘进
这台罗宾斯跨模式XRE隧道掘进机于2016年夏天开始挖掘,使用了一些最初的双护盾隧道掘进机中的备用组件和早就为该项目储备好的剩余管片。工作人员在被卡主的双护盾隧道掘进机的一边挖掘了一条旁路隧道,罗宾斯掘进机的组件由南边洞口进入,在一个地下出发仓内采用现场首次安装调试方案(OFTA)进行组装。涌水加大了机器部件的运输难度,但是定制化设计的平板车克服了这个问题,平板车配备的液压升降机将掘进机较大尺寸的部件通过隧道运送到组装仓
罗宾斯掘进机以一个轻微的坡度钻孔开挖隧道的剩余部分,绕过了被卡住的机器,然后逐渐与原来的隧道进行对准。由于遇到了高达32巴的水压、冲积土、流动物质和粘土,这台掘进机需要在土压平衡(EPB)模式下进行操作。通过后护盾超前钻机舱门排出地下水减低了水压,这些舱门配备了常闭型球阀。在通过起初被掩埋的双护盾隧道掘进机区域并继续推进50米(164英尺)后,超前钻进成为常态。至今为止,罗宾斯掘进机已经贯通了剩余隧道长度的25%,并且已经穿过了导致双护盾隧道掘进机被卡住的地段。
墨西哥城的TEP二期隧道
项目概况
作为墨西哥城废水管理工作的一部分,罗宾斯跨模式(XRE)掘进机被选为开挖项目一条5.8公里(3.6英里)的隧道,这使它成为第一台在北美开挖隧道的跨模式掘进机。直径8.7米(28.5英尺)的机器兼并硬岩单护盾和土压平衡模式,可以在截然不同的地质下作业。隧道一旦竣工,将防止城市地区的洪水泛滥,并将污水输送到该地区的第一个污水处理厂,影响210万人的生活。
地质状况
隧道的路径穿过一座高达170米(560英尺)的山脉,穿过离隧道顶部仅8.0米(26.2英尺)的断裂带。隧道的大部分隧道段包括带着凝灰岩带的安山岩,和断裂带里的软土,以及隧道尽头长874米(2,870英尺)的复合软土隧道段。
机器设计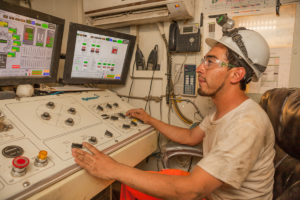
罗宾斯跨模式XRE掘进机的特点是配备可转换的刀盘,它可从坚硬的岩石刀盘转变为土压平衡的刀盘,另外还有一个可拆卸的带式输送机和螺旋输送机,以及多级变速箱,以增加在困难的地质下作业的扭矩。脱困扭矩是可以让掘进机在困难的地质下,不被卡住并自己推进–多级变速箱可以让设备在低速高扭矩下运行,类似土压平衡盾构机运行原理。多级表塑像,可以让刀盘在困难的地质下脱困,否则它可能会被卡住。在硬岩隧道段,掘进机会可以在标准的低转矩,高转速的硬岩模式下运行
这台跨模式的掘进机还有对付困难的地质的其他功能。独特的掘进机被设计抵御涌水,在几个山谷下面开挖。如果碰到大量涌水,位于淤泥槽上的切断台门能够将混合土仓从机器的其余部分封闭起来。通过这种方式,掘进机可以被动地承受较高的水压,而操作人员同时可以采取措施去排水和加固围岩
这台机器配备了连续的超前钻机,使得设备可以广泛的探测前方地质。除了标准的超前钻机外,拱梁钻机还提供了用于注浆和安装超前支架的另一个环,位于隧道顶部120度、靠近刀的位置;而第二套超前/ 注浆钻则位于机器后方,允许设备打出两种型式的孔。
隧道掘进
2015年8月,这台配备20英寸滚刀的跨模式掘进机在硬岩模式下始发。这是一种冒险的举动,因为设备在进入硬岩地质段前的第一段地质是软土。但是设备的速度很快就跟上来了,在12月创下了纪录,又在1月份的时候,机器达到了最快的日进尺42.8米(140英尺),最快周进尺185.1米(607英尺)。
在2016年年初,掘进机击中了几个接触区的第一个,一个30米(98.4英尺)宽包含破碎岩石和块状岩石。虽然通过接触区进行的挖掘工作进展缓慢,但在更坚硬的安山质碎屑岩石中速度再一次跟上了。在2016年3月,在80米(262.5英尺)深井贯通了隧道,随后设备经过检查和维修,继续前进。
到2016年6月,设备在相当坚硬的地质里掘进,并且创下了两项掘进机的国家纪录,它们分别是日进尺57米(187英尺),月进尺702.2 米(2303.8英尺)
设备在2016年秋天在破碎的安山质碎屑岩石中掘进时,遇到了一个自然发生的洞穴,它被认为是一个过渡地带的岩石坠落的结果,或者是一个古老的地下湖体它侵蚀了岩石造成。岩洞面积约90立方米,其中不稳定层面积约57立方米。掘进机此时停机,立即采取措施填补了洞穴。
模式替换
到2016年10月底,掘进机已经到达了软土地层的最后部分。在浅埋深的最后一个区域,从隧道顶部到地面的距离小于机器直径的1.5倍,地面有重塑土的一致性。居民区域意味着下沉必须保持在最低限度,并且施工团队决定设备转换为土压平衡模式
将掘进机转换为土压平衡模式需要多个步骤。转换过程开始于刀盘的修改,增加了新的泡沫线的管道,将碴石铲斗上的刀变成了土压平衡的软土刮刀,并去卸除碴石铲斗。在刀盘上的可移动的面板被改变,从硬岩石刀盘改变为土压平衡模式刀盘需要的开口率(从7.9%到18.95%的开口率)。其他步骤还包括在土仓里安装混合条,把掘进机的带式输送机切换城螺旋输送机,为土压平衡的添加剂改变流体系统,并安装盾尾密封和铰接密封,以使设备能在压力下掘进。
这台机器已经盖住完成,准备在2017年初开始继续掘进。由于地面坡度只有12到14米(39到46英尺),这台机器会在埋深大约18米(59英尺)的隧道段开始作业。到2017年3月,掘进机表现良好,只剩下517环(约7.75米,2.543英尺)。掘进机在软土地质段,仅在一个12小时排班操作下,最佳日进尺达到13环(19.5米,64英尺),尽管由于居民区域的限制,工作时间有限。设备还是在2017年5月下旬成功贯通。
卡基水力发电项目
罗宾斯双模式掘进机克服种种挑战,并促成了跨模式掘进机的诞生
项目概况
在600米(1,968英尺)埋深下穿越土耳其中部的山腰,Kargi Kizilirmak(卡基)水力发电项目是该地区完成的最具挑战性的隧道工程之一。承包商Gulermak采用了罗宾斯一个直径10米(32.8英尺)的双护盾硬岩掘进机为来开挖将水从大坝引到发电站的头道隧道。整个隧道,包括全断面隧道掘进机和爆钻开挖部分,长度为11.8公里(7.3英里)。该项目每年为项目业主Statkraft制造470千瓦时的电力,足以供应约15万户家庭。这个项目极具挑战性的地质条件使得机器必须在隧道内进行改造。这个项目遇到的种种困难很大程度上促成了今天使用罗宾斯的跨模式系列掘进机的诞生。
地质条
隧道沿线的地质预计由基里巴斯复杂卡基蛇绿岩(包括砂岩、粉砂岩和泥灰岩)最初的2300米(7545英尺),紧随其后的是1000米(3280英尺)的昆达斯变质岩(包括大理石、梅特拉瓦和变泥质岩),剩下的8500米(27887英尺)由比纳麻斯火山岩(包括玄武岩、聚结和安山岩)。岩石的强度预计达到了140 兆帕。多个断裂带和过渡区增加了地质条件的复杂性。
始发
在2010年初始发后不久,这台机器就遇到了地质报告中所描述的严重问题。地质学由块状岩石、沙和黏土组成。掘进至80米(262英尺)的设备被困在一段坍塌的地面上。为立即应对避免了刀盘被困在块状岩石中,工作人员开始了半次冲程半次重置。尽管采取了这些措施,但这台机器遇到了一段非常松散的地面,粘土含量很高。另一个坍塌发生在刀盘的前面和渣土的重量困住了刀盘
在评估了所有可用选项后,决定需要一个旁路隧道。罗宾斯现场服务协助施工商Gulermak设计隧道和制定解决方案,让刀盘脱困,稳定了受干扰的地面。爆破技术被排除,因为对爆炸引起的振动引起的进一步塌陷的担忧; 因此,挖掘工作是用气动的手持破碎机进行的。本希望这段不好的地方将会是偶然情况,很快就被证明是错误的,而且地质的实际复杂性变得很明显。在隧道的前2公里(1.2英里)内还需要6个旁通隧道。
承包商和制造商通力合作一起开发和改量了旁路隧道的掘进和手工隧道施工技术,这使得平均修建一条旁通隧道旁的时间仅为14天。虽然有明显的延误与停机时间有关,所有的隧道都安全及时地完成了。尽管遇到了很多挫折,但掘进机还是成功地穿越了许多可以卡住机器的断层。旁通隧道工程已经成功完成,这意味着,困难地质地段被认为将成为个别事件。
跨模式掘进机的诞生
为了在困难的条件下取得进展,承包商、业主、顾问和罗宾斯工程师共同努力制定了解决方案。承包商在现场服务团队的协助下,安装了一个罗宾斯定制的拱顶钻机和定位器,以允许管道支架通过前盾安装。钻机可以在刀盘之前达10米(33英尺)探测围岩,直径90毫米(9厘米)的铁管顶部120至140度的隧道顶部提供额外的支撑。在软土地上挖掘时,注入树脂和灰浆防止拱顶坍塌。由于成功使用的超前钻技术, 施工商Gulermak能够测量和回填高度高于刀盘在某些断层超过30米(98英尺)地围岩, 此外, 能够帮助检测松散土壤接缝和掌子面前方的破碎岩石。
为了进一步减轻挤压地层或倒塌的影响,定制的减速器被订购并改造成刀盘发动机。它们安装在驱动电机和主要两级行星变速箱之间。在标准掘进操作过程中,减速器以1:1的比例操作,不提供任何额外的减量,并允许刀盘转速达到挖掘硬岩的速度。当机器遇到松动或挤压围岩时,减速机投入使用,从而降低了刀盘速度,但可用扭矩增加了近一倍。这种修改使双护盾硬岩掘进机在断裂带和挤压地层区域可以像像土压平衡盾构机一样扭矩和低转速挤地运转。这些方法有效地防止了机器被卡住。此外,在正常的辅助推力与双重总推力之间安装了短冲程推力千斤顶。
从卡基项目掘进机的修改不被认为是孤立的地质应对设计,让罗宾斯开发新系列双模掘进机,现称为跨模式掘进机。跨模式掘进机也被称为混合模式或双模式掘进机,能够在地质迥异的隧道。跨模式掘进机的特征是兼并两种掘进机类型的操作模式,并且是本需要多台掘进机开挖的混合地质隧道的理想选择。
创新成果
尽管最初进展缓慢,但罗宾斯的双护盾掘进机在修改后取得了一些显著的进展,这使得它成为具有双模式特征的双护盾掘进机。在2013年3月实现了一个月600米(1,986英尺)的进尺,并在2014年春季取得了项目最佳月进尺约723米(2372英尺),其中包括2014年4月最好的日进尺39.6米(130英尺)。这些表现,让掘进机明显优于从隧道的另一端采用钻爆法的开挖。那一端采用钻爆法开挖的工作人员在相对良好的地质4公里(2.5英里)的隧道段下,月进尺可达近300米(984英尺)。采用隧道掘进机开挖的隧道段全长7.8公里(4.8英里),于2014年7月完成了隧道最后一个贯通。
格罗夫纳斜井隧道
首台应用在昆士兰采矿隧道上的掘进机
项目概况
格罗夫纳矿业, 一个以绿色煤矿开采的运营管理, 是第一个昆士兰采用全断面隧道掘进机技术开挖隧道的矿场。业主英美资源集团选择了直径8米的罗宾斯跨模式掘进机和连续输送机系统, 同时采用了罗宾斯经验丰富的现场服务团队提供的现场首次安装调试方案(OFTA)组装设备。由于隧道开挖速度和维护等因素表现更出众,项目选用了新型的跨模式掘进机而非传统的巷道挖掘机。设备分别开挖两条坡度为1:6和1:8的巷道, 一个用于输送机运输, 另一个用于工人和物料出入。
地质状况
两条隧道的地质状况非常复杂,它们都包含混合地层和硬岩组成。 两条隧道的前300米(984英尺)含大部分的复合软土,比如软粘土和土壤。
机器设计
这台跨模式掘进机可以兼并硬岩和复合软土作业下的功能。此外, 掘进机在气态条件下作业。独特的掘进机设计包括刀盘能互换硬岩和软土的切削刀具, 个两级式、中位安装的螺旋输送机, “快速拆卸系统”, 和抵抗地下环境中甲烷气体可能性的防爆组件。选择这台兼并土压平衡功能的设备,不仅由于软土复合地质, 也因为由于地质含有甲烷气体。 有这样的功能,它可以被稀释或安全地从隧道中清除。
开挖和贯通
格罗夫纳建设项目开始于2012年7月。用于输送机运输的第一条倾斜隧道,输送机, 在2013年12月底至2014年5月开挖作业, 实现进尺每周达90米(295英尺)。快速出渣系统是成功的设计, 它使掘进机的内盾从160米(525英尺)的表面深度,通过专门设计的传输车收回到地面。为了运输机器到下一条2公里(1.2英里)的隧道, 掘进机必须分拆分两个部分, 并需要一个大600吨龙门提升。
2014年11月, 机器再次投入开挖用于工人和材料通道的新隧道作业中。掘进工作用了88天完工,平均每天掘进10.9米(35.7英尺), 最好的一天为25.2米(82.7英尺)。掘进机的平均每周进尺为70米(229.7), 速度是传统巷道挖掘机的14倍。掘进环境和第一条隧道类似, 除了甲烷气体水平升高为了安全地把气体从隧道需要几个临时停工外,还攻克服了一些挑战。2015年2月9日最终贯通。机器在完成第二个隧道, 机器的盾体再次留在隧道内提供持续的支持。
最近要闻
- Twin Robbins EPBs make milestones near Taj Mahal
- Long Haul TBM: Use of a Rebuilt Main Beam Machine at the DigIndy Tunnel System in Indianapolis, IN
- Evaluating TBM Design and Performance, 30 Years Apart: The Lesotho Highlands Water Tunnel, Phase 1 and Phase 2
- Overcoming Mountainous Geology at Nepal's Sunkoshi Marin Project
- Swift Robbins TBM breaks through 11 Months Early